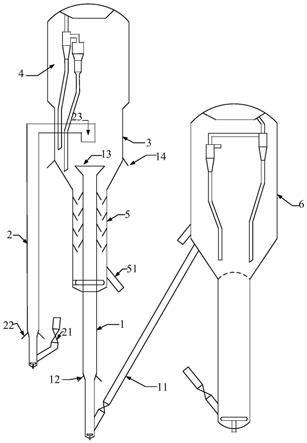
1.本技术涉及石油炼制及石油化工加工过程,具体地,涉及一种全馏分原油催化裂化生产低碳烯烃和轻芳烃的方法。
背景技术:
2.现有化工型炼厂的构型主要依托于蒸汽裂解、重整、加氢、加氢裂化、催化裂解等多套核心装置的组合。随着油消费量增速的持续放缓和低碳烯烃以及芳烃等基本有机原料需求量的高速增长,现有化工型炼厂逐渐不能满足实际的成产需要,全化工料型炼厂成为未来的发展趋势。催化裂解工艺在生产化工料和原料适应性方面具有其独特的优势,可以同时生产丙烯、乙烯和btx。
3.近年来的生产化工原料的催化裂化技术主要从提高反应苛刻度,使用新型反应器结构,使用含择形分子筛的催化剂或助剂和回炼富含丙烯前身物的馏分几个方面进行研究。
4.中国专利cn102899078a公开了一种生产丙烯的催化裂化方法,该方法基于双提升管与流化床构成的组合反应器,首先将重质原料油与第一股催化剂引入第一提升管反应器进行反应,油剂分离后进入分离系统。将裂解重油引入第二提升管反应器与引入第二提升管反应器的催化剂接触反应,将轻质烃引入第二提升管反应器,与裂解重油和第二股裂化催化剂接触反应形成的混合物接触,所述轻质烃包括产品分离系统得到的c4烃或汽油馏分。然后将第二提升管反应器反应后的油气与催化剂引入流化床反应器反应。通过工艺方案的优化,配备合适的催化剂,对不同进料进行选择性转化,具有较高的丙烯和丁烯产率。
5.中国专利cn103666551a公开了一种高温费托合成油的催化加工方法和装置,该方法充分考虑了馏程分布,将费托合成油分为气态烃,高温冷凝物和低温冷凝物三种馏分,该方法将气态烃和高温冷凝物进入第一提升管反应器进行催化转化,低凝物和回炼裂解轻汽油馏分进入组合床层反应器转化,该方法引入第二提升管反应器的催化剂为来自再生器的再生催化剂和来自汽提器的待生催化剂或二者的混合物,该方法构建了一条高温费托合成工艺合成油的加工路线,加工丙烯产率高。
6.上述方法在催化裂化多产低碳烯烃工艺设计方面做了大量的工作,取得了一定的效果,但在不同基属的原油分区转化中,如何最优化生产低碳烯烃和轻芳烃,仍是亟待解决的问题。
技术实现要素:
7.本公开的目的在于提供一种针对不同基属原油进行分区转化时,最大化生产低碳烯烃和轻芳烃的方法。
8.为了实现上述目的,本公开提供了一种全馏分原油催化裂化生产低碳烯烃和轻芳烃的方法,该方法包括如下步骤:
9.s1、将脱盐脱水的全馏分原油切割为轻组分和重组分;当所述全馏分原油的uop k
值在11.5-12.0时,所述切割的切割点为350-400℃之间的任意温度,当所述全馏分原油的uop k值大于12.0时,所述切割的切割点为305-350℃之间的任意温度;
10.s2、将所述重组分与第一股催化剂引入第一提升管反应器,进行第一催化裂化,得到第一催化裂化后的物料;
11.s3、将所述轻组分与第二股催化剂引入第二提升管反应器,进行第二催化裂化,得到第二催化裂化后的物料;
12.s4、将所述第一催化裂化后的物料和所述第二催化裂化后的物料引入流化床反应器中,进行第三催化裂化,得到第三催化裂化后的物料;
13.s5、将所述第三催化裂化后的物料进行气固分离,得到反应油气和积炭催化剂。
14.其中,uop k值是由石油馏分的平均沸点和相对密度来决定的:
15.,其中t为平均沸点,为相对密度。
16.可选地,该方法还包括:将所述积炭催化剂进行烧焦再生,得到再生催化剂;将所述反应油气进行分离,得到干气、c3、c4、轻汽油、重汽油、柴油、油浆。
17.可选地,所述第一股催化剂和所述第二股催化剂各自独立地包括再生催化剂。
18.可选地,所述第一股催化剂和所述第二股催化剂的微反活性各自独立地为50%-74%,优选为60%-70%。
19.可选地,所述第一提升管反应器中,所述第一催化裂化的条件包括:提升管出口温度为520-650℃,油气停留时间为0.1-5秒,催化剂与重组分的重量比为8-30:1;所述第二提升管反应器中,所述第二催化裂化的条件包括:提升管出口温度为600-720℃,油气停留时间为0.1-5秒,催化剂与轻组分的重量比为10-50:1;所述流化床反应器中,所述第三催化裂化的条件包括:反应温度560-640℃,重时空速为3-50h-1
。
20.可选地,所述第一提升管反应器中,所述第一催化裂化的条件包括:提升管出口温度为560-620℃,油气停留时间为0.5-3秒,催化剂与重组分的重量比为10-20:1;所述第二提升管反应器中,所述第二催化裂化的条件包括:提升管出口温度为640-680℃,油气停留时间为0.5-2秒,催化剂与轻组分的重量比为20-40:1;所述流化床反应器中,所述第三催化裂化的条件包括:反应温度580-620℃,重时空速为4-30h-1
。
21.可选地,该方法还包括:在所述流化床反应器中,喷入回炼油,所述回炼油包括c4和/或裂化轻汽油;所述回炼油与所述全馏分原油的重量比为1:5-30,优选为1:10-20。
22.可选地,所述裂化轻汽油为从所述反应油气中分离的30-180℃馏分的全馏分或部分馏分;所述回炼c4为从所述反应油气中分离得到的c4烷烃和/或c4烯烃的混合物。
23.可选地,原油为常规矿物油、煤液化油、合成油、油砂油、页岩油、致密油和动植物油脂中的一种或几种的混合物。
24.可选地,所述第一股催化剂和所述第二股催化剂各自独立地包括活性组分和载体,其中活性组分为选自含或不含稀土的y或hy型沸石、含或不含稀土的超稳y型沸石、zsm-5系列沸石、具有五元环结构的高硅沸石和β沸石中的至少一种。
25.通过上述技术方案,本公开提供的全馏分原油催化裂化生产低碳烯烃和轻芳烃的方法可以在提高乙烯、丙烯和btx产率的同时,明显降低干气和焦炭产率,并且本公开的方
法使用的装置具有较好的经济效益。
26.本公开的其他特征和优点将在随后的具体实施方式部分予以详细说明。
附图说明
27.附图是用来提供对本公开的进一步理解,并且构成说明书的一部分,与下面的具体实施方式一起用于解释本公开,但并不构成对本公开的限制。在附图中:
28.图1是本公开的一种具体的实施方式的装置图。
29.附图标记说明
30.1、第一提升管反应器;
31.11、第一提升管反应器再生催化剂输送管;
32.12、重组分进料喷嘴;
33.13、第一提升管反应器出口;
34.14、c4和或裂化轻汽油进料喷嘴;
35.2、第二提升管反应器;
36.21、第二提升管反应器再生催化剂输送管;
37.22、轻组分进料喷嘴;
38.23、第二提升管反应器出口;
39.3、流化床反应器;
40.4、沉降器;
41.5、汽提器;
42.51、待生催化剂输送管;
43.6、再生器。
具体实施方式
44.以下对本公开的具体实施方式进行详细说明。应当理解的是,此处所描述的具体实施方式仅用于说明和解释本公开,并不用于限制本公开。
45.本公开提供了一种全馏分原油催化裂化生产低碳烯烃和轻芳烃的方法,该方法包括如下步骤:
46.s1、将脱盐脱水的全馏分原油切割为轻组分和重组分;当所述全馏分原油的uop k值在11.5-12.0时,所述切割的切割点为350-400℃之间的任意温度,当所述全馏分原油的uop k值大于12.0时,所述切割的切割点为305-350℃之间的任意温度;
47.s2、将所述重组分与第一股催化剂引入第一提升管反应器,进行第一催化裂化,得到第一催化裂化后的物料;
48.s3、将所述轻组分与第二股催化剂引入第二提升管反应器,进行第二催化裂化,得到第二催化裂化后的物料;
49.s4、将所述第一催化裂化后的物料和所述第二催化裂化后的物料引入流化床反应器中,进行第三催化裂化,得到第三催化裂化后的物料;
50.s5、将所述第三催化裂化后的物料进行气固分离,得到反应油气和积炭催化剂。
51.其中,uop k值是由石油馏分的平均沸点和相对密度来决定的:
52.,其中t为平均沸点,为相对密度。
53.作为本领域技术人员所熟知的,全馏分原油具有馏程宽、碳数分布广的特点,以全馏分原油为催化裂解原料,不同馏分段生产低碳烯烃和轻芳烃的最佳操作窗口差异较大,需要通过切割成轻重组分进行分区转化,达到生产目的产物的优化操作。发明人经过大量实验发现不同基属的原油,最佳的轻重馏分切割点有所差异。因此,本发明提供了一种全馏分原油催化裂化生产低碳烯烃和轻芳烃的方法,明确不同基属原油的轻重组分切割点,结合双提升管 床层的反应器形式,最大化生产低碳烯烃和轻芳烃。
54.根据本公开,该方法还可以包括:将所述积炭催化剂进行烧焦再生,得到再生催化剂;将所述反应油气进行分离,得到干气、c3、c4、轻汽油、重汽油、柴油、油浆。
55.根据本公开,所述第一股催化剂和所述第二股催化剂可以各自独立地包括再生催化剂。
56.根据本公开,所述第一股催化剂和所述第二股催化剂的微反活性可以各自独立地为50%-74%,优选为60%-70%。
57.根据本公开,所述第一提升管反应器中,所述第一催化裂化的条件可以包括:提升管出口温度为520-650℃,油气停留时间为0.1-5秒,催化剂与重组分的重量比为8-30:1;所述第二提升管反应器中,所述第二催化裂化的条件可以包括:提升管出口温度为600-720℃,油气停留时间为0.1-5秒,催化剂与轻组分的重量比为10-50:1;所述流化床反应器中,所述第三催化裂化的条件可以包括:反应温度560-640℃,重时空速为3-50h-1
。
58.根据本公开,所述第一提升管反应器中,所述第一催化裂化的条件可以包括:提升管出口温度为560-620℃,油气停留时间为0.5-3秒,催化剂与重组分的重量比为10-20:1;所述第二提升管反应器中,所述第二催化裂化的条件可以包括:提升管出口温度为640-680℃,油气停留时间为0.5-2秒,催化剂与轻组分的重量比为20-40:1;所述流化床反应器中,所述第三催化裂化的条件可以包括:反应温度580-620℃,重时空速为4-30h-1
。
59.根据本公开,该方法还可以包括:在所述流化床反应器中,喷入回炼油,所述回炼油包括c4和/或裂化轻汽油;所述回炼油与所述全馏分原油的重量比为1:5-30,优选为1:10-20。
60.根据本公开,所述裂化轻汽油可以为从所述反应油气中分离的30-180℃馏分的全馏分或部分馏分;所述c4可以为从所述反应油气中分离得到的c4烷烃和/或c4烯烃的混合物。
61.根据本公开,原油可以为常规矿物油、煤液化油、合成油、油砂油、页岩油、致密油和动植物油脂中的一种或几种的混合物。
62.根据本公开,所述第一股催化剂和所述第二股催化剂可以各自独立地包括活性组分和载体,其中活性组分可以为选自含或不含稀土的y或hy型沸石、含或不含稀土的超稳y型沸石、zsm-5系列沸石、具有五元环结构的高硅沸石和β沸石中的至少一种。
63.本公开的一种具体的实施方式,如图1所示,将脱盐脱水的全馏分原油切割为轻组分和重组分,通过再生催化剂输送管11向第一提升管反应器1输送第一股催化剂。重组分通过进料喷嘴12喷入第一提升管反应器1中,与第一股催化剂接触并进行催化裂化反应得到
第一催化裂化后的物料;轻组分通过进料喷嘴22喷入第二提升管反应器2,与来自催化剂输送管21输送的第二股催化剂接触反应得到第二催化裂化后的物料;将第一催化裂化后的物料经第一提升管反应器出口13,将第二催化裂化后的物料经第二提升管反应器出口23与第一催化裂化后的物料共同引入流化床反应器3中反应。c4和或裂化轻汽油进料喷嘴14喷入流化床反应器3中,在流化床反应器3内反应后,进入沉降器4,在沉降器4中催化剂与油气分离,待生催化剂进入汽提器5,汽提出吸附的烃类产物,由输送管51送至再生器6进行再生,再生后的催化剂返回两个提升管反应器重复使用。反应油气进入分馏装置,进一步分离得到干气、c3、c4、轻汽油、重汽油、柴油、油浆。
64.以下通过实施例进一步详细说明本公开。实施例中所用到的原材料均可通过商购途径获得。其中,本公开中的实施例和对比例中所使用的催化裂化催化剂由中国石油化工股份有限公司催化剂齐鲁分公司工业生产,商品牌号为mmc-2。该催化剂含有超稳y型沸石和平均孔径小于0.7纳米的zsp沸石,催化剂在使用前在800℃的温度下经饱和蒸汽水热老化17小时,催化剂的主要物化性质见表1。实施例和对比例中所用的原油性质列于表2。
65.表1
[0066][0067]
表2
[0068]
[0069][0070]
实施例1
[0071]
实施例1说明:所加工的原油为uop k值为12.3的原油a,轻重组分切割点为310℃。
[0072]
采用改造的连续反应-再生操作的中型装置进行实验,其流程如附图1所示,该中型装置提升管反应器1内径为16毫米,长度为3800毫米,提升管反应器2的内径为12毫米,长度为3200毫米,流化床反应器的内径为64毫米,高度600毫米。700℃的高温再生催化剂经再生斜管由再生器分别引入提升管反应器1和2底部,并在预提升蒸汽作用下向上流动。重组分与雾化水蒸气混合后,通过进料喷嘴进入提升管反应器1与热的再生剂接触进行催化转化反应,反应后的油气经第一提升管反应器出口引入流化床反应器中反应。c4和馏程为30-180℃的裂化轻汽油引入流化床反应器中。轻组分在雾化水蒸气介质下通过进料喷嘴进入提升管反应器2下部与热的再生剂接触进行催化转化反应,反应油气和催化剂的混合物沿提升管反应器2上行通过提升管反应器2出口进入流化床反应器继续参与裂化反应,反应油剂引入沉降器进行油剂分离,反应油气引入产品分离系统分离成干气、c3、c4、轻汽油、重汽油、柴油、油浆。来自流化床的含有焦炭的待生催化剂进入汽提器,汽提水蒸气汽提出待生剂上吸附烃类产物后通过流化床进入沉降器进行气固分离。汽提后的待生剂通过待生剂斜管进入再生器,与空气接触在700℃高温烧焦再生。再生后的催化剂经再生斜管返回提升管反应器中循环使用。中型装置采用电加热维持反应-再生系统温度。
[0073]
主要操作条件和结果列于表3。
[0074]
实施例2
[0075]
实施例2说明:在与实施例1相同的反应条件下,所不同的是所加工的原油为uop k值为11.7的原油b,轻重组分切割点为360℃。
[0076]
采用的反应装置同实施例1,所用到催化剂和主要实验步骤同实施例1,所不同的是所加工的原油uop k值不同,轻重组分的切割点不同。
[0077]
主要操作条件和结果列于表3。
[0078]
对比例1
[0079]
对比例1说明:在与实施例1相同的反应条件下,所不同的是所加工原油a的轻重组分切割点为360℃。
[0080]
采用的反应装置同实施例1,所用到的原料、催化剂和主要实验步骤同实施例1,所不同的是轻重组分的切割点不同。
[0081]
主要操作条件和结果列于表3。
[0082]
对比例2
[0083]
对比例2说明:在与实施例1相同的反应条件下,所不同的是所加工原油a的轻重组分切割点为250℃。
[0084]
采用的反应装置同实施例1,所用到的原料、催化剂和主要实验步骤同实施例1,所不同的是轻重组分的切割点不同。
[0085]
主要操作条件和结果列于表3。
[0086]
对比例3
[0087]
对比例3说明:在与实施例2相同的反应条件下,所不同的是所加工原油b的轻重组分切割点为310℃。
[0088]
采用的反应装置同实施例2,所用到的原料、催化剂和主要实验步骤同实施例1,所不同的是轻重组分的切割点不同。
[0089]
主要操作条件和结果列于表3。
[0090]
表3
[0091]
项目实施例1实施例2对比例1对比例2对比例3原油名称abaab轻重组分切割点/℃310360360250310第一提升管出口温度/℃600580600600580第一提升管反应时间/s1.51.51.51.51.5第二提升管出口温度/℃670650670670650第二提升管反应时间/s11111床层反应温度/℃610590610610590床层重时空速/h-1
44444产物分布/%
ꢀꢀꢀꢀꢀ
干气17.113.219.415.412.6液化气40.128.140.439.327.2汽油24.523.121.226.323.2柴油5.212.53.96.113.4油浆1.97.21.62.28.1焦炭11.215.913.510.715.5总计100100100100100乙烯 丙烯 btx45.129.744.942.828.1燃料气 焦炭 油浆20.523.124.220.123
[0092]
由表3数据可以看出,使用本公开提供的全馏分原油催化裂化生产低碳烯烃和轻芳烃的方法,可以在获得较高乙烯、丙烯和btx产率的同时,燃料气、焦炭和油浆等低价值产品收率较低,装置的经济效益好。
[0093]
以上详细描述了本公开的优选实施方式,但是,本公开并不限于上述实施方式中的具体细节,在本公开的技术构思范围内,可以对本公开的技术方案进行多种简单变型,这些简单变型均属于本公开的保护范围。
[0094]
另外需要说明的是,在上述具体实施方式中所描述的各个具体技术特征,在不矛盾的情况下,可以通过任何合适的方式进行组合。为了避免不必要的重复,本公开对各种可
能的组合方式不再另行说明。
[0095]
此外,本公开的各种不同的实施方式之间也可以进行任意组合,只要其不违背本公开的思想,其同样应当视为本公开所公开的内容。
再多了解一些
本文用于企业家、创业者技术爱好者查询,结果仅供参考。