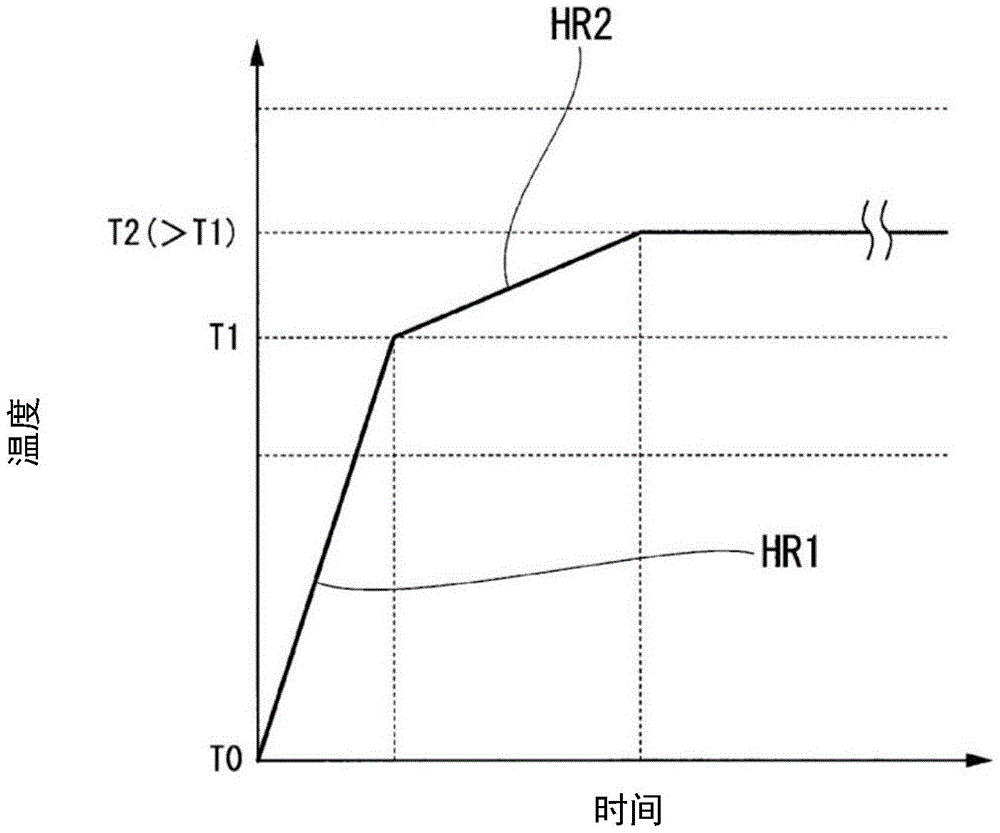
本发明涉及方向性电磁钢板的制造方法。
背景技术
方向性电磁钢板是在{110}<001>取向上集聚的晶粒(这样的晶粒也被称为高斯取向晶粒)高度地对齐、且以质量%计含有大概7%以下Si的钢板。这样的方向性电磁钢板的制造中的晶体取向的控制是通过利用被称为二次再结晶的突变性(catastrophic)的晶粒生长现象来达成的。
作为控制该二次再结晶的一种方法,在工业上实施下述方法:使抑制剂在热轧前的钢板坯加热时完全固溶后,在热轧及之后的热轧板退火工序中使其微细地析出。在该方法中,为了在热轧前的钢板坯加热时使抑制剂完全固溶,需要以1350~1400℃对钢板坯进行加热。但是,该加热温度与制造普通钢时的加热温度相比大约高200℃,因此存在下述问题:需要方向性电磁钢板的制造专用的加热炉。另外,由于需要将钢板坯加热到非常高的温度,因此还存在熔融氧化皮量增多等问题。
因此,对于在热轧前以低温对钢板坯进行加热的技术,一直在进行研究开发。作为这样的技术,例如专利文献1中公开了使用通过氮化处理形成的(Al、Si)N作为抑制剂的方法。此外,在专利文献2中,作为具体的氮化处理的方法,公开了通过将脱碳退火后的钢板制成带状来进行氮化的方法。非专利文献1中公开了以带状对钢板进行氮化的情况下的氮化物的行为。
这里,在于热轧前以低温对钢板坯进行加热的技术中,脱碳退火时的一次再结晶晶粒织构的调整在控制二次再结晶方面是重要的。但是,在该技术中,有时会在脱碳退火时无法充分地形成抑制剂。在此种情况下,根据专利文献3,一次再结晶晶粒织构的粒径分布的变动系数变得大于0.6,因此一次再结晶晶粒织构变得不均匀。其结果是,存在下述问题:二次再结晶晶粒组织变得不均匀、不稳定。
因此,一直在深入地进行有关二次再结晶的控制因子即一次再结晶晶粒织构的研究。在这样的研究中,认知到:一次再结晶晶粒织构中的{411}取向晶粒对{110}<001>二次再结晶晶粒的优先生长产生影响。例如,在专利文献4中公开了下述技术:在将脱碳退火后的一次再结晶晶粒织构的I{111}/I{411}的比率调整至3.0以下之后,通过对钢板实施氮化处理来强化抑制剂。专利文献4中公开了通过抑制剂的强化而能够在工业上稳定地制造磁通密度高的方向性电磁钢板。这里,I{111}及I{411}分别是{111}及{411}面与板面平行的晶粒的存在比例,表示通过X射线衍射测定在板厚为1/10层中测定的衍射强度值。
然后,在进行有关一次再结晶晶粒织构的研究中,得知:脱碳退火时时的加热温度的控制是控制一次再结晶后的晶粒组织的有效方法。例如,在专利文献5中公开的技术中,在脱碳退火工序的加热工序(升温过程)中,从钢板温度为600℃以下的入侧温度直至到达750~900℃的范围内的到达温度为止以40℃/秒以上的加热速度对钢板进行快速加热。由此,在脱碳退火后的一次再结晶晶粒织构中将I{111}/I{411}的比率控制为3以下。进而,在之后的退火中将钢板的氧化层的氧量调整为2.3g/m2以下。在专利文献5中公开了通过上述技术来使二次再结晶稳定化。
此外,专利文献6中公开了将钢板温度成为200℃~700℃的温度范围内的加热速度设定为50℃/秒以上的技术。另外,在专利文献6中公开的技术中,在250℃以上且低于500℃的任一温度下实施1~4次处理时间为0.5~10秒的保持处理,在500℃~700℃的任一温度下实施1次或2次处理时间为0.5秒~3秒的保持处理。专利文献6中公开了通过上述这样的处理能够制造铁损偏差小的方向性电磁钢板。
这里,在脱碳退火时的加热工序中,作为快速加热钢板的装置,在专利文献5中例示出了利用辐射管等辐射热源的装置、利用激光等高能热源的设备、感应加热装置及通电加热装置等。在这些装置中,出于加热速度的自由度高、能与钢板非接触地加热、在脱碳退火炉内的设置比较容易等方面,感应加热装置尤其有利。专利文献7中公开了采用感应加热装置进行脱碳退火时的加热的技术。
但是,在采用感应加热装置对板厚比较薄的钢板进行脱碳退火的情况下,由于钢板的板厚薄,因此如果处于居里点附近的温度,则涡电流的电流浸透深度加深。因此,发生绕板宽方向截面的表层部一周的涡电流的表里抵消,涡电流变得无法流动。因此,变得难以将钢板加热至居里点以上的温度。这里,钢板的居里点为750℃左右。因此,采用感应加热装置进行的快速加热只能进行到750℃。因此,在想要将钢板加热到该温度以上的温度的情况下,无法采用感应加热装置,需要并用其它加热装置。
但是,在并用其它加热装置的情况下,出现各式各样的问题。例如,由于通电加热装置等会与钢板接触,因此不仅存在损伤钢板等问题,还会失去感应加热装置的设备上的优点。
因此,在专利文献7中公开的技术中,通过控制热轧板退火工序的退火条件,从而在热轧板退火工序后的晶粒组织中将片层间距控制为20μm以上。专利文献7中公开了下述内容:通过上这样的技术能够使脱碳退火时的加热过程的快速加热温度范围(从入侧温度至到达温度为止的温度范围)降低到能够利用感应加热装置的温度。具体而言,在专利文献7中,在脱碳退火时的加热过程中,将钢板的温度从入侧温度直至到达550~720℃的到达温度为止的加热速度设定为40℃/秒以上,然后将直至均热温度区域为止的加热速度设定为10~15℃/秒。
现有技术文献
专利文献
专利文献1:日本特公昭62-45285号公报
专利文献2:日本特开平2-77525号公报
专利文献3:日本特公平8-32929号公报
专利文献4:日本特开平9-256051号公报
专利文献5:日本特开2002-60842号公报
专利文献6:日本特开2015-193921号公报
专利文献7:日本特开2008-1983号公报
非专利文献
非专利文献1:“Materials Science Forum”204-206(1996),pp593-598
技术实现要素:
发明所要解决的课题
但是,对于专利文献7中公开的技术,如果与通过专利文献5、6中所示那样的不管加热方式的装置将快速加热进行到750~900℃左右的技术相比,依然存在无法充分享受磁特性的改善效果的问题。更具体来说,根据专利文献7中公开的技术,虽然磁通密度提高,但二次再结晶晶粒后的钢板的晶体粒径(以下也称为“二次再结晶粒径”)大径化,因此存在铁损的改善余地小这样的问题。
另一方面,在专利文献1~3中公开的技术中,如上所述,存在一次再结晶晶粒织构不均匀、不稳定的问题。因此,铁损特性不充分。根据专利文献4~6中公开的技术,虽然能够期待铁损特性的改善,但要求方向性电磁钢板进一步改善铁损特性。
再者,方向性电磁钢板的铁损通过对方向性电磁钢板施加激光热变形、赋予机械槽、赋予蚀刻槽这样的磁畴控制而得到改善,但为实现更高的铁损,要求进一步改善磁畴控制前的铁损。
本发明是鉴于上述实情而开发的,目的是提供一种能够稳定地制造进一步改善了铁损特性的方向性电磁钢板的方向性电磁钢板的制造方法。
用于解决课题的手段
本发明的发明者为了解决上述课题而反复进行了深入研究。其结果是,本发明的发明者认知到:当在脱碳退火的加热过程中采用感应加热装置对钢板进行快速加热的情况下,在从到达温度至均热温度为止的加热速度慢的情况下,二次再结晶粒径发生大径化,铁损变差。进而,本发明的发明者认知到:通过以适当的条件控制快速加热温度范围(从入侧温度至到达温度为止的温度范围)的加热速度以及从到达温度至均热温度为止的加热速度,从而可稳定地制造使二次再结晶粒径小径化、铁损特性优异的方向性电磁钢板。即,本发明的主旨如下所述。
根据本发明的某个观点,提供一种方向性电磁钢板的制造方法,其特征在于,包含下述工序:再加热工序,其在1280℃以下的温度下对下述钢板坯进行加热,所述钢板坯作为化学成分,以质量%计含有Si:2.00~4.00%、C:0.085%以下、Al:0.01~0.065%、N:0.004~0.012%、Mn:0.05~1.00%、S:0.003~0.015%,剩余部分由Fe及杂质构成;热轧工序,其对加热后的钢板坯进行热轧;热轧板退火工序,其对通过热轧工序得到的热轧板进行退火;冷轧工序,其在进行了热轧板退火工序后,对热轧板进行冷轧;脱碳退火工序,其对通过冷轧工序得到的冷轧板进行脱碳退火;和成品退火工序,其对进行了脱碳退火工序后的冷轧板进行成品退火,其中,脱碳退火工序包含:将冷轧板从600℃以下的入侧温度T0℃加热到高于入侧温度T0℃的均热温度T2℃为止的加热工序;和在均热温度T2℃中维持冷轧板的温度的均热工序,在脱碳退火工序的加热工序中,将冷轧板的温度从入侧温度T0℃直至到达700~900℃的范围内且低于均热温度T2℃的到达温度T1℃为止的加热速度HR1设定为40℃/秒以上,将冷轧板的温度从到达温度T1℃直至到达均热温度T2℃为止的加热速度HR2设定为超过15℃/秒且为30℃/秒以下。
这里,加热速度HR1也可以为75~125℃/秒。
此外,钢板坯作为化学成分,也可以进一步以质量%计含有B:0.0100%以下、Cr:0.30%以下、Cu:0.40%以下、P:0.50%以下、Sn:0.30%以下、Sb:0.30%以下、Ni:1.00%以下、Mo:0.1%以下、Bi:0.01%以下中的1种或两种以上。
发明效果
根据本发明的上述观点,以适当的条件控制脱碳退火的加热(升温)工序中的快速加热温度范围的加热速度以及从到达温度至均热温度为止的加热速度。由此,可稳定地制造使二次再结晶粒径小径化、铁损特性进一步改善的方向性电磁钢板。此外,根据进一步添加的元素能够制造进一步改善了磁特性等的方向性电磁钢板。
附图说明
图1是对本实施方式的脱碳退火中的升温模式进行说明的曲线图。
图2是表示二次再结晶粒径与铁损的相关性的曲线图。
图3是示意性地表示如何形成织构的图。
具体实施方式
<1.本发明的发明者的研究>
本发明的发明者首先对专利文献7中公开的技术无法充分得到方向性电磁钢板的铁损改善效果的原因进行了调査。其结果是,本发明的发明者弄清楚了:在通过专利文献7中公开的技术而制造的方向性电磁钢板中,存在尽管磁通密度高、但铁损低劣者。因此,本发明的发明者调查了铁损低劣者的特征,结果弄清楚了存在二次再结晶粒径大径化的倾向。即,通过提高磁通密度,使得磁滞损耗降低。但是,在二次再结晶粒径为大径化的情况下,涡流损耗增加。因此,弄清楚了:在专利文献7中公开的技术中,磁滞损耗的降低被涡流损耗的增加所抵消,反而使铁损进一步变差。
本发明的发明者研究了解决此问题的方法,结果认知到:通过适当地控制脱碳退火中的从入侧温度至均热温度为止的加热速度,从而能够适当地控制一次再结晶晶粒织构中的{111}取向晶粒、{411}取向晶粒、高斯取向晶粒的频率。另外,本发明的发明者认知到:通过将如上述那样控制了一次再结晶晶粒织构的钢板进行成品退火,从而能够使二次再结晶晶粒小径化。以下,对本实施方式的方向性电磁钢板的制造方法详细地进行说明。再者,关于脱碳退火时的各温度,设定如下:入侧温度是指导入退火炉时的钢板的温度、均热温度是指钢板维持在固定的温度时的温度、到达温度是指比入侧温度高且比均热温度低的温度。各温度的具体的范围将在后述。
<2.方向性电磁钢板的制造方法>
(2-1.制造方法的概要)
接下来,对本实施方式的方向性电磁钢板的制造方法进行说明。本实施方式的方向性电磁钢板的制造方法包含:钢板坯准备工序、再加热工序、热轧工序、热轧板退火工序、冷轧工序、脱碳退火工序、氮化处理工序、退火分离剂涂布工序、成品退火工序、纯化退火工序及冷却工序。以下,对各工序详细地进行说明。
(2-2.钢板坯准备工序)
在该工序中,准备钢板坯。具体而言,例如通过转炉或电炉等熔炼钢。在根据需要对由此得到的钢水进行了真空脱气处理后,进行连续铸造或铸锭后开坯轧制。由此得到钢板坯。钢板坯的厚度没有特别限制,通常以150~350mm的范围、优选220~280mm的厚度来铸造。但是,钢板坯也可以是30~70mm的厚度范围的所谓薄板坯。在使用薄板坯的情况下,具有下述优点:在制造热轧板时不需要进行粗加工至中间厚度。
(2-2-1.钢板坯的成分组成)
钢板坯作为化学成分,以质量%计含有Si:2.00~4.00%、C:0.085%以下、Al:0.01~0.065%、N:0.004~0.012%、Mn:0.05~1.00%及S:0.003~0.015%,剩余部分由Fe及杂质构成。以下,涉及成分组成的“%”是指相对于钢板坯的总质量的质量%。
(Si:2.00~4.00%)
Si是提高钢板的电阻、改善铁损特性的元素。在Si浓度低于2.00%时,在成品退火时产生铁组织的γ相变,钢板的晶体取向受损,因此Si浓度设定为2.00%以上。Si浓度优选为2.50%以上,更优选为3.00%以上。另一方面,如果Si浓度超过4.00%,则方向性电磁钢板的加工性下降,轧制时发生裂纹,因此Si浓度设定为4.00%以下。Si浓度优选为3.50%以下。
(C:0.085%以下)
C是对控制一次再结晶组织有效的元素,但由于会对磁特性产生不良影响,因此是在成品退火前通过脱碳退火除去的元素。如果C浓度超过0.085%,则脱碳退火时间延长,生产率下降,因此C浓度设定为0.085%以下。C浓度优选为0.070%以下,更优选为0.050%以下。C浓度的下限包含0%,但如果将C浓度降低至低于0.0001%,则制造成本大幅度上升,因此在实用钢板上,0.0001%为实质上的下限。再者,在方向性电磁钢板中,C浓度通过脱碳退火通常被降低至0.001%左右以下。
(Al:0.010~0.065%)
Al是与N结合而生成作为抑制剂发挥功能的(Al、Si)N或AlN的元素。在Al浓度低于0.010%时,不会充分地显现出Al的添加效果,不会充分进行二次再结晶,因此Al浓度设定为0.010%以上。Al浓度优选为0.015%以上,更优选为0.020%以上。另一方面,如果Al浓度超过0.065%,则抑制剂的析出分散变的不均匀,得不到所需的二次再结晶组织,磁通密度下降,因此Al浓度设定为0.065%以下。Al浓度优选为0.050%以下,更优选为0.040%以下。
(N:0.004~0.012%)
N是与Al结合而生成作为抑制剂发挥功能的AlN的元素。但是,N也是在冷轧时在钢板中形成泡疤(空孔)的元素。在N的质量%低于0.004%时,AlN的形成变得不充分,因此N浓度设定为0.004%以上。优选为0.006%以上,更优选为0.007%以上。如果N浓度超过0.012%,则有可能在冷轧时在钢板中形成大量的泡疤,因此N浓度设定为0.012%以下。
(Mn:0.05~1.00%)
Mn是防止热轧时的裂纹,并且与S结合而形成作为抑制剂发挥功能的Mn化合物即MnS的元素。在Mn浓度低于0.05%时,不会充分地显现出Mn的添加效果,因此Mn浓度设定为0.05%以上。Mn浓度优选为0.07%以上,更优选为0.09%以上。另一方面,如果Mn浓度超过1.00%,则Mn化合物的析出分散变得不均匀,得不到所需的二次再结晶组织,磁通密度下降,因此Mn浓度设定为1.00%以下。Mn浓度优选为0.80%以下,更优选为0.60%以下。
(S:0.003~0.015%)
S是与Mn结合而形成作为抑制剂发挥功能的MnS的元素。在S浓度低于0.003%时,不会充分地显现出S的添加效果,因此S浓度设定为0.003%以上。S浓度优选为0.005%以上,更优选为0.007%以上。另一方面,如果S浓度超过0.015%,则MnS的析出分散变得不均匀,得不到所需的二次再结晶组织,磁通密度下降,因此S浓度设定为0.015%。S浓度优选为0.013%以下,更优选为0.011%以下。
在钢板坯的成分中,除了上述元素以外的剩余部分为Fe及杂质。杂质基本上是不可避免的杂质,但在钢板坯中含有后述的任选添加元素的情况下,杂质除了不可避免的杂质以外,还由这些任选添加元素构成。不可避免的杂质是从钢原料及炼钢过程这两者或任一者中不可避免地混入的元素,是在不妨碍本实施方式的方向性电磁钢板的特性的范围内被容许的元素。
此外,钢板坯中,以不妨碍其磁特性并且可提高其它特性为目的,也可以添加B:0.0100%以下、B:0.0100%以下、Cr:0.30%以下、Cu:0.40%以下、P:0.50%以下、Sn:0.30%以下、Sb:0.30%以下、Ni:1.00%以下、Mo:0.1%以下、Bi:0.01%以下中的1种或两种以上作为任选添加元素。这些元素是任选添加元素,因此浓度的下限值也可以为0%。
(B:0.0100%以下)
B是与母材钢板中的N结合、与MnS复合析出、形成作为抑制剂发挥功能的BN的元素。B浓度的下限没有特别限制,如上所述也可以为0%。但是,为了充分发挥B的添加效果,B浓度的下限优选为0.0005%。B浓度优选为0.001%以上,更优选为0.0015%以上。另一方面,如果B浓度超过0.0100%,则BN的析出分散变得不均匀,得不到所需的二次再结晶组织,磁通密度下降。因此,B浓度优选为0.0100%以下。B浓度更优选为0.0080%以下,进一步优选为0.0060%以下,进一步优选为0.0040%以下。
(Cr:0.30%以下)
Cr是改善脱碳退火时形成的内部氧化层,对形成玻璃覆膜有效的元素。因此,也可以以0.30%以下的范围在钢板坯中添加Cr。如果Cr浓度超过0.30%,则会显著地阻碍脱碳性,因此Cr浓度的上限优选为0.30%。
(Cu:0.40%以下)
Cu是对提高方向性电磁钢板的电阻率以使铁损降低有效的元素。如果C浓度超过0.40%,则铁损降低效果饱和,并且在热轧时成为“铜鳞状折叠”的表面瑕疵的原因,因此C浓度的上限优选为0.40%。
(P:0.50%以下)
P是对提高方向性电磁钢板的电阻率以使铁损降低有效的元素。如果P浓度超过0.50%,则轧制性产生问题,因此P浓度的上限优选为0.50%。
(Sn:0.30%以下、Sb:0.30%以下)
Sn和Sb是熟知的晶界偏析元素。本实施方式的钢板坯由于含有Al,因此有时根据成品退火的条件,因从退火分离剂中释放的水分而使Al被氧化,在卷材位置处抑制剂强度发生变动。其结果是,有时磁特性在卷材位置处发生变动。作为其对策之一,有通过添加这些晶界偏析元素来防止Al氧化的方法,因此也可以将Sn及Sb分别以0.30%以下的浓度添加至母材钢板中。另一方面,如果这些元素的浓度超过0.30%,则在脱碳退火时Si难以被氧化,玻璃覆膜的形成变得不充分,并且会显著地阻碍脱碳退火性。因此,这些元素的浓度的上限优选为0.30%。
(Ni:1.00%以下)
Ni是对提高方向性电磁钢板的电阻率以使铁损降低有效的元素。此外,Ni也是在控制热轧板的铁组织以使磁特性提高方面有效的元素。但是,如果Ni浓度超过1.00%,则二次再结晶变得不稳定,因此Ni浓度的上限优选为1.00%。
(Mo:0.1%以下)
Mo是对改善热轧时的表面性状有效的元素。但是,如果Mo浓度超过0.1%,则Mo的添加效果饱和,因此Mo浓度的上限优选为0.1%。
(Bi:0.01%以下)
Bi具有使硫化物等析出物稳定化以强化作为抑制剂的功能的效果。但是,如果Bi浓度超过0.01%,则Bi会对玻璃覆膜的形成产生不良影响,因此Bi浓度的上限优选为0.01%。
(2-3.再加热工序)
在该工序中,对钢板坯进行再加热。钢板坯的再加热温度优选为1280℃以下。在再加热温度超过1280℃的情况下,熔融氧化皮量增多。另外,MnS完全固溶于钢板坯中,在之后的工序中微细地析出,因此需要将用于得到所期望的一次再结晶粒径的脱碳退火温度设定为超过900℃。因此,在本实施方式中,优选将钢板坯在1280℃以下进行再加热。再加热温度的下限值没有特别限制,例如也可以为1100℃。再者,在本实施方式中,钢板坯或钢板的温度例如能够通过辐射温度计来测定。
(2-4.热轧工序、热轧板退火工序)
在热轧制(热轧)工序中,将再加热后的钢板坯进行热轧。在热轧板退火工序中,通过将由上述热轧工序得到的热轧板加热到1000~1150℃的第1段温度,从而使铁组织再结晶。接着,将热轧板在850~1100℃且比第1段温度低的第2段温度中进行退火。该热轧板退火工序主要以在热轧时产生的不均匀组织的均匀化为目的来进行。
即,为了使热轧时产生的不均匀的铁组织(履历)在最终冷轧前均匀化,在本实施方式中,优选进行1次以上的退火。此种情况下的第1段温度的上限值对抑制剂产生大的影响。例如,在第1段温度超过1150℃的情况下,有可能抑制剂会在之后的工序中微细地析出。因此,优选将第1段温度的上限设定为1150℃。另一方面,在第1段温度低于1000℃的情况下,有可能再结晶不充分而无法将热轧后的铁组织均匀化。因此,优选将第1段温度的下限设定为1000℃。第2段温度的上限值也对抑制剂产生大的影响。例如,在第2段温度超过1100℃的情况下,有时抑制剂在之后的工序中微细地析出。因此,优选将第2段温度的上限设定为1100℃。在第2段温度低于850℃的情况下,有可能不会产生γ相、无法进行铁组织的均匀化。因此,优选将第2段温度的下限设定为850℃。进而,优选第2段温度控制为比第1段温度低的值。
(2-5.冷轧工序)
在进行了热轧板退火工序后,对热轧板实施1次冷轧或夹着中间退火的2次以上的冷轧制(冷轧)。由此,制作最终冷轧板。各冷轧可以在常温下进行,也可以设定为将钢板温度提高至高于常温的温度例如200℃左右来进行轧制的温轧。
(2-6.脱碳退火工序)
脱碳退火工序包括下述工序:将冷轧工序后的钢板(冷轧板)从入侧温度T0℃加热到高于入侧温度的均热温度T2℃为止的加热工序;和使冷轧板的温度在均热温度T2℃中为规定时间的均热工序。脱碳退火工序在湿润气氛中进行。这里,入侧温度T0℃为将冷轧板导入退火炉时的温度,为大致600℃以下。均热温度设定为700~900℃的范围内的温度。
脱碳退火的均热工序是以钢中碳的除去和将一次再结晶粒径控制为所期望的粒径为目的来进行。均热工序例如优选的是,在700℃~900℃的温度区域的均热温度T2℃中,以一次再结晶粒径达到15μm以上那样的时间来进行。在均热温度T2℃低于700℃时,无法实现所期望的一次再结晶粒径,在均热温度T2℃超过900℃时,一次再结晶超过所期望的粒径。
在加热工序中,如图1所示的那样,将冷轧板的温度从入侧温度T0℃直至到达700~900℃的范围内且低于均热温度T2℃的到达温度T1℃为止(即快速加热温度范围)的加热速度HR1设定为40℃/秒以上。另外,将冷轧板的温度从到达温度T1℃直至到达均热温度T2℃为止的加热速度HR2设定为超过15℃/秒且为30℃/秒以下。到达温度T1℃可以在满足上述条件的范围内任意地设定,但通过将到达温度T1℃设定为钢板的居里点(750℃)以下,能够采用感应加热装置进行入侧温度T0℃~到达温度T1℃的温度范围(快速加热温度范围)内的加热。
这样一来,在本实施方式涉及的加热工序中,通过控制加热速度,从而适当地控制一次再结晶晶粒织构中的{111}取向晶粒、{411}取向晶粒、高斯取向晶粒的频率。具体而言,在一次再结晶晶粒织构中,优选减少{111}取向晶粒、{411}取向晶粒及高斯取向晶粒增加。再结晶的容易性根据晶体取向而异,{411}取向晶粒在100℃/秒附近的加热速度下最容易再结晶,此外,高斯取向晶粒变得容易与加热速度成比例地进行再结晶。因此,在本实施方式中,将冷轧板的温度从入侧温度T0℃直至到达均热T1℃为止的加热速度HR1设定为40℃/秒以上。由此,能够减少{111}取向晶粒,增加{411}取向晶粒及高斯取向晶粒。加热速度HR1优选为75℃/秒以上,更优选为75~125℃/秒。
进而,在本实施方式中,将冷轧板的温度从到达温度T1℃直至到达均热温度T2℃为止的加热速度HR2设定为超过15℃/秒且为30℃/秒以下。加热速度HR2的下限值优选为16℃/秒。这样一来,在本实施方式中,将冷轧板的温度到达至到达温度T1℃以后的加热速度HR2设定为超过15℃/秒且为30℃/秒以下这样高的值。由此,能够得到{411}取向晶粒及高斯取向晶粒的频率高、并且高斯取向晶粒的晶体粒径为大径化的一次再结晶晶粒织构。其结果是,在之后的成品退火的二次再结晶中二次再结晶粒径发生小径化,因此可得到铁损良好的方向性电磁钢板。
这里,在将加热速度HR2控制在超过15℃/秒且为30℃/秒以下的情况下可得到上述效果的理由尚不清楚,但本发明的发明者认为其理由如下所述。即,在从快速加热的从到达温度T1℃到处于700~900℃的均热温度T2℃为止的温度范围中,发生未再结晶晶粒的再结晶和已完成了再结晶的晶粒的生长。在均热温度T2℃时,未再结晶晶粒全部成为了再结晶晶粒。然后,在均热温度T2℃中的均热工序(均热退火)中,再结晶晶粒进入晶粒生长模式,晶体粒径小的取向晶粒被蚕食,晶体粒径大的取向晶粒发生大径化。这里,高斯取向晶粒在到达温度T1℃以下时完成了再结晶。通过将从到达温度T1℃到均热温度T2℃为止的加热速度HR2控制在超过15℃/秒且为30℃以下、优选为16℃/秒~30℃/秒,从而可促进已完成了再结晶的高斯取向晶粒的晶粒生长。即,在均热工序的开始时高斯取向晶粒已经成为了大径化的晶粒,因此在均热工序中能够以不被其它取向晶粒蚕食的方式存在。
这里,在加热速度HR2为15℃/秒以下的情况下,在到达温度T1℃以后进行再结晶的取向的晶粒的生长与高斯取向晶粒的生长发生冲突,高斯取向晶粒无法充分地晶粒生长。其结果是,在一次再结晶晶粒织构中高斯取向晶粒的频率降低,得不到具有良好的铁损特性的电磁钢板。另一方面,在加热速度HR2超过30℃/秒的情况下,在一次再结晶晶粒织构中高斯取向晶粒的频率、晶体粒径极端地增大,组织整体的晶粒规整性(均匀性)显著受损。因此,无法得到稳定的二次再结晶,结果铁损特性劣化。此外,HR2的上限也可以设定为25℃以下或低于25℃。HR2的范围如后文中详述那样,能够采用多种加热装置进行加热,但如果HR2变大而使均热温度T2超出规定,则有时会导致之后的二次再结晶不良。因此,通过HR2的上限设定为25℃以下或低于25℃,能够防止使均热温度T2超出规定,是优选的。
再者,通过脱碳退火工序,从而在冷轧板的表层部形成大量包含SiO2的内部氧化层。
(2-6-1.脱碳退火工序中的加热方法)
加热工序中的冷轧板的加热也可以用感应加热装置来进行。在此种情况下,可获得下述效果:加热速度的自由度高、能够与钢板非接触地加热、进而在脱碳退火炉内的设置比较容易等。特别是,在到达温度T1℃成为钢板的居里点即750℃以下的情况下,只用感应加热装置就能够将冷轧板从入侧温度T0℃快速加热至到达温度T1℃。
另一方面,从到达温度T1℃到均热温度T2℃为止的加热及之后的均热工序中的均热处理例如也可以利用使用了辐射管等辐射热源的加热装置来进行。就感应加热装置而言,居里点以后的加热是困难的,但如果是使用了辐射热源的加热装置,则即使是这样的温度区域也能够稳定地加热冷轧板。另外,采用辐射热的加热还具有下述优点:在加热速度HR2的范围内(比加热速度HR1慢的范围内)容易控制。
当然,加热方法没有特别的限定。加热方法除了上述方法以外,也可以是利用新型的激光器、等离子体等高能热源的方法、利用通电加热装置的方法等。也可以将它们适宜地组合。但是,通过利用感应加热装置或使用了辐射热源的加热装置,从而具有下述优点:加热装置不会与冷轧板直接接触就能够对冷轧板进行加热。
(2-7.氮化处理工序)
在脱碳退火后,对钢板实施氮化处理,以使钢板的氮浓度达到40ppm~1000ppm。在氮化处理后的钢板的氮浓度低于40ppm时,在钢板内AlN不会充分地析出,AlN无法作为抑制剂发挥功能。因此,钢板的氮浓度设定为40ppm以上。另一方面,在钢板的氮浓度超过1000ppm的情况下,在成品退火中二次再结晶完成后仍在钢板内过量地存在AlN。这样的AlN成为铁损劣化的原因。因此,钢板的氮浓度设定为1000ppm以下。
(2-8.退火分离剂涂布工序)
在氮化处理工序后,在钢板的表面涂布退火分离剂。后述的成品退火有时会在将钢板卷取成卷材状的状态下进行。当在这样的状态下进行了成品退火的情况下,有时卷材会发生热粘而变得难以将卷材开卷。因此,在本实施方式中,按照能够在成品退火后将卷材开卷的方式来涂布退火分离剂。这里,退火分离剂的主成分为MgO,退火分离剂中的MgO在成品退火时与内部氧化层中的SiO2发生固相反应,生成玻璃覆膜。
(2-9.成品退火工序)
成品退火工序也是被称为二次再结晶退火工序的退火,是促进铁组织的二次再结晶的处理。在成品退火工序中,将冷轧板(钢板)加热到后述的1200℃左右。这里,在加热过程中,优选的是,至少在1000℃~1100℃的温度范围中,将加热速度HR3设定为15℃/小时以下。此外,代替加热速度的控制,在1000℃~1100℃的温度范围内保持10小时以上也是有效的。即,使该温度区域中的加热速度极其缓慢。由此,能够促进高斯取向晶粒的优先成长(二次再结晶)。在加热速度HR3过快(超过15℃/小时)的情况下,高斯取向以外的晶体取向的晶粒生长。其它温度区域中的加热速度没有特别限制,只要是与以往的成品退火相同的程度即可。成品退火气氛没有特别限制,可以与以往的成品退火相同。例如,成品退火气氛也可以是氮氢的混合气氛。
特别是,在本实施方式中,成品退火前的一次再结晶晶粒织构中的{411}取向晶粒及高斯取向晶粒的频率较高,并且高斯取向晶粒的晶体粒径(在一次再结晶晶粒织构中相对地)为大径化。因此,二次再结晶晶粒织构成为了小径化的高斯取向晶粒高度一致的组织。即,(相对于通过现有技术得到的二次再结晶晶粒织构而言相对性地)高斯取向晶粒的频率非常高,并且高斯取向晶粒的粒径小。认为这是基于以下的理由。
即,由于成品退火前的一次再结晶晶粒织构中的{411}取向晶粒及高斯取向晶粒的频率高,并且高斯取向晶粒的晶体粒径(在一次再结晶晶粒织构中相对地)为大径化,因此在成品退火中高斯取向晶粒优先于其它取向晶粒地进行晶粒生长。因此,高斯取向晶粒的频率大(换言之,生长核多),各个高斯取向晶粒优先进行大径化,因此在二次再结晶后多个高斯取向晶粒生长,但由于所生长的多个高斯取向晶粒仅稍微具有取向差,所以没有合并,因此二次再结晶后的各个高斯取向晶粒所占的区域即粒径减小。
图3是示意性地表示如何形成本实施方式中的织构的图,为了参考还示出了现有技术中的织构是如何形成的。
像这样,在本实施方式中,以适当的条件控制脱碳退火的加热(升温)工序中的快速加热温度范围的加热速度HR1以及从到达温度至均热温度为止的加热速度HR2。由此,可稳定地制造使二次再结晶粒径小径化、铁损特性进一步改善的方向性电磁钢板。此外,根据进一步添加的元素能够制造进一步改善了磁特性等的方向性电磁钢板。
这里,HR1、HR2的测定方法没有特别的限定,例如可通过采用辐射温度计等测定钢板温度来算出。但是,在钢板温度T0、T1、T2的测定困难、HR1及HR2的开始、结束点的准确位置的推定困难的情况下,也可以通过类推升温过程的各个加热模式来推定这些位置。
再者,本发明的发明者准备了通过各种制造条件制作的方向性电磁钢板。然后,测定了它们的高斯取向晶粒的粒径(二次再结晶后的粒径)。具体而言,通过酸洗除去玻璃覆膜,使晶粒露出,对处于180cm2的范围内的晶粒的数量进行测量,由每1个二次再结晶晶粒的面积(=180/个数)算出粒径(当量圆直径)。进而,测定这些方向性电磁钢板的铁损W17/50。将其结果示于图2中。图2的横轴表示二次再结晶后的粒径,纵轴表示铁损。绘点P1表示各方向性电磁钢板的测定结果,直线L1是绘点P1的近似直线。根据图2可知:在二次再结晶后的粒径与铁损之间具有高的相关性,二次再结晶后的粒径越小,则铁损越变小。此外,详情将在后面叙述,在通过本实施方式的方向性电磁钢板的制造方法而制作的方向性电磁钢板中,铁损大概成为0.85(W/kg)以下。再者,也可以在成品退火工序后进一步进行以下工序。
(2-10.纯化退火工序)
在继成品退火工序之后的纯化退火工序中,通过在二次再结晶完成后进行纯化,从而进行作为抑制剂利用的析出物(AlN、MnS等)的无害化。由此,变得能够降低最终磁特性中的磁滞损耗。在纯化退火工序中,例如优选在氢气氛下、在1200℃下进行10小时以上的钢板的保持。在纯化退火后,对冷轧板(钢板)进行冷却。
(2-11.绝缘覆膜涂层)
在冷却工序后的钢板表面进一步涂布绝缘覆膜涂层,进行烧结。关于绝缘覆膜的种类,没有特别的限定,以往公知的一切绝缘覆膜都适合于本实施方式的方向性电磁钢板。作为绝缘覆膜的例子,可列举出涂布含有磷酸盐和胶体二氧化硅的水系涂布溶液而形成的覆膜。在此种情况下,作为磷酸盐,例如可列举出Ca、Al、Sr等的磷酸盐。其中,更优选磷酸铝盐。胶体二氧化硅没有特别的限定,其粒子尺寸也可以适宜使用。特别优选的粒子尺寸(平均粒径)为200nm以下。即使粒子尺寸低于100nm在分散方面也无问题,但制造成本提高,有时不现实。如果粒子尺寸超过200nm,则有时会在处理液中发生沉淀。
优选的是,通过采用辊涂等湿式涂布方法将绝缘覆膜涂层液涂布于钢板表面,在大气气氛中、于800~900℃的温度下烧结10~60秒,从而形成张力绝缘覆膜。
(2-12.磁畴控制工序)
磁畴控制工序的具体的处理方法没有特别限制,例如通过采用使用激光照射、电子束、蚀刻、齿轮的槽形成法来实施磁畴控制,从而可得到更低的铁损。再者,如上所述,即使是在磁畴控制前,就本实施方式的方向性电磁钢板而言,铁损也大幅地改善。
实施例
接下来,对本发明的实施例进行说明。需要说明的是,实施例中的条件是为了确认本发明的可实施性及效果而采用的一个条件例子,本发明并不限于这一个条件例子。只要不脱离本发明的主旨、实现本发明的目的,则本发明可采用各种条件。
<1.实施例1>
在实施例1中,将表1中所示的成分组成的钢板坯加热至1150℃后供于热轧,制成板厚为2.6mm的热轧板。接着,对于该热轧板,使第1段温度为1100℃、使第2段温度为900℃,实施热轧板退火。接着,对热轧板实施一次冷轧或夹着中间退火的多次冷轧,制作最终板厚为0.23mm的冷轧板。
表1
接着,对最终板厚成为0.23mm的冷轧板实施脱碳退火和氮化处理(增加钢板的氮量的退火)。脱碳退火中的加热速度HR1、HR2、到达温度T1℃、均热温度T2℃如表2所示。加热方式设定为辐射管方式。这里,入侧温度T0℃设定为550℃。此外,在均热工序中,将均热温度T2维持100秒。
然后,在钢板的表面涂布以氧化镁(MgO)为主成分的退火分离剂,进行成品退火。然后,在成品退火工序中,将钢板加热到1200℃。这里,将1000~1100℃的温度区域中的加热温度设定为10℃/小时。然后,在钢板上涂布由磷酸盐和胶体二氧化硅制成的水系涂布液,在空气中于800℃下烧成60秒。由此,在钢板的表面(更具体而言为玻璃覆膜的表面)形成张力绝缘覆膜。接着,对赋予了张力绝缘覆膜的方向性电磁钢板的铁损W17/50(在1.7T、50Hz的励磁条件下测定的能量损失)进行测定。测定是基于JIS C2550来实施的。将其结果示于表2中。
表2
就满足本实施方式的方向性电磁钢板的制造方法的所有条件(成分组成、脱碳退火工序中的温度控制)的发明例B1~B17而言,得到了铁损W17/50为0.85W/kg以下的良好的铁损。再者,就发明例B1~B17而言,将入侧温度T0℃(550℃)~到达温度T1℃的加热速度HR1设定为40℃/秒,将从到达温度T1℃到均热温度T2℃为止的加热速度HR2设定为超过15℃/秒且为30℃/秒以下。
就B18~B21而言,得到了铁损W17/50为0.85W/kg以下的良好的铁损。再者,就发明例B18~B21而言,将入侧温度T0℃(550℃)~到达温度T1℃的加热速度HR1分别设定为100、400、1000、1200℃/秒,将从到达温度T1℃到均热温度T2℃为止的加热速度HR2设定为超过15℃/秒且为30℃/秒以下。
另一方面,就比较例b2、b4、b6、b7、b9、b11而言,由于使用了一部分成分组成的质量%在本实施方式的范围外的钢板坯,因此没有进行二次再结晶,铁损W17/50成为1.00W/kg以上,明显低劣。此外,比较例b1由于脱碳不良、比较例b3、b5由于固有电阻低、比较例b10由于残留硫化物,因此铁损低劣,为0.9W/kg以上。就比较例b8而言,虽然铁损良好,但在制品钢板中大量发生泡疤,不适合作为商品。就比较例b12~b18而言,尽管成分组成的质量%处于本发明的范围内,但脱碳退火的加热条件为本发明的范围外。因此,铁损W17/50停留于0.89W/kg以上。具体而言,就比较例b12而言,由于加热速度HR2快,因此高斯取向晶粒的频率变得过高,在成品退火后无法得到卷材全长上的二次再结晶。比较例b13、b14分别由于加热速度HR1或加热速度HR2慢,因此在一次再结晶晶粒织构中高斯取向晶粒减少。因此,没有得到良好的铁损。就比较例b15、b18而言,由于均热温度T2℃超过900℃,因此超出规定。因此,一次再结晶粒径变得过大,在成品退火中没有形成二次再结晶。就比较例b16、b17而言,由于加热速度HR1慢,因此在一次再结晶晶粒织构中高斯取向晶粒没有发达,没有得到良好的铁损。
b19~b21将入侧温度T0℃(550℃)~到达温度T1℃的加热速度HR1分别设定为40、100、300℃/秒,将从到达温度T1℃到均热温度T2℃为止的加热速度HR2设定为15℃/秒。铁损W17/50为0.85W/kg以上,未达到良好的铁损。这是由于:一次再结晶织构中的高斯取向晶粒未发达。
b22~b24将入侧温度T0℃(550℃)~到达温度T1℃的加热速度HR1分别设定为100、350、1000℃/秒,将从到达温度T1℃到均热温度T2℃为止的加热速度HR2设定为26℃/秒,将所期望的均热温度T2分别设定为840、850、830℃。铁损W17/50大幅地超过1.00W/kg,发生了二次再结晶不良。这是由于:因为加热速度过高,因此T2过于高于所期望的温度(超出规定)。
<2.实施例2>
在实施例2中,将表1中所示的成分组成的钢板坯加热至1150℃后供于热轧,制成板厚为2.6mm的热轧钢板。接着,对于该热轧板,使第1段温度为1100℃、使第2段温度为900℃,实施热轧板退火。接着,对热轧板实施一次冷轧或夹着中间退火的多次冷轧,制作最终板厚为0.23mm的冷轧板。
接着,对最终板厚成为0.23mm的冷轧板实施脱碳退火和氮化处理(增加钢板的氮量的退火)。脱碳退火中的加热速度HR1、HR2、到达温度T1℃、均热温度T2℃如表2所示。将加热方式设定为辐射管方式。这里,入侧温度T0℃设定为550℃。此外,在均热工序中,将均热温度T2维持120秒。
然后,在钢板的表面涂布以氧化镁(MgO)为主成分的退火分离剂,进行成品退火。然后,在成品退火工序中,将钢板加热到1200℃。这里,将1000~1100℃的温度区域中的加热温度设定为10℃/小时。然后,在钢板上涂布由磷酸盐和胶体二氧化硅制成的水系涂布液,在空气中于800℃下烧成60秒。由此,在钢板的表面(更具体而言为玻璃覆膜的表面)形成张力绝缘覆膜。接着,对赋予了张力绝缘覆膜的方向性电磁钢板的铁损W17/50(在1.7T、50Hz的励磁条件下测定的能量损失)进行测定。测定是基于JIS C2550来实施的。将其结果示于表3中。
表3
发明例C1~C9由于全部都满足本实施方式的方向性电磁钢板的制造方法的所有条件(成分组成、脱碳退火工序中的温度控制),因此得到了铁损W17/50为0.85W/kg以下的良好的铁损。特别是,就发明例C5~C9而言,将入侧温度T0℃(550℃)~到达温度T1℃的加热速度HR1设定为100℃/秒,将从到达温度T1℃到均热温度T2℃为止的加热速度HR2设定为超过15℃/秒且为30℃/秒以下。即,提高了加热速度HR1。其结果是,就发明例C5~C9而言,得到了铁损W17/50为0.80W/kg以下的特别良好的铁损。
以上,参照附图对本发明的优选的实施方式详细地进行了说明,但本发明并不限于这些例子。只要是具有本发明所属的技术领域中的通常知识的人员,则显而易见能够在权利要求书中记载的技术构思的范畴内想到各种变更例或修正例,对于这些,当然应理解为也属于本发明的技术范围。
符号说明
P1:表示二次再结晶后的粒径及铁损的测定值的绘点
L1:绘点P1的近似直线
本文用于企业家、创业者技术爱好者查询,结果仅供参考。