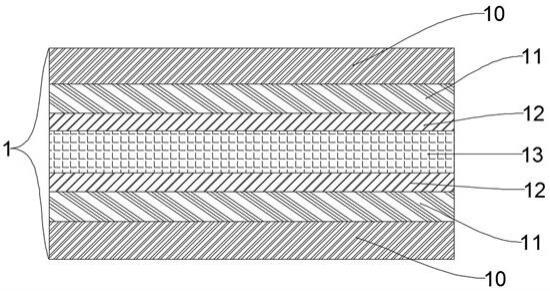
1.本发明涉及贴合膜技术领域,尤其是涉及一种车内织物用贴合膜及复合织物的生产工艺。
背景技术:
2.车内织物均由玻璃纤维或聚氨酯纤维制得,现有的车内织物之间粘贴牢固性不佳,长期使用过程中产品易出现脱落的现象,耐用性下降导致贴合膜的应用广泛性受限。贴合膜的防水性和隔音效果也是应用推广的重要因素之一,因此需要对现有贴合膜的性能进一步改进。
3.现有技术中,公开号为cn203543754u的专利公开了一种可成型防漏泡汽车地毯,包括三层结构,上层为起绒地毯面料层,中间层为pe/pa/pe共挤膜层,底层为可成型热熔毡层。该pe膜与汽车地毯粘合后的剥离力在3~5n,粘合性和耐用性不佳。
技术实现要素:
4.本发明的目的之一在于克服现有技术中存在的缺陷,提供一种车内织物用贴合膜,粘接牢固性更强。
5.为实现上述技术效果,本发明的技术方案为:一种车内织物用贴合膜,为多层共挤膜,由内至外包括阻隔芯层、聚乙烯层和表面粘接层;所述聚乙烯层的主要组成包括lldpe;所述表面粘接层为马来酸酐和/或乙烯丙烯酸甲酯接枝的改性层,所述改性层的基材为pet或lldpe;所述阻隔芯层与聚乙烯层通过内粘接层连接。
6.车内织物用贴合膜的总膜厚为40~60μm,车内织物用贴合膜为对称结构,共挤膜为七层、九层或十一层。阻隔芯层为尼龙层,pa为均聚尼龙,或均聚尼龙和共聚尼龙混合,均聚尼龙和共聚尼龙的质量比为(2~3):1。均聚尼龙和共聚尼龙混合能改善阻隔层的耐温性、韧性、抗穿刺性能和拉伸强度。表面粘接层的维卡软化点小于等于聚乙烯层的维卡软化点。进一步的,聚乙烯层的维卡软化点为100~105℃;表面粘接层的维卡软化点为70~100℃。维卡软化点越高耐高温性能越好。
7.为了提高车内织物用贴合膜的粘接牢固性,且适用于车身不同部件上或饰件上,优选的技术方案为,所述表面粘接层为马来酸酐接枝的改性层,所述改性层的基材为lldpe;所述表面粘接层中马来酸酐的接枝率为1~7%。车内织物常为玻璃纤维或聚氨酯纤维,表面粘接层为马来酸酐接枝的改性层,改性层的基材为lldpe,马来酸酐接枝改性lldpe增加了分子极性,增大了贴合膜与玻璃纤维布或聚氨酯纤维布的相容性,进而增强了贴合膜的粘接牢固性,且基材分子链分支结构降低基材分子的结晶度和结晶速率,有效提高改性层的表面粘度。为了达到最佳的粘接牢固性,且保证贴合膜的力学性能,进一步的,表面粘接层中马来酸酐的接枝率为2~6%。
8.为了提高车内织物用贴合膜的粘接牢固性,且适用于车身不同部件上或饰件上,优选的技术方案为,所述表面粘接层为乙烯丙烯酸甲酯接枝的改性层,所述改性层的基材
为pet,所述表面粘接层中乙烯丙烯酸甲酯的含量为20~35%。表面粘接层为乙烯/丙烯酸甲酯接枝的改性层,改性层的基材为pet,乙烯丙烯酸甲酯接枝的改性层通过乙烯/丙烯酸甲酯与甘油酯缩水得乙烯/丙烯酸甲酯缩水甘油酯,与基材pet混合,基材pet支链上引入官能团,不仅增大了贴合膜与玻璃纤维布或聚氨酯纤维布的相容性,进而增强了贴合膜的粘接牢固性,且乙烯丙烯酸甲酯具有不饱和键与聚乙烯层的lldpe交联反应,乙烯/丙烯酸甲酯缩水甘油酯含有环氧基团和pet分子链末端的羟基和羧基交联反应,粘合面的聚合物相互结合及穿插,形成聚合物网络,进一步增强了贴合膜的粘接牢固性。为了达到最佳的粘接牢固性,且保证贴合膜的力学性能,进一步的,表面粘接层中乙烯丙烯酸甲酯的含量为25~33%。
9.为了表面粘接层熔融进入车内织物纤维的空隙中,提高贴合膜与车内织物纤维的接触面积及粘接牢固性,优选的技术方案为,所述马来酸酐接枝的改性层密度为0.929~0.933g/cm3,熔融指数为3.2~4.5g/10min。为了贴合膜实现最优的粘接牢固性能,进一步的,马来酸酐接枝的改性层型号为lldpebynel41e755。
10.为了表面粘接层熔融进入车内织物纤维的空隙中,提高贴合膜与车内织物纤维的接触面积及粘接牢固性,优选的技术方案为,所述乙烯丙烯酸甲酯接枝的改性层密度为0.945~0.955g/cm3,熔融指数为1.5~3.5g/10min。为了贴合膜实现最优的粘接牢固性能,进一步的,所述乙烯丙烯酸甲酯接枝的改性层型号为ema lotryl29ma03t。
11.为了提高贴合膜加工稳定性及贴合膜抗皱性,优选的技术方案为,所述聚乙烯层的主要组成lldpe、mlldpe和ldpe的质量比为(2~3):(2~3):1。mlldpe能有效改善贴合膜的力学性能和透明度有助于减薄膜厚实现轻量化,其分子量分布窄,支链少不易加工成膜,过多不利于贴合膜与织物粘合相容或交联反应,对粘接性有消极影响;lldpe有效改善贴合膜的耐刺穿性和撕拉强度,提高贴合膜的耐用性,lldpe支链多与织物复合使用时,通过与表面粘接层融合进一步提高与织物的相容性,或与乙烯/丙烯酸甲酯接枝的改性层形成交联网状结构,增强贴合膜的粘接牢固性。ldpe的添加有效改善mlldpe的加工性能。
12.为了聚乙烯层熔融进入车内织物纤维的空隙中,进一步提高贴合膜与车内织物纤维的接触面积及粘接牢固性,优选的技术方案为,所述mlldpe的密度为0.910~0.920g/cm3,熔融指数为0.9~1.3g/10min;所述ldpe的密度为0.910~0.925g/cm3,熔融指数为1.5~2.1g/10min;所述lldpe的密度为0.915~0.935g/cm3,熔融指数为1.8~2.2g/10min。进一步的,mlldpe的熔融指数为1.1~1.3g/10min;ldpe的熔融指数为1.8~2.1g/10min;lldpe的熔融指数为1.9~2.2g/10min。
13.为了提高聚乙烯层与阻隔芯层的粘接牢固性,进一步提高贴合膜与织物的粘接牢固性及相容性,优选的技术方案为,所述内粘接层为马来酸酐接枝改性线性低密度聚乙烯,或马来酸酐接枝线性低密度聚乙烯和lldpe混合;所述马来酸酐接枝线性低密度聚乙烯和lldpe的质量比为1:(0.5~2.5)。内粘接层中马来酸酐接枝改性线性低密度聚乙烯的含量越高越有利于聚乙烯层与阻隔层的粘接牢固性,为了贴合膜的加工稳定性,符合粘接牢固性能的条件下同时满足生产经济性,进一步的,马来酸酐接枝线性低密度聚乙烯和lldpe的质量比为1:(0.8~2.0)。进一步的,马来酸酐接枝线性低密度聚乙烯的密度为0.910~0.921g/cm3,熔融指数为1.6~2.1g/10min。
14.优选的技术方案为,所述马来酸酐接枝改性线性低密度聚乙烯中马来酸酐接枝含
量为2000~8000ppm。
15.本发明的目的之二在于克服现有技术中存在的缺陷,一种车内织物用贴合膜复合织物的生产工艺,包括以下步骤:
16.s1:制备第一织物和第二织物;
17.s2:依次叠合所述第一织物、上述的车内织物用贴合膜和第二织物,并热复合;
18.所述热复合温度为145~155℃,压强为100~120mpa。
19.第一织物和第二织物均为pet纤维或玻璃纤维。车内织物用贴合膜与被粘合材料复合成一体。热复合温度温度过小,贴合膜中每层的熔融温度和熔融流动速率均不相同,层层熔融不够充分,对交联或相互作用相容性有消极影响,且聚合物过早冷却,进而对织物与贴合膜的粘接牢固性有消极影响;热复合温度温度过大,贴合膜受热变形,且易导致贴合膜中部分聚合物分解,影响织物与贴合膜的粘接牢固性。复合压强过小贴合膜熔融进入织物的内部间隙和深度均不充分,对贴合膜的粘接牢固性有消极影响;复合压强过大,织物变形,影响织物纤维的排列结构,对织物与贴合膜的粘接牢固性有消极影响。
20.本发明的优点和有益效果在于:
21.本发明车内织物用贴合膜结构合理,实现了贴合膜的轻量化,表层粘接层通过马来酸酐和/或乙烯丙烯酸甲酯接枝的改性层,增强贴合膜的粘接强度及与织物的相容性;聚乙烯层通过lldpe进一步提高贴合膜与织物的粘接牢固性及相容性。
附图说明
22.图1是本发明实施例1车内织物用贴合膜的结构示意图;
23.图2是本发明实施例1汽车地毯的结构示意图。
24.图中:1、车内织物用贴合膜;2、pet纤维毛毡;3、玻璃纤维布;10、表层粘接层;11、聚乙烯层;12、内粘接层、13、阻隔芯层。
具体实施方式
25.下面结合附图和实施例,对本发明的具体实施方式作进一步描述。以下实施例仅用于更加清楚地说明本发明的技术方案,而不能以此来限制本发明的保护范围。
26.定义
27.在本公开中,术语“ldpe”系指低密度聚乙烯。
28.在本公开中,术语“lldpe”系指线性低密度聚乙烯,线性低密度聚乙烯在结构上不同于一般的低密度聚乙烯,因为不存在长支链。
29.在本公开中,术语“mlldpe”系指以茂金属配位化合物为催化剂,进行乙稀聚合反应所制的聚合物。
30.在本公开中,术语“pa”系指聚酰胺,又称尼龙,是大分子链中含有酰胺基因的高分子聚合物制成的塑料总称。
31.茂金属线性低密度聚乙烯由埃克森美孚公司生产,商品牌号为1018mf;
32.低密度聚乙烯由埃克森美孚公司生产,商品牌号为100ac;
33.线性低密度聚乙烯由埃克森美孚公司生产,商品牌号为1002xbu;
34.马来酸酐接枝线性低密度聚乙烯由利安得巴塞尔公司生产,商品牌号为
px3838x01;
35.均聚尼龙由巴斯夫生产,商品牌号为b40ln;
36.共聚尼龙由巴斯夫生产,商品牌号为c40ln。
37.车内织物用贴合膜的制备方法:
38.表层粘接层的挤出温度为230~240℃;聚乙烯层的挤出温度为210~220℃;内粘接层的挤出温度为220~230℃;阻隔芯层的挤出温度为250~260℃。
39.实施例1
40.如图1~2所示,车内织物用贴合膜为七层共挤膜,阻隔芯层13、聚乙烯层11和表面粘接层10,阻隔芯层13为均聚尼龙和共聚尼龙混合,均聚尼龙和共聚尼龙的质量比为7:1,聚乙烯层11的组成lldpe、mlldpe和ldpe的质量比为2:2:1;表面粘接层10为马来酸酐接枝的改性层,改性层的基材为lldpe,表面粘接层10中马来酸酐的接枝率为4.2%,表面粘接层10型号为lldpebynel41e755;阻隔芯层13与聚乙烯层11通过内粘接层12连接,内粘接层12为马来酸酐接枝线性低密度聚乙烯和lldpe混合;马来酸酐接枝线性低密度聚乙烯和lldpe的质量比为1:1;马来酸酐接枝线性低密度聚乙烯中马来酸酐接枝含量为7000ppm。
41.马来酸酐接枝的改性层密度为0.932g/cm3,熔融指数为4.2g/10min。
42.聚乙烯层11的组成lldpe的密度为0.918g/cm3,熔融指数为2g/10min,mlldpe的密度为0.918g/cm3,熔融指数为1g/10min,ldpe的密度为0.923g/cm3,熔融指数为2g/10min。
43.内粘接层12中马来酸酐接枝线性低密度聚乙烯的密度为0.92g/cm3,熔融指数为1.8g/10min,lldpe的密度为0.918g/cm3,熔融指数为2g/10min。
44.车内织物用贴合膜为对称设置,阻隔芯层13两侧聚乙烯层11的层厚均相等,表面粘接层10的层厚均相等,贴合膜的总膜厚为55μm,两层表层粘接层10的层厚均为8μm,两层聚乙烯层11的层厚均为6.25μm,两层内粘接层12的层厚均为5μm,阻隔芯层13的层厚为16.5μm。
45.上述车内织物用贴合膜的制备方法:表层粘接层10的挤出温度为235℃;聚乙烯层11的挤出温度为215℃;内粘接层12的挤出温度为225℃;阻隔芯层13的挤出温度为255℃。
46.车内织物用贴合膜复合汽车地毯的生产工艺,包括以下步骤:
47.s1:制备pet纤维毛毡2和玻璃纤维布3;
48.s2:依次叠合pet纤维毛毡2、上述的车内织物用贴合膜1和玻璃纤维布3,并热复合;热复合温度为150℃,压强为105mpa。
49.实施例2
50.实施例2基于实施例1,区别在于,聚乙烯层的主要组成lldpe、mlldpe和ldpe的质量比为1:2:1。
51.实施例3
52.实施例3基于实施例1,区别在于,马来酸酐接枝线性低密度聚乙烯和lldpe的质量比为1:2.5。
53.实施例4
54.实施例4基于实施例1,区别在于,车内织物用贴合膜复合汽车地毯的生产工艺中复合的压强为95mpa。
55.对比例1
56.对比例1基于实施例1,区别在于,未包括表层粘接层,车内织物用贴合膜为七层共挤膜,表面为聚乙烯层,pe层与次外层的聚乙烯层组成相同,表面聚乙烯层的组成lldpe、mlldpe和ldpe的质量比为2:2:1。共挤膜的层叠结构为pe/pe/tie/pa/tie/pe/pe。
57.车内织物用贴合膜为对称设置,阻隔芯层两侧聚乙烯层的层厚均相等,表面聚乙烯层的层厚均相等,贴合膜的总膜厚为55μm,两层表面聚乙烯层的层厚均为8μm,两层聚乙烯层的层厚均为6.25μm,两层内粘接层的层厚均为5μm,阻隔芯层的层厚为16.5μm。
58.对比例2
59.对比例2基于实施例1,区别在于,聚乙烯层未包括lldpe,聚乙烯层的主要组成mlldpe和ldpe的质量比为2:1。
60.实施例5
61.实施例5基于实施例1,区别在于,表面粘接层10为乙烯丙烯酸甲酯接枝的改性层,改性层的基材为pet,表面粘接层中乙烯丙烯酸甲酯的质量为30%。乙烯丙烯酸甲酯接枝的改性层密度为0.95g/cm3,熔融指数为3.1g/10min,乙烯丙烯酸甲酯接枝的改性层型号为ema lotryl 29ma03t。其他层的组成不变,贴合膜的总膜厚和各层层厚均不变。
62.实施例6
63.实施例6基于实施例5,区别在于,聚乙烯层的主要组成lldpe、mlldpe和ldpe的质量比为1:2:1。
64.实施例7
65.实施例7基于实施例5,区别在于,马来酸酐接枝线性低密度聚乙烯和lldpe的质量比为1:2.5。
66.实施例8
67.实施例8基于实施例5,区别在于,车内织物用贴合膜复合汽车地毯的生产工艺中复合的压强为95mpa。
68.对比例3
69.对比例3基于实施例5,区别在于,聚乙烯层未包括lldpe,聚乙烯层的主要组成mlldpe和ldpe的质量比为2:1。
70.汽车地毯试样的检测方法:
71.剥离强力的测定:检测标准iso11857:1999。
72.实施例1~4和对比例1~2的检测数据如下:
73.测试项目剥离力/n实施例128实施例223实施例321实施例420对比例15对比例216
74.实施例5~8和对比例1、3的检测数据如下:
75.测试项目剥离力/n实施例530
实施例625实施例722实施例821对比例15对比例318
76.车内织物用贴合膜试样的检测方法:
77.1、水蒸气透过量:检测标准gb/t1037-1988;
78.2、氧气透过量:检测标准gb/t1038-2000;
79.3、拉伸强度测定:测试标准gb/t1040.3-2006;
80.4、断裂伸长率测定:测试标准gb/t1040.3-2006。
81.实施例1~3和对比例1~2的检测数据如下:
[0082][0083][0084]
实施例5~7和对比例1、3的检测数据如下:
[0085][0086]
以上所述仅是本发明的优选实施方式,应当指出,对于本技术领域的普通技术人员来说,在不脱离本发明技术原理的前提下,还可以做出若干改进和润饰,这些改进和润饰也应视为本发明的保护范围。
再多了解一些
本文用于企业家、创业者技术爱好者查询,结果仅供参考。