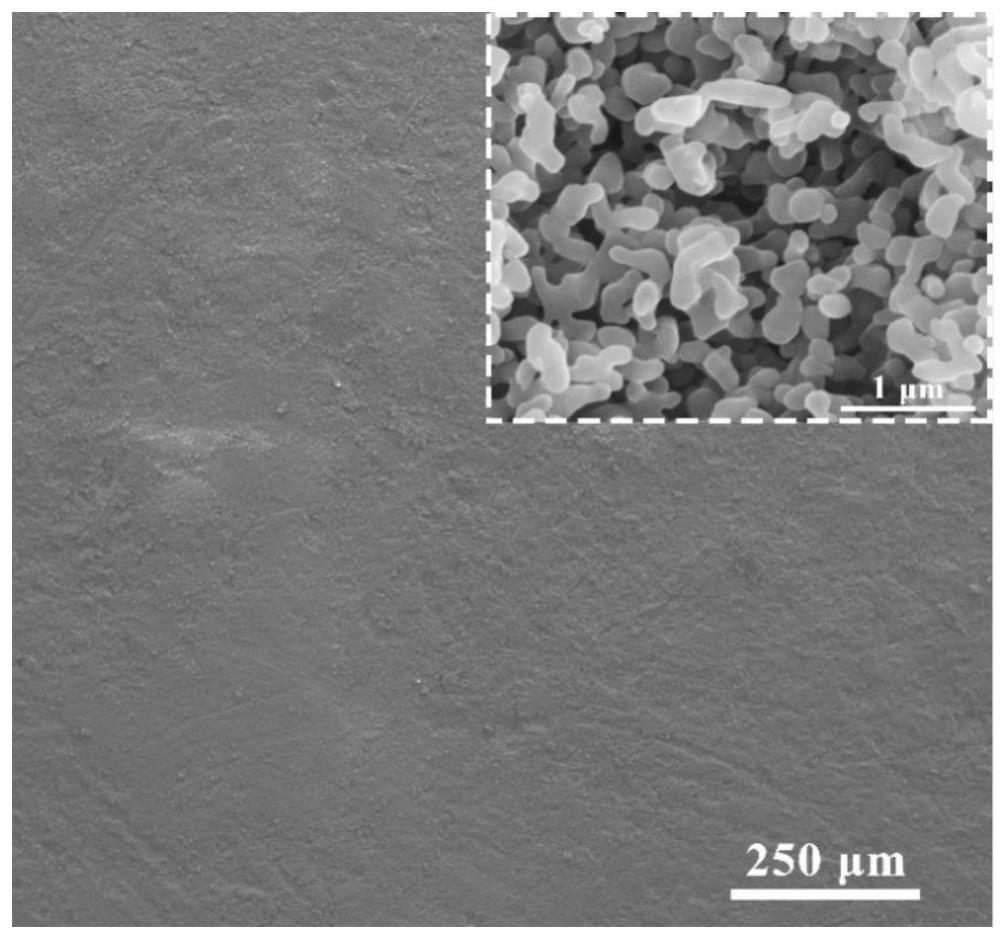
1.本发明属于陶瓷膜技术领域,涉及一种非对称陶瓷过滤膜及其制备方法,特别涉及一种高性能非对称陶瓷过滤膜及其制备方法。
背景技术:
2.就分离过程而言,膜通常被描述为一个分离两相的屏障,它可以选择性的传输物质。膜分为有机膜和无机膜,无机膜又包括金属膜、碳基膜和陶瓷膜。与有机膜、金属膜和碳基膜相比,陶瓷膜具有机械强度高、热稳定性和化学稳定性好、孔径分布可控、膜结垢率低、清洁效率高、再生性好和运营成本低等优势。基于这些优势,近年来陶瓷膜引起了人们极大的关注,被广泛用于污水处理和海水淡化、气体分离、烟气过滤、生物医药、纸浆和造纸、食品和饮料加工、(微生物)燃料电池和催化剂载体等领域。然而,工业上使用较多的仍然是有机膜,这是因为有机膜的制备和安装技术成熟,成本相对较低,而陶瓷膜因原料较贵和生产工艺复杂导致生产成本相对较高,且陶瓷膜的高渗透性和高选择性不统一。为了降低陶瓷膜的成本,改善陶瓷膜的性能,当前采用的方法主要有:使用廉价原料,添加烧成助剂和优化制膜工艺。但是,廉价的原料如高岭土、黏土和蒙脱土等会引入杂质,使陶瓷膜的性能降低;以廉价原料或者氧化物(例如tio2、cuo)做烧成助剂虽然能降低烧成温度,但陶瓷膜体系的耐腐蚀性相对变差,渗透性、强度也受到影响。相对来讲,优化制膜工艺更加可行。
3.传统的制备陶瓷膜的方法主要有溅射法、气相沉积法、喷涂法、浸渍法、相转化法和干压法等。其中,溅射法和气相沉积法设备昂贵、能耗高,对原料和操作条件要求高,需要预烧制支撑体;喷涂法操作简单,但需要配制合适的涂膜液和预烧制支撑体;浸渍法工艺简单,但成膜颗粒很容易渗入支撑体中而降低膜体系的渗透性能,且需要进行反复“涂覆-干燥-烧制”的复杂操作,同时也需要配制涂膜液和预烧制支撑体;相转化法在浸渍法的基础上增加了相转化操作;干压法工艺简单,但通常用来制备对称陶瓷膜(传统意义上的多孔陶瓷)。由此可见,采用传统的方法制备的陶瓷膜成本相对较高,膜的性能也会受到影响,且烧制时涂膜液中大量有机物的排放会污染环境。
4.近年来,在浸渍法的基础上进行优化的制膜工艺主要有粘度调控法(秦伍.氧化铝陶瓷微滤膜的一步法制备技术[d].广州:华南理工大学,2016.)、预封孔法(qin w.,et al.preparation of high-permeance ceramic microfiltration membranes using a pore-sealing method[j].rsc advances,2020,10(10):5560-5565.)和牺牲夹层法(cho y.h.,et al.sacrificial graphene oxide interlayer for highly permeable ceramic thin film composite membranes[j].journal of membrane science,2021,618:118442.),此类方法提高了陶瓷膜的渗透性能,但同时也需要制备额外的有机膜层,且仍然需要预烧制支撑体和配制涂膜液。在流延法的基础上发展起来的制膜工艺有膜转印法(cn112044285a),此方法在一定程度上提高了陶瓷膜的渗透性能降低了生产成本,但仍然需要配制涂膜液且需要预烧制支撑体。
技术实现要素:
[0005]
为了克服现有技术的缺点和不足,本发明的目的在于提供一种高性能非对称陶瓷膜的快速、简便和低成本制备方法。通过本发明方法所获得的陶瓷膜具有结构和性能易控、渗透通量和截留率高、抗污性能优越等特点。
[0006]
本发明将筛网技术和有机膜技术巧妙结合,通过一步共压共烧成制备膜层薄(厚度可达20μm)且无缺陷的陶瓷膜。此外,复合分散剂的使用不仅可以改善用于制备支撑体的铝硅混合料浆的流动性和分散性,还可以提高生坯强度和烧成后陶瓷膜的强度;而硅溶胶的引入不仅可以降低陶瓷膜的烧成温度,提高陶瓷膜强度,还可以保证膜层与支撑体间收缩率的匹配,避免共烧时因膜层与支撑体间收缩不匹配而出现膜开裂和强度降低等问题。同时,通过烧成温度、支撑体中铝硅比(al2o3/sio2质量比)及造孔剂添加量的调节,能够制备出结构和性能可控的高性能非对称陶瓷膜,且制备的陶瓷膜渗透通量和截留率均高,抗污性能优越,膜层与支撑体间结合强度高。
[0007]
本发明的目的通过以下技术方案实现:
[0008]
一种高性能非对称陶瓷过滤膜的共压共烧制备方法,包括以下步骤:
[0009]
(1)将al2o3微粉、硅溶胶、水和复合分散剂混合均匀制成料浆,料浆经烘干后研磨过筛得到不同铝硅比(al2o3/sio2质量比)的混合粉体;向混合粉体中加入聚乙烯醇溶液和造孔剂,造粒后倒入模具再干压成型,随后将模具倒立并取下底座,将与底座接触的支撑体生坯面朝上进行半脱模(即脱模时生坯面不露出模具);
[0010]
(2)将al2o3细粉加入到去离子水中,边搅拌边加入分散剂,搅拌一定时间(1-3h)后将悬浮液烘干、研磨并过筛,得到分散均匀的al2o3细粉;
[0011]
(3)向步骤(1)中半脱模的生坯表面喷洒一层聚乙烯醇溶液,然后在模具上放上筛网。取步骤(2)中分散均匀的一定量的al2o3细粉倒入筛网且正对生坯面,采取一定的措施使细粉落下并均匀铺展在生坯表面,而后在铺展的细粉上面放一片光滑有机膜,再在有机膜上放置底座,经共压成型后脱模得到一体化的支撑体生坯 生膜层(陶瓷膜生膜)。支撑体生坯和生膜层经干燥后在1000-1500℃条件下共烧0.5-4h即制得陶瓷膜。
[0012]
进一步地,步骤(1)中所述al2o3微粉的平均粒径为5-30μm,硅溶胶中sio2粒子的平均粒径为10-30nm,所述al2o3、硅溶胶中sio2、水的重量比为(8-10):(0-2):(10-30)。
[0013]
进一步地,步骤(1)中所述复合分散剂是指三聚磷酸钠-羟基改性丙烯酸,三聚磷酸钠与羟基改性丙烯酸的重量比为(3-7):(7-3),两者加入量占混合粉体的重量比为0.5-2%。
[0014]
进一步地,步骤(1)中所述粘结剂聚乙烯醇溶液的质量分数为2-12%,其加入量占铝硅混合粉体总重量的比例为0.2-2%;所述造孔剂为玉米淀粉或煤粉中的一种或多种,其加入量占铝硅混合粉体总重量的比例为0-30%;
[0015]
进一步地,步骤(1)中所述支撑体生坯成型压力为10-100mpa。
[0016]
进一步地,步骤(2)和步骤(3)中所述al2o3细粉的平均粒径为100-600nm。
[0017]
进一步地,步骤(2)中所述分散剂为六偏磷酸钠、聚丙烯酸、改性丙烯酸或聚乙二醇中的一种,其加入量占氧化铝细粉重量的比例为0.1-2%。
[0018]
进一步地,步骤(2)中所述筛网的目数为80-200目。
[0019]
进一步地,步骤(3)中所述聚乙烯醇溶液的质量分数为1-8%,所述一定量的细粉
其用量根据支撑体生坯的上表面面积而定,在0.004-0.020g/cm2之间。
[0020]
进一步地,步骤(3)中所述筛网的目数为80-200目,所述采取一定的措施是指采取震动、旋转或者往返移动筛网措施中的一种或几种方式使细粉落下并均匀铺展在生坯表面。
[0021]
进一步地,步骤(3)中所述光滑有机膜为聚四氟乙烯膜、硫酸纸或糯米纸中的一种。
[0022]
进一步地,步骤(3)中所述共压成型压力为10-100mpa。
[0023]
进一步地,步骤(3)中所述陶瓷膜生膜在常温下干燥的时间为0-2h,在烘箱中干燥的时间为0-2h,干燥温度为60-100℃。
[0024]
本发明中,所述高性能非对称陶瓷膜通过上述方法制备得到。
[0025]
本发明制备的非对称陶瓷膜的膜层厚度为20-80μm,平均孔径为85-106nm,纯水渗透通量为988-3830lm-2
h-1
bar-1
,过滤2-30min对油滴平均尺寸为200nm的水包油乳液的截留率可达100%。
[0026]
本发明的陶瓷膜可广泛应用于污水处理和海水淡化、气体分离、烟气过滤、生物医药、纸浆和造纸、食品和饮料加工、(微生物)燃料电池和催化剂载体等领域。
[0027]
与现有技术的陶瓷膜或其制备方法相比,本发明具有以下优点及有益效果:
[0028]
1.本发明将筛网技术和有机膜技术巧妙结合,使得采用基于干压法的共压法制备薄(厚度可达20μm)且无缺陷的膜层得以实现。
[0029]
2.本发明中三聚磷酸钠-羟基改性丙烯酸复合分散剂的使用不仅可以改善用于制备支撑体的铝硅混合料浆的流动性和分散稳定性,还可以提高生坯强度和烧成后陶瓷膜的强度;此外,引入的硅溶胶可以与氧化铝混合更均匀,硅溶胶不仅充当了原料、粘结剂,还充当了烧结助剂,降低了陶瓷膜的烧成温度。
[0030]
3.本发明中通过对烧成温度、支撑体中al2o3/sio2比和造孔剂添加量的调整,使得所制备的陶瓷膜的结构(厚度、孔参数等)和性能(渗透性和选择性等)可控。
[0031]
4.本发明只需对支撑体生坯和膜层粉体进行一步共压再共烧(共压共烧成法)便可得到高性能陶瓷膜,无需预烧支撑体和配制涂膜液,且所需干燥时间短。这大大简化了制膜工艺,缩短了制膜时间,降低了成本和能耗,且制备方法具有可重复性,更加经济环保,可推广性和应用前景较好。
[0032]
5.本发明所制备的非对称陶瓷膜膜层较薄且可有效避免膜层颗粒渗入支撑体,兼备高渗透性和高选择性、成本低、抗污性好。
附图说明
[0033]
图1为实施例3的高性能陶瓷膜的表面及表面放大图;
[0034]
图2为实施例3的高性能陶瓷膜的断面及断面放大图;
[0035]
图3为实施例3的高性能陶瓷膜的孔径分布图;
[0036]
图4为实施例3的高性能陶瓷膜对水包油乳液的截留率随时间的变化;
[0037]
图5为实施例3的高性能陶瓷膜的通量恢复率。
具体实施方式
[0038]
下面结合实施例及附图,对本发明作进一步地详细说明,但本发明的实施方式不限于此。
[0039]
实施例1
[0040]
一种高性能非对称陶瓷膜的共压共烧成制备方法,包括以下步骤:
[0041]
将1g平均粒径为100nm的al2o3细粉加入到50g去离子水中,边搅拌边加入占细粉总量0.5%的六偏磷酸钠,混合均匀后将悬浮液烘干,研磨并过200目筛,处理好的细粉备用。
[0042]
边搅拌边缓慢向去离子水中加入平均粒径为30μm的al2o3微粉和sio2粒子平均粒径为10nm的硅溶胶,三者的重量比为al2o3:sio2:水=8:2:10。然后依次加入占混合粉体总量分别为0.15%的三聚磷酸钠和0.35%的羟基改性丙烯酸复合分散剂,剧烈搅拌1h后放入烘箱,干燥后研磨过筛得到混合粉体。取3g混合粉体,加入占混合粉体总量0.5%的聚乙烯醇溶液(质量分数8%)和10%的煤粉,经造粒后倒入模具,并在100mpa压力下干压成型,之后将模具倒立取下底座,将与底座接触的支撑体生坯面朝上进行半脱模。
[0043]
向半脱模后的生坯表面喷洒一层质量分数为8%的pva溶液,然后在模具上放上200目筛网。取一定量(以每平方厘米生坯表面覆盖0.02g为准)的细粉倒入筛网且正对生坯面中心,逆时针旋转和往返移动筛网使细粉落下并均匀铺展在生坯表面,而后在铺展的细粉上面放一片光滑的硫酸纸,并放置底座,在100mpa压力下共压成型后脱模得到陶瓷膜生膜。将陶瓷膜生膜在60℃烘箱中干燥2h经烧制得到陶瓷膜成品,其中,共烧成温度为1300℃,保温时间为2h。制备的非对称陶瓷膜的膜层厚度为80μm,孔隙率为48%,平均孔径为95nm,渗透通量为988lm-2
h-1
bar-1
,过滤20min对油滴平均尺寸为200nm的水包油乳液的截留率达100%。
[0044]
实施例2
[0045]
一种高性能非对称陶瓷膜的共压共烧成制备方法,包括以下步骤:
[0046]
将1g平均粒径为600nm的al2o3细粉加入到50g去离子水中,边搅拌边加入占细粉总量0.1%的聚丙烯酸,混合均匀后将悬浮液烘干,研磨并过80目筛,处理好的细粉备用。
[0047]
边搅拌边缓慢向去离子水中加入平均粒径为10μm的al2o3微粉和sio2粒子平均粒径为30nm的硅溶胶,三者的重量比为al2o3:sio2:水=8:2:15,然后依次加入占混合粉体总量分别为1%的三聚磷酸钠和1%的羟基改性丙烯酸复合分散剂,剧烈搅拌3h后放入烘箱,干燥后研磨过筛得到混合粉体。取3g混合粉体,加入占混合粉体总量0.2%的聚乙烯醇溶液(质量分数12%)和20%的玉米淀粉以及10%的煤粉,经造粒后倒入模具,并在40mpa压力下干压成型,之后将模具倒立取下底座,将与底座接触的支撑体生坯面朝上进行半脱模。
[0048]
向半脱模后的生坯表面喷洒一层质量分数为5%的pva溶液,然后在模具上放上80目筛网。取一定量(以每平方厘米生坯表面覆盖0.006g为准)的细粉倒入筛网且正对生坯面中心,逆时针旋转筛网使细粉落下,再轻轻震动模具使细粉均匀铺展在生坯表面,而后在铺展的细粉上面放一片光滑聚四氟乙烯膜,并放置底座,在40mpa压力下共压成型后脱模得到陶瓷膜生膜。将生膜在80℃烘箱中干燥1h经烧制得到陶瓷膜成品,其中,共烧成温度为1200℃,保温时间为4h。制备的非对称陶瓷膜的膜层厚度为27μm,孔隙率为57%,平均孔径为94nm,渗透通量为3830lm-2
h-1
bar-1
,过滤10min对油滴平均尺寸为200nm的水包油乳液的截留率达100%。
[0049]
实施例3
[0050]
一种高性能非对称陶瓷膜的共压共烧成制备方法,包括以下步骤:
[0051]
将1g平均粒径为300nm的al2o3细粉加入到50g去离子水中,边搅拌边加入占细粉总量0.5%的改性丙烯酸,混合均匀后将悬浮液烘干,研磨并过100目筛,处理好的细粉备用。
[0052]
边搅拌边缓慢向去离子水中加入平均粒径为10μm的al2o3微粉和sio2粒子平均粒径为15nm的硅溶胶,三者的重量比为al2o3:sio2:水=8.7:1.3:15,然后依次加入占混合粉体总量分别为0.7%的三聚磷酸钠和0.3%的羟基改性丙烯酸复合分散剂,剧烈搅拌2hmin后放入烘箱,干燥后研磨过筛得到混合粉体。取3g混合粉体,加入占混合粉体总量0.5%的聚乙烯醇溶液(质量分数5%)和20%的玉米淀粉,经造粒后倒入模具,并在60mpa压力下干压成型,之后将模具倒立取下底座,将与底座接触的支撑体生坯面朝上进行半脱模。
[0053]
向半脱模后的生坯表面喷洒一层质量分数为3%的pva溶液,然后在模具上放上100目筛网。取一定量(以每平方厘米生坯表面覆盖0.008g为准)的细粉倒入筛网且正对生坯面中心,逆时针旋转使细粉落下,再轻轻震动模具使细粉均匀铺展在生坯表面,而后在铺展的细粉上面放一片光滑聚四氟乙烯膜,并放置底座,在30mpa压力下共压成型后脱模得到陶瓷膜生膜。将陶瓷膜生膜在80℃烘箱中干燥0.5h经烧制得到陶瓷膜成品,其中,共烧成温度为1200℃,保温时间为2h。制备的非对称陶瓷膜的膜层厚度为30μm,孔隙率为53%,平均孔径为85nm,纯水渗透通量为3680lm-2
h-1
bar-1
,过滤5min对油滴平均尺寸为200nm的水包油乳液的截留率达100%。图1为该高性能陶瓷膜的表面及表面放大图,可见膜的表面无缺陷;图2为该高性能陶瓷膜的断面及断面放大图,可以看出膜层与支撑体层间的结合情况很好,且无成膜颗粒渗入支撑体,从而保证陶瓷膜具有较高的渗透通量;图3为该高性能陶瓷膜的孔径分布图,可以看出膜的孔径分布较窄,从而保证陶瓷膜具有较高的截留率;图4为该高性能陶瓷膜对水包油乳液的截留率随时间的变化;图5为该高性能陶瓷膜的通量恢复率。图4和图5表明陶瓷膜具有较高的渗透通量和截留率。
[0054]
实施例4
[0055]
一种高性能非对称陶瓷膜的共压共烧成制备方法,包括以下步骤:
[0056]
将1g平均粒径为300nm的al2o3细粉加入到50g去离子水中,边搅拌边加入占细粉总量2%的聚乙二醇,混合均匀后将悬浮液烘干,研磨并过100目筛,处理好的细粉备用。
[0057]
将平均粒径为10μm的al2o3微粉和sio2粒子平均粒径为15nm的硅溶胶缓慢加入到去离子水中,边搅拌边加入,三者的重量比为al2o3:sio2:水=9.4:0.6:15,然后依次加入占混合粉体总量分别为0.25%的三聚磷酸钠和0.25%的羟基改性丙烯酸复合分散剂,剧烈搅拌120min后放入烘箱,干燥后研磨过筛得到混合粉体。取3g混合粉体,加入占混合粉体总量0.5%的聚乙烯醇溶液(质量分数5%)和3%的玉米淀粉以及3%的煤粉,经造粒后倒入模具,并在40mpa压力下干压成型,之后将模具倒立取下底座,将与底座接触的支撑体生坯面朝上进行半脱模。
[0058]
向半脱模后的生坯表面喷洒一层质量分数为3%的pva溶液,然后在模具上放上100目筛网,取一定量(以每平方厘米生坯表面覆盖0.008g为准)的细粉倒入筛网且正对生坯面中心,逆时针旋转使细粉落下,再轻轻震动模具使细粉均匀铺展在生坯表面,而后在铺展的细粉上面放一片光滑聚四氟乙烯膜,并放置底座,在30mpa压力下共压成型后脱模得到陶瓷膜生膜。将陶瓷膜生膜在80℃烘箱中干燥0.5h经共烧得到陶瓷膜成品,其中,共烧成温
度为1300℃,保温时间为2h。制备的非对称陶瓷膜的膜层厚度为29μm,孔隙率为48%,平均孔径为106nm,渗透通量为2350lm-2
h-1
bar-1
,过滤30min对油滴平均尺寸为200nm的水包油乳液的截留率达100%。
[0059]
实施例5
[0060]
一种高性能非对称陶瓷膜的共压共烧成制备方法,包括以下步骤:
[0061]
将1g平均粒径为200nm的al2o3细粉加入到50g去离子水中,边搅拌边加入占细粉总量0.1%的聚丙烯酸,混合均匀后将悬浮液烘干,研磨并过200目筛,处理好的细粉备用。
[0062]
边搅拌边向去离子水中缓慢加入平均粒径为5μm的al2o3微粉和sio2粒子平均粒径为10nm的硅溶胶,三者的重量比为al2o3:sio2:水=9.4:0.6:30,然后依次加入占混合粉体总量分别为0.3%的三聚磷酸钠和0.2%的羟基改性丙烯酸复合分散剂,剧烈搅拌2h后放入烘箱,干燥后研磨过筛得到混合粉体。取3g混合粉体,加入占混合粉体总量0.5%的聚乙烯醇溶液(质量分数5%)和5%的玉米淀粉,经造粒后倒入模具,并在10mpa压力下干压成型,之后将模具倒立取下底座,将与底座接触的支撑体生坯面朝上进行半脱模。
[0063]
向半脱模后的生坯表面喷洒一层质量分数为1%的pva溶液,然后在模具上放上100目筛网。取一定量(以每平方厘米生坯表面覆盖0.004g为准)的细粉倒入筛网且正对生坯面中心,逆时针旋转并往返移动筛网使细粉落下,再轻轻震动模具使细粉均匀铺展在生坯表面,而后在铺展的细粉上面放一片光滑的糯米纸,并放置底座,在10mpa压力下共压成型后脱模得到陶瓷膜生膜。将陶瓷膜生膜在常温下干燥2h,再在100℃烘箱中干燥0.5h经烧制得到陶瓷膜成品,其中,共烧成温度为1000℃,保温时间为2h。制备的非对称陶瓷膜的膜层厚度为20μm,孔隙率为45%,平均孔径为93nm,渗透通量为2160lm-2
h-1
bar-1
,过滤20min对油滴平均尺寸为200nm的水包油乳液的截留率达100%。
[0064]
实施例6
[0065]
一种高性能非对称陶瓷膜的共压共烧成制备方法,包括以下步骤:
[0066]
将1g平均粒径为300nm的al2o3细粉加入到50g去离子水中,边搅拌边加入占细粉总量1%的改性丙烯酸,混合均匀后将悬浮液烘干,研磨并过100目筛,处理好的细粉备用。
[0067]
边搅拌边向去离子水中缓慢加入一定量的平均粒径为10μm的al2o3粉,两者的重量比为al2o3:水=10:20,然后依次加入占混合粉体总量分别为0.25%的三聚磷酸钠和0.25%的羟基改性丙烯酸复合分散剂,剧烈搅拌1h后放入烘箱,干燥后研磨过筛得到分散均匀的氧化铝微粉。取3g氧化铝微粉,加入占微粉总量2%的聚乙烯醇溶液(质量分数2%),经造粒后倒入模具,并在40mpa压力下干压成型,之后将模具倒立取下底座,将与底座接触的支撑体生坯面朝上进行半脱模。
[0068]
向半脱模后的生坯表面喷洒一层质量分数为5%的pva溶液,然后在模具上放上80目筛网。取一定量(以每平方厘米生坯表面覆盖0.008g为准)的细粉倒入筛网且正对生坯面中心,逆时针旋转并往返移动筛网使细粉落下,再轻轻震动模具使细粉均匀铺展在生坯表面,而后在铺展的细粉上面放一片光滑的糯米纸,并放置底座,在10mpa压力下共压成型后脱模得到陶瓷膜生膜。将陶瓷膜生膜在80℃烘箱中干燥1h经烧制得到陶瓷膜成品,其中,共烧成温度为1500℃,保温时间为0.5h。制备的非对称陶瓷膜的膜层厚度为39μm,孔隙率为38%,平均孔径为98nm,纯水渗透通量为1260lm-2
h-1
bar-1
,过滤30min对油滴平均尺寸为200nm的水包油乳液的截留率达100%。
[0069]
最后所应当说明的是,以上实施例仅用以说明本发明的技术方案而非对本发明保护范围的限制,尽管参照较佳实施例对本发明作了详细说明,本领域的普通技术人员应当理解,可以对本发明的技术方案进行修改或者等同替换,而不脱离本发明技术方案的实质和范围。
再多了解一些
本文用于企业家、创业者技术爱好者查询,结果仅供参考。