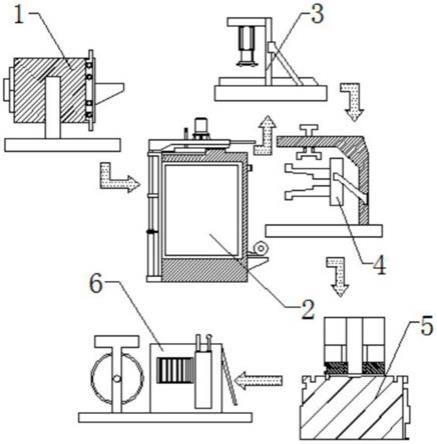
一种超级13cr无缝钢管生产系统
技术领域
1.本实用新型涉及无缝钢管技术领域,具体为一种超级13cr无缝钢管生产系统。
背景技术:
2.125钢级超级13cr合金元素比较高,变形抗力大,热加工温度区间范围窄,属于难变形合金,采用热穿孔轧制工艺生产容易产生粘钢和裂纹缺陷。热挤压工艺是钢管在三向压应力作用下成型,受力条件好,对难变形高合金生产有特殊优势。目前成熟的生产方法是:冶炼铸锭-锻造-退火-锻坯料外扒皮车光-挤压坯内掏孔加工-热挤压成型-调质处理。铸锭锻造要切除冒口,冒口重量约占 20%~25%,锻坯料外扒皮车光单边约7~12mm,挤压坯内掏孔加工直径约35~ 90mm,成材率比较低,生产流程长。连续铸造坯料,无冒口,金属缩孔疏松在坯料中心,与热挤压成型工艺结合,可以减少锻造工序,减少金属损失,提高成材率,有利于提高经济效益。
技术实现要素:
3.本实用新型的目的在于提供一种超级13cr无缝钢管生产系统,以解决上述背景技术中提出的锻坯 挤压工艺中冒口损失严重,金属收得率低,生产工序长的问题。
4.为实现上述目的,本实用新型提供如下技术方案:一种超级13cr无缝钢管生产系统,所述生产系统包括连续铸造机、退火炉、坯料加工设备、扩孔机、热挤压机和热处理机,包括:退火炉,其正上方连接有升降架,且退火炉的外侧开设有炉膛,所述退火炉的外侧嵌套固定有炉壳,所述计量仪贯穿连接在退火炉的顶部,且退火炉的正上方嵌套固定有循环风机;炉盖,其安装在退火炉的正上方,且退火炉的右侧安装固定有炉衬,所述电热丝安装在退火炉的内部,所述退火炉的右侧贯穿连接有冷却风机;挤压模具,其一侧嵌套连接有模中撑,且挤压模具的一侧螺栓固定有模支撑,所述模支撑的一侧设置有模座,且模座的一侧卡合连接有模中垫,所述模中垫的一侧贴合连接有模后垫,所述模座的一侧柱连接有挤压筒中衬,且挤压筒中衬的外侧嵌套连接有挤压筒内衬,所述挤压筒中衬的外侧包裹固定有挤压筒外套,所述挤压筒外套的外侧嵌套固定有挤压筒。
5.优选的,所述退火炉设有升降架、炉膛、炉壳、计量仪、循环风机、炉盖、炉衬、电热丝和冷却风机。
6.优选的,所述热挤压机为63mn卧式挤压机,包括挤压筒和挤压模具,所述挤压筒包括挤压筒外套、挤压筒中衬和挤压筒内衬,所述挤压模具包括模中撑、模支撑、模座、模中垫和模后垫。
7.优选的,所述升降架与循环风机为轴承连接,且升降架的长度大于炉壳的长度。
8.优选的,所述电热丝关于退火炉中心线对称分布,且电热丝与冷却风机为相互平行。
9.与现有技术相比,本实用新型的有益效果是:该超级13cr无缝钢管生产系统;采用连续铸造 热挤压成型的工艺路线,优化了生产过程,将锻坯改为连铸坯,与锻造坯料相比,
减少了冒口的损失,减少了锻造工序,金属收率高、成本低。挤压成型后组织致密,晶粒细小,机械性能好,提高了综合效益。
附图说明
10.图1为本实用新型生产系统流程结构示意图;
11.图2为本实用新型退火炉内部结构示意图;
12.图3为本实用新型热挤压机正剖结构示意图。
13.图中:1、连续铸造机;2、退火炉;3、坯料加工设备;4、扩孔机;5、热挤压机;6、热处理机;7、升降架;8、炉膛;9、炉壳;10、计量仪;11、循环风机;12、炉盖;13、炉衬;14、电热丝;15、冷却风机;16、挤压模具;17、模中撑;18、模支撑;19、挤压筒外套;20、模后垫;21、挤压筒;22、模中垫;23、模座;24、挤压筒内衬;25、挤压筒中衬。
具体实施方式
14.下面将结合本实用新型实施例中的附图,对本实用新型实施例中的技术方案进行清楚、完整地描述,显然,所描述的实施例仅仅是本实用新型一部分实施例,而不是全部的实施例。基于本实用新型中的实施例,本领域普通技术人员在没有做出创造性劳动前提下所获得的所有其他实施例,都属于本实用新型保护的范围。
15.请参阅图1-3,本实用新型提供一种技术方案:一种超级13cr无缝钢管生产系统,生产系统包括连续铸造机1、退火炉2、坯料加工设备3、扩孔机4、热挤压机5和热处理机6,包括:
16.退火炉2,其正上方连接有升降架7,且退火炉2的外侧开设有炉膛8,退火炉2的外侧嵌套固定有炉壳9,计量仪10贯穿连接在退火炉2的顶部,且退火炉2的正上方嵌套固定有循环风机11;
17.炉盖12,其安装在退火炉2的正上方,且退火炉2的右侧安装固定有炉衬 13,电热丝14安装在退火炉2的内部,退火炉2的右侧贯穿连接有冷却风机15;
18.挤压模具16,其一侧嵌套连接有模中撑17,且挤压模具16的一侧螺栓固定有模支撑18,模支撑18的一侧设置有模座23,且模座23的一侧卡合连接有模中垫22,模中垫22的一侧贴合连接有模后垫20,模座23的一侧柱连接有挤压筒中衬25,且挤压筒中衬25的外侧嵌套连接有挤压筒内衬24,挤压筒中衬 25的外侧包裹固定有挤压筒外套19,挤压筒外套19的外侧嵌套固定有挤压筒 21。
19.退火炉2设有升降架7、炉膛8、炉壳9、计量仪10、循环风机11、炉盖 12、炉衬13、电热丝14和冷却风机15。
20.热挤压机5为63mn卧式挤压机,包括挤压筒21和挤压模具16,挤压筒包括挤压筒外套19、挤压筒中衬25和挤压筒内衬24,挤压模具16包括模中撑17、模支撑18、模座23、模中垫22和模后垫20。
21.升降架7与循环风机11为轴承连接,且升降架7的长度大于炉壳9的长度。
22.电热丝14关于退火炉2中心线对称分布,且电热丝14与冷却风机15为相互平行。
23.利用本实用新型生产屈服强度125钢级的超级13cr无缝钢管,规格为φ 177.8mm
×
10.36mm
×
10000mm。生产步骤如下:
24.⑴
坯料制备:运用连续铸造工艺生产超级13cr连铸管坯;管坯的学成分符合表1要求:
25.表1. 177.8mm
×
10.36mm的超级13cr管坯成分化验数据/(质量百分数%)
[0026][0027]
⑵
坯料退火:对连续铸造管坯进行退火,降低其硬度;退火温度750~830℃,保温6h,随炉冷却到400℃以下。
[0028]
⑶
坯料加工:铸坯料的外圆单边加工到358mm,中心孔加工直径65mm,去除表面氧化皮、中心疏松、裂纹。
[0029]
⑷
扩孔前加热:用感应加热炉将机加工后的坯料均匀加热到1150
±
5℃。
[0030]
⑸
坯料热扩孔:加热后坯料首先过高压水除鳞,随后坯料的内壁和外壁分别均匀涂抹玻璃粉;在扩孔筒里进行热扩孔,扩孔筒内径365mm,扩孔头直径 170mm,扩孔速度160~180mm/s。
[0031]
⑹
料挤压前加热:扩孔后坯料过高压水除鳞,挤压前将扩孔后的坯料均匀加热到1170
±
20℃。
[0032]
⑺
坯料挤压:挤压前将坯料的内壁和外壁分别均匀涂抹玻璃粉,在挤压筒里进行挤压,挤压筒内径375mm,挤压模内径182.5mm,芯棒160mm,挤压速度 200~300mm/s,将挤压后的管子缓冷,生产出规格为φ177.8mm
×
10.36mm的挤压荒管。
[0033]
⑻
荒管热处理:钢管均匀加热到980℃,保温1h,然后用吹风快冷,待钢管温度冷却至常温,完成淬火处理;再均匀加热到580℃,保温2.0h,出炉空冷,进行回火处理,得到成品性能125钢级的超级13cr马氏体不锈钢管,增加了整体的实用性。
[0034]
本说明书中未作详细描述的内容属于本领域专业技术人员公知的现有技术。
[0035]
尽管已经示出和描述了本实用新型的实施例,对于本领域的普通技术人员而言,可以理解在不脱离本实用新型的原理和精神的情况下可以对这些实施例进行多种变化、修改、替换和变型,本实用新型的范围由所附权利要求及其等同物限定。
再多了解一些
本文用于企业家、创业者技术爱好者查询,结果仅供参考。