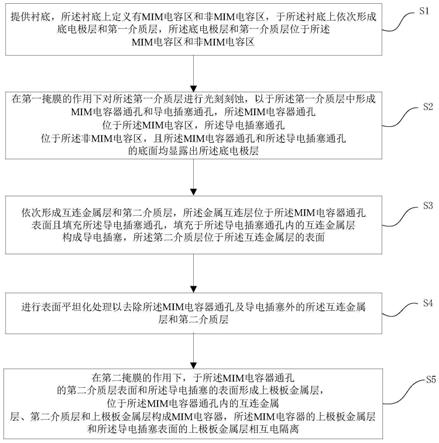
具有mim电容器的半导体器件及其制备方法
技术领域
1.本发明涉及半导体制造技术领域,具体涉及一种具有mim电容器的半导体器件及其制备方法。
背景技术:
2.随着集成电路技术的飞速发展,传统的电容器件已经不能满足射频等电路的需求,金属-绝缘体-金属电容器(metal-insulator-metal,简称mim电容器)成为替代传统电容器的新型电容器件。在器件特征尺寸日益缩小和器件集成度日益提高的环境下,mim电容器因具有电容密度高、电容电压系数小、漏电低等优点而得到越来越广泛的应用。但是当前工艺中金属-绝缘体-金属(mim)电容器制备需额外增加一层掩膜(mask,也称之为光罩,掩膜版),导致成本增加。当前典型的mim电容器的制备工艺流程至少包括如下步骤:
3.提供包括基底层311和介质层312的衬底,所述衬底上定义有mim电容区和非mim电容区,于所述衬底上依次形成下极板金属层32、介质层33和上极板金属层34,该过程可参考图1-3所示(通常在形成下极板金属层32后还需要对下极板金属层32进行刻蚀以形成隔离沟槽,以使位于mim电容区和非mim电容区的下极板金属层32相互电隔离,该隔离沟槽将被后续的介质层33的材质填充);
4.在第一掩膜38的作用下对所述上极板金属层34进行刻蚀,以去除位于所述非mim电容区的上极板金属层;该过程通常为,于所述上极板金属层34上涂布形成光刻胶层39,然后在所述第一掩膜38的作用下对所述光刻胶层39进行曝光显影以定义出所需的图形,之后依残余的光刻胶层对所述上极板金属层进行刻蚀,得到的结构如图4所示;
5.形成层间介质层35,所述层间介质层35覆盖所述mim电容区和非mim电容区,得到的结构如图5所示;
6.在第二掩膜(未示出,第二掩膜的作用过程可参考第一掩膜的作用过程)的作用下于所述层间介质层35内形成第一通孔351和第二通孔352,所述第一通孔351位于所述mim电容区,且显露出所述下极板金属层32,所述第二通孔352位于所述非mim电容区,且显露出所述下极板金属层32,得到的结构如图6所示,可以看到,其第二通孔352需穿过介质层33和层间介质层35,使得第二通孔352需刻蚀得比较深,而通孔越深刻蚀难度越大,越难以确保底部开口打开,同时后续的金属填充难度越大,容易造成填充孔洞(void)而导致器件的电性能下降;
7.形成互连金属层36,所述互连金属层36填充所述第一通孔351和第二通孔352,且延伸到所述层间介质层35的表面,得到的结构如图7所示;
8.在第三掩膜(同样未示出,作用过程参考前述对第一掩膜的作用过程描述)的作用下于所述互连金属层36中形成隔离槽37,以使位于所述mim电容区和非mim电容区的互连金属层37相互电隔离,得到的结构如图8所示,mim电容区的下极板金属层32、介质层33和上极板金属层34构成mim电容器。
9.从上述制备流程可以看到,采用现有的工艺要制备出mim电容器,至少需要用到三
个掩膜,如果后续要形成引出电极以分别对mim电容区和非mim电容区进行电性引出,则所需的掩膜数量还会增加,比如先要在前述步骤得到的结构表面形成覆盖互连金属层的上绝缘层41,之后在第四掩膜的作用下对上绝缘层41进行光刻刻蚀,以于上绝缘层41中形成分别位于mim电容区和非mim电容区的多个引出电极通孔以显露出互连金属层36,然后对引出电极通孔进行金属填充而得到引出电极42,之后在第五掩膜的作用下形成引出电极金属层43,以确保mim电容区的引出电极金属层和非mim电容区的引出电极金属层相互电隔离,最终得到的结构如图9所示。
10.众所周知,掩膜是一种定制化产品,不仅价格昂贵,生产周期长,因此使用的掩膜太多会导致生产成本的上升。而且光刻设备是半导体厂内单价最高的设备(单台光刻机价格可能上亿),每个半导体厂的光刻设备都非常有限,使得光刻工艺成为制约半导体厂产能提升的瓶颈工艺,因而使用的掩膜太多意味着单一产品需要经过多次光刻工艺,这将导致光刻工艺产能紧张,导致半导体厂内的产出下降。此外,光刻设备操作复杂,光刻工艺难度高,光刻良率极大影响最终产品良率,这些因素都限制了mim电容器的大规模推广应用。
技术实现要素:
11.鉴于以上所述现有技术的缺点,本发明的目的在于提供一种具有mim电容器的半导体器件及其制备方法,用于解决采用现有工艺制备mim电容器时至少需使用三个掩膜,导致生产成本的上升和半导体厂内的产出下降等问题。
12.为实现上述目的及其他相关目的,本发明提供一种具有mim电容器的半导体器件的制备方法,所述制备方法包括步骤:
13.提供衬底,所述衬底上定义有mim电容区和非mim电容区,于所述衬底上依次形成底电极层和第一介质层,所述底电极层和第一介质层位于所述mim电容区和非mim电容区;
14.在第一掩膜的作用下对所述第一介质层进行光刻刻蚀,以于所述第一介质层中形成mim电容器通孔和导电插塞通孔,所述mim电容器通孔位于所述mim电容区,所述导电插塞通孔位于所述非mim电容区,且所述mim电容器通孔和所述导电插塞通孔的底面均显露出所述底电极层;
15.依次形成互连金属层和第二介质层,所述互连金属层位于所述mim电容器通孔表面且填充所述导电插塞通孔,填充于所述导电插塞通孔内的互连金属层构成导电插塞,所述第二介质层位于所述互连金属层的表面;
16.进行表面平坦化处理以去除所述mim电容器通孔及导电插塞外的所述互连金属层和第二介质层;
17.在第二掩膜的作用下,于所述mim电容器通孔的第二介质层表面和所述导电插塞的表面形成上极板金属层,位于所述mim电容器通孔内的互连金属层、第二介质层和上极板金属层构成mim电容器,所述mim电容器的上极板金属层和所述导电插塞表面的上极板金属层相互电隔离。
18.可选地,所述导电插塞通孔为两个以上,两个以上导电插塞通孔平行间隔分布。
19.可选地,所述第一介质层包括氧化硅、氮化硅和氮氧化硅中的一种或两种以上,所述第二介质层包括氧化硅、氮化硅、氧化铝、氧化钽、氧化钇、硅酸铪氧化合物、氧化铪、氧化镧和氧化锆中的一种或两种以上;所述互连金属层包括钛、氮化钛、铜和钨中的一种或两种
以上。
20.可选地,所述第一介质层的厚度大于所述第二介质层的厚度,所述导电插塞通孔和所述mim电容器通孔的顶部开口尺寸均大于底部开口尺寸,且所述导电插塞通孔的顶部尺寸小于所述mim电容器通孔的顶部尺寸。
21.可选地,在第二掩膜的作用下,于所述mim电容器通孔的第二介质层表面和所述导电插塞的表面形成上极板金属层的过程包括:
22.可选地,于进行表面平坦化处理后得到的结构形成上极板金属材料层,所述上极板金属材料层覆盖所述mim电容区和非mim电容区;
23.可选地,在所述第二掩膜的作用下对所述上极板金属材料层进行光刻刻蚀,以分别形成位于所述第二介质层表面的上极板金属层和所述导电插塞表面的上极板金属层。
24.可选地,所述制备方法还包括在形成所述上极板金属层后形成多个引出电极的步骤,所述多个引出电极分别与所述第二介质层表面的上极板金属层和所述导电插塞表面的上极板金属层电连接。
25.更可选地,形成所述多个引出电极的方法包括:
26.形成第三介质层,所述第三介质层覆盖所述mim电容区和非mim电容区;
27.在第三掩膜的作用下对所述第三介质层进行光刻刻蚀,以于所述第三介质层中形成相互间隔的第一引出电极孔和第二引出电极孔,所述第一引出电极孔显露出所述mim电容器的上极板金属层,所述第二引出电极孔显露出所述导电插塞上的上极板金属层;
28.对所述第一引出电极孔和第二引出电极孔进行金属填充以分别形成第一引出电极和第二引出电极;
29.形成引出电极金属层,所述引出电极金属层位于所述第一引出电极和第二引出电极的表面,且延伸到所述第三介质层的上表面;
30.在第四掩膜的作用下对所述引出电极金属层进行光刻刻蚀,以使所述mim电容区和非mim电容区的引出电极金属层相互电隔离。
31.本发明还提供一种具有mim电容器的半导体器件,所述半导体器件包括衬底、底电极层、互连金属层、第一介质层、第二介质层和上极板金属层;所述衬底上定义有mim电容区和非mim电容区;所述底电极层位于所述衬底的上表面;所述第一介质层位于所述底电极层的上表面,且所述第一介质层中形成有mim电容器通孔和导电插塞通孔,所述mim电容器通孔位于所述mim电容区,所述导电插塞通孔位于所述非mim电容区,且所述mim电容器通孔和所述导电插塞通孔的底面均显露出所述底电极层;所述互连金属层位于所述mim电容器通孔表面且填充所述导电插塞通孔,填充于所述导电插塞通孔内的互连金属层构成导电插塞;所述第二介质层位于所述mim电容器通孔的互连金属层的上表面;所述上极板金属层位于所述第二介质层的表面和所述导电插塞的表面,其中,位于所述mim电容器通孔内的所述互连金属层、第二介质层和上极板金属层构成mim电容器,所述mim电容器的上极板金属层和所述导电插塞表面的上极板金属层相互电隔离,所述mim电容器的互连金属层和所述导电插塞相互电隔离。
32.可选地,所述导电插塞为多个,所述导电插塞部分延伸到所述底电极层内。
33.可选地,所述半导体器件还包括相互间隔的第一引出电极和第二引出电极,所述第一引出电极与所述mim电容器电连接,所述第二引出电极与所述导电插塞电连接。
34.如上所述,本发明的具有mim电容器的半导体器件及其制备方法,具有以下有益效果:本发明经改善的流程设计,借用通孔蚀刻产生高低台阶,在对互连金属层进行表面平坦化处理(例如化学机械研磨)时,台阶底部的导电金属不会被去除而作为下极板,上层金属作为上极板,加上位于下极板和上极板之间的介质层,三者共同构成mim电容器。相较于现有技术,本发明可有效减少掩膜版的使用,有助于降低成本,且通过减少光刻工艺,有助于提高生产效率和良率。依本发明制备的具有mim电容器的半导体器件,其性能可得到有效提升。
附图说明
35.图1-9显示为现有技术中在制备mim电容器的过程中于各步骤所呈现出的截面结构示意图。
36.图10-17显示为依本发明提供的制备方法在制备具有mim电容器的半导体器件的过程中于各步骤呈现出的截面结构示意图。
37.图18显示为本发明提供的具有mim电容器的半导体器件的制备方法的流程图。
38.元件标号说明
39.11
ꢀꢀꢀꢀ
衬底
40.111
ꢀꢀꢀ
基底层
41.112
ꢀꢀꢀ
层间介质层
42.12
ꢀꢀꢀꢀ
底电极层
43.13
ꢀꢀꢀꢀ
第一介质层
44.131
ꢀꢀꢀ
mim电容器通孔
45.132
ꢀꢀꢀ
导电插塞通孔
46.14
ꢀꢀꢀꢀ
互连金属层
47.15
ꢀꢀꢀꢀ
第二介质层
48.16
ꢀꢀꢀꢀ
导电插塞
49.17
ꢀꢀꢀꢀ
上极板金属层
50.17a
ꢀꢀꢀ
上极板金属材料层
51.18
ꢀꢀꢀꢀ
mim电容器
52.19
ꢀꢀꢀꢀ
第三介质层
53.20
ꢀꢀꢀꢀ
第一引出电极
54.21
ꢀꢀꢀꢀ
第二引出电极
55.22
ꢀꢀꢀꢀ
引出电极金属层
具体实施方式
56.以下通过特定的具体实例说明本发明的实施方式,本领域技术人员可由本说明书所揭露的内容轻易地了解本发明的其他优点与功效。本发明还可以通过另外不同的具体实施方式加以实施或应用,本说明书中的各项细节也可以基于不同观点与应用,在没有背离本发明的精神下进行各种修饰或改变。如在详述本发明实施例时,为便于说明,表示器件结构的剖面图会不依一般比例作局部放大,而且所述示意图只是示例,其在此不应限制本发
明保护的范围。此外,在实际制作中应包含长度、宽度及深度的三维空间尺寸。
57.为了方便描述,此处可能使用诸如“之下”、“下方”、“低于”、“下面”、“上方”、“上”等的空间关系词语来描述附图中所示的一个元件或特征与其他元件或特征的关系。将理解到,这些空间关系词语意图包含使用中或操作中的器件的、除了附图中描绘的方向之外的其他方向。此外,当一层被称为在两层“之间”时,它可以是所述两层之间仅有的层,或者也可以存在一个或多个介于其间的层。
58.在本技术的上下文中,所描述的第一特征在第二特征“之上”的结构可以包括第一和第二特征形成为直接接触的实施例,也可以包括另外的特征形成在第一和第二特征之间的实施例,这样第一和第二特征可能不是直接接触。
59.需要说明的是,本实施例中所提供的图示仅以示意方式说明本发明的基本构想,遂图式中仅显示与本发明中有关的组件而非按照实际实施时的组件数目、形状及尺寸绘制,其实际实施时各组件的型态、数量及比例可为一种随意的改变,且其组件布局型态也可能更为复杂。为使图示尽量简洁,各附图中并未对所有的结构全部标示。
60.现有技术中,在制备mim电容器时,至少需要使用三个掩膜,这导致生产成本上升和生产效率下降。对此,本技术的发明人经长期研究,提出了一种改善方案。
61.如图10-18所示,本发明提供一种具有mim电容器的半导体器件的制备方法,所述制备方法(参考图18)包括步骤:
62.s1:提供衬底11,所述衬底11上定义有mim电容区和非mim电容区,于所述衬底11上依次形成底电极层12和第一介质层13,所述底电极层12和第一介质层13位于所述mim电容区和非mim电容区,即所述底电极层12和第一介质层13覆盖所述衬底11;所述mim电容区和非mim电容区通常相邻设置,mim电容区通常用于制备mim电容器等功能器件,非mim电容区通常用于制备外围电路,当然,mim电容区和非mim电容区也可以间隔设置而在两者之间设置过渡区;所述衬底11可以为单层结构,也可以为如本实施例所示的多层结构,比如包括基底层111和位于基底层111表面的层间介质层112,所述基底层111包括但不限于硅基底、锗基底、锗硅基底、蓝宝石基底、soi基底等半导体基底,所述层间介质层112包括但不限于氧化硅层、氮化硅层、氮氧化硅层或其他绝缘层,所述层间介质层112的形成方法包括但不限于气相沉积法;所述底电极层12的材质包括但不限于铜、铝、金属硅化物等材料中的一种或多种,形成所述底电极层12的方法包括但不限于物理气相沉积法,且mim电容区和非mim电容区的底电极层12通常是电隔离的,比如通过隔离沟槽(该隔离沟槽可被第一介质层13的材料填充)进行隔离;所述第一介质层13包括但不限于氧化硅、氮化硅和氮氧化硅中的一种或两种以上,形成所述第一介质层13的方法包括但不限于气相沉积法,各结构层的厚度可以根据器件需要设置,比如底电极层12的厚度可以为200nm-1000nm(本说明书中在涉及数值范围的描述时,如无特殊说明,均包括端点值),第一介质层13的厚度为500nm-5000nm,较佳地为2000nm-3000nm,以确保后续刻蚀出的mim电容器通孔131有一定的深度而确保通孔内部不会被金属完全填充而保有台阶;该步骤后得到的结构如图10所示;
63.s2:在第一掩膜(未示出)的作用下对所述第一介质层13进行光刻刻蚀,以于所述第一介质层13中形成mim电容器通孔131和导电插塞通孔132,所述mim电容器通孔131位于所述mim电容区;所述导电插塞通孔132位于所述非mim电容区;所述mim电容器通孔131和所述导电插塞通孔132的底面均显露出所述底电极层12;具体地,使用第一掩膜对所述介质层
进行光刻刻蚀的过程可以为,先于所述第一介质层13表面形成光刻胶层,接着在所述第一掩膜的作用下对所述光刻胶层进行曝光显影以定义出所需的图形,然后依残余的光刻胶层对所述第一介质层13进行干法或湿法刻蚀而形成所述mim电容器通孔131和导电插塞通孔132,最后去除残余的光刻胶层;由于光刻刻蚀工艺为本领域技术人员所知晓,故而本说明书中并未图示;所述mim电容器通孔131数量通常为单个,也可以为两个以上,所述导电插塞通孔132数量可以为单个,但通常为两个以上,当数量为两个以上时,多个导电插塞通孔132平行间隔排布;且在较佳的示例中,所述mim电容器通孔131和导电插塞通孔132均为顶部开口大于底部开口的结构(即横截面为上宽下窄的梯形结构),这有助于后续的金属填充;所述mim电容器通孔131和导电插塞通孔132的深度可以相同或不同,比如所述导电插塞通孔132可以稍微深入到所述底电极层12内,这将有助于确保器件的电性连接,且作为示例,mim电容器通孔131的尺寸通常大于导电插塞通孔132的尺寸(包括前者的顶部开口尺寸大于后者的顶部开口尺寸以及前者的底部开口尺寸大于后者的底部开口尺寸);该步骤后得到的结构如图11所述;
64.s3:依次形成互连金属层14和第二介质层15,所述互连金属层14位于所述mim电容器通孔131表面(但并未填满所述mim电容器通孔131而确保mim电容器通孔131底面和上表面仍有一定的高度差,即形成台阶)且填充所述导电插塞通孔132,填充于所述导电插塞通孔132内的互连金属层14构成导电插塞16,所述第二介质层15位于所述互连金属层14的表面;作为示例,所述互连金属层14包括但不限于钛、氮化钛、铜和钨中的一种或两种以上,其形成方法包括但不限于溅射法,厚度通常大于第一介质层13的厚度,以确保在填充mim电容器通孔131和导电插塞通孔132后还能延伸到第一介质层13的表面;作为示例,所述第二介质层15包括但不限于氧化硅和氮化硅中的一种或两种的结合,也可以采用高k介质材料,比如选自但不限于氧化铝、氧化钽、氧化钇、硅酸铪氧化合物、氧化铪、氧化镧和氧化锆中的一种或两种以上,其形成方法包括但不限于气相沉积法,厚度可为200nm-500nm;该步骤后得到的结构如图12所示;
65.s4:采用包括但不限于化学机械研磨(cmp)进行表面平坦化处理以去除所述mim电容器通孔131及导电插塞16外的所述互连金属层14和第二介质层15,而仅保留位于所述mim电容器通孔131内表面的互连金属层14和第二介质层15,以及位于导电插塞通孔132内的互连金属层14,即使得导电插塞16的上表面和第一介质层13的上表面相平齐;经平坦化处理后,mim电容器通孔131的底部仍和器件的上表面,比如与第一介质层13的上表面具有一定的高度差;该步骤后得到的结构如图13所示;
66.s5:在第二掩膜的作用下,于所述mim电容器通孔131的第二介质层15表面和所述导电插塞16的表面形成上极板金属层17,位于所述mim电容器通孔131内的互连金属层14、第二介质层15和上极板金属层17构成mim电容器18,mim电容器18可以为单个或多个,所述mim电容器18的上极板金属层17和所述导电插塞16表面的上极板金属层17相互电隔离;在一示例中,该过程可以为:先采用包括但不限于物理气相沉积法于进行表面平坦化处理后得到的结构表面形成上极板金属材料层17a,所述上极板金属材料层17a覆盖所述mim电容区和非mim电容区,即mim电容区和非mim电容区的上极板金属材料层17a在同一工艺中同步形成,且是相互连接的,所述上极板金属材料层17a的材质可以和互连金属层14的材质相同或不同,比如同样可以包括但不限于钛、氮化钛、铜和钨中的一种或两种以上,也可以和底
电极层12的材质相同,该步骤后得到的结构如图14所示;
67.在所述第二掩膜的作用下对所述上极板金属材料层17a进行光刻刻蚀,以在位于mim电容区和非mim电容区之间的上极板金属材料层17a之间形成隔离沟槽而使两个区域的上极板金属材料层17a相互断开,以分别形成位于所述第二介质层15表面的上极板金属层17(由位于第二介质层15表面的上极板金属材料层形成)和所述导电插塞16表面的上极板金属层17(由位于导电插塞16表面的上极板金属材料层形成,且当导电插塞16为多个时,不同的导电插塞16表面的上极板金属层17相互电隔离),该步骤后得到的结构如图15所示。至此为此,本实施例完成了mim电容器18的制备。
68.从上述过程可以看到,本发明在制备得到mim电容器的过程中,经优化的流程设计,借用通孔(mim电容器通孔)蚀刻产生高低台阶,在对互连金属层进行表面平坦化处理时,台阶底部的导电金属不会被去除而作为mim下极板,上层金属作为上极板,加上位于下极板和上极板之间的介质层,三者共同构成mim电容器。相较于现有技术,本发明可有效减少掩膜版的使用,有助于降低成本,且仅使用两次掩膜版意味着仅需进行两次光刻工艺,有助于提升光刻机台的产出率,同时因减少光刻工艺,降低了工艺的整体难度,有助于提升产品良率。依本发明制备的半导体器件,在刻蚀形成非mim区的导电插塞通孔时,仅需刻蚀单一的第一介质层,有助于确保导电插塞通孔底部完全打开,且在后续填充互连金属材料时能够确保良好的填充,减少孔洞的产生,有助于提高器件的电性能。
69.作为示例,为实现器件的电性引出,所述制备方法还包括在形成所述上极板金属层17后形成多个引出电极的步骤,所述多个引出电极分别与所述第二介质层15表面的上极板金属层17和所述导电插塞16表面的上极板金属层17电连接。在进一步的示例中,形成所述多个引出电极的方法包括:
70.形成第三介质层19,所述第三介质层19覆盖所述mim电容区和非mim电容区,所述第三介质层19可以和第一介质层13的材质相同,也可以不同,包括但不限于氮化硅、氧化硅、氮氧化硅或其他绝缘材料中的若干种,形成工艺包括但不限于气相沉积工艺,且在形成第三介质层19后,通常需对其进行化学机械研磨,以使其上表面相平齐,研磨后的第三介质层19的上表面需和导电插塞16上的上极板金属层17具有一定的间距,该步骤后得到的结构如图16所示;
71.在第三掩膜的作用下对所述第三介质层19进行光刻刻蚀,以于所述第三介质层19中形成相互间隔的第一引出电极孔和第二引出电极孔,所述第一引出电极孔显露出所述mim电容器18的上极板金属层17,所述第二引出电极孔显露出所述导电插塞16上的上极板金属层17;第一引出电极孔和第二引出电极21均可以为单个或两个以上;
72.采用包括但不限于溅射沉积工艺对所述第一引出电极孔和第二引出电极孔进行金属填充以分别形成第一引出电极20和第二引出电极21,填充的金属包括但不限于钨和/或铜;
73.采用包括但不限于物理气相沉积工艺形成引出电极金属层22,所述引出电极金属层22位于所述第一引出电极20和第二引出电极21的表面,且延伸到所述第三介质层19的上表面,所述引出电极金属层22包括但不限于铜、铝、金或金属硅化物;
74.在第四掩膜的作用下对所述引出电极金属层22进行光刻刻蚀,以使所述mim电容区和非mim电容区的引出电极金属层22相互电隔离,即,使第一引出电极20和第二引出电极
21不相连,而多个第一引出电极20之间相互电连接,多个第二引出电极21之间根据器件需要,可以相互电隔离;该步骤后得到的结构如图17所示。当然,在其他示例中,形成所述引出电极的过程也可以在刻蚀出所述第一引出电极孔和第二引出电极孔后,继续借助掩膜覆盖无需形成引出金属的区域而仅对特定区域进行金属沉积(这对沉积设备的要求比较高,因而难度相对比较大),比如仅对第一引出电极孔和第二引出电极孔进行金属填充。
75.本发明还提供一种具有mim电容器的半导体器件,所述半导体器件可依前述任一方法制备而成,故前述内容可以全文引用至此。当然所述半导体器件也可以依其他方法制备而成。如图17所示,所述半导体器件包括衬底11、底电极层12、互连金属层14、第一介质层13、第二介质层15和上极板金属层17;所述衬底11上定义有mim电容区和非mim电容区,mim电容区和非mim电容区通常相邻设置,当然也可以相互间隔;所述底电极层12位于所述衬底11的上表面,所述底电极层12的材质包括但不限于铜、铝和金属硅化物;所述第一介质层13位于所述底电极层12的上表面,且所述第一介质层13中形成有mim电容器通孔131和导电插塞通孔132,所述mim电容器通孔131位于所述mim电容区,所述导电插塞通孔132位于所述非mim电容区,且所述mim电容器通孔131和所述导电插塞通孔132的底面均显露出所述底电极层12;所述互连金属层14位于所述mim电容器通孔131表面且填充所述导电插塞通孔132,填充于所述导电插塞通孔132内的互连金属层14构成导电插塞16,导电插塞16可以为单个或多个,当为多个时,多个导电插塞16间隔分布;所述第二介质层15位于所述mim电容器通孔131的互连金属层14的上表面;所述上极板金属层17位于所述第二介质层15的表面和所述导电插塞16的表面,其中,位于所述mim电容器通孔131内的所述互连金属层14、第二介质层15和上极板金属层17构成mim电容器18,所述mim电容器18的上极板金属层17和所述导电插塞16表面的上极板金属层17相互电隔离,所述mim电容器18的互连金属层14和所述导电插塞16相互电隔离。
76.所述衬底11可以为单层结构,也可以为如本实施例所示的多层结构,比如包括基底层111和位于基底层111表面的层间介质层112,所述基底层111包括但不限于硅基底、锗基底、锗硅基底、蓝宝石基底、soi基底等半导体基底,所述层间介质层112包括但不限于氧化硅层、氮化硅层、氮氧化硅层或其他绝缘层。
77.作为示例,所述互连金属层14的材质包括但不限于钛、氮化钛、铜和钨中的一种或两种以上。所述上极板金属层17和下极板金属层的材质可以相同或不同,比如包括但不限于钛、氮化钛、铜和钨中的一种或两种以上。
78.作为示例,所述第二介质层15包括但不限于氧化硅和氮化硅中的一种或两种的结合,也可以采用高k介质材料,比如选自但不限于氧化铝、氧化钽、氧化钇、硅酸铪氧化合物、氧化铪、氧化镧和氧化锆中的一种或两种以上。
79.在一示例中,所述导电插塞16延伸到所述底电极层12内,以确保导电插塞16和底电极层12的电连接。
80.在一示例中,所述半导体器件还包括相互间隔的第一引出电极20和第二引出电极21,所述第一引出电极20与所述mim电容器18电连接,第一引出电极20可以为多个且相互电连接,所述第二引出电极21与所述导电插塞16电连接,第二引出电极21的数量通常与导电插塞16的数量一致且一一对应。
81.对所述半导体器件的更多介绍还请参考前述内容,出于简洁的目的不赘述。
82.综上所述,本发明提供一种具有mim电容器的半导体器件及其制备方法。本发明在制备得到mim电容器的过程中,经优化的流程设计,借用通孔(mim电容器通孔)蚀刻产生高低台阶,在对互连金属层进行表面平坦化处理时,台阶底部的导电金属不会被去除而作为mim下极板,上层金属作为上极板,加上位于下极板和上极板之间的介质层,三者共同构成mim电容器。相较于现有技术,本发明可有效减少掩膜版的使用,有助于降低成本,且仅使用两次掩膜版意味着仅需进行两次光刻工艺,有助于提升光刻机台的产出率,同时因减少光刻工艺,降低了工艺的整体难度,有助于提升产品良率。依本发明制备的半导体器件,在刻蚀形成非mim区的导电插塞通孔时,仅需刻蚀单一的第一介质层,有助于确保导电插塞通孔底部完全打开,且在后续填充互连金属材料时能够确保良好的填充,有助于提高器件的电性能。所以,本发明有效克服了现有技术中的种种缺点而具高度产业利用价值。
83.上述实施例仅例示性说明本发明的原理及其功效,而非用于限制本发明。任何熟悉此技术的人士皆可在不违背本发明的精神及范畴下,对上述实施例进行修饰或改变。因此,举凡所属技术领域中具有通常知识者在未脱离本发明所揭示的精神与技术思想下所完成的一切等效修饰或改变,仍应由本发明的权利要求所涵盖。
再多了解一些
本文用于企业家、创业者技术爱好者查询,结果仅供参考。