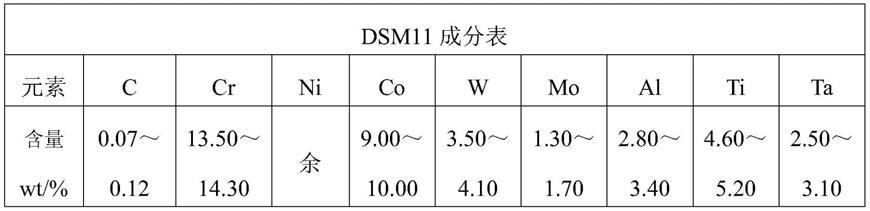
1.本发明涉及金属防护涂层技术领域,具体涉及一种提高金属型芯涂层界面稳定性的方法。
背景技术:
2.涡轮叶片是航空发动机、燃气轮机的热端关键部件之一,叶片的承温能力越高,工作效率越高。为了提高工作效率,叶片从材料和结构方面进行改善,叶片材料熔点越高,则工作效率越高,然而叶片的工作温度已经超过高温合金的熔点,材料的承温能力已经非常接近极限;另一方面,则设计叶片的结构,叶片的空心结构不能通过机械加工形成,只能在浇注叶片前预先放置精密铸造型芯,然后通过化学腐蚀手段去除型芯,进而达到空心结构,通入冷却空气带走热量,实现了空气冷却,空气冷却能有效的提高叶片的使用温度,因此冷却效率对于涡轮叶片尤为重要。
3.随着冷却技术和铸造工艺的发展,铸造型芯的使用性能要求越来越高,目前陶瓷型芯为追求高的冷却效率,冷却通道设计的更加精细和复杂,相应的尺寸更加精细、细小。但是陶瓷型芯细小部位性能会下降,尤其是强度、抗热冲击能力都会下降,因此陶瓷材料由自身的性质尺寸会受到限制。为了解决该部分陶瓷材料的问题,因此采用钼基金属型芯替代细小的陶瓷型芯的部分,进而制备出具有更加先进的冷却结构的陶瓷-金属复合型芯,然而钼基金属型芯应用的关键,则是合理设计钼合金的防护涂层。
4.钼基金属型芯的制备、服役过程,通过在钼基金属型芯预先沉积金属间化合物层,然后预氧化形成惰性氧化物涂层,经过一系列的精密铸造过程,包括型芯组装、制备蜡模、型壳、脱蜡等,陶瓷模组进入定向炉中,抽真空,升温至1000℃~1300℃保温,然后升温到1500℃~1650℃,保温一段时间,然后浇注高温合金,保持一定速率抽出,待冷却后取出,去壳、脱芯。
5.如图1(a)所示,在1550℃浇注dsm11高温合金后,涂层能够抵抗住合金的侵蚀,保护住钼基金属型芯的基体,但dsm11合金表面会发生严重的界面反应(如图1(b)所示),这可能是由于氧化硅在高于1550℃时与高温合金中的活性元素al、cr、ti等发生化学反应,造成氧化硅黏连在铸造件表面,造成表面缺陷(如图2)。为了避免氧化硅的影响,有必要提高金属型芯涂层界面的稳定性和铸造件的表面质量。
技术实现要素:
6.为了解决金属钼型芯的惰性氧化物层中氧化硅与高温合金的界面不稳定问题,本发明提供一种提高金属型芯涂层界面稳定性的方法,该方法能够减少惰性氧化物中氧化硅的含量,并能利用高熔点金属元素稳固涂层中的氧化硅,从而提高涂层的界面稳定性。
7.为实现上述目的,本发明所采用的技术方案如下:
8.一种提高金属型芯涂层界面稳定性的方法,该方法是在钼基金属型芯表面制备涂层过程中,通过优化涂层成分和预氧化技术提高型芯与涂层之间界面的稳定性;该方法具
体包括如下步骤:
9.(1)以纯钼或钼合金作为金属型芯基体,采用化学气相沉积或原位化学气相沉积工艺在型芯基体上进行硅、铝元素的共沉积(在加热炉或化学气相沉积炉中进行),沉积温度为900℃-1300℃,沉积时间为2h~30h;沉积结束后以1~15℃/min的降温速率降温到800℃,然后关闭加热系统,随炉冷却至室温,即在基体上形成含铝硅的复合涂层。
10.(2)预氧化处理:对步骤(1)沉积有涂层的型芯基体进行预氧化处理,处理过程为:先通入空气或氧气,控制流量在1~100sscm,然后升温至1000-1100℃,保温1h~5h;再以1~15℃/min的升温速率升温至1200~1400℃,保温1~8h;保温结束后打开真空系统进行抽真空或通入惰性气体,使炉内氧气的浓度下降,并关闭加热系统,随炉冷却。
11.(3)在步骤(2)预氧化处理后的试样表面沉积高熔点金属涂层,沉积方式为电弧离子镀、电镀、磁控溅射、真空蒸镀、化学气相沉积等;所述高熔点金属涂层的熔点高于1600℃。
12.上述步骤(1)中,所述金属型芯基体在使用前先进行预处理,过程为:先采用240#-800#砂纸进行打磨,然后依次在去离子水和无水酒精中清洗,烘干后备用。
13.上述步骤(1)中,进行硅、铝元素的共沉积时,由于铝硅元素的差异,涂层首先形成低熔点铝化物涂层,然后转化(全部或一部分)为高熔点硅化物涂层。
14.上述步骤(1)中,进行硅、铝元素的共沉积时,首先在基体上形成含铝金属间化合物层,然后再在金属间化合物层上形成惰性氧化物层(氧化铝和氧化硅);复合涂层的总厚度大于30μm,低熔点相能够在后期预氧化过程中消失。
15.上述步骤(3)中,所述高熔点金属涂层为铬、铪、铱、或铂涂层。
16.上述步骤(1)中,在型芯基体上进行硅、铝元素的共沉积时,还可以同时沉积铬、锆、钛和镁元素中的一种或几种。
17.上述步骤(2)中,预氧化之后,在降温过程中随炉冷却至500℃以下取出。
18.上述步骤(3)中,沉积的金属涂层厚度为0.1μm-20μm。
19.本发明的设计机理如下:
20.本发明首先采用铝、硅元素共沉积在钼基金属型芯基体上制备复合涂层,复合涂层结构为基体/金属间化合物层/惰性氧化层/金属涂层;共沉积时,由于al和si元素自身特点的差异,导致在沉积的过程呈现出不同的差异,al的熔点660℃,si的熔点为1414℃,在1000℃条件下al的活性高于si的活性,涂层首先沉积al出现al8mo3相,随着温度升高,si的活性升高,si在基体的扩散系数变大(dsi>d
al
),si的含量上升取代al8mo3出现mo(si,al)2,直至al8mo3部分或全部变为mo(si,al)2,甚至最内层为mosi2。因此涂层首先形成低于1600℃的低熔点al8mo3相,然后出现高于1600℃的改性硅化物相(mo(si,al)2和mosi2)。再采用预氧化技术,预氧化技术中氧化膜生长过程为多级阶梯升温氧化,在降温过程中随炉冷却至500℃以下取出。预氧化技术的温度必须高于1000℃以上,以保证涂层中可能残存的低熔点al8mo3相在高温下分解且要保证在预氧化过程中消失,其总涂层厚度在30μm以上。预氧化技术中,氧化膜中氧化铝含量达到最大后,进行抽真空或通入氩气降低氧气浓度,保护样品;
21.最后将高熔点金属涂层沉积在金属型芯的表面,在真空、高温的环境中利用元素化学反应和扩散,形成更加稳定界面类型,降低氧化硅的影响,从而提高界面的稳定性。高
熔点涂层金属熔点在1600℃以上,保证高熔点金属涂层在未浇注高温合金之前不发生融化,浇注高温合金后,该金属进入合金熔体后不产生影响或提高合金的性能。
22.本发明的有益的结果如下:
23.1、通过在涂层中添加活性元素,调整涂层结构,保证涂层抵抗高温合金的侵蚀的作用,涂层的强韧性明显增强,与基体界面结合力增加。
24.2、通过优化控制预氧化参数(时间、温度、氧气浓度),使涂层中氧化铝的含量达到了最大。
25.3、预先沉积金属涂层,对型芯的基体防护涂层,沉积的金属元素与氧化硅在高温真空下进行反应,使外部的氧化层的界面更加稳定,同时沉积的金属元素熔入高温合金中对其性能不产生影响。
26.4、通过稳固界面,将型芯与高温合金的界面间隙降低到最23um,易于精确控制叶片的空腔的尺寸。
附图说明
27.图1为低熔点al8mo3相存在时试样失效截面照片;其中:(a)在1550℃浇注dsm11高温合金后的型芯基体,(b)在1550℃浇注后的dsm11高温合金表面。
28.图2为经本发明改进前的型芯;其中:(a)型芯与合金的界面,(b)dsm11合金的表面,(c)型芯的表面。
29.图3为本发明工艺改进后的型芯;其中:(a)型芯与合金的界面,(b)dsm11合金的表面,(c)型芯的表面。
具体实施方式
30.为了进一步理解本发明,以下结合实例对本发明进行描述,但实例仅为对本发明的特点和优点做进一步阐述,而不是对本发明权利要求的限制。
31.本发明通过优化涂层和预氧化技术以及利用高熔点金属涂层提高金属型芯涂层界面的稳定性,采用的具体方案如下:
32.所述的优化涂层为采用铝、硅元素共沉积,并可进一步涂层中添加铬、锆、钛、镁等有益元素。由于元素的自身性质的差异,铝硅共沉积过程会先形成al8mo3涂层,而后形成硅化物涂层,涂层中低熔点al8mo3相要在经过预氧化技术后全部消除,保持高熔点涂层结构,确保在浇注试样中不发生失效。该方法包括如下步骤:步骤一,预先经过240#-800#砂纸进行打磨,依次在去离子水和无水酒精中清洗,烘干备用,步骤二,采用化学气相沉积-共沉积元素,温度为900℃-1300℃,时间为2h~30h,步骤三,按程序以1~15℃/min降温到800℃,关闭加热系统,随炉冷却至室温。
33.所述的预氧化技术按照预先放置试样、打开预制加热程序、真空低氧条件下冷却的顺序进行,包含如下步骤:步骤一,将已沉积好的并已冷却至室温的涂层试样放入氧化铝坩埚中,试样之间设有一定间隙,为保持均匀受热,试样不发生变形,可填入5目~120目的氧化铝;步骤二,打开升温设备,升温至1000℃-1100℃预热并保温1h~5h,保温时间可随试样的尺寸而定;步骤三,将预热后的涂层试样以1℃/min~15℃/min的速率升温至1200℃~1400℃,保温时间为1h~8h;步骤四,打开真空系统或通入惰性气体,使得炉内氧气的浓度
下降;同时关闭加热系统,随炉冷却。
34.沉积高熔点金属涂层,可通过不同方法沉积制备金属涂层,例如真空蒸镀、电弧离子镀、电镀等,可根据沉积的金属元素沉积方法而设定。
35.所述放入高熔点涂层服役环境为在定向炉中过程:模组放进真空定向炉至浇注高温合金前之间的特定时间。
36.所述的高熔点金属涂层熔点高于1600℃,在真空定向炉中未浇注高温合金之间不发生熔化。同时在浇注高温合金后,该金属进入合金熔体后不产生影响或提高合金的性能。
37.所述的高熔点金属,能在真空、高温环境与氧化硅发生界面化学反应,形成更稳定的氧化物,降低涂层表面氧化硅的影响,进一步改善界面。
38.对比例1
39.以冷轧钼板(纯度99.99%)为型芯基体,用电火花线切割成为尺寸24mm*20mm*0.4mm,用240#~800#砂纸打磨表面,用去离子水清洗,烘干,用无水酒精超声清洗,烘干。采用原位化学气相沉积方法进行硅铝共沉积,其中原料为:硅粉(300~500目,分析纯99.95%)、铝粉(300~500目,分析纯99.95%)、活化剂(nh4cl,分析纯99.5%)、惰性填充剂(al2o
3 100~300目),按硅粉:铝粉:活化剂:惰性填充剂=15:3:2:80(wt%)比例进行混粉,混合后粉末球磨机混合10h,将型芯基体与混合粉末放入沉积罐,将沉积罐放入加热炉的中心区,关闭加热炉炉门,保持良好的气密性,打开加热炉出气阀门,打开氩气,通入氩气15min~20min或更长,以5℃/min加热至200℃,保温30min,同时再次通入氩气30min,关闭进气阀门,然后打开真空泵,将真空压力调至-0.06mpa~-0.02mpa,关闭出气阀门,以5min/℃加热至1000℃,再以2℃/min加热至1100℃,保持压力在 0mpa~0.04mpa,保温5~20h,再以2℃/min的速率至1000℃,自然冷却至室温。对共沉积后的涂层进行检测发现型芯涂层中存在低熔点al8mo3相,如直接浇注dsm11合金会造成涂层失效,如图1所示,在浇注高温的温度使低熔点相发生熔化,涂层很快被破坏。
40.将上述进行原位化学气相沉积的金属型芯用去离子水清洗表面,烘干,用无水酒精清洗试样表面,烘干,将试样放入氧化铝坩埚,再放入马弗炉中;炉内通入空气,空气流量控制在5sscm,1300℃等温氧化1~10h,取出后冷却。将型芯组装进蜡膜,制壳(沾浆、撒沙反复直至所要求的厚度,干燥),在100℃~260℃进行蒸汽脱蜡,加热到900℃保温1h烧制型壳。将壳组放入真空定向炉,抽真空至1pa以下,加热到1550℃后,浇注dsm11高温合金,以6mm/min抽出,然后冷却至室温,取出去壳。
[0041][0042]
本例对共沉积si、al后的型芯进行等温氧化,虽然低熔点相全部转化为高熔点相(氧化铝和氧化硅),但涂层表面生成的氧化硅含量较高,在浇注dsm11高温合金后,影响合金质量。
[0043]
对比例2
[0044]
在本例中,与对比例1的区别为:涂层采用化学气相沉积制备,过程为:将基体打孔,便于基体放入试样架上,放入反应腔室中,关闭cvd炉门,将反应腔室的抽至真空200pa以下,加热至900℃~1200℃,打开流量控制器,体积流量比h2:alcl3:sicl4=1:1.2:2,保温2h~20h,然后按程序以10℃/min降温到800℃,关闭加热系统,随炉冷却。取出试样后用去离子水清洗试样表面,烘干,用无水酒精清洗试样表面,烘干,将试样放入氧化铝坩埚,再放入马弗炉中;炉内通入空气,空气流量控制在5sscm,1300℃等温氧化1h~10h,取出后冷却。将型芯组装进蜡膜,制壳(沾浆、撒沙反复直至所要求的厚度,干燥),在100℃~260℃进行蒸汽脱蜡,加热到900℃保温1h烧制型壳。将壳组放入真空定向炉,抽真空至1pa以下,加热到1550℃后,浇注dsm11高温合金,以6mm/min抽出,然后冷却至室温,取出去壳。
[0045]
本例对共沉积si、al后的型芯进行等温氧化,虽然低熔点相全部转化为高熔点相(氧化铝和氧化硅),但涂层表面生成的氧化硅含量较高,在浇注dsm11高温合金后,影响合金质量。
[0046]
对比例3
[0047]
在本例中,与对比例1-2的区别在于:在型芯基体表面采用化学气相沉积或原位化学气相沉积制备含al、si的涂层后,进行预氧化处理的过程不同;本例预氧化过程为:将试样放入加热炉中,将已沉积好的并已冷却至室温的涂层试样放入氧化铝坩埚中,试样之间设有一定间隙,为保持均匀受热,试样不发生变形,可填入36目的氧化铝;炉内通入空气,空气流量控制在5sscm,打开升温设备,升温至1100℃预热并保温2h,保温时间可随试样的尺寸而定;将预热后的涂层试样以5℃/min的速率升温至1300℃,保温时间为2h;打开真空系统或通入惰性气体,使得炉内氧气的浓度下降;同时关闭加热系统,随炉冷却。在沉积结束后,关闭基体,停止,待基体冷却至室温,打开腔室,取出工件。将型芯组装进蜡膜,制壳(沾浆、撒沙反复直至所要求的厚度,干燥),在100℃~260℃进行蒸汽脱蜡,加热到900℃保温1h烧制型壳。将壳组放入真空定向炉,抽真空至1pa以下,加热到1550℃后,浇注dsm11高温合金,以6mm/min抽出,然后冷却至室温,取出去壳。
[0048]
本例对共沉积si、al后的型芯进行阶梯氧化,使低熔点相al8mo3相分解转化为高熔点相,且由于采用了阶梯氧化,涂层表面生成的氧化硅含量较低,但由于氧化硅的存在,在浇注dsm11高温合金后,少量氧化硅仍然会破坏合金表面,影响合金质量。
[0049]
实施例1
[0050]
在本实施例中,与对比例1-3的区别在于,在对比例3进行预氧化处理后,采用电弧离子镀沉积金属涂层,将试样安装在镀膜腔室内的,打开真空系统抽真空至1
×
10-3
pa以下,然后对腔室中试样进行加热,加热至300℃~600℃,通入工作气体氩气,对试样施加负偏压1000v~300v,每间隔一定时间,依次升高负压进行离子轰击,然后铬靶电弧电流为40a~120a,基体与靶材的距离260mm,对试样处施加负偏压200v,镀铬时间为25min,将负偏压调节到100v,镀铬时间35min,将负偏压调节到70v,镀铬时间300min,反复进行,直至铬层厚度为4μm,镀铬结束。在沉积结束后,停止加热,待基体冷却至室温,打开腔室,取出工件,将型芯组装进蜡膜,制壳(沾浆、撒沙反复直至所要求的厚度,干燥),在100℃~260℃进行蒸汽脱蜡,加热到900℃保温1h烧制型壳。将壳组放入真空定向炉,抽真空至1pa以下,加热到1550℃后,浇注dsm11高温合金,以6mm/min抽出,然后冷却至室温,取出去壳。
[0051]
如图3所示为改进后的型芯:(a)型芯与合金的界面,(b)dsm11合金的表面,(c)型
芯的表面,可以看出,浇注高温合金后,本发明制备的涂层能够抵抗高温合金的侵蚀,涂层的强韧性明显增强,与基体界面结合力增加。由于金属涂层的存在,可以阻挡氧化硅对合金的影响。
[0052]
实施例2
[0053]
在本实施例中,与对比施例1-3的区别在于:在对比例3进行预氧化处理后的试样采用离子溅射仪镀铂金属层。靶材为纯铂,预氧化的试样放入离子溅射仪的反应腔室,打开真空泵将调整至10pa以后,设置时间400s,待沉积结束后,关闭电源,取出试样。将型芯组装进腊膜,制壳(沾浆、撒沙反复直至所要求的厚度,干燥),在100℃~260℃进行蒸汽脱蜡,加热到900℃保温1h烧制型壳。将壳组放入真空定向炉,抽真空至1pa以下,加热到1550℃后,浇注dsm11高温合金高温合金,以6mm/min抽出,然后冷却至室温,取出去壳。
[0054]
本发明制备的涂层能够抵抗高温合金的侵蚀,涂层的强韧性明显增强,与基体界面结合力增加。由于金属涂层的存在,可以阻挡氧化硅对合金的影响。
[0055]
以上所述的实施案例,并不局限于本发明,凡是在本发明的原则和之内,本领域人员所做的任何修改、改变,均在本发明的保护所述权利要求保护范围内。
再多了解一些
本文用于企业家、创业者技术爱好者查询,结果仅供参考。