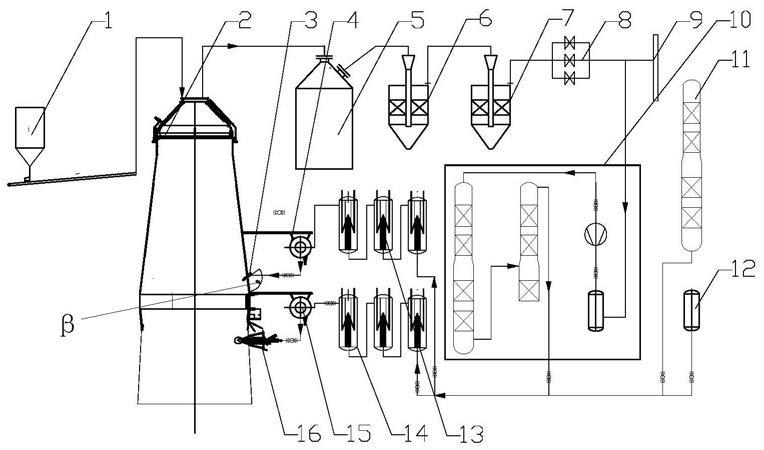
1.本发明属于低碳冶金领域,具体涉及一种富氢碳循环高炉的炼铁系统。
背景技术:
2.钢铁工业消耗大量资源,同时排放大量温室气体,其中以烧结球团、焦化、高炉及热风炉所组成的传统高炉炼铁系统能耗及co2排放所占钢铁行业的比例分别高达69%及73%。当前,传统高炉炼铁技术在生产效率、能量利用等方面已发挥到极致,仅依靠操作手段的改进难以实现高炉炼铁较大幅度的节能减排。针对全球环保意识增强、资源日益枯竭的现状, 必须对现有的高炉炼铁工艺加以改进,使之在技术上、经济上及环境上更加符合时代发展的需要。全氧高炉炼铁技术是最有可能实现规模化应用的炼铁新工艺之一,它具有高喷煤量、低焦比、生产率高、煤气品质高等优点,有可能使煤粉取代焦炭成为主要的炼铁能源物质,从而大幅度降低成本。更为重要的是,可以大幅度减少co2排放,大大减轻钢铁行业所面临的减排压力。但是其存在高炉顶气循环量不足的问题,对炉内矿石还原及进一步降低焦比等化石燃料严重制约。
技术实现要素:
3.本发明的目的在于提出一种富氢碳循环高炉的炼铁系统,通过设置和使用煤气循环加热,可有效解决全氧高炉顶气循环量不足的问题,进而大幅度的降低焦比和煤比,对化石燃料的需求减少,吨铁co2排放减少。
4.一种富氢碳循环高炉的炼铁系统,包括:富氢碳循环高炉、煤气炉顶循环脱碳装置、欧冶炉煤气脱碳装置,焦炉煤气系统;其中,富氢碳循环高炉所使用的原燃料由加料系统通过称量后由传输带及料车运输至炉顶,加入炉内,富氢碳循环高炉用于炼铁,以便得到合格的铁水,并产生炉渣和高炉炉顶粗煤气;除尘装置分别对高炉炉顶的粗煤气进行粗除尘和精细除尘,进行除尘处理,含尘处理后通过煤气脱水装置脱水后进入调压阀组调整富氢碳循环高炉的炉顶压力;经过含尘处理的煤气一部分经过炉顶煤气循环脱碳装置之后分成2路,一路经过风口煤气加热系统,煤气温度加热到1100-1200℃,在富氢碳循环高炉炉缸上环形设置有氧气风口、喷煤气口的复合风口装置,送入风口加热煤气环管,由环管分配加热煤气至14个复合风口装置,与氧气同时送入炉内;另一路经过炉身煤气加热系统,煤气温度加热到850-950℃,在富氢碳循环高炉炉身中下部设置有炉身加热煤气环管,由环管分配加热煤气设有14个炉身加热煤气入口,喷口内径φ100mm,喷吹能力20000nm3/h,压力0.35mpa,喷吹管道承压按0.6mpa,钢壳材质采用耐热钢q355r,通过冷却壁错台形成喷吹环道向炉内喷吹渗透热煤气;所述的炉身加热煤气入口与所述复合风口装置煤气入口之间的距离为l1,炉身加热煤气入口与炉顶的距离为l2,其中l1:l2为6.5:8.2,所述炉身加热煤气入口与炉身外壁下部的夹角为β,所述β的夹角度数范围为112~130
°
。
5.本发明有益效果:氧气高炉普遍存在炉缸内产生的煤气量少,对高炉上部炉料的加热能力不足,导致高炉上部还原能力变差,炼铁效率低的缺陷。为此,本发明的富氢碳循环高炉的生产系统将炉顶煤气脱碳循环,同时补充欧冶炉脱碳煤气和焦炉煤气,并经过煤气电加热,经过加热后的高温还原气的温度可以达到900-1200摄氏度。进而可以直接通入富氢碳循环高炉的风口与炉身下部,进而将该加热后的高炉炉顶气循环返回富氢碳循环高炉内。 由此可以为富氢碳循环高炉提供足够多的还原煤气,使高炉上部区域间接还原程度大大增加,同时减少高炉下部区域直接还原,减少炉缸高温区的热耗。 从而有效地解决了高炉炉顶气还原能力弱、温度低的问题,进而有效增加了富氢碳循环高炉系统的造气能力,同时设计了补充欧冶炉脱碳煤气和焦炉煤气避免了循环煤气量不足。
6.根据本发明的具体实施例,将上述在加热后得到的高温还原气通入富氢碳循环高炉的风口的同时,降低风口回旋区理论燃烧温度,适宜低硅冶炼。 炉身通入高温煤气进而可以,利用高温还原气对富氢碳循环高炉内的上部炉料进行预热和还原。
7.由此,通过上述工艺加热后得到的高温还原气从风口和炉身通入富氢碳循环高炉内。首先,从位于炉缸处的风口通入的高温还原气与烟气混合促进煤气燃烧, 同时降低风口回旋区理论燃烧温度;其次,从位于炉身处的煤气通入的热还原气可以对高炉上部炉料预热,改善氧气高炉内部热分布。富氢碳循环高炉以纯氧代替传统高炉热风,即排除了空气中占79%体积的n2,炉腹处煤气量相比传统高炉显著减少,因此降低了炉料透气性要求,连同富氢碳循环高炉内煤气还原势大幅提高,可使冶炼强度及生产效率大幅提高。
附图说明
8.图1为本发明富氢碳循环高炉工艺示意图。
9.其中:1-加料系统,2-富氢碳循环高炉,3-炉身加热煤气入口,4-炉身加热煤气环管,5-煤气重力除尘装置,6-煤气精细除尘装置,7-煤气脱水装置,8-调压阀组,9-并网煤气管道,10-炉顶煤气循环脱碳装置,11-欧冶炉煤气脱碳装置,12-焦炉煤气系统,13-炉身煤气加热系统,14-风口煤气加热系统,15-风口加热煤气环管,16-复合风口装置,l1-复合风口装置16与炉身加热煤气入口3之间的距离,l2-炉身加热煤气入口3与炉顶的距离,β-上部提质煤气入口与炉身外壁下部的夹角。
具体实施方式
10.下面详细描述本发明的实施例,所述实施例的示例在附图中示出,下面通过参考附图描述的实施例是示例性的,旨在用于解释本发明。
11.一种富氢碳循环高炉的炼铁系统,包括:富氢碳循环高炉2、煤气炉顶循环脱碳装置10、欧冶炉煤气脱碳装置11,焦炉煤气系统12;其中,富氢碳循环高炉2所使用的原燃料由加料系统1通过称量后由传输带及料车运输至炉顶,加入炉内,富氢碳循环高炉2用于炼铁,以便得到合格的铁水,并产生炉渣和高炉炉顶粗煤气;除尘装置5、6分别对高炉炉顶的粗煤气进行粗除尘和精细除尘,进行除尘处理,含尘处理后通过煤气脱水装置7脱水后进入调压阀组8调整富氢碳循环高炉的炉顶压力;
经过含尘处理的煤气一部分经过炉顶煤气循环脱碳装置10之后分成2路,一路经过风口煤气加热系统14,煤气温度加热到1100-1200℃,在富氢碳循环高炉炉缸上环形设置有氧气风口、喷煤气口的复合风口装置16,送入风口加热煤气环管15,由环管分配加热煤气至14个复合风口装置16,与氧气同时送入炉内;另一路经过炉身煤气加热系统13,煤气温度加热到850-950℃,在富氢碳循环高炉炉身中下部设置有炉身加热煤气环管4,由环管分配加热煤气设有14个炉身加热煤气入口3,喷口内径φ100mm,喷吹能力20000nm3/h,压力0.35mpa,喷吹管道承压按0.6mpa,钢壳材质采用耐热钢q355r,通过冷却壁错台形成喷吹环道向炉内喷吹渗透热煤气;所述的炉身加热煤气入口3与所述复合风口装置16煤气入口之间的距离为l1,炉身加热煤气入口3与炉顶的距离为l2,其中l1:l2为6.5:8.2,所述炉身加热煤气入口3与炉身外壁下部的夹角为β,所述β的夹角度数范围为112~130
°
。
12.经过含尘处理的煤气另一部分由于富氢碳循环高炉为全氧系统,鼓风中没有n2,但是安保联锁系统需要n2安保,为了消除n2富集,部分煤气并入并网煤气管道9。
实施例
13.参考图1,富氢碳循环高炉的生产系统具体为:1) 富氢碳循环高炉炼铁的工艺系统包括富氢碳循环高炉和炉顶煤气循环脱碳及加热喷吹系统,在富氢碳循环高炉炉缸上环形设置有氧气风口、喷煤气口的复合风口装置,在高炉炉身中下部设置有炉身加热煤气入口,喷吹煤气压力0.35mpa(表压),温度850~950℃。
14.所述复合风口装置用于鼓入纯氧和风口加热煤气,风口加热煤气、炉身加热煤气入口用于鼓入从炉顶循环脱除co2后采用电加热的形式产生的高温提质煤气,所述高温提质煤气入高炉的温度为炉身为950℃,风口为1200℃。
15.所述富氢碳循环高炉顶气循环量不足时可将欧冶炉煤气通过脱碳后,通过压缩机及煤气管道汇入富氢炉的炉顶煤气循环管道,通过加热后喷入富氢碳循环高炉内部。所述富氢碳循环高炉顶气循环量不足时可将焦炉煤气,通过压缩机及煤气管道汇入富氢炉的炉顶煤气循环管道,通过加热后喷入富氢碳循环高炉内部。
16.富氢碳循环高炉生产技术指标如下:炉料结构:不使用块矿炉料结构:(烧结矿:球团=54%:46%), 使用块矿炉料结构:(烧结矿:球团矿:块矿=50%:47%:3%),使用现有的八钢自产烧结矿碱度r=1.75倍
±
0.05。二元碱度b2=cao/sio2=1.03-1.10。
17.下部风口煤气的操作工艺参数:脱碳还原气入口压力:0.6mpa(g),入口温度:40℃,流量:0-45000nm3/h。
18.焦炉煤气入口压力:0.8mpa(g),入口温度:40℃,流量:0-30000nm3/h。
19.混合煤气出口压力:0.4~0.5mpa,出口温度:1200℃,流量:55000nm3/h。
20.上部炉身煤气的操作工艺参数:脱碳还原气入口压力:0.6mpa(g),入口温度:40℃,流量:10000-20000nm3/h。
21.焦炉煤气入口压力:0.8mpa(g),入口温度:40℃,流量:0-10000nm3/h。
22.加热后混合气:出口压力:0.35mpa(g),出口温度:850~950℃,20000nm3/h。
再多了解一些
本文用于企业家、创业者技术爱好者查询,结果仅供参考。