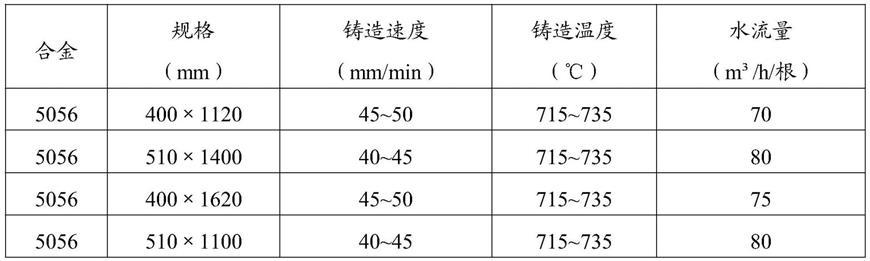
1.本发明属于铝合金领域,尤其涉及一种5056铝合金铸锭的制备方法。
背景技术:
2.航天用铝蜂窝板材主要为5052和5056铝合金蜂窝结构板材,合金及规格特殊,质量要求高。目前,我国的国航天用铝蜂窝板材主要依赖于进口,不仅价格昂贵,而且时常面临禁买禁运,对我国航天事业的发展造成严重影响。因此,如何自主攻关研发满足航天用铝蜂窝芯材要求的铝合金铸锭,是目前亟待解决的技术问题。
技术实现要素:
3.有鉴于此,本发明的目的在于提供一种5056铝合金铸锭的制备方法,采用本发明方法制备的铝合金铸锭氢含量低,纯净度高,可用于制备航天用铝蜂窝芯材。
4.本发明提供了一种5056铝合金铸锭的制备方法,包括以下步骤:
5.a)将除mg之外的5056铝合金原料装炉熔炼,扒渣,然后向炉内加入mg锭继续熔炼,得到5056铝合金熔体;
6.分别在除mg之外的5056铝合金原料装炉完毕后、进行扒渣前和mg锭加入完毕后对炉内物料表面进行熔剂覆盖;
7.所述装炉熔炼的温度为750~760℃;所述加入mg锭继续熔炼的温度比所述装炉熔炼的温度低5~20℃;
8.b)将所述5056铝合金熔体进行搅拌,得到搅拌后熔体;
9.c)将所述搅拌后熔体在混合气体气氛中进行精炼,得到精炼后熔体;
10.所述混合气体的成分包括氩气与氯气;所述精炼的温度为720~750℃;所述精炼的时间为30~45min;
11.d)将所述精炼后熔体依次进行在线除气和在线过滤,得到在线处理后熔体;
12.所述在线除气的方式为旋转喷吹除气;所述旋转喷吹除气所用除气装置的转子转速为300~400转/min;所述旋转喷吹除气的喷吹压力为0.1mpa~0.3mpa;所述旋转喷吹除气所用除气装置每根转子的气体流量为3000~5000l/h;
13.e)将所述在线处理后熔体进行铸造,得到铸锭粗品;
14.f)将所述铸锭粗品依次进行均热和机加工,得到5056铝合金铸锭。
15.优选的,步骤b)中,所述搅拌方式为电磁搅拌。
16.优选的,步骤c)中,所述氩气在混合气体中的含量为85~90wt%;所述氯气在混合气体中的含量为10~15wt%。
17.优选的,步骤c)中,在进行精炼之前,先向所述搅拌后熔体中加入熔剂。
18.优选的,步骤c)中,完成精炼之后,在所述精炼后熔体表面覆盖熔剂并进行静置。
19.优选的,步骤d)中,所述在线过滤所使用的过滤装置内表面喷涂有氮化硼涂料。
20.优选的,步骤d)中,所述在线过滤为双级过滤;其中,一级过滤板的孔隙密度≥
40ppi,二级过滤板的孔隙密度≥50ppi。
21.优选的,步骤e)中,所述铸造过程的流盘末端熔体温度为690℃~710℃。
22.优选的,步骤f)中,所述均热的方式为双级均热;其中,一级均热的温度为420~460℃,时间为2~6h;二级均热的温度为500~550℃,时间为2~6h。
23.优选的,步骤f)中,所述机加工的方式包括锯切和铣面。
24.与现有技术相比,本发明提供了一种5056铝合金铸锭的制备方法。本发明提供的制备方法包括以下步骤:a)将除mg之外的5056铝合金原料装炉熔炼,扒渣,然后向炉内加入mg锭继续熔炼,得到5056铝合金熔体;分别在除mg之外的5056铝合金原料装炉完毕后、进行扒渣前和mg锭加入完毕后对炉内物料表面进行熔剂覆盖;所述装炉熔炼的温度为750~760℃;所述加入mg锭继续熔炼的温度比所述装炉熔炼的温度低5~20℃;b)将所述5056铝合金熔体进行搅拌,得到搅拌后熔体;c)将所述搅拌后熔体在混合气体气氛中进行精炼,得到精炼后熔体;所述混合气体的成分包括氩气与氯气;所述精炼的温度为720~750℃;所述精炼的时间为30~45min;d)将所述精炼后熔体依次进行在线除气和在线过滤,得到在线处理后熔体;所述在线除气的方式为旋转喷吹除气;所述旋转喷吹除气所用除气装置的转子转速为300~400转/min;所述旋转喷吹除气的吹气压力为0.1mpa~0.3mpa;所述旋转喷吹除气所用除气装置每根转子的气体流量为3000~5000l/h;e)将所述在线处理后熔体进行铸造,得到铸锭粗品;f)将所述铸锭粗品依次进行均热和机加工,得到5056铝合金铸锭。在本发明中,首先在熔炼过程中选择适宜的熔炼温度及mg锭的加入时机,能够显著降低熔体中的氢含量;同时在熔炼过程中在熔体表面使用熔剂均匀覆盖,将熔体表面形成的致密氧化膜破碎为细小颗粒并且将其吸入熔剂层,进一步降低熔体中的氢含量,并可以有效去除熔体中的氧化夹杂物;熔体熔化后优选使用电磁搅拌方式对熔体进行搅拌,在保证熔体化学成分均匀性的同时,可以避免机械搅拌带入熔体的硅、铁等杂质元素,从而最大程度上保证熔体的纯净度;在精炼过程中采用氩气和氯气的混合气体作为精炼介质,并选择适宜的精炼温度和实际,可进一步降低了熔体中的液态氢含量,同时提高了熔体的纯净度;在在线除气的过程中,除气装置选择合适的气体压力、气体流量与转子转速,将混合气体剪切为更为细小的气泡,进一步除去熔体的氢气和碱金属元素;在在线除气与在线过滤的过程中,表面在过滤装置内优选喷涂氮化喷涂料,防止内壁沾铝,同时优选使用40ppi 50ppi过滤板对熔体进行过滤,最大程度上保证了熔体的纯净度;在铸造的过程中优选严格控制流盘末端熔体温度,有效避免化合物、氧化夹渣等缺陷。总而言之,本发明提供的技术方案通过对各制备阶段进行严格控制,有效避免了铝合金铸锭制备过程中存在的氢含量较高、氧化膜多以及含钛夹杂物等问题,使最终制备得到的5056铝合金铸锭具有极低的氢含量和较高的纯净度,可以满足制备航天用铝蜂窝芯材的要求。
具体实施方式
25.下面对本发明实施例中的技术方案进行清楚、完整地描述,显然,所描述的实施例仅仅是本发明一部分实施例,而不是全部的实施例。基于本发明中的实施例,本领域普通技术人员在没有做出创造性劳动前提下所获得的所有其他实施例,都属于本发明保护的范围。
26.本发明提供了一种5056铝合金铸锭的制备方法,包括以下步骤:
27.a)将除mg之外的5056铝合金原料装炉熔炼,扒渣,然后向炉内加入mg锭继续熔炼,得到5056铝合金熔体;
28.b)将所述5056铝合金熔体进行搅拌,得到搅拌后熔体;
29.c)将所述搅拌后熔体在混合气体气氛中进行精炼,得到精炼后熔体;
30.d)将所述精炼后熔体依次进行在线除气和在线过滤,得到在线处理后熔体;
31.e)将所述在线处理后熔体进行铸造,得到铸锭粗品;
32.f)将所述铸锭粗品依次进行均热和机加工,得到5056铝合金铸锭。
33.在本发明提供的制备方法中,步骤a)中,所述5056铝合金原料的成分包括:si、fe、cu、mn、mg、cr、zn、ti和al;其中,所述si的含量优选为0.02~0.05wt%,具体可为0.02wt%、0.025wt%、0.03wt%、0.035wt%、0.04wt%、0.045wt%或0.05wt%;所述fe的含量优选为0.1~0.2wt%,具体可为0.1wt%、0.11wt%、0.12wt%、0.13wt%、0.14wt%、0.15wt%、0.16wt%、0.17wt%、0.18wt%、0.19wt%或0.2wt%;所述cu的含量优选为0.05~0.1wt%,具体可为0.05wt%、0.055wt%、0.06wt%、0.065wt%、0.07wt%、0.075wt%、0.08wt%、0.085wt%、0.09wt%、0.095wt%或0.1wt%;所述mn的含量优选为0.15~0.2wt%,具体可为0.15wt%、0.155wt%、0.16wt%、0.165wt%、0.17wt%、0.175wt%、0.18wt%、0.185wt%、0.19wt%、0.195wt%或0.2wt%;所述mg的含量优选为4.5~5wt%,具体可为4.5wt%、4.55wt%、4.6wt%、4.65wt%、4.7wt%、4.72wt%、4.75wt%、4.8wt%、4.85wt%、4.9wt%、4.95wt%、4.98wt%或5wt%;所述cr的含量优选为0.1~0.2wt%,具体可为0.1wt%、0.11wt%、0.12wt%、0.13wt%、0.14wt%、0.15wt%、0.16wt%、0.17wt%、0.18wt%、0.19wt%或0.2wt%;所述zn的含量优选为0.005~0.02wt%,具体可为0.005wt%、0.006wt%、0.007wt%、0.008wt%、0.009wt%、0.01wt%、0.012wt%、0.015wt%、0.017wt%或0.02wt%;所述ti的含量优选为0.005~0.02wt%,具体可为0.005wt%、0.006wt%、0.007wt%、0.008wt%、0.009wt%、0.01wt%、0.012wt%、0.015wt%、0.017wt%或0.02wt%;所述al的含量优选为余量。
34.在本发明提供的制备方法中,步骤a)中,所述5056铝合金原料中的al优选为原铝锭(即,非废料及复化料);所述原铝锭的品味≥99.90%。
35.在本发明提供的制备方法中,步骤a)中,分别在除mg之外的5056铝合金原料装炉完毕后、进行扒渣前和mg锭加入完毕后对炉内物料表面进行熔剂覆盖。在本发明中,所述熔剂的成分优选包括kcl、mgcl2、bacl2和cacl2,其中,所述kcl在熔剂中的含量优选为35~45wt%,更优选为40wt%,所述mgcl2在熔剂中的含量优选为40~50wt%,更优选为46wt%,所述bacl2在熔剂中的含量优选为5~10wt%,更优选为8wt%,所述cacl2在熔剂中的含量优选为≤8wt%,更优选为余量。在本发明中,所述熔剂在步骤a)中的合计使用量优选为1~5kg/tal(吨.铝),具体可为1kg/tal、1.5kg/tal、2kg/tal、2.5kg/tal、3kg/tal、3.5kg/tal、4kg/tal、4.5kg/tal或5kg/tal;其分别在原料装炉完毕后、进行扒渣前和mg锭加入完毕后的使用量独立地优选为0.3~2kg/tal,具体可为0.3kg/tal、0.5kg/tal、0.7kg/tal、1kg/tal、1.3kg/tal、1.5kg/tal、1.7kg/tal或2kg/tal。
36.在本发明提供的制备方法中,步骤a)中,所述装炉熔炼的温度优选为750~760℃,具体可为750℃、751℃、752℃、753℃、754℃、755℃、756℃、757℃、758℃、759℃或760℃;所述加入mg锭继续熔炼的温度比所述装炉熔炼的温度低5~20℃,具体可低5℃、6℃、7℃、8
℃、9℃、10℃、11℃、12℃、13℃、14℃、15℃、16℃、17℃、18℃、19℃或20℃。
37.在本发明提供的制备方法中,步骤b)中,所述搅拌方式包括但不限于电磁搅拌和/或机械搅拌,优选为电磁搅拌。
38.在本发明提供的制备方法中,步骤c)中,所述混合气体的成分包括氩气与氯气;所述氩气中的水和氧含量优选均≤15ppm;所述氩气在混合气体中的含量优选为85~90wt%,具体可为85wt%、86wt%、87wt%、88wt%、89wt%或90wt%;所述氯气中的水含量优选≤500ppm;所述氯气在混合气体中的含量优选为10~15wt%,具体可为10wt%、11wt%、12wt%、13wt%、14wt%或15wt%。
39.在本发明提供的制备方法中,步骤c)中,所述精炼的温度为720~750℃,具体可为720℃、723℃、725℃、727℃、730℃、732℃、735℃、737℃、740℃、742℃、745℃、747℃或750℃;所述精炼的时间为30~45min,具体可为30min、31min、32min、33min、34min、35min、36min、37min、38min、39min、40min、41min、42min、43min、44min或45min。
40.在本发明提供的制备方法中,步骤c)中,在进行精炼之前,优选先向所述搅拌后熔体中加入熔剂。其中,所述熔剂的成分优选包括kcl、mgcl2、bacl2和cacl2,所述kcl在熔剂中的含量优选为35~45wt%,更优选为40wt%,所述mgcl2在熔剂中的含量优选为40~50wt%,更优选为46wt%,所述bacl2在熔剂中的含量优选为5~10wt%,更优选为8wt%,所述cacl2在熔剂中的含量优选为≤8wt%,更优选为余量;所述熔剂的使用量优选为0.5~3kg/tal,具体可为0.5kg/tal、1kg/tal、1.5kg/tal、2kg/tal、2.5kg/tal或3kg/tal。
41.在本发明提供的制备方法中,步骤c)中,完成精炼之后,优选在所述精炼后熔体表面覆盖熔剂并进行静置。其中,所述熔剂的成分优选包括kcl、mgcl2、bacl2和cacl2,所述kcl在熔剂中的含量优选为35~45wt%,更优选为40wt%,所述mgcl2在熔剂中的含量优选为40~50wt%,更优选为46wt%,所述bacl2在熔剂中的含量优选为5~10wt%,更优选为8wt%,所述cacl2在熔剂中的含量优选为≤8wt%,更优选为余量;所述熔剂的使用量优选为0.5~3kg/tal,具体可为0.5kg/tal、1kg/tal、1.5kg/tal、2kg/tal、2.5kg/tal或3kg/tal;所述静置的时间优选为20~60min,具体可为20min、25min、30min、35min、40min、45min、50min、55min或60min。
42.在本发明提供的制备方法中,步骤d)中,所述在线除气的方式为旋转喷吹除气;所述旋转喷吹除气所用除气装置的转子转速为300~400转/min,具体可为300转/min、310转/min、320转/min、330转/min、340转/min、350转/min、360转/min、370转/min、380转/min、390转/min或400转/min;所述旋转喷吹除气的喷吹压力为0.1mpa~0.3mpa,具体可为0.1mpa、0.12mpa、0.15mpa、0.18mpa、0.2mpa、0.23mpa、0.25mpa、0.27mpa或0.3mpa;所述旋转喷吹除气所用除气装置每根转子的气体流量为3000~5000l/h,具体可为3000l/h、3200l/h、3500l/h、3700l/h、4000l/h、4200l/h、4500l/h、4700l/h或5000l/h。
43.在本发明提供的制备方法中,步骤d)中,所述在线过滤所使用的过滤装置内表面优选喷涂有氮化硼涂料;所述过滤装置优选为过滤盆。
44.在本发明提供的制备方法中,步骤d)中,所述在线过滤优选为双级过滤;其中,一级过滤板的孔隙密度优选≥40ppi,二级过滤板的孔隙密度优选≥50ppi。
45.在本发明提供的制备方法中,步骤e)中,所述铸造的温度优选为700~750℃,更优选为715~735℃;所述铸造的速度优选为30~60mm/min,更优选为40~50mm/min;所述铸造
过程中每个结晶器(即,每根铸锭)的水流量优选为70~80m3/h,具体可为70m3/h、71m3/h、72m3/h、73m3/h、74m3/h、75m3/h、76m3/h、77m3/h、78m3/h、79m3/h或80m3/h;所述铸造过程的流盘末端熔体温度优选为690℃~710℃,具体可为690℃、691℃、692℃、693℃、694℃、695℃、696℃、697℃、698℃、699℃、700℃、701℃、702℃、703℃、704℃、705℃、706℃、707℃、708℃、709℃或710℃。
46.在本发明提供的制备方法中,步骤f)中,所述均热的方式优选为双级均热;其中,一级均热的温度优选为420~460℃,具体可为420℃、425℃、430℃、435℃、440℃、445℃、450℃、455℃或460℃;一级均热的时间优选为2~6h,具体可为2h、2.5h、3h、3.5h、4h、4.5h、5h、5.5h或6h;二级均热的温度优选为500~550℃,具体可为500℃、505℃、510℃、515℃、520℃、525℃、530℃、535℃、540℃、545℃或550℃;二级均热的时间优选为2~6h,具体可为2h、2.5h、3h、3.5h、4h、4.5h、5h、5.5h或6h。
47.在本发明提供的制备方法中,步骤f)中,所述机加工的方式包括锯切和铣面。
48.在本发明提供的技术方案中,首先在熔炼过程中选择适宜的熔炼温度及mg锭的加入时机,能够显著降低熔体中的氢含量;同时在熔炼过程中在熔体表面使用熔剂均匀覆盖,将熔体表面形成的致密氧化膜破碎为细小颗粒并且将其吸入熔剂层,进一步降低熔体中的氢含量,并可以有效去除熔体中的氧化夹杂物;熔体熔化后优选使用电磁搅拌方式对熔体进行搅拌,在保证熔体化学成分均匀性的同时,可以避免机械搅拌带入熔体的硅、铁等杂质元素,从而最大程度上保证熔体的纯净度;在精炼过程中采用氩气和氯气的混合气体作为精炼介质,并选择适宜的精炼温度和实际,可进一步降低了熔体中的液态氢含量,同时提高了熔体的纯净度;在在线除气的过程中,除气装置选择合适的气体压力、气体流量与转子转速,将混合气体剪切为更为细小的气泡,进一步除去熔体的氢气和碱金属元素;在在线除气与在线过滤的过程中,表面在过滤装置内优选喷涂氮化喷涂料,防止内壁沾铝,同时优选使用40ppi 50ppi过滤板对熔体进行过滤,最大程度上保证了熔体的纯净度;在铸造的过程中优选严格控制流盘末端熔体温度,有效避免化合物、氧化夹渣等缺陷。
49.总而言之,本发明提供的技术方案通过对各制备阶段进行严格控制,有效避免了铝合金铸锭制备过程中存在的氢含量较高、氧化膜多以及含钛夹杂物等问题,使最终制备得到的5056铝合金铸锭具有极低的氢含量和较高的纯净度,可以满足制备航天用铝蜂窝芯材的要求。
50.为更清楚起见,下面通过以下实施例进行详细说明。
51.在本发明的下述实施例中,所使用的2#熔剂的成分为:40wt%的kcl、46wt%的mgcl2、8wt%的bacl2、余量的cacl2。
52.实施例1
53.配料:要求使用al99.90%品味的原铝锭,且原铝锭使用量100%,不使用废料及复化料,以控制熔体中的硅、铁、钛、钒含量,保证最终熔炼后的熔体的纯净度;配料后的原料包括:0.04wt%的si、0.13wt%的fe、0.07wt%的cu、0.15wt%的mn、4.98wt%的mg、0.12wt%的cr、0.01wt%的zn、0.01wt%的ti与余量的铝。
54.熔炼:将除mg之外的上述原料在熔炼炉中进行熔炼,熔炼温度为760℃;待熔体熔化完后进行扒渣,接着向炉内加入mg锭继续熔炼,加入mg锭继续熔炼的温度控制在750℃;装炉后、扒渣前及加镁后采用2#熔剂覆盖,熔剂合计使用量为3kg/tal,每次的使用量为
1kg/tal。
55.搅拌:在进行炉内物料全部熔化之后对熔体进行搅拌,所述搅拌方式为电磁搅拌,在保证熔体化学成分均匀性的同时,可以避免机械搅拌带入熔体的硅、铁等杂质元素,最大程度上保证熔体的纯净度。
56.静置炉内处理:熔炼炉中的熔体导入静置炉后即可进行精炼,在熔体导入时均匀的加入2#熔剂,加入量为1.5kg/tal,静置炉内采用hd2000除气装置和“t”型精炼器进行精炼,精炼介质为ar cl2(ar:88wt%,cl2:12wt%)混合气体精炼,其中氩气水、氧含量均要求≤15ppm,氯气中水蒸气含量≤500ppm,精炼时间40分钟,精炼温度为742℃,精炼气泡要求不超过80mm;精炼后在熔体表面均匀撒如2#熔剂进行覆盖,熔剂用量为1.5kg/tal,然后静置30min。
57.在线处理:对精炼后的熔体依次进行在线除气和在线过滤,在线除气采用旋转喷吹法除气,使用一台除气装置,除气装置的转子转速为350转/min,气体压力为0.18mpa,每根转子的气体流量为3500l/h,通过炉内在线除气,熔体液态氢含量控制在0.109ml/100gal,na元素含量控制在2ppm;在线过滤采用40ppi 50ppi过滤板,过滤盆内表面喷涂氮化硼涂料,最大程度上保证了熔体的纯净度。
58.铸造:将在线过滤后的熔体进行铸造,得到400mm
×
1120mm规格的方铸锭;铸造过程中通过温度自动调节,控制流盘末端熔体温度为700℃,在抑制化合物的产生同时也能降低氧化渣的产生;铸造过程中的其他参数详见表1。
59.表1实施例1~4涉及的参数数据表
[0060][0061]
均热:将铸造成型后得到的400mm
×
1120mm规格方铸锭进行双级均热制度,一级均热的温度为435℃~445℃,保温时间为4h,二级均热的温度为520℃~530℃,保温时间为4h。
[0062]
机加工:将均热后的方铸锭浇口部锯切300mm,底部锯切400mm,大面单面铣面15mm,小面及转角铣面约15~17mm,可以有效的提高铸锭表面质量,减少轧制开裂和探伤缺陷;铣面后的铸锭表面应无气孔、缩孔、裂纹、成层、夹渣、腐蚀等缺陷,以及无锯屑、油污、灰尘等脏物。
[0063]
将本实施例制备的5056铝合金铸锭进行低倍及断口检测:一级氧化膜和一级疏松,无裂纹、气孔、夹杂物、白斑、晶层分裂、光晶、花边、初晶(一次晶、金属化合物或粗大化合物、化合物偏析),晶粒度≤2级(国家8级晶粒度标准);高倍检测:无过烧。将制备的方铸锭进行轧制,得到的0.018mm5056铝合金超薄铝箔能满足制备航天用铝蜂窝芯材的要求。
[0064]
实施例2
[0065]
配料:要求使用al99.90%品味的原铝锭,且原铝锭使用量100%,不使用废料及复
化料,以控制熔体中的硅、铁、钛、钒含量,保证最终熔炼后的熔体的纯净度;配料后的原料包括:0.05wt%的si、0.20wt%的fe、0.10wt%的cu、0.20wt%的mn、4.60wt%的mg、0.18wt%的cr、0.01wt%的zn、0.01wt%的ti与余量的铝。
[0066]
熔炼:将除mg之外的上述原料在熔炼炉中进行熔炼,熔炼温度为755℃;待熔体熔化完后进行扒渣,接着向炉内加入mg锭继续熔炼,加入mg锭继续熔炼的温度控制在740℃;装炉后、扒渣前及加镁后采用2#熔剂覆盖,熔剂合计使用量为3kg/tal,每次的使用量为1kg/tal。
[0067]
搅拌:在进行炉内物料全部熔化之后对熔体进行搅拌,所述搅拌方式为电磁搅拌,在保证熔体化学成分均匀性的同时,可以避免机械搅拌带入熔体的硅、铁等杂质元素,最大程度上保证熔体的纯净度。
[0068]
静置炉内处理:熔炼炉中的熔体导入静置炉后即可进行精炼,在熔体导入时均匀的加入2#熔剂,加入量为1.5kg/tal,静置炉内采用hd2000除气装置和“t”型精炼器进行精炼,精炼介质为ar cl2(ar:88wt%,cl2:12wt%)混合气体精炼,其中氩气水、氧含量均要求≤15ppm,氯气中水蒸气含量≤500ppm,精炼时间35分钟,精炼温度为735℃,精炼气泡要求不超过80mm;精炼后在熔体表面均匀撒如2#熔剂进行覆盖,熔剂用量为1.5kg/tal,然后静置30min。
[0069]
在线处理:对精炼后的熔体依次进行在线除气和在线过滤,在线除气采用旋转喷吹法除气,使用一台除气装置,除气装置的转子转速为330转/min,气体压力为0.25mpa,每根转子的气体流量为4000l/h,通过在线除气,可以将熔体液态氢含量控制在0.101ml/100gal,na元素含量控制在3ppm;在线过滤采用40ppi 50ppi过滤板,过滤盆内表面喷涂氮化硼涂料,最大程度上保证了熔体的纯净度。
[0070]
铸造:将在线过滤后的熔体进行铸造,得到510mm
×
1400mm规格的方铸锭;铸造过程中通过温度自动调节,控制流盘末端熔体温度为695℃,在抑制化合物的产生同时也能降低氧化渣的产生;铸造过程中的其他参数详见表1。
[0071]
均热:将铸造成型后得到的510mm
×
1400mm规格方铸锭进行双级均热制度,一级均热的温度为435℃~445℃,保温时间为4h,二级均热的温度为520℃~530℃,保温时间为5h。
[0072]
机加工:将均热后的方铸锭浇口部锯切300mm,底部锯切400mm,大面单面铣面15mm,小面及转角铣面约15~17mm,可以有效的提高铸锭表面质量,减少轧制开裂和探伤缺陷。铣面后的铸锭表面应无气孔、缩孔、裂纹、成层、夹渣、腐蚀等缺陷,以及无锯屑、油污、灰尘等脏物。
[0073]
将本实施例制备的5056铝合金铸锭进行低倍及断口检测:一级氧化膜和一级疏松,无裂纹、气孔、夹杂物、白斑、晶层分裂、光晶、花边、初晶(一次晶、金属化合物或粗大化合物、化合物偏析),晶粒度≤2级(国家8级晶粒度标准);高倍检测:无过烧。将制备的方铸锭进行轧制,得到的0.018mm5056铝合金超薄铝箔能满足制备航天用铝蜂窝芯材的要求。
[0074]
实施例3
[0075]
配料:要求使用al99.95%品味的原铝锭,且原铝锭使用量100%,不使用废料及复化料,以控制熔体中的硅、铁、钛、钒含量,保证最终熔炼后的熔体的纯净度;配料后的原料包括:0.02wt%的si、0.15wt%的fe、0.08wt%的cu、0.17wt%的mn、4.80wt%的mg、
0.15wt%的cr、0.01wt%的zn、0.01wt%的ti与余量的铝。
[0076]
熔炼:将除mg之外的上述原料在熔炼炉中进行熔炼,熔炼温度为750℃;待熔体熔化完后进行扒渣,接着向炉内加入mg锭继续熔炼,加入mg锭继续熔炼的温度控制在745℃;装炉后、扒渣前及加镁后采用2#熔剂覆盖,熔剂合计使用量为3kg/tal,每次的使用量为1kg/tal。
[0077]
搅拌:在进行炉内物料全部熔化之后对熔体进行搅拌,所述搅拌方式为电磁搅拌,在保证熔体化学成分均匀性的同时,可以避免机械搅拌带入熔体的硅、铁等杂质元素,最大程度上保证熔体的纯净度。
[0078]
静置炉内处理:熔炼炉中的熔体导入静置炉后即可进行精炼,在熔体导入时均匀的加入2#熔剂,加入量为1.5kg/tal,静置炉内采用hd2000除气装置和“t”型精炼器进行精炼,精炼介质为ar cl2(ar:88wt%,cl2:12wt%)混合气体精炼,其中氩气水、氧含量均要求≤15ppm,氯气中水蒸气含量≤500ppm,精炼时间40分钟,精炼温度为730℃,精炼气泡要求不超过80mm;精炼后在熔体表面均匀撒如2#熔剂进行覆盖,熔剂用量为1.5kg/tal,然后静置40min。
[0079]
在线处理:对精炼后的熔体依次进行在线除气和在线过滤,在线除气采用旋转喷吹法除气,使用一台除气装置,除气装置的转子转速为350转/min,气体压力为0.15mpa,每根转子的气体流量为5000l/h,通过在线除气,可以将熔体液态氢含量控制在0.095ml/100gal,na元素含量控制在3ppm;在线过滤采用40ppi 50ppi过滤板,过滤盆内表面喷涂氮化硼涂料,最大程度上保证了熔体的纯净度。
[0080]
铸造:将在线过滤后的熔体进行铸造,得到400mm
×
1620mm规格的方铸锭;铸造过程中通过温度自动调节,控制流盘末端熔体温度为698℃,在抑制化合物的产生同时也能降低氧化渣的产生;铸造过程中的其他参数详见表1。
[0081]
均热:将铸造成型后得到的400mm
×
1620mm规格方铸锭进行双级均热制度,一级均热的温度为435℃~445℃,保温时间为4h,二级均热的温度为520℃~530℃,保温时间为5h。
[0082]
机加工:将均热后的方铸锭浇口部锯切300mm,底部锯切400mm,大面单面铣面15mm,小面及转角铣面约15~17mm,可以有效的提高铸锭表面质量,减少轧制开裂和探伤缺陷;铣面后的铸锭表面应无气孔、缩孔、裂纹、成层、夹渣、腐蚀等缺陷,以及无锯屑、油污、灰尘等脏物。
[0083]
将本实施例制备的5056铝合金铸锭进行低倍及断口检测:一级氧化膜和一级疏松,无裂纹、气孔、夹杂物、白斑、晶层分裂、光晶、花边、初晶(一次晶、金属化合物或粗大化合物、化合物偏析),晶粒度≤2级(国家8级晶粒度标准);高倍检测:无过烧。将制备的方铸锭进行轧制,得到的0.018mm5056铝合金超薄铝箔能满足制备航天用铝蜂窝芯材的要求。
[0084]
实施例4
[0085]
配料:要求使用al99.95%品味的原铝锭,且原铝锭使用量100%,不使用废料及复化料,以控制熔体中的硅、铁、钛、钒含量,保证最终熔炼后的熔体的纯净度;配料后的原料包括:0.03wt%的si、0.20wt%的fe、0.09wt%的cu、0.18wt%的mn、4.720wt%的mg、0.14wt%的cr、0.01wt%的zn、0.01wt%的ti与余量的铝。
[0086]
熔炼:将除mg之外的上述原料在熔炼炉中进行熔炼,熔炼温度为755℃;待熔体熔
化完后进行扒渣,接着向炉内加入mg锭继续熔炼,加入mg锭继续熔炼的温度控制在735℃;装炉后、扒渣前及加镁后采用2#熔剂覆盖,熔剂合计使用量为3kg/tal,每次的使用量为1kg/tal。
[0087]
搅拌:在进行炉内物料全部熔化之后对熔体进行搅拌,所述搅拌方式为电磁搅拌,在保证熔体化学成分均匀性的同时,可以避免机械搅拌带入熔体的硅、铁等杂质元素,最大程度上保证熔体的纯净度。
[0088]
静置炉内处理:熔炼炉中的熔体导入静置炉后即可进行精炼,在熔体导入时均匀的加入2#熔剂,加入量为1.5kg/tal,静置炉内采用hd2000除气装置和“t”型精炼器进行精炼,精炼介质为ar cl2(ar:88wt%,cl2:12wt%)混合气体精炼,其中氩气水、氧含量均要求≤15ppm,氯气中水蒸气含量≤500ppm,精炼时间30分钟,精炼温度为725℃,精炼气泡要求不超过80mm;精炼后在熔体表面均匀撒如2#熔剂进行覆盖,熔剂用量为1.5kg/tal,然后静置40min。
[0089]
在线处理:对精炼后的熔体依次进行在线除气和在线过滤,在线除气采用旋转喷吹法除气,使用一台除气装置,除气装置的转子转速为380转/min,气体压力为0.15mpa,每根转子的气体流量为4500l/h,通过在线除气,可以将熔体液态氢含量控制在0.092ml/100gal,na元素含量控制在2ppm;在线过滤采用40ppi 50ppi过滤板,过滤盆内表面喷涂氮化硼涂料,最大程度上保证了熔体的纯净度。
[0090]
铸造:将在线过滤后的熔体进行铸造,得到510mm
×
1100mm规格的方铸锭;铸造过程中通过温度自动调节,控制流盘末端熔体温度为700℃,在抑制化合物的产生同时也能降低氧化渣的产生;铸造过程中的其他参数详见表1。
[0091]
均热:将铸造成型后得到的510mm
×
1100mm规格方铸锭进行双级均热制度,一级均热的温度为435℃~445℃,保温时间为4h,二级均热的温度为520℃~530℃,保温时间为5h。
[0092]
机加工:将均热后的方铸锭浇口部锯切300mm,底部锯切400mm,大面单面铣面15mm,小面及转角铣面约15~17mm,可以有效的提高铸锭表面质量,减少轧制开裂和探伤缺陷;铣面后的铸锭表面应无气孔、缩孔、裂纹、成层、夹渣、腐蚀等缺陷,以及无锯屑、油污、灰尘等脏物。
[0093]
将本实施例制备的5056铝合金铸锭进行低倍及断口检测:一级氧化膜和一级疏松,无裂纹、气孔、夹杂物、白斑、晶层分裂、光晶、花边、初晶(一次晶、金属化合物或粗大化合物、化合物偏析),晶粒度≤2级(国家8级晶粒度标准);高倍检测:无过烧。将制备的方铸锭进行轧制,得到的0.018mm5056铝合金超薄铝箔能满足制备航天用铝蜂窝芯材的要求。
[0094]
以上所述仅是本发明的优选实施方式,应当指出,对于本技术领域的普通技术人员来说,在不脱离本发明原理的前提下,还可以做出若干改进和润饰,这些改进和润饰也应视为本发明的保护范围。
再多了解一些
本文用于企业家、创业者技术爱好者查询,结果仅供参考。