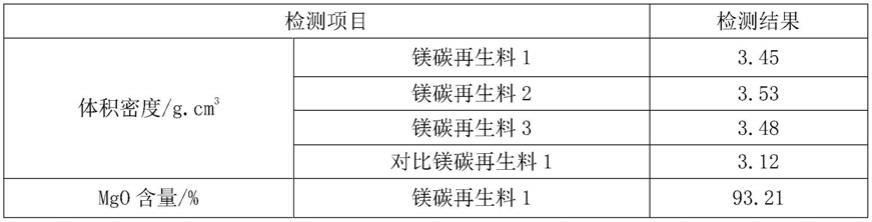
1.本技术涉及耐火材料技术领域,更具体地说,它涉及一种耐火材料及其制备方法。
背景技术:
2.耐火材料是指耐火度不低于1580℃的一类无机非金属材料。耐火度是指耐火材料锥形体试样在没有荷重情况下,抵抗高温作用而不软化熔倒的摄氏温度。镁碳砖是耐火材料中最常用的材料之一,镁碳砖是以高熔点碱性氧化物(氧化镁,熔点2800℃)和难以被炉渣侵润的高熔点碳素材料作为原料,添加各种非氧化物添加剂,用炭质结合剂结合而成的复合耐火材料。镁碳砖具有良好的耐高温性能,抗渣能力强,抗热震性好且高温蠕变低。
3.近年来,耐火原料及其制品的产量的稳步增长,目前国内耐火材料产量约占全球的65%,而与此同时,由于无序开采、加工技术水平,资源综合利用水平较低,浪费较为严重等原因,耐火原料资源已越来越少,节约资源、综合利用资源已是当务之急。据不完全统计,我国每年会产生高达900万吨以上的用后耐火材料,其中多数被当成垃圾废弃,不仅污染环境,又浪费资源,用后耐火材料的回收利用具有重大的意义,尤其是用后镁碳砖,在用后耐火材料中所占比重很大,亟待需要回收利用。
技术实现要素:
4.为了实现废弃镁碳砖的回收利用,本技术提供一种耐火材料及其制备方法。
5.第一方面,本技术提供一种耐火材料,采用如下的技术方案:一种耐火材料,由包含以下重量份的原料制成:骨料77-86份、鳞片状鳞片状石墨10-15份、热固性酚醛树脂3-5份、抗氧化剂1-3份;所述骨料为矾土、电熔镁砂和镁碳再生料,且所述矾土、电熔镁砂和镁碳再生料的重量比为(0.5-1):(1-3):(15-20);所述镁碳再生料由废弃的镁碳砖制得。
6.通过采用上述技术方案,将由废弃的镁碳砖制得镁碳再生料用于制备耐火材料,可减少废弃镁碳砖的丢弃和堆积,减少对环境的污染,与此同时,将废弃的镁碳砖回收利用,可变废为宝,实现资源的循环利用,节约成本。更重要的是,采用本技术的配方,用镁碳再生料制得的耐火材料具有优良的性能,其基本性能可与全新的镁碳砖性能媲美,甚至在某些方面,性能可更好。
7.优选的,所述矾土、电熔镁砂和镁碳再生料的重量比为0.75:1.3:17.7时,制得的耐火材料的综合性能好且此时,所用的镁碳再生料较多,可尽可能地使用再生资源。
8.优选的,所述镁碳再生料由以下制备方法制得:s1、除杂除渣:选择废弃镁碳砖,并去除表面粘附的杂质层和钢渣层;s2、破碎:对除杂除渣后的废弃镁碳砖进行一级破碎,破碎成粒径为≤50mm的颗粒,然后进行二级破碎,得到粒径为≤5mm的颗粒;
s3、磁选:对破碎后的颗粒进行磁选,去除铁杂质;s4、筛分:对磁选后的颗粒进行筛分,得到规格为3-5mm、1-3mm和0-1mm的颗粒;s5、水化处理:筛分后三种不同规格的颗粒分别与水按重量比为10:(0.8-1.1)的比例混合,随后在25-100℃的环境中处理4-8h,烘干,即可得到镁碳再生料。
9.废弃的耐火材料经过破碎后,由于骨料与基质没有完全分离,或发生蚀变而与原砖纯原料颗粒(一次颗粒)的性态产生差异,这种不同于一次颗粒、而与废砖相组合和结构有关、骨料与基质共存的二次颗粒,就是所谓的“假颗粒”,假颗粒会影响耐火材料的基本性能。而按本技术的方法制备镁碳再生料,可极大的减少镁碳再生料中的假颗粒,降低空隙率,从而可提高镁碳再生料的抗腐蚀性能。水化处理可去除材料中的碳化铝(al4c3)等易水化物质,防止材料在使用过程中出现吸潮而开裂。
10.现有废弃镁碳砖的回收利用步骤依次为:分类存放、除渣、水化、烘干、破碎和筛分;而本技术中则依次采用除杂除渣、破碎、磁选、筛分、水化处理和烘干的方式进行。现有的是先水化,后破碎、筛分,而本技术中,则采用先破碎、筛分,再水化,本技术不仅可节约用水(现有的水化处理,废弃镁碳砖与水的重量比约为1:2.7),且能更好的去除碳化铝(al4c3)等易水化物质,且去除效率更高。
11.进一步优选,粒径为3-5mm的颗粒与水按重量比为10:0.8的比例混合,随后加热到25℃,处理4h,烘干;粒径为1-3mm的颗粒与水按重量比为10:0.9的比例混合,随后加热到60℃,处理4h,烘干;粒径为0-1mm的颗粒与水按重量比为10:1.1的比例混合,随后加热到90℃,处理4h,烘干。
12.通过采用上述技术方案,水化处理时可节约能源,节约用水量且能提高水化效率,提高碳化铝(al4c3)等易水化物质的去除率。
13.碳残量大小:粒径为0-1mm的颗粒>粒径为1-3mm的颗粒>粒径为1-3mm的颗粒。
14.优选的,所述镁碳再生料的粒径分布:粒径为3-5mm的颗粒占18%-26%,粒径为1-3mm的颗粒占60%-72%,粒径为0-1mm的颗粒占2%-14%。
15.镁碳再生料按上述粒径分布,可改善耐火材料的体积密度,降低显气孔率,增强常温抗压强度和提高高温抗折强度。
16.优选的,所述镁碳再生料的体积密度为3.45-3.53g/cm3。最优选为3.53g/cm3。
17.镁碳再生料的体积密度为3.45-3.53g/cm3,此时,再生料含假颗粒数量少,可改善再生耐火材料的性能。体积密度越大,假颗粒含量越少。
18.优选的,所述镁碳再生料中,mgo含量≥88.31%,c含量≤6.1%。最优的,mgo含量为93.21%,c含量为3.11。
19.mgo含量越高且c碳含越低,再生料所含的假颗粒越少。
20.优选的,所述抗氧化剂为硅粉和α-al2o3微粉,所述硅粉和α-al2o3微粉的用量比为(1-3):(7-11)。
21.体系中加入硅粉和α-al2o3微粉,可提高耐火材料的抗氧化性能,能防止耐火材料出现龟裂或膨胀现象。此外,还能增强耐火材料的常压抗压强度和高温抗折强度。
22.优选的,所述电熔镁砂选择多级配料:0.5mm以下,0.5-1mm,1-2mm,2-3mm和3-5mm;且0.5mm以下的颗粒占10-15%,0.5-1mm的颗粒占2-7%,1-2mm的颗粒占15-25%,2-3mm的
颗粒占40-55%,3-5mm的颗粒占20-35%。
23.电熔镁砂按上述粒径分布,可改善耐火材料的体积密度,降低显气孔率,增强常温抗压强度和提高高温抗折强度。
24.优选的,所述热固性酚醛树脂的黏度为1.2-1.6pa.s,固含量为68%-77%,残碳量为43%-48.3%。进一步优选,所述热固性酚醛树脂的黏度为1.43-1.6pa.s,固含量为72%-77%,残碳量为44.4%-46.8%。
25.第二方面,本技术提供一种耐火材料的制备方法,采用如下的技术方案:一种耐火材料的制备方法,包括如下步骤:将矾土、电熔镁砂和镁碳再生料混合均匀,得到骨料,随后向骨料中加入热固性酚醛树脂,搅拌均匀,再加入鳞片状石墨和抗氧化剂,搅拌均匀,得到泥料,将泥料放置20-40h后压制成型,然后在200-1400℃下烧制,即可制得镁碳砖。
26.优选的,在200-160℃下烧制时,采用分段烧制,分段温度为200
±
5℃、600℃
±
5℃、800℃
±
5℃、1200℃
±
5℃和1400℃
±
5℃。
27.通过采用上述技术方案,按照本技术的制备方法制备耐火材料,可制得性能优异的耐火材料,即镁碳砖。本技术的制备方法简单,易于实施,易于工业化生产。
28.综上所述,本技术具有以下有益效果:1、由废弃的镁碳砖制得镁碳再生料用于制备耐火材料,可减少废弃镁碳砖的丢弃和堆积,减少对环境的污染,实现资源的循环利用,节约成本,与此同时,不会损害耐火材料的基本性能;2、采用本技术的配方,用镁碳再生料制得的耐火材料具有优良的性能,其基本性能可与全新的镁碳砖性能媲美,甚至在某些方面,性能更好;3、按本技术的方法制备镁碳再生料,可极大的减少镁碳再生料中的假颗粒,同时,能极大的节约用水且能更好的去除碳化铝(al4c3)等易水化物质,且去除效率更高。
具体实施方式
29.以下结合实施例对本技术作进一步详细说明。予以特别说明的是:以下实施例中未注明具体条件者,按照常规条件或制造商建议的条件进行;以下实施例中所用原料除特殊说明外均可来源于普通市售。
30.实施例中,热固性酚醛树脂的黏度为1.43pa.s,固含量为72%,残碳量为44.4%。
31.镁碳再生料的制备例制备例1一种镁碳再生料的制备方法如下:s1、除杂除渣:选择废弃镁碳砖,并去除表面粘附的杂质层和钢渣层;s2、破碎:对除杂除渣后的废弃镁碳砖进行一级破碎,破碎成粒径为≤50mm的颗粒,然后进行二级破碎,得到粒径为≤5mm的颗粒;s3、磁选:对二级破碎后的颗粒进行磁选,去除铁杂质;s4、筛分:对磁选后的颗粒进行筛分,得到规格为3-5mm、1-3mm和0-1mm的颗粒;s5、水化处理:将筛分后的三种不同规格的颗粒分别与水按重量比为10:1的比例混合,随后在40℃的环境中处理6h,烘干,即可得到镁碳再生料1。
32.制备例2一种镁碳再生料的制备方法如下:s1、除杂除渣:选择废弃镁碳砖,并去除表面粘附的杂质层和钢渣层;s2、破碎:对除杂除渣后的废弃镁碳砖进行一级破碎,破碎成粒径为≤50mm的颗粒,然后进行二级破碎,得到粒径为≤5mm的颗粒;s3、磁选:对二级破碎后的颗粒进行磁选,去除铁杂质;s4、筛分:对磁选后的颗粒进行筛分,得到规格为3-5mm、1-3mm和0-1mm的颗粒;s5、水化处理:粒径为3-5mm的颗粒与水按重量比为10:0.8的比例混合,随后加热到25℃,处理4h,烘干;粒径为1-3mm的颗粒与水按重量比为10:0.9的比例混合,随后加热到60℃,处理4h,烘干;粒径为0-1mm的颗粒与水按重量比为10:1.1的比例混合,随后加热到90℃,处理4h,烘干;水化处理后,即可制得镁碳再生料2。
33.制备例3一种镁碳再生料的制备方法如下:s1、除杂除渣:选择废弃镁碳砖,并去除表面粘附的杂质层和钢渣层;s2、破碎:对除杂除渣后的废弃镁碳砖进行一级破碎,破碎成粒径为≤50mm的颗粒,然后进行二级破碎,得到粒径为≤5mm的颗粒;s3、磁选:对二级破碎后的颗粒进行磁选,去除铁杂质;s4、筛分:对磁选后的颗粒进行筛分,得到规格为3-5mm、1-3mm和0-1mm的颗粒;s5、水化处理:粒径为3-5mm的颗粒与水按重量比为10:1.1的比例混合,随后加热到100℃,处理4h,烘干;粒径为1-3mm的颗粒与水按重量比为10:0.8的比例混合,随后加热到20℃,处理4h,烘干;粒径为0-1mm的颗粒与水按重量比为10:0.9的比例混合,随后加热到40℃,处理4h,烘干;水化处理后,即可制得镁碳再生料3。
34.对比制备例1一种镁碳再生料的制备方法如下:s1、除杂除渣:选择废弃镁碳砖,并去除表面粘附的杂质层和钢渣层;s4、水化处理:将除杂除渣的废弃镁碳砖与水按重量比为10:27的比例混合,随后加热到60℃,处理4h,烘干;s2、破碎:对水化处理后的废弃镁碳砖进行一级破碎,破碎成粒径为≤50mm的颗粒,然后进行二级破碎,得到粒径为≤5mm的颗粒;s3、磁选:对二级破碎后的颗粒进行磁选,去除铁杂质;s5、筛分:对磁选后的颗粒进行筛分,得到规格为3-5mm、1-3mm和0-1mm的颗粒;即可制得对比镁碳再生料1。
35.对不同镁碳再生料进行质量检测,检测结果具体如下表1所示。
36.表1
实施例
37.实施例1将2.3kg矾土、4.6kg电熔镁砂和70.1kg镁碳再生料1混合均匀,得到骨料,随后向骨料中加入5kg热固性酚醛树脂,搅拌均匀,再加入15kg鳞片状石墨和3kg硅粉,搅拌均匀,得到泥料,将泥料放置24h后压制成型,然后依次在200℃、600℃、1400℃下烧制,即可制得镁碳砖。
38.本实施例中,4.6kg电熔镁砂由1.15kg 0-1mm颗粒、2.5kg 1-3mm颗粒和0.92kg 3-5mm颗粒混合而成;70.1kg镁碳再生料1由制备例1中的23.36kg 0-1mm颗粒、23.37kg 1-3mm颗粒和23.37kg 3-5mm颗粒混合而成。
39.实施例2将2.6kg矾土、5.2kg电熔镁砂和78kg镁碳再生料1混合均匀,得到骨料,随后向骨料中加入3.2kg热固性酚醛树脂,搅拌均匀,再加入10kg鳞片状石墨和1kg硅粉,搅拌均匀,得到泥料,将泥料放置24h后压制成型,然后依次在200℃、600℃、1400℃下烧制,即可制得镁碳砖。
40.本实施例中,5.2kg电熔镁砂由1.3kg 0-1mm颗粒、2.86kg 1-3mm颗粒和1.04kg 3-5mm颗粒混合而成;78kg镁碳再生料1由制备例1中的26kg 0-1mm颗粒、26kg 1-3mm颗粒和26kg 3-5mm颗粒混合而成。
41.实施例3将2.5kg矾土、5kg电熔镁砂和75kg镁碳再生料1混合均匀,得到骨料,随后向骨料中加入3.5kg热固性酚醛树脂,搅拌均匀,再加入11.3kg鳞片状石墨和2.7kg硅粉,搅拌均匀,得到泥料,将泥料放置24h后压制成型,然后依次在200℃、600℃、1400℃下烧制,即可制得镁碳砖。
42.本实施例中,5kg电熔镁砂由1.25kg 0-1mm颗粒、2.75kg 1-3mm颗粒和1kg 3-5mm颗粒混合而成;
75kg镁碳再生料1由制备例1中的25kg 0-1mm颗粒、25kg 1-3mm颗粒和25kg 3-5mm颗粒混合而成。
43.实施例4将3.11kg矾土、5.4kg电熔镁砂和73.45kg镁碳再生料1混合均匀,得到骨料,随后向骨料中加入4kg热固性酚醛树脂,搅拌均匀,再加入11.3kg鳞片状石墨和2.7kg硅粉,搅拌均匀,得到泥料,将泥料放置24h后压制成型,然后依次在200℃、600℃、800℃、1200℃、1400℃下烧制,即可制得镁碳砖。
44.本实施例中,5.4kg电熔镁砂由1.35kg 0-1mm颗粒、2.97kg 1-3mm颗粒和1.08kg 3-5mm颗粒混合而成;73.45kg镁碳再生料1由制备例1中的24.48kg 0-1mm颗粒、24.48kg 1-3mm颗粒和24.49kg 3-5mm颗粒混合而成。
45.实施例5将3.42kg矾土、10.26kg电熔镁砂和68.4kg镁碳再生料1混合均匀,得到骨料,随后向骨料中加入4kg热固性酚醛树脂,搅拌均匀,再加入11.3kg鳞片状石墨和2.7kg硅粉,搅拌均匀,得到泥料,将泥料放置24h后压制成型,然后依次在200℃、600℃、800℃、1200℃、1400℃下烧制,即可制得镁碳砖。
46.本实施例中,10.26kg电熔镁砂由2.57kg 0-1mm颗粒、5.64kg 1-3mm颗粒和2.05kg 3-5mm颗粒混合而成;68.4kg镁碳再生料1由制备例1中的22.8kg 0-1mm颗粒、22.8kg 1-3mm颗粒和22.8kg 3-5mm颗粒混合而成。
47.实施例6实施例6与实施例4的区别仅在于:实施例6中,用制备例2中制得的镁碳再生料2代替镁碳再生料1,其余均与实施例4保持一致。
48.实施例7实施例7与实施例4的区别仅在于:实施例7中,用制备例3中制得的镁碳再生料3代替镁碳再生料1,其余均与实施例4保持一致。
49.实施例8-9实施例8-9与实施例6的区别仅在于:实施例8-9中镁碳再生料2的粒径分布不同,具体如下表2所示。
50.表2镁碳再生料2的粒径实施例6/kg实施例8/kg实施例9/kg3-5mm24.4819.113.221-3mm24.4844.0752.880-1mm24.4910.287.35实施例10-12实施例10-12与实施例9的区别仅在于:实施例10-12中电熔镁砂的粒径分布不同,具体如下表3所示。
51.表3电熔镁砂的粒径实施例10实施例11实施例12
0.5mm以下0.540.811.080.5-1mm0.270.271.081-2mm1.080.811.082-3mm2.162.161.083-5mm1.351.351.08实施例13-15实施例13-15与实施例10的区别仅在于:实施例13-15中抗氧化剂不同,具体如下表4所示。
52.表4抗氧化剂实施例13实施例14实施例15硅粉0.620.331.35α-al2o3微粉2.082.371.35对比例对比例1对比例1与实施例4的区别仅在于:对比例1中,用对比制备例1中制得的对比镁碳再生料1代替镁碳再生料1,其余均与实施例4保持一致。
53.对比例2对比例2与与实施例14的区别仅在于:对比例2不添加矾土和镁碳再生料,即骨料为82kg电熔镁砂,其余均与实施例14保持一致。
54.性能检测试验检测实施例1-15和对比例1-2所制得的耐火材料(镁碳砖)的基本性能,具体检测结果如下表5所示。
55.根据标准gb/t2998—1982测定试样的显气孔率;根据标准gb/t2997—1985测定试样的体积密度;根据标准gb/t 5072—1985测定试样的常温耐压强度;根据标准gb/t13243-91测定试样的高温抗折强。
56.表5
试样常温耐压强度/mpa高温抗折强/mpa体积密度/g.cm3显气孔率/%实施例155.210.5 3.011.9实施例255.310.2 3.001.8实施例357.510.9 3.011.9实施例458.711.4 3.011.9实施例558.211.2 3.021.9实施例660.112.6 3.011.9实施例759.512.1 3.001.8实施例861.312.9 3.081.4实施例962.513.2 3.061.3实施例1063.413.8 3.121.2实施例1164.113.5 3.181.3
实施例1263.112.9 3.101.4实施例1365.114.5 3.181.2实施例1465.614.3 3.181.2实施例1563.513.6 3.181.2对比例144.78.92 2.692.8对比例262.312.2 3.151.5
结合实施例3-5和对比例2并结合表5可以看出,耐火材料中骨料对耐火材料性能的影响较大,当骨料由矾土、电熔镁砂和镁碳再生料按重量比为(0.5-1):(1-3):(15-20)的比例混合时,可改善耐火材料的性能。
57.结合实施例4、6-7和对比例1并结合表5可以看出,镁碳再生料的制备方法对耐火材料性能的影响比较大,按本技术的方法制备镁碳再生料,有利于改善耐火材料的性能,尤其有利于提高耐火材料的常温耐压强度和高温抗折强度。
58.结合实施例6、8-9和实施例10-12并结合表5可以看出,镁碳再生料的粒径和电熔镁砂的粒径分布会均会影响耐火材料性能,两者按本技术的粒级级配配置,有利于改善耐火材料的性能,尤其有利于改善耐火材料的体积密度和显气孔率。
59.结合实施例12、13-15并结合表5可以看出,由重量比为(1-3):(7-11)的硅粉和α-al2o3微粉配置而成的抗氧化剂有利于改善耐火材料的性能。
60.本具体实施例仅仅是对本技术的解释,其并不是对本技术的限制,本领域技术人员在阅读完本说明书后可以根据需要对本实施例做出没有创造性贡献的修改,但只要在本技术的权利要求范围内都受到专利法的保护。
再多了解一些
本文用于企业家、创业者技术爱好者查询,结果仅供参考。