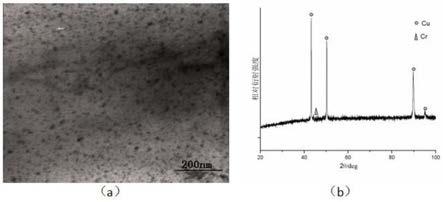
1.本发明涉及合金铸造技术领域,特别是一种凝固过程中形成纳米铬相的铜合金铸件及铸造方法。
背景技术:
2.高强高导铜合金的研发已近50年,高强高导铜合金研究开发的中心任务主要是解决高强度与高导电率导热率的矛盾,即如何在不降低铜电导率的前提下,大幅度提高铜材料的强度。大量研究主要集中在以下三个方面:
①
加入适当数量的强化相;
②
采用室温下在铜中溶解度不高的元素;
③
选择对铜合金导电率影响较小的元素。所以,目前的强化方式基本有两种:一是合金化法,即通过引进适量元素形成固溶体合金,再通过机械加工和热处理使其组织和结构发生变化,而获得高强高导兼备的铜合金;二是复合材料法,即引进复合材料作为第二相强化铜基体,进而提高强度。目前,比较成熟有效的强化方式有:形变强化、纤维强化、颗粒强化、弥散强化、细晶强化、固溶强化、沉淀强化等,多种制备工艺和多种强化手段综合运用是目前该类合金研究的重点。
3.holzwarth等人研究表明,cu-0.75cr-0.105zr(wt%)合金凝固时形成的亚微观尺度粒子(1~10μm),在后续的固溶处理时不易溶解,影响时效处理后微观尺度粒子(≤100nm)的强化效果。
技术实现要素:
4.本发明的目的是要解决现有技术中存在的不足,提供一种凝固过程中形成纳米铬相的铜合金铸件及铸造方法。
5.为达到上述目的,本发明是按照以下技术方案实施的:
6.本发明的第一个目的是要提供一种凝固过程中形成纳米铬相的铜合金铸件的铸造方法,具体步骤如下:
7.步骤一、将用于浇注铸件的熔模模壳加热到850℃,保温2h,然后将加热后的熔模模壳安装在真空炉内的离心盘上;
8.步骤二、将合金原料放入坩埚,在真空炉内抽真空状态下熔炼10-15分钟至合金全部熔化,确定合金的化学成分为cu-0.43cr-0.22zr-0.092mg,合金全部熔化后保温20分钟;
9.步骤三、停止抽真空,向真空炉内充入保护气体,开启真空炉离心控制系统,调至离心转速为300r/min,待离心盘平稳转动后,将合金液浇注到熔模模壳中,浇注温度为1250℃;
10.步骤四、浇注结束后,真空炉离心控制系统持续运行10-20分钟,使合金液凝固为铸件,铸件在熔模模壳内缓慢冷却至室温,然后破壳清理,取出铸件。
11.进一步地,所述步骤二中,真空炉内抽真空状态下的真空度为4
×
10-1
pa。
12.进一步地,所述步骤三中,保护气体为氩气,氩气的充入量为至真空炉内压强为0.08mpa。
13.进一步地,所述步骤三中,浇注时长为10-20秒。
14.本发明的第二个目的是要提供一种利用上述方法铸造的铜合金铸件。
15.与现有技术相比,本发明采用“熔模 离心”铸造技术,通过控制熔炼温度、浇注温度、真空度、离心机转数等工艺参数制备出的cu-0.43cr-0.22zr-0.092mg合金铸件,铸态组织中存在大量的纳米粒子,这些纳米粒子在固溶处理过程中,容易溶于基体中,为随后的时效过程中形成更多细小的纳米析出相奠定了良好的基础,且其导电率达到80.6%iacs,抗拉强度达到580mpa。
附图说明
16.图1为cu-0.43cr-0.22zr-0.092mg合金铸件的tem图和xrd结果:(a)为tem图;(b)为xrd结果。
17.图2为cu-0.43cr-0.22zr-0.092mg合金铸件的hrtem图、衍射斑点及标定:(d)为衍射斑点;(e)为标定。
具体实施方式
18.为使本发明的目的、技术方案及优点更加清楚明白,以下结合实施例,对本发明进行进一步的详细说明。此处所描述的具体实施例仅用于解释本发明,并不用于限定发明。
19.实施例1
20.将熔模模壳定位在耐热钢砂桶内,周围用石英砂填充,在砂桶的上层用石英砂与水玻璃混合物覆盖并捣实,干燥后形成固化层,可以防止在离心过程中砂桶内填充的石英砂甩出。然后砂桶放在电阻加热炉内加热到850℃,并保温2h,然后将将耐热钢砂桶从电阻炉内取出并安装在真空炉内的离心盘上;
21.将合金原料放入坩埚,在真空炉内抽至4
×
10-1
pa真空状态下熔炼10分钟至合金全部熔化,确定合金的化学成分为cu-0.43cr-0.22zr-0.092mg(wt%),合金全部熔化后保温20分钟;
22.停止抽真空,向真空炉内充入氩气至真空炉内压强为0.08mpa,开启真空炉离心控制系统,调至离心转速为300r/min,待离心盘平稳转动后,在10秒内将合金液浇注到熔模模壳中,浇注温度为1250℃;
23.浇注结束后,真空炉离心控制系统持续运行10分钟,使合金液凝固为铸件,铸件在熔模模壳内缓慢冷却至室温,然后破壳清理,取出铸件即为含有纳米铬相的铜合金铸件。
24.实施例2
25.将熔模模壳定位在耐热钢砂桶内,周围用石英砂填充,在砂桶的上层用石英砂与水玻璃混合物覆盖并捣实,干燥后形成固化层,可以防止在离心过程中砂桶内填充的石英砂甩出。然后砂桶放在电阻加热炉内加热到850℃,并保温2h,然后将将耐热钢砂桶从电阻炉内取出并安装在真空炉内的离心盘上;
26.将合金原料放入坩埚,在真空炉内抽至4
×
10-1
pa真空状态下熔炼15分钟至合金全部熔化,确定合金的化学成分为cu-0.43cr-0.22zr-0.092mg(wt%),合金全部熔化后保温20分钟;
27.停止抽真空,向真空炉内充入氩气至真空炉内压强为0.08mpa,开启真空炉离心控
制系统,调至离心转速为300r/min,待离心盘平稳转动后,在20秒内将合金液浇注到熔模模壳中,浇注温度为1250℃;
28.浇注结束后,真空炉离心控制系统持续运行20分钟,使合金液凝固为铸件,铸件在熔模模壳内缓慢冷却至室温,然后破壳清理,取出铸件即为含有纳米铬相的铜合金铸件。
29.实施例3
30.将熔模模壳定位在耐热钢砂桶内,周围用石英砂填充,在砂桶的上层用石英砂与水玻璃混合物覆盖并捣实,干燥后形成固化层,可以防止在离心过程中砂桶内填充的石英砂甩出。然后砂桶放在电阻加热炉内加热到850℃,并保温2h,然后将将耐热钢砂桶从电阻炉内取出并安装在真空炉内的离心盘上;
31.将合金原料放入坩埚,在真空炉内抽至4
×
10-1
pa真空状态下熔炼12分钟至合金全部熔化,确定合金的化学成分为cu-0.43cr-0.22zr-0.092mg(wt%),合金全部熔化后保温20分钟;
32.停止抽真空,向真空炉内充入氩气至真空炉内压强为0.08mpa,开启真空炉离心控制系统,调至离心转速为300r/min,待离心盘平稳转动后,在15秒内将合金液浇注到熔模模壳中,浇注温度为1250℃;
33.浇注结束后,真空炉离心控制系统持续运行15分钟,使合金液凝固为铸件,铸件在熔模模壳内缓慢冷却至室温,然后破壳清理,取出铸件即为含有纳米铬相的铜合金铸件。
34.上述实施例中,由于采用的浇注系统的特点,浇注速度不能过快,因为如浇注速度过快,容易卷入气泡和夹杂,金属液体不利于从直浇道的底部向横浇道分散,从而不利于形成底注式浇注。但是,浇注速度又不能太小,甚至导致金属液出现断流,容易使铸件产生浇不足和冷隔等缺陷。因此,在浇注过程中应该合理操作,浇注速度先慢后快,避免出现金属液断流的情况。一般在15秒左右浇注充型完毕。
35.为了保证金属液体在离心力的作用下凝固,在浇注结束后离心机持续运行15分钟左右,直至铸件凝固。为了防止铸件冷却速度大而产生应力集中导致产生裂纹,要求铸件在耐热钢砂桶内缓慢冷却至室温。然后破壳清理,取出铸件,切除浇注系统。
36.由前所述,影响铸件质量的工艺参数主要来源于两方面:熔炼过程和浇注过程。熔炼过程中的真空度、熔体温度控制、保温时间的控制以及浇注过程中的浇注速度、离心转速等参数都影响到铸件的质量。如何选择工艺参数的数值,实现彼此之间的合理匹配,是成功进行实验和获得高质量铸件的保证。
37.浇注温度过高,则容易导致金属液体过烧,造成cr、zr元素的过多损失;而浇注温度过低,则导致金属液体流动性、充型能力变差。因此应该合理的确定浇注温度。
38.浇注过程中,浇注速度应合理控制,浇注太快,导致浇口杯内金属液过多,容易形成紊流,甚至金属液溢出浇口杯等现象,浇注速度太小,则导致金属液温度降低太快,降低了金属液的流动性。因此,浇注过程中,应该保持金属液体均匀的浇入模壳,不允许中间过程断流。
39.采用非真离心浇注工艺,利用离心力的作用来增加铸件的致密度,并能有效防止铸件内部出现缩孔、缩松等缺陷。离心转速越高,铸件的质量越好,但是还应该综合考虑设备的额定转速以及模壳的承受能力来确定转速。
40.取实施例1-3制得的含有纳米铬相的铜合金铸件,以实施例3制得含有纳米铬相的
铜合金铸件为例,其tem图、xrd结果、hrtem图、衍射斑点及标定分别如图1、图2所示,从图1中可以看出中细小弥散的黑色相为单质cr,从图2中可以进一步证明图1中细小弥散的黑色相为单质cr,说明该铜合金铸件的铸态组织中存在大量的铬纳米粒子。
41.该铜合金铸件经过时效热处理后,抗拉强度可达580mpa,屈服强度达到428mpa,延伸率达到25.3%,电导率达到80.6%iacs,可以用于制作核潜艇惯性导航用连接件,可以广泛应用于集成电路和半导体器件的引线框架材料、电气化铁路接触线、触头材料、冶金连铸用结晶器以及高科技领域。
42.本发明的技术方案不限于上述具体实施例的限制,凡是根据本发明的技术方案做出的技术变形,均落入本发明的保护范围之内。
再多了解一些
本文用于企业家、创业者技术爱好者查询,结果仅供参考。