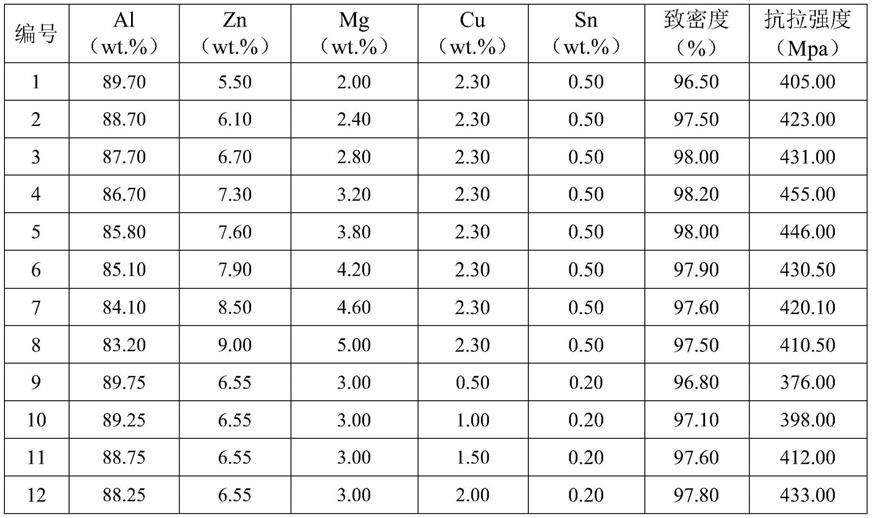
一种利用粉末注射成形技术制备al-zn-mg-cu系铝合金的方法
技术领域
1.本发明提供一种利用粉末注射成形技术制备al-zn-mg-cu系铝合金的方法,属于粉末冶金领域。
背景技术:
2.近年来,随着汽车、3c产品、5g通讯、可穿戴设备和工业机器人等领域逐渐向小型化和轻量化发展,对轻质高强的小型复杂形状结构件的需求越来越高,采用高强铝合金替代传统铁基材料是实现轻量化的重要途径。采用机械加工,铸造和3d打印等手段制备小型复杂形状铝合金零部件存在成本高和不利于大规模生产等难题。采用压制-烧结工艺制备铝合金零部件也往往受限于模具的形状。金属注射成形技术在制备小型复杂形状零部件方面具有独特的优势,无需后续加工,适合大批量生产,是一种节约能源、资源、低成本的零部件加工技术。然而,将粉末注射成形技术应用于铝合金零部件的制备上,需要面临以下问题:
①
与压制工艺相比,注射成形铝合金粉末未经过塑性变形,表面的氧化膜更加完整;
②
与传统的压制-烧结粉末冶金工艺相比,注射成形胚体中含有30-40vol.%的粘结剂,在粘结剂脱除后,留有大量孔隙,使得颗粒间通过扩散烧结更加困难;
③
铝粉以及其他原料粉末在喂料制备过程以及脱脂过程中,会和空气以及粘结剂中氧和水发生反应,增加粉末表面的氧化膜厚度,进一步增加了铝合金粉末烧结致密化的难度。
3.目前,仅有极少数文献和专利报道了铝合金注射成形技术。acar等人使用气雾化纯铝粉,中粒径d
50
为7.35μm,在650℃的高纯n2环境烧结60min下获得最高密度96.2%,最高的抗拉强度126mpa,最高的硬度46hb[acar l,gulsoy h o.sintering parameters and mechanical properties of injection moulded aluminium powder[j].powder metallurgy.2011,54(3):427-431.]。liu等人采用aa6061(al-0.95mg-0.65si-0.27cu)合金粉为原料,通过添加sn元素以促进烧结,研究发现合金致密度随着sn的增加而提高,最终在2wt.%sn时获得了致密度为97%的烧结坯,时效后抗拉强度为300mpa[liu z y,sercombe t b,schaffer g b.metal injection moulding of aluminium alloy 6061with tin[j].powder metallurgy.2008,51(1):78-83.]。ni等人采用al-si预合金粉为原料,在550℃的高纯n2环境下烧结3h,其致密度、抗拉强度和硬度分别可达95.5%、154mpa和58hbw[ni j,yu m,han k.debinding and sintering of an injection-moulded hypereutectic al
–
si alloy[j].materials,2018,11(5):807.]。杜智渊等人使用al、cu、sn单质粉和al-50mg、al-12si中间合金粉为原料制备al-4cu-2mg-0.8si-0.5sn,在氮气烧结气氛下致密度达到98%以上,时效处理后抗拉强度达到400mpa[杜智渊,吴茂,邱婷婷,曲选辉.al-cu-mg-si系铝合金的注射成形[j].中国有色金属学报,2019,29(11):2471-2480.]。同时,中国发明专利《一种利用粉末注射成形技术制备高性能铝合金的方法》,申请号:201711182052.5,公开了一种基于al-cu-mg-si系的铝合金注射成形技术,其中,铝合金成分的质量百分含量为:cu 3-6%,mg 1-3%,si 0.2-2.0%,sn 0.1-2.0%,al为余量的合
金体系,制备的铝合金零部件抗拉强度达到300mpa。
[0004]
综上所述,注射成形铝合金的研究主要集中在纯al、al-si体系、al-cu-mg-si等合金体系,由于材料体系和增强相的种类不同,使用这些体系制备的注射成形铝合金零件的强度普遍不高,性能难以满足如今更高强度的要求,因此需借鉴传统7系高强铝合金的成分,制备al-zn-mg-cu系注射成形铝合金。但采用注射成形技术制备al-zn-mg-cu系铝合金有如下问题:
①
现有的al-zn-mg-cu系合金都是基于铸锻铝合金的标准成分,没有适合用于注射成形工艺的al-zn-mg-cu系合金成分;
②
zn元素在al中具有很高的扩散系数,且易挥发,在烧结过程中形成的al-zn共晶液相具有瞬态性,且其余液相形成元素cu含量较少,使得al-zn-mg-cu体系中的液相量难以控制;
③
由于铝合金烧结过程中依靠液相的填隙使坯体致密化,由于al-zn合金液相形成温度就较低(380℃),此时传统的粘结剂体系难以挥发干净,影响合金的致密化。
[0005]
本发明提供一种适用于注射成形技术的al-zn-mg-cu系铝合金成分及其粘结剂体系,制备的铝合金材料强度高于450mpa。
技术实现要素:
[0006]
本发明提供一种利用粉末注射成形技术制备al-zn-mg-cu系铝合金的方法。以纯铝粉为主要原料,通过合金元素成分的设计、粘结剂体系的优化、脱脂及烧结制度的优化等手段,提高注射成形铝合金致密化烧结,实现高性能复杂形状铝合金零部件的低成本大批量制备。
[0007]
一种利用粉末注射成形技术制备高性能铝合金的方法,其特征在于:以al-zn-mg-cu合金体系为基础,添加少量sn元素;原料粉末采用纯al粉、cu粉、sn粉、al-50zn粉和al-50mg粉;将原料粉末按一定的比例混匀后,加入特定配比的蜡基粘结剂,并置于辊式混炼机上进行混炼获得喂料,通过注射成形技术制备得到生坯,经过溶剂脱脂,在高纯氮气气氛下进行热脱脂-烧结一体化步骤,得到高致密度的注射成形铝合金制品。
[0008]
进一步地,所述的注射成形用铝合金中各合金元素的质量百分含量为:zn 5.5-9%、mg 2.0-5.0%、cu 1.0-4.5%和sn 0.1-2%,al为余量。
[0009]
进一步地,所述的用于注射成采用的原料粉末的粒径分别为al:10-30μm、cu:10-40μm、sn:5-20μm、al-50zn:15-45μm和al-50mg:35-50μm。
[0010]
进一步地,所述的注射成形用铝合金的粘结剂各组元的质量百分含量为:石蜡(32-64%)、蜂蜡(0-32%)、聚乙烯蜡(0-32%)、低密度聚乙烯(0-21%)、高密度聚乙烯(0-23%)、聚丙烯(0-8.5%)和硬脂酸(4-13.5%)。本发明选择优选的粘结剂成分为:石蜡(58-64%),高密度聚乙烯(20-23%),聚丙烯(5.5-8.5%),硬脂酸(7.5-13.5%)。
[0011]
进一步地,所述的注射成形用铝合金喂料的装载量为58-66vol.%,即喂料中铝合金粉末的占总体积的58-66%;混炼的参数为:混炼温度160-180℃,混炼时间为1.5-2.5h。
[0012]
进一步地,所述的注射成形用铝合金的注射参数为:注射温度为155-170℃,注射压力170-180bar,注射速度为70-80%,模具温度40-60℃。优选的注射参数为:注射温度为160℃,注射压力175bar,注射速度为75%,模具温度50℃。
[0013]
进一步地,所述的注射成形用铝合金生坯的脱脂工艺分为溶剂脱脂和热脱脂两个步骤,其中溶剂脱脂的溶剂为正庚烷,温度40-50℃,脱脂时间为9-15h。优选的温度为45℃,
优选的脱脂时间为9h。
[0014]
进一步地,所述的注射成形用铝合金热脱脂与烧结过程采用一步法完成,具体工艺参数为:以0.5-2℃/min升温至190-210℃,保温20-40min;以0.5-2℃/min升温至280-320℃,保温120-210min;以0.5-2℃/min升温至360-400℃,保温120-180min;以0.5-2℃/min升温至440-460℃,保温210-240min;以1-10℃/min的速率升至温度550-570℃,保温30-60min;以1-10℃/min升温至600-630℃,保温60-180min;以1-3℃/min缓慢冷却到200℃再随炉冷却。热脱脂过程与烧结过程均采用高纯氮气保护,氮气速率为0.1-1ml/min。
[0015]
进一步地,所述的注射成形用铝合金的固溶处理制度为:以1-5℃/min速率升温至450-470℃,保温60-240min,水淬。
[0016]
进一步地,所述的注射成形用铝合金的时效处理制度为:以1-5℃/min速率升温至150-170℃,时效时间2-24h。
[0017]
说明1:相比粉末压制烧,注射成形铝合金在的溶剂和热脱脂后,留有大量孔孔隙,因此需要在烧结过程中产生更多得液相,来实现致密化烧结。而压制烧结合金实现致密化需要的液相量一般为20vol.%。此外,考虑到注射成形坯体在脱脂后空隙量较多,注射成形铝合金体系中的液相量应保持在在30-40vol.%左右。
[0018]
其中,zn和mg元素是该体系中主要的强化元素,在时效过程中形成mgzn2相从而使合金的强度得到提高;此外,mg元素可以破除铝粉表面的氧化膜;zn和cu元素是该体系中主要的液相形成元素,用于液相辅助烧结过程中铝合金的致密化;微量合金元素sn可以降低烧结过程中生成液相的表面张力,使合金液相更容易填充孔隙,同时可以降低al颗粒的氮化速率,改善烧结性能。
[0019]
说明2:相比于采用合金粉,原材料采用单质粉或二元合金粉,有利于根据不同的使用需求调整合金的具体成分,满足多种性能需求。同时,所选用原料粉末均为常见的商用铝合金粉末,成本比定制多元铝合金粉末会大幅下降。
[0020]
说明3:由于铝合金中al-zn、al-mg和al-cu的共晶温度较低,分别为380℃、460℃和550℃,为了减少脱脂过程中液相量形成对脱脂过程的影响,本发明选用石蜡、高密度聚乙烯、聚丙烯和硬脂酸这四种具有较低挥发温度的粘结剂。此外,这几种粘结剂具有不同的挥发温度,在脱脂过程中可形成脱脂温度梯度,有利于铝合金的坯体在脱脂过程中保持形状。其中,硬脂酸主要起到润滑剂的作用。
[0021]
说明4:混炼的温度与时间将直接影响喂料的质量,混炼温度过高会导致粘结剂的挥发,使得确定的粉末装载量有所偏差,混炼温度过低,粘结剂不能充分的熔化来润湿粉末。混炼时间过长,导致剪切过度,使得粉末黏度过大,时间过短混合不够均匀。
[0022]
说明5:注射温度影响了粉末动性以及充模性;适当的注射压力可挤压出样品内部的气泡,减少边缘飞边现象,保证样品表面光洁度;合理的注射速度,可以有效地提高注射样品的效率和质量。上述注射成形工艺参数都可以制备表面完整光洁,强度较高的铝合金生胚。
[0023]
说明6:随着脱脂温度的升高以及脱脂时间的延长,粘结剂可溶解组元(pw和sa)的脱除率在不断的增大;但在特定温度下脱脂时间也不宜过长,否则溶剂会向粘结剂中扩散,增加注射坯的c含量,不利于后续的热脱脂和烧结;而在45℃下脱脂8~10h的注射坯脱脂率较高且不会产生明显缺陷,有利于后续的热脱脂和烧结正常进行。
[0024]
说明7:在脱脂阶段应采用较慢的升温速率(0.5-1℃/min),防止脱脂胚出现鼓泡、开裂、变形等问题;在烧结过程采用较快的升温速率可以抑制在烧结过程中生成的液相向基体中扩散,使得孔隙更充分的被液相填充,获得更致密的组织。450-470℃和550-570℃分别对应al-mg、al-cu共晶液相生成的温度区间,在这几个温度区间进行保温,有利于合金中液相的充分生成,促进烧结体的致密化。在冷却过程中,采用较慢的降温速率可以在孔隙处析出非均质相,从而大大减小孔隙,获得更高的致密度。
[0025]
本发明和现有技术相比所具有的有益效果在于:
[0026]
1.本发明成功将注射成形技术应用于al-zn-mg-cu系铝合金的制备,并实现致密化烧结;相比于传统的al-zn-mg-cu系铝合金制备方法,注射成形方法具有生产效率高,材料利用率高,成分分布均匀,不需后续加工等特点,在批量制备小型复杂形状铝合金零部件方面具有独特优势。
[0027]
2.本发明所述方法制备的铝合金材料微观组织均匀,致密度可达98.2%,抗拉强度可达455mpa;可实现高性能复杂形状铝合金零部件的低成本大批量制备。
附图说明
[0028]
附图1注射成形铝合金烧结后的微观组织形貌;
[0029]
附图2注射成形铝合金经过固溶和时效处理后的微观形貌。
具体实施方式
[0030]
实施例1:注射成形al-zn-mg-cu系铝合金体系的成分优化
[0031]
a.配料:选择不同的al-zn-mg-cu系合金成分;将合金粉末按照成分配比在混料机上干混2h制得预混合粉;粘结剂采用蜡基粘结剂,各组元按质量百分比石蜡∶高密度聚乙烯∶硬酯酸∶聚丙烯=62∶21∶9.5∶7.5称量,粉末和粘结剂的计量精度为0.1g。
[0032]
b.喂料制备:将混合均匀得混合粉与配制好的粘结剂按62vol.%的粉末装载量称量,按步骤置于cf-1l型强力加压式密炼机中进行混炼,混炼温度为165℃,经2h混合物形成熔融态,充分混匀后,取出冷却。
[0033]
c.脱脂-烧结:溶剂脱脂采用正庚烷,溶脱温度45℃,溶脱时长9h;热脱脂和烧结气氛采用高纯氮气,热脱脂升温制度为以2℃/min升温至200℃,保温30min;以1℃/min升温至300℃,保温180min;以1℃/min升温至380℃,保温180min;以1℃/min升温至460℃,保温200min;以10℃/min的速率升至温度550-570℃,保温30-60min;以10℃/min升温至620℃,保温60min,以2℃/min降至200℃。
[0034]
表1为不同成分的铝合金成分烧结后的致密度与抗拉强度
[0035][0036]
由表1可以看出,经优化后的铝合金烧结后致密度最大值高达98.0%,抗拉强度可达455mpa。
[0037]
实施例2:注射成形铝合金粘结剂体系的成分优化
[0038]
a.配料:将al-zn-mg-cu-sn各元素按照质量比89:6.5:2.3:2:0.2配好后在混料机上干混2h制得预混合粉;粘结剂采用蜡基粘结剂,各组元按质量百分比按表2称量,粉末和粘结剂的计量精度为0.1g。
[0039]
b.喂料制备:将混合均匀得混合粉与配制好的粘结剂按62vol.%的粉末装载量称量,按步骤置于cf-1l型强力加压式密炼机中进行混炼,混炼温度为165℃,经2h混合物形成熔融态,充分混匀后,取出冷却。
[0040]
c.注射成形:将喂料破碎后,倒入em120-svp/2型注射机料筒中,进行注射操作,对比不同配比的粘结剂对注射过程的影响,以及注射生坯的完整性、光洁度和强度。注射温度为160℃,注射压力175bar,模具温度50℃。经实验对比得出,优选的粘结剂的质量百分比成分为:石蜡:58-64%、硬脂酸7.5-13.5%、高密度聚乙烯20-23%、聚丙烯5.5-8.5%。
[0041]
表2不同成分的粘结剂体系对脱脂与烧结性能的影响
[0042]
再多了解一些
本文用于企业家、创业者技术爱好者查询,结果仅供参考。