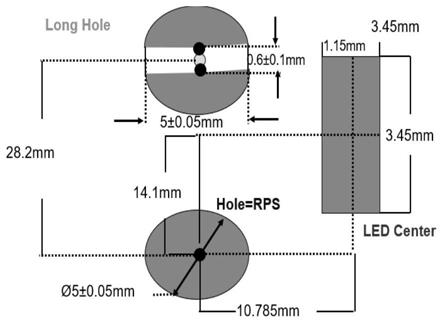
一种基于omar工艺技术的节拍提升方法
技术领域
1.本发明涉及led位置度装配技术领域,具体涉及一种基于omar工艺技术的节拍提升方法。
背景技术:
2.在汽车电子行业中,为保证led精密装配,采用omar(optically validated milling after reflow)工艺技术,使用的工艺设备称之为led calibration machine,但目前的工艺技术中,生产节拍时间较长,导致单位时间内的生产产能较低,因而对应的,生产成本较高。
技术实现要素:
3.发明目的:为了克服现有技术的不足,本发明提供一种基于omar工艺技术的节拍提升方法,该方法可以解决由于生产节拍时间较长,导致的生产产能较低,生产成本较高的问题。
4.技术方案:本发明所述的基于omar工艺技术的节拍提升方法,该方法包括以下步骤:
5.(1)将待处理led产品载入到搭载了相机的钻孔设备,所述钻孔设备包括钻孔的铣刀,且所述钻孔设备与信息管理系统连接;
6.(2)所述钻孔设备对待处理led产品的条形码进行读取,并将相关信息传输给所述信息管理系统,信息管理系统记录并比对,进而实现待处理led灯实时状态的追溯;
7.(3)若信息读取成功,则所述钻孔设备对准led产品进行基准标记识别,若信息读取失败,则报警提示,退出生产,人工确认问题所在;
8.(4)先在pcb板边上钻一个rps孔,即参考定位孔,然后相机识别该孔径的实际大小,并根据获取的实际数据进行铣刀磨损度的补偿;
9.(5)若钻孔识别成功,则进行步骤6,否则,报警提示钻孔识别异常,退出生产;
10.(6)针对pcb panel(1panel=24pcs,1pcs=1个led成品)中的第一个pcs产品,先识别led中心位置(采用长通滤波蓝光ccd精准计算led中心位置偏移量),并采用一定的速度对rps孔的孔径进行扩孔作业,使之孔径达到工艺需求的5
±
0.05mm;同时满足led中心位置和rps孔的孔径中心位置度偏差控制在0.2mm内,然后采用一定的速度再对腰孔进行扩孔作业,达到同样的工艺需求的5
±
0.05mm;在完成rps孔和腰孔进行扩充作业后,ccd重新检测led中心位置和孔径大小。其目的是把检测结果反馈给信息管理系统。所述中心位置偏移量参考的基准数据为rps孔中心位置和led中心两者间的相对恒定坐标;
11.(7)循环步骤6,完成对第一个panel中的其它pcs产品识别-扩孔-再检测作业;
12.(8)对每个panel的若干pcs中的led产品进行抽样检测,抽样检测的每个led产品具体包括:相机重新识别led中心位置,并对所钻的rps孔径和腰孔进行实际检测,检出的孔径实际尺寸进行信息显示及反馈给信息管理系统。
13.进一步的,包括:
14.所述长通滤波蓝光ccd为相机自带的。
15.进一步的,包括:
16.所述rps孔、腰孔和led中心位置的位置关系为:
17.led中心与rps孔相对恒定坐标为:x:10.785mm y:14.1mm,
18.rps孔与腰孔中心位置相对恒定坐标为28.2mm。
19.进一步的,包括:
20.采用rps孔和腰孔进行led中心位置识别的方法具体为:
21.(61)把led中心所在pcba中的理论绝对坐标写入nc程序中,即钻孔程序;
22.(62)根据nc程序设定ccd自动移动至该位置;
23.(63)ccd自动抓取led中心在经过reflow后实际的坐标值;
24.(64)ccd实际测量的坐标和理论坐标对比,计算偏移量;
25.(65)把偏移值补偿到led中心与rps孔相对坐标x10.785mm/y14.1mm中;
26.(66)根据步骤(65)的数值,进行扩充rps孔;
27.(67)根据rps孔扩充腰孔;
28.进一步的,包括:
29.所述根据获取的实际数据进行铣刀磨损度的补偿,具体补偿方法为:
30.(41)在pcb板边上钻一个rps孔,该孔尺寸在钻孔程序中设定理论值,如果是未经磨损的铣刀,相机实测该孔径,实测值就等于理论值;
31.(42)由于铣刀使用时有磨损,那么钻出的孔径相机实测值就小于理论值,那么磨损值=理论值-实测值;
32.(43)在正式钻led旁定位孔前,把所述磨损值以公式形式补偿并写到nc程序中;
33.(44)以此理论类推,在执行pcb内led产品钻孔时,实际钻孔的尺寸半径r执行公式(=磨损值 nc程序中设定的半径r),从而实现铣刀磨损度补偿的作用。
34.进一步的,包括:
35.对rps孔的孔径进行扩孔作业和对腰孔进行扩孔作业采用的速度为600mm/min~750mm/min。
36.进一步的,包括:
37.所述对rps孔的孔径进行扩孔作业和对腰孔进行扩孔作业采用的速度为700mm/min。
38.进一步的,包括:
39.所述步骤(8)中,对每个panel的1~24(pcs)中的led灯均进行抽样检测。
40.进一步的,包括:
41.所述步骤(8)中,对每个panel中任意2个pcs的led灯进行抽样检测。
42.有益效果:本发明通过改变相机检查每个panel中led灯的个数实现对钻孔的节拍进行改善,优化钻孔速度,且本发明的上述改进可以克服缩减的环节带来的不稳定因素,及提速后带来的不确定因素,保证优化后稳定,恒定,整个生产过程控制在工艺需求范围中,使整体的omar工艺方法的节拍缩短,提高了生产产能。
附图说明
43.图1为本发明实施例所述的单led灯的钻孔流程示意图;
44.图2为本发明实施例所述的改进后的omar工艺方法的流程示意图;
45.图3为本发明实施例所述的改进之前的各环节具体节拍时间占比示意图;
46.图4为本发明实施例所述的对孔径检查环节中两种改进方案导致的铣刀寿命与孔径尺寸的趋势图;
47.图5为本发明实施例所述的不同钻孔优化速度与节拍优化的关系示意图。
具体实施方式
48.下面将结合本发明实施例中的附图,对本发明实施例中的技术方案进行清楚、完整地描述,显然,所描述的实施例仅仅是本发明一部分实施例,并不是全部的实施例。基于本发明中的实施例,本领域普通技术人员在没有做出创造性劳动前提下所获得的所有其他实施例,都属于本发明保护的范围。
49.本发明提供一种基于omar工艺技术的节拍提升方法,omar的基本原理就是高精密钻孔设备搭载相机,先识别smt reflow后的led中心位置,根据led中心在经过reflow(回流焊)后焊锡的拉力作用存在的微小偏差,在进行钻孔作业时,自动把其偏移量补偿到钻孔中心位置中,使led中心和钻孔中心相对位置保持恒定不变或者两者中心位置度控制在0.2mm内,从而实现高精密装配,其中,smt,即surface mounting technology(表面贴装技术)。
50.本发明将现有的omar工艺方法进行改进,包括以下步骤,如图1和2所示:
51.(1)将待处理led产品载入到搭载了相机的钻孔设备,钻孔设备包括钻孔的铣刀,且钻孔设备与信息管理系统mes连接;
52.(2)钻孔设备对待处理led产品的条形码进行读取,并将相关信息传输给所述信息管理系统mes,信息管理系统记录并比对,进而实现待处理led灯实时状态的追溯;本实施例中,panel即一大块pcb原材料,可以同时拼出n块pcb,每个pcb都是独立的一个成品件。本实施例中,led经过smt工艺贴装至pcb中,1panel拼有24个pcb,即每个pcb都有独立的一颗led在其中。
53.(3)若信息读取成功,则所述钻孔设备对准led产品进行标记识别fiducial mark,若信息读取失败,则报警提示,退出生产,人工确认问题所在;
54.(4)先在pcb板边钻一个钻孔即trimming孔,钻孔的直径为4.1mm,然后相机识别该孔径的实际大小,并根据获取的实际数据进行铣刀磨损度的补偿;
55.补偿原理说明:
56.①
在pcb板边,钻一个参考孔,其孔尺寸在nc程序中设定理论值,如果是未经磨损的铣刀,相机实测该孔径,实测值就等于理论值。
57.②
由于铣刀使用时有磨损,那么钻出的孔径相机实测值就小于理论值,那么磨损值=理论值-实测值。
58.③
在正式钻led旁定位孔时,会把磨损值以公式形式补偿并写到nc钻孔程序中。举例说明:在pcb板边,钻一个直径4.1mm的圆孔,铣刀直径为2.0mm,那么钻头就需要以1.05mm的半径画一个圆就可以了。如果相机实测值该圆直径为4mm,那么铣刀磨损值=(4.1-4)/2=0.05mm,即铣刀磨损产生的影响为实际钻孔直径4.2mm((1.05 0.05 1)mm*2)的圆,方可
达到需求值直径为4.1mm的圆。
59.④
以此理论类推,在执行pcb内led产品钻孔时,实际钻孔的尺寸半径r执行公式(=磨损值 nc程序中设定的半径r),从而实现铣刀磨损度补偿的作用。
60.(5)若钻孔识别成功,则进行步骤6,否则,报警提示钻孔识别异常,退出生产;
61.(6)针对pcb panel(1panel等于24pcs,1pcs即为一个led产品)中的第一个led产品,先识别led中心位置,采用长通滤波蓝光ccd精准计算led中心位置偏移量,并采用一定的速度对rps孔的孔径进行扩孔作业,
62.①
其中心位置偏移量参考的基准数据为rps孔中心位置(rps=reference point system)和led center两者间的相对恒定坐标(x:10.785mm y:14.1mm)。具体请参考图1所示。
63.对rps孔的孔径进行扩孔作业,使孔径达到工艺需求的5
±
0.05mm;同时满足led中心位置和rps孔rps,reference point system的孔径中心位置度偏差控制在0.2mm内,然后采用一定的速度再对腰孔进行扩孔作业,达到同样的工艺需求的5
±
0.05mm。
64.①
此裸pcb(未有元器件在表面)在来料时,rps孔让pcb板厂进行预钻直径为4.5mm的孔径。
65.②
然后在我司实现smt工艺设备led位置贴装,及reflow led焊接。
66.③
鉴于led中心在经过reflow后焊锡的拉力作用存在的微小偏差,需继续对预钻的rps 4.5mm孔径进行扩孔作业,以达到产品所需的5
±
0.05mm规格。
67.④
实施
③
是建立在rps孔中心位置和led center两者间的相对恒定坐标下进行的。
68.⑤
led center与rps孔相对恒定坐标为:x:10.785mm y:14.1mm,
69.⑥
基于
⑤
,rps孔和led中心位置有恒定的x/y相对坐标条件限制。
70.⑦
只有这样才能在进行钻孔作业时,把led center偏移量补偿到钻孔中心位置中,使led center与钻孔中心相对坐标保持恒定不变或者两者中心位置度控制在0.2mm内,从而实现led高精密装配。
71.无论是rps孔还是腰孔(long hole)它的作用都是装配孔,用于成型产品的安装,都是为了实现led高精密装配。但rps孔除此功能外还起到一个参考基准定位的作用。腰孔也是pcb板厂在出厂前进行预钻直径为4.5mm的孔径,然后实现在rps孔进行扩充后y方向中心为28.2mm距离扩充到直径为5
±
0.05mm孔径的。腰孔和led中心没有直接关系,但和rps孔有直接关系,具体图示请参考图1所示。
72.其中,rps孔、腰孔和led中心位置的位置关系,腰孔和rps孔是各自独立的孔,rps孔和led中心位置有恒定的x/y相对坐标条件限制,rps孔又和腰孔两者有恒定的y方向相对坐标条件限制。
73.led中心与rps孔相对恒定坐标为:x:10.785mm y:14.1mm,
74.rps孔与腰孔中心位置相对恒定坐标为28.2mm。
75.利用rps孔和腰孔进行led中心位置的调整和识别的方法为:
76.把led center所在pcba中的理论绝对坐标写入nc程序中。
77.根据nc程序设定ccd自动移动至该位置。
78.ccd自动抓取led中心在经过reflow后实际的坐标值。
79.ccd实际测量的坐标和理论坐标对比,计算偏移量。
80.把偏移值补偿到led center与rps孔相对坐标x10.785mm/y14.1mm中。
81.根据
⑤
的数值,然后进行扩充rps孔。
82.根据rps孔,扩充腰孔。
83.(7)循环步骤6,完成对第一个panel中的其它pcs产品识别-扩孔-再检测作业;
84.具体为:
85.第2pcs,和首pcs作业方式雷同,相机先识别led中心位置,通过cnc程序采用长通滤波蓝光精准计算led中心位置偏移量,并对直径为4.5mm的rps孔径进行扩孔作业,然后再对直径为4.5mm腰孔进行扩孔作业,使rps孔径和腰孔满足工艺5
±
0.05mm需求。
86.第3,4,5,6
…
24pcs,和首pcs同样作业方式。
87.上述中对rps孔的孔径进行扩孔作业和对腰孔进行扩孔作业采用的速度为600mm/min~750mm/min。具体的,对rps孔的孔径进行扩孔作业和对腰孔进行扩孔作业采用的速度为700mm/min。
88.(8)对每个panel的若干pcs中的led产品进行抽样检测,抽样检测的每个led产品具体包括:相机重新识别led中心位置,并对所钻的rps孔径和腰孔进行实际检测,检出的孔径实际尺寸进行信息显示及反馈给信息管理系统。
89.对每个panel的1~24(pcs)中的led灯均进行抽样检测。进一步地,对每个panel中任意2个pcs的led灯进行抽样检测。通过改变抽检的数量,达到节拍节省的目的。
90.上述方案是基于现有的omar技术改进得到的,生产节拍长是当前omar技术应用实践中存在的问题,1panel(24pcs)生产节拍为360s,1pcs生产节拍为15s。
91.如图3所示,改善前节拍为360s/panel,各环节具体节拍时间(具体如下图所示),发现孔径检查节拍为74.2s,钻孔节拍为258.8s,占比分别20.61%,71.89%。从上述数据得知,重点改善孔径检查节拍和钻孔节拍可实现缩减整个流程的节拍时间。
92.孔径检查环节节拍改善,即涉及到步骤8的部分,考虑的方案包括:
93.方案一:钻孔后,不进行孔径检测作业可行性?
94.方案二:对于24pcs,取样2pcs孔径检测可行性?不检测或者取样检测怎么实现位置度和扩孔直径满足工艺需求?
95.上述问题,从工艺pfmea角度分析否决方案一,因为存在数据失控风险。方案二可行性较好,通过每panel取样2pcs进行孔径检测,可实时监控数据趋势走向,满足工艺需求,且可实现节拍节省;同时对于影响位置度和孔直径精度的唯一变量-铣刀磨损度,通过验证铣刀使用寿命进行管控,定义铣刀使用寿命在13m时,设备自动更换铣刀,从而保证位置度和扩孔孔径精度在受控范围内,如图4所示,其中,pfmea:process failure mode and effects analysis(潜在失效模式及影响分析)。
96.综上所述,修改cnc控制程序,执行钻孔后,相机检查实际孔径尺寸环节由每panel检测24pcs变更至每panel抽样检测2pcs,经生产验证,节拍节省68s/panel,实际生产时间为292s/panel,当然,该抽样检测可放在所有的pcs钻孔环节结束之后,也可在某个pcs钻孔以后对该led灯中的相关孔进行检测,本技术的附图2是将抽样检测放在所有的钻孔环节结束后。
97.如图5所示,对步骤6中钻孔节拍的改善,鉴于钻孔节拍为258.8s,占比71.89%,优
化钻孔速度:
98.由250mm/min至400mm/min,在首次节拍节省的基础上继续节省至260s/panel。
99.由400mm/min至500mm/min,节拍优化至227s/panel。
100.由500mm/min至600mm/min,节拍优化至207s/panel。
101.由600mm/min至700mm/min,节拍优化至最终193s/panel。
102.由700mm/min至800mm/min,节拍可改善至180s/panel,但钻孔边缘出现毛刺异常,不符合工艺需求。
103.综上,以700mm/min为优化后最终速度,最终节拍为193s/panel。
104.上述的优化基于设备的cmk≧1.67,工艺的cpk≧1.67。鉴于优化前,工艺管控明确提出“执行每两小时使用go-no go治具抽检检测孔径直径,且使用cmm测试位置度”的需求,为优化后数据的采集提供了良好的环境条件。上述节拍的优化,其时间跨度较长(近2个月),每一次的节拍优化,数据验证均需生产追踪10天左右,待各数据收集均在管控范围内,方可进行下一步的优化动作。其中,cmm:coordinate measuring machine(三坐标测试仪)。
105.总结,优化前生产节拍为360s/panel,单pcs节拍为15s,通过优化nc程序中钻孔后孔径检查频次及提升钻孔速度,使优化后节拍为193s/panel,单pcs节拍为8s,达到节拍节省的目的,单位时间内提高了生产产能,降低了生产成本,经生产测试,实际效果满意度高。现场使用实用性较好是此次发明的亮点。
106.尽管已描述了本发明的优选实施例,但本领域内的技术人员一旦得知了基本创造性概念,则可对这些实施例作出另外的变更和修改。所以,所附权利要求意欲解释为包括优选实施例以及落入本发明范围的所有变更和修改。
107.显然,本领域的技术人员可以对本发明实施例进行各种改动和变型而不脱离本发明实施例的精神和范围。这样,倘若本发明实施例的这些修改和变型属于本发明权利要求及其等同技术的范围之内,则本发明也意图包含这些改动和变型在内。
再多了解一些
本文用于企业家、创业者技术爱好者查询,结果仅供参考。