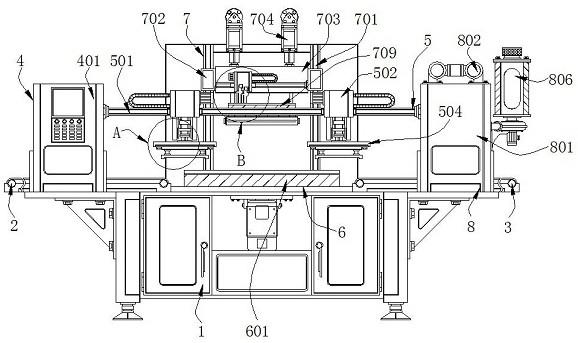
1.本发明涉及膜印机技术领域,具体为一种膜印机。
背景技术:
2.膜印机就是在贴膜表面印刷各种各样的图样,以增加贴膜的美观度,广泛运用于各类膜印刷产品中,使得贴膜有很好的韧性,质地均匀,没有砂眼气泡,表面很平整,它通常是聚丙烯材料做成的,它还预涂了热塑性高分子粘合剂以便和纸张结合,这样一来,贴膜的表面有了更好的光泽,质地更厚实。
3.市场上的膜印机无法对膜印的贴膜进行膜印前的检测工作,无法剔除表面存在污垢及划痕的贴膜,导致无效加工,造成原料浪费的情况。
技术实现要素:
4.本发明的目的在于提供一种膜印机,以解决上述背景技术中提出的问题。
5.为实现上述目的,本发明提供如下技术方案:一种膜印机,包括承载座和检测组件,所述承载座的上端左侧中部设置有上料输送带,且承载座的上端右侧中部设置有下料输送带,用于膜检测的所述检测组件设置于承载座的上端左侧上方,且检测组件包括检测框、调节气缸、调节板、影像检测仪、检测摄像头和照明灯,所述检测框的内部两侧设置有调节气缸,且调节气缸的下端连接有调节板,所述调节板的上端中部安置有影像检测仪,且调节板的下端两侧安置有检测摄像头,所述检测框的内部两侧下部安置有照明灯,所述承载座的上端中部前端设置有用于膜体转运的送料组件,且承载座的上端中心位置设置有用于膜印的承载组件,所述承载座的上端中部后端设置有用于膜印刷的膜印组件,且承载座的上端右侧上方设置有用于膜烘干的干燥组件。
6.进一步的,所述调节气缸关于调节板的中心位置对称设置有两个,且检测摄像头的竖直中轴线与调节板的竖直中轴线相重合。
7.进一步的,所述送料组件包括限位横轨、x轴驱动块、送料气缸、连接板、限位槽、吸盘和紧固螺栓,且限位横轨的上端两侧连接有x轴驱动块,所述x轴驱动块的下端中部设置有送料气缸,且送料气缸的下端连接有连接板,所述连接板下端中部开设有限位槽,且限位槽的内侧连接有吸盘,所述吸盘的四角穿设有紧固螺栓。
8.进一步的,所述连接板与送料气缸呈垂直状分布,且限位槽与连接板呈一体化结构,并且吸盘通过紧固螺栓与限位槽之间螺纹连接。
9.进一步的,所述包括承载组件、承载转盘、承载块、连接螺栓、承载槽、橡胶层、吸附口和红外传感器,且承载转盘的上端安置有承载块,所述承载块的两侧穿设有连接螺栓,且承载块的上端开设有承载槽,所述承载槽的内壁设置有橡胶层,且承载槽的底部中心位置设置有吸附口,所述承载槽的底部两侧设置有红外传感器。
10.进一步的,所述承载块等距分布于承载转盘的上端,且承载块设置有四个,并且承载槽与承载块呈一体化结构,并且橡胶层与承载槽嵌入连接。
11.进一步的,所述膜印组件包括限位导轨、限位滑块、安置块、膜印气缸、连接导轨、膜印驱动块、刮板、印板和膜印油框,且限位导轨的外侧连接有限位滑块,所述限位滑块的外侧衔接有安置块,且安置块的上端两侧连接有膜印气缸,所述安置块的前端设置有连接导轨,且连接导轨的上端连接有膜印驱动块,所述膜印驱动块的下端左侧连接有刮板,且膜印驱动块的下端右侧连接有印板,所述安置块的下端衔接有膜印油框。
12.进一步的,所述膜印油框与连接导轨呈平行状分布,且刮板和印板的下表面贴合于膜印油框的内侧底部上表面。
13.进一步的,所述干燥组件包括干燥框、风机、出风框、加热管、吸风机、净化筒、安置滑轨、安置滑块和活性炭滤芯,且干燥框的上端安置有风机,所述风机的下端连接有出风框,所述干燥框的内侧下部设置有加热管,且干燥框的右侧连接有吸风机,所述吸风机的上端连接有净化筒,且净化筒的内壁设置有安置滑轨,所述安置滑轨的外侧连接有安置滑块,且安置滑块的另一侧衔接有活性炭滤芯。
14.进一步的,所述出风框与加热管呈平行状分布,且加热管设置有三个。
15.本发明提供了一种膜印机,具备以下有益效果:该膜印机,通过多个组件之间的相互配合,实现对贴膜的检测、送料、膜印及干燥的自动化加工,避免工作人员手动进行上下料,存在安全风险,可以对上料的贴膜进行表面的检测,避免贴膜表面存在污垢及划痕的情况,导致无效加工造成原料浪费,可以对贴膜进行连续性膜印加工,提升该膜印机的实际加工效率,同时可以对膜印完成的贴膜进行干燥处理,可以根据实际加工情况选择对贴膜的干燥程度,并且可以对干燥过程中产生的废气进行净化处理,确保生产环境不受污染;1、本发明通过设置在承载座上端左侧上方的检测组件,可以对上料输送带上端输送的贴膜进行膜印前的检测工作,通过影像检测仪配合检测摄像头,可以检测贴膜是否存在污垢及划痕的情况,当检测贴膜为不合格时影像检测仪发出报警,提醒工作人员及时进行处理,当检测为合格时,则继续通过上料输送带对贴膜进行输送,连接在调节板上端两侧的调节气缸,可以根据实际使用情况对检测摄像头的高度进行调节,配合设置在检测框内侧下部两侧的照明灯,确保检测摄像头对贴膜检测的持续性与有效性。
16.2、本发明通过垂直状分布的连接板与送料气缸,可以保证之间位置的准确性,通过送料气缸驱动连接板使得吸盘下降至上料输送带输送的贴膜上表面,通过吸盘对贴膜进行吸附夹持,配合送料气缸上端连接有的x轴驱动块和限位横轨,可以驱动吸附夹持贴膜的吸盘进行x轴直线移动,配合送料气缸将贴膜放置于承载槽内部等待膜印,通过紧固螺栓与连接板相连接的吸盘,便于根据实际膜印的贴膜尺寸进行对应型号的更换,确保吸盘对贴膜的吸附夹持效果,限位槽可以对吸盘的安装起到很好的限位效果,同时吸盘设置有两组,分别实现对贴膜的上料及下料工作。
17.3、本发明通过设置在承载转盘上端的四个承载块,配合承载转盘下端连接有的伺服电机,使得贴膜可以连续放置于承载槽内部,配合承载转盘的顺时针转动进行连续性的膜印加工,提升膜印的效率,通过连接螺栓与承载转盘相连接的承载块便于根据实际膜印的贴膜尺寸进行对应型号的更换工作,当设置在承载槽内侧底部两侧的红外传感器检测到贴膜放置于承载槽内部时,控制吸附口对贴膜进行吸附固定,确保贴膜子啊膜印过程中的稳定性,同时通过伺服电机驱动承载转盘进行顺时针转运工作,配合设置在承载槽内壁的橡胶层,有效防止贴膜在转运过程中表面出现划痕的情况,确保该膜印机的生产质量。
18.4、本发明通过平行状分布的膜印油框与连接导轨,可以保证之间位置的准确性,设置在安置块后端的限位滑块,配合限位滑块内侧连接有的限位导轨,使得膜印气缸可以驱动安置块保持竖直直线位置上进行上下移动,从而确保膜印油框与承载转盘上端贴膜之间相对位置的准确性,通过连接在连接导轨上端的膜印驱动块带动印板和刮板在膜印油框内部向右移动完成对贴膜的膜印工作,相互贴合的刮板和印板的下表面和膜印油框的内侧底部上表面相贴合,可以确保油印准确印在贴膜表面,该膜印机的实际膜印效果。
19.5、本发明通过设置在承载座上端右侧上方的干燥组件,可以对下料输送带上端输送的膜印完成的贴膜进行干燥处理,设置在干燥框内侧下部的三个加热管,配合设置在干燥框上端的风机和出风框,可以对膜印完成的贴膜进行有效的干燥处理,同时可以根据实际加工需求进行加热管数量的选择性开启,从而实现不同干燥程度的干燥处理工作,配合设置在干燥框右侧的吸风机和净化筒,可以对干燥处理过程中产生的废气进行净化处理,吸风机将废气吸入净化筒内部,通过活性炭滤芯净化处理后再排出,避免废气直接排入空气,对环境造成污染的情况,确保该膜印机使用的环保性。
附图说明
20.图1为本发明一种膜印机的整体结构示意图;图2为本发明一种膜印机的承载转盘俯视结构示意图;图3为本发明一种膜印机的检测组件结构示意图;图4为本发明一种膜印机的干燥框内部结构示意图;图5为本发明一种膜印机的净化筒内部结构示意图;图6为本发明一种膜印机的图1中a处放大结构示意图;图7为本发明一种膜印机的图1中b处放大结构示意图;图8为本发明一种膜印机的图2中c处放大结构示意图。
21.图中:1、承载座;2、上料输送带;3、下料输送带;4、检测组件;401、检测框;402、调节气缸;403、调节板;404、影像检测仪;405、检测摄像头;406、照明灯;5、送料组件;501、限位横轨;502、x轴驱动块;503、送料气缸;504、连接板;505、限位槽;506、吸盘;507、紧固螺栓;6、承载组件;601、承载转盘;602、承载块;603、连接螺栓;604、承载槽;605、橡胶层;606、吸附口;607、红外传感器;7、膜印组件;701、限位导轨;702、限位滑块;703、安置块;704、膜印气缸;705、连接导轨;706、膜印驱动块;707、刮板;708、印板;709、膜印油框;8、干燥组件;801、干燥框;802、风机;803、出风框;804、加热管;805、吸风机;806、净化筒;807、安置滑轨;808、安置滑块;809、活性炭滤芯。
具体实施方式
22.请参阅图1-8,本发明提供一种技术方案:一种膜印机,包括承载座1和检测组件4,承载座1的上端左侧中部设置有上料输送带2,且承载座1的上端右侧中部设置有下料输送带3,用于膜检测的检测组件4设置于承载座1的上端左侧上方,且检测组件4包括检测框401、调节气缸402、调节板403、影像检测仪404、检测摄像头405和照明灯406,检测框401的内部两侧设置有调节气缸402,且调节气缸402的下端连接有调节板403,调节板403的上端中部安置有影像检测仪404,且调节板403的下端两侧安置有检测摄像头405,检测框401的
内部两侧下部安置有照明灯406,承载座1的上端中部前端设置有用于膜体转运的送料组件5,且承载座1的上端中心位置设置有用于膜印的承载组件6,承载座1的上端中部后端设置有用于膜印刷的膜印组件7,且承载座1的上端右侧上方设置有用于膜烘干的干燥组件8。
23.具体操作如下,设置在承载座1上端左侧上方的检测组件4,可以对上料输送带2上端输送的贴膜进行膜印前的检测工作,通过影像检测仪404配合检测摄像头405,可以检测贴膜是否存在污垢及划痕的情况,当检测贴膜为不合格时影像检测仪404发出报警,提醒工作人员及时进行处理,当检测为合格时,则继续通过上料输送带2对贴膜进行输送,连接在调节板403上端两侧的调节气缸402,可以根据实际使用情况对检测摄像头405的高度进行调节,配合设置在检测框401内侧下部两侧的照明灯406,确保检测摄像头405对贴膜检测的持续性与有效性。
24.请参阅图1、图3和图6,调节气缸402关于调节板403的中心位置对称设置有两个,且检测摄像头405的竖直中轴线与调节板403的竖直中轴线相重合,送料组件5包括限位横轨501、x轴驱动块502、送料气缸503、连接板504、限位槽505、吸盘506和紧固螺栓507,且限位横轨501的上端两侧连接有x轴驱动块502,x轴驱动块502的下端中部设置有送料气缸503,且送料气缸503的下端连接有连接板504,连接板504下端中部开设有限位槽505,且限位槽505的内侧连接有吸盘506,吸盘506的四角穿设有紧固螺栓507,连接板504与送料气缸503呈垂直状分布,且限位槽505与连接板504呈一体化结构,并且吸盘506通过紧固螺栓507与限位槽505之间螺纹连接。
25.具体操作如下,垂直状分布的连接板504与送料气缸503,可以保证之间位置的准确性,通过送料气缸503驱动连接板504使得吸盘506下降至上料输送带2输送的贴膜上表面,通过吸盘506对贴膜进行吸附夹持,配合送料气缸503上端连接有的x轴驱动块502和限位横轨501,可以驱动吸附夹持贴膜的吸盘506进行x轴直线移动,配合送料气缸503将贴膜放置于承载槽604内部等待膜印,通过紧固螺栓507与连接板504相连接的吸盘506,便于根据实际膜印的贴膜尺寸进行对应型号的更换,确保吸盘506对贴膜的吸附夹持效果,限位槽505可以对吸盘506的安装起到很好的限位效果,同时吸盘506设置有两组,分别实现对贴膜的上料及下料工作。
26.请参阅图1、图2和图8,包括承载组件6、承载转盘601、承载块602、连接螺栓603、承载槽604、橡胶层605、吸附口606和红外传感器607,且承载转盘601的上端安置有承载块602,承载块602的两侧穿设有连接螺栓603,且承载块602的上端开设有承载槽604,承载槽604的内壁设置有橡胶层605,且承载槽604的底部中心位置设置有吸附口606,承载槽604的底部两侧设置有红外传感器607,承载块602等距分布于承载转盘601的上端,且承载块602设置有四个,并且承载槽604与承载块602呈一体化结构,并且橡胶层605与承载槽604嵌入连接。
27.具体操作如下,设置在承载转盘601上端的四个承载块602,配合承载转盘601下端连接有的伺服电机,使得贴膜可以连续放置于承载槽604内部,配合承载转盘601的顺时针转动进行连续性的膜印加工,提升膜印的效率,通过连接螺栓603与承载转盘601相连接的承载块602便于根据实际膜印的贴膜尺寸进行对应型号的更换工作,当设置在承载槽604内侧底部两侧的红外传感器607检测到贴膜放置于承载槽604内部时,控制吸附口606对贴膜进行吸附固定,确保贴膜子啊膜印过程中的稳定性,同时通过伺服电机驱动承载转盘601进
行顺时针转运工作,配合设置在承载槽604内壁的橡胶层605,有效防止贴膜在转运过程中表面出现划痕的情况,确保该膜印机的生产质量。
28.请参阅图1和图7,膜印组件7包括限位导轨701、限位滑块702、安置块703、膜印气缸704、连接导轨705、膜印驱动块706、刮板707、印板708和膜印油框709,且限位导轨701的外侧连接有限位滑块702,限位滑块702的外侧衔接有安置块703,且安置块703的上端两侧连接有膜印气缸704,安置块703的前端设置有连接导轨705,且连接导轨705的上端连接有膜印驱动块706,膜印驱动块706的下端左侧连接有刮板707,且膜印驱动块706的下端右侧连接有印板708,安置块703的下端衔接有膜印油框709,膜印油框709与连接导轨705呈平行状分布,且刮板707和印板708的下表面贴合于膜印油框709的内侧底部上表面。
29.具体操作如下,平行状分布的膜印油框709与连接导轨705,可以保证之间位置的准确性,设置在安置块703后端的限位滑块702,配合限位滑块702内侧连接有的限位导轨701,使得膜印气缸704可以驱动安置块703保持竖直直线位置上进行上下移动,从而确保膜印油框709与承载转盘601上端贴膜之间相对位置的准确性,通过连接在连接导轨705上端的膜印驱动块706带动印板708和刮板707在膜印油框709内部向右移动完成对贴膜的膜印工作,相互贴合的刮板707和印板708的下表面和膜印油框709的内侧底部上表面相贴合,可以确保油印准确印在贴膜表面,该膜印机的实际膜印效果。
30.请参阅图1、图4和图5,干燥组件8包括干燥框801、风机802、出风框803、加热管804、吸风机805、净化筒806、安置滑轨807、安置滑块808和活性炭滤芯809,且干燥框801的上端安置有风机802,风机802的下端连接有出风框803,干燥框801的内侧下部设置有加热管804,且干燥框801的右侧连接有吸风机805,吸风机805的上端连接有净化筒806,且净化筒806的内壁设置有安置滑轨807,安置滑轨807的外侧连接有安置滑块808,且安置滑块808的另一侧衔接有活性炭滤芯809,出风框803与加热管804呈平行状分布,且加热管804设置有三个。
31.具体操作如下,设置在承载座1上端右侧上方的干燥组件8,可以对下料输送带3上端输送的膜印完成的贴膜进行干燥处理,设置在干燥框801内侧下部的三个加热管804,配合设置在干燥框801上端的风机802和出风框803,可以对膜印完成的贴膜进行有效的干燥处理,同时可以根据实际加工需求进行加热管804数量的选择性开启,从而实现不同干燥程度的干燥处理工作,配合设置在干燥框801右侧的吸风机805和净化筒806,可以对干燥处理过程中产生的废气进行净化处理,吸风机805将废气吸入净化筒806内部,通过活性炭滤芯809净化处理后再排出,避免废气直接排入空气,对环境造成污染的情况,确保该膜印机使用的环保性。
32.综上,该膜印机,使用时,首先通过上料输送带2对贴膜进行上料输送,设置在承载座1上端左侧上方的检测组件4,可以对上料输送带2上端输送的贴膜进行膜印前的检测工作,通过影像检测仪404配合检测摄像头405,可以检测贴膜是否存在污垢及划痕的情况,当检测贴膜为不合格时影像检测仪404发出报警,提醒工作人员及时进行处理,当检测为合格时,则继续通过上料输送带2对贴膜进行输送,垂直状分布的连接板504与送料气缸503,可以保证之间位置的准确性,通过送料气缸503驱动连接板504使得吸盘506下降至上料输送带2输送的贴膜上表面,通过吸盘506对贴膜进行吸附夹持,配合送料气缸503上端连接有的x轴驱动块502和限位横轨501,可以驱动吸附夹持贴膜的吸盘506进行x轴直线移动,配合送
料气缸503将贴膜放置于承载槽604内部等待膜印,设置在承载转盘601上端的四个承载块602,配合承载转盘601下端连接有的伺服电机,使得贴膜可以连续放置于承载槽604内部,配合承载转盘601的顺时针转动进行连续性的膜印加工,当贴膜通过承载转盘601转运输送至膜印组件7下方时,设置在安置块703后端的限位滑块702,配合限位滑块702内侧连接有的限位导轨701,使得膜印气缸704可以驱动安置块703保持竖直直线位置上进行上下移动,从而确保膜印油框709与承载转盘601上端贴膜之间相对位置的准确性,通过连接在连接导轨705上端的膜印驱动块706带动印板708和刮板707在膜印油框709内部向右移动完成对贴膜的膜印工作,相互贴合的刮板707和印板708的下表面和膜印油框709的内侧底部上表面相贴合,可以确保油印准确印在贴膜表面,完成膜印的贴膜继续通过承载转盘601进行顺时针转运输送,当贴膜转运至右侧的吸盘506下方时,通过吸盘506吸附转运至下料输送带3上端进行输送,设置在承载座1上端右侧上方的干燥组件8,可以对下料输送带3上端输送的膜印完成的贴膜进行干燥处理,设置在干燥框801内侧下部的三个加热管804,配合设置在干燥框801上端的风机802和出风框803,可以对膜印完成的贴膜进行有效的干燥处理,同时可以根据实际加工需求进行加热管804数量的选择性开启,从而实现不同干燥程度的干燥处理工作,配合设置在干燥框801右侧的吸风机805和净化筒806,可以对干燥处理过程中产生的废气进行净化处理。
再多了解一些
本文用于企业家、创业者技术爱好者查询,结果仅供参考。