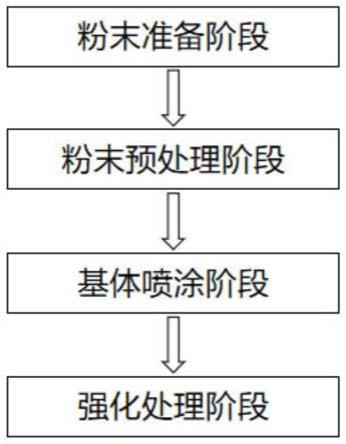
1.本发明属于表面强化技术领域,具体涉及一种抗空蚀复合涂层及其制备方法。
背景技术:
2.水轮机、船舶等过流部件在长期运行后普遍存在空蚀问题,其不但会破坏设施设备,产生振动和噪音,还会降低运行效率,严重影响了设备的使用性能与服役寿命。据不完全统计,我国因空化空蚀造成的经济损失达到数十亿元/年。空蚀现象可以简化为空化和气蚀的两个过程,历经空化泡形成、空化泡长大和剧烈溃灭三个阶段。空化泡溃灭后产生的高速微射流和高压冲击波,对基体材料产生强大的应力冲击效应,此外,由于电化学腐蚀、热力学作用、机械疲劳应力的附加影响,导致过流表面侵蚀损伤程度大大增加。
3.当前抗空蚀表面涂层材料主要包括合金材料、陶瓷材料、有机高分子材料、复合材料等,可采用热喷涂、熔覆涂敷、气相沉积和堆焊等方法制备。但是研究表明,涂层硬质相脆性失效和韧性相疲劳失效是空蚀的主要失效机制。合金涂层价格便宜,但耐腐蚀和抗空蚀性能一般;陶瓷涂层硬度高,抗空蚀性能较高,但易受孔隙率和硬质相脆性失效影响;有机高分子涂层韧性好,但与金属基体结合力不高、易出现剥落问题;部分复合材料制备复杂、成本高且效率低,较难大批量应用。
4.材料的抗空蚀性能不但取决于硬度,还取决于材料的韧性和刚性,一般的非应变率敏感材料能更好地承受塑性变形而具有更好的抗空蚀能力。高熵合金具有高熵效应、迟滞扩散效应、晶格畸变效应和“鸡尾酒”效应等强化机制,强度和硬度、塑性等性能显著提升,理论上是较为理想的抗空蚀材料,但目前其在相关领域的开发应用仍较为有限。
5.目前抗空蚀涂层制备方法复杂繁琐,所得涂层存在强度低、脆性大、易剥落失效等问题。因此,一种结合强度高、服役寿命长、生产简便的抗空蚀涂层及其制备方法亟待开发。
技术实现要素:
6.针对上述现有技术存在的抗空蚀涂层制备方法繁琐,且现有的抗空蚀涂层存在强度低、脆性大、易剥落失效的技术问题,本发明的目的在于提供一种抗空蚀复合涂层,本发明还提出一种上述抗空蚀复合涂层的制备方法,本发明通过设计双相混合晶格结构高熵合金,采用均匀弥散第二相强化和表面强化等技术方法优化处理,获得兼具硬度高、刚度好和韧塑性佳等特性的复合强化涂层,解决当前抗空蚀涂层制备方法繁琐和要求苛刻的问题,克服现有涂层在周期疲劳交变应力下强度低、脆性大、易剥落失效的缺点。
7.根据本发明第一方面的抗空蚀复合涂层,所述抗空蚀复合涂层由高熵合金粉末源和0.01wt%-50wt%的第二相强化粉末源组成的复合粉体经超音速火焰喷涂制备而成;所述高熵合金粉末源由元素al、ti、v以及m代表的元素和n代表的元素组成。
8.高熵合金粉末源中的元素al、ti元素可以促进高密度析出相或微小金属间化合物的形成,提高材料强度;v元素可以与其他金属元素形成固溶相,提高材料刚度和韧性,另外v与c、o、n等形成高硬度、高弥散度的细小化合物,降低涂层的杂质含量的同时起到二次硬
化作用,进一步提高了材料强度和硬度。掺加的第二相强化粉末源起到沉淀强化和弥散强化的作用,细化晶粒的同时阻碍位错运动和裂纹延伸,进一步提高涂层强度和刚度,降低材料的非应变敏感性。
9.本发明的抗空蚀复合涂层在采用高熵合金的基础上,利用弥散第二相强化粉末源等技术,获得硬度高、刚度好、韧性佳的复合抗空蚀涂层。
10.在一些实施例中,所述m代表的元素为ni、cr、mn、mo、co、zr、cu、fe中的一种或多种,所述n代表的元素为nb、hf、ta、re、la中的一种或多种。
11.在一些实施例中,所述第二相强化粉末源为bn、si3n4、tin、hfn、sic、cr3c2、wc、tic、zrc、hfc、al2o3、zro2、la2o3、ceo2、tio2中的一种或多种。
12.进一步地,第二相强化粉末源还可以是石墨烯等其他合适材料。
13.在一些实施例中,组成所述高熵合金粉末源的原子百分比表达式为al
x
ti
yvz
(mn)
100-x-y-z
,通过调整所述al、v的原子比例形成bcc和fcc双相混合晶格固溶体结构,其中,x为al的原子数百分含量,y为ti的原子数百分含量,z为v的原子数百分含量。
14.优选通过调整al、v的原子比例形成bcc和fcc双相混合晶格固溶体结构,还可以通过调整ti、m代表的元素、n代表的元素的原子比例形成其他双相至多相混合晶格固溶体结构,同样起到强化作用,例如hcp bcc、hcp fcc、hcp bcc fcc结构。
15.高熵合金元素间金属元素粉末按照摩尔比5at%-35at%配比,元素间最大原子半径差小于20%,合金混合焓介于-50-20kj/mol。本发明的高熵合金为bcc fcc双相混合晶格固溶体结构,其中bcc相具有高强度、高硬度特性,起到微骨架支撑结构作用;fcc相韧塑性好,可填充孔隙缺陷,并紧密结合基体和黏结包覆第二相、弥散化合物,起到应力缓冲作用。
16.在一些实施例中,所述高熵合金粉末源的粒径为15-45μm,所述第二相强化粉末源的粒径为0.001-10μm,所述高熵合金粉末源和所述第二相强化粉末源的纯度均为99.95%以上。
17.本发明第二方面的抗空蚀复合涂层的制备方法:包括以下步骤:
18.(1)粉末准备阶段:称取所述高熵合金粉末源和所述第二相强化粉末源;
19.(2)粉末预处理阶段:所述高熵合金粉末源和所述第二相强化粉末源经气流破碎、震动过筛、三维混料机处理后获得混合均匀的所述复合粉体;
20.(3)基体喷涂阶段:对所述基体表面进行处理,然后采用超音速火焰喷涂机对所述基体进行所述复合粉体喷涂处理,得到所述抗空蚀复合涂层,所述超音速火焰喷涂机的工艺参数:火焰温度为2000℃-2500℃,丙烷流量为50-100nlpm,液氧流量为150-300nlpm,送粉量为20-80g/min,喷涂线速度为30-90m/min,压道量为1-7mm。
21.步骤(2)中高熵合金粉末源和第二相强化粉末源经气流破碎机打散团聚颗粒后,通过90-150目振动筛可筛除残余大颗粒,使粉体粒度分布和成分分布更均匀,气流破碎频率范围50-80hz/min;三维混料机的混合时间为6-12h,三维混料机转速为10-50r/min,以保证粉体混合均匀,无局部富集情况。
22.步骤(2)中超音速火焰喷涂机的其他工艺参数:压缩空气流量为250-450nlpm,载气流量为10-30nlpm,喷涂距离为200-400mm。
23.步骤(3)中采用超音速火焰喷涂机对所述基体进行所述复合粉体喷涂处理,复合粉体喷涂材料经高温焰流熔融雾化后,以超音速喷向基体表面,急速冷却、沉积,形成致密、
均匀、低氧化物含量的高结合力高熵合金复合涂层。火焰温度高达2000℃-2500℃,充分燃烧后游离碳氧含量显著降低,避免了粉末原材料氧化分解或形成涂层夹杂的问题;喷涂过程迅速,复合粉体喷涂材料经高温焰流熔融雾化急速冷却、沉积,机械结合和轻微冶金结合显著提高基体与涂层的结合效果。另外,丙烷为高纯度丙烷,液氧为高压液氧。
24.所述基体可以为不锈钢材质,但不限于不锈钢材质。
25.在一些实施例中,所述抗空蚀复合涂层的厚度为100-400μm。
26.在一些实施例中,在所述步骤(3)之后还包括强化处理阶段。
27.在一些实施例中,所述强化处理阶段的处理方法为采用涂敷薄膜材料的方式或采用表面重熔技术对所述抗空蚀复合涂层表面进行处理。
28.采用涂敷薄膜材料的方式对抗空蚀复合涂层表面进行处理为:利用涂敷机涂敷环氧树脂或聚氨酯弹性体等薄膜材料,对抗空蚀复合涂层表面进行封孔处理,降低表面粗糙度,提高水下光滑过流性和抗空蚀冲击性能,进一步提高涂层使用寿命。其中,涂敷速度为0.5-20m2/min,涂敷薄膜厚度为0.02-2mm。
29.采用重熔技术对抗空蚀复合涂层表面进行处理为:选用电子束、电弧、电火花、小功率激光等表面重熔技术对抗空蚀复合涂层表面进行处理,焊合表面喷涂缺陷,保持涂层内部韧塑性的同时,细化晶粒和快速淬火作用增强了抗空蚀复合涂层表面强度、刚度和耐蚀度,且不会对基体造成应力变形、组织变化等负面影响。优选地,采用微激光重熔方法,其中,重熔速度为2-50m/min,重熔层深度为5-300μm。
30.在一些实施例中,对所述基体表面进行处理的过程为对所述基体表面进行除锈除油后喷砂粗化,然后采用有机溶剂超声清洗。
31.其中,喷砂材质为金刚砂、氧化铝、棕刚玉等。优选地,喷砂材质为金刚砂,目数范围为40-100目,金刚砂的粗化效果好。有机溶剂可以为酒精或丙酮,但不限于酒精或丙酮。
32.相对于现有技术,本发明的技术效果为:
33.本发明所选用原材料为常规市售品,无需真空雾化等特殊方法专门制备高熵合金粉末,简化生产流程,显著地降低了产品成本和生产难度。经气流破碎、震动过筛后三维混料方法制备复合粉体均匀程度度高,可有效避免局部富集问题;也避免了球磨混料等方法导致粉末颗粒形貌产生变化。
34.本发明制备的双相混合高熵合金中固溶相结构简单、分布均匀。其中bcc相具有高强度、高硬度特性,起到微骨架支撑结构作用;fcc相韧塑性好,可填充孔隙缺陷并紧密结合基体和黏结包覆第二相,起到应力缓冲作用。此外,掺加的第二相强化源起到沉淀强化和弥散强化的作用,细化晶粒的同时阻碍位错运动和裂纹延伸,进一步提高涂层强度和刚度,降低材料的非应变敏感性。
35.本发明采用高纯丙烷和液氧条件下的超音速火焰喷涂方法并优化设备及工艺,火焰温度最高达2000℃~2500℃,充分燃烧后游离碳氧含量显著降低,解决了粉末原材料氧化分解或形成涂层夹杂的问题;喷涂过程迅速,合金材料经高温焰流熔融雾化急速冷却沉积,机械结合和轻微冶金结合显著提高基体与涂层的结合效果,结合强度可达到75mpa以上,优于当前行业常规涂层水平。
36.本发明采用超音速火焰喷涂和表面强化法制备高熵合金复合涂层。涂敷薄膜材料可进一步提升水下光滑过流性和抗空蚀冲击性能,有效提高涂层使用寿命。表面重熔在不
影响基体的前提下,显著增强了涂层表面强度和刚度并保持涂层内部韧塑性,表面维氏硬度可达到750hv
0.3
以上,内部屈服强度高和塑性应变性能好。
37.本发明制备方法成本较低、简便易控、生产效率高,且不受基体形状限制,适合批量化应用。
附图说明
38.本发明上述的和/或附加的方面和优点从下面结合附图对实施例的描述中将变得明显和容易理解,其中:
39.图1为本发明抗空蚀复合涂层制备流程图;
40.图2为本发明实施例2制备的抗空蚀复合涂层的金相照片。
具体实施方式
41.下面详细描述本发明的实施例,所述实施例的示例在附图中示出,其中自始至终相同或类似的标号表示相同或类似的元件或具有相同或类似功能的元件。下面通过参考附图描述的实施例是示例性的,旨在用于解释本发明,而不能理解为对本发明的限制。
42.下面参照附图描述根据本发明实施例提出的抗空蚀复合涂层及其制备方法。
43.本发明所选用原材料为常规市售品,无需真空雾化等特殊方法专门制备高熵合金粉末,简化生产流程,显著地降低了产品成本和生产难度。
44.本发明提供的抗空蚀复合涂层由高熵合金粉末源和0.01wt%-50wt%的第二相强化粉末源组成的复合粉体经超音速火焰喷涂制备而成;高熵合金粉末源由元素al、ti、v以及m代表的元素和n代表的元素组成。m代表的元素为ni、cr、mn、mo、co、zr、cu、fe中的一种或多种,n代表的元素为nb、hf、ta、re、la中的一种或多种。第二相强化粉末源为bn、si3n4、tin、hfn、sic、cr3c2、wc、tic、zrc、hfc、al2o3、zro2、la2o3、ceo2、tio2中的一种或多种,第二相强化粉末源不限于上述物质。高熵合金粉末源的粒径为15-45μm,第二相强化粉末源的粒径为0.001-10μm,高熵合金粉末源和第二相强化粉末源的纯度均为99.95%以上。
45.组成高熵合金粉末源的原子百分比表达式为al
x
ti
yvz
(mn)
100-x-y-z
,通过调整al、v的原子比例形成bcc fcc双相混合晶格固溶体结构,其中,x为al的原子数百分含量,y为ti的原子数百分含量,z为v的原子数百分含量。
46.本发明提供的抗空蚀复合涂层的制备方法,如图1所示,包括以下步骤:
47.(1)粉末准备阶段;
48.(2)粉末预处理阶段;
49.(3)基体喷涂阶段;
50.(4)强化处理阶段。
51.粉末准备阶段:
52.选择符合要求的金属粉末源和第二相强化源,按照一定的摩尔比进行准备,并按照一定的质量比值称取高熵合金粉末源和第二相强化粉末源。
53.粉末预处理阶段:
54.高熵合金粉末源和第二相强化粉末源复合粉体经气流破碎、震动过筛、三维混料机处理后获得混合均匀的复合粉体。具体为,复合粉体经分级气流破碎机打散团聚颗粒后,
通过90-150目振动筛,再经三维混料机混合均匀。气流破碎频率范围50-80hz/min,三维混料机的混合时间为6-12h,三维混料机转速为10-50r/min。
55.基体喷涂阶段:
56.对基体表面进行处理,然后采用超音速火焰喷涂机对基体进行复合粉体喷涂处理,得到抗空蚀复合涂层。具体为,对基体表面进行处理的过程为对基体表面进行除锈除油后喷砂粗化,然后采用有机溶剂超声清洗,并干燥备用。其中,喷砂材质为金刚砂、氧化铝、棕刚玉等。喷砂材质为金刚砂,目数范围为40-100目时粗化效果较好。有机溶剂可以为酒精或丙酮,或其他合适物质。
57.超音速火焰喷涂机的工艺参数:火焰温度为2000℃-2500℃,丙烷流量为50-100nlpm,液氧流量为150-300nlpm,送粉量为20-80g/min,喷涂线速度为30-90m/min,压道量为1-7mm,压缩空气流量为250-450nlpm,载气流量为10-30nlpm,喷涂距离为200-400mm。复合粉体喷涂材料经高温焰流熔融雾化后,以超音速喷向基体表面,急速冷却、沉积,形成致密、均匀、低氧化物含量的高结合力高熵合金复合涂层,形成的抗空蚀涂层的厚度为100-400μm。超音速火焰喷涂过程迅速,复合粉体材料经高温焰流熔融雾化急速冷却沉积,机械结合和轻微冶金结合显著提高了基体与涂层的结合效果,结合强度可达到75mpa以上。
58.强化处理阶段:
59.强化处理阶段的处理方法为采用涂敷薄膜材料的方式或采用表面重熔技术对抗空蚀复合涂层表面进行处理。
60.采用涂敷薄膜材料的方式对抗空蚀复合涂层表面进行处理为:利用涂敷机涂敷环氧树脂或聚氨酯弹性体等薄膜材料,对抗空蚀复合涂层表面进行封孔处理。其中,涂敷速度为0.5-20m2/min,涂敷薄膜厚度为0.02-2mm。采用重熔技术对抗空蚀复合涂层表面进行处理为:选用电子束、电弧、电火花、小功率激光等表面重熔技术对抗空蚀复合涂层表面进行处理,焊合表面喷涂缺陷。优先采用微激光重熔方法,当采用微激光重熔方法进行强化处理时,重熔速度为2-50m/min,重熔层深度为5-300μm。
61.本发明采用超音速火焰喷涂和表面强化制备抗空蚀高熵合金复合涂层。涂敷薄膜材料可进一步提升水下光滑过流性和抗空蚀冲击性能,有效提高涂层使用寿命;表面重熔在不影响基体的前提下,显著增强了涂层表面强度和硬度,并保持内部韧塑性,表面维氏硬度可达到750hv
0.3
以上。
62.下面结合具体实施例对本发明进一步说明。以下实施例中所用原料均可由市场购得。
63.结合强度检测按照gbt8642-2002《热喷涂-抗拉结合强度的测定》进行,硬度检测按照gb/t 4340.1-1999《金属维氏硬度试验第1部分:试验方法》进行,厚度检测按照gbt11374-2012《热喷涂涂层厚度的无损测量方法》进行。孔隙率检测按照astme2109-2001(2014)《测定热喷镀涂层孔隙率面积百分比的标准试验方法》进行。
64.实施例1:alticovnb/bn复合涂层
65.按照重量百分比为95%:5%准备满足要求的高熵合金粉末源和bn第二相强化粉末源。其中,高熵合金粉末源为按摩尔配比1:1:1:1:1配制的al、ti、co、v、nb合金粉末。复合粉体经50hz/min频率气流破碎后,过100目震动筛后,将筛下物装入混料罐,采用三维混料机混合8h,三维混料机的转速为30r/min,获得均匀高熵合金复合粉末。
66.常用水电马氏体不锈钢(牌号为zg0cr16ni5mo)基体表面经除锈除油后,进行60目金刚砂喷砂粗化预处理,并使用酒精超声清洗干净,干燥备用。对基体进行高熵合金复合粉末多道次超音速喷涂处理,具体工艺参数为:高纯度丙烷流量为70nlpm,高压液氧流量为220nlpm,压缩空气流量为350nlpm,载气流量为20nlpm,送粉量为60g/min,喷涂距离为300mm,喷涂线速度为60m/min,压道量为4mm,获得组织均匀、结合强度高的涂层厚度为320μm的双相高熵合金复合涂层。对涂层进行表面涂敷聚氨酯弹性体强化处理,涂敷速度为10m2/min,涂敷薄膜厚度为0.5mm,最终获得抗空蚀复合强化涂层。
67.参见表1,alticovnb/bn复合涂层厚度为382μm,表面硬度为780hv
0.3
,涂层与基体结合强度为75mpa,孔隙率为0.28%。
68.实施例2:alnitimovnb/sic复合涂层
69.按照重量百分比为90%:10%准备满足要求的高熵合金粉末源和sic第二相强化粉末源。其中,高熵合金粉末源为按摩尔配比0.8:1:1:1:1:0.5配制的al、ni、ti、mo、v、nb合金粉末。复合粉体经50hz/min频率气流破碎后,过120目震动筛后,将筛下物装入混料罐,采用三维混料机混合6h,三维混料机的转速为40r/min,获得均匀高熵合金复合粉末。
70.常用水电马氏体不锈钢(牌号为zg0cr13ni4mo)基体表面经除锈除油后,进行80目氧化铝喷砂粗化预处理,并使用酒精超声清洗干净,干燥备用。对基体进行高熵合金复合粉末多道次超音速喷涂处理,具体工艺参数为:高纯度丙烷流量为90nlpm,高压液氧流量为300nlpm,压缩空气流量为410nlpm,载气流量为28nlpm,送粉量为65g/min,喷涂距离为270mm,喷涂线速度为58m/min,压道量为4mm,获得组织均匀、结合强度高的涂层厚度为360μm的双相高熵合金复合涂层。选用电火花表面重熔技术对涂层表面进行处理,重熔速度为20m/min,深度为40μm,最终获得抗空蚀复合强化涂层。alnitimovnb/sic复合涂层的金相照片如图2所示,从图中可以看出本发明制备的复合涂层厚度和组织均匀,第二相弥散均匀细小,与基体结合情况良好。
71.参见表1,alnitimovnb/sic复合涂层厚度为340μm,表面硬度为850hv
0.3
,涂层与基体结合强度为88mpa,孔隙率为0.35%。
72.实施例3:alcrtimovta/cr3c2复合涂层
73.按照重量百分比为70%:30%准备满足要求的高熵合金粉末源和cr3c2第二相强化粉末源。其中,高熵合金粉末源为按摩尔配比1:1:1:1:1:0.5配制的al、cr、ti、mo、v、ta合金粉末。复合粉体经60hz/min频率气流破碎后,过100目震动筛后,将筛下物装入混料罐,采用三维混料机混合9h,三维混料机的转速为45r/min,获得均匀高熵合金复合粉末。
74.常用水电马氏体不锈钢(牌号为zg0cr13ni4mo)基体表面经除锈除油后,进行100目金刚砂喷砂粗化预处理,并使用酒精超声清洗干净,干燥备用。对基体进行高熵合金复合粉末多道次超音速喷涂处理,具体工艺参数为:高纯度丙烷流量为80nlpm;高压液氧流量为300nlpm,压缩空气流量为400nlpm,载气流量为25nlpm,送粉量为62g/min,喷涂距离为300mm,喷涂线速度为65m/min,压道量为3mm,获得组织均匀、结合强度高的涂层厚度为350μm的双相高熵合金复合涂层。对涂层进行表面喷涂环氧树脂强化处理,涂敷速度为15m2/min,涂敷薄膜厚度为0.1mm,最终获得抗空蚀复合强化涂层。
75.参见表1,alcrtimovta/cr3c2复合涂层厚度为300μm,表面硬度为880hv
0.3
,涂层与基体结合强度为84mpa,孔隙率为0.48%。
76.上述本发明复合涂层性能对比如表1所示,表1中的显微硬度即为表面维氏硬度。
77.表1:复合涂层性能对比
[0078][0079]
从表1可以看出,alticovnb/bn、alnitimovnb/sic、alcrtimovta/cr3c2三种复合涂层的结合强度分别为75mpa、88mpa、84mpa,均在75mpa以上;显微硬度分别为780hv
0.3
、850hv
0.3
、880hv
0.3
,均在750hv
0.3
以上,可知,本发明提供的抗空蚀复合涂层结合强度高、硬度大。
[0080]
在本说明书的描述中,参考术语“一个实施例”、“一些实施例”、“示例”、“具体示例”、或“一些示例”等的描述意指结合该实施例或示例描述的具体特征、结构、材料或者特点包含于本发明的至少一个实施例或示例中。在本说明书中,对上述术语的示意性表述不必须针对的是相同的实施例或示例。而且,描述的具体特征、结构、材料或者特点可以在任一个或多个实施例或示例中以合适的方式结合。此外,在不相互矛盾的情况下,本领域的技术人员可以将本说明书中描述的不同实施例或示例以及不同实施例或示例的特征进行结合和组合。
[0081]
此外,术语“第一”、“第二”仅用于描述目的,而不能理解为指示或暗示相对重要性或者隐含指明所指示的技术特征的数量。由此,限定有“第一”、“第二”的特征可以明示或者隐含地包括至少一个该特征。在本发明的描述中,“多个”的含义是至少两个,例如两个,三个等,除非另有明确具体的限定。
[0082]
尽管已经示出和描述了本发明的实施例,本领域的普通技术人员可以理解:在不脱离本发明的原理和宗旨的情况下可以对这些实施例进行多种变化、修改、替换和变型,本发明的范围由权利要求及其等同物限定。
再多了解一些
本文用于企业家、创业者技术爱好者查询,结果仅供参考。