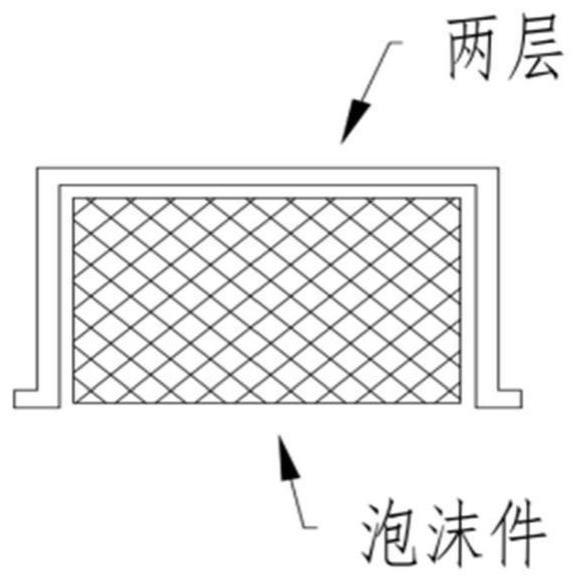
1.本发明属于航空航天复合材料液体成型领域,具体提供了一种碳纤维复合材料飞机纵向构件的制备工艺。
背景技术:
2.由于复合材料碳纤维增强材料具有高的比强度,因此在航空航天领域得到了越来越广泛的应用。复合材料的成型工艺有手糊成型、液体真空导入等方法。手糊成型的缺点是依赖人工,分散性大,一般不为生产所采用。热压罐成型的缺点是能耗大,成本高。而液体成型生产方式为:通过模具结合真空导入树脂制备,模具的采用多为金属材质。尽管一次性液体成型比较方便实用,但是液体成型所需的模具比较多而且具有对应性,模具的适应性范围窄,制备成本增高,且研制模具需要周期长,更改成本高。
3.另一种成型方式则采用泡沫模具来作为支撑,外部将前后腹板、上下缘条铺层独立成型而后拼接一次注胶一次成型,通过环氧树脂固化粘接固定上下缘条、前后腹板之间的缝隙,因为其四个组成部分分开制作最后由树脂一次固化,该工艺方法导致其碳布叠层气泡率高、叠层之间小幅度串位,进而对其力学性能造成不良影响。且液体导入成型后将泡沫包裹住,则需要将成型制件的端部锯开来抠除泡沫,该方法虽然可以去除泡沫模具件,但是泡沫与成型制件均遭到了损坏,而且抠除过程中比较费时费力。
技术实现要素:
4.鉴于上述问题,本发明提供了一种碳纤维复合材料飞机纵向构件的制备工艺,所述纵向构件包括上缘条、下缘条、前腹板及后腹板结构件,该制备工艺包括如下步骤,
5.步骤1:制备内层模具支撑件,所述内层模具支撑件与上缘条、前腹板及后腹板三者组合后形状相互匹配;
6.步骤2:制备下缘条结构件;
7.步骤3:对内层模具支撑件进行首次铺层,得到结构件a;
8.步骤4:将结构件a与下缘条结构件组装后,在结构件a外包裹铺剩余层数,经树脂导入、固化成型制备成品纵向构件。
9.进一步的,所述步骤1中内层模具支撑件通过如下步骤制备而成:
10.步骤1.1:采用泡沫雕刻机根据纵向构件的外形切割泡沫支撑件;
11.步骤1.2:采用碳布原料对上述泡沫支撑件除底部之外的其他面进行两层铺层,铺层顺序为[(0,90
°
)]2;两侧底边具有凸起的弯部,形成ω形铺层剖面;
[0012]
步骤1.3:对铺层后的泡沫支撑件进行树脂导入、固化成型、切割得到∩形的内层模具支撑件。
[0013]
进一步的,步骤1.3中,具体包括如下操作步骤:
[0014]
步骤1.3.1:在铺层后的泡沫支撑件上由下至上依次铺有脱模布、有孔隔离膜及导流网,置于一底板上;外部套有真空袋,真空袋边缘粘接在底板上,采用真空泵除去真空袋
内空气,得到待成型组件;
[0015]
步骤1.3.2:取液体成型用环氧树脂与固化剂,按照质量比4:1混合搅拌,放置真空罐除去内部气泡,备用;
[0016]
步骤1.3.3:通过真空泵向待成型组件内导入前述搅拌除气泡后的环氧树脂,至环氧树脂完全浸润泡沫支撑件和碳布原料,导入完毕;
[0017]
步骤1.3.4:将导入树脂后的待成型组件置于固化炉中,固化温度80℃,时间4.5小时,取出;
[0018]
步骤1.3.5:将碳布原料与泡沫支撑件分离得到碳布成型ω型件;对ω型件进行切除得到剖面为∩形的内层模具支撑件。
[0019]
进一步的,步骤2中制备泡沫件的下缘条,铺层顺序为[[(0,90
°
)3,(
±
45
°
)4]经过导入树脂、固化得到下缘条。
[0020]
进一步的,步骤3中对内层模具支撑件进行二次铺层,上缘条、前腹板及后腹板分开铺层,其中前腹板、后腹板的铺层顺序为[(0,90
°
)3,(
±
45
°
)4];上缘条的铺层顺序为[(0,90
°
)5,(
±
45
°
)3]。
[0021]
进一步的,制备成型各结构件,真空导入树脂后,对多余的树脂通过出胶管与真空泵连接真空出胶;出胶过程中,出胶管中部支撑一支件,该支件将出胶管支撑形成一具有拐点的倒v形,该拐点高于整体件≥1m,且上升出胶的边与水平面呈60
°
夹角。
[0022]
进一步的,步骤1中泡沫支撑件的高度高于预定高度2-5mm。
[0023]
进一步的,步骤1.2中,所述碳布原料通过如下方法制备:取碳纤维布与定型剂,所述定型剂用丙酮溶解后,按照每平方米≤12g的用量比例均匀涂抹在碳纤维布上,静置至丙酮完全挥发,得到碳布原料。
[0024]
进一步的,在固化炉中,从常温按照0.5-2.5℃/分钟的速率升温至80℃。
[0025]
进一步的,该制备工艺适用于结构件铺层数》5层。
[0026]
本成型工艺将飞机纵向构件的各个结构件分组来成型,采用纵向构件最终结构的一部分内层模具支撑件来当成型模具,再与下缘板进行组装,液体二次成型,相对于采用泡沫件做模具,则无需截断制件取出内部模具,相对于分体成型再组装粘接工艺则具有更高的力学承载。
附图说明
[0027]
图1为内层模具支撑件的铺层示意图;
[0028]
图2为真空导入示意图;
[0029]
图3为经过二次铺层的结构件a示意图;
[0030]
图4为成品纵向构件结构示意图;
[0031]
图5为成品纵向构件的加载示意图;
[0032]
图6为纵向构件危险截面应力分布图;
[0033]
图7为试件位移-载荷对比图;
[0034]
图8为试件时间-载荷对比图;
[0035]
图9本发明制件超声波检测波形图;
[0036]
图10为旧工艺制件超声波检测波形图;
[0037]
图11为一种真空导入出胶系统结构示意图;
具体实施方式
[0038]
为了使本发明的目的、技术方案及优点更加清楚明白,以下结合附图及实施例,对本发明进行进一步详细说明。应当理解,此处所描述的具体实施例仅仅用以解释本发明,并不用于限定本发明。
[0039]
在碳纤维复合材料飞机纵向构件的制备过程中,目前常采用分体成型再粘接固化方式,具体的将制备好的前后腹板、上下缘条铺层独立成型而后拼接,内置有泡沫件做支撑,一次注胶一次成型,通过环氧树脂固化粘接固定上下缘条、前后腹板之间的缝隙,因为其四个组成部分分开制作最后由树脂一次固化,该工艺方法导致其各个部件的碳布叠层气泡率高、叠层之间小幅度串位,进而对其力学性能造成不良影响,且抠除泡沫比较麻烦。
[0040]
参考图1-3,本发明提供了一种碳纤维复合材料飞机纵向构件的制备工艺,所述纵向构件包括上缘条、下缘条、前腹板及后腹板结构件,该制备工艺包括如下步骤;
[0041]
步骤1:制备与上缘条、前腹板及后腹板组合后形状相互匹配的内层模具支撑件;
[0042]
步骤1.1:采用泡沫雕刻机根据纵向构件的外形切割泡沫支撑件;
[0043]
步骤1.2:采用碳布原料对上述泡沫支撑件除底部之外的其他面进行两层铺层;铺层剖面ω形,两侧底边具有凸起的弯部;
[0044]
步骤1.3:对铺层后的泡沫支撑件进行树脂导入、固化成型、切割得到∩形的内层模具支撑件。
[0045]
步骤1.3.1:在铺层后的泡沫支撑件上由下至上依次铺有脱模布、有孔隔离膜及导流网,并置于一底板上;外部套有真空袋,真空袋边缘粘接在底板上,采用真空泵除去真空袋内空气,得到待成型组件;
[0046]
步骤1.3.2:取液体成型用环氧树脂与固化剂,按照质量比4:1混合搅拌,放置真空罐除去内部气泡,备用;
[0047]
步骤1.3.3:通过真空泵向待成型组件内导入前述搅拌除气泡后的环氧树脂,至环氧树脂完全浸润泡沫支撑件和碳布原料;
[0048]
步骤1.3.4:将导入树脂后的待成型组件置于固化炉中,固化温度80℃,时间4.5小时,取出;
[0049]
步骤1.3.5:将碳布原料与泡沫支撑件分离得到碳布成型ω型件;切除ω型件两侧与顶面水平的部分及底部的圆角,得到剖面为∩形的内层模具支撑件。
[0050]
步骤2:制备下缘条结构件,制作的时候尺寸略大于实际尺寸;
[0051]
步骤3:对内层模具支撑件进行二次铺层成型,得到结构件a;
[0052]
步骤4:将结构件a与下缘条结构件组装后整体铺层一层90度,该最外层铺层的两侧底边搭在下缘条表面,再经树脂导入、固化成型,切除掉多余部分,制备成品纵向构件。
[0053]
该方案中所述纵向构件包括梁、长桁、桁条等。
[0054]
本技术方案中将纵向构件分为2组来成型,第一组为前后腹板及上缘条,通过雕刻泡沫支撑件,采用碳布原料对该泡沫支撑件进行2层铺层、导入树脂成型形成“ω”型件即内层模具支撑件,这里面的内层模具支撑件的铺层层数要小于二次铺层的层数,以导入树脂后解除泡沫支撑件后,可以承载二次铺层后与下缘条组合导入树脂成型的压力来选择内层
模具支撑件的首次铺层层数,一般优选为2层。本方案中制备的内层模具支撑件不仅是纵向构件结构的一部分主要承担了模具的作用,采用工件本身作为模具支撑打破了传统的制备工艺思路。
[0055]
本技术方案中将除下缘条部分分为三层进行制备,除去最外一层包裹层90度的碳布和最内层的2层90度碳布模具支撑件,中间的夹层部分即二次铺层部分是承力的主体,最内最外的铺层主要的目的是为了对中间的主要承力部分提供有效的支撑与包裹,碳布比较软,若不分层进行处理,则在导树脂的过程中真空处理下容易产生串位滑移,影响制件性能。
[0056]
在本方案中,其中最里层的模具支撑件是经历了二次注胶,其他层尤其是中间层只经历一次注胶,二次注胶的主要缺点是造成碳布间隙的树脂不均,影响制件的力学性能,但对于本制件而言,二次注胶影响的最内层并非承力的主体,所以可忽略其对本制件力学性能的负面影响。如果一次将上面三个面注胶固化,将无法保证作为承力主体的碳布铺层是否在最外一层的碳布下发生滑移,故不能有效保证其力学性能稳定。
[0057]
作为方案的改进,步骤2中制备泡沫件的下缘条,铺层顺序为[(0,90
°
)3,(
±
45
°
)4]经过导入树脂、固化得到下缘条。45度铺层将力沿水面45度方向传递,产生平行于纵向构件方向的扭矩,提高纵向构件抗扭能力,90度铺层一方面将力从上缘条传递到下缘条,另一方面提高纵向构件抗剪能力。45度铺设在90度下方主要是考虑到制件表面承受剪力,45度抗扭能力强但抗剪能力弱,故90度铺设在45度上方可起到保护作用。该铺层顺序从力学传递方向角度设计,以此提高整体性能。
[0058]
作为方案的改进,步骤3中对内层模具支撑件进行二次铺层,其中前腹板、后腹板的铺层顺序为[(0,90
°
)3,(
±
45
°
)4];上缘条的铺层顺序为[(0,90
°
)5,(
±
45
°
)3]。
[0059]
作为方案的改进,为了进一步的排除树脂内的气泡,制备成型各结构件形成整体件,真空导入树脂后,对多余的树脂通过出胶管与真空泵连接真空出胶;参考图11,出胶过程中,出胶管中部支撑一支件1,该支件将出胶管支撑形成一具有拐点的倒v形,该拐点高于整体件≥1m,且上升出胶的边与水平面呈60
°
夹角。多余的树脂在经过上述处理后的出胶管从真空袋流向树脂收集器时,使得气泡与树脂的流动路径变为向上运行,经过拐点再向下运行,该运行轨迹使得其内部的气泡由于高度升高,体积增大,同时树脂受重力作用比气泡更显著,因此气泡会不断与树脂分离,提前进入树脂收集器,达到二次除去气泡的效果,本设计在于成型过程中排除气泡,相对于在搅拌过程中排除气泡,进一步减少了气泡。本装置结构简单,操作简便,成本低廉的优势,并能更好地除去树脂中的气泡,提高成品件的质量。
[0060]
作为方案的改进,步骤1中泡沫支撑件的高度高于预定高度2-5mm。本技术方案的成型技术适用于纵向构件结构件铺层大于5层的结构件成型制备,由于碳纤维布具有一定的弹性,且真空导入时难免出现树脂在碳纤维层间分布不均堆积于下方情况。另外,当碳布铺层多于5层,制作“ω”型件时底部难免会发生弯曲,因此应在步骤1中将泡沫支撑件高度加工得高一些,高于预定高度2-5mm,在碳纤维成型后将切去弯曲部分,以提高整体精度。
[0061]
作为方案的改进,步骤1.2中,所述碳布原料通过如下方法制备:取碳纤维布与定型剂,所述定型剂用丙酮溶解后,按照每平方米≤12g的用量比例均匀涂抹在碳纤维布上,优选选为12g,静置至丙酮完全挥发,得到碳布原料;制备内层模具支撑件铺层中。定型剂选择丙酮溶液能防止碳布发生散丝,但过多的定型剂会导致制品的气泡率增加,12g/m2是一
个临界的状态,综合性能达到最优值。丙酮虽然有毒,但固化剂在其中溶解度高,在备选溶剂中性价比最高。
[0062]
作为方案的改进,步骤1.3.1中底板上贴有特氟龙薄膜。
[0063]
作为方案的改进,为了保障制件内部与外部同时固化制,从常温按照0.5-2.5℃/分钟的速率升温至80℃。在固化炉中制件越厚,所需的上升温度速率越小。
[0064]
对试件1与试件2进行如下两方面对比实验:
[0065]
其中试件1为采用分体成型再粘接固化方式制备的纵向构件结构件。试件2本发明技术方案生产制造的纵向构件结构件。
[0066]
对比实验一:采用超声波检测仪材料性能及工艺碳布夹层气泡率对比
[0067]
如图9显示为试件2超声波检测波形图,图10为试件1超声波检测波形图,可以对比两次超声波检测的波形,显而易见,旧工艺制件中底波衰减过快,进而可推知旧工艺的气泡率要高于新工艺即旧工艺制件相对新工艺制件存在缺陷。分析其原因,碳布间摩擦阻力很小相比其堆叠后人工的挤压和真空泵提供的真空压可忽略不计,所以当碳布层数堆叠超过5层时其难免将会出现贴合不紧或相对滑动的现象。新工艺模具制品一体化工艺大范围限制了碳布铺层间相对移动的空间,有效地减小了制件的气泡率,提高了力学性能。
[0068]
对比实验二:通过对梁进行加载,对比试件1与试件2的力学性能,加载原理:纵向构件的两末端放置在支架上,没有额外的固定,在中间部位施加一个垂直于整个梁表面且竖直向下的集中力,进行静力试验。直到试件破坏,记录其最大位移。参考图6,由纵向构件的加载方式可知,纵向构件所受的载荷特点为主要承受弯曲载荷和少量的扭转载荷。纵向构件主要受弯曲载荷,可知加载区域为危险截面,即应力最大的区域。截面应力大小由公式:
[0069][0070]
得出,其中m为此处弯矩大小,y为点到中性层的距离,iz为对z轴的截面惯性矩。纵向构件上缘条表面受到的压应力最大,下缘条表面受到的拉应力最大。碳纤维的材料特性为抗拉不抗压,上缘条表面最为危险。剪切弯曲时,梁的横截面上除弯矩外还存在剪力,因此必然存在切应力。由于梁的切应力与截面形状有关,故需分别研究。截面切应力公式为
[0071][0072]
其中,fs为剪力,sz为静距,b为截面宽度。剪应力最大值在前后腹板的中间处,计算得剪应力远小于主应力故忽略。
[0073]
通过加载试验发现:参考图7-8,
[0074]
试件一使用原始工艺制作,加载速度为5mm/min,在2.49kn、位移25.15mm时发生破坏。
[0075]
试件二采用模具制品一体化工艺制作,加载速度为20mm/min,在4.18kn、位移24.53mm时发生破坏。由此可见,采用本技术方案模具制品工艺的试件能够承受更大的载荷。
[0076]
其中试件二采用较快的加载速度,试件一采用相对慢的加载速度;按照正常推理相同的加载下更容易造成试件二的破坏,但从结果上看试件二的承载性能依旧远优于慢速
加载。
[0077]
综上,造成新旧工艺制件的力学性能差异的因素除上述因气泡率造成的制件缺陷外(此制件缺陷为影响力学性能的主要因素),旧工艺通过环氧树脂固化粘接固定上下缘条、前后腹板之间的缝隙,也是其力学性能弱于新工艺制件的原因之一,新工艺制件将上缘条与前后腹板制为一体,最后与下缘条进行拼接,此拼接工艺考虑到纵向构件上缘条表面受到的压应力最大,下缘条表面受到的拉应力最大。碳纤维的材料特性为抗拉不抗压,加载过程中上缘条表面最为危险。相比上缘条,下缘条在此加载情况下并不容易发生破坏,故新工艺(模具制品一体化工艺)相比旧工艺在制件的加工过程中充分发挥了碳纤维抗拉的特性,同时回避其抗压性能差的特点,扬长避短,从而使其力学性能得到较大提升。需要说明的是,其它类似的二次成型工艺也在本专利的保护范围内,如:步骤12中“ω”型件也看可以制成其他形状,做两个c型,固化后修剪,对着放,形成矩形,用结构胶粘好,形成阳模,然后在上下放置缘条,二次注胶。
[0078]
以上所述仅为本发明的较佳实施例而已,并不用以限制本发明,凡在本发明的精神和原则之内所作的任何修改、等同替换和改进等,均应包含在本发明的保护范围之内。
再多了解一些
本文用于企业家、创业者技术爱好者查询,结果仅供参考。