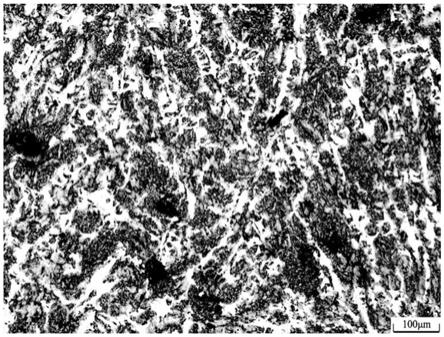
1.本发明涉及轧辊制造技术领域,尤其是一种中厚板轧机用抗表面粗糙轧辊的制备方法。
背景技术:
2.当前中厚板轧线工作辊均使用高镍铬,部分轧线已开始使用高铬钢、高铬铁及高速钢轧辊,对于中厚板轧线上用的球铁辊尚无相关研究,而球铁材质在型钢-轨梁轧线作为开坯轧机用辊已成功使用,国外加拿大evraz regina炉卷轧机及土耳其某热连轧粗轧机架一直使用球铁辊作为粗轧工作辊。球铁辊在基体中均匀分布一定的石墨,均有良好的导热及润滑性能,韧性良好,较好的适应中厚板轧线工作辊需求辊面保持能力需求。但常规球铁材质相较于常规高镍铬等材质耐磨性略低,整体添加高合金容易对辊颈组织及性能产生不利影响。球铁因含有一定量的石墨,在轧制过程中起到润滑作用,起到抗表面粗糙的作用。
3.如何针对中厚板轧线用辊针对性的设计材质,如何确定制备工艺,都是开发中厚板轧线用工作辊急需解决的问题。
技术实现要素:
4.本发明需要解决的技术问题是提供一种中厚板轧机用抗表面粗糙轧辊的制备方法,能够提高轧制行业轧辊抗冲击以及抗热疲劳高耐磨及高辊面保持能力的性能,提升轧辊质量。
5.为解决上述技术问题,本发明所采用的技术方案是:
6.一种中厚板轧机用抗表面粗糙轧辊的制备方法,包括以下步骤:
7.步骤1、采用废钢、镍铁、钒铁、铬铁、钼铁、电极粉作为原料,采用工频炉分别冶炼轧辊外层铁水和轧辊芯部铁水,直至熔炼成分达到设计的成分要求;
8.轧辊外层化学成分及各成分的重量百分含量为:c2.8~4.0%,si0.5~3.0%,mn0.2~1.2%,cr0.3-2.0%,ni0.5-6.0%,mo0.2-3.0%,w v nb≤1.0%,p≤0.10%,s≤0.1%,余量为fe和不可避免的杂质;轧辊芯部化学成分及各成分的重量百分含量为:c2.5~4.0%,si1.0~4.0%,mn0.1~1.0%,cr≤1.0%,ni≤2.0%,mo0.01-2.0%,w v nb≤0.8%,p≤0.10%,s≤0.1%,余量为fe和不可避免的杂质;
9.步骤2、熔炼成分达到设计的成分要求后,轧辊外层铁水及轧辊芯部铁水均送电加热后出炉,降温后离心浇注,离心浇注时进行球化孕育;
10.步骤3、离心浇注完毕120-200h后冷开箱,冷开箱后进行粗加工;
11.步骤4、粗加工完毕后采用差温热处理方式对轧辊辊身进行正火加热并整体回火处理;
12.步骤5、正火回火结束后进行精加工、检测直至轧辊成品。
13.本发明技术方案的进一步改进在于:步骤1中,轧辊外层铁水的熔炼温度为1400-1700℃;轧辊芯部铁水的熔炼温度为1300-1600℃。
14.本发明技术方案的进一步改进在于:步骤1中,轧辊外层化学成分及各成分的重量百分含量为:c2.8~4.0%,si1.0~1.25%,mn0.8~1.0%,cr0.3-2.0%,ni1.5-3.2%,mo0.5-3.0%,w v nb≤0.15%,p≤0.07%,s≤0.08%,余量为fe和不可避免的杂质;轧辊芯部化学成分及各成分的重量百分含量为:c2.85~3.13%,si1.4~1.5%,mn0.7~0.80%,cr≤0.05%,ni≤0.25%,mo0.02-0.1%,w v nb≤0.06%,p≤0.08%,s≤0.09%,余量为fe和不可避免的杂质。
15.本发明技术方案的进一步改进在于:步骤2中,送电加热至温度为1500-1800℃后出炉,温度降至1200-1500℃时离心浇注。
16.本发明技术方案的进一步改进在于:步骤2中,轧辊外层铁水采用翻包铁水包浇注,浇注时随浇注铁水量进行球化孕育,球化剂加入量为轧辊外层铁水量的0.2-1.5%;
17.轧辊芯部铁水采用底漏式铁水包或翻包浇注,浇注时采用包底加入球化剂的方式进行球化孕育,球化剂上方采用10-20mm厚度钢板压盖,并在钢板周围采用废钢屑覆盖,球化剂加入量为轧辊芯部铁水量的0.2-1.5%。
18.本发明技术方案的进一步改进在于:球化孕育时,孕育剂为硅铁、硅钙及硅锆合金、锰铁合金中的任意一种或几种;球化剂是稀土镁、富铈稀土中的一种或两种。
19.本发明技术方案的进一步改进在于:步骤4中,差温热处理方式选择在炉体温度为900-1150℃时对粗加工后的轧辊外层加热,加热时间为60-300min;冷却方式为喷雾10-80min、吹风30-120min后空冷至轧辊外层温度为200-450℃时回火,回火温度为460-600℃,保温时间为20-60h。
20.本发明技术方案的进一步改进在于:步骤4中,差温热处理方式采用对粗加工后的轧辊整体加热方式进行,加热温度为900-1150℃,加热时间为60-300min;冷却方式为喷雾20-90min、吹风30-120min后空冷至辊温200-450℃回火,回火温度为460-600℃,保温时间为20-60h。
21.本发明技术方案的进一步改进在于:步骤4中的差温热处理方式采用准差温方式进行,对粗加工后的轧辊采用350-500℃预热20-50h,然后以炉体最大升温速率进行升温,升温至1000-1100℃保温30-50h,冷却方式为喷雾20-90min、吹风30-120min后空冷至辊温200-450℃回火,回火温度为460-600℃,保温时间为20-60h。
22.本发明技术方案的进一步改进在于:当轧辊外层的ni的重量百分含量达到1.5%以上时,步骤4中的热处理方式采用退火工艺替代,退火温度为450-650℃,退火时间为30-100h。
23.由于采用了上述技术方案,本发明取得的技术进步是:
24.1、本发明对球铁材质成分、制造方式、球化、孕育工艺、浇注工艺等铸造工艺参数及热处理工艺进行了研究,通过各合金元素在球铁基体中的作用机理,对材质组分进行了专项设计,保证球铁产品外层具有良好耐磨性的同时,具备良好的辊面保持能力。
25.2、本发明通过形成石墨润滑相,在实际使用过程中通过石墨的润滑作用减少摩擦磨损带来轧辊辊耗,延长轧辊使用寿命,通过石墨良好的导热性能防止在使用过程中急冷急热导致的收缩不一致而产生热裂纹。
26.3、本发明采用离心浇注复合的方式进行制备,保证了轧辊的外层高合金、芯部高韧性等良好的综合性能。
附图说明
27.图1是本发明制备的中厚板轧机用抗表面粗糙轧辊放大50倍的酸腐蚀前石墨组织图;
28.图2是本发明制备的中厚板轧机用抗表面粗糙轧辊酸腐蚀后的基体组织图。
具体实施方式
29.下面结合附图及实施例对本发明做进一步详细说明:
30.一种中厚板轧机用抗表面粗糙轧辊的制备方法,包括以下步骤:
31.步骤1、采用废钢、镍铁、钒铁、铬铁、钼铁、电极粉作为原料,采用工频炉分别冶炼轧辊外层铁水和轧辊芯部铁水,轧辊外层铁水的熔炼温度为1400-1700℃,轧辊芯部铁水的熔炼温度为1300-1600℃,直至熔炼成分达到设计的成分要求;
32.镍铁可用镍板替代、钼铁可同合金钼替代,上述物料也可以是多元合金的化合物,只要成分配比满足合金范围要求即可。
33.轧辊外层化学成分及各成分的重量百分含量为:c2.8~4.0%,si0.5~3.0%,mn0.2~1.2%,cr0.3-2.0%,ni0.5-6.0%,mo0.2-3.0%,w v nb≤1.0%,p≤0.10%,s≤0.1%,余量为fe和不可避免的杂质;轧辊芯部化学成分及各成分的重量百分含量为:c2.5~4.0%,si1.0~4.0%,mn0.1~1.0%,cr≤1.0%,ni≤2.0%,mo0.01-2.0%,w v nb≤0.8%,p≤0.10%,s≤0.1%,余量为fe和不可避免的杂质;
34.当w v nb≤1.0%或w v nb≤0.8%时,w、v、nb的成分为三种全有或任意两种或任意一种或没有。
35.优选的,轧辊外层化学成分及各成分的重量百分含量为:c2.8~4.0%,si1.0~1.25%,mn0.8~1.0%,cr0.3-2.0%,ni1.5-3.2%,mo0.5-3.0%,w v nb≤0.15%,p≤0.07%,s≤0.08%,余量为fe和不可避免的杂质;轧辊芯部化学成分及各成分的重量百分含量为:c2.85~3.13%,si1.4~1.5%,mn0.7~0.80%,cr≤0.05%,ni≤0.25%,mo0.02-0.1%,w v nb≤0.06%,p≤0.08%,s≤0.09%,余量为fe和不可避免的杂质。
36.步骤2、熔炼成分达到设计的成分要求后,轧辊外层铁水及轧辊芯部铁水均送电加热至温度为1500-1800℃时出炉,温度降至1200-1500℃时离心浇注,离心浇注时进行球化孕育;
37.轧辊外层铁水采用翻包铁水包浇注,浇注时随浇注铁水量进行球化孕育,球化剂加入量为轧辊外层铁水量的0.2-1.5%;
38.轧辊芯部铁水采用底漏式铁水包或翻包浇注,浇注时采用包底加入球化剂的方式进行球化孕育,球化剂上方采用10-20mm厚度钢板压盖,并在钢板周围采用废钢屑覆盖,球化剂加入量为轧辊芯部铁水量的0.2-1.5%。
39.球化孕育时孕育剂的种类为硅铁、硅钙及硅锆合金、锰铁合金中的任意一种或几种;球化剂是稀土镁、富铈稀土中的一种或两种。
40.步骤3、离心浇注完毕120-200h后冷开箱,冷开箱后进行粗加工,粗加工时辊身直径方向留量5-15mm,轴向留量5-200mm;轴向余量可根据炉体尺寸进行加长;
41.步骤4、粗加工完毕后采用差温热处理方式对轧辊辊身进行正火加热并整体回火处理;
42.差温热处理方式有三种:
43.(1)差温热处理方式选择在炉体温度为900-1150℃时对粗加工后的轧辊外层加热,加热时间为60-300min;冷却方式为喷雾10-80min、吹风30-120min后空冷至轧辊外层温度为200-450℃时回火,回火温度为460-600℃,保温时间为20-60h。
44.(2)差温热处理方式采用对粗加工后的轧辊整体加热方式进行,加热温度为900-1150℃,加热时间为60-300min;冷却方式为喷雾20-90min、吹风30-120min后空冷至辊温200-450℃回火,回火温度为460-600℃,保温时间为20-60h。
45.(3)差温热处理方式采用准差温方式进行,对粗加工后的轧辊采用350-500℃预热20-50h,然后以炉体最大升温速率进行升温,升温至1000-1100℃保温30-50h,冷却方式为喷雾20-90min、吹风30-120min后空冷至辊温200-450℃回火,回火温度为460-600℃,保温时间为20-60h。
46.另,当轧辊外层的ni的重量百分含量达到1.5%以上时,步骤4中的处理方式采用退火工艺替代,退火温度为450-650℃,退火时间为30-100h。
47.步骤5、正火回火结束后进行精加工、检测直至轧辊成品。
48.实施例1
49.一种中厚板轧机用抗表面粗糙轧辊的制备方法,包括以下步骤:
50.步骤1,以废钢、镍铁、钒铁、铬铁、钼铁、电极粉作为原料,采用中频炉冶炼,达到球铁设计成分范围:轧辊外层铁水化学成分及各成分的重量百分含量为:c3.33%,si1.1%,mn0.9%,p0.05%,s0.06%,cr0.8%,ni2.1%,mo0.85%,w v nb=0.15%,余量为fe和不可避免的杂质;轧辊芯部铁水化学成分及各成分的重量百分含量为:c3.01%,si1.5%,mn0.8%,p0.08%,s0.09%,cr0.05%,ni0.1%,mo0.1%,w v nb=0.06%,余量为fe。
51.步骤2,轧辊外层铁水在温度1610℃熔炼,成分达到设计要求后升温至1630℃后出炉离心浇注,浇注铁水中加入0.35%的稀土镁球化剂,随流加入硅钙孕育剂,轧辊芯部铁水熔炼温度为1445℃,浇注温度为1355℃;
52.步骤3,离心浇注完毕后150h冷开箱,粗加轴向留量25mm,径向直径方向留量12mm;
53.步骤4,采用差温加热的方式热处理,在990℃加热230min,辊身喷雾60min,吹风30min后空冷,辊身400℃时装炉回火35h。
54.步骤5,正火回火结束后进行精加工、检测直至轧辊成品。
55.实施例2
56.一种中厚板轧机用抗表面粗糙轧辊的制备方法,包括以下步骤:
57.步骤1,以废钢、镍铁、钒铁、铬铁、钼铁、电极粉作为原料,采用中频炉冶炼,达到球铁设计成分范围:
58.轧辊外层铁水化学成分及各成分的重量百分含量为:c2.80%,si1.0%,mn0.8%,p0.06%,s0.08%,cr0.9%,ni2.89%,mo0.79%,w v nb=0.12%,余量为fe;轧辊芯部铁水化学成分及各成分的重量百分含量为:c2.95%,si1.45%,mn0.75%,p0.06%,s0.08%,cr0.03%,ni0.25%,mo0.05%,w v nb=0.03%,余量为fe和不可避免的杂质。
59.步骤2,轧辊外层铁水在温度1611℃熔炼,成分达设计要求后升温至1659℃后出炉离心浇注,浇注温度铁水中加入0.36的稀土镁球化剂,随流加入硅钙孕育剂,轧辊芯部铁水熔炼温度为1486℃,浇注温度为1350℃;
60.步骤3,离心浇注完毕后192h冷开箱,粗加轴向留量22mm,径向直径方向留量15mm;
61.步骤4,采用退火方式进行热处理,退火温度580℃,退火保温时间60h;
62.步骤5,正火回火结束后进行精加工、检测直至轧辊成品。
63.实施例3
64.一种中厚板轧机用抗表面粗糙轧辊的制备方法,包括以下步骤:
65.步骤1,以废钢、镍铁、钒铁、铬铁、钼铁、电极粉作为原料,采用中频炉冶炼,达到球铁设计成分范围:
66.轧辊外层铁水化学成分及各成分的重量百分含量为:c2.92%,si1.25%,mn0.88%,p0.06%,s0.05%,cr1.56%,ni2.53%,mo0.91%,w v nb=0.11%,余量为fe;轧辊芯部铁水化学成分及各成分的重量百分含量为:c2.93%,si1.43%,mn0.76%,p0.03%,s0.05%,cr0.02%,ni0.22%,mo0.06%,w v nb=0.02%,余量为fe和不可避免的杂质。
67.步骤2,外层在温度1585℃熔炼,成分达标后升温至1655℃后出炉离心浇注,浇注温度铁水中加入0.39%的稀土镁球化剂,随流加入硅钙孕育剂,芯部钢水熔炼温度为1470℃,浇注温度为1340℃;
68.步骤3,离心浇注完毕后199h冷开箱,粗加轴向留量25mm,径向直径方向留量15mm;
69.步骤4,采用准差温加热的方式热处理,在400℃预热40h,1030℃加热265min,辊身喷雾61min,吹风55min后空冷,辊身450℃时装炉回火60h;
70.步骤5,正火回火结束后进行精加工、检测直至轧辊成品。
71.实施例4
72.一种中厚板轧机用抗表面粗糙轧辊的制备方法,包括以下步骤:
73.步骤1,以废钢、镍铁、钒铁、铬铁、钼铁、电极粉作为原料,采用中频炉冶炼,达到球铁设计成分范围:
74.轧辊外层铁水化学成分及各成分的重量百分含量为:c3.23%,si1.1%,mn1.0%,p0.07%,s0.07%,cr1.65%,ni3.20%,mo0.73%,w v nb=0.11%,余量为fe和不可避免的杂质;轧辊芯部铁水化学成分及各成分的重量百分含量为:c2.93%,si1.43%,mn0.72%,p0.03%,s0.05%,cr0.02%,ni0.22%,mo0.06%,w v nb=0.02%,余量为fe和不可避免的杂质。
75.步骤2,轧辊外层铁水在温度1630℃熔炼,成分达标后升温至1660℃后出炉离心浇注,浇注铁水中加入0.36%的稀土镁球化剂,随流加入硅钙孕育剂,芯部钢水熔炼温度为1490℃,浇注温度为1383℃;
76.步骤3,离心浇注完毕后200h冷开箱,粗加轴向留量20mm,径向直径方向留量13mm;
77.步骤4,采用差温加热的方式热处理,在9650℃加热270min,辊身喷雾63min,吹风60min后空冷,辊身460℃时装炉回火70h;
78.步骤5,正火回火结束后进行精加工、检测直至轧辊成品。
79.实施例5
80.一种中厚板轧机用抗表面粗糙轧辊的制备方法,包括以下步骤:
81.步骤1,以废钢、镍铁、钒铁、铬铁、钼铁、电极粉作为原料,采用中频炉冶炼,达到球铁设计成分范围;
82.轧辊外层铁水化学成分及各成分的重量百分含量为:c3.12%,si1.05%,mn0.90%,p0.06%,s0.05%,cr1.86%,ni2.98%,mo0.69%,w v nb=0.10%,余量为fe和不可避免的杂质;轧辊芯部铁水化学成分及各成分的重量百分含量为:c3.13%,si1.41%,mn0.71%,p0.03%,s0.03%,cr0.02%,ni0.21%,mo0.05%,w v nb=0.03%,余量为fe和不可避免的杂质。
83.步骤2,轧辊外层铁水在温度1585℃熔炼,成分达标后升温至1655℃后出炉离心浇注,浇注温度铁水中加入0.31%的稀土镁球化剂,随流加入硅钙孕育剂,轧辊芯部铁水熔炼温度为1490℃,浇注温度为1350℃;
84.步骤3,离心浇注完毕后198h冷开箱,粗加轴向留量23mm,径向直径方向留量13mm,
85.步骤4,采用退火方式热处理,退火温度560℃,退火保温时间75h;
86.步骤5,正火回火结束后进行精加工、检测直至轧辊成品。
87.实施例6
88.一种中厚板轧机用抗表面粗糙轧辊的制备方法,包括以下步骤:
89.步骤1,以废钢、镍铁、钒铁、铬铁、钼铁、电极粉作为原料,采用中频炉冶炼,达到球铁设计成分范围:
90.轧辊外层铁水化学成分及各成分的重量百分含量为:c4.0%,si1.03%,mn0.89%,p0.05%,s0.03%,cr2.0%,ni3.02%,mo3.0%,w v nb=0.08%,余量为fe和不可避免的杂质;轧辊芯部铁水化学成分及各成分的重量百分含量为:c2.85%,si1.40%,mn0.70%,p0.04%,s0.05%,cr0.03%,ni0.13%,mo0.02%,w v nb=0.05%,余量为fe和不可避免的杂质。
91.步骤2,轧辊外层铁水在温度1590℃熔炼,成分达标后升温至1660℃后出炉离心浇注,浇注铁水中加入0.33%的稀土镁球化剂,随流加入硅钙孕育剂,轧辊芯部铁水熔炼温度为1490℃,浇注温度为1339℃;
92.步骤3,离心浇注完毕后182h冷开箱,粗加轴向留量22mm,径向直径方向留量13mm;
93.步骤4,采用差温加热的方式热处理,在975℃加热285min,辊身喷雾65min,吹风62min后空冷,辊身463℃时装炉回火72h;
94.步骤5,正火回火结束后进行精加工、检测直至轧辊成品。
95.实施例7
96.一种中厚板轧机用抗表面粗糙轧辊的制备方法,包括以下步骤:
97.步骤1,以废钢、镍铁、钒铁、铬铁、钼铁、电极粉作为原料,采用中频炉冶炼,达到球铁设计成分范围:
98.轧辊外层铁水化学成分及各成分的重量百分含量为:c3.33%,si1.15%,mn0.95%,p0.05%,s0.03%,cr0.3%,ni1.5%,mo0.5%,w v nb=0.08%,余量为fe和不可避免的杂质;轧辊芯部铁水化学成分及各成分的重量百分含量为:c2.95%,si1.30%,mn0.65%,p0.04%,s0.05%,cr0.03%,ni0.15%,mo0.02%,w v nb=0.05%,余量为fe和不可避免的杂质。
99.步骤2,轧辊外层铁水在温度1600℃熔炼,成分达标后升温至1650℃后出炉离心浇注,浇注铁水中加入0.32%的稀土镁球化剂,随流加入硅钙孕育剂,轧辊芯部铁水熔炼温度为1480℃,浇注温度为1340℃;
100.步骤3,离心浇注完毕后181h冷开箱,粗加轴向留量22mm,径向直径方向留量13mm;
101.步骤4,采用差温加热的方式热处理,在980℃加热288min,辊身喷雾67min,吹风60min后空冷,辊身465℃时装炉回火73h;
102.步骤5,正火回火结束后进行精加工、检测直至轧辊成品。
103.对照例
104.为常规生产的高镍铬轧辊。
105.取实施例1~实施例7及对照例制备的轧辊进行试样拉伸力学性能检测,性能检测执行国家标准gb/t228.检测结果见表1。
106.表1实施例及对照例产品性能检测结果
[0107][0108][0109]
由以上表1可知,通过对采用本发明方法制备的中厚板轧机用抗表面粗糙轧辊(球铁辊)和常规生产的高镍铬轧辊的材质进行相对耐磨性及冷热疲劳性能试验可知,中厚板轧机用抗表面粗糙轧辊(球铁辊)的工作层相对耐磨性在4.15-5.21之间,要优于常规生产的高镍铬轧辊的工作层相对而磨性2.23;同时,中厚板轧机用抗表面粗糙轧辊(球铁辊)的冷热疲劳性能在975-990之间也远远高于常规生产的高镍铬轧辊的冷热疲劳性能585。
[0110]
由图1和图2可知:
[0111]
图1是本发明制备的中厚板轧机用抗表面粗糙轧辊放大50倍的酸腐蚀前石墨组织图,图中黑色球状组织为石墨,石墨圆整,形态良好。
[0112]
图2是本发明制备的中厚板轧机用抗表面粗糙轧辊酸腐蚀后的基体组织图,组织为索氏体 碳化物。
[0113]
由此可知,本发明制备的中厚板轧机用抗表面粗糙轧辊(球铁辊)在基体中均匀分布一定的石墨,均有良好的导热及润滑性能,韧性良好,能较好的适应中厚板轧线工作辊需求辊面保持能力需求。
[0114]
本发明的工艺参数(如质量百分含量、温度、时间、留量等)的上下限取值以及区间
值都能实现本发明,在此不一一列举实施例。
[0115]
综上,根据性能检测结果可知,本发明方法制备的中厚板轧机用抗表面粗糙轧辊(球铁辊)辊身外层高耐磨、芯部高韧性,较高镍铬轧辊耐磨性更好,冷热疲劳性能更好,在实际使用过程中,能更好的适应中厚板轧机的工况特点。
再多了解一些
本文用于企业家、创业者技术爱好者查询,结果仅供参考。