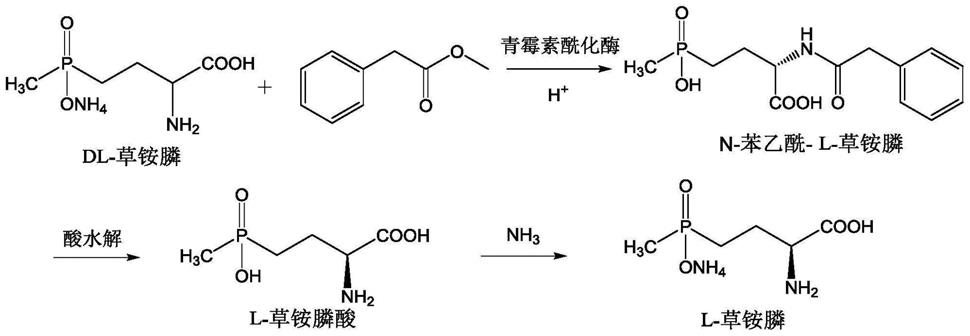
一种酶拆分法制备l-草铵膦的工艺
技术领域
1.本发明涉及一种酶拆分法制备l-草铵膦的工艺,属于农药制备技术领域。
背景技术:
2.草铵膦是一种谷氨酰胺类似物,能与植物体内谷氨酰胺合成酶结合,抑制酶活性,导致植物谷氨酰胺合成受阻,造成植物死亡。草铵膦具有高效、广谱、低毒的特点,已成长为世界第二大除草剂。草铵膦具有氨基酸结构,存在d、l两种构型,其中仅l构型具有灭草活性,因此,开发光学纯的l-草铵膦能够有效降低农药使用量,对农药使用减量增效具有重要意义。
3.现有混旋草铵膦工艺成熟,产量大,以混旋草铵膦拆分出l-草铵膦是合成l-草铵膦的重要研究方向,包括化学拆分法和酶拆分法。
4.美国专利us5767309报道了dl-草铵膦的化学拆分法:利用奎宁与l-草铵膦成盐后结晶析出,再用氨中和得到l-草铵膦。该方法需要使用价格昂贵的奎宁且所得产品光学纯度低。专利cn201811235641中dl-草铵膦和手性辅基、金属离子络合形成配位化合物,使d-草铵膦构型反转生成l-草铵膦,再水解得到l-草铵膦,该方法路线简单、收率高,但手性辅基不易得、所得产品旋光值低。
5.美国专利us4389488、us4922013报道了通过dl-草铵膦苯乙酰化衍生,再用青霉素g酰化酶选择性水解n-苯乙酰-l-草铵膦衍生物,得到高旋光值的l-草铵膦, n-苯乙酰-d-草铵膦通过消旋后,继续酶拆分。该方法中草铵膦经脱氨后,与苯乙酰氯反应,得到苯乙酰衍生物,加酸至ph1-2结晶得到n-苯乙酰-dl-草铵膦酸,n-苯乙酰-dl-草铵膦酸加碱溶解加入青霉素g酰化酶选择性水解n-苯乙酰-l-草铵膦酸,再加酸至ph1-2结晶除去未反应的n-苯乙酰-d-草铵膦酸,所得l-草铵膦酸溶液经加碱调ph,提纯后得到l-草铵膦酸,进一步反应得到l-草铵膦。该工艺收率达到80%以上,产品光学纯度99%以上,但该工艺过程长,需要两次调碱、两次调酸,使用大量酸碱,同时产生大量强酸废水。具体合成路线如图2所示。
技术实现要素:
6.本发明的目的是提供一种酶拆分法制备l-草铵膦的工艺,工艺路线短,操作简便,拆分效率高,三废量少,适合工业化生产。
7.为了实现上述目的,本发明采用的技术方案是:一种酶拆分法制备l-草铵膦的工艺,包括以下步骤:步骤一、将dl-草铵膦和苯乙酸甲酯加入混合溶剂中,加入十二烷基磺酸钠,加酸调节ph至5.5-6.5,加入青霉素酰化酶反应,反应过程控制ph维持5.5-6.5,反应完成后加入有机溶剂萃取未反应的苯乙酸甲酯,水相加酸调ph至1.5-2.5,结晶得到n-苯乙酰-l-草铵膦酸,母液为d-草铵膦酸溶液,d-草铵膦酸溶液高温消旋后套用;步骤二、将步骤一得到的n-苯乙酰-l-草铵膦酸加入水中悬浮,加入酸,加热回流,反应完成后加有机溶剂萃取反应生成的苯乙酸,并得到l-草铵膦酸溶液;
步骤三、向步骤二得到的l-草铵膦酸溶液中加入氨水,调节ph为7-8,减压脱水至含水30-40%,加甲醇稀释至水分质量含量为10-20%结晶,过滤除盐得到l-草铵膦甲醇溶液,蒸干后加甲醇重结晶,得l-草铵膦。
8.本发明技术方案的进一步改进在于:步骤一中所述十二烷基磺酸钠的加入量为dl-草铵膦质量的0.5-1%。
9.本发明技术方案的进一步改进在于:步骤一中所述青霉素酰化酶为青霉素酰化酶溶液或固定化青霉素酰化酶,酶的加入量为dl-草铵膦质量的2-5%,反应温度为15-20℃,反应时间10-20h。
10.本发明技术方案的进一步改进在于:所述步骤一中dl-草铵膦和苯乙酸甲酯的摩尔比为1:0.6-1.0。
11.本发明技术方案的进一步改进在于:步骤一中所述混合溶剂为水和醇的混合溶液,溶剂的量为dl-草铵膦质量的3-4倍,醇的用量为水质量的5-20%,所述醇为异丙醇、异丁醇、仲辛醇和异辛醇中的一种。
12.本发明技术方案的进一步改进在于:所述步骤二中水的加入量为n-苯乙酰-l-草铵膦酸质量的3-5倍,酸的加入量为n-苯乙酰-l-草铵膦酸摩尔量的0.5-2倍。
13.本发明技术方案的进一步改进在于:步骤一、二中所述有机溶剂均为二氯甲烷、氯仿、甲苯和二甲苯中的一种,步骤一中有机溶剂的加入质量为dl-草铵膦质量的1-3倍,步骤二中有机溶剂的加入质量为n-苯乙酰-l-草铵膦酸质量的2-3倍。
14.本发明技术方案的进一步改进在于:步骤一、二中所述的酸为盐酸或硫酸。
15.由于采用了上述技术方案,本发明取得的技术效果有:本发明克服了酶拆分法中工艺路线长,反复调酸碱,后处理复杂,废水量大的问题,使用草铵膦铵盐直接酶合成苯乙酰草铵膦,省去了原方法中化学合成苯乙酰草铵膦需要的脱氨步骤,避免了脱氨废水的产生。本发明实现了经过1次调酸和1次调碱生产l-草铵膦,较原工艺两次调酸调碱大大缩短了操作流程,降低废水量。
16.本发明收率高,单次拆分收率达到85%以上,且光学纯度达到99%以上,适合工业化生产;拆分出的d-草铵膦酸消旋后继续套用不浪费物料,不污染环境,安全环保。
附图说明
17.图1是本发明的工艺路线图;图2是现有技术工艺路线图。
具体实施方式
18.下面结合具体实施例对本发明做进一步详细说明:一种酶拆分法制备l-草铵膦的工艺,工艺路线如图1所示,包括以下步骤:步骤一、将dl-草铵膦和苯乙酸甲酯加入溶剂中,所述dl-草铵膦和苯乙酸甲酯的摩尔比为1:0.6-1.0,优选1:0.6-0.75;所述溶剂为水和醇的混合溶剂,醇的用量为水质量的5-20%,所述醇为异丙醇、异丁醇、仲辛醇和异辛醇中的一种,优选仲辛醇,混合溶剂的用量为dl-草铵膦质量的3-4倍;加入十二烷基磺酸钠,加入量为dl-草铵膦质量的0.5-1%,再加盐酸或硫酸调节ph至5.5-6.5,加入青霉素酰化酶反应,所述青霉素酰化酶为青霉素酰化
酶溶液或固定化青霉素酰化酶,优选固定化青霉素酰化酶,酶的加入量为dl-草铵膦质量的2-5%(酶活为200-500 iu/g),反应温度为15-20℃,反应过程控制ph维持5.5-6.5,反应时间10-20h,反应完成后过滤出酶,滤液加入有机溶剂萃取未反应的苯乙酸甲酯,有机溶剂的量为dl-草铵膦质量的1-3倍,所述有机溶剂为二氯甲烷、氯仿、甲苯和二甲苯中的一种,得到的水相加盐酸或硫酸调ph至1.5-2.5,结晶得到n-苯乙酰-l-草铵膦酸,母液为d-草铵膦酸溶液,d-草铵膦酸溶液高温消旋后结晶套用;步骤二、将步骤一得到的n-苯乙酰-l-草铵膦酸加入3-5倍质量的水中悬浮,加盐酸或硫酸,加入量为n-苯乙酰-l-草铵膦酸摩尔量的0.5-2倍,加热回流,反应完成后,加有机溶剂萃取反应生成的苯乙酸,所述有机溶剂为二氯甲烷、氯仿、甲苯和二甲苯中的一种,加入量为n-苯乙酰-l-草铵膦酸质量的2-3倍,并得到l-草铵膦酸溶液;步骤三、向步骤二得到的l-草铵膦酸溶液中加氨水,调节ph为7-8,减压脱水至含水30-40%,加甲醇稀释至含水10-20%结晶,过滤除盐,得到l-草铵膦甲醇溶液,蒸干后加余重的2倍甲醇结晶,得l-草铵膦。
19.实施例1一种酶拆分法制备l-草铵膦的工艺,包括以下步骤:步骤一、取dl-草铵膦104g(95%,0.5mol)、苯乙酸甲酯45g(0.3mol)加入1l四口瓶,加入水300g、仲辛醇15g、十二烷基苯磺酸钠0.5g,搅拌,用硫酸调ph至5.5,加入固定化青霉素酰化酶5.2g(200iu/g),温度15℃反应,反应时间10h,反应过程滴加2%的氢氧化钠溶液控制反应液维持ph5.5。反应完成后过滤出酶,滤液加入104g甲苯萃取,取水相加入硫酸调ph至1.5搅拌结晶、过滤、烘干得n-苯乙酰-l-草铵膦酸65.8g,含量99.1%,收率87.1%。母液为d-草铵膦酸溶液。甲苯相含未反应的苯乙酸甲酯,蒸馏回收甲苯、苯乙酸甲酯。
20.步骤二、取步骤一中n-苯乙酰-l-草铵膦酸加入200g水中悬浮,加入硫酸11g(98%),加热回流25h,反应完成后加甲苯130g萃取反应生成的苯乙酸,得l-草铵膦酸溶液。
21.步骤三、向l-草铵膦酸溶液加氨水调ph为7-8,减压脱水至含固量70%,加甲醇调节水分质量含量为20%,结晶30min,过滤除盐,取滤液减压蒸干后加甲醇100g结晶,过滤烘干得l-草铵膦44.1g,含量95.5%,ee值99.7%,收率以原料dl-草铵膦中l-草铵膦计85%。含量及ee值检测方法为高效液相色谱法,色谱柱250 mm
×
4.6 mm (i.d.) 强阴离子交换不锈钢柱,内装sax,5μm填充物;流动相:称取6.80g磷酸二氢钾,用970ml新蒸二次蒸馏水溶解,加入30ml甲醇,经滤膜过滤,并进行脱气,c(kh2po4) = 0.05 mol/l。检测波长:195 nm。测定l-草铵膦、d-草铵膦含量,计算ee值。
22.实施例2一种酶拆分法制备l-草铵膦的工艺,包括以下步骤:步骤一、取dl-草铵膦104g(95%,0.5mol)、苯乙酸甲酯75g(0.5mol)加入1l四口瓶,加入水350g、仲辛醇70g,十二烷基磺酸钠1g搅拌,用盐酸调ph至6.5,加入固定化青霉素酰化酶2g(200iu/g),温度20℃反应,反应时间20h,反应过程滴加2%的氢氧化钠溶液控制反应液维持ph6.5。反应完成后过滤出酶,滤液加入312g甲苯萃取,取水相加入盐酸调ph至2.5搅拌结晶、过滤过滤、烘干得n-苯乙酰-l-草铵膦酸68.0g,含量99%,收率90.0%。甲苯相含未反应的苯乙酸甲酯,蒸馏回收甲苯、苯乙酸甲酯。
23.步骤二、取步骤一中n-苯乙酰-l-草铵膦酸加入340g水中悬浮,加入硫酸45g
(98%),加热回流15h,反应完成后加甲苯200g萃取反应生成的苯乙酸,得l-草铵膦酸溶液。
24.步骤三、向l-草铵膦酸溶液加入氨水调ph为7-8,减压脱水至含固量70%,加甲醇调节水分质量含量为20%,结晶30min,过滤除盐,取滤液减压蒸干后加甲醇100g结晶,过滤烘干得l-草铵膦45.0g,含量95.7%,ee值99.8%,收率以原料dl-草铵膦中l-草铵膦计87%。
25.实施例3一种酶拆分法制备l-草铵膦的工艺,包括以下步骤:步骤一、取dl-草铵膦104g(95%,0.5mol)、苯乙酸甲酯56.2g(0.375mol)加入1lml四口瓶,加入水300g、异辛醇50g,十二烷基磺酸钠0.7g搅拌,用盐酸调ph至6.5,加入固定化青霉素酰化酶3g(200iu/g),温度20℃反应,反应时间15h,反应过程滴加2%的氢氧化钠溶液控制反应液维持ph=6.0。反应完成后过滤出酶,滤液加入200g二氯甲烷萃取,取水相加入盐酸调ph至2.0搅拌结晶、过滤得湿固体n-苯乙酰-l-草铵膦酸90g,含水约25%。
26.步骤二、取步骤一中n-苯乙酰-l-草铵膦酸加入250g水中悬浮,加入盐酸50g(38%),加热回流20h,反应完成后加二氯甲烷200g萃取反应生成的苯乙酸,得l-草铵膦酸溶液。
27.步骤三、向l-草铵膦酸溶液减压脱水浓缩,加入氨水至ph为7-8,减压脱水至含固量70%,加甲醇调节水分质量含量为15%,结晶30min,过滤除盐,取滤液减压蒸干后加甲醇100g结晶,过滤烘干得l-草铵膦45.7g,含量95.4%,ee值99.7%,收率以原料dl-草铵膦中l-草铵膦计88%。
28.实施例4一种酶拆分法制备l-草铵膦的工艺,包括以下步骤:步骤一、取dl-草铵膦104g(95%,0.5mol)、苯乙酸甲酯56.2g(0.375mol)加入1lml四口瓶,加入水300g、异丙醇50g,十二烷基磺酸钠0.5g搅拌,用盐酸调ph至6.5,加入固定化青霉素酰化酶5g(200iu/g),温度20℃反应,反应时间10h,反应过程滴加2%的氢氧化钠溶液控制反应液维持ph=6.0。反应完成后过滤出酶,滤液加入200g二氯甲烷萃取,取水相加入盐酸调ph至2.0搅拌结晶、过滤得湿固体n-苯乙酰-l-草铵膦酸87g,含水约25%。
29.步骤二、取步骤一中n-苯乙酰-l-草铵膦酸加入250g水中悬浮,加入硫酸11g(98%),加热回流25h,反应完成后加二甲苯200g萃取反应生成的苯乙酸,得l-草铵膦酸溶液。
30.步骤三、向l-草铵膦酸溶液加氨水调ph为7-8,减压脱水至含固量70%,加甲醇调节水分质量含量为20%,结晶30min,过滤除盐,取滤液减压蒸干后加甲醇100g结晶,过滤烘干得l-草铵膦44.8g,含量95.1%,ee值99.3%,收率以原料dl-草铵膦中l-草铵膦计86%。
31.实施例5d-草铵膦的消旋实施例2中,步骤一中结晶n-苯乙酰-l-草铵膦酸过滤所得母液为d-草铵膦酸溶液,加入5-硝基水杨醛2g,加热至回流反应20h,得消旋dl-草铵膦,蒸出部分水,加甲醇至水分质量含量20%,滤除盐,滤液加甲醇稀释至水分质量含量为10-15%,室温结晶得到dl-草铵膦酸,继续酶拆分。
32.对比例1一种酶拆分法制备l-草铵膦的工艺,包括以下步骤:n-苯乙酰-l-草铵膦酸的制备:取dl-草铵膦104g(95%,0.5mol)、苯乙酸甲酯45g
(0.3mol)加入1l四口瓶,加入水300g、甲醇60g、十二烷基苯磺酸钠0.5g,搅拌,用硫酸调ph至5.5,加入固定化青霉素酰化酶5.2g(200iu/g),温度15℃反应,反应时间10h,反应过程滴加2%的氢氧化钠溶液控制反应液维持ph5.5。反应完成后过滤出酶,滤液加入200g甲苯萃取,取水相加入硫酸调ph至1.5搅拌结晶、过滤、烘干得n-苯乙酰-l-草铵膦酸34.1g,含量99.1%,收率45.2%。
33.对比例2一种酶拆分法制备l-草铵膦的工艺,包括以下步骤:n-苯乙酰-l-草铵膦酸的制备:取dl-草铵膦104g(95%,0.5mol)、苯乙酸甲酯75g(0.5mol)加入1l四口瓶,加入水350g、仲辛醇70g,十二烷基磺酸钠1g搅拌,用氢氧化钠调ph至8,加入固定化青霉素酰化酶2g(200iu/g),温度20℃反应,反应时间20h,反应过程滴加2%的氢氧化钠溶液控制反应液维持ph8。反应完成后过滤出酶,滤液加入312g甲苯萃取,取水相加入盐酸调ph至2.5搅拌结晶、过滤过滤、烘干得n-苯乙酰-l-草铵膦酸4.5g,含量99.0%,收率6%。
34.上述实施例和对照例所用的反应原料及酶均为同一批次。
35.以上所述仅为本发明的较佳实施例而已,并不用以限制本发明,凡在本发明的精神和原则之内所作的任何修改、等同替换或改进等,均应包含在本发明的保护范围之内。
再多了解一些
本文用于企业家、创业者技术爱好者查询,结果仅供参考。