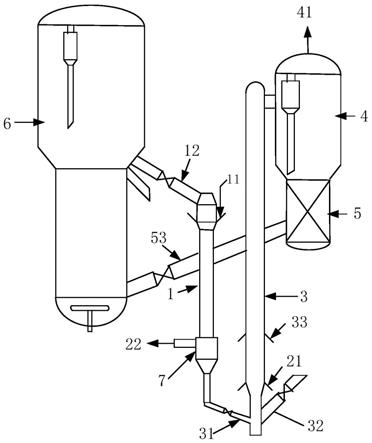
一种原油催化裂解生产低碳烯烃和btx的方法
技术领域
1.本技术涉及石油炼制及石油化工加工过程,具体地,涉及一种全馏分原油催化裂解生产低碳烯烃和btx的方法。
背景技术:
2.随着成品油消费量增速的持续放缓,低碳烯烃以及芳烃等基本有机原料需求量的高速增长,化工料型炼厂成为未来的发展趋势。目前化工型炼厂的构型主要包括以下三种,一是原油通过溶剂脱沥青或加氢精制等预处理后,直接进入蒸汽裂解单元生产化工料,但这种方式一般仅限于轻质原油;二是通过原油各馏分加氢裂化后,最大化生成重质石脑油,然后通过重整单元最大化生产芳烃;三是原油的轻馏分进入蒸汽裂解单元,重馏分进入催化裂解单元,最大化生产低碳烯烃。以上三种方式均已实现工业化,化学品的收率在35%-55%之间。可以看出,现有化工型炼厂的构型主要依托蒸汽裂解、重整、加氢精制、加氢裂化、催化裂解等多套核心装置的组合。而催化裂解工艺在生产化工料和原料适应性方面具有其独特的优势,可同时生产丙烯、乙烯和btx。
3.中国专利cn1978411公开了一种制取小分子烯烃的组合工艺方法,该方法将催化裂化催化剂和裂化原料在一个反应器中混合接触,分离待生催化剂和反应油气,其中待生催化剂送入再生器进行烧焦再生,再生后的热催化剂分为两部分,其中一部分再生后的热催化剂返回上述反应器;另一部分再生后的热催化剂先和重质石油烃类在另外一个反应器中混合接触,进行预结焦,富含c4-c8的烯烃原料再和结焦的催化剂混合接触,发生催化裂解反应,分离待生催化剂反应油气,该待生催化剂与上步中所述待生催化剂送入再生器进行烧焦再生;分离反应油气得到丙烯等小分子烯烃目的产品。该方法可将富含烯烃的轻质原料高选择性地转化为丙烯等小分子烯烃产物,同时维持装置自身的热平衡。
4.中国专利cn102899078a公开了一种生产丙烯的催化裂化方法,该方法基于双提升管与流化床构成的组合反应器,首先将重质原料油与第一股催化剂引入第一提升管反应器进行反应,油剂分离后进入分离系统。将裂解重油引入第二提升管反应器与引入第二提升管反应器的催化剂接触反应,将轻质烃引入第二提升管反应器,与裂解重油和第二股裂化催化剂接触反应形成的混合物接触,所述轻质烃包括产品分离系统得到的c4烃或汽油馏分。然后将第二提升管反应器反应后的油气与催化剂引入流化床反应器反应。通过工艺方案的优化,配备合适的催化剂,对不同进料进行选择性转化,具有较高的丙烯和丁烯产率。
5.中国专利cn101045667公开了一种多产低碳烯烃的组合式催化转化方法,该方法将重油原料在下行管反应器内与再生催化剂和任选的积炭催化剂接触,将分离的除低碳烯烃的其余产物中至少一部分引入提升管反应器与再生催化剂接触反应,提升管反应后催化剂引入下行管反应器催化剂预提升段,与进入下行管反应器的再生催化剂混合后和重油原料接触。该方法采用重油原料在下行式反应器反应,中间产物烯烃在提升管反应器内反应的组合反应器形式,提高低碳烯烃的产率。
6.中国专利cn109370644a公开了一种原油催化裂解制低碳烯烃和芳烃的方法,该方
法将原油分成轻重组分,切割点在150℃-300℃之间,轻馏分和重馏分在同一个反应器不同反应区进行反应,催化剂采用以二氧化硅和三氧化二铝组成的硅铝酸盐为主要组分,包括碱金属氧化物,碱土金属氧化物,钛、铁氧化物,钒和镍的氧化物。该方法是基于重油催化裂解生成低碳烯烃的密相输送床反应器的基础上,针对原油催化裂解生成低碳烯烃提出的解决方案。
7.以上方法从新型反应器结构开发、新型催化材料研制以及控制反应深度提高丙烯选择性等方面进行研究,提出了催化裂解制取低碳烯烃和芳烃的方法,但目前仍没有针对原油最大化生产化工料的专用反应器结构。
技术实现要素:
8.本公开的目的在于针对原油的烃类组成特点,提出一种适于加工原油催化裂解生产低碳烯烃和btx的专用反应器结构及其方法。
9.为了实现上述目的,本公开提供了一种原油催化裂化生产低碳烯烃和轻芳烃的方法,该方法包括如下步骤:
10.s1、将脱盐脱水的原油切割为轻馏分油和重馏分油;所述切割的切割点为100-400℃之间的任意温度;
11.s2、将所述轻馏分油与第一股催化剂引入第一下行式反应器,进行第一催化裂解,得到第一催化裂解后的物料;
12.s3、将所述第一催化裂解后的物料进行气固分离,得到第一反应油气和第一待生催化剂;或者,将所述第一催化裂解后的物料送入流化床反应器进行第二催化裂解,然后进行气固分离,得到第二反应油气和第二待生催化剂;
13.s4、将半待生催化剂、所述重馏分油与第二股催化剂引入第二上行式反应器,进行第三催化裂解,然后进行气固分离,得到第三反应油气和第三待生催化剂;所述半待生催化剂为所述第一待生催化剂或所述第二待生催化剂;所述第二股催化剂与所述半待生催化剂的重量比为0.2-5:1;
14.s5、从所述第一油气和所述第二油气中分离出轻烯烃馏分,并将所述轻烯烃馏分返回所述流化床反应器中或所述第二上行式反应器中。
15.可选地,步骤s1中,所述切割的切割点为200-380℃之间的任意温度。
16.可选地,步骤s4中,所述第二股催化剂与所述半待生催化剂的重量比为0.5-3:1。
17.可选地,所述第一下行式反应器中,所述第一催化裂化的条件包括:所述第一下行式反应器的出口温度为610-720℃,气固停留时间为0.1-3.0秒;所述流化床反应器中,所述第二催化裂化的条件包括:所述流化床反应器中的反应温度为600-670℃,质量空速为2-20h-1
;所述第二上行式反应器中,所述第三催化裂化的条件包括:所述第二上行式反应器的出口温度为530-650℃,气固停留时间为0.5-8秒。
18.优选地,所述第一下行式反应器中,所述第一催化裂化的条件包括:所述第一下行式反应器的出口温度为650-690℃,气固停留时间为0.5-1.5秒;所述流化床反应器中,所述第二催化裂化的条件包括:所述流化床反应器中的反应温度为620-640℃,质量空速为4-12h-1
;所述第二上行式反应器中,所述第三催化裂化的条件包括:所述第二上行式反应器的出口温度为560-640℃,气固停留时间为1.5-5秒。
19.可选地,将所述轻烯烃馏分先于所述重馏分油0.3-1.0秒与所述第二股催化剂进行催化裂解;优选将所述轻烯烃先于所述重馏分油0.4-0.8秒与所述第二股催化剂进行催化裂解。
20.可选地,该方法还包括:将所述第三待生催化剂进行烧焦再生,得到再生催化剂;将所述第一油气和所述第二油气进行分离,得到干气、c3馏分、c4馏分、轻汽油、重汽油、柴油和油浆;所述轻烯烃馏分为所述第一油气和所述第二油气中的c4馏分和/或所述第一油气和所述第二油气中60-90℃范围内的馏分。
21.可选地,所述原油为常规矿物油、煤液化油、合成油、油砂油、页岩油、致密油和动植物油脂中的一种或几种的混合物。
22.可选地,所述第一股催化剂和所述第二股催化剂各自独立地包括活性组分和载体,所述活性组分为选自含或不含稀土的超稳y型沸石、zsp系列沸石、具有五元环结构的高硅沸石和β沸石中的至少一种。
23.可选地,所述第一股催化剂和所述第二股催化剂各自独立地包括所述再生催化剂。
24.通过上述技术方案,本公开提供的原油催化裂化生产低碳烯烃和btx的方法,可以明显提高低碳烯烃和轻芳烃的产率和装置经济性。
25.本公开的其他特征和优点将在随后的具体实施方式部分予以详细说明。
附图说明
26.附图是用来提供对本公开的进一步理解,并且构成说明书的一部分,与下面的具体实施方式一起用于解释本公开,但并不构成对本公开的限制。在附图中:
27.图1是实施例1中原油催化裂化生产低碳烯烃和轻芳烃的装置图。
28.图2是实施例3中原油催化裂化生产低碳烯烃和轻芳烃的装置图。
29.附图标记说明
30.1、下行式反应器
ꢀꢀꢀꢀꢀꢀꢀꢀꢀꢀꢀꢀꢀꢀꢀꢀꢀꢀ
32、第二再生催化剂输送管
31.11、轻馏分油进料喷嘴
ꢀꢀꢀꢀꢀꢀꢀꢀꢀꢀꢀꢀꢀ
33、重馏分油进料喷嘴
32.12、第一再生催化剂输送管
ꢀꢀꢀꢀꢀꢀꢀꢀꢀ
4、沉降器
33.13、蘑菇头分布器
ꢀꢀꢀꢀꢀꢀꢀꢀꢀꢀꢀꢀꢀꢀꢀꢀꢀ
41、上行床反应器油气出口
34.2、流化床反应器
ꢀꢀꢀꢀꢀꢀꢀꢀꢀꢀꢀꢀꢀꢀꢀꢀꢀꢀ
51、第一汽提器
35.21、轻烯烃进料喷嘴
ꢀꢀꢀꢀꢀꢀꢀꢀꢀꢀꢀꢀꢀꢀꢀ
52、第二汽提器
36.22、第一油气出口
ꢀꢀꢀꢀꢀꢀꢀꢀꢀꢀꢀꢀꢀꢀꢀꢀꢀ
53、第二待生催化剂输送管
37.3、上行床反应器
ꢀꢀꢀꢀꢀꢀꢀꢀꢀꢀꢀꢀꢀꢀꢀꢀꢀꢀ
6、再生器
38.31、第一待生催化剂输送管
ꢀꢀꢀꢀꢀꢀꢀꢀꢀ
7、气固分离器
具体实施方式
39.以下对本公开的具体实施方式进行详细说明。应当理解的是,此处所描述的具体实施方式仅用于说明和解释本公开,并不用于限制本公开。
40.本公开提供了一种原油催化裂化生产低碳烯烃和轻芳烃的方法,该方法包括如下步骤:
41.s1、将脱盐脱水的原油切割为轻馏分油和重馏分油;所述切割的切割点为100-400℃之间的任意温度;
42.s2、将所述轻馏分油与第一股催化剂引入第一下行式反应器,进行第一催化裂解,得到第一催化裂解后的物料;
43.s3、将所述第一催化裂解后的物料进行气固分离,得到第一反应油气和第一待生催化剂;或者,将所述第一催化裂解后的物料送入流化床反应器进行第二催化裂解,然后进行气固分离,得到第二反应油气和第二待生催化剂;
44.s4、将半待生催化剂、所述重馏分油与第二股催化剂引入第二上行式反应器,进行第三催化裂解,然后进行气固分离,得到第三反应油气和第三待生催化剂;所述半待生催化剂为所述第一待生催化剂或所述第二待生催化剂;所述第二股催化剂与所述半待生催化剂的重量比为0.2-5:1;
45.s5、从所述第一油气和所述第二油气中分离出轻烯烃馏分,并将所述轻烯烃馏分返回所述流化床反应器中或所述第二上行式反应器中。
46.本公开根据原油不同馏分段的烃类组成特点和裂解反应特性,提供了一种原油催化裂解生产低碳烯烃和btx的方法。通过将脱盐脱水的原油切割为轻馏分油和重馏分油两部分,将轻馏分油在下行式反应器中高温、短停留时间下裂解,可以高选择性生产低碳烯烃和btx,同时可以明显降低甲烷生成。由于轻馏分油生焦较低,反应后催化剂仍具有较高的活性,因此将此催化剂引入重馏分油裂化区,能够明显降低重馏分油与催化剂的接触温度,同时采用上行式反应器,可以最大化生产低碳烯烃和btx。产物中的轻烯烃是低碳烯烃的前身物,在下行床下部设置流化床反应器,将轻烯烃在适宜的温度和停留时间下进一步转化,可以最大化生产低碳烯烃。因此,本公开提供的方法反应温度分布更合理,催化剂活性与馏分油裂解性能更匹配,在最大化生产低碳烯烃和btx的同时,可以明显降低干气和焦炭的产率。
47.根据本公开,步骤s1中,所述切割的切割点可以为200-380℃之间的任意温度。
48.根据本公开,步骤s4中,所述第二股催化剂与所述半待生催化剂的重量比可以为0.5-3:1。
49.根据本公开,所述第一下行式反应器中,所述第一催化裂化的条件可以包括:所述第一下行式反应器的出口温度为610-720℃,气固停留时间为0.1-3.0秒;所述流化床反应器中,所述第二催化裂化的条件可以包括:所述流化床反应器中的反应温度为600-670℃,质量空速为2-20h-1
;所述第二上行式反应器中,所述第三催化裂化的条件可以包括:所述第二上行式反应器的出口温度为530-650℃,气固停留时间为0.5-8秒。作为本公开的一种优选的实施方式,所述第一下行式反应器中,所述第一催化裂化的条件可以包括:所述第一下行式反应器的出口温度为650-690℃,气固停留时间为0.5-1.5秒;所述流化床反应器中,所述第二催化裂化的条件可以包括:所述流化床反应器中的反应温度为620-640℃,质量空速为4-12h-1
;所述第二上行式反应器中,所述第三催化裂化的条件可以包括:所述第二上行式反应器的出口温度为560-640℃,气固停留时间为1.5-5秒。
50.本公开的一种优选的实施方式,将所述轻烯烃馏分先于所述重馏分油0.3-1.0秒与所述第二股催化剂进行催化裂解;优选将所述轻烯烃先于所述重馏分油0.4-0.8秒与所述第二股催化剂进行催化裂解。
51.根据本公开,该方法还可以包括:将所述第三待生催化剂进行烧焦再生,得到再生催化剂;将所述第一油气和所述第二油气进行分离,得到干气、c3馏分、c4馏分、轻汽油、重汽油、柴油和油浆。其中,所述轻烯烃馏分可以为所述第一油气和所述第二油气中的c4馏分和/或所述第一油气和所述第二油气中60-90℃范围内的馏分。
52.根据本公开,所述原油可以为常规矿物油、煤液化油、合成油、油砂油、页岩油、致密油和动植物油脂中的一种或几种的混合物。
53.根据本公开,所述第一股催化剂和所述第二股催化剂可以各自独立地包括活性组分和载体,所述活性组分为选自含或不含稀土的超稳y型沸石、zsp系列沸石、具有五元环结构的高硅沸石和β沸石中的至少一种。
54.根据本公开,所述第一股催化剂和所述第二股催化剂可以各自独立地包括所述再生催化剂。
55.本公开的一种具体的实施方式,如图1所示,热的第一股催化剂通过第一再生催化剂输送管12向下行床反应器1输送。轻馏分油通过进料喷嘴11喷入下行床反应器1中,与第一股催化剂接触并进行催化裂解反应,反应后的第一催化裂解后的物料在气固分离器2进行催化剂与油气分离,所得第一反应油气通过下行床反应器油气出口22引入分馏装置,第一待生催化剂通过第一待生催化剂输送管31引入上行床反应器3底部,再生催化剂通过第二再生催化剂输送管32引入上行床反应器3底部,催化剂通过预提升介质向上提升。轻烯烃通过轻烯烃进料喷嘴21喷入上行床反应器3,与催化剂接触并发生反应。重馏分油通过重馏分油进料喷嘴33喷入上行床反应器3与来自底部的油剂混合物接触反应,反应后进入沉降器4,在沉降器4中进行催化剂与油气分离,第三反应油气通过上行床反应器油气出口41进入分馏装置,待生催化剂进入汽提器5,汽提出吸附的烃类产物,由输送管53送至再生器6进行再生,再生后的催化剂返回反应器重复使用。将反应油气经分离装置进一步分离得到干气、c3、c4、轻汽油、重汽油、柴油、油浆。
56.本公开的一种具体的实施方式,如图2所示,热的第一股催化剂通过第一再生催化剂输送管12向下行床反应器1输送再生催化剂。轻馏分油通过进料喷嘴11喷入下行床反应器1中,与第一股催化剂接触并进行催化裂解反应,反应后的油剂通过下行床出口蘑菇头分布器13引入流化床反应器2中,在流化床反应器内继续发生裂解反应,反应后的物流经旋分分离后,反应油气由第一油气出口22引入分馏装置,反应后催化剂进入第一汽提器52汽提出吸附的烃类产物后,通过第一待生催化剂输送管31引入上行床反应器3底部,再生催化剂通过第二再生催化剂输送管32引入上行床反应器3底部,催化剂通过预提升介质向上提升。重馏分油通过重馏分油进料喷嘴33喷入上行床反应器3与催化剂接触反应,反应后进入沉降器4,在沉降器4中进行催化剂与油气分离,反应油气通过上行床反应器油气出口41引入分馏装置,待生催化剂进入第二汽提器52,汽提出吸附的烃类产物,由第二待生催化剂输送管53送至再生器6进行再生,再生后的催化剂返回反应器重复使用。反应油气经分馏装置进一步分离得到干气、c3、c4、轻汽油、重汽油、柴油、油浆。
57.以下通过实施例进一步详细说明本公开。实施例中所用到的原材料均可通过商购途径获得。本公开的实施例和对比例中所使用的催化裂化催化剂由中国石油化工股份有限公司催化剂齐鲁分公司工业生产,商品牌号为dmmc-2。该催化剂含有平均孔径小于0.7纳米的zsp沸石和超稳y型沸石,催化剂在使用前在800℃的温度下经饱和蒸汽水热老化10小时,
催化剂的主要物化性质见表1。实施例和对比例中所用的原料性质列于表2。
58.表1
59.催化剂催化剂物理性质 比表面/m2·
g-1
125孔体积/cm-3
·
g-1
0.197表观密度g
·
cm-3
0.86化学组成 al2o3/%56.8sio2/%42.9微反活性/%68
60.表2
[0061][0062][0063]
实施例1
[0064]
本实施例中所加工的原油轻重馏分油切割点为250℃。
[0065]
采用改造的连续反应-再生操作的中型装置进行试验,其流程如附图2所示。700℃的高温再生催化剂经再生斜管由再生器引入下行管反应器1顶部,预热的轻馏分油经水蒸气雾化后,通过进料喷嘴进入下行管反应器1与第一股催化剂接触进行催化裂解反应,第一催化裂解后的物料经旋流分离出第一反应油气和第一待生催化剂,第一反应油气进入分离系统,第一待生催化剂引入提升管反应器3底部。同时将第二股催化剂引入提升管反应器3底部,第二股催化剂在预提升蒸汽作用下向上流动,c4和轻汽油在雾化水蒸气介质下通过进料喷嘴进入提升管反应器3下部,与热的催化剂接触发生反应,重馏分油喷嘴在轻烯烃进料喷嘴的上方800毫米处,重馏分油经水蒸气雾化后,经重馏分油进料喷嘴喷入提升管反应发生催化裂解反应,第三反应油气和第三待生催化剂引入沉降器进行油剂分离,第三反应油气引入产品分离系统分离成干气、c3、c4、轻汽油、重汽油、柴油、油浆。来自提升管的第一待生催化剂进入汽提器,汽提出待生催化剂上吸附的烃类产物后,通过待生剂斜管进入再生器,与空气接触在700℃下烧焦再生。再生后的催化剂经再生斜管返回反应器中循环使用。中型装置采用电加热维持反应-再生系统温度。
[0066]
主要操作条件和结果列于表3。
[0067]
实施例2
[0068]
实施例2说明:在与实施例1相同的反应条件下,所不同的是所加工原油的轻重组分切割点为350℃。
[0069]
采用的反应装置同实施例1,所用到的原料、催化剂和主要实验步骤同实施例1,所不同的是轻重组分的切割点不同。
[0070]
主要操作条件和结果列于表3。
[0071]
实施例3
[0072]
实施例3说明:所加工的原油轻重馏分油切割点为250℃。
[0073]
本发明的实施例是在中型试验装置进行,其流程图如附图2所示。700℃的高温再生催化剂经再生斜管由再生器引入下行管反应器1顶部,预热的轻馏分油经水蒸气雾化后,通过进料喷嘴进入下行管反应器1,与第一股催化剂进行催化裂解反应,反应后的第一催化裂解后的物料通过出口分布器进入流化床反应器,c4和轻汽油经水蒸气雾化后通过进料喷嘴进入流化床反应器2底部,与热的催化剂接触发生反应,反应后油剂进行旋分分离,分离后油气引入后续分离系统,分离后催化剂经汽提后引入提升管反应器3底部。同时将部分高温再生催化剂引入提升管反应器3底部,重馏分油经水蒸气雾化后,经重馏分油喷嘴喷入提升管反应器3,与催化剂接触发生催化裂解反应,反应油剂引入沉降器进行油剂分离,反应油气引入产品分离系统分离成干气、c3、c4、轻汽油、重汽油、柴油、油浆。来自提升管的待生催化剂进入汽提器,汽提出待生催化剂吸附的烃类产物后,通过待生剂斜管进入再生器,与空气接触在700℃下烧焦再生。再生后的催化剂经再生斜管返回反应器中循环使用。中型装置采用电加热维持反应、再生系统温度。
[0074]
主要操作条件和结果列于表3。
[0075]
对比例1
[0076]
对比例1说明:在与实施例1相同的反应条件下,所不同的是产物中的烯烃不进行回炼。
[0077]
采用的反应装置同实施例1,所用到的原料、催化剂和主要实施步骤同实施例1,所不同的是提升管反应器底部不注入轻烯烃。
[0078]
主要操作条件和结果列于表3。
[0079]
对比例2:
[0080]
对比例2说明:在与实施例1相同的反应条件下,所不同的是提升管底部催化剂中的再生催化剂与第一股待生催化剂的质量比为0.14:1。
[0081]
采用的反应装置同实施例1,所用到的原料、催化剂和主要实验步骤同实施例1,所不同的是提升管反应底部引入的再生催化剂与第一待生催化剂的质量比不同。
[0082]
主要操作条件和结果列于表3。
[0083]
对比例3:
[0084]
对比例3说明:在与实施例1相同的反应条件下,所不同的是轻馏分油进入提升管反应器,反应后的催化剂直接进入汽提器。
[0085]
所用到的原料、催化剂和主要实验步骤同实施例1,所不同的是反应装置采用双提升管反应器。
[0086]
主要操作条件和结果列于表3。
[0087]
表3
[0088][0089][0090]
由表3的数据可以看出,使用本公开提供的原油催化裂化生产低碳烯烃和btx的方法,可以明显提高低碳烯烃和轻芳烃的产率和装置经济性。
[0091]
以上详细描述了本公开的优选实施方式,但是,本公开并不限于上述实施方式中的具体细节,在本公开的技术构思范围内,可以对本公开的技术方案进行多种简单变型,这些简单变型均属于本公开的保护范围。
[0092]
另外需要说明的是,在上述具体实施方式中所描述的各个具体技术特征,在不矛盾的情况下,可以通过任何合适的方式进行组合。为了避免不必要的重复,本公开对各种可能的组合方式不再另行说明。
[0093]
此外,本公开的各种不同的实施方式之间也可以进行任意组合,只要其不违背本公开的思想,其同样应当视为本公开所公开的内容。
再多了解一些
本文用于企业家、创业者技术爱好者查询,结果仅供参考。