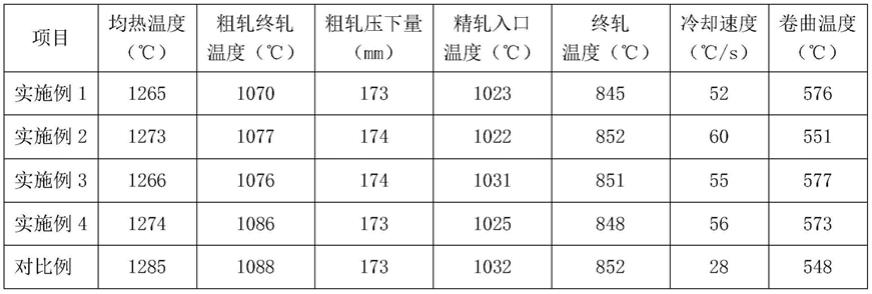
1.本发明涉及一种钢铁生产方法,特别是一种基于超快冷工艺的集装箱鹅颈槽用板带耐候钢产品的制造方法。
背景技术:
2.集装箱及其运输让全球各个角落的产品轻松登录全球各地,是全球贸易流的重要承载工具,在国际贸易和世界经济中发挥了不可或缺的作用。中国已连续多年蝉联世界集装箱产销量第一,形成了完整的、标准化程度高度统一的集装箱制造产业链。
3.集装箱制造中,鹅颈槽是最为特殊的一个零部件,为保障鹅颈槽用板带产品满足集装箱制造的技术要求,因此对所采用的spa-h板带产品性能要求高,需要厚度厚,宽度大,加工成型复杂且加工后尺寸精度保持稳定,无回弹。在鹅颈槽用板带生产时通过加入大量合金cu、cr、ni来改善产品组织性能,这也造成板带产品制造成本大幅升高。例如专利《一种无p偏析的耐候钢热轧薄带及其制造方法》(cn201410591781.6)公布了一种耐候钢,成分为c:0.07~0.12%;si:0.30~0.50%;mn:0.4~0.55%;p:0.06~0.15%;s:≤0.02%且大于0;cr:0.6~0.8%;ni:0.03~0.11%;cu:0.2~0.5%;al:≤0.046%且大于0;b:≤0.003%且大于0;可生产屈服强度≥390mpa,抗拉强度≥490mpa,断后延伸率≥21%,但是其合金元素加入较多cr:0.6%~0.8%,且需要加入b元素,合金成本较高。并且cr在 6价状态下严重危害人的身体健康,有巨大毒性,为了降低cr含量,不得不添加其他合金元素,导致生产成本增加。
4.此外,现有spa-h板带还存在鹅颈槽加工过程中因强度不均,造成边部90
°
折弯加工后回弹角度>5
°
的技术缺陷,不满足后续组装焊接装配尺寸要求。
技术实现要素:
5.本发明的技术任务是针对以上现有技术的不足,提供一种集装箱鹅颈槽用板带耐候钢产品的制造方法,通过新的层流冷却工艺和成分体系设计,使鹅颈槽用耐候钢规格带钢宽度方向上性能更均匀,屈强比更低,以解决客户加工使用过程中折弯回弹造成的装配精度不满足装配尺寸要求,效率降低的问题。
6.本发明解决其技术问题的技术方案是:一种集装箱鹅颈槽用板带耐候钢产品的制造方法,工序包含转炉
→
lf炉精炼
→
连铸
→
铸坯热送轧钢加热炉
→
轧制
→
冷却
→
卷取,其特征在于:所述的冷却分超快冷段和层流冷却段两段冷却模式;超快冷冷速50-60℃/s,层流冷却出口温度设定在550-580℃。
7.上述的耐候钢产品化学成份及质量百分比为:c:0.08%~0.11%,si:0.20%~0.35%,mn:0.45%~0.55%,p:0.075%~0.090%,s≤0.010%,cu:0.26%~0.32%,cr:0.35%~0.42%,ni:0.09%~0.13%,余量为fe和不可避免杂质。
8.上述超快冷段设置四组冷却集管,每组集管开6闭4组水。
9.上述超快冷段超快冷压力设定值0.5mpa中压模式,上下水比0.7。
10.上述超快冷段出口温度630-650℃。
11.与现有技术相比较,本发明具有以下突出的有益效果:
12.1、本发明采用低铜、低铬合金成分设计,在保证性能的前提下,降低了生产成本;
13.2、采取了超快冷专用工艺,优化加热、轧制、层冷工艺,以获得屈服强度均匀的耐候钢产品(屈服强度≥355mpa,抗拉强度≥490mpa,延伸率≥22%),生产出性能合格、表面质量满足集装箱制造,满足jis3125标准要求和客户后期加工中折弯回弹的要求,折弯回弹角度≤2
°
;
14.3、实现了4.0-4.5x1390-1400mm尺寸范围的集装箱鹅颈槽用耐候钢在常规热连轧生产线的批量稳定生产,单次轧程可连续生产1200吨以上,成材率达到97.5%以上;
15.4、实现了集装箱鹅颈槽用耐候钢极限负差生产,集装箱成箱率达到107.5%以上,在满足集装箱鹅颈槽加工和使用性能的情况下节约钢材3%。
具体实施方式
16.下面结合具体实施方式对本发明进一步说明。
17.本发明通过新的成分和冷却工艺设计,提供一种基于超快冷工艺的集装箱鹅颈槽用板带产品的轧制方法,表面质量、板形质量稳定,性能满足标准且加工回弹量小,可批量稳定生产的轧制方法。
18.本发明公开的集装箱鹅颈槽用板带耐候钢成分体系,化学成份及质量百分比为:c:0.08%~0.11%,si:0.20%~0.35%,mn:0.45%~0.55%,p:0.075%~0.090%,s≤0.010%,cu:0.26%~0.32%,cr:0.35%~0.42%,ni:0.09%~0.13%,余量为fe和不可避免杂质。
19.c:能够提高强度,是主要的间隙固溶强化元素,可大幅度提高钢材的强度。但是c含量过高会显著恶化钢的焊接性能、冷成型性能和冲击韧性,同时将造成回弹过大等问题,并且会促进珠光体转变,降低钢的耐大气腐蚀性能,c含量较高时还会在板坯连铸过程中,铁水凝固时发生包晶反应,容易在板坯表面产生裂纹,影响成品表面质量。本发明采用低c设计,c含量为0.08~0.11%;优化方案中为0.08~0.09%。
20.si:既可通过固溶强化提高钢的强度,适量的硅能够抑制锰和磷的偏聚,也可提高钢的耐大气腐蚀性能,低于0.20%时,冶炼成本增加,高于0.30%时,易导致热轧钢板表面粗糙,因此本发明中si含量为0.20~0.35%;优化方案中为0.31~0.33%。
21.mn:不仅可以通过固溶强化提高强度,而且可以降低钢的相变温度,细化晶粒,提高钢的低温韧性,但mn含量过多会使淬透性增加,导致可焊性和焊接热影响区韧性恶化,同时增加成本,本发明中通过合金搭配,采用相对低锰设计,mn含量为0.45~0.55%;优化方案中为0.49~0.52%。
22.p:是传统耐候钢中主要的合金元素,磷含量过低,耐候性能难以保证,但磷含量过高时,既容易产生高温裂纹,又增加低温裂纹敏感性,使焊缝的延展性和韧性变坏,本发明中p含量为0.075~0.09%;优化方案中为0.079~0.085%。
23.s:是有害元素,生成的硫化物夹杂不仅严重影响钢的力学性能,而且对钢的耐腐蚀性能产生严重的恶化作用,因此应尽可能降低钢种的s含量,使其含量在0.010%以下;优化方案中为0.004~0.005%。
24.cu:是提高钢耐大气腐蚀性能最主要的元素,同时也能提高强度,钢种的cu含量达到0.25%时,能有效提高钢的耐大气腐蚀性能,但含量过高时,在加热过程中,钢表面易产生裂纹,引起铜的热脆,本发明中cu含量为0.26~0.32%;优化方案中为0.26~0.27%。
25.cr对改善钢的钝化能力具有显著效果,可促进表面形成致密的钝化膜或保护性锈层,但过高的cr含量对焊接及韧性不利,本发明中cr含量为0.35~0.42%;优化方案中为0.37~0.39%。
26.ni是提高耐候钢耐海洋大气腐蚀性能的重要合金元素。此外,ni能够细化钢的晶粒,提高钢的低温韧性,有效阻止cu热脆引起的网裂,本发明钢中ni含量设计为0.09~0.13%;优化方案中为0.10~0.11%。
27.现有技术中,cr是提高钢耐大气腐蚀性能最主要的元素,cr含量提高利于细化α-feooh,当锈层/金属界面的α-feooh中cr含量超过5%时,能有效抑制腐蚀性阴离子,特别是cl-离子的侵入,该作用在海洋性环境尤其重要,一般的含量范围为:0.6~0.8%。但同时,cr在 6价状态下易产生毒性,严重危害人的身体健康。因此,生产中多添加nb、ti,以克服了配方中cr含量低造成的强度和耐腐蚀性能的不足,但合金元素添加导致生产成本上扬。因此,cr含量高低之间的取舍矛盾一直是本领域技术的一个难点。本发明技术仅仅通过加入一种ni并配合生产工艺控轧控冷,来实现0.08~0.11%c含量下低cr成分钢板强度和耐腐蚀性能的平衡,保障宽度方向上冷却均匀性,以获得均匀的屈服强度的耐候钢产品。
28.本发明生产工艺,工序包含转炉
→
lf炉精炼
→
连铸
→
铸坯热送轧钢加热炉
→
轧制
→
超快冷冷却
→
层流冷却
→
卷取。
29.s1、转炉、lf炉精炼
30.s2、连铸
31.s3、铸坯加热
32.板坯长度8500-10800mm,宽度1400-1420mm,厚度210mm,在炉时间热坯≥120min,冷坯≥150min,确保均热段温度1220℃~1280℃,保证板坯温度均匀,同板坯温差≤15℃。
33.s4、粗轧
34.粗轧轧制6道次(3 3模式),粗轧终轧温度控制在1060-1100℃,中间坯厚度34-38mm,粗轧压下量172-176mm,粗轧出口投用保温罩,确保中间坯整体温度,减少边部温降。
35.s5、精轧
36.精轧机架间冷却水开2组,工作辊上水切间隙≤1mm,保证轧制过程中板坯温度均匀稳定。
37.精轧开轧温度整体控制在980℃~1050℃,精轧7道次,终轧温度830~860℃。
38.精轧f1~f7压下率分别为34-38%、36-42%、31-35%、24-28%、18-21%、10-13%、7.5-10%,前两道次压下率保证>30%,保证轧后钢板晶粒细化。
39.s6、层冷
40.超快冷工艺设计:冷却段分超快冷段和层流冷却段两段冷却模式,超快冷段设置四组冷却集管,对鹅颈槽用耐候钢采用专用冷却模式,每组集管开6闭4组水,超快冷压力设定值0.5mpa中压模式,上下水比0.7,超快冷冷速50-60℃/s,在4s内,让精轧出口温度830-850℃快速冷速到超快冷出口温度630-650℃,以获得细化的铁素体、珠光体组织,层流冷却出口温度设定在550-580℃。相对于常规层流冷却工艺,以上超快冷工艺的细节设置解决了
宽度方向冷却不均,厚度冷却不透的缺陷。
41.以上工艺,保障宽度方向上冷却均匀性,以获得均匀的屈服强度的耐候钢产品,同卷屈服强度波动幅度降低至10mpa以内,折弯回弹角度≤2
°
。
42.s7、卷取
43.卷取温度550-580℃。
44.本发明通过新的成分设计、超快冷工艺和模型的开发与应用、加热、粗轧、精轧、卷取工序等工艺管控,从而获得性能稳定、回弹量小、批量稳定生产且板形、表面质量好的集装箱鹅颈槽用板带产品。
45.为了更好地比较本技术配方和现有技术,进行了对比试验。
46.实施例1~4采用本发明中的化学成分及工艺技术特征;对比例1的化学成分与实施例2相同,工艺采用传统工艺生产。生产规格范围为厚度4.0-4.5mm,宽度1390-1400mm。
47.实施例1-4和对比例的化学成分(按重量百分比计)如下表所示,余量为铁及不可避免杂质。
48.项目csimnpscucrni实施例10.0920.3240.510.0820.0050.260.390.11实施例20.0890.3130.490.0790.0040.270.380.10实施例30.0930.3320.520.0830.0040.270.390.11实施例40.0940.3310.500.0850.0050.260.370.10对比例0.0890.3130.490.0790.0040.270.380.10
49.实施例1-4和对比例工艺流程路线为:板坯加热
→
粗轧
→
精轧
→
层流冷却(冷却策略为前段)
→
卷取。其主要工艺控制参数见下表。
[0050][0051]
各实施例与对比例产品钢材性能情况见下表。
[0052]
[0053]
从上表的数据可知,实施例1~3生产得到钢材,带钢宽度方向上强度波动幅度由22mpa降低至10mpa以内;90
°
加工成型后回弹角度控制在了2
°
以内,满足jis3125标准要求和客户后期加工中折弯回弹的要求,折弯回弹角度≤2
°
,满足了用户的要求,且折弯机无需再增加2s保持时间,提高了作业效率和后续装配精度。所得钢材轧制表面质量、板形稳定,单次轧程可连续生产1200吨以上,成材率在97.5%以上,实现了集装箱鹅颈槽用耐候钢极限负差生产,集装箱成箱率达到107.5%以上,在满足集装箱鹅颈槽加工和使用性能的情况下节约钢材3%。而对比例即使在成分上和实施例现实的,但是控轧控冷方式不同造成,同为前段冷却,冷却速度低,且冷却方式不同,因此并不能克服宽度大的情况下,宽度方向上的强度波动幅度,并且因材料屈服强度偏高,客户加工过程中出现批量的折弯回弹现象,回弹角度达到5-9
°
,造成后续装配尺寸精度不达标,影响集装箱组装生产节奏。
[0054]
要需要说明的是,本发明的特定实施方案已经对本发明进行了详细描述,对于本领域的技术人员来说,在不背离本发明的精神和范围的情况下对它进行的各种显而易见的改变都在本发明的保护范围之内。
再多了解一些
本文用于企业家、创业者技术爱好者查询,结果仅供参考。