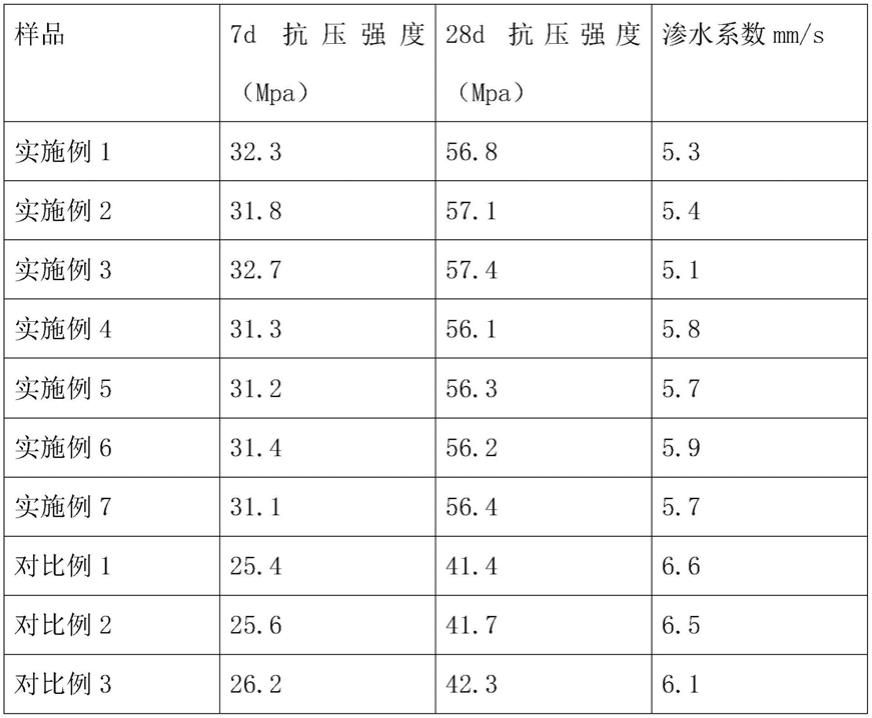
1.本技术涉及建筑材料技术领域,尤其是涉及一种高强度抗裂混凝土。
背景技术:
2.混凝土广泛应用于地下工程、桥梁、水池、水塔、涵洞、隧道、码头、堤坝、水电站等工程领域,通常要求其不仅要有较高的强度、韧性和稳定性,同时还需有一定的防水、抗冻性能。
3.中国专利文献cn104056874b公开了一种混凝土,包括以下原料:水泥、砂、碎石、废弃物煅烧料、外加剂和水,废弃物煅烧料经过以下方法制得:将废混凝土和废砖按照10:3的质量比混合,破碎、研磨成小于30mm的碎粉,备用;将碎粉放入水中,泡2-3天,然后取出烘干;将烘干的碎粉在1000-1100℃下煅烧4-5h,冷却后进行研磨、筛分,分别取粒径为0.15-3mm和5-10mm的煅烧产物,为废弃物煅烧料;通过添加外加剂引入含泥量高的混凝土仍然能够满足建筑要求。
4.针对上述中的相关技术,发明人发现混凝土受环境、温度和疲劳损伤等因素的影响,会不可避免地会产生裂缝,裂缝为外界有害物质进入混凝土内部提供了通道,加剧了内部钢筋的锈蚀,降低了混凝土强度,故有待改善。
技术实现要素:
5.为了提高混凝土的强度,本技术提供一种高强度抗裂混凝土,该混凝土通过添加改性剂,增强了骨料与其他材料的结合紧密度,提高了骨料抵抗断裂的能力,从而提高了混凝土的强度。
6.本技术提供的一种高强度抗裂混凝土采用如下的技术方案:
7.一种高强度抗裂混凝土,包括以下质量份数的原料:水泥100-120份,粗骨料80-85份,细骨料90-100份,改性剂20-30份,耐磨剂6-8份,水50-70份。
8.通过采用上述技术方案,向混凝土中加入改性剂,增强了骨料与其他材料的结合紧密度,提高了骨料抵抗断裂的能力,从而提高了混凝土的强度;耐磨剂的加入,提高了混凝土表面的耐磨性。
9.作为优选,所述改性剂包括硅酸钠和硅烷。
10.通过采用上述技术方案,硅酸钠在骨料表面发生水化反应生成水化产物,水化产物填充了骨料表面的空隙和微小裂缝;水化产物中的凝胶具有胶结能力,会将原本疏松多孔的表面砂浆层和微裂缝进行胶结;硅烷在骨料表面形成一层憎水膜,使得骨料的吸水率降低,而且可以改善凹面结构,使得表面更加光滑,增大了原料之间的接触面积,减小了原料之间的间隙;硅酸钠反应生成的凝胶提高了憎水膜的粘结性,从而提高了憎水膜与其他材料之间的结合紧密度,进而提高了混凝土的强度。
11.作为优选,所述改性剂还包括聚乙烯醇。
12.通过采用上述技术方案,聚乙烯醇本身具有粘结性,不仅可以提高骨料与凝胶之
间的粘结力,使得骨料与其他材料的结合紧密度进一步加强,也可以增强憎水膜与其他材料之间的结合紧密度,从而大大加强了混凝土的强度。
13.作为优选,所述硅酸钠、硅烷、聚乙烯醇的质量比为(3-3.5):(6-7):1。
14.通过采用上述技术方案,将硅酸钠、硅烷、聚乙烯醇的质量比控制在上述范围内,制备出的改性剂使得混凝土的强度具有很大的提升。
15.作为优选,所述耐磨剂为矿渣粉、硅渣粉、硅灰中的一种或几种。
16.作为优选,采用如下步骤制备而成:
17.s1、将改性剂、耐磨剂和水倒入搅拌机中进行搅拌,搅拌一段时间后,制得添加剂;
18.s2、将水泥、粗骨料、细骨料倒入添加剂中,进行搅拌,搅拌一段时间后,制得混合物;
19.s3、倒出混合物,并进行装模、养护,制得混凝土。
20.通过采用上述技术方案,使得水泥、粗骨料、细骨料、改性剂、耐磨剂均匀混合,从而得到质量均一的混凝土。
21.作为优选,所述步骤s1中的搅拌速度为200-250r/min,步骤s2中的搅拌速度为100-150r/min。
22.作为优选,所述步骤s1中的搅拌时间为5-10min,步骤s2中的搅拌时间为10-20min。
23.综上所述,本技术包括以下至少一种有益技术效果:
24.1、向混凝土中加入改性剂,增强了骨料与其他材料的结合紧密度,提高了骨料抵抗断裂的能力,从而提高了混凝土的强度;耐磨剂的加入,提高了混凝土表面的耐磨性。
25.2、硅酸钠在骨料表面发生水化反应生成水化产物,水化产物填充了骨料表面的空隙和微小裂缝;水化产物中的凝胶具有胶结能力,会将原本疏松多孔的表面砂浆层和微裂缝进行胶结;硅烷在骨料表面形成一层憎水膜,使得骨料的吸水率降低,而且可以改善凹面结构,使得表面更加光滑,增大了原料之间的接触面积,减小了原料之间的间隙;硅酸钠反应生成的凝胶提高了憎水膜的粘结性,从而提高了憎水膜与其他材料之间的结合紧密度,进而提高了混凝土的强度。
26.3、聚乙烯醇本身具有粘结性,不仅可以提高骨料与凝胶之间的粘结力,使得骨料与其他材料的结合紧密度进一步加强,也可以增强憎水膜与其他材料之间的结合紧密度,从而大大加强了混凝土的强度。
具体实施方式
27.本技术实施例公开一种高强度抗裂混凝土。
28.实施例1
29.高强度抗裂混凝土包含以下质量份数的原料:水泥100g,粗骨料80g,细骨料90g,改性剂20g,耐磨剂6g,水50g,其中改性剂为硅酸钠、硅烷、聚乙烯醇质量比为3:7:1混合而成,耐磨剂为矿渣粉、硅渣粉混合而成。
30.高强度抗裂混凝土的制备方法为:
31.s1、将改性剂、耐磨剂和水倒入搅拌机中进行搅拌,搅拌速度为200r/min,搅拌5min后,制得添加剂;
32.s2、将水泥、粗骨料、细骨料倒入添加剂中,进行搅拌,搅拌速度为100r/min,搅拌10min后,制得混合物;
33.s3、倒出混合物,并进行装模、养护,制得混凝土。
34.实施例2
35.高强度抗裂混凝土包含以下质量份数的原料:水泥120g,粗骨料85g,细骨料100g,改性剂30g,耐磨剂8g,水70g,其中改性剂为硅酸钠、硅烷、聚乙烯醇质量比为3.5:6:1混合而成,耐磨剂为硅渣粉。
36.高强度抗裂混凝土的制备方法为:
37.s1、将改性剂、耐磨剂和水倒入搅拌机中进行搅拌,搅拌速度为250r/min,搅拌10min后,制得添加剂;
38.s2、将水泥、粗骨料、细骨料倒入添加剂中,进行搅拌,搅拌速度为150r/min,搅拌20min后,制得混合物;
39.s3、倒出混合物,并进行装模、养护,制得混凝土。
40.实施例3
41.高强度抗裂混凝土包含以下质量份数的原料:水泥110g,粗骨料83g,细骨料95g,改性剂25g,耐磨剂7g,水60g,其中改性剂为硅酸钠、硅烷、聚乙烯醇质量比为3.3:6.5:1混合而成,耐磨剂为硅灰。
42.高强度抗裂混凝土的制备方法为:
43.s1、将改性剂、耐磨剂和水倒入搅拌机中进行搅拌,搅拌速度为230r/min,搅拌8min后,制得添加剂;
44.s2、将水泥、粗骨料、细骨料倒入添加剂中,进行搅拌,搅拌速度为130r/min,搅拌15min后,制得混合物;
45.s3、倒出混合物,并进行装模、养护,制得混凝土。
46.实施例4
47.实施例4与实施例3的不同之处在于,硅酸钠、硅烷、聚乙烯醇质量比为2.5:6.5:1。
48.实施例5
49.实施例5与实施例3的不同之处在于,硅酸钠、硅烷、聚乙烯醇质量比为4:6.5:1。
50.实施例6
51.实施例6与实施例3的不同之处在于,硅酸钠、硅烷、聚乙烯醇质量比为3.3:5:1。
52.实施例7
53.实施例7与实施例3的不同之处在于,硅酸钠、硅烷、聚乙烯醇质量比为3.3:8:1。
54.对比例1
55.实施例1与实施例3的不同之处在于,硅酸钠、硅烷、聚乙烯醇质量比为0:6.5:1。
56.对比例2
57.实施例2与实施例3的不同之处在于,硅酸钠、硅烷、聚乙烯醇质量比为3.3:0:1。
58.对比例3
59.对比例3与实施例3的不同之处在于,硅酸钠、硅烷、聚乙烯醇质量比为3.3:6.5:0。
60.性能检测试验
61.对由实施例1-7以及对比例1-3制得的混凝土进行取样,并对样品进行以下性能检
测试验。
62.1、混凝土的强度检测试验
63.根据国家标准gb/t5081-2002,对7天、28天后样品的抗压强度进行检测,抗压强度越大、抗压能力越强,说明混凝土的强度越高,将检测结果记录在表1。
64.2、混凝土的渗水性检测试验
65.根据国家标准cjj135-2009,对样品的渗水系数进行检测,渗水系数越大,抗冻性能越差,混凝土越容易开裂,将检测结果记录在表1。
66.表1
[0067][0068]
检测数据分析
[0069]
从表1可以看出,实施例1-7所制备的混凝土的7天的抗压强度为31.1-32.7mpa,28天的抗压强度为56.1-57.4mpa,从而可以看出本技术制备的混凝土具有较高的强度。
[0070]
从表1可以看出,实施例1-7所制备的混凝土的渗水系数为5.1-5.9mm/s,从而可以看出本技术制备的混凝土渗水系数较低,抗冻性较好,具有较好的防开裂性。
[0071]
从表1可知,实施例3和实施例4的区别在于硅酸钠、硅烷、聚乙烯醇质量比,当实施例4将硅酸钠、硅烷、聚乙烯醇的质量比调整至2.5:6.5:1时,实施例4所制备的混凝土在7天的抗压强度由32.7mpa降低至31.3mpa,15天的抗压强度由57.4mpa降低至56.1mpa,抗压强度降低,这是由于改性剂中硅酸钠的含量变少,导致骨料表面的空隙和微小裂缝无法得到较好的填充,最终使得实施例4所制备的混凝土的强度降低;实施例4所制备的混凝土的渗水系数由5.1mm/s升高至5.8mm/s,渗水系数升高,抗冻性能降低,混凝土易开裂。
[0072]
从表1可知,实施例3和实施例5的区别在于硅酸钠、硅烷、聚乙烯醇质量比,当实施例5将硅酸钠、硅烷、聚乙烯醇的质量比调整至4:6.5:1时,实施例5所制备的混凝土在7天的抗压强度由32.7mpa降低至31.2mpa,15天的抗压强度由57.4mpa降低至56.3mpa,抗压强度降低,这是由于改性剂中硅酸钠的含量变多,硅烷、聚乙烯醇的含量变少,导致憎水膜的完整性降低,最终使得实施例5所制备的混凝土的强度降低;实施例5所制备的混凝土的渗水系数由5.1mm/s升高至5.7mm/s,渗水系数升高,抗冻性能降低,混凝土易开裂。
[0073]
从表1可知,实施例3和实施例6的区别在于硅酸钠、硅烷、聚乙烯醇质量比,当实施例6将硅酸钠、硅烷、聚乙烯醇的质量比调整至3.3:5:1时,实施例6所制备的混凝土在7天的抗压强度由32.7mpa降低至31.4mpa,15天的抗压强度由57.4mpa降低至56.2mpa,抗压强度降低,这是由于改性剂中硅烷的含量变少,导致憎水膜的完整性降低,最终使得实施例6所制备的混凝土的强度降低;实施例6所制备的混凝土的渗水系数由5.1mm/s升高至5.9mm/s,渗水系数升高,抗冻性能降低,混凝土易开裂。
[0074]
从表1可知,实施例3和实施例7的区别在于硅酸钠、硅烷、聚乙烯醇质量比,当实施例7将硅酸钠、硅烷、聚乙烯醇的质量比调整至3.3:8:1时,实施例7所制备的混凝土在7天的抗压强度由32.7mpa降低至31.1mpa,15天的抗压强度由57.4mpa降低至56.4mpa,抗压强度降低,这是由于改性剂中硅烷的含量变多,硅酸钠、聚乙烯醇的含量变少,导致骨料表面的空隙和微小裂缝无法得到较好的填充,最终使得实施例7所制备的混凝土的强度降低;实施例7所制备的混凝土的渗水系数由5.1mm/s升高至5.7mm/s,渗水系数升高,抗冻性能降低,混凝土易开裂。
[0075]
由表1可知,对比例1与实施例3的区别仅在于改性剂中未添加硅酸钠的情况下,对比例1所制备的混凝土在7天的抗压强度由32.7mpa降低至25.4mpa,15天的抗压强度由57.4mpa降低至41.4mpa,抗压强度明显降低,这是由于改性剂中缺少硅酸钠,导致骨料表面的空隙和微小裂缝无法得到填充,最终使得对比例1所制备的混凝土的强度明显降低;对比例1所制备的混凝土的渗水系数由5.1mm/s升高至6.6mm/s,渗水系数明显升高,抗冻性能明显降低,混凝土极易开裂。
[0076]
由表1可知,对比例2与实施例3的区别仅在于改性剂中未添加硅烷的情况下,对比例2所制备的混凝土在7天的抗压强度由32.7mpa降低至25.6mpa,15天的抗压强度由57.4mpa降低至41.7mpa,抗压强度明显降低,吸水率明显升高,这是由于改性剂中缺少硅烷,导致原料表面的凹面结构无法得到改善,最终使得对比例2所制备的混凝土的强度明显降低;对比例2所制备的混凝土的渗水系数由5.1mm/s升高至6.5mm/s,渗水系数明显升高,抗冻性能明显降低,混凝土极易开裂。
[0077]
由表1可知,对比例3与实施例3的区别仅在于改性剂中未添加聚乙烯醇的情况下,对比例3所制备的混凝土在7天的抗压强度由32.7mpa降低至26.2mpa,15天的抗压强度由57.4mpa降低至42.3mpa,抗压强度明显降低,吸水率明显升高,这是由于改性剂中缺少聚乙烯醇,不仅导致骨料与凝胶之间的粘结力无法得到加强,而且憎水膜与其他材料之间的结合紧密度也无法得到加强,最终使得对比例3所制备的混凝土的强度明显降低;对比例3所制备的混凝土的渗水系数由5.1mm/s升高至6.1mm/s,渗水系数明显升高,抗冻性能明显降低,混凝土极易开裂。
[0078]
以上均为本技术的较佳实施例,并非依此限制本技术的保护范围,故:凡依本技术
的结构、形状、原理所做的等效变化,均应涵盖于本技术的保护范围之内。
再多了解一些
本文用于企业家、创业者技术爱好者查询,结果仅供参考。