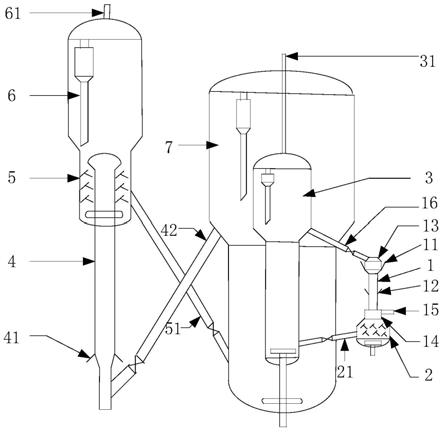
一种原油催化裂解生产低碳烯烃和btx的方法
技术领域
1.本技术涉及石油炼制及石油化工加工过程,具体地,涉及一种原油催化裂解生产低碳烯烃和btx的方法。
背景技术:
2.目前市场上成品油消费量增速持续放缓,而低碳烯烃以及芳烃等基本有机原料需求量仍高速增长,面对这样的态势,化工料型炼厂是未来的发展趋势。目前化工型炼厂的构型主要包括以下三种,一是原油通过溶剂脱沥青或加氢精制等预处理后,直接进入蒸汽裂解单元生产化工料,但这种方式一般仅限于轻质原油;二是通过原油各馏分加氢裂化后,最大化生成重质石脑油,然后通过重整单元最大化生产芳烃;三是原油的轻馏分进入蒸汽裂解单元,重馏分进入催化裂解单元,最大化生产低碳烯烃。以上三种方式均已实现工业化,化学品的收率在35%-55%之间。可以看出,现有化工型炼厂的构型主要依托蒸汽裂解、重整、加氢精制、加氢裂化、催化裂解等多套核心装置的组合。而催化裂解工艺在生产化工料和原料适应性方面具有其独特的优势,可同时生产丙烯、乙烯和btx。
3.中国专利cn109370644a公开了一种原油催化裂解制低碳烯烃和芳烃的方法,该方法将原油分成轻重组分,切割点在150℃-300℃之间,轻馏分和重馏分在同一个反应器不同反应区进行反应,催化剂采用以二氧化硅和三氧化二铝组成的硅铝酸盐为主要组分,包括碱金属氧化物,碱土金属氧化物,钛、铁氧化物,钒和镍的氧化物。该方法是基于重油催化裂解生成低碳烯烃的密相输送床反应器的基础上,针对原油催化裂解生成低碳烯烃提出的解决方案。
4.中国专利cn1315990公开了一种双催化剂系统耦合再生工艺方法。该方法在常规催化裂化装置再生器旁边设立一个用于新型流化催化反应过程的专用催化剂再生的专用再生器,其中专用催化剂颗粒直径》700μm,再生后通过重力的作用将常规催化裂化催化剂与专用催化剂分离,高温再生后的专用催化剂与一小部分常规催化剂经过通道进入副分离器,在副分离器的底部引入空气对催化剂进行流化,通过重力作用将专用催化剂与常规催化剂进一步分离。该方法根据专用催化剂颗粒物性的不同,将常规催化裂化装置的过剩热量引入热量不足的新型流化催化反应过程补充热量。
5.中国专利cn102690682公开了一种生产丙烯的催化裂化方法和装置,该方法使重质原料与以y型沸石为主要活性组元的第一催化裂化催化剂自第一提升管反应器中接触反应,使轻质烃与孔径小于0.7nm择形沸石为主要活性组元的第二催化裂化催化剂在第二提升管反应器接触反应,将反应后的油气与催化剂引入与第二提升管反应器串联的流化床反应器反应。所述催化裂化装置的汽提器用隔板分隔为两个独立汽提区,一个汽提区与提升管和流化床构成的组合反应器形成反应、汽提路线,另一个汽提区则与另一提升管形成相应另一路反应、汽提路线。该发明提供的催化裂化装置,结构简单,可以在一套装置中使用两种催化剂分别进行反应和再生。
6.以上方法涉及到以原油为原料,通过新型催化材料研制制取低碳烯烃和芳烃,同
时涉及设置不同反应区采用各自专用催化剂最大化生产化工料的方法,但没有针对原油的最大化生产化工料的专用反应器结构。
技术实现要素:
7.本公开的目的在于提出一种适于加工原油催化裂解生产低碳烯烃和btx的反应再生系统。
8.为了实现上述目的,本公开提供了一种原油催化裂化生产低碳烯烃和轻芳烃的方法,该方法包括如下步骤:
9.s1、将脱盐脱水的原油切割为轻馏分油和重馏分油;所述切割的切割点为100-400℃之间的任意温度;
10.s2、将所述轻馏分油与第一催化剂引入第一下行式反应器,进行第一催化裂解,得到第一催化裂解后的物料,然后进行气固分离,得到第一反应油气和第一待生催化剂;或者将所述轻馏分油与第一催化剂引入第二上行式反应器,进行第二催化裂解,得到第二催化裂解后的物料,然后进行气固分离,得到第二反应油气和第二待生催化剂;
11.s3、所述重馏分油与第二催化剂引入第三上行式反应器,进行第三催化裂解,然后进行气固分离,得到第三反应油气和第三待生催化剂;
12.s4、将所述第一待生催化剂或所述第二待生催化剂引入第一再生器中进行第一烧焦再生,分别得到第一再生剂或第二再生剂;将所述第三待生催化剂引入第二再生器中进行第二烧焦再生;所述第一再生器与所述第二再生器之间传热不传质;
13.可选地,所述第一再生器和所述第二再生器为独立的两个再生器;或者,所述第一再生器和所述第二再生器各自为由一个再生器分隔出来的独立的两部分中的一个。
14.可选地,所述第一再生器设置于所述第二再生器的内部;或者,所述第一再生器与所述第二再生器各自为由一个再生器用导热板分隔出来的独立的两部分中的一个。
15.可选地,以催化剂干基重量计,所述第一催化剂包括10-50重量%的平均孔径小于0.7nm的择形沸石、0-25重量%的β沸石、10-45重量%的粘土和25-50重量%的无机氧化物粘结剂;所述第二催化剂包括20-40重量%的平均孔径小于0.7nm的择形沸石、5-25重量%的y型沸石、10-45重量%的粘土和25-50重量%的无机氧化物粘结剂。
16.可选地,所述第一再生器和所述第二再生器的催化剂密相温度为650-740℃,优选680-720℃。
17.可选地,所述第一下行式反应器中,所述第一催化裂化的条件包括:所述第一下行式反应器的出口温度为640-720℃,气固停留时间为0.3-2.0秒;所述第二上行式反应器中,所述第二催化裂化的条件包括:所述第二上行式反应器的出口温度为620-710℃,气固停留时间为0.3-5秒;所述第三上行式反应器中,所述第三催化裂化的条件包括:所述第三上行式反应器的出口温度为530-650℃,气固停留时间为0.5-8秒。
18.优选地,所述第一下行式反应器中,所述第一催化裂化的条件包括:所述第一下行式反应器的出口温度为650-710℃,气固停留时间为0.5-1.5秒;所述第二上行式反应器中,所述第二催化裂化的条件包括:所述第二上行式反应器的出口温度为640-690℃,气固停留时间为0.5-3秒;所述第三上行式反应器中,所述第三催化裂化的条件包括:所述第三上行式反应器的出口温度为560-640℃,气固停留时间为1-5秒。
19.可选地,所述第一下行式反应器为等径或变径的下行管反应器;所述第二上行式反应器和第三上行式反应器选自等径或变径的提升管反应器、等径或变径的提升管反应器和流化床复合反应器中的一种。
20.可选地,该方法还包括:将反应油气中分离出轻烯烃馏分,并将所述轻烯烃馏分返回所述第一下行式反应器中或第二上行式反应器中进行反应;所述轻烯烃馏分为所述反应油气中的c4馏分和/或所述反应油气中60-90℃范围内的馏分。
21.可选地,将所述轻烯烃馏分后于所述轻馏分油0.2-1.0秒与所述第一股催化剂进行催化裂解;优选将所述轻烯烃馏分后于所述轻馏分油0.4-0.8秒与所述第一催化剂进行催化裂解。
22.可选地,所述原油为常规矿物油、煤液化油、合成油、油砂油、页岩油、致密油和动植物油脂中的一种或几种的混合物。
23.通过上述技术方案,本公开提供的原油催化裂化生产低碳烯烃和btx的方法,可以明显提高低碳烯烃和轻芳烃的产率,提高装置经济性。
24.本公开的其他特征和优点将在随后的具体实施方式部分予以详细说明。
附图说明
25.附图是用来提供对本公开的进一步理解,并且构成说明书的一部分,与下面的具体实施方式一起用于解释本公开,但并不构成对本公开的限制。在附图中:
26.图1是实施例1中原油催化裂化生产低碳烯烃和轻芳烃的装置图。
27.图2是实施例2中原油催化裂化生产低碳烯烃和轻芳烃的装置图。
28.附图标记说明
29.1、下行床反应器
ꢀꢀꢀꢀꢀꢀꢀꢀꢀꢀꢀꢀꢀꢀꢀꢀꢀꢀ
41、重馏分油进料喷嘴
30.11、轻馏分油进料喷嘴
ꢀꢀꢀꢀꢀꢀꢀꢀꢀꢀꢀꢀꢀ
42、第二再生催化剂输送管
31.12、轻烯烃进料喷嘴
ꢀꢀꢀꢀꢀꢀꢀꢀꢀꢀꢀꢀꢀꢀꢀ
5、第二汽提器
32.13、油剂混合器
ꢀꢀꢀꢀꢀꢀꢀꢀꢀꢀꢀꢀꢀꢀꢀꢀꢀꢀꢀ
51、第二待生催化剂输送管
33.14、油剂分离器
ꢀꢀꢀꢀꢀꢀꢀꢀꢀꢀꢀꢀꢀꢀꢀꢀꢀꢀꢀ
6、沉降器
34.15、下行床反应器油气出口
ꢀꢀꢀꢀꢀꢀꢀꢀꢀ
61、上行床反应器油气出口
35.16、第一再生催化剂输送管
ꢀꢀꢀꢀꢀꢀꢀꢀꢀ
7、第二再生器
36.2、第一汽提器
ꢀꢀꢀꢀꢀꢀꢀꢀꢀꢀꢀꢀꢀꢀꢀꢀꢀꢀꢀꢀ
8、第一提升管反应器
37.21、第一待生催化剂输送管
ꢀꢀꢀꢀꢀꢀꢀꢀꢀ
81、轻馏分油进料喷嘴
38.3、第一再生器
ꢀꢀꢀꢀꢀꢀꢀꢀꢀꢀꢀꢀꢀꢀꢀꢀꢀꢀꢀꢀ
82、轻烯烃进料喷嘴
39.31、再生烟气输送管
ꢀꢀꢀꢀꢀꢀꢀꢀꢀꢀꢀꢀꢀꢀꢀ
83、第一再生催化剂输送管
40.4、上行床反应器
ꢀꢀꢀꢀꢀꢀꢀꢀꢀꢀꢀꢀꢀꢀꢀꢀꢀꢀ
84、第一油气出口
具体实施方式
41.以下对本公开的具体实施方式进行详细说明。应当理解的是,此处所描述的具体实施方式仅用于说明和解释本公开,并不用于限制本公开。
42.本公开提供了一种原油催化裂化生产低碳烯烃和轻芳烃的方法,该方法包括如下步骤:
43.s1、将脱盐脱水的原油切割为轻馏分油和重馏分油;所述切割的切割点为100-400℃之间的任意温度;
44.s2、将所述轻馏分油与第一催化剂引入第一下行式反应器,进行第一催化裂解,得到第一催化裂解后的物料,然后进行气固分离,得到第一反应油气和第一待生催化剂;或者将所述轻馏分油与第一催化剂引入第二上行式反应器,进行第二催化裂解,得到第二催化裂解后的物料,然后进行气固分离,得到第二反应油气和第二待生催化剂;
45.s3、所述重馏分油与第二催化剂引入第三上行式反应器,进行第三催化裂解,然后进行气固分离,得到第三反应油气和第三待生催化剂;
46.s4、将所述第一待生催化剂或所述第二待生催化剂引入第一再生器中进行第一烧焦再生,分别得到第一再生剂或第二再生剂;将所述第三待生催化剂引入第二再生器中进行第二烧焦再生;所述第一再生器与所述第二再生器之间传热不传质;
47.作为本领域技术人员所熟知的,原油具有馏程宽、碳数分布广、烃类组成复杂的特点,以全馏分原油为催化裂解原料,不同馏分段生产低碳烯烃和轻芳烃的最佳反应条件和催化剂性能差异较大。因此,本公开根据原油不同馏分段的烃类组成特点和裂解反应特性,提供了一种原油催化裂解生产低碳烯烃和btx的方法。通过本公开的方法一方面将轻馏分油和重馏分油在各自适宜的催化剂组成下反应,能够最大化生产低碳烯烃和btx;另一方面采用可进行热量交换但不进行物质交换的再生器,可将重馏分油裂解过程中过剩的热量转移到轻馏分油裂解过程中,从而达到轻、重馏分油裂解过程的热平衡。
48.根据本公开,所述第一再生器和所述第二再生器可以为独立的两个再生器;或者,所述第一再生器和所述第二再生器可以各自为由一个再生器分隔出来的独立的两部分中的一个。
49.根据本公开,所述第一再生器可以设置于所述第二再生器的内部;或者,所述第一再生器与所述第二再生器可以各自为由一个再生器用导热板分隔出来的独立的两部分中的一个。
50.根据本公开,以催化剂干基重量计,所述第一催化剂可以包括10-50重量%的平均孔径小于0.7nm的择形沸石、0-25重量%的β沸石、10-45重量%的粘土和25-50重量%的无机氧化物粘结剂;所述第二催化剂可以包括20-40重量%的平均孔径小于0.7nm的择形沸石、5-25重量%的y型沸石、10-45重量%的粘土和25-50重量%的无机氧化物粘结剂。
51.根据本公开,所述第一再生器和所述第二再生器的催化剂密相温度可以为650-740℃,优选地所述第一再生器和所述第二再生器的催化剂密相温度可以为680-720℃。
52.根据本公开,本公开的轻馏分油于第一下行式反应器中在高温、短停留时间、专用催化剂的情况下催化裂解,既可以高选择性的生产低碳烯烃和btx,也可以明显降低甲烷生成。其中,所述第一下行式反应器中,所述第一催化裂化的条件可以包括:所述第一下行式反应器的出口温度为640-720℃,气固停留时间为0.3-2.0秒;所述第二上行式反应器中,所述第二催化裂化的条件包括:所述第二上行式反应器的出口温度为620-710℃,气固停留时间为0.3-5秒;所述第三上行式反应器中,所述第三催化裂化的条件可以包括:所述第三上行式反应器的出口温度为530-650℃,气固停留时间为0.5-8秒。作为本公开的一种优选的实施方式,所述第一下行式反应器中,所述第一催化裂化的条件可以包括:所述第一下行式反应器的出口温度为650-710℃,气固停留时间为0.5-1.5秒;所述第二上行式反应器中,所
述第二催化裂化的条件包括:所述第二上行式反应器的出口温度为640-690℃,气固停留时间为0.5-3秒;所述第三上行式反应器中,所述第三催化裂化的条件可以包括:所述第三上行式反应器的出口温度为560-640℃,气固停留时间为1-5秒。
53.根据本公开,所述第一下行式反应器可以为等径或变径的下行管反应器;所述第二上行式反应器和第三上行式反应器可以选自等径或变径的提升管反应器、等径或变径的提升管反应器和流化床复合反应器中的一种。
54.根据本公开,该方法还可以包括:将反应油气中分离出轻烯烃馏分,并将所述轻烯烃馏分返回所述第一下行式反应器中或第二上行式反应器中进行反应;所述轻烯烃馏分为所述反应油气中的c4馏分和/或所述反应油气中60-90℃范围内的馏分。本公开的轻烯烃馏分后于轻馏分油与催化剂接触进行反应,一方面有利于将轻烯烃馏分进一步转化为低碳烯烃,另一方面能降低轻烯烃馏分与催化剂的初始接触温度,从而可以明显降低干气和焦炭产率。
55.根据本公开,将所述轻烯烃馏分可以后于所述轻馏分油0.2-1.0秒与所述第一催化剂进行催化裂解;优选地,将所述轻烯烃馏分后于所述轻馏分油0.4-0.8秒与所述第一催化剂进行催化裂解。
56.根据本公开,所述原油可以为常规矿物油、煤液化油、合成油、油砂油、页岩油、致密油和动植物油脂中的一种或几种的混合物。
57.本公开的一种具体的实施方式,如图1所示,热的第一催化剂通过第一再生催化剂输送管16向下行床反应器1输送,轻馏分油通过进料喷嘴11喷入油剂混合器13与第一催化剂接触,油剂混合后在下行床反应器1中进行催化裂解反应,轻烯烃通过轻烯烃进料喷嘴12喷入下行床反应器1,与来自上部的油剂混合物接触反应,反应后的油剂在油剂分离器14进行催化剂与油气分离,所得第一反应油气通过下行床反应器油气出口15引入分馏装置,待生催化剂进入第一汽提器2,汽提出吸附的烃类产物,由第一待生催化剂输送管21送至第一再生器3进行催化剂再生,再生后的催化剂返回下行床反应器1重复使用。热的第二催化剂通过第二再生催化剂输送管42引入上行床反应器4底部,催化剂通过预提升介质向上提升,重馏分油通过重馏分油进料喷嘴41喷入上行床反应器4与来自底部的油剂混合物接触反应,反应后进入沉降器6,在沉降器6中进行催化剂与油气分离,将得到的第三反应油气通过上行床反应器油气出口61进入分馏装置,第三待生催化剂进入第二汽提器5,汽提出吸附的烃类产物,由输送管51送至第二再生器7进行再生,再生后的催化剂返回反应器重复使用。再生烟气通过再生烟气输送管31进入烟气系统。第二再生器位于第一再生器内部。反应油气经分馏装置进一步分离得到干气、c3、c4、轻汽油、重汽油、柴油、油浆。
58.本公开的一种具体的实施方式,如图2所示,热的第一催化剂通过第一再生催化剂输送管83引入第一提升管反应器8底部,第一催化剂通过预提升介质向上提升。轻馏分油通过进料喷嘴81喷入第一提升管反应器8中,与第一催化剂接触进行催化裂解反应,轻烯烃通过轻烯烃进料喷嘴82喷入第一提升管反应器8,与来自下部的油剂混合物接触反应,反应后的油剂进行催化剂与油气分离,所得第二反应油气通过第一油气出口84引入分馏装置,待生催化剂进入第一汽提器2,汽提出吸附的烃类产物,由第一待生催化剂输送管21送至第一再生器3进行催化剂再生,再生后的催化剂返回第一提升管反应器1重复使用。热的第二催化剂通过第二再生催化剂输送管42引入第二提升管反应器4底部,第二催化剂通过预提升
介质向上提升,重馏分油通过重馏分油进料喷嘴41喷入第二提升管反应器4与来自底部的油剂混合物接触反应,反应后进入沉降器6,在沉降器6中进行催化剂与油气分离,反应油气通过第二油气出口61进入分馏装置,第三待生催化剂进入第二汽提器5,汽提出吸附的烃类产物,由输送管51送至第二再生器7进行再生,再生后的催化剂返回反应器重复使用。再生烟气通过再生烟气输送管31进入烟气系统。第二再生器位于第一再生器内部。反应油气经分馏装置进一步分离得到干气、c3、c4、轻汽油、重汽油、柴油、油浆。
59.以下通过实施例进一步详细说明本公开。实施例中所用到的原材料均可通过商购途径获得。其中,本公开的实施例和对比例中所使用的催化剂包括两种,催化剂a和催化剂b,两种催化剂的性质见表1,催化剂使用前在800℃的温度下经饱和蒸汽水热老化10小时,催化剂的主要物化性质见表1。实施例和对比例中所用的原料性质列于表2。
60.表1
61.催化剂催化剂a催化剂b化学组成,%
ꢀꢀ
zsp分子筛3530β分子筛5-usy分子筛-10粘土2525无机氧化物3535
62.表2
63.项目原油a密度(20℃)/(g
·
cm-3
)0.864凝固点/℃32运动粘度(50℃)/(mm2/s)23.23残炭/%3.18蜡含量/%32.1沥青质/%0.2小于250℃馏分质量分数/%13.7小于350℃馏分质量分数/%21.2
64.实施例1
65.实施例1说明:所加工的原油轻重馏分切割点为350℃。
66.采用两套连续反应-再生操作的中型装置进行试验,其中一套中型装置为下行管反应器,700℃的高温再生催化剂a经再生斜管引入下行管反应器顶部,预热的轻馏分油经水蒸气雾化后,通过进料喷嘴进入下行管反应器与热的再生催化剂a接触进行催化裂解反应,距离轻馏分油喷嘴下方600毫米处,c4和轻汽油在雾化水蒸气介质下通过进料喷嘴进入下行管反应器,与来自上部的油剂混合物接触反应,反应后的油剂经旋流分离出反应油气与待生催化剂a,反应油气进入后续产品分离系统,待生催化剂a引入汽提器汽提后进入再生器,再生后的催化剂a返回下行式反应器循环使用。另一套中型装置为提升管反应器。重馏分油经水蒸气雾化后,经重馏分油喷嘴喷入提升管反应器,与700℃的高温再生催化剂b接触发生催化裂解反应,反应油剂引入沉降器进行油剂分离,反应油气引入产品分离系统
分离成干气、c3、c4、轻汽油、重汽油、柴油、油浆。来自提升管的待生催化剂b进入汽提器,汽提出待生催化剂吸附的烃类产物后,通过待生剂斜管进入再生器,与空气接触在700℃下烧焦再生。再生后的催化剂b经再生斜管返回反应器中循环使用。中型装置采用电加热维持反应、再生系统温度。
67.主要操作条件和结果列于表3。
68.实施例2
69.实施例2说明:所加工的原油轻重馏分切割点为260℃。
70.采用两套连续反应-再生操作的中型装置进行试验,其中一套中型装置为提升管反应器,700℃的高温再生催化剂a经再生斜管引入提升管反应器底部,预热的轻馏分油经水蒸气雾化后,通过进料喷嘴进入提升管反应器与热的再生催化剂a接触进行催化裂解反应,距离轻馏分油喷嘴上方600毫米处,碳四和轻汽油在雾化水蒸气介质下通过进料喷嘴进入提升管反应器,与来自下部的油剂混合物接触反应,反应后的油剂经旋风分离器分离出反应油气与待生催化剂a,反应油气进入后续产品分离系统,待生催化剂a引入汽提器汽提后进入再生器,再生后的催化剂a返回提升管反应器循环使用。另一套中型装置同为提升管反应器。重馏分油经水蒸气雾化后,经重馏分油喷嘴喷入提升管反应器,与700℃的高温再生催化剂b接触发生催化裂解反应,反应油剂引入沉降器进行油剂分离,反应油气引入产品分离系统分离成干气、c3、c4、轻汽油、重汽油、柴油、油浆。来自提升管的待生催化剂b进入汽提器,汽提出待生催化剂吸附的烃类产物后,通过待生剂斜管进入再生器,与空气接触在700℃下烧焦再生。再生后的催化剂b经再生斜管返回反应器中循环使用。
71.中型装置采用电加热维持反应、再生系统温度。
72.主要操作条件和结果列于表3。
73.对比例1
74.对比例1说明:在与实施例2相同的反应条件下,所不同的是上行床反应器采用与提升管反应器相同的催化剂b。
75.采用的反应装置同实施例1,所用到的原料和主要实施步骤同实施例1,所不同的是下行床反应器采用催化剂b。
76.主要操作条件和结果列于表3。
77.表3
[0078][0079][0080]
由表3可以看出,使用本公开提供的原油催化裂化生产低碳烯烃和btx的方法,明显提高低碳烯烃和轻芳烃的产率,提高装置经济性。
[0081]
以上详细描述了本公开的优选实施方式,但是,本公开并不限于上述实施方式中的具体细节,在本公开的技术构思范围内,可以对本公开的技术方案进行多种简单变型,这些简单变型均属于本公开的保护范围。
[0082]
另外需要说明的是,在上述具体实施方式中所描述的各个具体技术特征,在不矛盾的情况下,可以通过任何合适的方式进行组合。为了避免不必要的重复,本公开对各种可能的组合方式不再另行说明。
[0083]
此外,本公开的各种不同的实施方式之间也可以进行任意组合,只要其不违背本公开的思想,其同样应当视为本公开所公开的内容。
再多了解一些
本文用于企业家、创业者技术爱好者查询,结果仅供参考。