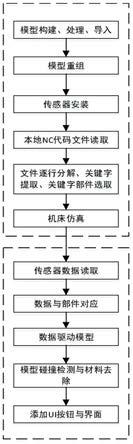
1.本发明涉及仿真与监控系统技术领域,尤其涉及一种机床仿真与监控方法。
背景技术:
2.随着“中国制造2025”、“工业4.0”概念的深入,智能工厂的无人化管理成为高端企业研究的重点,尤其近些年数字孪生技术的快速发展,目前在各个领域的应用也逐渐趋于成熟。数字孪生的重点在于数据交互,随着传感器和通信技术的快速发展解决了数字孪生技术在获取数据方面的难点问题,使得此项技术可以在数字化工厂得到应用。
3.目前对于数控机床加工,为了防止发生撞刀等现象对机床和刀具造成损伤,对nc代码仿真是必不可少的一步。现有的仿真软件对nc代码仿真速度缓慢,急需一种快速高效的仿真方式,在仿真过后实际生产过程运行状态的监控,目前也是无人化管理研究的重点,对机床加工过程的可视化行为监控技术亟待突破。
技术实现要素:
4.本发明的目的在于克服上述现有技术存在的问题和缺陷,提供一种机床仿真与监控方法。
5.本发明通过读取nc代码文件和传感器数据完成机床仿真与监控,利用检测碰撞模型在发生撞刀时控制机床急停,解决机床仿真速度慢、可视化监控程度低和反应不及时造成撞刀等问题。
6.为达到上述目的,本发明采用的技术方案为:
7.一种机床仿真与监控方法,包括如下步骤:
8.步骤s1,构建机床三维模型,并通过3d max中对其渲染,最后导入仿真软件中;
9.步骤s2,在仿真软件中对机床模型所有零部件重新分解与重组;
10.步骤s3,将需要监控信息安装传感器;
11.步骤s4,根据机床nc代码,利用软件读取文件,通过关键字对机床运动件进行驱动仿真;
12.步骤s5,将步骤s3获得的数据信号传输至仿真软件中,驱动软件中的虚拟设备运动,实现对机床运动的实时监控;
13.步骤s6,对所有零件、刀具和加工材料构建碰撞检测模型,并对刀具和加工材料赋予物理特性,使其达到加工时切削效果;
14.步骤s7,对仿真软件添加ui按钮,当步骤s6中刀具与机床检测模型达到设计的碰撞临界值时,触发该ui按钮,该按钮向与pc连接的plc发出指令控制机床急停;
15.步骤s8,添加ui界面,在ui界面中显示运行的nc代码和重要机床数据,并绘制折线图。
16.进一步地,步骤s1中,构建三维模型软件为solidworks;仿真软件为unity 3d。
17.进一步地,步骤s2“在仿真软件中对机床模型所有零部件重新分解与重组”具体包
括如下步骤:
18.步骤1):将所有零部件整合为机床模型;
19.步骤2):把机床模型分为固定件、旋转件、移动件;
20.步骤3):在固定件中分为箱体、床身,旋转件中分为主轴、丝杠、刀具转台,在移动件中分为移动滑台、导轨。
21.进一步地,步骤s3中,监控信息具体为:主轴的转速与位置、滑台的速度与位置、刀具速度与位置、工件速度与位置。
22.进一步地,步骤s4“利用软件读取文件,通过关键字对机床运动件进行驱动仿真”具体包括如下步骤:
23.步骤1):通过仿真软件对nc代码文件读取;
24.步骤2):将文件逐行读取,并提取关键字,如m、t、g、f、s、x、z、r;
25.步骤3):对关键字赋予对应意义,并利用关键字后面数据对其对应模块驱动仿真。
26.进一步地,步骤s6中碰撞检测模型构建方法为层次包围盒检测法。
27.本发明相比于现有技术,具有以下显著优势
28.(1)机床nc仿真速度快,一帧(0.02s)可以执行一个动作,可在很短时间内检测是否有碰撞并标记碰撞点;
29.(2)数字孪生模型与实际加工过程同步,操作者可远程观察机床各项数据和运行进度;
30.(3)添加模型碰撞检测,采用层次包围盒检测法在刀具与机床将要发生碰撞时pc自动发出指令控制机床停机。
附图说明
31.图1为本发明的方法流程图。
32.图2为本发明的虚拟模型构建流程图。
33.图3为本发明的机床模型部件划分方案图。
34.图4为本发明的nc代码关键字与模型对应图。
35.图5为本发明的实验平台数据通讯示意图。
具体实施方式
36.为使本技术实施例的目的、技术方案和优点更加清楚,下面将结合本技术实施例中的附图,对本技术实施例中的技术方案进行清楚、完整地描述,显然,所描述的实施例是本技术一部分实施例,而不是全部的实施例。基于本技术中的实施例,相同方法不同对象的所有其他实施例,都属于本技术保护的范围。
37.本实施例使用的一种虚实结合数字孪生仿真实验平台,包括:位移传感器、速度传感器、plc、装有上述软件的pc,其中所述plc与位移传感器、速度传感器通过以太网分别接入pc。
38.如图1所示,为本发明的一种机床仿真与监控方法,步骤是:首先利用solidworks软件对被控设备零部件进行三维建模,把所有零件配合在一起后输出step格式到3d max软件中对零部件赋予材质及贴图,利用polygon cruncher优化模型三角形面片数量,优化后
导出为fbx格式文件导入unity 3d中。模型构建流程见图2。
39.在unity 3d中重组模型,重组后模型划分见图3。在层级列表中创建一级单元命名为机床,把导入后所有文件整体拖入到一级单元机床中;在一级单元内创建两个二级单元,分别命名为固定件和运动件,把箱体、床身、灯、把手整体拖入到二级单元固定件中;在二级单元运动件中创建两个三级单元,分别命名为转动件和移动件,把主轴、丝杠、刀具转台整体拖入到三级单元转动件中,把刀具滑台、拖板整体拖入到三级单元移动件中。
40.虚拟机床模型分解与重组完成后对需要的数据安装传感器,包括主轴转速传感器、丝杠转速传感器、刀具转台角度传感器、刀具滑台距离传感器、拖板距离传感器、主轴电流传感器和刀具温度传感器。
41.创建ui界面,在该界面中添加文本栏,添加文本栏脚本读取本地nc文件显示在该文本栏,另添加脚本,逐行读取nc文件,提取出nc代码中关键字m、t、g、f、s、x、z、r,把关键字与重组后模型对应,对应关系见图4,并利用关键字后面数据对模型驱动仿真,例:s800表示主轴转速800r/min。全选所有模型,添加刚体组件,添加脚本挂在机床上检测刚体碰撞,采用oncollisionenter回调方式在碰撞发生点用红色标记。
42.如图5所示,为发明的实验平台数据通讯示意图。在数据传输之前需要在unity 3d中添加arduino通讯协议包,以有线的方式把传感器、plc和pc连接,在unity 3d中对传入数据编辑成脚本,按照图4的对应方式对应到模型驱动模型运动。
43.选择刀具和加工材料,添加碰撞器组件collider进行检测,对加工材料添加一个检测碰撞的脚本组件cubecollision,在刀具和加工材料碰撞时对材料碰撞部位自动去除。
44.添加ui按钮,对按钮添加脚本寻找刀具和机床模型,对刀具和机床模型添加碰撞网络,其中刀具碰撞网格设置为刀具模型尺寸的1.2倍,采用层次包围盒检测法,在碰撞发生时触发按钮向plc发出信号控制机床急停。
45.新建一个空的gameobject,在这个gameobject上填加linerenderer组件并设置materials生成图片材质,点击输入的主轴电流和刀具温度数据进入c#脚本编译界面,然后将上述脚本挂在这个gameobject上面,以折线图形式显示主轴电流和刀具温度数据。
再多了解一些
本文用于企业家、创业者技术爱好者查询,结果仅供参考。