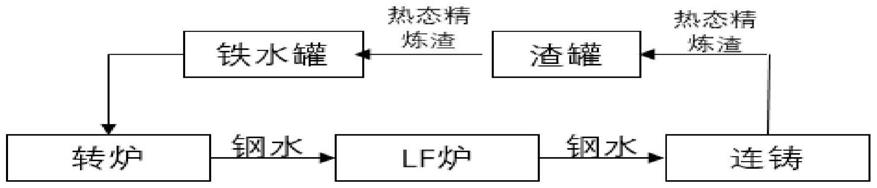
1.本发明涉及一种炼钢工艺技术,特别是一种热态精炼渣重复利用的工艺。
背景技术:
2.钢水在连铸浇铸结束后,钢包内的精炼渣是不可避免的。现有技术中,关于连铸钢包铸余精炼渣分为两部分处理,在钢水跨一部分倒入渣罐,见钢流后停止倒渣,将剩余部分精炼渣连带钢水全部折入精炼钢包内重复利用。其中倒入渣罐部分,转运至渣处理工序,经处理后生产水泥。
3.虽然后续渣处理实现了精炼渣成分的再利用,但是:
①
渣处理工序需要热闷、盘泼、滚筒、风碎等多种手段,所需工艺的设备资金投入也较大;
②
渣处理工序需要将1600℃左右高温的液态钢渣冷却至250℃左右,而冷却多为水介质,水资源消耗大,而液态钢渣中的热量造成了事实上的浪费。
4.近年来,也有技术在探讨应用钢渣内部循环利用,这样可以不仅有利于节能降耗和温室气体减排,提高转炉渣内循环利用比例、有效回收转炉渣中的fe等有价值组分。但是钢渣内部循环的难点在于:
①
连铸钢包铸余精炼渣在渣罐中有凝固结壳现象,在倒渣过程中有渣壳冲破,大量炉渣涌出会烧损铁水车及其附属设备;
②
部分精炼渣因脱氧不完全,在折铁过程中,发生c feo=fe co反应,有折铁过程中冒渣的风险。基于以上原因,目前能够进入内循环利用的仅仅为与钢水混合那一小部分精炼渣,倒入渣罐的铸余精炼渣还是无法进入内循环。
5.此外,转炉提高废钢量,有助于降低铁水消耗,将大幅降低环境污染和综合能耗,具有较高的经济、环保和社会效益。但是提高废钢量后,转炉热量明显不足,需要补加提温剂和降低辅料消耗满足生产所需要的的热量。转炉辅料降低后,导致转炉渣量降低,同时吹炼前期熔池温度较低,影响前期石灰熔化,不利于吹炼前期化渣,影响转炉脱磷效率,吹炼终点磷高炉次增多。
技术实现要素:
6.本发明的技术任务是针对以上现有技术的不足,提供一种热态精炼渣在转炉冶炼过程中重复利用的工艺,来解决精炼渣带来的渣处理成本以及精炼渣对环境的污染的问题,以及解决精炼渣中带的金属损失和热量损失,降低炼钢成本高。
7.本发明解决其技术问题的技术方案是:一种热态精炼渣在转炉冶炼过程中重复利用的工艺,其特征在于:包括以下步骤:
8.s1、lf炉所得钢水进入连铸工序,所产生的热态连铸钢包铸余精炼渣分为两部分处理,在钢水跨一部分倒入渣罐,见钢流后停止倒渣,将剩余部分精炼渣连带钢水全部折入精炼钢包内重复利用;其中,每次铸余精炼渣进入渣罐后,即向渣罐中投入铝粒;在连铸铸余渣全部倒完后,向渣罐内加入100-150kg低碳钢包覆盖剂;
9.s2、将渣罐运至加料跨,将渣罐中的热态铸余渣倒入满罐的铁水罐中;
10.s3、将铁水罐中的铁水兑入转炉中;
11.s4、转炉中所得钢水进入lf炉精炼。
12.进一步的,对于低碳低硅铝镇静钢,精炼造渣选用cao-al2o3渣系。
13.进一步的,上述的渣中cao含量50-60%,al2o3含量为28-33%。
14.进一步的,在步骤s2中,通过过跨车道将渣罐运至加料跨。
15.进一步的,在步骤s3中,每罐铁水倒入热态铸余渣3-5吨。
16.进一步的,在步骤s3中,控制使用炉数。
17.进一步的,在步骤s3中,控制使用炉数具体为:使用铸余渣在同一组转炉连续使用三炉,然后转为正常生产两炉后,方可继续使用铸余渣。
18.进一步的,使用精炼铸余渣的炉次,每炉少加入石灰500-1000kg。
19.与现有技术相比较,本发明具有以下突出的有益效果:
20.1、本发明方法通过对热态炉渣进行渣罐内改质,以克服现有技术中渣罐内铸余精炼渣无法进入内循环的缺陷,实现钢渣内部循环利用,减少石灰、萤石等造渣材料的用量,提高成渣速度,减少耐材侵蚀,降低电耗,同时可以实现浇注后钢包余钢回收利用,提高金属收得率;
21.2、本方法可以解决因大废钢比,转炉脱磷率低的问题,在保证废钢比不变的情况下,提高脱磷率5%-7%,并且在保证脱磷效果的情况下,吨钢降低石灰消耗3-5kg;
22.3、本方法对连铸铸余渣进行热态回收,降低转炉钢铁料消耗;
23.4、本方法适用于所有使用转炉,适用面广,推广价值高。
附图说明
24.图1是本发明的转炉渣内循环示意图。
具体实施方式
25.下面结合说明书附图和具体实施方式对本发明进一步说明。
26.本发明为一种热态精炼渣在转炉冶炼过程中重复利用的工艺,充分利用精炼渣的物理热,减少因加入冷态精炼渣对转炉吹炼前期的温度影响。
27.lf炉精炼渣热态在转炉冶炼过程中利用如图1所示,包括:
28.s1.lf炉所得钢水进入连铸工序,所产生的热态连铸钢包铸余精炼渣分为两部分处理,在钢水跨一部分倒入渣罐,见钢流后停止倒渣,将剩余部分精炼渣连带钢水全部折入精炼钢包内重复利用。
29.在本步骤中,对于低碳低硅铝镇静钢,为保证lf精炼炉渣具备脱硫及吸附夹杂,同时避免钢水回硅,精炼造渣选用cao-al2o3渣系。lf精炼炉渣中cao含量50-60%,al2o3含量为28-33%,al2o3可以与cao形成低熔点化合物,可以作为助溶剂用于转炉炼钢过程。
30.下表为各实施例精炼炉渣成分:
31.内部钢种caosio2feoal2o3mgocao/sio2(r)h0130158.43.30.630.05.517.7h0130157.63.81.629.44.915.2h0130158.13.61.029.05.816.0
h0130156.62.51.134.45.822.3h0130160.02.60.730.35.122.9h0130157.53.22.030.65.117.8
32.以下渣罐投放量按照每个渣罐贮存精炼渣25-30吨为基准,每个渣罐可以接6-7次铸余精炼渣,也即每次铸余精炼渣量为4~5吨。
33.在连铸铸余渣倒完后,向渣罐内加入100-150kg低碳钢包覆盖剂,解决渣罐表面结壳问题,防止之后在倒渣过程中存在渣壳冲破,大量炉渣涌出烧损铁水车及其附属设备。
34.如遇到生产脱氧不完全钢种,例如bof-rh-cc生产工艺的钢种,其所得精炼渣因脱氧不完全,在折铁过程中,发生c feo=fe co反应,有折铁过程中冒渣的风险。每次铸余精炼渣进入渣罐后,即向渣罐中投入铝粒,进行精炼渣脱氧。每个渣罐总量在30-50kg。
35.对于转炉废钢加入种类为重型废钢的,因前期吹炼温度低,增加废钢熔化难度。因此,每次铸余精炼渣进入渣罐后,即向渣罐中投入400-500kg石灰粉,每个渣罐石灰粉投入总量控制在2-3吨,提高精炼渣碱度,在转炉吹炼前期减少石灰加入量,提高吹炼前提温度。
36.对于高炉出铁过程中向铁水罐中加入废钢的,加入铁水罐中的废钢熔化后,导致铁水硅低、温度低,铁水温度普遍为1230-1260℃,对转炉生产过程中废钢熔化不利。部分炉次需要向炉内增加硅铁进行升温,但是硅铁在吹炼过程中加入,容易导致转炉吹炼喷溅,不利于吹炼操作过程控制。如果向铁水中投入含硅量75%的硅铁,硅铁熔点为1300-1330℃,加入的硅铁回收率只有60%-80%左右,不能及时熔化的硅铁容易造成粘罐,或者硅铁漂浮在铁流上增加烧损度。这种情况下,需要在渣罐内加入含硅量75%的硅铁,加入量以每次铸余精炼渣加200-300kg为宜。连铸浇至后期钢包内钢水温度>1560℃,高温的连铸铸余精炼渣有利于硅铁熔化。液态硅溶于液态炉渣中,当硅浓度为1%时,其标准自由能为:si(l)=[si]
△
gsiθ=-131500-17.61t,可见硅的溶解始终是放热反应,它能够弥补增硅过程中硅铁熔化吸热和散热损失,同时能够弥补加入石灰粉的温降。通过增加精炼渣中的硅含量,这部分精炼渣折入铁水罐中,能够增加铁水中的硅含量,提高硅铁的回收率。
[0037]
s2.通过过跨车道将渣罐运至加料跨,将渣罐中的热态铸余渣倒入满罐的铁水罐中。
[0038]
在本步骤中,每罐铁水倒入热态铸余渣3-5吨。本实施例中的铁水罐规格为300吨。
[0039]
s3.将铁水罐中的铁水兑入转炉中。
[0040]
热态精炼渣随着铁水倒入转炉内,可以促进化渣,提高转炉脱磷率,还可以降低辅料消耗。可以解决因大废钢比导致转炉吹炼前提温度低,加入冷态精炼渣影响前期废钢熔化的问题。
[0041]
精炼渣中含有30%左右的al2o3,这部分al2o3能够降低炉渣熔点有利于化渣,但因为炉渣变性,低熔点和低粘度的炉渣在熔池中搅拌,对转炉炉衬侵蚀较为严重。因此,需要合理控制使用炉数,使用铸余渣在同一组转炉连续使用三炉,然后转为正常生产两炉后,方可继续使用铸余渣,保证转炉炉衬侵蚀受控。
[0042]
使用精炼铸余渣炉次,每炉少加入石灰500-1000kg。本实施例中的转炉规格为300吨。
[0043]
s4.转炉中所得钢水进入lf炉精炼。
[0044]
本发明方法通过对热态炉渣进行渣罐内改质,以克服现有技术中渣罐内铸余精炼
渣无法进入内循环的缺陷,实现钢渣内部循环利用,减少石灰、萤石等造渣材料的用量,提高成渣速度,减少耐材侵蚀,降低电耗,同时可以实现浇注后钢包余钢回收利用,提高金属收得率;还可以解决因大废钢比,转炉脱磷率低的问题,在保证废钢比不变的情况下,提高脱磷率5%-7%,并且在保证脱磷效果的情况下,吨钢降低石灰消耗3-5kg。对连铸铸余渣进行热态回收,降低转炉钢铁料消耗。
[0045]
本方法适用于所有使用转炉,适用面广,推广价值高。
[0046]
需要说明的是,本发明的特定实施方案已经对本发明进行了详细描述,对于本领域的技术人员来说,在不背离本发明的精神和范围的情况下对它进行的各种显而易见的改变都在本发明的保护范围之内。
再多了解一些
本文用于企业家、创业者技术爱好者查询,结果仅供参考。