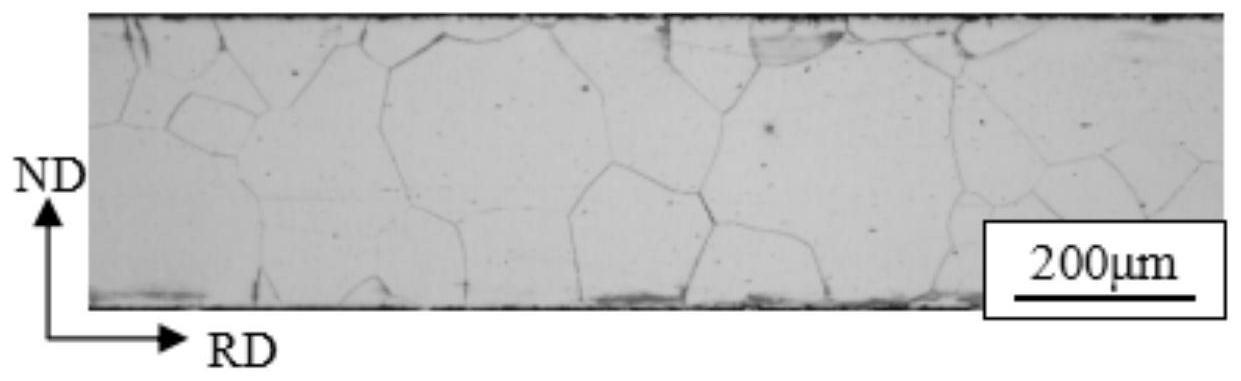
1.本发明属于冶金技术领域,具体涉及一种基于纳米析出强化制备高强度无取向硅钢的方法。
背景技术:
2.高速电机的电机转子高速运转(速度可达10000~20000r/min),故要求所使用的电工钢片具有足够高的强度抵抗离心力,特别是对于磁极镶嵌于转子之中的永磁驱动电机,因此保证转子的强度至关重要。而为了提高能源转换效率,要求电机所用电工钢片具有优秀的磁性能,即中低磁场下的高磁感和高频下的低铁损。但对于硅钢而言很难同时兼顾磁性能和力学性能,因此高强度无取向硅钢的成分与工艺设计至关重要,这也决定了其强化手段的选择。
3.电机所用的电工钢片成分通常都是超低碳、氮(质量分数均小于50ppm)和高硅,有时还需要加入高al含量来保证其优异的磁性能特别是低的铁损。驱动电机要求的电工钢片要较传统无取向电工钢强度高200mpa以上,并且提高强度同时还需保证不能损害其优良的磁性能。因此开发此类钢的关键就是在高si al含量的无取向硅钢成分体系下,如何大幅度提高强度而不会恶化磁性能。由于电工钢的超低碳含量以及冷轧后需进行再结晶退火,一般情况下无法通过相变和位错强化机制进行强化,而电工钢产品为了防止磁滞时效,其碳、氮含量均很低,因此也无法进行间隙原子固溶强化。因此可行的强化机制只有代位原子固溶强化和析出强化。
4.中国发明专利公开号cn112030076a,公开了一种高速电机用高强度电工钢及其制备方法,通过控制固溶强化元素si,p与mn兼顾提高电工钢强度和可轧性,并通过纯净化冶炼控制夹杂物数量,晶界偏聚元素sn有利于获得对磁性能有利的{100}织构,提高磁性能。但屈服强度提高幅度较小,仅为520mpa左右。
5.中国发明专利公开号cn111321344a,公开了一种电动汽车驱动电机用高强度冷轧无取向电工钢及其生产方法,通过添加cu、nb等强化元素得到析出相并阻止晶界迁移来提高强度,同时添加sn、sb等微量元素来改善无取向电工钢织构组分提高磁感。其屈服强度rp
0.2
≥600mpa,但高频铁损较高,p
1.0/400
达到35w/kg。
6.为满足新能源汽车驱动电机对无取向硅钢的严格要求,需要进一步采用新的技术手段,开发高磁感、低铁损、高强度的无取向硅钢。
技术实现要素:
7.为了克服现有技术缺陷,本发明的目的在于提供一种工艺较简单、生产成本低的基于纳米nial析出强化的高强度无取向硅钢及其制造方法,通过成分和工艺设计优化,最终制备的高强无取向硅钢磁性可以满足用户对新能源汽车驱动电机用无取向硅钢性能要求。
8.本发明采取的技术方案为:
9.一种基于纳米析出强化制备高强度无取向硅钢的方法,该高强度无取向硅钢的化学成分是:si 2.5~4.5wt.%,ni 2.5~6.5wt.%,al 1.0~3.0wt.%,mn 0.1~1.0wt.%,cu 0~1.0wt.%,(c n o s)≤100ppm,其余为fe。
10.所述的基于纳米析出强化制备高强度无取向硅钢的方法,高强度无取向硅钢薄带采用以下步骤生产:
11.a.真空冶炼;
12.b.浇铸锻造及热轧加工,或者薄带连铸;
13.c.常化热处理;
14.d.酸洗与冷轧加工;
15.e.再结晶退火;
16.f.时效热处理。
17.所述的基于纳米析出强化制备高强度无取向硅钢的方法,步骤a中,采用纯度均为99.99wt.%及以上的原料,以真空感应炉对混合原料进行冶炼,在真空度≤10pa条件下真空脱气30min以上,冶炼温度为1400~1600℃,得到无取向硅钢钢水。
18.所述的基于纳米析出强化制备高强度无取向硅钢的方法,步骤b中,将钢水浇铸为铸锭并于1000~1200℃锻造为方坯,方坯随后进入加热炉,加热温度为1000~1200℃,保温时间30~180min,经热轧至1.5~3mm厚度,终轧温度大于800℃;或者,将钢水浇入由两个相反方向旋转的铸辊及侧封组成的熔池内得到1.5~3mm厚薄带。
19.所述的基于纳米析出强化制备高强度无取向硅钢的方法,步骤c中,在900~1100℃进行常化热处理,并控制常化热处理时间为3~15min。
20.所述的基于纳米析出强化制备高强度无取向硅钢的方法,步骤d中,使用浓度为10%~20%盐酸进行酸洗后,在室温条件下冷轧至0.20~0.50mm。
21.所述的基于纳米析出强化制备高强度无取向硅钢的方法,步骤e中,退火温度900~1100℃,时间3~15min,按体积百分比计,使用(5%~40%)h2 (60%~95%)n2的混合保护气氛。
22.所述的基于纳米析出强化制备高强度无取向硅钢的方法,步骤f中,在450~600℃保温0.5~8h进行时效处理,使纳米金属间化合物nial充分析出。
23.所述的基于纳米析出强化制备高强度无取向硅钢的方法,高强度无取向硅钢的性能指标:磁感应强度b
50
为1.60~1.70t,p
10/400
为10~31w/kg,屈服强度rp
0.2
为700~1000mpa,抗拉强度rm为740~1150mpa,延伸率a为8~20%。
24.本发明硅钢成分的设计原理为:
25.si:si在α-fe中固溶后使电阻率增加,γ相区缩小、涡流损耗降低和使铁损值降低的同时磁感值也降低,si起固溶强化作用能提高高强无取向硅钢强度,但si含量过高时会使钢板轧制困难。因此,本发明中si含量设计为2.5~4.5wt.%,优选为2.8~3.8wt.%;
26.ni与al:是本发明主要强化相金属间化合物nial相的形成元素,同时固溶少量al元素可明显提高电阻率,而对钢强度和硬度影响不像si那样明显,并可使{100}组分提高和{111}组分减少。因此,本发明中ni含量设计为2.5~6.5wt.%,优选为2.5~4.0wt.%;al含量设计为1.0~3.0wt.%,优选为1.5~2.5wt.%;
27.mn:mn在钢中起固溶强化作用,提高电工钢的电阻率降低铁损;mn易与s形成mns夹
杂物,防止fes引起的热脆,mns粗化后利于晶粒长大,加mn有利于冲片性和切削性。因此,本发明中mn的含量设计为0.1~1.0wt.%,优选为0.1~0.8wt.%;
28.cu:cu在铁素体中的溶解度很小,固溶处理后再进行时效可得到大量细小并且弥散分布析出相,具有灵活的热轧工艺控制窗口,操作简单成本经济。cu析出还可以增加有益的{110}织构强度,降低有害的{111}织构强度,从而使退火板的铁损降低,磁感也没有明显恶化。此外,cu可与nial相协同析出,使得纳米析出的粗化速率明显降低。因此,本发明中cu的含量设计为0~1.0wt.%,优选为0.3~1.0%;
29.c、n、o、s为杂质或对磁性能有害元素,其中c容易导致产生磁时效,n和s易于al、si、mn等元素结合,形成析出物,影响无取向硅钢铁损值。因此,本发明中(c n o s)含量应控制在100ppm以下。
30.与现有技术相比,本发明具有以下优点及有益效果:
31.1)本发明通过ni和al固溶强化元素添加,时效处理后高强度无取向硅钢板内会形成大量纳米b2型金属间化合物nial,可明显提高无取向硅钢力学性能,同时不损害无取向硅钢磁性能。同时,该nial相强化技术手段同时适用于无取向硅钢的常规热轧制备流程和薄带连铸制备流程。
32.2)本发明结合热轧、常化和冷轧工艺优化调整,可制备0.20~0.50mm厚度规格无取向硅钢,厚度规格更宽,可满足新能源汽车驱动电机不同频率工况下的使用要求。
33.3)采用本发明生产的高强无取向硅钢产品,当产品厚度为0.35mm时磁感应强度b
50
典型值范围1.60~1.70t,铁损p
10/400
典型值范围16~23w/kg。
34.4)本发明制备的无取向硅钢屈服强度rp
0.2
典型值范围700~1000mpa,抗拉强度rm典型值范围为740~1150mpa,延伸率a为8~20%,相比常规产品屈服强度rp
0.2
和抗拉强度rm提升35%以上。与普通无取向硅钢生产流程相比,仅在再结晶退火后增加低温时效处理工序,用于控制nial相析出,制备方法简单可行,且产品性能优良。
附图说明
35.图1为实施例1中的基于纳米析出强化制备高强度无取向硅钢成品板的金相显微组织图。
具体实施方式
36.在具体实施过程中,本发明对基于纳米b2型金属间化合物nial析出强化制备的高强度无取向硅钢进行性能测试时,磁性能测试采用mata磁性材料自动测试系统v4.0进行实验材料的磁性测量和数据分析记录,使用mats-2010m硅钢测量装置测量无取向硅钢单片的磁性能。铁损p
10/400
为频率400hz交变磁场,磁极化强度在1.0t下测得的比总损耗,磁感b
50
为磁场强度为5000a/m条件下测得的磁极化强度。
37.本发明实施例中,拉伸试验采用gb/t 228.1-2010国家标准室温进行。
38.下面,结合实施例对本发明进行详细说明。
39.实施例1
40.本实施例中,一种基于纳米析出强化制备高强度无取向硅钢的常规热轧流程制造方法,具体步骤如下:
41.1)采用纯度均为99.99wt.%及以上的原料,以真空感应炉按设定成分冶炼钢水,其成分按重量百分比含si 3.3wt.%,ni 4.0wt.%,al 2.2wt.%,mn 0.7wt.%,cu 0.5wt.%,c 39ppm,n 22ppm,o 17ppm,s 15ppm,其余为fe,在真空度10pa条件下真空脱气40min,冶炼温度为1520℃,得到无取向硅钢钢水,浇铸为铸锭并于1115℃锻造为方坯。
42.2)加热炉温度1200℃,保温时间120min,经热轧至2mm厚度,终轧温度950℃。
43.3)在1050℃进行常化热处理,并控制常化热处理时间为5min。
44.4)使用浓度为10%盐酸进行酸洗后,在室温条件下多道次冷轧至0.50mm。
45.5)将冷轧板进行退火处理,最终退火处理是将冷轧板置于15%(体积)h2 85%(体积)n2混合气氛条件下,升温至1000℃,保温10min,获得无取向硅钢的退火板。
46.6)将冷轧板进行时效处理,在550℃保温4h,最后获得无取向硅钢的成品板。
47.经上述工艺制造的汽车发电机用无取向硅钢表面质量优良,其金相组织为铁素体。成品的磁感应强度b
50
为1.605t,铁损值p
10/400
为30.0w/kg;屈服强度rp
0.2
为850mpa,抗拉强度rm为950mpa,延伸率a为15%。
48.如图1所示,实施例1中的基于纳米析出强化制备高强度无取向硅钢成品板的金相显微组织图,从图中可以看出,再结晶组织相对均匀,晶粒长大充分,平均晶粒尺寸约为150μm,可获得较低的铁损值。
49.实施例2
50.本实施例中,一种基于纳米析出强化制备高强度无取向硅钢的常规热轧流程制造方法,具体步骤如下:
51.1)采用纯度均为99.99wt.%及以上的原料,以真空感应炉按设定成分冶炼钢水,其成分按重量百分比含si 3.1wt.%,ni 4.1wt.%,al 2.0wt.%,mn 1.0wt.%,c 37ppm,n 31ppm,o 19ppm,s 13ppm,其余为fe,在真空度10pa条件下真空脱气40min,冶炼温度为1515℃,得到无取向硅钢钢水,浇铸为铸锭并于1106℃锻造为方坯。
52.2)加热炉温度1150℃,保温时间120min,经热轧至2mm厚度,终轧温度950℃。
53.3)在1000℃进行常化热处理,并控制常化热处理时间为5min。
54.4)使用浓度为10%盐酸进行酸洗后,在室温条件下多道次冷轧至0.35mm。
55.5)将冷轧板进行退火处理,最终退火处理是将冷轧板置于5%(体积)h2 95%(体积)n2混合气氛条件下,升温至1000℃,保温10min,获得无取向硅钢的退火板。
56.6)将冷轧板进行时效处理,在550℃保温3.5h,最后获得无取向硅钢的成品板。
57.经上述工艺制造的汽车发电机用无取向硅钢表面质量优良,其金相组织为铁素体。成品的磁感应强度b
50
为1.608t,铁损值p
10/400
为21.0w/kg;屈服强度rp
0.2
为836mpa,抗拉强度rm为895mpa,延伸率a为16%。
58.实施例3
59.本实施例中,一种基于纳米析出强化制备高强度无取向硅钢的常规热轧流程制造方法,具体步骤如下:
60.1)采用纯度均为99.99wt.%及以上的原料,以真空感应炉按设定成分冶炼钢水,其成分按重量百分比含si 3.2wt.%,ni 3.1wt.%,al 2.2wt.%,mn 0.6wt.%,cu 0.5wt.%,c 36ppm,n 24ppm,o 17ppm,s 21ppm,其余为fe,在真空度10pa条件下真空脱气40min,冶炼温度为1512℃,得到无取向硅钢钢水,浇铸为铸锭并于1125℃锻造为方坯。
61.2)加热炉温度1100℃,保温时间120min,经热轧至2mm厚度,终轧温度950℃。
62.3)在980℃进行常化热处理,并控制常化热处理时间为5min。
63.4)使用浓度为10%盐酸进行酸洗后,在室温条件下多道次冷轧至0.50mm。
64.5)将冷轧板进行退火处理,最终退火处理是将冷轧板置于20%(体积)h2 80%(体积)n2混合气氛条件下,升温至1000℃,保温10min,获得无取向硅钢的退火板。
65.6)将冷轧板进行时效处理,在550℃保温5h,最后获得无取向硅钢的成品板。
66.经上述工艺制造的汽车发电机用无取向硅钢表面质量优良,其金相组织为铁素体。成品的磁感应强度b
50
为1.621t,铁损值p
10/400
为31.0w/kg;屈服强度rp
0.2
为822mpa,抗拉强度rm为871mpa,延伸率a为20%。
67.实施例4
68.本实施例中,一种基于纳米析出强化制备高强度无取向硅钢的常规热轧流程制造方法,具体步骤如下:
69.1)采用纯度均为99.99wt.%及以上的原料,以真空感应炉按设定成分冶炼钢水,其成分按重量百分比含si 3.0wt.%,ni 2.5wt.%,al 1.0wt.%,mn 0.5wt.%,cu 1.0wt.%,c 33ppm,n 26ppm,o 14ppm,s 18ppm,其余为fe,在真空度10pa条件下真空脱气40min,冶炼温度为1522℃,得到无取向硅钢钢水,浇铸为铸锭并于1130℃锻造为方坯。
70.2)加热炉温度1000℃,保温时间120min,经热轧至2mm厚度,终轧温度950℃。
71.3)在1050℃进行常化热处理,并控制常化热处理时间为5min。
72.4)使用浓度为10%盐酸进行酸洗后,在室温条件下多道次冷轧至0.20mm。
73.5)将冷轧板进行退火处理,最终退火处理是将冷轧板置于15%(体积)h2 85%(体积)n2混合气氛条件下,升温至1000℃,保温10min,获得无取向硅钢的退火板。
74.6)将冷轧板进行时效处理,在550℃保温4.5h,最后获得无取向硅钢的成品板。
75.经上述工艺制造的汽车发电机用无取向硅钢表面质量优良,其金相组织为铁素体。成品的磁感应强度b
50
为1.625t,铁损值p
10/400
为11.0w/kg;屈服强度rp
0.2
为700mpa,抗拉强度rm为740mpa,延伸率a为18%。
76.实施例5
77.本实施例中,一种基于纳米析出强化制备高强度无取向硅钢的薄带连铸流程制造方法,具体步骤如下:
78.1)采用纯度均为99.99wt.%及以上的原料,以真空感应炉按设定成分冶炼钢水,其成分按重量百分比含si 3.1wt.%,ni 4.3wt.%,al 2.2wt.%,mn 0.6wt.%,cu 0.5wt.%,c 34ppm,n 23ppm,o 19ppm,s 15ppm,其余为fe,在真空度5pa条件下真空脱气40min,冶炼温度为1517℃;将钢水浇入由两个相反方向旋转的铸辊及侧封组成的熔池内,通过薄带连铸得到2.5mm厚无取向硅钢铸带。
79.2)在1050℃进行常化热处理,并控制常化热处理时间为5min。
80.3)使用浓度为10%盐酸进行酸洗后,在室温条件下多道次冷轧至0.50mm。
81.4)将冷轧板进行退火处理,最终退火处理是将冷轧板置于15%(体积)h2 85%(体积)n2混合气氛条件下,升温至1000℃,保温10min,获得无取向硅钢的退火板。
82.5)将冷轧板进行时效处理,在550℃保温4h,最后获得无取向硅钢的成品板。
83.经上述工艺制造的汽车发电机用无取向硅钢表面质量优良,其金相组织为铁素
1.0wt.%,c 30ppm,n 30ppm,o 15ppm,s 20ppm,其余为fe,在真空度5pa条件下真空脱气40min,冶炼温度为1525℃;将钢水浇入由两个相反方向旋转的铸辊及侧封组成的熔池内,通过薄带连铸得到2.4mm厚无取向硅钢铸带。
103.2)在1050℃进行常化热处理,并控制常化热处理时间为5min。
104.3)使用浓度为10%盐酸进行酸洗后,在室温条件下多道次冷轧至0.35mm。
105.4)将冷轧板进行退火处理,最终退火处理是将冷轧板置于30%(体积)h2 70%(体积)n2混合气氛条件下,升温至1000℃,保温10min,获得无取向硅钢的退火板。
106.5)将冷轧板进行时效处理,在600℃保温4h,最后获得无取向硅钢的成品板。
107.经上述工艺制造的汽车发电机用无取向硅钢表面质量优良,其金相组织为铁素体。成品的磁感应强度b
50
为1.652t,铁损值p
10/400
为19.0w/kg;屈服强度rp
0.2
为735mpa,抗拉强度rm为815mpa,延伸率a为11%。
108.实施例9
109.本实施例中,一种基于纳米析出强化制备高强度无取向硅钢的薄带连铸流程制造方法,具体步骤如下:
110.1)采用纯度均为99.99wt.%及以上的原料,以真空感应炉按设定成分冶炼钢水,其成分按重量百分比含si 3.5wt.%,ni 3.1wt.%,al 2.0wt.%,mn 0.6wt.%,c 25ppm,n 32ppm,o 20ppm,s 15ppm,其余为fe,在真空度5pa条件下真空脱气40min,冶炼温度为1525℃;将钢水浇入由两个相反方向旋转的铸辊及侧封组成的熔池内,通过薄带连铸得到2.4mm厚无取向硅钢铸带。
111.2)在1050℃进行常化热处理,并控制常化热处理时间为5min。
112.3)使用浓度为10%盐酸进行酸洗后,在室温条件下多道次冷轧至0.35mm。
113.4)将冷轧板进行退火处理,最终退火处理是将冷轧板置于35%(体积)h2 65%(体积)n2混合气氛条件下,升温至1000℃,保温10min,获得无取向硅钢的退火板。
114.5)将冷轧板进行时效处理,在600℃保温1h,最后获得无取向硅钢的成品板。
115.经上述工艺制造的汽车发电机用无取向硅钢表面质量优良,其金相组织为铁素体。成品的磁感应强度b
50
为1.700t,铁损值p
10/400
为19.5w/kg;屈服强度rp
0.2
为755mpa,抗拉强度rm为824mpa,延伸率a为12%。
再多了解一些
本文用于企业家、创业者技术爱好者查询,结果仅供参考。