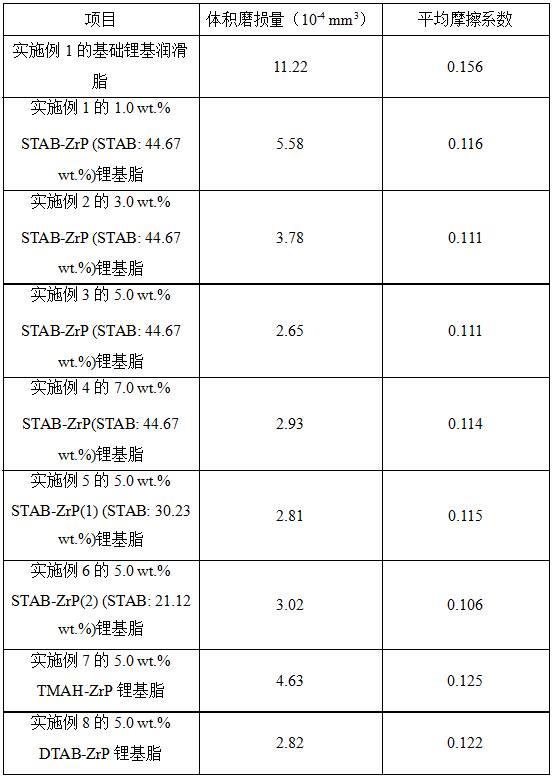
1.本发明属于润滑脂添加剂技术领域,具体涉及一种润滑脂添加剂及其复配体系、以及其承载能力和抗磨减摩性能。
背景技术:
2.随着现代工业技术的不断发展,越来越多的机械设备需要在苛刻的工况条件下(例如高速重载、低速重载、高温或强冲击等)运行。在这些苛刻条件下,机械设备常会发生过度磨损,严重时甚至会卡咬,对设备造成灾难性的损坏。为了有效地阻止这一现象的发生,需要在润滑剂中添加固体添加剂和极压剂。这是因为在摩擦过程中,润滑剂会改变摩擦副表面的状况。对于含有固体添加剂和极压剂的润滑脂,摩擦副表面主要存在油膜、固体物理膜和化学反应膜三种保护膜。油膜对润滑脂的承载力提高有限;固体添加剂通常为具有微米尺寸的晶体,能够提供额外的物理保护,提高润滑剂的承载力;有机极压剂与摩擦副表面的金属元素发生化学反应,形成纳米尺寸的化学保护膜,可以提高润滑剂的烧结负荷。因此在苛刻工况下,一个优良的润滑剂体系需要两种类型添加剂的协同作用,摩擦副表面同时存在反应型化学保护膜与固体物理保护膜,使得润滑剂具有更高的极压性能,从而实现对机械设备的保护。
3.层状磷酸锆材料α-zrp(分子式:zr(hpo4)2·
h2o)具有良好的热稳定性、化学稳定性和机械强度,α-zrp的层板由zro6八面体和hpo4四面体构成,hpo4四面体将zr原子夹在中间,分布在zro6八面体两侧,层板间的作用力是氢键和范德华力,属于典型的层状化合物材料,α-zrp作为润滑油脂固体添加剂表现出优良的承载力和抗磨性能。
4.针对苛刻工况,单独使用有机含硫极压剂,虽然可以大幅提高润滑脂的极压性能,特别是烧结负荷;但高的活性硫含量会造成摩擦副接触表面的过度腐蚀,削弱了润滑剂的抗磨损性能。固体添加剂α-zrp与极压剂复配后,虽然润滑剂保持了良好的抗磨性能,但极压能力的提高有限。研究发现,在运行过程中,α-zrp颗粒粘附在摩擦副表面形成了致密的物理保护膜,阻碍了有机极压剂与摩擦副表面形成化学保护膜,造成两种添加剂不能形成良好的协同增效作用。因此,急需合成能够提供物理保护但不形成致密的物理保护膜的晶体材料,从而获得能够与极压剂化学保护膜形成协同作用的润滑体系。
技术实现要素:
5.本发明旨在提供一种润滑脂复配添加剂及其制成的润滑脂组合物,用本发明制备的润滑脂加入复配添加剂的组合物得到的润滑脂,同时具备优良的极压、抗磨性能,防锈性能和抗氧化性等多方面的性能。
6.本发明中的有机碱插层磷酸锆化合物包含有机胺插层磷酸锆、单长链有机铵插层磷酸锆和双长链有机铵插层磷酸锆。
7.进一步地,有机胺插层磷酸锆包含甲胺插层磷酸锆、丁胺插层磷酸锆、苯胺插层磷酸锆、十二胺插层磷酸锆dda-zrp、乙二胺插层磷酸锆;单长链有机铵插层磷酸锆包含四甲
基氢氧化铵插层磷酸锆tmah-zrp、十二烷基三甲基溴化铵插层磷酸锆dtab-zrp、十四烷基三甲基溴化铵插层磷酸锆mtab-zrp、十六烷基三甲基溴化铵插层磷酸锆ctab-zrp和十八烷基三甲基溴化铵插层磷酸锆stab-zrp;双长链有机铵插层磷酸锆包含双十二烷基二甲基溴化铵插层磷酸锆、双十四烷基二甲基溴化铵插层磷酸锆、双十六烷基二甲基溴化铵插层磷酸锆和双十八烷基二甲基溴化铵插层磷酸锆ddab-zrp。所述有机碱插层磷酸锆优选单长链有机铵插层磷酸锆,优选四甲基氢氧化铵插层磷酸锆tmah-zrp、十二烷基三甲基溴化铵插层磷酸锆dtab-zrp和十八烷基三甲基溴化铵插层磷酸锆stab-zrp。
8.单长链有机铵插层磷酸锆和双长链有机铵插层磷酸锆的制备方法如下:按照质量比α-zrp(zr(hpo4)2·
h2o):蒸馏水(h2o)= 1 : 150称取α-zrp,混合后,在常温下均匀搅拌,然后按照摩尔比甲胺(ch5n):α-zrp(zr(hpo4)2·
h2o)= 1 : 1的比例加入甲胺,常温下搅拌24小时,得到甲胺预插层的磷酸锆悬浮液;接着按照摩尔比单长链有机铵或双长链有机铵:α-zrp(zr(hpo4)2·
h2o)= 0.2 ~ 1.0称取单长链有机铵或双长链有机铵加入到甲胺预插层的α-zrp悬浮液中,在常温下搅拌24小时,产物经离心分离、蒸馏水洗涤后,在室温下干燥风干,得到单长链有机铵插层磷酸锆或双长链有机铵插层磷酸锆,粒径大小为0.6 ~ 1.0 μm。
9.有机胺插层磷酸锆的制备方法如下:按照质量比α-zrp(zr(hpo4)2·
h2o):蒸馏水(h2o)= 1 : 150称取α-zrp,混合后,在常温下均匀搅拌,然后按照摩尔比有机胺:α-zrp(zr(hpo4)2·
h2o)= 1 : 1的比例加入有机胺,常温下搅拌24小时,产物经离心分离、蒸馏水和乙醇洗涤后,在室温下风干,得到有机胺插层磷酸锆,粒径大小为0.6 ~ 1.0 μm。
10.极压剂是在苛刻条件下与金属表面发生化学反应生成具有低剪切强度的化学保护膜,是工业润滑剂中的重要添加剂。极压剂主要包含硫化烯烃、硫化的动物或植物油、硫化芳烃、二硫代氨基甲酸酯、二巯基噻二唑及巯基苯并噻唑衍生物。所述极压剂优选硫化烯烃,优选硫化异丁烯sib。
11.本发明提供了一种由上述润滑脂复配添加剂制成的润滑脂组合物,其包含:基础脂:90.0 ~ 98.0份,有机碱插层磷酸锆化合物:1.0 ~ 7.0份,极压剂:0 ~ 3.0份,防锈剂:0.5 ~ 1.0份;抗氧剂:0.5 ~ 2.0份。
12.进一步地,所述基础脂包括基础油和稠化剂,将稠化剂分散到基础油中获得固体或半流体物质;基础油和稠化剂的质量比为8 ~ 10:1。
13.所述稠化剂包含锂皂、复合锂皂、复合锂钙皂或钙皂。
14.通常,用于制备本发明润滑脂的基础油可以是矿物油、合成油、费托合成衍生的基础油、煤焦油衍生的烷基萘基础油、动植物油或其组合。矿物油包括溶剂处理或氢加工生成的链烷烃、环烷烃等。合成油包括聚α烯烃、多元醇酯、聚醚、有机硅油等。它们单独或作为混合油。
15.所述基础脂的制备方法为:在温度为70 ~ 90 ℃下,将一种或两种脂肪酸、小分子酸溶解在部分基础油或基础油混合物中,在上述酸溶解在基础油后,加入金属化合物,随后在温度105 ~ 220 ℃下进行皂化反应,皂化反应结束后,再加入剩余的部分基础油作为降温油,得到基础脂。在已冷却的基础脂中加入所需的复配添加剂和其它添加剂,用三辊机均质化得到润滑脂组合物。
16.所述长链脂肪酸通常碳链长度为14到28个碳原子的长链脂肪酸,优选12-羟基硬脂酸和硬脂酸,短链脂肪酸为碳链长度为6到10个碳原子的短链脂肪酸,优选癸二酸、壬二
酸、苯甲酸中的一种或两种。小分子酸优选醋酸。
17.所述金属化合物优选金属氢氧化物或金属氧化物,优选锂和钙的金属化合物。
18.防锈剂的极性基团优先吸附到金属表面,形成保护膜,防止金属表面腐蚀和锈蚀。防锈剂主要包含十二烯基丁二酸t746、石油磺酸钡、石油磺酸钠、二壬基奈磺酸钡、二壬基奈磺酸锌、二壬基奈磺酸钙、十二烯基丁二胺、苯并三氮唑、亚硝酸钠、磷酸三钠,优选十二烯基丁二酸t746。
19.抗氧剂能够中断氧化初期的自由链反应或分解过氧化物,终止自由基反应,从而延缓润滑油的氧化。常见的抗氧剂有二苯胺、二异辛基二苯胺、酚类抗氧剂、有机硒化物、2,6-二叔丁基-4-甲基苯酚bht,优选2,6-二叔丁基-4-甲基苯酚bht。
20.本发明的有益效果:(1)本发明将有机碱插层磷酸锆化合物与极压剂组合作为润滑脂添加剂组合物的主要组分表现出优异的复合增效性,尤其在极压性能和稳定的抗磨性能方面。
21.(2)本发明在分析了固体添加剂和有机极压剂在摩擦副表面的形成状态,巧妙地设计和制备了有机碱插层磷酸锆化合物,改善了磷酸锆化合物在摩擦副表面粘附的状态,实现了与极压剂复合的增效性能。
22.(3)本发明添加剂组合物结合了固体添加剂和有机极压剂的优点,揭示了有机碱插层磷酸锆和极压剂的复配增效性机理,即摩擦副表面同时存在亚微米尺寸的插层磷酸锆物理保护膜和纳米尺寸的极压剂化学保护膜的双重保护,提高了润滑脂的极压性能,保证了稳定的抗磨性能,有效地延长了设备的使用寿命。
23.(4)该润滑脂添加剂组合物具有优良的极压、抗磨、防锈和抗氧功能,可以满足多种工况的需求。
具体实施方式
24.下面通过实施例来进一步说明本发明,但不局限于以下实施例。
25.实施例1stab-zrp化合物的制备方法:按照质量比α-zrp(zr(hpo4)2·
h2o):蒸馏水(h2o)= 1 : 150称取α-zrp,混合后,在常温下均匀搅拌,然后按照摩尔比甲胺(ch5n):α-zrp(zr(hpo4)2·
h2o)= 1 : 1的比例加入甲胺,常温下搅拌24小时,得到甲胺预插层的磷酸锆悬浮液;接着按照摩尔比stab(c
21h46
brn):α-zrp(zr(hpo4)2·
h2o)= 1 : 1称取stab加入到甲胺预插层的α-zrp悬浮液中,在常温下搅拌24小时,产物经离心分离、蒸馏水洗涤后,在室温下干燥风干,利用用x射线衍射仪(xrd)进行晶体结构的表征,利用c、h、n元素分析对层间有机物含量进行表征,获得层间有机物含量为44.67 wt.%的stab-zrp,粒径大小为0.6 ~ 1.0 μm。
26.基础锂基润滑脂制备方法如下:将计量40%的基础油和脂肪酸依次倒入制脂釜中,启动搅拌器,升温至70 ~ 80 ℃,待脂肪酸在基础油中完全溶解后,再加入预先制备好的氢氧化锂溶液(h2o与lioh
·
h2o质量比为1.25 : 1),并升温至120 ~ 130 ℃,反应2 ~ 3 h;皂化结束后,加入计量30%的基础油,温度升至200 ~ 220 ℃,恒温10 ~ 15 min后,停止加热;当温度降到170 ~ 190 ℃时,加入剩余计量30%的基础油,温度降至100 ℃时,停止搅拌。待润滑脂冷却后,在三辊机研磨3次后得到基础锂基润滑脂。进一步地,所述脂肪酸为硬脂酸
和12-羟基硬脂酸的混合物,其中硬脂酸与12-羟基硬脂酸的摩尔比为1 : 4。
27.在98.0 g基础锂基润滑脂中加入1.0 g stab-zrp (stab: 44.67 wt.%)、0.5 g t746、和0.5 g bht作为润滑脂添加剂,利用三辊研磨机滚动研磨3遍,使得添加剂在基础锂基润滑脂中混合均匀,得到含有1.0 wt.% stab-zrp (stab: 44.67 wt.%)的锂基润滑脂产品(简写为1.0 wt.% stab-zrp (stab: 44.67 wt.%)锂基脂)。
28.采用srv-v摩擦磨损试验机,对所制得润滑脂产品进行抗磨减摩性能表征。载荷200 n,频率50 hz,步长1 mm,温度80 ℃,时间30 min。数据见表1。
29.实施例2采用实施例1中制备的stab-zrp (stab: 44.67 wt.%);基础锂基润滑脂制备同实施例1;在94.5 g基础锂基润滑脂中加入3.0 g stab-zrp (stab: 44.67 wt.%)、0.5 g t746和2.0 g bht作为润滑脂添加剂,利用三辊研磨机滚动研磨3遍,使得添加剂在基础锂基润滑脂中混合均匀,得到含有3.0 wt.% stab-zrp (stab: 44.67 wt.%)的锂基润滑脂产品(简写为3.0 wt.% stab-zrp (stab: 44.67 wt.%)锂基脂)。
30.采用srv-v摩擦磨损试验机,对所制得润滑脂产品进行抗磨减摩性能表征。载荷200 n,频率50 hz,步长1 mm,温度80 ℃,时间30 min。数据见表1。
31.实施例3采用实施例1中制备的stab-zrp (stab: 44.67 wt.%);基础锂基润滑脂制备同实施例1;在93.0 g基础锂基润滑脂中加入5.0 g stab-zrp (stab: 44.67 wt.%)、1.0 g t746和1.0 g bht作为润滑脂添加剂,利用三辊研磨机滚动研磨3遍,使得添加剂在基础锂基润滑脂中混合均匀,得到含有5.0 wt.% stab-zrp (stab: 44.67 wt.%)的锂基润滑脂产品(简写为5.0 wt.% stab-zrp (stab: 44.67 wt.%)锂基脂)。
32.采用srv-v摩擦磨损试验机,对所制得润滑脂产品进行抗磨减摩性能表征。频率50 hz,步长1 mm,温度80 ℃,时间30 min。数据见表1、2。
33.实施例4采用实施例1中制备的stab-zrp (stab: 44.67 wt.%);基础锂基润滑脂制备同实施例1;在90.0 g基础锂基润滑脂中加入7.0 g stab-zrp (stab: 44.67 wt.%)、1.0 g t746和2.0 g bht作为润滑脂添加剂,利用三辊研磨机滚动研磨3遍,使得添加剂在基础锂基润滑脂中混合均匀,得到含有7.0 wt.% stab-zrp (stab: 44.67 wt.%)的锂基润滑脂产品(简写为7.0 wt.% stab-zrp (stab: 44.67 wt.%)锂基脂)。
34.采用srv-v摩擦磨损试验机,对所制得润滑脂产品进行抗磨减摩性能表征。载荷200 n,频率50 hz,步长1 mm,温度80 ℃,时间30 min。数据见表1。
35.实施例5stab-zrp(1)化合物的制备方法:按照质量比α-zrp(zr(hpo4)2·
h2o):蒸馏水(h2o)= 1 : 150称取α-zrp,混合后,在常温下均匀搅拌,然后按照摩尔比甲胺(ch3nh2):α-zrp(zr(hpo4)2·
h2o)= 1 : 1的比例加入甲胺,常温下搅拌24小时,得到甲胺预插层的磷酸锆悬浮液;接着按照摩尔比stab(c
21h46
brn):α-zrp(zr(hpo4)2·
h2o)= 0.4 : 1称取stab加
入到甲胺预插层的α-zrp悬浮液中,在常温下搅拌24小时,产物经离心分离、蒸馏水洗涤后,在室温下干燥风干,利用x射线衍射仪(xrd)进行晶体结构的表征,利用c、h、n元素分析对层间有机物含量进行表征,获得层间有机物含量为30.23 wt.%的stab-zrp(1),粒径大小为0.6 ~ 1.0 μm。
36.基础锂基润滑脂制备同实施例1;在93.0 g基础锂基润滑脂中加入5.0 g stab-zrp(1) (stab: 30.23 wt.%)、1.0 g t746和1.0 g bht作为润滑脂添加剂,利用三辊研磨机滚动研磨3遍,使得添加剂在基础锂基润滑脂中混合均匀,得到含有5.0 wt.% stab-zrp(1) (stab: 30.23 wt.%)的锂基润滑脂产品(简写为5.0 wt.% stab-zrp(1) (stab: 30.23 wt.%)锂基脂)。
37.采用srv-v摩擦磨损试验机,对所制得润滑脂产品进行承载力和抗磨减摩性能表征。频率50 hz,步长1 mm,温度80 ℃,时间30 min。数据见表1、2。
38.实施例6stab-zrp(2)化合物的制备方法:按照质量比α-zrp(zr(hpo4)2·
h2o):蒸馏水(h2o)=1 : 150称取α-zrp,混合后,在常温下均匀搅拌,然后按照摩尔比甲胺(ch5n):α-zrp(zr(hpo4)2·
h2o)= 1 : 1的比例加入甲胺,常温下搅拌24小时,得到甲胺预插层的磷酸锆悬浮液;接着按照摩尔比stab(c
21h46
brn):α-zrp(zr(hpo4)2·
h2o)= 0.2 : 1称取stab加入到甲胺预插层的α-zrp悬浮液中,在常温下搅拌24小时,产物经离心分离、蒸馏水洗涤后,在室温下干燥风干,利用x射线衍射仪(xrd)进行晶体结构的表征,利用c、h、n元素分析对层间有机物含量进行表征,获得层间有机物含量为21.12 wt.%的stab-zrp,粒径大小为0.6 ~ 1.0 μm。
39.基础锂基润滑脂制备同实施例1;在93.0 g基础锂基润滑脂中加入5.0 g stab-zrp(2) (stab: 21.12 wt.%)、1.0 g t746和1.0 g bht作为润滑脂添加剂,利用三辊研磨机滚动研磨3遍,使得添加剂在基础锂基润滑脂中混合均匀,得到含有5.0 wt.% stab-zrp(2) (stab: 21.12 wt.%)的锂基润滑脂产品(简写为stab-zrp(2) (stab: 21.12 wt.%)锂基脂)。
40.采用srv-v摩擦磨损试验机,对所制得润滑脂产品进行承载力和抗磨减摩性能表征。频率50 hz,步长1 mm,温度80 ℃,时间30 min。数据见表1、2。
41.实施例7tmah-zrp化合物的制备方法:按照质量比α-zrp(zr(hpo4)2·
h2o):蒸馏水(h2o)= 1 : 150称取α-zrp,混合后,在常温下均匀搅拌,然后按照摩尔比四甲基氢氧化铵(c4h
13
no):α-zrp(zr(hpo4)2·
h2o)= 1 : 1的比例加入四甲基氢氧化铵,常温下搅拌24小时,在常温下搅拌24小时,产物在室温下风干,用x射线衍射仪(xrd)进行晶体结构的表征,利用c、h、n元素分析对层间有机物含量进行表征,获得层间有机物含量为13.94 wt.%的tmah-zrp,粒径大小为0.6 ~ 1.0 μm。
42.基础锂基润滑脂制备同实施例1;在93.0 g基础锂基润滑脂中加入5.0 g tmah-zrp、1.0 g t746和1.0 g bht作为润滑脂添加剂,利用三辊研磨机滚动研磨3遍,使得添加剂在基础锂基润滑脂中混合均匀,得到含有5.0 wt.% tmah-zrp的锂基润滑脂产品(简写为5.0 wt.% tmah-zrp锂基脂)。
43.采用srv-v摩擦磨损试验机,对所制得润滑脂产品进行承载力和抗磨减摩性能表
征。频率50 hz,步长1 mm,温度80 ℃,时间30 min。数据见表1、2。
44.实施例8dtab-zrp化合物的制备方法:按照质量比α-zrp(zr(hpo4)2·
h2o):蒸馏水(h2o)= 1 : 150称取α-zrp,混合后,在常温下均匀搅拌,然后按照摩尔比甲胺(ch5n):α-zrp(zr(hpo4)2·
h2o)= 1 : 1的比例加入甲胺,常温下搅拌24小时,得到甲胺预插层的磷酸锆悬浮液;接着按照摩尔比dtab(c
15h34
brn):α-zrp(zr(hpo4)2·
h2o)= 1 : 1称取dtab加入到甲胺预插层的α-zrp悬浮液中,在常温下搅拌24小时,产物经离心分离、蒸馏水洗涤后,在室温下风干,利用x射线衍射仪(xrd)进行晶体结构的表征,利用c、h、n元素分析对层间有机物含量进行表征,获得层间有机物含量为30.47 wt.%的dtab-zrp,粒径大小为0.6 ~ 1.0 μm。
45.基础锂基润滑脂制备同实施例1;在93.0 g基础锂基润滑脂中加入5.0 g dtab-zrp、1.0 g t746和1.0 g bht作为润滑脂添加剂,利用三辊研磨机滚动研磨3遍,使得添加剂在基础锂基润滑脂中混合均匀,得到含有5.0 wt.% dtab-zrp的锂基润滑脂产品(简写为5.0 wt.% dtab-zrp锂基脂)。
46.采用srv-v摩擦磨损试验机,对所制得润滑脂产品200 n运行载荷下进行承载力和抗磨减摩性能表征。频率50 hz,步长1 mm,温度80 ℃,时间30 min。数据见表1、2。表1列出了实施例1~8所得产品的润滑数据。
47.表1 锂基脂润滑数据
从表1可以看出,随着stab-zrp添加量的增加,stab-zrp锂基脂的体积磨损量明显降低,当添加量为5.0 wt.%时,体积磨损量达到最低,添加量对平均摩擦系数的影响较小。对比研究了添加量为5.0 wt.% stab-zrp (stab: 44.67 wt.%)锂基脂、5.0 wt.% stab-zrp (stab: 30.23 wt.%)锂基脂和5.0 wt.% stab-zrp (stab: 21.12 wt.%)锂基脂的摩擦学性能。可以看出,在相同添加量下,stab含量最高的stab-zrp (stab: 44.67 wt.%)锂基脂的体积磨损量最低,表明层间有机铵含量越高,体积磨损量越低。对于不同碳链长度的
有机铵插层磷酸锆材料,tmah-zrp锂基脂的体积磨损量明显高于dtab-zrp锂基脂和stab-zrp锂基脂,dtab-zrp锂基脂的体积磨损量略高于stab-zrp锂基脂。可见,有机铵插层磷酸锆作为固体添加剂改善了基础脂的润滑性能,层间有机铵含量越高,体积磨损量越低;层间有机铵碳链长度对体积磨损量有影响,碳链长度越长体积磨损量越低。
48.实施例9采用实施例7中制备的tmah-zrp;基础锂基润滑脂制备同实施例1;在91.5 g基础锂基润滑脂中加入5.0 g tmah-zrp、0.5 g t746、1.0 g bht和2.0 g sib作为润滑脂添加剂,利用三辊研磨机滚动研磨3遍,使得添加剂在基础锂基润滑脂中混合均匀,得到含有5.0 wt.% tmah-zrp和2.0 wt.% sib的锂基润滑脂产品(简写为tmah-zrp/sib锂基脂)。
49.采用srv-v摩擦磨损试验机,对所制得润滑脂产品进行承载力和抗磨性能表征。频率50 hz,步长1 mm,温度80 ℃,时间30 min。数据见表2。
50.实施例10采用实施例8中制备的dtab-zrp;基础锂基润滑脂制备同实施例1;在91.5 g基础锂基润滑脂中加入5.0 g dtab-zrp、0.5 g t746、1.0 g bht和2.0 g sib作为润滑脂添加剂,利用三辊研磨机滚动研磨3遍,使得添加剂在基础锂基润滑脂中混合均匀,得到含有5.0 wt.% dtab-zrp和2.0 wt.% sib的锂基润滑脂产品(简写为dtab-zrp/sib锂基脂)。
51.采用srv-v摩擦磨损试验机,对所制得润滑脂产品进行承载力和抗磨性能表征。频率50 hz,步长1 mm,温度80 ℃,时间30 min。数据见表2。
52.实施例11采用实施例1中制备的stab-zrp (stab: 44.67 wt.%);基础锂基润滑脂制备同实施例1;在91.5 g基础锂基润滑脂中加入5.0 g stab-zrp、0.5 g t746、1.0 g bht和2.0 g sib作为润滑脂添加剂,利用三辊研磨机滚动研磨3遍,使得添加剂在基础锂基润滑脂中混合均匀,得到含有5.0 wt.% stab-zrp和2.0 wt.% sib的锂基润滑脂产品(简写为stab-zrp/sib (stab: 44.67 wt.%)锂基脂)。
53.采用srv-v摩擦磨损试验机,对所制得润滑脂产品进行承载力和抗磨性能表征。频率50 hz,步长1 mm,温度80 ℃,时间30 min。数据见表2。
54.实施例12采用实施例5中制备的stab-zrp(1) (stab: 30.23 wt.%);基础锂基润滑脂制备同实施例1;在91.5 g基础锂基润滑脂中加入5.0 g stab-zrp(1) (stab: 30.23 wt.%)、0.5 g t746、1.0 g bht和2.0 g sib作为润滑脂添加剂,利用三辊研磨机滚动研磨3遍,使得添加剂在基础锂基润滑脂中混合均匀,得到含有5.0 wt.% stab-zrp(1) (stab: 30.23 wt.%)和2.0 wt.% sib的锂基润滑脂产品(简写为stab-zrp(1)/sib (stab: 30.23 wt.%)锂基脂)。
55.采用srv-v摩擦磨损试验机,对所制得润滑脂产品进行承载力和抗磨性能表征。频率50 hz,步长1 mm,温度80 ℃,时间30 min。数据见表2。
56.实施例13采用实施例6中制备的stab-zrp(2) (stab: 21.12 wt.%);基础锂基润滑脂制备同实施例1;在91.5 g基础锂基润滑脂中加入5.0 g stab-zrp(2) (stab: 21.12 wt.%)、0.5 g t746、1.0 g bht和2.0 g sib作为润滑脂添加剂,利用三辊研磨机滚动研磨3遍,使得添加剂在基础锂基润滑脂中混合均匀,得到含有5.0 wt.% stab-zrp(2)和2.0 wt.% sib的锂基润滑脂产品(简写为stab-zrp(2)/sib (stab: 21.12 wt.%)锂基脂)。
57.采用srv-v摩擦磨损试验机,对所制得润滑脂产品进行承载力和抗磨性能表征。频率50 hz,步长1 mm,温度80 ℃,时间30 min。数据见表2。
58.实施例14dda-zrp化合物的制备方法:按照质量比α-zrp(zr(hpo4)2·
h2o):蒸馏水(h2o)=1: 150称取α-zrp,混合后,在常温下均匀搅拌,然后按照摩尔比十二胺(c
12h27
n):α-zrp(zr(hpo4)2·
h2o)= 1 : 1的比例加入十二胺,常温下搅拌24小时,产物经离心分离、蒸馏水和乙醇洗涤后,在室温下风干,利用x射线衍射仪(xrd)进行晶体结构的表征,得到dda-zrp,粒径大小为0.6 ~ 1.0 μm。
59.实施例15ddab-zrp化合物的制备方法:按照质量比α-zrp(zr(hpo4)2·
h2o):蒸馏水(h2o)= 1 : 150称取α-zrp,混合后,在常温下均匀搅拌,然后按照摩尔比甲胺(ch3nh2):α-zrp(zr(hpo4)2·
h2o)= 1 : 1的比例加入甲胺,常温下搅拌24小时,得到甲胺预插层的磷酸锆悬浮液;接着按照摩尔比ddab(c
38h80
brn):α-zrp(zr(hpo4)2·
h2o)= 1 : 1称取ddab加入到甲胺预插层的α-zrp悬浮液中,在常温下搅拌24小时,产物经离心分离、蒸馏水和乙醇洗涤后,在室温下干燥风干,利用x射线衍射仪(xrd)进行晶体结构的表征,得到ddab-zrp,粒径大小为0.6 ~ 1.0 μm。
60.对比例1基础锂基润滑脂制备同实施例1;在93.0 g基础锂基润滑脂中加入5.0 g α-zrp、1.0 g t746和1.0 g bht作为润滑脂添加剂,利用三辊研磨机滚动研磨3遍,使得添加剂在基础锂基润滑脂中混合均匀,得到含有5.0 wt.% α-zrp的锂基润滑脂产品(简写为5.0 wt.% α-zrp锂基脂)。
61.采用srv-v摩擦磨损试验机,对所制得润滑脂产品进行承载力和抗磨性能表征。频率50 hz,步长1 mm,温度80 ℃,时间30 min。数据见表2。
62.对比例2基础锂基润滑脂制备同实施例1;在91.5 g基础锂基润滑脂中加入5.0 g α-zrp、0.5 g t746、1.0 g bht和2.0 g sib作为润滑脂添加剂,利用三辊研磨机滚动研磨3遍,使得添加剂在基础锂基润滑脂中混合均匀,得到含有5.0 wt.% α-zrp和2.0 wt.% sib的锂基润滑脂产品(简写为α-zrp/sib锂基脂)。
63.采用srv-v摩擦磨损试验机,对所制得润滑脂产品进行承载力和抗磨性能表征。频
率50 hz,步长1 mm,温度80 ℃,时间30 min。数据见表2。
64.对比例3基础锂基润滑脂制备同实施例1;在96.5 g基础锂基润滑脂中加入0.5 g t746、1.0 g bht和2.0 g sib作为润滑脂添加剂,利用三辊研磨机滚动研磨3遍,使得添加剂在基础锂基润滑脂中混合均匀,得到含有2.0 wt.% sib的锂基润滑脂产品(简写为sib锂基脂)。
65.采用srv-v摩擦磨损试验机,对所制得润滑脂产品进行承载力和抗磨性能表征。频率50 hz,步长1 mm,温度80 ℃,时间30 min。数据见表2。表2 列出了对比例1~3、实施例3、5~13所得产品复配性能的润滑数据。
66.表2 产品复配性能的数据对比
表2为复配润滑脂的对比润滑数据。可以看出,与sib复配后,α-zrp/sib锂基脂的最高运行载荷没有增加,而tmah-zrp/sib锂基脂、dtab-zrp/sib锂基脂和stab-zrp/sib锂基脂的最高运行载荷分别增加了100 n、400 n和500 n;在抗磨性能方面,长碳链dtab-zrp/sib锂基脂和stab-zrp/sib锂基脂的抗磨性能优于短碳链tmah-zrp/sib锂基脂。层间有机
铵碳链越长,复配增效性越明显。
67.层间不同有机物含量的stab-zrp/sib (stab: 44.67 wt.%)锂基脂、stab-zrp(1)/sib (stab: 30.23 wt.%)锂基脂和stab-zrp(2)/sib (21.12 wt.%)锂基脂复配性能的润滑数据表明,stab-zrp/sib (stab: 44.67 wt.%)锂基脂、stab-zrp(1)/sib (stab: 30.23 wt.%)锂基脂和stab-zrp(2)/sib (21.12 wt.%)锂基脂的最高运行载荷分别增加了300 n、400 n和500 n,stab-zrp/sib (stab: 44.67 wt.%)锂基脂具有更好的抗磨性能,层间有机物含量越高,复配增效性越明显。
再多了解一些
本文用于企业家、创业者技术爱好者查询,结果仅供参考。