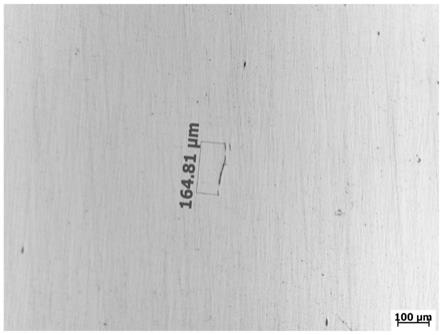
1.本发明属于齿轮用钢技术领域,具体涉及一种易切削齿轮钢硫化物形态的控制方法。
背景技术:
2.随着精密齿轮等机械零部件的加工要求越来越高,加工成本占据了制造成本的主要部分,有时甚至超过了总成本的一半,所以通过减少加工成本来控制总制造成本愈发受到重视,易切削齿轮钢应运而生。
3.目前常见的有硫系、铅系、钙系、铋系等易切削钢。易切削齿轮钢的优点是:切削时断削容易,刀具受力小从而使得刀具使用寿命延长,能耗较低。目前全球易切削钢年需求量在400万吨以上,以美国和日本为代表的发达国家,其易切削钢产量和增速遥遥领先。我国自上世纪50年代开始研制易切削钢,目前国内年产量尚不及需求量的一半,仍然依赖大量进口。虽然近年来我国易切削钢发展迅猛,但在一些高性能易切削钢材产品上,无论是产量、质量还是生产水平,都和国外先进钢生产国(如美国、日本)有较大差距。尤其是世界上使用最广的硫系易切削钢,在硫化物形貌控制方面,一旦控制不当,极易产生宏观缺陷,降低钢材力学性能。
技术实现要素:
4.本发明的目的是针对以上不足,提供一种易切削齿轮钢,并提供了其制备方法,采用微合金化,增加锰、铬的含量提高产品力学性能,控制淬透性在较窄的范围内;通过钙处理来改善浇注性;采用低铝、低硫控制硫化物形态,改善最终产品的切削性能;加入一定量的钛提高产品淬透性,且钛和钢水中的氮元素生成细小弥散分布的氮化钛,改善产品金相组织。
5.为实现上述目的,本发明是通过以下技术方案实现的:
6.首先提供一种易切削齿轮钢,包括以下重量百分比的化学成分:
7.碳0.17~0.23,硅0.17~0.37,锰0.90~1.20,铬1.10~1.40,铝0.010~0.030,钛0.030~0.090,铜≤0.20,镍≤0.25,磷≤0.030,硫0.010~0.035,氮0.0020-0.0080,余量为fe和不可避免的杂质。
8.优选地,所述易切削齿轮钢包括以下重量百分比的化学成分:碳0.20~0.23,硅0.23~0.37,锰0.98~1.03,铬1.23~1.28,铝0.010~0.025,钛0.045~0.065,铜≤0.10,镍≤0.10,磷≤0.020,硫0.010~0.018,氮0.0025~0.0070,余量为fe和不可避免的杂质。
9.本发明还提供一种上述的易切削齿轮钢硫化物形态的控制方法,包括电炉冶炼、lf精炼、vd真空处理、连铸和连续轧制等步骤,各步骤的具体要求如下:
10.(1)电炉冶炼:
11.为控制钢中有害残余元素,实行优质铁水、纯净废钢的合理搭配,大大降低炼钢的制造成本,电炉采用铁水热装技术,需控制铁水比≥80%。
12.出钢终点的[c]≥0.05%,[p]≤0.015%,出钢温度≥1580℃;
[0013]
所述电炉冶炼出钢至lf精炼过程中钢水的成分及钢水温度控制目标要求为:c:0.08~0.17%、si:0.10~0.20%、mn:0.86~1.01%、cr:1.10~1.25%;温度≥1530℃;
[0014]
(2)lf精炼:
[0015]
该步骤采用沉淀脱氧 扩散脱氧,降低钢水硫含量;
[0016]
钢水进站造白渣,控制白渣保持时间≥20min,冶炼时间≥40min;
[0017]
(3)vd真空处理:
[0018]
所述vd真空处理步骤中,真空度67pa以下,保持时间≥10min,破空后先喂入铝线脱氧,调整钢水中[al]的含量在0.010%~0.025%,再喂入钛铁线调整微合金元素钛含量在0.045~0.065%,喂入硅钙线50~80m使高熔点氧化铝夹杂变性为液态钙铝酸盐类夹杂以提高连浇炉数,间隔10min后喂入硫磺线使硫含量为0.010~0.018%,以提高产品切削性;软吹时间≥20min,以保证钢水中非金属夹杂物充分上浮;该步骤中全过程采用底吹氮气增氮,防止钢水的二次氧化,提高了钢水的纯净度。
[0019]
(4)连铸工艺:
[0020]
连铸弧形半径17m,静压力大,有利于凝固补缩。
[0021]
该步骤中全程保护浇铸,防止钢水二次氧化。采用低过热度浇铸,钢水过热度控制在18~30℃,采用三段式电磁搅拌,浇铸断面的直径为φ380mm,采用全程恒拉速拉坯,拉速为0.65m/min,减少液面波动,防止表面卷渣;
[0022]
连铸后进行缓冷,所述入坑缓冷的入坑温度≥500℃,缓冷时间≥30h,出坑温度≤200℃。
[0023]
(5)连续轧制:
[0024]
缓冷后的连铸坯经过加热炉加热,具体为:预热温度880℃、加热温度900~1100℃、均热温度1200~1280℃,总加热时间≥3.5h;连铸坯出炉后,经过高压水除鳞去除表面氧化皮,然后进行初轧,控制初轧温度1100~1200℃,进连轧温度≥900℃,下冷床温度≥580℃;
[0025]
(6)缓冷:
[0026]
经连续轧制后得到的圆钢下冷床后入坑缓冷,入坑温度≥550℃,出坑温度≤200℃,消除圆钢内外的拉压应力。在圆钢缓冷步骤之后,即可对得到的圆钢进行精整、检验、称重、标识、入库,后续操作均为现有技术实现,本发明对此不再赘述。
[0027]
优选的,所述步骤(1)电炉冶炼出钢至lf精炼过程中,在钢水中加入铝块,加入量为每吨钢水加入1.0~1.3kg,再加入造渣辅料,造渣辅料为石灰和促净剂;其中石灰加入量为每吨钢水加入6.0~7.0kg,促净剂加入量为每吨钢水加入2.0~2.5kg。
[0028]
优选的,所述步骤(1)电炉冶炼的铁水比为80%~88%,出钢终点的[c]为0.05%~0.15%,出钢温度为1580~1650℃;进lf站钢水的温度控制为1530~1620℃。
[0029]
优选的,为有效降低钢中氧含量,lf冶炼20min后进入中后期,在此阶段分4-6个批次加入扩散脱氧剂以保持还原性气氛;所述步骤(2)lf精炼步骤中扩散脱氧时使用的是扩散脱氧剂,扩散脱氧剂的加入量为每吨钢水加入1.5~1.8kg;所述扩散脱氧剂为复合碳化硅和硅铁粉的混合物,其质量比为7:1。
[0030]
优选的,所述步骤(3)vd真空处理步骤中,根据钢水中的氮含量,进行氩气切换;当
氮含量为50~60ppm时,进行氩气切换。
[0031]
优选的,所述步骤(4)连铸步骤中,所述三段式电磁搅拌为结晶器电磁搅拌、二冷段电磁搅拌和末端电磁搅拌(m-ems s-ems f-ems)。
[0032]
优选的,所述步骤(5)中总加热时间为3.5-8h;所述连续轧制的过程所述均热温度处理的保温时间为2~5h;所述轧制的压缩比为6~26;以达到破碎硫化物的目的,从而得到小尺寸、短杆状硫化锰,改善热轧圆钢的切削性能。
[0033]
优选的,步骤(6)中所述入坑缓冷的入坑温度为550~580,缓冷时间为30~80h,出坑温度≤200℃。
[0034]
与现有技术相比,本发明的有益效果为:
[0035]
(1)本发明通过增加锰、铬元素的含量以提高产品力学性能,控制淬透性在较窄的范围内;通过弱钙处理来改善浇注性;采用低铝、低硫控制硫化物形态,改善最终产品的切削性能;采用微合金化,加入一定含量的钛元素提高产品淬透性,且钛和钢水中的氮元素生成细小弥散分布的氮化钛,改善产品金相组织;通过延长坯料高温(即均热温度)保持时间、较大轧制比达到均匀组织、小尺寸短杆状硫化锰的目的,以改善热轧圆钢切削性。
[0036]
(2)本发明所述组分方案和冶炼、轧制方法制得的易切削齿轮钢满足以下性能要求:
[0037]
非金属夹杂物:a细≤2.5,a粗≤2.5,b细≤2.0,b粗≤2.0,c细≤1.5,c粗≤1.0,d细≤2.0,d粗≤2.0,ds≤2.0;
[0038]
奥氏体晶粒度:890℃保温1小时水淬,奥氏体晶粒度6.0~8.0级,极差不超过3级;
[0039]
力学性能:抗拉强度≥1250mpa,屈服强度≥1000mpa,断后伸长率≥11%,断面收缩率≥45%;冲击ku2(室温)≥80j;
[0040]
末端淬透性:j9在36~42rhc,j15在31~38hrc;
[0041]
(3)本发明所述硫化物形态的控制方法可有效控制热轧圆钢硫化物的形貌,提高圆钢的切削性,控制淬透性在较窄范围内。
附图说明
[0042]
图1为本发明实施例提供的易切削齿轮钢热轧圆钢1/2r处硫化物形貌图片;
[0043]
图2为对比例1中的传统齿轮钢热轧圆钢的1/2r处硫化物形貌图片。
[0044]
图3为对比例2中的传统齿轮钢热轧圆钢的1/2r处块状氮化物形貌图片。
具体实施方式
[0045]
下面将结合具体实施例更详细地描述本发明的优选实施方式。
[0046]
实施例1:
[0047]
一种易切削齿轮钢,包括以下质量百分含量的化学成分:c:0.21%,si:0.27%,mn:1.01%,p:0.007%,s:0.015%,cr:1.25%,ti:0.055%,al:0.018%,[n]:0.0055%,其它为fe和不可避免的杂质。
[0048]
上述易切削齿轮钢硫化物形态的控制方法,包括如下步骤:铁水 废钢
→
电炉冶炼
→
lf精炼
→
vd真空处理
→
连铸
→
缓冷
→
加热
→
轧制
→
缓冷
→
精整
→
称重
→
标识
→
入库。
[0049]
(1)电炉冶炼:
[0050]
采用铁水热装技术,控制铁水比(铁水占总量的质量百分比)为80~85%。
[0051]
1.终点要求:出钢终点的目标[c]0.06~0.13%;目标[p]≤0.007%;目标温度1630~1650℃;2.出钢辅料要求:电炉冶炼出钢至lf精炼过程中,在钢水中加入铝块,加入量为每吨钢水加入1.1~1.2kg,再加入造渣辅料,造渣辅料为石灰和促净剂;其中石灰加入量为每吨钢水加入6.0kg,促净剂加入量为每吨钢水加入2.0kg;
[0052]
3.eaf至lf目标要求;按合金要求下限加入金属元素或合金,防止合金超目标要求,确保钢水的成分为:c:0.08~0.17%、si:0.10~0.20%、mn:0.86~1.01%、cr:1.10~1.25%;钢水的温度1530~1620℃;
[0053]
(2)lf精炼工艺:
[0054]
所述lf精炼采用沉淀脱氧 扩散脱氧,其中扩散脱氧剂为复合碳化硅140kg和硅铁粉20kg,在在lf冶炼开始20min后进入中后期,此时分多批次加入扩散脱氧剂,每间隔5min加一次,每次加入量为10~20kg;钢水进站迅速造白渣,白渣时间20~40分钟,冶炼时间40~80分钟;
[0055]
(3)vd真空处理工艺:
[0056]
在vd真空处理步骤中,控制真空度为30-50pa,保持时间18~23分钟;破空后喂入铝线以调整钢水中[al]的含量在0.010%~0.025%;再喂入钛铁线调整微合金元素钛含量在0.055%,喂入硅钙线50~80m使高熔点氧化铝夹杂变性为液态钙铝酸盐类夹杂促进上浮以提高连浇炉数,间隔10min后喂入硫磺线(控制硫在0.015%)以提高产品切削性;软吹时间20~30min,以保证钢水中非金属夹杂物充分上浮;vd冶炼过程,采用底吹氮气增氮至55ppm;
[0057]
(4)连铸工艺:
[0058]
所述连铸配置组合式电磁搅拌系统,具体为电磁搅拌为结晶器电磁搅拌、二冷段电磁搅拌和末端电磁搅拌三段式电磁搅拌;采用长水口氩气保护、整体浸入式水口、中间包采用专用覆盖剂等措施,实现全程保护浇铸,防止二次氧化;
[0059]
采用低过热度浇铸,钢水过热度控制在18~30℃,浇铸断面φ380mm,在冷却水作用下,硫化锰以细小的氮化钛或尖晶石为核心,改善硫化物及其他夹杂物形貌;采用全程恒拉速拉坯,拉速为0.65m/min;
[0060]
连铸后进行缓冷,所述入坑缓冷的入坑温度≥500℃,缓冷时间≥30h,出坑温度≤200℃;
[0061]
(5)连续轧制:
[0062]
缓冷后的连铸坯经过加热炉加热,具体为:预热温度为880℃、加热温度为900~1100℃、均热温度为1200~1280℃,总加热时间为5.5h。其中均热段加热时间为2.5h;连铸坯出炉后,经过高压水除鳞去除表面氧化皮。控制初轧温度为1100~1200℃,进连轧温度为900℃,下冷床温度为580℃;
[0063]
(6)缓冷工艺:
[0064]
连轧后得到的圆钢下冷床后入坑缓冷,入坑温度550~600℃,缓冷时间≥30h,出坑温度≤200℃。
[0065]
在圆钢缓冷冷却步骤之后,即可对得到的圆钢进行精整、检验、称重、标识、入库即得到处理后的易切削齿轮钢;
[0066]
对比例1及对比例2均为市场上购买的常规中低碳含硫易切削crmnti齿轮钢(20crmnti系列圆钢)。
[0067]
将本实施例1制备的易切削齿轮钢热轧圆钢和传统齿轮钢(对比例1、对比例2)检测结果做对比,化学成分见表1所示。
[0068]
表1化学成分wt%
[0069][0070]
将实施例1和对比例1、2圆钢均在皮下1/2r处取样检测夹杂物,按gb/t 10561标准a法检测,夹杂评级结果见表2,实施例1的硫化物形貌如图1所示,对比例1硫化物形貌见图2,对比例2氮化物形貌见图3。
[0071]
通过图可以看出,实施例1产品的最大硫化物长度约165um,一方面这种较短塑性夹杂可随着基体变形,不会引发材料断裂失效,另一方面在材料车削过程润滑刀具,延长刀具使用寿命,减少材料加工成本;对比例1硫化物长度已经超出视场范围,实际长约935um,这种超长尺寸夹杂一是使钢铁基体与其产生较大空隙,硫化物剥落后会在产品表面留下肉眼可见缺陷,二是材料在车削过程会粘连刀具,影响产品车削性;对比例2中大量脆性氮化物(长约157um)聚集在一起,割裂了基体组织,其棱角处极易作为裂纹源,引起材料失效断裂。
[0072]
表2非金属夹杂物
[0073][0074]
实施例1产品的力学性能(拉伸、冲击)优异,见表3。
[0075]
表3力学性能
[0076]
[0077]
实施例1产品的淬透性稳定,在以实施例1所述方法制备的钢材中选择2个样品,记为样品1和样品2;同样对比例1和2中的钢材也分别选2个样品,具体测定结果见表4。
[0078]
表4淬透性
[0079][0080][0081]
实施例1产品的晶粒尺寸细小均匀,奥氏体晶粒度均为7.5级,结果见表5。
[0082]
表5晶粒度
[0083][0084]
说明:以上实施例仅用以说明本发明而并非限制本发明所描述的技术方案;因此,尽管本说明书参照上述的各个实施例对本发明已进行了详细的说明,但是本领域的普通技术人员应当理解,仍然可以对本发明进行修改或等同替换;而一切不脱离本发明的精神和范围的技术方案及其改进,其均应涵盖在本发明的权利要求范围内。
再多了解一些
本文用于企业家、创业者技术爱好者查询,结果仅供参考。