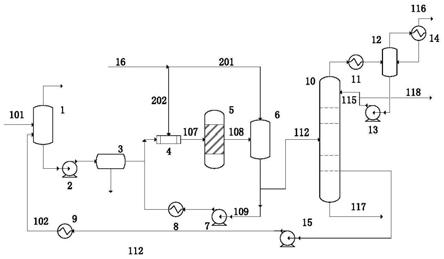
1.本发明涉及石油化工领域,更具体地,涉及一种丁二烯抽提尾气选择加氢装置及选择加氢方法。
背景技术:
2.目前丁二烯抽提装置一般通过两段萃取精馏和普通精馏的方法从乙烯装置裂解碳四馏分中回收1,3-丁二烯,同时副产一股富含炔烃及二烯烃的尾气。因丁二烯抽提装置采用的工艺技术不同,副产的炔烃尾气有液相和气相两种状态,但共同特点为尾气中乙烯基乙炔(va)、乙基乙炔(ea)浓度较高,其中va最高可超过40wt%。目前,为确保安全性,这股富含炔烃及二烯烃的尾气还需要采用碳四抽余液稀释,随后作为液化气销售,或直接排放火炬燃烧。若将这股尾气进行回收及利用,将会创造很好的经济效益和社会效益。
3.目前,针对这股富含炔烃及二烯烃的碳四资源,工业上主要还是通过加氢精制的办法将其转化为高附加值的产品,其中一种方法即是选择加氢精制。虽然不饱和烃类的加氢活性随着其不饱和程度的增加,碳四中的炔烃优先于二烯烃及单烯烃与氢气发生反应,但在催化剂的作用下,碳四组分中的二烯烃与单烯烃也可以在较低温度下与氢气发生激烈反应生成烷烃。碳四选择加氢反应是气、液、固三相反应,但由于反应所需氢气量小,氢气受限溶解于碳四,再与碳四中的反应物如炔烃及二烯烃等通过质量传递穿过液膜到达催化剂表面进行反应。发明人研究发现:加氢反应受到氢气限制,在催化剂表面,氢气不足的地方,炔烃无法发生加氢反应,导致产品中无法脱除干净,且容易发生聚合反应生成重组分降低催化剂性能;氢气过量的地方导致炔烃加氢反应生成的二烯烃和丁烯进一步发生加氢反应生成烯烃和烷烃,导致炔烃加氢反应选择性降低。
4.近年来,碳四选择加氢催化剂研究工作较多,且催化剂的活性及选择性均得到了较大提高。但正如上文所述,氢气的非精确控制及分布不均匀严重限制了催化剂选择性的发挥,导致选择加氢反应很难同时满足炔烃及二烯烃转化率高和单烯烃收率高的要求。实际工业装置相比于实验室的小试装置,生产规模增加百倍,氢气的精确控制更困难,分布更不均匀,针对工业装置的特点,从工艺及控制方面对选择加氢反应条件进行改进显得更有必要。
5.cn102285859a公开了一种碳四物流选择加氢方法,采用以氧化铝作为载体的钯银双组份或钯银多组分催化剂,将高丁二烯含量高的碳四物流选择加氢得到富含1-丁烯的产品,产品中丁二烯和炔烃含量低于10ppm,可作为mtbe装置的原料。该专利并未涉及富含乙烯基乙炔(va)及乙基乙炔(ea)的丁二烯尾气,且是将炔烃及二烯烃选择加氢,目标产品为1-丁烯。
6.cn103121905a公开了一种丁二烯抽提尾气的回收方法,采用镍钯铜银多金属催化剂,将炔烃选择加氢得到富含丁二烯的产品,送入丁二烯装置进一步回收丁二烯。该方法氢气是通过在反应器入口直接配入,分布容易受到设备及管道布置影响,很难确保氢气分布均匀,进而限制催化剂选择性的发挥,且用于稀释原料的加氢碳四未脱除选择加氢反应产
生的多聚物等重组分,容易在系统内累积从而导致催化剂的性能及寿命降低。
7.cn108863697a公布了一种炔烃选择加氢回收丁二烯的方法,采用钯-钼系选择加氢催化剂,碳四物流中的炔烃经加氢后乙烯基乙炔含量低于1.0wt%,丁二烯选择性高于46%,产品满足丁二烯抽提装置进料要求。但该专利采用含有贵金属的钯催化剂,成本较高,且并未涉及丁二烯尾气选择加氢装置的工艺流程。
技术实现要素:
8.本发明的目的是为解决现有技术存在的缺陷,提供一种丁二烯抽提尾气的选择加氢装置及加氢方法。通过改进选择加氢反应所需氢气的配入及计量方法,在确保氢气得到精确计量的同时促进选择加氢反应中的均匀分布,提高选择加氢反应选择性,减少副反应的发生,延长催化剂的使用寿命。
9.为了实现上述目的,本发明的一方面提供一种丁二烯抽提尾气选择加氢装置,其特征在于,该装置包括:原料罐、进料泵、聚结器、混合器、加氢反应器、反应器出口缓冲罐、循环碳四冷却器、稳定塔及氢气进料管线;
10.所述原料罐、进料泵、聚结器、混合器、加氢反应器和反应器出口缓冲罐依次连通;
11.所述反应器出口缓冲罐出口管线分为两路,第一路与循环碳四冷却器、混合器和加氢反应器依次连通;第二路与所述稳定塔连通;
12.氢气进料管线至少分为第一股和任选的第二股,第一股与所述反应器出口缓冲罐连通,第二股与所述混合器连通。
13.本发明的另一方面提供一种丁二烯抽提尾气的选择加氢方法,利用上述丁二烯抽提尾气选择加氢装置,该选择加氢方法包括:
14.(1)自丁二烯抽提装置来的含炔烃尾气进入原料罐;
15.(2)原料罐内的原料经进料泵增压至反应所需压力后与来自反应器出口缓冲罐的循环碳四汇合后进入混合器,在混合器中与氢气混合后进入加氢反应器进行加氢反应,反应得到的反应物流进入反应器出口缓冲罐;
16.所述加氢反应器反应所需氢气通过第一加入方式或第二加入方式配入;
17.所述第一加入方式为:反应所需的全部氢气通过所述反应器出口缓冲罐进入,然后通过所述反应器出口缓冲罐出口的第一路进入所述加氢反应器;
18.所述第二加入方式为:反应所需的部分氢气通过所述反应器出口缓冲罐进入,然后通过所述反应器出口缓冲罐出口的第一路进入所述加氢反应器;另一部分氢气通过混合器进入,然后进入所述加氢反应器;
19.(3)所述反应器出口缓冲罐无气相排放,液相产品分为两股,第一股作为所述循环碳四返回加氢反应器,第二股作为稳定塔进料;
20.(4)加氢反应器反应得到的反应物流通过反应器出口缓冲罐进入稳定塔,经稳定塔分离后采出碳四加氢产品。
21.本发明的技术方案具有如下有益效果:
22.(1)采用本发明所述的装置及方法,能够对丁二烯尾气(自丁二烯抽提装置来的含炔烃尾气)充分回收利用,并通过优化选择加氢工艺氢气配入方式,提高丁二烯尾气选择加氢反应1,3-丁二烯的选择性。
23.(2)本发明通过优化原料的稀释方式,采用1,3-丁二烯、丁烯-1及重组分含量低的碳四加氢产品稀释原料,既解决了原料罐高炔烃浓度的问题,同时降低稀释碳四返混导致的1,3-丁二烯及丁烯-1再次加氢的几率,还进一步延长了催化剂的使用寿命;有效减少1,3-丁二烯的损失,同时延长催化剂使用寿命。
24.(3)本发明采用不含贵金属的催化剂,能够有效降低装置投资及运行成本。
25.本发明的其它特征和优点将在随后具体实施方式部分予以详细说明。
附图说明
26.通过结合附图对本发明示例性实施方式进行更详细的描述。
27.图1示出了根据本发明的一个实施例的丁二烯抽提尾气选择加氢装置示意图。
28.设备标记说明:
29.1原料罐;2进料泵;3聚结器;4混合器;5加氢反应器;6反应器出口缓冲罐;7循环泵;8循环碳四冷却器;9稀释碳四冷却器;10稳定塔;11塔顶冷凝器;12回流罐;13回流泵;14尾气冷凝器;15稀释碳四泵;16氢气进料管线;
30.物流标记说明:
31.101自丁二烯抽提装置来的含炔烃尾气(丁二烯尾气);102稀释碳四;107加氢反应器原料;108加氢反应器产品;109循环碳四;112稳定塔进料;115稳定塔回流;116不凝气;117重组分;118碳四加氢产品;201反应补压氢气;202反应补充氢气。
具体实施方式
32.下面将更详细地描述本发明的优选实施方式。虽然以下描述了本发明的优选实施方式,然而应该理解,可以以各种形式实现本发明而不应被这里阐述的实施方式所限制。
33.本发明的一方面提供一种丁二烯抽提尾气选择加氢装置,该装置包括:原料罐、进料泵、聚结器、混合器、加氢反应器、反应器出口缓冲罐、循环碳四冷却器、稳定塔及氢气进料管线;
34.所述原料罐、进料泵、聚结器、混合器、加氢反应器和反应器出口缓冲罐依次连通;
35.所述反应器出口缓冲罐出口管线分为两路,第一路与循环碳四冷却器、混合器和加氢反应器依次连通;第二路与所述稳定塔连通;
36.氢气进料管线至少分为第一股和任选的第二股,第一股与所述反应器出口缓冲罐连通,第二股与所述混合器连通。
37.本发明中,原料罐设置有丁二烯抽提尾气及稀释碳四的接口。
38.根据本发明,优选地,所述稳定塔的一出口与所述原料罐的稀释碳四接口连通。
39.根据本发明,优选地,所述稳定塔的一出口、稀释碳四泵、稀释碳四冷却器和所述原料罐的稀释碳四接口依次连通。
40.根据本发明,优选地,所述反应器出口缓冲罐出口管线的第一路经循环泵与所述循环碳四冷却器连通。
41.根据本发明,优选地,所述稳定塔的顶部出口依次连接有塔顶冷凝器和回流罐;
42.所述回流罐一出口与尾气冷凝器连通,所述尾气冷凝器的一出口与所述回流罐一入口连通;
43.所述回流罐的另一出口经回流泵与所述稳定塔一入口连通。
44.根据本发明,优选地,所述加氢反应器为固定床反应器。
45.本发明的第二方面提供一种丁二烯抽提尾气的选择加氢方法,利用上述丁二烯抽提尾气选择加氢装置,该选择加氢方法包括:
46.(1)自丁二烯抽提装置来的含炔烃尾气进入原料罐;
47.(2)原料罐内的原料经进料泵增压至反应所需压力后与来自反应器出口缓冲罐的循环碳四汇合后进入混合器,在混合器中与氢气混合后进入加氢反应器进行加氢反应,反应得到的反应物流进入反应器出口缓冲罐;
48.所述加氢反应器反应所需氢气通过第一加入方式或第二加入方式配入;
49.所述第一加入方式为:反应所需的全部氢气通过所述反应器出口缓冲罐进入,然后通过所述反应器出口缓冲罐出口的第一路进入所述加氢反应器;
50.所述第二加入方式为:反应所需的部分氢气通过所述反应器出口缓冲罐进入,然后通过所述反应器出口缓冲罐出口的第一路进入所述加氢反应器;另一部分氢气通过混合器进入,然后进入所述加氢反应器;
51.(3)所述反应器出口缓冲罐无气相排放,液相产品分为两股,第一股作为所述循环碳四返回加氢反应器,第二股作为稳定塔进料;
52.(4)加氢反应器反应得到的反应物流通过反应器出口缓冲罐进入稳定塔,经稳定塔分离后采出碳四加氢产品。
53.本发明中,经稳定塔分离后塔顶回流罐采出碳四加氢产品,所述碳四加氢产品包括1,3-丁二烯和丁烯-1。
54.根据本发明,优选地,步骤(1)中,原料罐中的含炔烃尾气采用来自稳定塔的侧线稀释碳四进行稀释;
55.优选地,稀释碳四与含炔烃尾气的质量流量比为1~30:1。
56.本发明中,步骤(2)中,所述原料罐内的原料优选为经稀释后的原料。
57.本发明中,稳定塔的侧线稀释碳四主要包括低含量的1,3-丁二烯、丁烯-1及容易对催化剂活性和寿命产生不利影响的重组分。
58.根据本发明,优选地,步骤(2)中,所述第二加入方式中,所述反应所需的部分氢气与加氢反应所需氢气的质量比不小于0.3,优选不小于0.5,所述加氢反应所需氢气为反应所需的部分氢气与另一部分氢气之和。
59.本发明中,第二加入方式中,反应所需的部分氢气和另一部分氢气的计量之和等于加氢反应所需的全部氢气的计量。
60.本发明中,第一加入方式中,加氢反应器所需氢气通过补压控制反应系统压力,全部氢气通过溶解的方式进入到液相碳四中,随反应器循环碳四进入加氢反应器;第二加入方式中,反应所需部分氢气通过反应器出口缓冲罐配入,这部分氢气通过补压控制反应系统压力,同时通过溶解的方式进入到液相碳四中,随反应器循环碳四进入加氢反应器。
61.根据本发明,优选地,步骤(1)中,所述原料罐的操作压力为0.5~1.0mpag;
62.步骤(2)中,经稀释后的原料由进料泵增压至1.0~4.0mpag,循环碳四与稀释后碳四原料的质量流量比为5~30:1;
63.加氢反应器的入口温度各自独立地为5~60℃,液体空速为1~40h-1
;加氢反应器
的压力由反应器出口缓冲罐补压氢气控制,反应的压力为1.0~4.0mpag;
64.步骤(4)中,所述稳定塔的操作压力为0.4~1.0mpag,理论板数为10~40,侧线采出理论板位置为5~35。
65.本发明中,步骤(4)中,稳定塔的侧线采出相态为液相。
66.本发明中,稳定塔塔顶采用两级冷凝器回收不凝气中夹带的碳四组分;塔顶回流罐液相采出1,3-丁二烯及丁烯-1含量高的加氢产品;从塔釜脱除重组分;从侧线得到含量低的1,3-丁二烯、丁烯-1及容易对催化剂活性和寿命产生不利影响的重组分的碳四加氢产品,用于稀释原料。
67.本发明中,选择加氢反应可选用公知技术中的选择加氢催化剂cn102886262、cn10886397和/或cn104707622等,优选cn104707622公开的选择加氢催化剂,以催化剂的总重量计,优选催化剂包括以下组分:含量为5~15%wt的铜,0.1~3%wt的依,0.1~3%wt的磷,含量为0.5~3.0%wt且选自镍、锆、铅及锡中的一种或多种助剂金属,余量为载体,所述载体选自氧化铝、氧化钛、氧化硅、氧化钛-氧化铝复合氧化物、氧化钛-氧化硅复合氧化物和氧化铝-氧化硅复合氧化物中的至少一种载体。
68.本发明中,液相丁二烯尾气经稀释升压后,采用不含贵金属的催化剂进行选择加氢反应,并经稳定塔脱除轻重组分得到炔烃含量低,富含1,3-丁二烯的碳四烯烃产品,可返回丁二烯抽提装置进一步回收1,3-丁二烯及单烯烃。
69.以下通过实施例进一步说明本发明:
70.以下各实施例所用催化剂为:以催化剂的总重量计,催化剂由以下组分组成:含量为7wt%的铜,含量为0.3wt%的依,含量为2wt%的磷,含量为3wt%的镍,余量为载体,所述载体氧化钛-氧化铝复合氧化物。
71.实施例1
72.如图1所示,本实施例提供一种丁二烯抽提尾气选择加氢装置,该装置包括:原料罐1、进料泵2、聚结器3、混合器4、加氢反应器5、反应器出口缓冲罐6、循环泵7、循环碳四冷却器8、稀释碳四冷却器9、稳定塔10、塔顶冷凝器11、回流罐12、回流泵13,尾气冷凝器14,稀释碳四泵15及氢气进料管线16;
73.其中,原料罐1设置有丁二烯抽提尾气及稀释碳四的接口,所述原料罐1底部、进料泵2、聚结器3、混合器4、加氢反应器5和反应器出口缓冲罐6依次连通;
74.所述反应器出口缓冲罐6出口管线分为两路,第一路与循环碳四冷却器8、混合器4和加氢反应器5依次连通;第二路与所述稳定塔10连通;其中,所述反应器出口缓冲罐6出口管线的第一路经循环泵7与所述循环碳四冷却器8连通;
75.氢气进料管线16至少分为第一股和任选的第二股,第一股与所述反应器出口缓冲罐6顶部入口连通,第二股与所述混合器4连通;
76.其中,所述稳定塔10的一出口、稀释碳四泵15、稀释碳四冷却器9和所述原料罐1的稀释碳四接口依次连通;所述稳定塔10的顶部出口依次连接有塔顶冷凝器11和回流罐12;所述回流罐12一出口与尾气冷凝器14连通,所述尾气冷凝器14的一出口与所述回流罐12一入口连通;所述回流罐12的另一出口和回流泵13连通,所述回流泵13出口与所述稳定塔10一入口连通。
77.其中,所述加氢反应器5为固定床反应器。
78.利用本实施例的丁二烯抽提尾气选择加氢装置进行丁二烯抽提尾气的选择加氢方法,该选择加氢方法包括:
79.(1)自丁二烯抽提装置来的含炔烃尾气101(以含炔烃尾气的总重量计,含炔烃尾气的主要组成:丁烯58.69%,丁二烯10.35%,乙基乙炔17.65%和乙烯基乙炔4.00%,碳五及以上2.05%,水0.02%)进入原料罐1,原料罐中的含炔烃尾气采用来自稳定塔10的侧线经冷却后的稀释碳四102进行稀释;其中,含炔烃尾气101的流量为1825kg/h,压力为0.8mpag;稀释碳四102流量为5000kg/h,稀释后原料罐1中液相乙烯基乙炔含量为5.32%,气相中乙烯基乙炔含量为4.75%。
80.(2)原料罐1内经稀释后的原料经进料泵增压至2.7mpag后与来自反应器出口缓冲罐6的循环碳四109汇合后进入混合器4,在混合器中与氢气混合后(即得到加氢反应器原料107)进入加氢反应器5进行加氢反应,反应得到的反应物流(加氢反应器产品108)进入反应器出口缓冲罐6;循环碳四109流量为45000kg/h,混合后的碳四进料流量为46825kg/h,温度为20℃。
81.所述加氢反应器5反应所需氢气通过第一加入方式配入;
82.所述第一加入方式为:反应所需的全部氢气通过所述反应器出口缓冲罐6进入,然后通过所述反应器出口缓冲罐6出口的第一路进入所述加氢反应器5;其中,加氢反应器5反应所需氢气通过补压控制反应系统压力,压力为2.3mpag,氢气通过溶解的方式进入到液相碳四中,随反应器循环碳四109进入加氢反应器,循环碳四109流量为45000kg/h,溶解于其中的氢气流量为34.0kg/h,加氢反应器5入口混合器4不再配入氢气,反应液相总空速为15h-1
;加氢反应器5的入口温度为20℃;
83.(3)所述反应器出口缓冲罐6无气相排放,液相产品分为两股,第一股作为所述循环碳四109返回加氢反应器,第二股作为稳定塔进料112;稳定塔进料112的流量为6853kg/h。
84.(4)加氢反应器5反应得到的反应物流(加氢反应器产品108)通过反应器出口缓冲罐6进入稳定塔10,经稳定塔10分离后采出碳四加氢产品118。其中,稳定塔10从塔顶脱除不凝气116,从塔釜脱除重组分117,从塔顶采出富含1,3-丁二烯及单烯烃的液相碳四加氢产品118,从侧线采出用于稀释原料的稀释碳四102,流量为5000kg/h。稳定塔10理论板数为30块,操作压力为0.5mpag,塔顶温度为56.7℃,塔釜温度为100.2℃,回流(稳定塔回流115)量为5600kg/h,侧线采出理论板位置为25。
85.各主要物流结果见表1。
86.表1
87.物流号101102108118201202相态液液液液气气温度[c]40.020.135.315.015.815.8压力[mpa(g)]0.800.652.300.502.402.40摩尔组成%%%%%%氢气0.000.000.000.1795.0095.00甲烷0.000.000.460.605.005.00丙烷0.000.000.000.000.000.00
丙烯0.010.000.000.010.000.00丙炔0.000.000.000.000.000.00正丁烷2.574.143.913.400.000.00异丁烷4.670.841.874.750.000.00丁烯-114.2011.3214.5723.100.000.00异丁烯22.059.3212.7222.570.000.00顺-2-丁烯18.7944.1337.3119.700.000.00反-2-丁烯3.6511.4810.478.060.000.001,3-丁二烯6.359.3010.7816.290.000.001,2-丁二烯4.005.063.930.910.000.00乙基乙炔4.000.310.260.120.000.00乙烯基乙炔17.630.760.640.310.000.00正戊烷1.803.212.820.000.000.00碳五 0.250.060.270.000.000.00水0.020.000.000.000.000.00摩尔流量[kmol/h]32.7888.561186.7931.0212.510.00质量流量[kg/h]1825.005000.00668251724.5034.000.00
[0088]
由表1可见,在产品中,1,3-丁二烯含量较原料提高约10个百分点,炔烃含量小于0.5%,炔烃总转化率大于97%,可满足丁二烯抽提装置的原料要求。
[0089]
实施例2
[0090]
如图1所示,本实施例与实施例1相比,有以下不同:
[0091]
步骤(2)中,加氢反应器5反应所需氢气通过第二加入方式配入;所述第二加入方式为:反应所需的部分氢气通过所述反应器出口缓冲罐6进入,然后通过所述反应器出口缓冲罐6出口的第一路进入所述加氢反应器5;另一部分氢气通过混合器4进入,然后进入所述加氢反应器5;其中,大部分氢气通过加氢反应器出口缓冲罐6配入,这部分氢气通过补压控制反应系统压力,同时通过溶解的方式进入到液相碳四中,随反应器循环碳四109进入反应器,循环碳四109流量为32000kg/h,溶解于其中的氢气流量为20.0kg/h;少部分氢气通过加氢反应器5入口设置的混合器4配入,流量为17.0kg/h。
[0092]
各主要物流结果见表2。
[0093]
表2
[0094]
物流号101102108118201202相态液液液液气气温度[c]402041.71515.815.8压力[mpa(g)]0.80.652.30.52.42.4摩尔组成%%%%%%氢气0000.189595甲烷000.500.5555丙烷000.000.0000丙烯0.0100.000.0100
丙炔000.000.0000正丁烷2.574.013.763.2200异丁烷4.670.861.884.7500丁烯-114.212.0615.3625.2000异丁烯22.059.5212.8422.5500顺-2-丁烯18.7944.7837.7819.6100反-2-丁烯3.6512.5511.408.65001,3-丁二烯6.358.7610.0714.12001,2-丁二烯44.063.160.7200乙基乙炔40.410.340.1300乙烯基乙炔17.630.960.800.3300正戊烷1.81.931.880.0000碳五 0.250.100.22000水0.0200000摩尔流量[kmol/h]32.7888.87695.130.757.366.26质量流量[kg/h]182550003884217102017
[0095]
由表2可见,在产品中,1,3-丁二烯含量较原料提高约7.8个百分点,炔烃含量小于0.5%,炔烃总转化率大于97%,可满足丁二烯抽提装置的原料要求。与实施例1相比,本实施例由于氢气未完全通过溶解的方式进入反应器,导致氢气分布的均匀性略差于实施例1,进而使得部分1,3-丁二烯发生加氢反应被消耗,导致产品中1,3-丁二烯含量较原料增加值降低。
[0096]
以上已经描述了本发明的各实施例,上述说明是示例性的,并非穷尽性的,并且也不限于所披露的各实施例。在不偏离所说明的各实施例的范围和精神的情况下,对于本技术领域的普通技术人员来说许多修改和变更都是显而易见的。
再多了解一些
本文用于企业家、创业者技术爱好者查询,结果仅供参考。