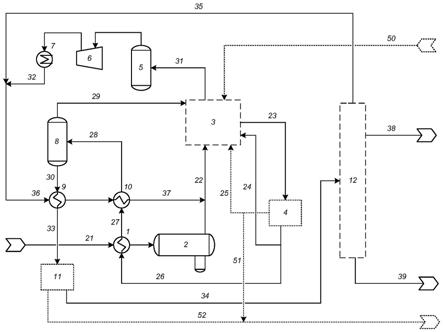
1.本发明涉及石油化工领域,更具体地,涉及一种硫酸烷基化反应方法和装置。
技术背景
2.随着国内各行业的蓬勃发展,以及对环境保护的日益重视,汽油升级已成为各大国内石油企业面临的重要课题之一。烷基化汽油通过异丁烷和烯烃发生烷基化反应得到,不含芳烃、硫和烯烃等杂质,且辛烷值较高。不论是从抗爆震性能还是芳烃含量、烯烃含量、硫含量的角度出发,烷基化汽油都是一种理想的清洁汽油调和组分。
3.烷基化技术包括液体酸烷基化技术和固体酸烷基化技术,主要使用四种催化剂:硫酸、氢氟酸、固体酸和离子液体,而工业化应用较为成熟的技术则是硫酸法和氢氟酸法烷基化。但考虑到氢氟酸催化剂的挥发性、腐蚀性和毒性,氢氟酸法烷基化技术基本不再拥有广阔的发展前景。
4.作为成熟应用的工艺技术,不同公司研发的硫酸法烷基化技术的差异主要在反应单元、制冷单元和分馏单元等方面。反应进料的烷烯比通常控制在7~10,通过机械搅拌、静态混合、多点进料等方式,提高反应器内部的烷烯比,实现良好的酸烃分布和传质效果,抑制二次反应。硫酸法烷基化技术的反应温度较低,一般控制在-4~10℃,烷基化反应为放热反应需要及时移走反应热,通常采用流出物制冷、汽化取热制冷技术和压缩制冷工艺实现反应取热。
5.cn105219428a公开了一种硫酸烷基化反应的方法,在反应区内异丁烷、丁烯在硫酸的催化作用下充分接触进行烷基化反应;从反应区出来的流出物和硫酸催化剂一起进入酸烃分离器,分离出的硫酸打回反应器循环使用,烷基化油去产品分离系统,异丁烷循环进入反应器,轻烃去气压机系统进行分离,异丁烷冷却后返回反应器做循环冷剂,丙烷排出系统。
6.硫酸烷基化技术中大多采用烃自汽化取热流程。反应流出物进入闪蒸罐,闪蒸罐内的气相进入压缩机升压冷却后再次循环进入闪蒸罐进行低压闪蒸。气相返回压缩机系统,液相返回反应单元。含有轻烃、烷基油和少量酸的反应产物经过酸烃聚结、原料换热后直接进入产物分馏单元中,分离出的异丁烷换热后,与原料混合后提高反应进料的烷烯比。该流程虽然通过汽化取热、压缩制冷等技术手段取走反应热量,但仍然存在几个问题:烃自汽化得到的轻烃气相并没有全部返回反应单元,部分气相在压缩机系统中自循环。反应产物中含有大量的正/异丁烷,造成分馏单元的能耗占装置总能耗60%以上。
技术实现要素:
7.本发明要解决的技术问题之一是在现有技术的基础上,提供一种硫酸烷基化反应方法,该方法可显著降低能耗。
8.本发明要解决的技术问题之二是提供一种硫酸烷基化反应装置,该装置投资低、操作费用低。
9.本发明要解决的技术问题之三是提供一种硫酸烷基化反应的取热方法。
10.一种硫酸烷基化反应方法,碳四原料进入烷基化反应器,异丁烷和丁烯在硫酸催化剂的作用下进行烷基化反应,反应物流经气液分离得到轻烃和液相物流,轻烃去气压机系统做循环冷剂,液相物流进入酸烃一级分离器,分离出的硫酸返回烷基化反应器循环使用,分离出的粗反应产物经酸烃二级分离脱除微量酸后进入产物分馏单元,分离得到的异丁烷返回烷基化反应器,分离出的正丁烷和烷基化油产品出装置。
11.优选地,所述的粗反应产物先经闪蒸分离出第二股轻烃,所述的第二股轻烃作为循环异丁烷返回烷基化反应器中;其余液相物流经酸烃二级分离脱除微量酸后进入产物分馏单元。
12.一种硫酸法烷基化反应装置,包括烷基化反应器,所述的烷基化反应器设有原料入口、气相出口和液相产物出口,与烷基化反应器液相产物出口依次相通的酸烃一级分离器、反应产物闪蒸罐、酸烃二级分离器和分馏单元;与烷基化反应器的气相出口依次相通的压缩机入口缓冲罐、制冷压缩机、冷剂冷却器和烷基化反应器原料入口。
13.一种硫酸烷基化反应的取热方法,来自烷基化反应器的轻烃经缓冲罐进入压缩机,经升压升温到50-90℃后,经取热器冷却降温到35-55℃,返回所述的烷基化反应器中。
14.本发明提供的硫酸烷基化反应方法和装置的有益效果为:
15.与现有技术相比,本发明提供的硫酸烷基化反应方法减少了来自产物分馏单元的循环异丁烷的量,显著降低了产物分馏单元的处理量,有效降低了产物分馏单元分离过程的能耗,产物分馏单元的能耗占硫酸烷基化装置总能耗60%以上,因此显著降低了烷基化反应装置总能耗。显著减少了压缩系统中循环轻烃量,降低设备投资。同时也充分利用反应产物的冷量。因此,本发明提供的硫酸烷基化反应方法和装置对硫酸法烷基化技术的节能有显著效果,并且降低了装置投资。
16.本发明提供的硫酸烷基化反应装置的取热方法的有益效果为:
17.本发明提供的硫酸烷基化反应装置的取热方法的压缩机出口的循环冷剂不再闪蒸,直接与循环异丁烷混合返回反应单元,增加反应进料烷烯比,有利于烷基化反应;另外显著减少了压缩系统中循环轻烃量,降低了装置投资。取热效果好。
附图说明
18.图1为硫酸烷基化反应方法一种实施方式的流程示意图。
19.图2为硫酸烷基化反应方法第二种实施方式的流程示意图。
20.图3为对比例1的硫酸烷基化反应方法的流程示意图。
21.图4为对比例2的硫酸烷基化反应方法的流程示意图。
22.其中:1-原料/反应产物换热器;2-脱水罐;3-烷基化反应器;4-酸烃一级分离器;5-压缩机入口缓冲罐;6-制冷压缩机;7-冷却器;8-反应产物闪蒸罐;9-异丁烷/反应产物预换热器;10-异丁烷/反应产物换热器;11-酸烃二级分离器;12-产物分馏单元;13-冷剂节能罐;21、22、23、24、25、26、27、28、29、30、31、32、33、34、35、36、37、38、39、50、51、52-管线。
具体实施方式
23.以下详细说明本发明的具体实施方式。
24.一种硫酸烷基化反应方法,碳四原料进入烷基化反应器,异丁烷和丁烯在硫酸催化剂的作用下进行烷基化反应,反应物流经气液分离得到轻烃和液相物流,轻烃去气压机系统做循环冷剂,液相物流进入酸烃一级分离器,分离出的硫酸返回烷基化反应器循环使用,分离出的粗反应产物经酸烃二级分离脱除微量酸后进入产物分馏单元,分离得到的异丁烷返回烷基化反应器,分离出的正丁烷和烷基化油产品出装置。
25.本发明提供的方法中,所述异丁烷包括循环异丁烷和补充异丁烷,所述循环异丁烷为来自气压机系统的循环冷剂和来自产物分馏单元的循环异丁烷的混合物,其中异丁烷含量不小于80%,其余为正丁烷、丙烷、和少量戊烷。
26.所述的硫酸催化剂为浓度不小于90%的循环硫酸和/或新酸。
27.所述的碳四原料包括裂解碳四、醚后碳四、催化裂化碳四、甲醇制烯烃碳四和丁烷脱氢碳四中的一种或多种,优选为自醚后碳四或催化裂化碳四。
28.所述的产物分馏单元包括脱异丁烷塔和脱正丁烷塔,反应产物混合物进入脱异丁烷塔分离,塔顶出料为循环异丁烷,塔底物流进入脱正丁烷塔,塔顶出料为正丁烷,塔底出料为烷基化油。
29.优选地,所述的粗反应产物中含有少量硫酸,所述的粗反应产物分成两部分,其中的一部分作为循环烃返回烷基化反应器,另一部分经酸烃二级分离脱除微量酸后进入产物分馏单元。
30.优选地,所述的烷基化反应器包括反应区和闪蒸区,所述的闪蒸区至少一步闪蒸分离,烷基化反应区出口物流在所述的闪蒸区进行气液分离,每步闪蒸分离出的轻烃混合后作为制冷剂进入所述的气压机系统。在反应区内异丁烷、丁烯在硫酸的催化作用下充分接触进行烷基化反应生成烷基化油,在闪蒸区内反应物流分离为气相的轻烃和液相的未反应原料和反应产物。
31.优选地,所述的闪蒸区的操作压力为0.1~1.0mpa。
32.优选地,所述的粗反应产物换热到8~18℃后经闪蒸分离为第二股轻烃和液相组分,所述的第二股轻烃作为循环异丁烷返回烷基化反应器中;所述的液相组分经酸烃二级分离脱除微量酸后进入产物分馏单元。
33.本发明提供的方法中,所述的气压机系统优选采用两级压缩系统,反应产物经气液分离后得到的轻烃进入压缩机入口缓冲罐,也可以直接进入气压机二级压缩入口。
34.优选地,本发明提供的硫酸烷基化反应方法的一种实施方式,所述的制冷剂经缓冲罐进入气压机压缩增压升温到50-90℃,进入换热器冷却到35-55℃,与循环异丁烷混合后返回烷基化反应器,所述的制冷剂的组成为异丁烷、正丁烷、丙烷和少量烷基化产物的混合物。
35.优选地,本发明提供的硫酸烷基化反应方法的第二种实施方式,所述的气压机系统采用两级气体压缩系统,来自烷基化反应器的轻烃进入压缩机入口缓冲罐,所述的粗反应产物换热到8~18℃后经闪蒸分离为第二股轻烃和液相组分,其中,第二股轻烃作为制冷剂直接进入气压机二级压缩入口;所述的液相组分经酸烃二级分离脱除微量酸后进入产物分馏单元。
36.优选地,碳四原料换热到5-15℃后,进入脱水罐脱除其中游离水,然后进入所述的烷基化反应器,烷基化反应器混合进料温度为5~30℃。
37.优选地,所述的粗反应产物先后与碳四原料和循环异丁烯换热后进行闪蒸分离。
38.优选地,所述的制冷剂由异丁烷、正丁烷、丙烷和少量烷基化产物组成,其中异丁烷含量在65%~95%;所述的循环异丁烷由异丁烷、正丁烷、丙烷和少量烷基化产物组成,其中异丁烷含量不小于85%。
39.本发明提供的方法中,所述的烷基化反应器的操作条件为:温度为0~15℃,压力为0.02-0.5mpa,碳四原料中烷烯比控制在1~1.1;所述的循环异丁烷质量流量为原料进料量的0.5~3倍;所述的制冷剂用量为原料进料量的0.5~9倍。
40.本发明提供的方法中,所述的硫酸催化剂为浓度不小于90%的循环硫酸或新酸。
41.本发明提供的方法中,所述的碳四原料包括裂解碳四、醚后碳四、催化裂化碳四、甲醇制烯烃碳四和丁烷脱氢碳四中的一种或多种。
42.本发明提供的方法中,所述的产物分馏单元分馏出的异丁烷组分中,异丁烷纯度在80%~99%,其余组分为丙烷、正丁烷和少量烷基化产物。
43.优选地,所述的烷基化反应器中来自酸烃一级分离器的循环酸体积流量为碳四原料量的30~90倍。
44.优选地,所述烷基化反应器中来自酸烃一级分离器的循环烃流量为碳四原料量的3~15倍。
45.优选地,所述的酸烃一级分离器和所述的酸烃二级分离中分离出的硫酸一部分作为酸耗排出装置,所述的酸耗在50~120kg/t烷基化油。
46.优选地,所述的烷基化反应物流分离出的轻烃经压缩机增压升温到50-90℃,然后经换热冷却降温到35-55℃后返回烷基化反应器。
47.优选地,所述的粗反应产物顺序与碳四原料换热到8-18℃,再与来自产物分馏单元的循环异丁烷换热到20-50℃后进入闪蒸塔中气液分离,分离出的第二股轻烃返回烷基化反应器中;其余液相物流进一步分离。
48.具体地,本发明提供的硫酸法烷基化反应方法的一个优选方案包括以下步骤:
49.1)碳四原料与反应产物换热至温度为5-15℃,在脱水罐中脱除轻烃中的游离水,与冷剂(主要组成为异丁烷、正丁烷、丙烷、戊烷及少量烷基化产物,温度为35-5℃)、循环异丁烷混合后进入烷基化反应器;
50.2)在硫酸的催化下,丁烯和异丁烷反应生成烷基化油,反应后液相物流23经酸烃一级分离4得到含少量酸的粗产物26和硫酸,循环酸25和循环烃24返回烷基化反应器3继续反应,废酸51排出装置;
51.3)烷基化反应器3得到的轻烃闪蒸气31(温度2-10℃)经制冷压缩机6增压,加压后的轻烃(温度为50-90℃)在冷剂冷却器7中冷却至40℃,与循环异丁烷35(温度为35-50℃)混合,与粗反应产物和脱轻烃前粗反应产物降温冷却(温度为5-25℃),与原料混合进入烷基化反应器3;
52.4)自酸烃一级分离4得到的粗反应产物依次与碳四原料、异丁烷换热升温后,经过闪蒸分离出的轻烃组分(温度为5-25℃)返回烷基化反应器,重组分与循环异丁烷换热后经过酸烃二级分离脱除微量酸后进入分馏单元;
53.5)反应产物经分馏分离得到异丁烷组分(主要组成异丁烷、正丁烷、丙烷、戊烷等,温度35-50℃)、正丁烷组分和烷基化油,其中,所述的异丁烷组分与冷剂混合(温度为30-45
℃),经过两级换热降温(温度为5-25℃),与原料混合进入烷基化反应器。
54.本发明提供的硫酸法烷基化反应方法中,所述的压缩机出口的循环冷剂不再闪蒸,直接与循环异丁烷混合返回反应单元,增加反应进料烷烯比,有利于烷基化反应;同时制冷压缩机可以改为一级压缩,减少设备投资;反应产物通过闪蒸分离出部分轻烃后,再返回至分馏单元,减少分馏单元的处理量,进而降低能耗及设备投资;能够将过程能耗降低10%~40%。
55.本发明提供一种硫酸法烷基化反应装置,包括烷基化反应器,所述的烷基化反应器设有原料入口、气相出口和液相产物出口,与烷基化反应器液相产物出口依次相通的酸烃一级分离器、反应产物闪蒸罐、酸烃二级分离器和分馏单元;与烷基化反应器的气相出口依次相通的压缩机入口缓冲罐、制冷压缩机、冷剂冷却器和烷基化反应器原料入口。
56.优选地,碳四原料入口经换热器、脱水罐与所述的烷基化反应器原料入口相通。
57.优选地,所述的酸烃一级分离器之后串联原料/反应产物换热器、异丁烷/反应产物换热器与反应产物闪蒸罐连通,所述的反应产物闪蒸罐经异丁烷/反应产物预换热器与所述的酸烃二级分离器连通。
58.优选地,所述的酸烃一级分离器设有酸出口和混合烃出口分别连通硫酸循环管线和废酸管线,所述的硫酸循环管线与烷基化反应器连通。所述的酸烃二级分离器的硫酸出口连通所述的废酸管线。
59.优选地,所述的烷基化反应器由反应区和闪蒸区组成,在反应区内异丁烷和丁烯在硫酸的催化作用下充分接触进行烷基化反应,生成烷基化油。在闪蒸区进行初步的气液分离。
60.一种硫酸烷基化反应的取热方法,来自烷基化反应器的轻烃经缓冲罐进入气压机系统,经升压升温到50-90℃后,经取热器冷却降温到35-55℃,返回所述的烷基化反应器中。
61.优选地,所述的气压机系统采用两级气体压缩系统,来自烷基化反应器的轻烃进入压机入口缓冲罐,来自烷基化反应器的液相物流进入酸烃一级分离器,分离出的粗反应产物换热到8~18℃后经闪蒸分离为第二股轻烃和液相组分,第二股轻烃作为制冷剂直接进入气压机气压机二级压缩入口;经升压取热后返回所述的烷基化反应器中。其中,烷基化反应器的反应物流经气液分离后得到的轻烃和液相物流。
62.以下参照附图说明本发明提供的硫酸法烷基化反应方法,但本发明并不因此而受到任何限制。
63.附图1为本发明提供的硫酸烷基化反应方法一种实施方式的流程示意图。如图1所示,碳四原料经管线21经过原料/反应产物换热器1与反应产物换热后,在脱水罐2中脱除轻烃中的游离水,与来自管线37的制冷剂和循环异丁烷混合后进入烷基化反应器3。硫酸经管线50、循环酸经管线25进入烷基化反应器3中。在硫酸作用下,进料中的丁烯和异丁烷反应生成烷基化油,反应液相物流经管线23进入酸烃一级分离器4中,分离出的硫酸经管线25返回烷基化反应器3中循环使用,废酸经管线51排出装置;分离出的粗反应产物分成两部分,其中的一部分作为循环烃经管线24返回烷基化反应器,另一部分经管线26依次经过原料/反应产物换热器1、异丁烷/反应产物换热器10换热升温后,进入反应产物闪蒸罐8中气液分离,分离出的轻烃组分经管线29返回压缩机6一级入口;分离出的液相组分经管线30进入换
热器9,与循环异丁烷、制冷剂换热后进入酸烃二级分离器11脱除微量酸后,经管线34进入产物分馏单元12。
64.产物分馏单元12中分离出的异丁烷组分经管线35排出,与制冷剂混合后,作为循环异丁烷先后经过两级换热9、10降温,经管线37与原料混合进入烷基化反应器3中。产物分馏单元12分离的正丁烷组分经管线39和烷基化油经管线40排出装置。
65.自烷基化反应器3闪蒸区得到的轻烃经管线31进入气压机入口缓冲罐5,经气压机6增压,加压升温后的轻烃在冷却器7中冷却,经管线32与来自管线35的循环异丁烷混合,先后经过异丁烷/反应产物预换热器9和异丁烷/反应产物换热器10降温冷却,与碳四原料混合经管线22进入烷基化反应器3。
66.附图2为本发明提供的硫酸烷基化反应方法第二种实施方式的流程示意图,与附图1不同的是,反应粗产物进入反应产物闪蒸罐8中进行气液分离,分离出的轻烃组分经管线29返回气压机6二级入口,经过气压机6压缩升温后进入换热器7中取热,然后返回烷基化反应器3。
67.下面的实施例对本发明提供的硫酸法烷基化反应方法及装置进行进一步的说明。
68.实施例和对比例中:
69.碳四原料a取自中国石油化工股份有限公司燕山分公司炼油厂气分装置醚前碳四组分,质量组成见表1。碳四原料b取自中国石油化工股份有限公司燕山分公司炼油厂mtbe装置的醚后碳四组分,质量组成件表1。
70.硫酸为市售,质量浓度为98wt%。
71.对比例1
72.附图3为对比例1硫酸烷基化反应方法和装置的流程示意图。如附图3所示,来自管线21的碳四原料与来自管线27的反应产物换热后,在脱水罐2中脱除其中的游离水,与来自管线36的循环异丁烷、来自管线30的冷剂节能罐分离的液相物料混合后,经管线22进入烷基化反应器3中。在来自管线50的补充硫酸和来自管线25的循环硫酸的催化下,进料中的丁烯和异丁烷反应生成烷基化油,反应后物流经酸烃一级分离设备4分离得到含有少量酸的粗反应产物和硫酸,循环酸经管线25和循环烃经管线24返回烷基化反应器3中继续反应,废酸管线51排出装置。粗反应产物经过酸烃二级分离设备11分离脱酸,顺序与碳四原料、循环异丁烷换热后,经管线37进入产物分馏单元12进行产物分离。所述的产物分馏单元包括一个脱异丁烷塔和脱正丁烷塔,分馏得到异丁烷、烷基化油。
73.来自烷基化反应器的轻烃作为气压机系统的制冷剂(主要组成为异丁烷、正丁烷、丙烷、戊烷和少量烷基化产物,温度为2-10℃)经管线31进入气压机入口缓冲罐5,经过压缩机增压液化的轻烃(温度为35-55℃)在换热器7中换热降温后,进入冷剂节能罐13中闪蒸分离,分离得到的气相物料(组成异丁烷、正丁烷、丙烷、戊烷及少量烷基化产物,温度5-25℃)首先返回至压缩机入口6,分离得到的液相物料(组成异丁烷、正丁烷、丙烷、戊烷及烷基化产物,温度5-25℃)经管线30与来自管线36的循环异丁烷混合后返回烷基化反应器3。
74.碳四原料采用碳四原料a。烷基化反应的主要操作条件见表2,气压机系统处理循环冷剂量见表3,产物分馏单元处理量及循环异丁烷组成见表4-1、表4-2。产物分离设备包括一个脱异丁烷塔和脱正丁烷塔,主要结构参数见表5。公用工程物料消耗见表6。
75.对比例2
76.附图4为对比例2硫酸烷基化反应方法和装置的流程示意图。如附图4所示,与对比例1不同的是,来自烷基化反应器3的轻烃作为制冷剂经管线31进入气压机入口缓冲罐5,经过压缩机增压液化的轻烃在换热器7中换热降温后,进入冷剂节能罐13中闪蒸分离,分离得到的气相物料经管线29返回至压缩机入口缓冲罐5,再经过压缩机6实现循环制冷的目的。
77.碳四原料采用碳四原料a,烷基化反应的主要操作条件见表2,气压机系统处理循环冷剂量见表3,产物分馏单元处理量及产物组成见表4-1、表4-2。产物分馏设备包括一个脱异丁烷塔和脱正丁烷塔,主要结构参数见表5。公用工程物料消耗见表6。
78.实施例1
79.采用图1所示的硫酸法烷基化反应方法和装置,如图1所示,碳四原料经管线21与反应产物换热后,在脱水罐2中脱水,与来自管线37循环异丁烷混合后进入烷基化反应器3。在硫酸作用下,进料中的丁烯和异丁烷反应生成烷基化油,反应液相物流经管线23进入酸烃一级分离器4中,分离出的硫酸作为循环酸循环使用;分离出的粗反应产物分成两部分,一部分作为循环烃经管线24返回烷基化反应器,另一部分换热升温后,经管线28进入反应产物闪蒸罐8中,分离出的轻烃组分经管线29返回气压机6一级入口;分离出的液相组分经换热后进入酸烃二级分离器11中脱除微量酸后,经管线34进入产物分馏单元12。
80.产物分馏单元中分离出的异丁烷组分经管线35排出,作为循环异丁烷换热降温后与碳四原料混合进入烷基化反应器3中。产物分馏单元12分离的正丁烷组分经管线39、烷基化油经管线40排出装置。
81.烷基化反应器3闪蒸区得到的轻烃经管线31进入气压机入口缓冲罐5,经气压机6增压升温后在冷却器7中冷却,经管线32与循环异丁烷混合,经换热后返回烷基化反应器3中。
82.碳四原料采用碳四原料a,烷基化反应的主要操作条件见表2,压缩机处理循环冷剂量见表3,产物分馏单元处理量及产物组成见表4-1、表4-2。产物分馏设备包括一个脱异丁烷塔和脱正丁烷塔,主要设备的结构参数见表5。公用工程物料消耗见表6。
83.实施例2
84.硫酸法烷基化反应方法的流程同实施例1。
85.硫酸法烷基化反应方法碳四原料b。烷基化反应器的主要操作条件见表2,压缩机处理循环冷剂量见表3,产物分离单元处理量及产物组成见表4-1、表4-2。产物分离设备包括一个脱异丁烷塔和脱正丁烷塔,主要结构参数见表5。公用工程物料消耗见表6。
86.实施例3
87.采用图2所示的硫酸法烷基化反应装置和方法,气压机系统采用二级气体压缩系统。与实施1不同的是,反应粗产物进入闪蒸罐8中进行气液分离,分离出的轻烃组分经管线29直接返回压缩机二级入口。
88.硫酸法烷基化反应方法碳四原料a,烷基化反应器的主要操作条件见表2,压缩机处理循环冷剂量见表3,产物分馏单元处理量及产物组成见表4-1、表4-2。产物分离设备包括一个脱异丁烷塔和脱正丁烷塔,主要结构参数见表5。公用工程物料消耗见表6。
89.表1碳四原料组成
90.组分,wt%碳四原料a碳四原料b丙烷0.241.44
异丁烷45.3148.85正丁烷13.4210.94正丁烯11.1312.98异丁烯13.900.23反丁烯9.8914.85顺丁烯6.0810.71c5 0.030.00合计100.00100.00
91.表2烷基化反应器操作条件
[0092][0093]
表3压缩机系统内循环冷剂量及质量组成
[0094]
组分实施例1-3对比例1对比例2丙烷-7.75.9异丁烷-83.484.7正丁烷-8.79.1烷基化产物-0.20.2合计-100100质量流量/[kg
·
h-1
]-1835037610温度/℃ 18.2-4.7压力/bar 2.91.3
[0095]
表4-1烷基化反应分馏单元处理量及组成
[0096] 实施例1实施例2实施例3对比例1-2组分
ꢀꢀꢀꢀ
丙烷0.71.90.80.7异丁烷43.447.644.850.7正丁烷11.612.111.710.9烷基化产物44.438.442.837.7合计100.00100.00100.00100.00质量流量/[kg
·
h-1
]78300685408115092226温度/℃77.477.577.779.4压力/bar14.314.314.314.3
[0097]
表4-2循环异丁烷流量及质量组成
[0098] 实施例1实施例2实施例3对比例1-2组分
ꢀꢀꢀꢀ
丙烷1.41.91.61.2异丁烷899089.291.3正丁烷9.68.19.37.5合计100.00100.00100.00100.00质量流量/[kg
·
h-1
]36050300503895050000温度/℃191919.122.4压力/bar14.314.314.314.3
[0099]
表5主要设备操作参数
[0100][0101]
表6公用工程物料消耗表
[0102][0103]
如表4-1、5、6所示,实施例3具有与实施例1类似的效果,能将装置总能耗标油降至10-20%,产物分离过程能耗明显降至20-40%。
再多了解一些
本文用于企业家、创业者技术爱好者查询,结果仅供参考。