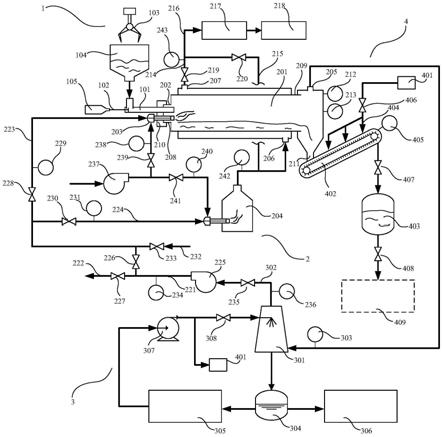
1.本发明涉及一种有机固废热解系统及方法。
背景技术:
2.有机固废(如生活垃圾、农林生物质等,含有一定量有机物成分,低位热值不高但大多可以实现自持燃烧)的处理方法中,以缺氧甚至无氧为处理条件的热解技术可以脱除和热裂解原料中的有机成分,达到减量化和无害化的目标,同时没有电站汽轮机对焚烧线的最小处理规模要求,具有规模更加灵活的特点,可适用于5t/d~200t/d内不同需求场景。但目前的热解技术仍存在一些缺点。
3.例如,专利文献cn111635773a公开了一种有机固废热解气化系统及方法,其存在如下几个问题:
4.(1)将燃烧室设置在回转气化窑尾部,并将回转窑生产得到的部分热解气送回燃烧室焚烧,且该部分热解气焚烧产生的高温烟气作为热源,经高温除尘网后进入回转气化窑内,与物料直接接触,实现对流换热。高温烟气与物料的对流换热和间壁式换热的强度均不如辐射换热,所以采用对流换热或间壁式导热的回转窑,通常窑体直径与长度都较大,而物料实际填充度却很低,通常为5%~8%。
5.(2)该系统需提供过量的高温烟气与物料换热,而物料产生的热解气会与烟气中的惰性成分发生混合,导致混合气的热值降低。随着循环次数的增加,回转气化窑产生热解气的热值逐渐趋于平衡。因此该系统无法处理热值低(如含有机物的工业废盐、未做分类的生活垃圾、含水率较高的污泥与油泥)或热值波动较大(如工业园区多种危废混合物)的物料,甚至还需原料掺煤或燃烧室补燃才能保证稳定运行。
6.再例如,专利文献cn204829926u公开了一种回转窑气化、等离子熔融的生活垃圾分级气化系统,其以熔融炉产生的高温气体作为热解气化的外热源,同时回收合成气热量,提高系统热效率。回转窑式热解气化器为高温合成气与物料对流换热,进行热解反应,也存在专利文献cn111635773a中换热效率低、设备尺寸大、物料填充率低的问题。
7.综上所述,现有技术中的有机固废热裂解技术亟需提升热解反应器的换热效率。
技术实现要素:
8.本发明为了解决现有技术中的有机固废热裂解技术存在间壁回转窑的换热效率低的问题,而提供了一种有机固废热解系统及方法。本发明的间壁回转窑结合窑内辐射换热和筒体间壁式换热,换热效率高,且热解反应系统运行安全稳定。
9.本发明通过下述技术方案解决上述技术问题。
10.本发明提供一种有机固废热解系统,其包括依次连接的进料子系统、热解子系统连接和热解气净化子系统;
11.所述进料子系统包括进料管;
12.所述热解子系统包括间壁回转窑、窑内燃烧器和不凝气焚烧炉;
13.所述间壁回转窑包括进料口、热解气出口、夹套烟气进口和夹套烟气出口;
14.所述进料管穿设于所述进料口,且所述进料管的出口位于所述间壁回转窑的内部;
15.所述窑内燃烧器设于所述间壁回转窑的窑头;
16.所述热解气出口与所述热解气净化子系统的入口连接,用于将热解气净化得到不凝气;
17.所述热解气净化子系统通过第一不凝气输送管路与所述窑内燃烧器连接,为所述窑内燃烧器的燃烧提供不凝气;所述热解气净化子系统通过第二不凝气输送管路与所述不凝气焚烧炉的入口连接,用于产生烟气;
18.所述不凝气焚烧炉的第一出口与所述夹套烟气进口连接;
19.所述夹套烟气进口和所述夹套烟气出口分别设于所述间壁回转窑的外夹套的两端。
20.本发明中,所述窑内燃烧器在所述间壁回转窑内焚烧热解不凝气,焚烧产生的火焰以辐射换热形式提供原料热解所需部分热量。所述不凝气焚烧炉的第一出口与所述夹套烟气进口连接,利用焚烧获得的高温烟气为所述间壁回转窑进行换热。由此,窑内辐射换热与外夹套间壁换热共同满足原料热解所需全部热量。
21.本发明中,较佳地,所述进料子系统还包括原料储罐和原料输送设备。所述原料储罐用于储存干燥后的原料。
22.其中,较佳地,所述原料输送设备包括抓斗起重机和料仓。所述抓斗起重机将所述原料储罐中的原料输送至所述料仓,所述料仓底部的出口与所述进料管的入口管道连接,将原料输送至所述进料管。
23.本发明中,较佳地,所述进料管的管路中还设有液压柱塞泵和活塞推杆。由所述液压柱塞泵驱动所述进料管中的所述活塞推杆,原料在所述进料管中受挤压力被压缩,原料间隙中的空气被排出,减少不可计量的外界空气随原料进入下游的热解子系统;同时,被压缩的原料形成料塞,阻绝微正压运行的所述热解子系统中的高温气体向所述进料管反涌。
24.本发明中,本领域技术人员知晓,所述间壁回转窑的两端分别可称为窑头和窑尾,间壁回转窑的进料口一般设于窑头。
25.本发明中,较佳地,所述间壁回转窑靠近窑头的一端设有窑头密封罩,且所述窑头密封罩与所述间壁回转窑转动连接,形成动静密封。
26.其中,较佳地,所述窑内燃烧器固定于所述窑头密封罩内。
27.其中,较佳地,所述进料管固定于所述窑头密封罩内。
28.较佳地,所述进料管位于所述窑内燃烧器的上方,所述进料管与所述窑内燃烧器外切设置,所述进料管和所述窑内燃烧器分别与所述窑头密封罩内切设置;所述进料管的圆心、所述窑内燃烧器的圆心和所述间壁回转窑的圆心在一条直线上。由此,所述进料管与所述窑内燃烧器的圆心连线与物料堆积面垂直(如图2,即∠a ∠b=90
°
),且所述窑内燃烧器位于所述进料管与物料之间。根据物料在窑体内动态堆积角,确定了进料管与窑内燃烧器角度,优化辐射换热效果。
29.本发明中,较佳地,所述窑头为缩口结构,以减小动静密封面积。
30.本发明中,较佳地,所述间壁回转窑的窑尾为直筒结构,所述间壁回转窑的窑尾密
封罩与间壁回转窑转动连接,形成动静密封。
31.本发明中,较佳地,所述间壁回转窑还包括物料出口;所述物料出口位于所述间壁回转窑的窑尾下方,所述物料出口用于回收所述间壁回转窑热解后的物料。
32.本发明中,较佳地,所述间壁回转窑的窑尾密封罩还设有第一热解气温度计和热解气压力计。
33.本发明中,较佳地,所述热解子系统还包括第一烟气支路、第二烟气支路和烟气总路;
34.所述夹套烟气出口与所述第一烟气支路的进口连接;所述不凝气焚烧炉的第二出口与所述第二烟气支路的进口连接,所述第一烟气支路和所述第二烟气支路汇集为所述烟气总路。
35.其中,较佳地,所述烟气总路的出口与原料干燥单元和烟气净化单元依次连接。
36.其中,较佳地,所述第一烟气支路上设有第一流量调节阀,所述第二烟气支路上设有第二流量调节阀,所述第一流量调节阀和所述第二流量调节阀用以调节分配通往所述间壁回转窑的外夹套的烟气流量与所述第二烟气支路的烟气流量的比例。
37.其中,较佳地,所述不凝气焚烧炉的第一出口与所述夹套烟气进口连接的管路中设有第一烟气温度计,所述第一烟气支路上还设有第二烟气温度计。
38.本发明中,较佳地,所述热解子系统还包括不凝气总管路、排空管和天然气管路;所述不凝气总管路的入口与所述热解气净化子系统连接,所述不凝气总管路的出口分别与所述第一不凝气输送管路和所述第二不凝气输送管路连接,所述不凝气总管路上设有不凝气引风机、第一关断阀、排空口和天然气入口;所述排空管的入口与所述不凝气总管路的排空口连接,所述排空管上设有第二关断阀;所述天然气管路的出口与所述天然气入口连接,且所述天然气入口位于所述第一关断阀的下游管路中。
39.其中,较佳地,所述第一不凝气输送管路中设有第三流量调节阀和第一不凝气流量计。
40.其中,较佳地,所述第二不凝气输送管路中设有第四流量调节阀和第二不凝气流量计。
41.其中,较佳地,所述天然气管路上设有第三关断阀,作为切入或切除天然气通入操作。
42.其中,较佳地,所述不凝气引风机的出口还设有不凝气燃气分析仪。一优选实施方式中,所述不凝气燃气分析仪可检测不凝气的热值、含氧量等信息。
43.其中,较佳地,所述热解子系统还包括不凝气入口压力调节阀和不凝气温度计,所述不凝气入口压力调节阀和所述不凝气温度计设于所述不凝气引风机和所述热解气净化子系统连接的管路中。一优选实施方式中,以压阻节流调节所述不凝气入口压力调节阀的方式可控制所述热解气压力计的压力,维持所述间壁回转窑微正压运行,利用所述不凝气温度计可监测不凝气降温和焦油脱除情况。
44.本发明中,较佳地,所述热解子系统还包括送风机,用于向所述热解子系统提供空气和/或氧气;所述送风机的第一出口管路与所述窑内燃烧器连接,所述送风机的第二出口管路与所述不凝气焚烧炉的入口连接。
45.其中,较佳地,所述送风机的第一出口管路上设有第一氧化剂流量计和第五流量
调节阀;所述送风机的第二出口管路上设有第二氧化剂流量计和第六流量调节阀。一优选实施方式中,可通过控制第五流量调节阀和第三流量调节阀,使得所述间壁回转窑内空气系数为0.7左右,实现窑内燃烧器微缺氧燃烧,防止未反应氧气混入高温热解气;另外,可通过控制第六流量调节阀和第四流量调节阀,保证不凝气焚烧炉的出口的烟气温度为650℃左右,防止管路和所述间壁回转窑的筒体超温。
46.本发明中,较佳地,所述热解气净化子系统包括喷淋塔,所述喷淋塔的入口与所述热解气出口连接,所述喷淋塔的不凝气出口管路分别与所述第一不凝气输送管路和所述第二不凝气输送管路连接。一优选实施方式中,所述喷淋塔的不凝气出口管路与不凝气总管路连接后,分别与所述第一不凝气输送管路和所述第二不凝气输送管路连接。
47.其中,较佳地,所述喷淋塔的入口与所述热解气出口连接的管路中设有第二热解气温度计。
48.其中,较佳地,所述喷淋塔的液体出口与油水分离罐连接,所述油水分离罐位于所述喷淋塔的下方,进行油水分离。
49.较佳地,所述油水分离罐的水相出口与喷淋水冷却单元连接;所述油水分离罐的油相出口与焦油处理单元连接,或者所述油水分离罐的油相出口与所述不凝气焚烧炉的入口连接。所述喷淋水冷却单元可采用闭式风冷。
50.较佳地,所述油水分离罐的水相出口与喷淋水冷却单元和所述喷淋塔依次连接,由此,喷淋塔的喷淋水可回收利用。
51.更佳地,所述喷淋水冷却单元还与出料子系统的所述雾化水管路连接。
52.更佳地,所述喷淋水冷却单元和所述喷淋塔连接的管路中还设有喷淋泵和喷淋水量调节阀。
53.本发明中,较佳地,所述有机固废热解系统还包括出料子系统;所述出料子系统和所述间壁回转窑的物料出口连接。
54.其中,较佳地,所述出料子系统包括依次连接的封闭式出渣刮板机和产物储罐。
55.较佳地,所述封闭式出渣刮板机沿热解残炭行进方向设有若干雾化喷水口。较佳地,所述出料子系统还包括雾化水管路,所述雾化水管路上设有若干所述雾化喷水口;所述封闭式出渣刮板机的出口更佳地设有排焦温度计,所述雾化水管路上设有雾化水调节阀,以调节喷淋量,使得排焦温度计测得的温度维持在150~200℃,实现热解残炭半干熄焦。出料子系统采用封闭式半干法熄焦工艺,增加系统气密性、提高排渣可再利用性,也不会产生废水。一优选实施方式中,所述雾化水管路的入口与所述热解气净化子系统的第一雾化水出口连接。
56.较佳地,所述封闭式出渣刮板机的出口管路中设有第四关断阀,所述产物储罐的出口管路中设有第五关断阀。
57.较佳地,所述产物储罐的出口与热解残渣处理单元连接,将热解残渣送至热解残渣处理单元,分离可回收金属后做无害化处理,如卫生填埋、直接焚烧或做气化原料等。
58.本发明还提供了一种有机固废热解方法,其采用如前所述的有机固废热解系统进行,包括如下步骤:
59.将有机固废通过所述进料管输送至所述间壁回转窑,通过所述窑内燃烧器燃烧,得到热解气;
60.将所述热解气输送至所述热解气净化子系统,将所述热解气净化得到不凝气;
61.将所述不凝气分为至少两部分,将一部分所述不凝气输送至所述窑内燃烧器,为所述窑内燃烧器的燃烧提供不凝气;并将一部分所述不凝气输送至所述不凝气焚烧炉,通过焚烧得到烟气;
62.将所述烟气输送至所述间壁回转窑的外夹套,为所述间壁回转窑提供热量。
63.本发明一优选实施方式中,所述有机固废热解系统的启动包括:间壁回转窑启动步骤、不凝气焚烧炉启动步骤、间壁回转窑内氧气置换步骤、负荷升调步骤、以不凝气替代天然气步骤和系统动态平衡步骤;
64.所述间壁回转窑启动步骤包括:
65.s1.1.在系统冷态下,所述间壁回转窑开始低速转动,转动过程中检查所述间壁回转窑的窑头和窑尾的定位标尺,确定所述间壁回转窑的窑体的径向跳动及轴向定位是否满足窑头密封罩和窑尾密封罩的密封要求;
66.s1.2.逐步提高所述间壁回转窑的转速直至额定转速,并检查所述间壁回转窑的窑体的转动和跳动情况;
67.所述低速转动的转速,本领域技术人员知晓,一般为额定转速的5~25%;
68.所述不凝气焚烧炉启动步骤包括:
69.s2.1.启动喷淋塔、喷淋水冷却单元和喷淋泵;
70.s2.2.打开第二关断阀,并关闭第一关断阀,启动不凝气引风机,调节不凝气入口压力调节阀的开度,使得热解气压力计显示微负压;
71.s2.3.打开第三关断阀,打开送风机,协调控制第三流量调节阀、第五流量调节阀和第四流量调节阀、第六流量调节阀的阀门开度,使所述窑内燃烧器微缺氧燃烧(即过量空气系数《1)、所述不凝气焚烧炉正常燃烧(即过量空气系数》1);通过不凝气焚烧炉与窑内燃烧器预热所述间壁回转窑的窑体,并以烟气置换所述间壁回转窑内的空气;
72.s2.4.调节不凝气入口压力调节阀的开度,保持热解气压力计显示微负压,以维持所述间壁回转窑的窑体内微负压稳定;
73.所述间壁回转窑内氧气置换步骤包括:
74.s3.1.调节不凝气入口压力调节阀的开度,保持热解气压力计显示微正压;
75.s3.2.保持所述窑内燃烧器稳定在微缺氧燃烧状态,观察不凝气燃气分析仪测得的氧浓度由21%(即空气中氧浓度)逐渐降低至安全范围(≤0.5%vol.);直至所述间壁回转窑与其热解气管路中氧气置换完全;
76.所述负荷升调步骤包括:
77.s4.1.以第二热解气温度计作为热解气管路预热程度判定指标,防止温度较低造成热解气在管路中冷凝堵塞;
78.s4.2.开启液压柱塞泵,以小负荷(30%~50%)开始进料,进料过程中观察液压柱塞泵的油压缸压力变化情况(反映物料在所述进料管中的挤压情况和形成的料塞形态);同时调整不凝气引风机的风量和不凝气入口压力调节阀的开度,保持热解气压力计显示微正压;
79.s4.3.逐步提高负荷,直至负荷达到100%;
80.所述以不凝气替代天然气步骤包括:
81.s5.1.观察出料子系统排出的热解残渣的形态,判断物料是否热解充分;以不凝气燃气分析仪测得的热值大小判断不凝气品质是否达标(即判断是否满足稳定燃烧需求);
82.s5.2.打开第一关断阀,关闭第二关断阀,使不凝气输送入不凝气总管路;逐渐减小第三关断阀的开度直至第三关断阀完全关闭,使天然气完全切除;同时调节送风机的风量及第五流量调节阀和第六流量调节阀的开度,保持所述窑内燃烧器微缺氧燃烧、所述不凝气焚烧炉正常燃烧;
83.所述系统动态平衡步骤包括:
84.s6.1.分析热解残渣性质,观察有无夹生等情况;
85.s6.2.观察第一热解气温度计(热解气温度是否达标)、热解气压力计(所述间壁回转窑是否稳定微正压运行)、不凝气温度计(喷淋塔是否工作正常)、不凝气燃气分析仪(不凝气热值及氧浓度水平是否达标)、第一烟气温度计和第二烟气温度计(所述间壁回转窑外夹套中烟气提供热量是否充分)的测量结果,达到设定目标则表明系统已实现稳定运行。
86.本发明一优选实施方式中,所述有机固废热解系统的不凝气热值低或含氧量超标的处理步骤包括:天然气替代不凝气步骤、负荷降调步骤、间壁回转窑内氧气置换步骤、负荷升调步骤、以不凝气替代天然气步骤和系统动态平衡步骤;
87.所述天然气替代不凝气步骤包括:
88.s1.1.缓慢开启第三关断阀的开度,将少量天然气输送至不凝气总管路,提高不凝气热值,以保持所述窑内燃烧器与所述不凝气焚烧炉燃烧稳定;
89.s1.2.在开启第三关断阀的开度的过程中,缓慢增加第二关断阀的开度并减小第一关断阀的开度,直至第三关断阀和第二关断阀完全开启、第一关断阀关闭;过程中维持所述窑内燃烧器于微缺氧条件下燃烧、所述不凝气焚烧炉正常燃烧、热解气压力计显示微正压;
90.所述负荷降调步骤包括:
91.s2.1.降低液压柱塞泵的推送料频率,使进料量降低至小负荷(30%~50%),过程中观察液压柱塞泵的油压缸压力和热解气压力计的压力变化情况,维持进料管的料塞密封以及所述间壁回转窑于微正压条件下运行;
92.s2.2.减小送风机的风量,并减小第三关断阀的开度,减小天然气流量;以降低所述窑内燃烧器、所述不凝气焚烧炉的热功率;
93.所述间壁回转窑内氧气置换步骤包括:
94.s3.1.调节不凝气入口压力调节阀的开度,保持热解气压力计显示微正压;
95.s3.2.保持所述窑内燃烧器稳定在微缺氧燃烧状态,观察不凝气燃气分析仪测得的氧浓度逐渐降低至安全范围(≤0.5%vol.);直至所述间壁回转窑与其热解气管路中氧气置换完全;
96.所述负荷升调步骤包括:
97.s4.1.以第二热解气温度计作为热解气管路预热程度判定指标,防止温度较低造成热解气在管路中冷凝堵塞;
98.s4.2.开启液压柱塞泵,以小负荷(30%~50%)开始进料,进料过程中观察液压柱塞泵的油压缸压力变化情况(反映物料在所述进料管中的挤压情况和形成的料塞形态);同时调整不凝气引风机的风量和不凝气入口压力调节阀的开度,保持热解气压力计显示微正
压;
99.s4.3.逐步提高负荷,直至负荷达到100%;
100.所述以不凝气替代天然气步骤包括:
101.s5.1.观察出料子系统排出的热解残渣的形态,判断物料是否热解充分;以不凝气燃气分析仪测得的热值大小判断不凝气品质是否达标(即判断是否满足稳定燃烧需求);
102.s5.2.打开第一关断阀,关闭第二关断阀,使不凝气输送入不凝气总管路;逐渐减小第三关断阀的开度直至第三关断阀完全关闭,使天然气完全切除;同时调节送风机的风量及第五流量调节阀和第六流量调节阀的开度,保持所述窑内燃烧器微缺氧燃烧、所述不凝气焚烧炉正常燃烧;
103.所述系统动态平衡步骤包括:
104.s6.1.分析热解残渣性质,观察有无夹生等情况;
105.s6.2.观察第一热解气温度计(热解气温度是否达标)、热解气压力计(所述间壁回转窑是否稳定微正压运行)、不凝气温度计(喷淋塔是否工作正常)、不凝气燃气分析仪(不凝气热值及氧浓度水平是否达标)、第一烟气温度计和第二烟气温度计(所述间壁回转窑外夹套中烟气提供热量是否充分)的测量结果,达到设定目标则表明系统已实现稳定运行。
106.本发明一优选实施方式中,所述有机固废热解系统的停炉包括:天然气替代不凝气步骤、负荷降调步骤、天然气切除步骤和间壁回转窑停机步骤;
107.所述天然气替代不凝气步骤包括:
108.s1.1.缓慢开启第三关断阀的开度,将少量天然气输送至不凝气总管路,提高不凝气热值,以保持所述窑内燃烧器与所述不凝气焚烧炉燃烧稳定;
109.s1.2.在开启第三关断阀的开度的过程中,缓慢增加第二关断阀的开度并减小第一关断阀的开度,直至第三关断阀和第二关断阀完全开启、第一关断阀关闭;过程中维持所述窑内燃烧器于微缺氧条件下燃烧、所述不凝气焚烧炉正常燃烧、热解气压力计显示微正压;
110.所述负荷降调步骤包括:
111.s2.1.停止液压柱塞泵的推进料动作;
112.s2.2.所述间壁回转窑持续以额定转速运行,直至所述间壁回转窑内的物料全部排出;
113.所述天然气切除步骤包括:
114.s3.关闭第三流量调节阀和第三关断阀,关闭送风机,关闭所述窑内燃烧器;
115.所述间壁回转窑停机步骤包括:
116.s4.1.观察不凝气燃气分析仪检测得到的气体热值降为0,即所述间壁回转窑及其管路中可燃气成分全部置换完全后,开启送风机,开启第五流量调节阀,使外界冷空气自所述窑内燃烧器输送至所述间壁回转窑内,观察不凝气燃气分析仪检测得到的氧浓度恢复至21%,表示窑体内烟气已置换完全,即可关闭送风机;
117.s4.2.降低所述间壁回转窑的转速,直至所述间壁回转窑降至安全停机温度,即可关闭所述间壁回转窑。
118.在符合本领域常识的基础上,上述各优选条件,可任意组合,即得本发明各较佳实例。
119.本发明所用试剂和原料均市售可得。
120.本发明的积极进步效果在于:
121.本发明的间壁回转窑结合窑内辐射换热和筒体间壁式换热,换热效率高,且热解反应系统运行安全稳定。本发明的有机固废热解系统可实现系统安全稳定运行,可广泛适用于城镇生活垃圾、含油污泥、危废盐等处置。
附图说明
122.图1为实施例1的有机固废热解系统示意图。
123.图2为实施例1的窑内燃烧器与进料管横截面示意图。
124.图3为实施例1的窑内燃烧器与进料管示意图。
125.图4为实施例1的有机固废热解系统启动步骤流程图。
126.图5为实施例1的有机固废热解系统的不凝气热值低或含氧量超标的处理步骤流程图。
127.图6为实施例的有机固废热解系统停炉步骤示意图。
128.附图标记说明
129.进料子系统1
130.进料管101
131.活塞推杆102
132.抓斗起重机103
133.料仓104
134.液压柱塞泵105
135.热解子系统2
136.间壁回转窑201
137.进料口202
138.窑内燃烧器203
139.不凝气焚烧炉204
140.热解气出口205
141.夹套烟气进口206
142.夹套烟气出口207
143.窑头208
144.窑尾209
145.窑头密封罩210
146.物料出口211
147.第一热解气温度计212
148.热解气压力计213
149.第一烟气支路214
150.第二烟气支路215
151.烟气总路216
152.原料干燥单元217
153.烟气净化单元218
154.第一流量调节阀219
155.第二流量调节阀220
156.不凝气总管路221
157.排空管222
158.第一不凝气输送管路223
159.第二不凝气输送管路224
160.不凝气引风机225
161.第一关断阀226
162.第二关断阀227
163.第三流量调节阀228
164.第一不凝气流量计229
165.第四流量调节阀230
166.第二不凝气流量计231
167.天然气管路232
168.第三关断阀233
169.不凝气燃气分析仪234
170.不凝气入口压力调节阀235
171.不凝气温度计236
172.送风机237
173.第一氧化剂流量计238
174.第五流量调节阀239
175.第二氧化剂流量计240
176.第六流量调节阀241
177.第一烟气温度计242
178.第二烟气温度计243
179.热解气净化子系统3
180.喷淋塔301
181.不凝气出口管路302
182.第二热解气温度计303
183.油水分离罐304
184.喷淋水冷却单元305
185.焦油处理单元306
186.喷淋泵307
187.喷淋水量调节阀308
188.出料子系统4
189.雾化水管路401
190.封闭式出渣刮板机402
191.产物储罐403
192.雾化喷水口404
193.排焦温度计405
194.雾化水调节阀406
195.第四关断阀407
196.第五关断阀408
197.热解残渣处理单元409
具体实施方式
198.下面通过实施例的方式进一步说明本发明,但并不因此将本发明限制在的实施例范围之中。下列实施例中未注明具体条件的实验方法,按照常规方法和条件,或按照商品说明书选择。
199.实施例1
200.如图1所示,实施例1的有机固废热解系统包括依次连接的进料子系统1、热解子系统2连接和热解气净化子系统3;进料子系统1包括进料管101;热解子系统2包括间壁回转窑201、窑内燃烧器203和不凝气焚烧炉204;间壁回转窑201包括进料口202、热解气出口205、夹套烟气进口206和夹套烟气出口207;进料管101穿设于进料口202,且进料管101的出口位于间壁回转窑201的内部;窑内燃烧器203设于间壁回转窑201的窑头208;热解气出口205与热解气净化子系统3的入口连接,用于将热解气净化得到不凝气;热解气净化子系统3通过第一不凝气输送管路223与窑内燃烧器203连接,为窑内燃烧器203的燃烧提供不凝气;热解气净化子系统3通过第二不凝气输送管路224与不凝气焚烧炉204的入口连接,用于产生烟气;不凝气焚烧炉204的第一出口与夹套烟气进口206连接;夹套烟气进口206和夹套烟气出口207分别设于间壁回转窑201的外夹套的两端。
201.窑内燃烧器203在间壁回转窑201内焚烧热解不凝气,焚烧产生的火焰以辐射换热形式提供原料热解所需部分热量。不凝气焚烧炉204的第一出口与夹套烟气进口206连接,利用焚烧获得的高温烟气为间壁回转窑201进行换热。由此,窑内辐射换热与外夹套间壁换热共同满足原料热解所需全部热量。
202.进料子系统1还包括原料储罐和原料输送设备。原料储罐用于储存干燥后的原料。原料输送设备包括抓斗起重机103和料仓104。抓斗起重机103将原料储罐中的原料输送至料仓104,料仓104底部的出口与进料管101的入口管道连接,将原料输送至进料管101。进料管101的管路中还设有液压柱塞泵105和活塞推杆102。由液压柱塞泵105驱动进料管101中的活塞推杆102,原料在进料管101中受挤压力被压缩,原料间隙中的空气被排出,减少不可计量的外界空气随原料进入下游的热解子系统2;同时,被压缩的原料形成料塞,阻绝微正压运行的热解子系统2中的高温气体向进料管101反涌。
203.间壁回转窑201的两端分别为窑头208和窑尾209。间壁回转窑201靠近窑头208的一端设有窑头密封罩210,且窑头密封罩210与间壁回转窑201转动连接,形成动静密封。窑内燃烧器203固定于窑头密封罩210内。进料管101固定于窑头密封罩210内。
204.如图2和图3所示,进料管101位于窑内燃烧器203的上方,进料管101与窑内燃烧器203外切设置,进料管101和窑内燃烧器203分别与窑头密封罩210内切设置;进料管101的圆心、窑内燃烧器203的圆心和间壁回转窑201的圆心在一条直线上。由此,进料管101与窑内
燃烧器203的圆心连线与物料堆积面垂直(如图2,即∠a ∠b=90
°
),且窑内燃烧器203位于进料管101与物料之间。根据物料在窑体内动态堆积角,确定了进料管101与窑内燃烧器203角度,优化辐射换热效果。
205.窑头208为缩口结构,以减小动静密封面积。
206.间壁回转窑201的窑尾209为直筒结构,间壁回转窑201的窑尾密封罩与间壁回转窑201转动连接,形成动静密封。
207.间壁回转窑201还包括物料出口211;物料出口211位于间壁回转窑201的窑尾209下方,物料出口211用于回收间壁回转窑201热解后的物料。间壁回转窑201的窑尾密封罩还设有第一热解气温度计212和热解气压力计213。
208.热解子系统2还包括第一烟气支路214、第二烟气支路215和烟气总路216;夹套烟气出口207与第一烟气支路214的进口连接;不凝气焚烧炉204的第二出口与第二烟气支路215的进口连接,第一烟气支路214和第二烟气支路215汇集为烟气总路216。烟气总路216的出口与原料干燥单元217和烟气净化单元218依次连接。第一烟气支路214上设有第一流量调节阀219,第二烟气支路215上设有第二流量调节阀220,第一流量调节阀219和第二流量调节阀220用以调节分配通往间壁回转窑201的外夹套的烟气流量与第二烟气支路215的烟气流量的比例。
209.不凝气焚烧炉204的第一出口与夹套烟气进口206连接的管路中设有第一烟气温度计242,第一烟气支路214上还设有第二烟气温度计243。
210.热解子系统2还包括不凝气总管路221、排空管222和天然气管路232;不凝气总管路221的入口与热解气净化子系统3连接,不凝气总管路221的出口分别与第一不凝气输送管路223和第二不凝气输送管路224连接,不凝气总管路221上设有不凝气引风机225、第一关断阀226、排空口和天然气入口;排空管222的入口与不凝气总管路221的排空口连接,排空管222上设有第二关断阀227;天然气管路232的出口与天然气入口连接,且天然气入口位于第一关断阀226的下游管路中。第一不凝气输送管路223中设有第三流量调节阀228和第一不凝气流量计229。第二不凝气输送管路224中设有第四流量调节阀230和第二不凝气流量计231。天然气管路232上设有第三关断阀233,作为切入或切除天然气通入操作。不凝气引风机225的出口还设有不凝气燃气分析仪234。不凝气燃气分析仪234可检测不凝气的热值、含氧量等信息。
211.热解子系统2还包括不凝气入口压力调节阀235和不凝气温度计236,不凝气入口压力调节阀235和不凝气温度计236设于不凝气引风机225和热解气净化子系统3连接的管路中。以压阻节流调节不凝气入口压力调节阀235的方式可控制热解气压力计213的压力,维持间壁回转窑201微正压运行,利用不凝气温度计236可监测不凝气降温和焦油脱除情况。
212.热解子系统2还包括送风机237,用于向热解子系统2提供空气和/或氧气;送风机237的第一出口管路与窑内燃烧器203连接,送风机237的第二出口管路与不凝气焚烧炉204的入口连接。
213.送风机237的第一出口管路上设有第一氧化剂流量计238和第五流量调节阀239;送风机237的第二出口管路上设有第二氧化剂流量计240和第六流量调节阀241。可通过控制第五流量调节阀239和第三流量调节阀228,使得间壁回转窑201内空气系数为0.7左右,
实现窑内燃烧器203微缺氧燃烧,防止未反应氧气混入高温热解气;另外,可通过控制第六流量调节阀241和第四流量调节阀230,保证不凝气焚烧炉204的出口的烟气温度为650℃左右,防止管路和间壁回转窑201的筒体超温。
214.热解气净化子系统3包括喷淋塔301,喷淋塔301的入口与热解气出口205连接,喷淋塔301的不凝气出口管路302与不凝气总管路221连接后,分别与第一不凝气输送管路223和第二不凝气输送管路224连接。喷淋塔301的入口与热解气出口205连接的管路中设有第二热解气温度计303。喷淋塔301的液体出口与油水分离罐304连接,油水分离罐304位于喷淋塔301的下方,进行油水分离。油水分离罐304的水相出口与喷淋水冷却单元305连接;油水分离罐304的油相出口与焦油处理单元306连接。喷淋水冷却单元305可采用闭式风冷。油水分离罐304的水相出口与喷淋水冷却单元305和喷淋塔301依次连接,由此,喷淋塔301的喷淋水可回收利用。喷淋水冷却单元305还与出料子系统4的雾化水管路401连接。喷淋水冷却单元305和喷淋塔301连接的管路中还设有喷淋泵307和喷淋水量调节阀308。
215.有机固废热解系统还包括出料子系统4;出料子系统4和间壁回转窑201的物料出口211连接。出料子系统4包括依次连接的封闭式出渣刮板机402和产物储罐403。封闭式出渣刮板机402沿热解残炭行进方向设有若干雾化喷水口404。雾化水管路401上设有若干雾化喷水口404;封闭式出渣刮板机402的出口设有排焦温度计405,雾化水管路401上设有雾化水调节阀406,以调节喷淋量,使得排焦温度计405测得的温度维持在150~200℃,实现热解残炭半干熄焦。出料子系统4采用封闭式半干法熄焦工艺,增加系统气密性、提高排渣可再利用性,也不会产生废水。封闭式出渣刮板机402的出口管路中设有第四关断阀407,产物储罐403的出口管路中设有第五关断阀408。
216.产物储罐403的出口与热解残渣处理单元409连接,将热解残渣送至热解残渣处理单元409,分离可回收金属后做无害化处理,如卫生填埋、直接焚烧或做气化原料等。
217.实施例1的有机固废热解系统的有机固废热解方法包括如下步骤:
218.将有机固废通过进料管101输送至间壁回转窑201,通过窑内燃烧器203燃烧,得到热解气;将热解气输送至热解气净化子系统3,将热解气净化得到不凝气;将不凝气分为至少两部分,将一部分不凝气输送至窑内燃烧器203,为窑内燃烧器203的燃烧提供不凝气;并将一部分不凝气输送至不凝气焚烧炉204,通过焚烧得到烟气;将烟气输送至间壁回转窑201的外夹套,为间壁回转窑201提供热量。
219.如图4所示,有机固废热解系统的启动包括:间壁回转窑201启动步骤、不凝气焚烧炉204启动步骤、间壁回转窑201内氧气置换步骤、负荷升调步骤、以不凝气替代天然气步骤和系统动态平衡步骤;
220.间壁回转窑201启动步骤包括:
221.s1.1.在系统冷态下,间壁回转窑201开始低速转动(0.5r/min),转动过程中检查间壁回转窑201的窑头208和窑尾209的定位标尺,确定间壁回转窑201的窑体的径向跳动≤1.5mm及轴向定位是否满足窑头密封罩210和窑尾密封罩的密封要求;
222.s1.2.逐步提高间壁回转窑201的转速直至额定转速(2r/min),并检查间壁回转窑201的窑体的转动和跳动≤1.5mm情况;
223.不凝气焚烧炉204启动步骤包括:
224.s2.1.启动喷淋塔301、喷淋水冷却单元305和喷淋泵307,调整喷淋水量为30t/h、
水温35℃以下;
225.s2.2.打开第二关断阀227,并关闭第一关断阀226,启动不凝气引风机225,频率设定20hz,调节不凝气入口压力调节阀235的开度为30%,使得热解气压力计213显示微负压(-100pa~-50pa);
226.s2.3.打开第三关断阀233,打开送风机237,频率设定40hz,协调控制第三流量调节阀228、第五流量调节阀239和第四流量调节阀230、第六流量调节阀241的阀门开度,使窑内燃烧器203微缺氧燃烧(天然气流量7nm3/h,过量空气系数=0.7)、不凝气焚烧炉204正常燃烧(天然气流量10nm3/h,过量空气系数=1.1;通过不凝气焚烧炉204与窑内燃烧器203预热间壁回转窑201的窑体,并以烟气置换间壁回转窑201内的空气;
227.s2.4.调节不凝气入口压力调节阀235的开度至80%,保持热解气压力计213显示微负压,以维持间壁回转窑201的窑体内微负压(-100pa~-50pa)稳定;
228.间壁回转窑201内氧气置换步骤包括:
229.s3.1.调节不凝气入口压力调节阀235的开度至70%,保持热解气压力计213显示微正压( 50pa~ 100pa);
230.s3.2.保持窑内燃烧器203稳定在微缺氧燃烧状态,观察不凝气燃气分析仪234测得的氧浓度由21%(即空气中氧浓度)逐渐降低至安全范围(降低至0.03%vol.);直至间壁回转窑201与其热解气管路中氧气置换完全;
231.负荷升调步骤包括:
232.s4.1.以第二热解气温度计303(达到200℃)作为热解气管路预热程度判定指标,防止温度较低造成热解气在管路中冷凝堵塞;
233.s4.2.开启液压柱塞泵105,以小负荷(40%)开始进料,进料过程中观察液压柱塞泵105的油压缸压力变化情况(反映物料在进料管101中的挤压情况和形成的料塞形态);同时调整不凝气引风机225的风量至30hz和不凝气入口压力调节阀235的开度至75%,保持热解气压力计213显示微正压( 50pa~ 100pa);
234.s4.3.逐步提高负荷,直至负荷达到100%;
235.以不凝气替代天然气步骤包括:
236.s5.1.观察出料子系统4排出的热解残渣的形态,判断物料是否热解充分;以不凝气燃气分析仪234测得的热值大小(热值约4.5mj/nm3)判断不凝气品质是否达标(即判断是否满足稳定燃烧需求);
237.s5.2.打开第一关断阀226,关闭第二关断阀227,使不凝气输送入不凝气总管路221;逐渐减小第三关断阀233的开度直至第三关断阀233完全关闭,使天然气完全切除;同时调节送风机237的风量及第五流量调节阀239和第六流量调节阀241的开度,保持窑内燃烧器203微缺氧燃烧、不凝气焚烧炉204正常燃烧;
238.系统动态平衡步骤包括:
239.s6.1.分析热解残渣性质,观察有无夹生等情况;
240.s6.2.观察第一热解气温度计212(热解气温度是否达450℃)、热解气压力计213(间壁回转窑201是否稳定于约 80pa运行)、不凝气温度计236(喷淋塔301是否工作正常,40℃)、不凝气燃气分析仪234(不凝气热值及氧浓度水平是否达标,热值4.5mj/nm3、氧浓度0.08%vol.)、第一烟气温度计242和第二烟气温度计243(间壁回转窑201外夹套中烟气提
供热量是否充分,第一烟气温度计242和第二烟气温度计243分别为650℃和160℃左右)的测量结果,达到设定目标则表明系统已实现稳定运行。
241.如图5所示,有机固废热解系统的不凝气热值低或含氧量超标的处理步骤包括:天然气替代不凝气步骤、负荷降调步骤、间壁回转窑201内氧气置换步骤、负荷升调步骤、以不凝气替代天然气步骤和系统动态平衡步骤;
242.天然气替代不凝气步骤包括:
243.s1.1.缓慢开启第三关断阀233的开度,将少量天然气输送至不凝气总管路221,提高不凝气热值,以保持窑内燃烧器203与不凝气焚烧炉204燃烧稳定;
244.s1.2.在开启第三关断阀233的开度的过程中,缓慢增加第二关断阀227的开度并减小第一关断阀226的开度,直至第三关断阀233和第二关断阀227完全开启、第一关断阀226关闭;过程中维持窑内燃烧器203于微缺氧条件下燃烧、不凝气焚烧炉204正常燃烧、热解气压力计213显示微正压( 50pa~ 100pa);
245.负荷降调步骤包括:
246.s2.1.降低液压柱塞泵105的推送料频率,使进料量降低至小负荷(30%),过程中观察液压柱塞泵105的油压缸压力和热解气压力计213的压力变化情况,维持进料管101的料塞密封以及间壁回转窑201于微正压条件下运行;
247.s2.2.减小送风机237的风量,并减小第三关断阀233的开度,减小天然气流量;以降低窑内燃烧器203、不凝气焚烧炉204的热功率;
248.间壁回转窑201内氧气置换步骤包括(可与有机固废热解系统的启动中的间壁回转窑201内氧气置换步骤相同):
249.s3.1.调节不凝气入口压力调节阀235的开度,保持热解气压力计213显示微正压;
250.s3.2.保持窑内燃烧器203稳定在微缺氧燃烧状态,观察不凝气燃气分析仪234测得的氧浓度逐渐降低至安全范围(≤0.5%vol.);直至间壁回转窑201与其热解气管路中氧气置换完全;
251.负荷升调步骤包括(可与有机固废热解系统的启动中的负荷升调步骤相同):
252.s4.1.以第二热解气温度计303作为热解气管路预热程度判定指标,防止温度较低造成热解气在管路中冷凝堵塞;
253.s4.2.开启液压柱塞泵105,以小负荷(30%~50%)开始进料,进料过程中观察液压柱塞泵105的油压缸压力变化情况(反映物料在进料管101中的挤压情况和形成的料塞形态);同时调整不凝气引风机225的风量和不凝气入口压力调节阀235的开度,保持热解气压力计213显示微正压;
254.s4.3.逐步提高负荷,直至负荷达到100%;
255.以不凝气替代天然气步骤包括(可与有机固废热解系统的启动中的以不凝气替代天然气步骤相同):
256.s5.1.观察出料子系统4排出的热解残渣的形态,判断物料是否热解充分;以不凝气燃气分析仪234测得的热值大小判断不凝气品质是否达标(即判断是否满足稳定燃烧需求);
257.s5.2.打开第一关断阀226,关闭第二关断阀227,使不凝气输送入不凝气总管路221;逐渐减小第三关断阀233的开度直至第三关断阀233完全关闭,使天然气完全切除;同
时调节送风机237的风量及第五流量调节阀239和第六流量调节阀241的开度,保持窑内燃烧器203微缺氧燃烧、不凝气焚烧炉204正常燃烧;
258.系统动态平衡步骤包括(可与有机固废热解系统的启动中的系统动态平衡步骤相同):
259.s6.1.分析热解残渣性质,观察有无夹生等情况;
260.s6.2.观察第一热解气温度计212(热解气温度是否达标)、热解气压力计213(间壁回转窑201是否稳定微正压运行)、不凝气温度计236(喷淋塔301是否工作正常)、不凝气燃气分析仪234(不凝气热值及氧浓度水平是否达标)、第一烟气温度计242和第二烟气温度计243(间壁回转窑201外夹套中烟气提供热量是否充分)的测量结果,达到设定目标则表明系统已实现稳定运行。
261.如图6所示,有机固废热解系统的停炉包括:天然气替代不凝气步骤、负荷降调步骤、天然气切除步骤和间壁回转窑201停机步骤;
262.天然气替代不凝气步骤包括:
263.s1.1.缓慢开启第三关断阀233的开度,将少量天然气输送至不凝气总管路221,提高不凝气热值,以保持窑内燃烧器203与不凝气焚烧炉204燃烧稳定;
264.s1.2.在开启第三关断阀233的开度的过程中,缓慢增加第二关断阀227的开度并减小第一关断阀226的开度,直至第三关断阀233和第二关断阀227完全开启、第一关断阀226关闭;过程中维持窑内燃烧器203于微缺氧条件下燃烧、不凝气焚烧炉204正常燃烧、热解气压力计213显示微正压;
265.负荷降调步骤包括:
266.s2.1.停止液压柱塞泵105的推进料动作;
267.s2.2.间壁回转窑201持续以额定转速运行,直至间壁回转窑201内的物料全部排出;
268.天然气切除步骤包括:
269.s3.关闭第三流量调节阀228和第三关断阀233,关闭送风机237,关闭窑内燃烧器203;
270.间壁回转窑201停机步骤包括:
271.s4.1.观察不凝气燃气分析仪234检测得到的气体热值降为0,即间壁回转窑201及其管路中可燃气成分全部置换完全后,开启送风机237,开启第五流量调节阀239,使外界冷空气自窑内燃烧器203输送至间壁回转窑201内,观察不凝气燃气分析仪234检测得到的氧浓度恢复至21%,表示窑体内烟气已置换完全,即可关闭送风机237;
272.s4.2.降低间壁回转窑201的转速,直至间壁回转窑201降至安全停机温度,即可关闭间壁回转窑201。
再多了解一些
本文用于企业家、创业者技术爱好者查询,结果仅供参考。