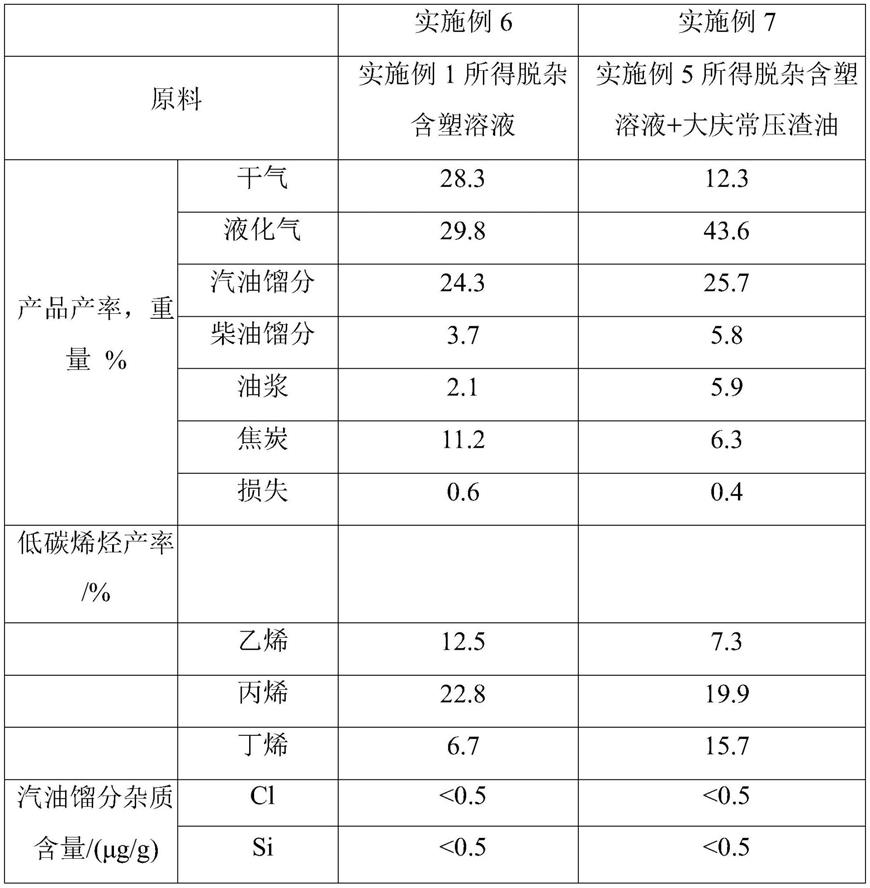
1.本发明涉及固体废塑料处理技术领域,具体涉及一种废塑料的催化裂解方法和系统。
背景技术:
2.塑料工业的发展给社会发展做出了巨大的贡献,目前我国的年塑料生产量已经高达1.2亿吨左右,其中绝大多数经过一次使用后即丢弃到环境中。据统计,我国的废塑料产量约为240~480万吨/年;到2035年全球约有80亿吨废塑料存在于自然环境中,由于塑料完全降解需要200~500年,因此废塑料的不断累积不仅造成了严重的环境污染,甚至影响了自然环境中的生态平衡。
3.现有的废塑料处理技术主要有填埋和焚烧两种方式,填埋除了占用大量土地外,极易造成二次污染,并不能从本质上解决问题;而目前国内有能够处理废塑料的垃圾焚烧发电厂仅约400个,如将所有废塑料采用垃圾焚烧发电的方式解决,预计仍需建设1000个以上,这明显是不可行的。此外,废塑料物理回收工艺成本高,经济价值低,企业获利不足且回收过程中易造成二次污染,均导致废旧塑料资源回收发展较慢。
4.现阶段,废塑料化学转化被认为是唯一能实现可持续发展的工艺。其中的热解工艺因其环保性、高收益率等优点被各国的研究人员和企业所关注。然而对混合废塑料而言,废塑料热解工艺的油收较低,且由于废塑料组成复杂,本身含有大量的杂原子;在塑料生产过程中也会添加大量有机或无机的各类添加剂以提高塑料性能;塑料在丢弃过程中易粘连大量的杂质等原因,现有的热解技术生产的热解油中存在杂质,特别是cl、si等杂质含量高等问题。cl元素极易导致废塑料热解油在后续加工过程中产生腐蚀,而si则易导致催化剂彻底失活,从而提高了生产成本,降低了热解工艺的附加值。有研究人员也开展了废塑料气化方面的研究,利用废塑料制备合成气,然后通过ft合成制备成其它产品,该路线的经济性有待考量。
5.废塑料中的主要种类,如pe、pp、ps等均为小分子烯烃聚合而成,特别是pe和pp其结构和组成与石蜡基原油具有相似性,如果能够将这部分废塑料通过处理再次变为单体,则可真正实现塑料的闭合循环,实现塑料制品的可持续发展。
技术实现要素:
6.本发明是为了解决现有废塑料热解工艺中油收率低、产品不达标、产品附加值较低,且热解油无法直接进行后加工等问题,提供一种废塑料的催化裂解方法和系统。
7.本发明的第一方面提供一种废塑料的催化裂解方法,包括以下步骤:
8.(1)废塑料进入废塑料预处理单元,与预处理剂、溶剂油接触进行预处理反应,预处理后物料经固液分离单元,分离为不溶物和脱杂含塑溶液,所述脱杂含塑溶液中氯含量为小于20μg/g、硅含量为小于3μg/g;所述预处理剂为腐殖土、赤泥、炼油装置废催化剂、高岭土、半焦、活性炭、气化灰渣中的一种或几种,以及任选的碱性氧化物;
9.(2)步骤(1)所得脱杂含塑溶液进入催化裂解单元,与催化裂解催化剂接触进行反应,反应流出物经分离后至少得到低碳烯烃产物,所述催化裂解催化剂为金属氧化物型催化裂解催化剂、沸石型催化裂解催化剂中的一种或多种。
10.在本发明中,所述废塑料为新鲜生活垃圾中废塑料、工农业生产中废塑料、陈化垃圾中废塑料中的一种或几种,可以是上述废塑料初步加工形成的废塑料棒、废塑料粒、废塑料片等中的一种或几种,优选无法物理回收再生的品质较差废塑料,废塑料的种类为pe、pp、ps、pvc中的一种或多种。
11.在本发明一个实施方式中,废塑料在进入废塑料预处理单元前进行清洗、干燥和破碎,破碎后的废塑料粒度为1~200mm,优选为1~50mm。
12.在本发明的一个实施方式中,在步骤(1)中,废塑料预处理单元的反应条件为:反应温度为250~410℃,压力为0.1~5mpa,废塑料的停留时间为10~60min。在优选的情况下,废塑料预处理单元的反应条件为:反应温度为280~390℃,压力为0.5~4.0mpa,废塑料的停留时间为15~45min。
13.在本发明一个实施方式中,溶剂油的馏程范围为80~550℃,溶剂油中总芳烃含量高于50质量%,单环芳烃含量高于20质量%;在优选的情况下,溶剂油中单环芳烃含量高于40质量%。溶剂油与废塑料的重量比例为1:10~10:1,在优选的情况下,溶剂油与废塑料的重量比例为1:1~7:1。
14.在本发明一个实施方式中,预处理剂的粒径范围为75~150μm;预处理剂与废塑料的重量比例为1:10~2:1,优选为1:7~1:5。
15.在本发明优选的一个实施方式中,所述预处理剂为废催化裂化催化剂、催化裂解单元废催化裂解催化剂、腐殖土、活性炭中的一种或几种,以及任选的碱性氧化物。
16.在本发明中,“任选的”含义是可选组分的意思。在本发明其中一个的实施方式中,预处理剂中除了其他组分外,还含有碱性氧化物。
17.本发明所述的腐殖土为垃圾填埋场挖掘出的废塑料夹带的由植物物质及各类有机垃圾腐烂后形成的混合物。
18.所述半焦为煤、生物质、废塑料等含碳物质在350~600℃条件下热解生成的固体产物。
19.所述气化灰渣为煤、半焦、焦炭、生物质、石油焦、废塑料等含碳物质在高于600℃、常压或加压条件下与气化剂反应后剩余的固体产物。
20.在本发明所述废塑料预处理单元中,将废塑料中氯杂质、硅杂质和金属杂质进行脱除,其中硅杂质是以塑料加工过程中添加的有机硅高分子的原始形态脱除,有效避免了硅杂质对后续加工单元催化剂的影响作用。通过降低废塑料中的氯含量,有效避免了氯杂质对后续加工装置的影响作用。
21.在本发明优选的一个实施方式中,所得脱杂含塑溶液中总金属含量小于5μg/g,氯含量小于10μg/g,硅含量小于2μg/g。
22.在本发明其中一个实施方式中,还包括步骤(3):
23.(3)步骤(1)所得不溶物进入抽提单元,与有机溶剂接触进行溶剂抽提,所得产物经分离后,得到固相物料和液相物料,固相物料在预处理剂回收单元经处理后,至少部分作为循环预处理剂返回步骤(1);液相物料在溶剂回收单元,进行析出处理和分离,得到固体
塑料颗粒和回收的有机溶剂。
24.在优选的情况下,有机溶剂选自苯、甲苯、三氯甲烷、环己酮、乙酸乙酯、乙酸丁酯、二硫化碳、四氢呋喃、汽油中的一种或几种。
25.在本发明中,抽提单元中设置溶剂抽提塔或静态混合抽提器中的一种或几种,抽提单元的具体操作条件与所选有机溶剂相匹配,抽提的目的是脱除外排固相物料上粘附的溶剂油,降低外排固体物料总量,最终达到减排的目的。
26.在本发明的一个实施方式中,预处理剂回收单元包括筛分、再生处理方式中的一种或几种。
27.在本发明的一个实施方式中,在溶剂回收单元中,所述析出处理选自反萃取、简单蒸馏、闪蒸、精馏中一种或几种方式。具体操作温度根据所选溶剂种类及配比灵活调控。
28.本发明对固液分离单元的具体形式没有限定,可以是各种形式的过滤器、离心机中的一种或多种。在本发明的一个实施方式中,所述固液分离单元设置加热及保温装置,加热装置是外热式或内热式的一种或几种,固液分离单元的操作温度为250~410℃。所述的固液分离单元为过滤器时,滤网孔径为0.1~1mm,优选为0.1~10μm。
29.在本发明步骤(2)中,固液分离单元所得脱杂含塑溶液进入催化裂解单元,与催化裂解催化剂接触进行反应,反应流出物经分离后得到低碳烯烃、催化裂解石脑油、催化裂解汽油、催化裂解柴油和催化裂解油浆。所述低碳烯烃包括丙烯、乙烯和丁烯,均是化学工业的基础原料,具有广泛的用途。
30.在本发明的一个实施方式中,催化裂解单元的进料包括任选的催化裂解原料,所述催化裂解原料为石油烃油和/或矿物油,所述石油烃油选自减压蜡油、焦化蜡油、脱沥青油、渣油、汽油和柴油中的至少一种,所述矿物油选自煤液化油、油砂和页岩油中的至少一种。
31.在本发明中,“任选的”含义是可选组分的意思,催化裂解单元的进料包括任选的催化裂解原料,是指催化裂解单元进料中除了脱杂含塑溶液外,可以包括其他催化裂解原料。
32.在本发明中,所述催化裂解单元选自dcc、cpp、hcc、催化-蒸汽裂解、thr、快速裂解工艺中的一种或几种;反应器选自固定床、移动床、流化床、提升管、下行输送床中的一种或几种。
33.在本发明的一个实施方式中,催化裂解单元的反应温度为500~850℃,剂油重量比为(1~50):1,水油质量比为(0.01~1):1,反应压力为0.1~2mpa。所述催化裂解催化剂为金属氧化物型催化裂解催化剂、沸石型催化裂解催化剂中的一种或多种。
34.在本发明的一个实施方式中,沸石型催化裂解催化剂的组成为:以沸石型催化裂解催化剂的干基重量为基准,所述沸石型催化裂解催化剂包括1-50重量%的沸石、5-99重量%的无机氧化物和0-70重量%的粘土。
35.在优选的情况下,以沸石的干基重量为基准,所述沸石包括50-100重量%的大孔沸石和0-50重量%的中孔沸石,所述大孔沸石包括选自rey、rehy、usy和高硅y中的至少一种,所述中孔沸石包括zsm系列沸石和/或zrp沸石;所述无机氧化物包括氧化硅和/或氧化铝;所述粘土包括高岭土和/或多水高岭土。
36.在本发明的一个实施方式中,金属氧化物型催化裂解催化剂中含有氧化铝和/或
硅铝酸盐,以及含有选自碱金属氧化物、碱土金属氧化物、第viii族金属氧化物中的一种或几种金属氧化物。
37.在优选的情况下,所述硅铝酸盐选自氧化硅-氧化铝、无定形硅酸铝、分子筛。
38.在优选的情况下,所述金属氧化物选自k、na、ca、fe、co、ni、mo氧化物中一种或几种。
39.本发明另一方面还提供一种用于上述任一方法的废塑料的催化裂解系统,包括,废塑料预处理单元、固液分离单元、催化裂解单元;
40.所述废塑料预处理单元设置废塑料入口、预处理剂入口、溶剂油入口和预处理后物料出口,预处理后物料出口与固液分离单元的入口连通,固液分离单元设置不溶物出口和脱杂含塑溶液出口;
41.催化裂解单元设置脱杂含塑溶液入口、任选的催化裂解原料入口、至少一个低碳烯烃出口,所述固液分离单元的脱杂含塑溶液出口与催化裂解单元的脱杂含塑溶液入口连通。
42.在本发明的一个实施方式中,催化裂解单元设置废催化裂解催化剂出口,该出口与废塑料预处理单元的预处理剂入口连通。
43.在本发明的一个实施方式中,还包括抽提单元、预处理剂回收单元、溶剂回收单元;
44.抽提单元设置不溶物入口、有机溶剂入口、固相物料出口、液相物料出口,固液分离单元的不溶物出口与抽提单元的不溶物入口连通;
45.预处理剂回收单元设置固相物料入口,循环预处理剂出口,抽提单元的固相物料出口与预处理剂回收单元的固相物料入口连通,预处理剂回收单元的循环预处理剂出口与废塑料预处理单元的预处理剂入口连通;
46.溶剂回收单元设置液相物料入口,固体塑料颗粒出口和回收的有机溶剂出口,抽提单元的液相物料出口与溶剂回收单元的液相物料入口连通。
47.在本发明的一个实施方式中,催化裂解单元的废催化裂解催化剂出口与预处理剂回收单元的固相物料入口连通。
48.本发明的特点:
49.本发明在废塑料预处理单元,将废塑料中的氯杂质和硅杂质进行脱除,有效避免了氯脱除,有效避免了氯杂质对后续加工装置的影响作用;其中,硅杂质是以塑料加工过程中添加的有机硅高分子的原始形态脱除,有效避免了后续加工单元催化剂的失活问题。所得的脱杂含塑溶液在催化裂解单元进行反应,得到包括乙烯、丙烯和丁烯的低碳烯烃。本发明将废塑料制备成烯烃单体,使废塑料进行闭合循环,真正实现了塑料的循环利用。
50.本发明不仅有助于解决“白色污染”,而且在生产过程中排污小,环保性好,降低碳排放,具有良好的环境效益、社会效益和经济效益。
附图说明
51.图1是本发明提供的废塑料的催化裂解方法的其中一个实施方式的示意图。
52.其中:1、干燥单元;2、污水处理单元;3、破碎单元;4、废塑料预处理单元;5、固液分离单元;6、抽提单元;7、溶剂回收单元;8、流体输送单元;9、催化裂解单元;10、预处理剂回
收单元。
具体实施方式
53.下面结合附图对本发明进行进一步的说明,但并不因此而限制本发明。
54.图1是本发明提供的废塑料的催化裂解方法的其中一个实施方式的示意图,如图1所示,初步处理后的废塑料在干燥单元1中进行干燥,水蒸气冷凝后所得废水是进入污水处理单元2进行处理后外排。干燥后的废塑料进入破碎单元3破碎为1~200mm的废塑料碎片。所得废塑料碎片与溶剂油、预处理剂一并进入废塑料预处理单元4,其中的pvc充分分解为hcl并被预处理剂捕获,其它大多数塑料溶解于溶剂油后进入固液分离单元5,分离为脱杂溶液和固相物料(不溶物)。所得固相物料进入抽提单元6进行抽提并进一步分离为脱油固相物料和液相物料(含塑有机溶剂),所得的液相物料进入溶剂回收单元7回收有机溶剂,同时回收固体塑料颗粒。抽提单元6所得脱油固相物料进入预处理剂回收单元10处理,部分作为预处理剂循环使用,部分作为固相物料外排。固液分离单元5所得的脱杂溶液通过流体输送单元8进入催化裂解单元9并在此发生催化裂解反应,反应流出物经分离后得到包括低碳烯烃的催化裂解产物。
55.下面结合实施例对本发明作进一步的说明,但并不因此而使本发明受到任何限制。
56.在实施例中,固体混合物中氯含量采用库仑法进行测定,具体方法为《石油化工分析方法》(ripp试验方法)中的《电量法测定原油中总氯含量》(ripp 64-90)的方法进行测定。所用仪器为微库仑分析仪。试样为冷冻粉碎后的废塑料粉末样品。
57.在实施例中,液体混合物中氯含量同样采用《电量法测定原油中总氯含量》(ripp 64-90)的方法进行测定。所不同的是试样为液体混合物。
58.在实施例中,液体混合物中硅含量采用《使用过的润滑油中添加剂元素、磨损金属和污染物以及基础油中某些元素测定法(电感耦合等离子体发射光谱法)》(gb17476-1998)方法进行测定。
59.废塑料a为广东某垃圾填埋场挖掘出陈化垃圾的废塑料,经清洗、干燥后破碎为《50mm,破碎后废塑料a中灰分为9.5%,水分为0。
60.实施例1
61.将破碎后废塑料a通过螺旋进料器送往废塑料预处理单元,废塑预处理单元采用外热式溶解釜,与预处理剂、溶剂油混合后,在320℃、1mpa下进行脱杂处理,废塑料a的停留时间为30min,反应后物料经固液分离单元分离为不溶物和脱杂含塑溶液。所得脱杂含塑溶液中硅含量为1.8μg/g,氯含量为17.3μg/g。
62.采用的溶剂油为本发明催化裂解单元所得催化裂解柴油馏分,其馏程范围为205~360℃,总芳烃含量为78.2质量%,单环芳烃含量为53.1质量%;溶剂油与废塑料的重量比例为5:1。
63.采用的预处理剂为催化裂解单元的废催化剂,粒径为75~150μm;预处理剂与废塑料的重量比例为1:8。
64.实施例2
65.将破碎后废塑料a通过螺旋进料器送往废塑料预处理单元,废塑预处理单元采用
外热式溶解釜,与预处理剂、溶剂油混合后,在300℃、2mpa下进行脱杂处理,废塑料a的停留时间为30min,反应后物料经固液分离单元分离为不溶物和脱杂含塑溶液。所得脱杂含塑溶液中硅含量为2.5μg/g,氯含量为18.2μg/g。
66.采用的溶剂油为炼厂vgo,其馏程范围为275~581℃,总芳烃含量为45.1质量%,单环芳烃含量为21质量%;溶剂油与废塑料的重量比例为5:1。
67.采用的预处理剂为活性炭与fe2o3的混合物,活性炭与fe2o3的质量比为9:1,粒径为75~150μm。预处理剂与废塑料的重量比例为1:8。
68.实施例3
69.将破碎后废塑料a通过螺旋进料器送往废塑料预处理单元,废塑预处理单元采用外热式溶解釜,与预处理剂、溶剂油混合后,在300℃、2mpa下进行脱杂处理,废塑料a的停留时间为30min,反应后物料经固液分离单元分离为不溶物和脱杂含塑溶液。所得脱杂含塑溶液中硅含量为1.5μg/g,氯含量为17.7μg/g。
70.采用的溶剂油为催化裂化轻循环油,其馏程范围为156~338℃,总芳烃含量为76.8质量%,单环芳烃含量为63.8质量%;溶剂油与废塑料的重量比例为5:1。
71.采用的预处理剂为活性炭与fe2o3的混合物,活性炭与fe2o3的质量比为9:1,粒径为75~150μm。预处理剂与废塑料的重量比例为1:8。
72.实施例4
73.将破碎后废塑料a通过螺旋进料器送往废塑料预处理单元,废塑预处理单元采用外热式溶解釜,与预处理剂、溶剂油混合后,在350℃、1.5mpa下进行脱杂处理,废塑料a的停留时间为30min,反应后物料经固液分离单元分离为不溶物和脱杂含塑溶液。所得脱杂含塑溶液中硅含量为1.9μg/g,氯含量为16.8μg/g。
74.采用的溶剂油为本发明催化裂解单元所得催化裂解柴油馏分,其馏程范围为205~360℃,总芳烃含量为78.2质量%,单环芳烃含量为53.1质量%;溶剂油与废塑料的重量比例为5:1。
75.采用的预处理剂为腐殖土与cao的混合物,腐殖土与cao的质量比为8:2,粒径为75~150μm。预处理剂与废塑料的重量比例为1:5。
76.实施例5
77.将破碎后废塑料a通过螺旋进料器送往废塑料预处理单元,废塑预处理单元采用外热式溶解釜,与预处理剂、溶剂油混合后,在330℃、2mpa下进行脱氯、脱硅反应,废塑料a的停留时间为30min,反应后物料经固液分离单元分离为不溶物和脱杂含塑溶液。所得脱杂含塑溶液中硅含量为2.2μg/g,氯含量为12.3μg/g,总金属含量为3.6μg/g。
78.采用的溶剂油为催化裂解柴油与直馏柴油的混合馏分,其馏程范围为162~360℃,总芳烃含量为51质量%,单环芳烃含量为32质量%,溶剂油与废塑料的重量比例为6:1。
79.采用的预处理剂为半焦与催化裂解单元的废催化剂,重量比为1:1混合物,粒径为75~150μm。预处理剂与废塑料的重量比例为1:5。
80.对比例1
81.本对比例与实施例5的废塑料原料、溶剂油、脱杂处理反应条件都相同,不同的是本对比例中不采用任何预处理剂。反应后物料经固液分离单元分离为不溶物和脱杂含塑溶液。所得脱杂含塑溶液中硅含量为72μg/g,氯含量为425μg/g,总金属含量为13μg/g。
82.本对比例所得脱杂含塑溶液中硅杂质、氯杂质含量均过高,不能作为后续加工单元的进料。
83.实施例6
84.将实施例1所得脱杂含塑溶液送至催化裂解单元,与催化裂解催化剂接触进行反应,反应流出物经分离后得到包括低碳烯烃的催化裂解产物。催化裂解单元采用中国石化石油化工科学研究院的cpp技术。
85.催化裂解催化剂牌号为cep,由中国石化催化剂分公司生产。
86.催化裂解反应温度为610℃,反应压力为0.08mpa,剂油比为17,水油比为0.4,空速为4.0h-1
,催化剂再生温度为720℃。
87.所得产品产率如表1所示。由于有机硅分解产物主要为八甲基环四硅氧烷(d4)和十甲基环五硅氧烷(d5),主要集中在汽油馏分中,因此重点分析汽油馏分中的杂质含量。
88.实施例7
89.将实施例5所得脱杂含塑溶液和大庆常压渣油一起送至催化裂解单元,脱杂含塑溶液与大庆常压渣油的重量比为1:2,与催化裂解催化剂接触,进行催化裂解反应,经分离得到包括乙烯、丙烯、丁烯的催化裂解产品。
90.催化裂解单元采用中国石化石油化工科学研究院的dcc技术。
91.催化裂解催化剂牌号为crp,由中国石化催化剂分公司生产。
92.催化裂解反应温度为560℃,反应压力为0.11mpa,剂油比为12,水油比为0.2,空速为4.0h-1
,催化剂再生温度为720℃。
93.所得产品产率如表1所示。
94.表1
[0095][0096]
实施例8
[0097]
所用废塑料b为广东省某垃圾填埋场挖出陈化垃圾中分选出的废塑料,分选后的废塑料基本无水分存在,灰分含量约为9.9重量%。分选回收的废塑料通过传送带送入间歇换热式干燥器中,干燥器温度为105℃,废塑料在干燥器中的停留时间为30min;干燥后的废塑料通过传送带送往剪切式破碎机,将废塑料破碎成小于10mm碎片;通过螺旋进料器将破碎的废塑料b送至废塑料预处理单元,与预处理剂、溶剂油混合后,在350℃、1.5mpa下进行脱杂处理,废塑料b的停留时间为30min,反应后物料经固液分离单元分离为固相物料(不溶物)和脱杂含塑溶液。所得脱杂含塑溶液中硅含量为1.2μg/g,氯含量为9.2μg/g。
[0098]
将固相物料送至抽提单元,与四氢呋喃接触进行溶剂抽提,所得产物经分离后,得到脱油固相物料和液相物料,固相物料在预处理剂回收单元经处理后,部分作为循环预处理剂返回废塑料预处理单元。液相物料在溶剂回收单元,用反萃取剂(水)进行析出处理和分离,得到固体塑料颗粒和混合液,所得的混合液经精馏分别回收四氢呋喃和反萃取剂(水),回收的四氢呋喃和反萃取剂(水)循环使用。
[0099]
将脱杂含塑溶液送往催化裂解单元。与催化裂解催化剂接触进行反应,反应产物经分离得到包括低碳烯烃的催化裂解产品,所得产品产率及部分杂质含量如表2所示。
[0100]
溶剂油为催化裂解单元的馏分油,其馏程范围为150~350℃,总芳烃含量为73质量%,单环芳烃含量为61质量%。
[0101]
预处理剂为催化裂解单元的废催化裂化裂解催化剂(催化裂解平衡剂),预处理剂与废塑料b的重量比1:5。
[0102]
催化裂解单元采用中国石化石油化工科学研究院的dcc技术。
[0103]
催化裂解催化剂牌号为crp,由中国石化催化剂分公司生产。
[0104]
催化裂解反应温度为545℃,反应压力为0.11mpa,剂油比为8.9,水油比为0.2,空速为4.0h-1
,催化剂再生温度为711℃。
[0105]
实施例9
[0106]
废塑料b原料,废塑料预处理单元的预处理剂、溶剂油和反应条件,催化裂解单元的催化剂与反应条件均与实施例8相同。所不同的是,进入催化裂解单元的进料是脱杂含塑溶液与催化裂解原料大庆vgo重量比为1:1的混合原料。
[0107]
原料中杂质、反应过程的积碳沉积于催化剂上会导致催化剂失活,为提高催化剂使用寿命,实施例8和实施例9所用催化裂解单元装置为循环流化床装置,即失活的催化剂在另一装置中再生处理,但金属杂质导致的永久性失活无法再生,因此为维持催化裂解装置稳定运转,需要置换其中的部分催化剂,以使催化剂活性处于较平衡、稳定的状态。通常以维持原有装置稳定运转时处理1t原料油所需的催化剂置换量为指标,本实施例中催化裂解催化剂置换量为1.2kg/t。
[0108]
所得产品产率及部分杂质含量如表2所示。
[0109]
对比例2
[0110]
采用大庆vgo在催化裂解单元进行反应,催化裂解单元的催化剂与反应条件均与实施例8相同。所得产品产率及部分杂质含量如表2所示。
[0111]
对比例3
[0112]
本对比例采用的废塑料b原料,废塑料预处理单元的溶剂油和反应条件,催化裂解单元的催化剂与反应条件均与实施例9相同。所不同的是,废塑料预处理单元没有预处理剂。
[0113]
本对比例中催化裂解催化剂置换量为1.25kg/t。
[0114]
所得产品产率及部分杂质含量如表2所示。
[0115]
表2
[0116][0117]
通过实施例与对比例的催化裂解结果的比较可以发现,当预处理单元无预处理剂时,所得汽油馏分中含有大量的cl和si杂质无法完全脱除;大庆vgo与废塑料共催化裂解乙烯和丙烯均有所提高,特别是乙烯收率因废塑料中废pe含量可能较高而有明显提高;相同来源废塑料与不同的溶剂油共催化裂解时,所得产物分布差异较大。
[0118]
需说明的是,以上所述仅为本发明的任意实施例,并不用于限制本发明,对于本领域的技术人员来讲,本发明可以有各种更改和变化。凡在本发明的精神和原则之内,所做的任何修改、等同替换、改进等,均应包含在本发明的保护范围之内。
再多了解一些
本文用于企业家、创业者技术爱好者查询,结果仅供参考。