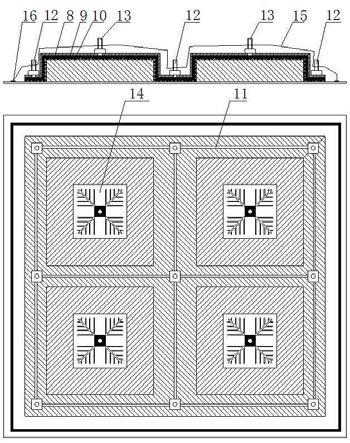
1.本发明属于复合材料制备技术领域,特别涉及含凸台多面复杂复合材料壳体真空辅助制备工艺。
背景技术:
2.目前多面复杂壳体由于结构复杂,涉及的平面较多,大多采用金属材料一体制备成型,或采用短切纤维增强树脂基复合材料注塑而成;金属材料存在着制作能耗高、易被酸碱、海水、盐雾等腐蚀,环境适应性差,尤其是比重大等缺点;短切纤维增强树脂基复合材料存在强度和模量低等缺点。目前真空辅助工艺制备的复合材料壳体,大多采用平纹织物进行整体铺层,这种铺层工艺适用于复合材料平板结构或简单壳体结构,对于含凸台多面复杂复合材料壳体,应用常规的铺层方式,在壳体成型过程中会出现大量的纤维断面和纤维变形情况,导致含凸台多面复杂复合材料壳体结构性能降低。
3.目前真空辅助工艺制备复合材料壳体多采用螺旋管形成注胶管路,在注胶时胶液通过螺旋管之间的缝隙注入复合材料预制件中,如出现螺旋管局部压馈或螺旋管缝隙闭合时,可能会导致胶液无法或较慢注入预制件中,导致注胶失败,另外在真空压力下,螺旋管会在复合材料坯料上留下压痕,导致外观缺陷。
技术实现要素:
4.本发明所要解决的技术问题是提供一种含凸台多面复杂复合材料壳体一体化成型方法。
5.为解决上述技术问题,本发明采用如下技术方案:在复合材料壳体下模具上铺置连续纤维单向织物,通过设计每一个面纤维单向织物之间0
°
/90
°
正交铺层方法,形成一种含凸台多面复杂复合材料壳体预制件,在其预制件上科学的布设注胶管路、抽气管路和抽气位置上模板的设计,并通过真空辅助灌注工艺实现一体化成型含凸台多面复杂复合材料壳体。
6.本发明涉及的一种含凸台多面复杂复合材料壳体的一体化成型方法,其步骤如下:1)根据含凸台多面复杂复合材料壳体性能要求及成型工艺要求,选择合适的增强纤维织物及热固性树脂;2)根据含凸台多面复杂复合材料壳体结构尺寸及拟采用的正交铺层方法,将增强纤维织物裁剪为纤维单向织物ⅰ(0
°
)、纤维单向织物ⅱ(0
°
)、纤维单向织物ⅲ、纤维单向织物ⅳ(90
°
)及纤维单向织物
ⅴ
(90
°
);3)准备模具:模具包括下模具和上模板;下模具包括底板和下模具凸台;上模板,与下模具结构相对应,包括底板和上模板凸台,底板上围绕上模板凸台设置厚度方向贯通、长度方向间断的流道;下模具表面脱模蜡处理;4)含凸台多面复杂复合材料壳体预制件制备:采用单向纤维正交铺层法,因此,每
两层为一个铺设周期,每层的拼接处为无重叠闭合拼接,相邻层拼接处位置相互错开,具体步骤如下:第一层铺层:确定铺层0
°
方向;沿铺层0
°
方向,在经过下模具凸台的非平面区域,紧贴下模具上表面铺设纤维单向织物ⅰ(0
°
);在平面区域,紧贴下模具上表面铺设纤维单向织物ⅱ(0
°
);纤维单向织物ⅰ(0
°
)和纤维单向织物ⅱ(0
°
)的两末端,超出最接近凸台侧壁面不少于50mm;在凸台侧壁面区域,根据其结构,采用分区域铺层法,铺设一周纤维单向织物ⅲ;第二层铺层:确定铺层90
°
方向;沿铺层0
°
方向,在经过下模具凸台的非平面区域,紧贴第一层铺层表面铺设纤维单向织物ⅳ(90
°
);在平面区域,紧贴第一层铺层表面铺设纤维单向织物
ⅴ
(90
°
);纤维单向织物ⅳ(90
°
)和纤维单向织物
ⅴ
(90
°
)的两末端,超出最接近凸台侧壁面不少于50mm;以上为一个0
°
/90
°
铺设周期,按照以上铺层方式铺设剩余周期,完成含凸台多面复杂复合材料壳体预制件的制备;5)含凸台多面复杂复合材料壳体坯料的制备:采用真空辅助成型工艺,将热固性树脂灌入制备的含凸台多面复杂复合材料壳体预制件中,具体步骤如下:在含凸台多面复杂复合材料壳体上表面从下往上依次铺设脱模布、导流网、上模板和真空袋;在脱模布、导流网、上模板和真空袋对应下模具凸台上表面的位置处开口,设置抽气口;在真空袋对应上模板流道的合适位置处开口,设置注胶口;将真空袋密封在下模具底板上;在真空状态下,将热固性树脂灌入含凸台多面复杂复合材料壳体预制件中;树脂固化后,完成含凸台多面复杂复合材料壳体坯料的制备;6)脱模;7)后处理:按照产品的要求,对外形进行加工修整,制得含凸台多面复杂复合材料壳体。
7.本发明涉及的含凸台多面复杂复合材料壳体的一体化成型方法,其特征在于:所述模具还包括抽气座布设板;所述上模板凸台上方设置开口;抽气座布设板,结构与上模板凸台开口相匹配,厚度方向设置有布设抽气口用开口,开口周围设置厚度方向非贯通的槽;抽气座布设板嵌入上模板的开口中。该结构在真空辅助制备工艺的抽气过程中,可以有效避免出现胶液抽入抽气管堵塞抽气管路的现象发生。
8.本发明涉及的含凸台多面复杂复合材料壳体的一体化成型方法,其特征在于:所述抽气座布设板的槽包括主干槽和与主干槽相连的支干槽。
9.本发明涉及的含凸台多面复杂复合材料壳体的一体化成型方法,其特征在于:所述设置抽气口的位置处,导流网的开口小于脱模布的开口。
10.本发明涉及的含凸台多面复杂复合材料壳体的一体化成型方法,其特征在于:所述纤维单向织物ⅰ(0
°
)、纤维单向织物ⅱ(0
°
)、纤维单向织物ⅳ(90
°
)以及纤维单向织物
ⅴ
(90
°
)的铺层方式,是从中间向两边方向铺。
11.本发明涉及的含凸台多面复杂复合材料壳体的一体化成型方法,其特征在于:采用分区域铺层法,对凸台侧壁面区域铺层时,增强纤维织物的上下部分只在凸台侧壁面出现高度变化时,才会进行裁剪分离。该铺层方案与现有的纤维铺层方案相比,沿纤维长度方
向断点最少,因此,制品的力学性能最好。
12.本发明涉及的含凸台多面复杂复合材料壳体的一体化成型方法,其特征在于:所述增强纤维织物为单向玻璃纤维织物、单向碳纤维织物、单向芳纶纤维织物或单向石英纤维织物本发明涉及的含凸台多面复杂复合材料壳体的一体化成型方法,其特征在于:所述热固性树脂为乙烯基酯树脂、环氧树脂或不饱和聚酯树脂。
13.本发明涉及的含凸台多面复杂复合材料壳体的一体化成型方法,通过纤维织物铺层方案的设计,大大减少了铺层时沿纤维织物长度方向的断点数量,明显提高了含凸台多面复杂复合材料壳体的结构性能。通过对注胶管路和抽气管路的设计,代替常规螺旋管注胶方案,解决了在真空辅助制备工艺中出现注胶短路、抽气管中聚集大量树脂,导致含凸台多面复杂复合材料壳体中真空度降低,注胶容易失败等问题;采用带有胶道的抽气管路上模板,在胶液注满含凸台多面复杂复合材料壳体坯料后会先流入流道中,避免直接进入抽气管路,大大降低了注胶失败的风险。另外,本发明方法还具有操作方便等优点。
附图说明
14.图1是本发明含凸台多面复杂复合材料壳体结构示意图;图2是本发明含凸台多面复杂复合材料壳体用下模具结构示意图;图3是本发明沿下模具长度方向单向织物铺层示意图;图4是本发明单向织物在凸台侧壁面铺层示意图;图5是本发明沿下模具宽度方向单向织物铺层示意图;图6是第一个实施例真空辅助树脂灌注工艺结构示意图;图7是第二个实施例真空辅助树脂灌注工艺结构示意图。
15.其中,1-含凸台多面复杂复合材料壳体, 2-下模具,21-下模具凸台,22-下模具浅凹槽,23-下模具深凹槽,24-凸台侧壁面,3-纤维单向织物ⅰ(0
°
),4-纤维单向织物ⅱ(0
°
),5-纤维单向织物ⅲ,6-纤维单向织物ⅳ(90
°
),7-纤纤维单向织物
ⅴ
(90
°
),8-脱模布,9-导流网,10-上模板,11-流道,12-注胶口,13-抽气口,14-抽气座布设板,15-真空袋,16-密封胶条。
具体实施方式
16.下面结合实施例对本发明提出的方案进行进一步说明,但不作为对技术方案的限制。任何一种可以实现本发明的技术方法均构成本发明涉及技术方案的一部分。
17.实施例一本实施例的含凸台多面复杂复合材料壳体1,如图1所示,是壁厚为5mm的矩形结构,外廓最大尺寸为1200mm
×
1100mm
×
105mm。四个边角处分别设置矩形槽,四个矩形槽外部形成了两个凹槽,分别为壳体深凹槽高度为100mm,宽度为200mm,壳体浅凹槽高度为50mm,宽度为100mm。
18.制备含凸台多面复杂复合材料壳体1时,采用单向纤维正交铺层法,因此,每两层为一个铺设周期,相邻层闭合处位置相互错开,具体步骤如下:1)增强纤维织物选用面密度为200g/m2的t700级碳纤维单向织物,根据含凸台多
面复杂复合材料壳体1的外廓尺寸,裁剪纤维织物,铺层所用,如表1所示。
19.表1 含凸台多面复杂复合材料壳体1用碳纤维单向织物尺寸2)模具准备:模具包括下模具2、上模板10和抽气座布设板14。下模具2包括底板和四个下模具凸台21,四个下模具凸台21的相互之间形成了下模具浅凹槽22和下模具深凹槽23;上模板10,结构与下模具2相对应,材质为聚丙烯,厚度为6mm,包括底板和四个上模板凸台,底板上围绕四个上模板凸台加工宽5mm的田字形贯通流道11,流道11的口字形外围中,留有八个宽10mm的连接条,用于避免上模板10底板被流道11分割成独立的两部分,八个连接条分别位于流道11中间的十字形与外围的口字形相交位置的两侧200mm处,在上模板凸台中心位置设置240mm
×
240mm的开口。抽气座布设板14,厚6mm的平板结构,尺寸为240mm
×
240mm,中心位置设置φ30mm的开口,开口向外开宽2mm、深5mm的主干槽,主干槽两边各开与其贯通连接的五对宽2mm、深5mm的支干槽,支干槽的末端距离相邻边界20mm。将抽气座布设板14嵌入上模板凸台中心位置的开口处,如图6所示。下模具2用脱模蜡处理表面3遍,待用;3)制备含凸台多面复杂复合材料壳体1预制件:第一层铺层:以下模具2的长度方向为铺层0
°
方向。
20.沿铺层0
°
方向,分别紧贴下模具2表面铺设一层纤维单向织物ⅰ(0
°
)3,如图3所示,铺层宽度与下模具凸台21宽度一致。铺层时,以下模具浅凹槽22宽度方向的中心处为铺层原点,纤维单向织物ⅰ(0
°
)3的长度方向中心处与铺层原点重合,向两边铺层,跨过下模具凸台21后,沿下模具2底板表面继续向外延伸50mm,多余织物裁剪去除,如图3所示。铺层时,在拐角处要将纤维织物压实,避免出现纤维织物悬空的情况。
21.沿铺层0
°
方向,紧贴下模具深凹槽23表面铺设一层纤维单向织物ⅱ(0
°
)4,如图3所示。铺层时,铺层原点同样位于下模具浅凹槽22宽度方向的中心处,纤维单向织物ⅱ(0
°
)4的长度方向中心处与铺层原点重合,向两边铺层,纤维单向织物ⅱ(0
°
)4的两末端与纤维单向织物ⅰ(0
°
)3平齐,如图3所示。
22.紧贴凸台侧壁面24,沿纤维方向铺设一层纤维单向织物ⅲ5。铺设时,选择凸台外壁面24的任意位置作为铺层起点,在凸台外壁面24高度出现变化位置,即下模具浅凹槽22的内外端口处,纤维单向织物ⅲ5以下模具浅凹槽22的底面为界,上半部分围绕单个下模具凸台21形成闭合,下半部分以恒定宽度继续铺设,至伸入相邻下模具凸台21下方200mm;相邻下模具凸台21的外壁面在铺设时,将其纤维单向织物ⅲ5按照已铺设纤维单向织物ⅲ5的区域尺寸进行裁切,使两者的交界处闭合,但不形成重叠,裁剪掉如图4所示。因为是单向织物,该种从宽度方向分开的铺设方式,不会影响纤维的力学性能。
23.第二层铺层:以下模具2的宽度方向为铺层90
°
方向。
24.沿铺层90
°
方向,紧贴第一层铺层表面铺设一层纤维单向织物ⅳ(90
°
)6,如图5所示,铺层宽度与下模具凸台21长度一致。铺层时,以下模具深凹槽23宽度方向的中心处为铺
层原点,纤维单向织物ⅳ(90
°
)6的长度方向中心处与铺层原点重合,向两边铺层,跨过下模具凸台21后,沿下模具2底板表面继续向外延伸50mm,多余织物裁剪去除,如图5所示。铺层时,在拐角处要将纤维织物压实,避免出现纤维织物悬空的情况。
25.沿铺层90
°
方向,紧贴第一层铺层表面铺设一层纤维单向织物
ⅴ
(90
°
)7,如图5所示。铺层时,铺层原点同样位于下模具深凹槽23宽度方向的中心处,纤维单向织物
ⅴ
(90
°
)7的长度方向中心处与铺层原点重合,向两边铺层,纤维单向织物
ⅴ
(90
°
)7的两末端与纤维单向织物ⅳ(90
°
)6平齐,铺设方式见图5。
26.以上为一个0
°
/90
°
铺设周期。按照以上铺层方式铺设10个周期,完成含凸台多面复杂复合材料壳体1预制件的制备。
27.4)利用真空辅助成型工艺,将乙烯基酯树脂灌入含凸台多面复杂复合材料壳体1预制件中:在含凸台多面复杂复合材料壳体1预制件上方铺置脱模布8,其外廓尺寸大于含凸台多面复杂复合材料壳体1预制件50mm;在下模具2的下模具凸台21的居中位置对应处,将脱模布8裁剪250mm
×
250mm的正方形开口。
28.在脱模布8上表面以相同布设方式铺设导流网9,导流网9的开口尺寸为240mm
×
240mm,位于脱模布8开口的中心位置,其尺寸小于脱模布8的开口尺寸,可以防止导流网9被树脂粘到含凸台多面复杂复合材料壳体1坯料的表面上。
29.在导流网9上表面布设上模板10,在其每个流道11的交叉处布设注胶口12,见图6中所示。
30.在上模板10的开口位置布置抽气座布设板14,其开口处设置抽气口13。设置抽气座布设板14的目的是为了在树脂浸满含凸台多面复杂复合材料壳体1预制件后,在树脂未固化前多余的树脂优先填满抽气座布设板14的空隙再抽入抽气管路,这样可有效减少含凸台多面复杂复合材料壳体1预制件的富脂区。
31.在脱模布8、导流网9和抽气座布设板14的开口位置布设抽气口13。
32.用粘有密封胶条16的真空袋15在下模具2上将含凸台多面复杂复合材料壳体1预制件密封;开启抽气管,当真空度达到-0.095mpa后,通过真空注胶系统的注胶口12将乙烯基酯树脂通过流道11注入含凸台多面复杂复合材料壳体1预制件中,在整个注胶过程中保证注胶管路中树脂不间断,真空系统见图6所示。灌注结束后,真空保持6h,待树脂固化后,关闭真空泵,完成含凸台多面复杂复合材料壳体1坯料制备。
33.8)脱模。在树脂固化后进行脱模工序,将含凸台多面复杂复合材料壳体1坯料从下模具2上取下,完成含凸台多面复杂复合材料壳体1坯料的脱模工序。
34.9)后处理。按照产品要求,对外形进行加工修整,制得含凸台多面复杂复合材料壳体1。
35.本实施例制备的含凸台多面复杂复合材料壳体1坯料为一体成型,结构性能好,工艺成本低。
36.实施例二与实施例一区别之处在于:制备含凸台多面复杂复合材料壳体1预制件,对第一层铺层的凸台侧壁面24进行铺层时,纤维单向织物ⅲ5,以下模具浅凹槽22的底面为界,进行上下裁剪分离,上半部分围
绕单个下模具凸台21形成闭合,下半部分围绕下模具浅凹槽22两侧的两个下模具凸台21形成闭合。
37.实施例三本实施例的含凸台多面复杂复合材料壳体1,是壁厚为8mm的矩形结构,外廓最大尺寸为1500mm
×
1300mm
×
208mm,四个边角处分别设置矩形槽,四个矩形槽外部形成了两个相同的凹槽,凹槽高度为200mm,宽度为200mm。
38.制备含凸台多面复杂复合材料壳体1时,采用单向纤维正交铺层法,因此,每两层为一个铺设周期,相邻层拼接处位置相互错开,具体步骤如下:1)增强纤维织物选用面密度为200g/m2的ewr200玻璃纤维单向织物,根据含凸台多面复杂复合材料壳体1的外廓尺寸,裁剪纤维织物,铺层所用,如表1所示。
39.表1 含凸台多面复杂复合材料壳体1用玻璃纤维单向织物尺寸2)模具准备:模具包括下模具2和上模板10。下模具2包括底板和四个下模具凸台21,四个下模具凸台21的相互之间形成了下模具浅凹槽22和下模具深凹槽23;上模板10,结构与下模具2相对应,材质为聚丙烯,厚度为6mm,包括底板和四个上模板凸台,底板上围绕四个上模板凸台加工宽4mm的田字形贯通流道11。下模具2用脱模蜡处理表面3遍,待用;3)制备含凸台多面复杂复合材料壳体1预制件:第一层铺层:以下模具2的长度方向为铺层0
°
方向。
40.沿铺层0
°
方向,紧贴下模具2表面铺设一层纤维单向织物ⅰ(0
°
)3,如图3所示的两处位置,铺层宽度与下模具凸台21宽度一致。铺层时,以下模具浅凹槽22宽度方向的中心处为铺层原点,纤维单向织物ⅰ(0
°
)3的长度方向中心处与铺层原点重合,向两边铺层,跨过下模具凸台21后,沿下模具2底板表面继续向外延伸60mm,多余织物裁剪去除。铺层时,在拐角处要将纤维织物压实,避免出现纤维织物悬空的情况。
41.沿铺层0
°
方向,紧贴下模具深凹槽23表面铺设一层纤维单向织物ⅱ(0
°
)4,如图3所示。铺层时,铺层原点同样位于凹槽22宽度方向的中心处,纤维单向织物ⅱ(0
°
)4的长度方向中心处与铺层原点重合,向两边铺层,纤维单向织物ⅱ(0
°
)4的两末端与纤维单向织物ⅰ(0
°
)3平齐,如图3所示。
42.紧贴凸台侧壁面24,沿纤维方向铺设一层纤维单向织物ⅲ5。铺设时,纤维单向织物ⅲ5围绕所有下模具凸台21都形成闭合。
43.第二层铺层:以下模具2的宽度方向为铺层90
°
方向。
44.沿铺层90
°
方向,紧贴第一层铺层表面铺设一层纤维单向织物ⅳ(90
°
)6,如图5所示,铺层宽度与下模具凸台21长度一致。铺层时,以下模具深凹槽23宽度方向的中心处为铺层原点,纤维单向织物ⅳ(90
°
)6的长度方向中心处与铺层原点重合,向两边铺层,跨过下模具凸台21后,沿下模具2底板表面继续向外延伸60mm,多余织物裁剪去除,如图5所示。铺层
时,在拐角处要将纤维织物压实,避免出现纤维织物悬空的情况。
45.沿铺层90
°
方向,紧贴第一层铺层表面铺设一层纤维单向织物
ⅴ
(90
°
)7,如图5所示。铺层时,铺层原点同样位于凹槽23宽度方向的中心处,纤维单向织物
ⅴ
(90
°
)7的长度方向中心处与铺层原点重合,向两边铺层,纤维单向织物
ⅴ
(90
°
)7的两末端与纤维单向织物ⅳ(90
°
)6平齐,铺设方式见图5。
46.以上为一个0
°
/90
°
铺设周期。按照以上铺层方式铺设16个周期,完成含凸台多面复杂复合材料壳体1预制件的制备。
47.4)利用真空辅助成型工艺,将不饱和聚酯树脂灌入含凸台多面复杂复合材料壳体1预制件中:在含凸台多面复杂复合材料壳体1预制件上表面铺设脱模布8,其外廓尺寸大于含凸台多面复杂复合材料壳体1预制件50mm。在每个下模具凸台21居中位置对应处,将脱模布8裁剪300mm
×
300mm的正方形开口。
48.在脱模布8上表面以相同布设方式铺设导流网9,导流网9的开口尺寸为280mm
×
280mm,位于脱模布8开口的中心位置,其尺寸小于脱模布8的开口尺寸,可以防止导流网9粘到含凸台多面复杂复合材料壳体1预制件的表面上。
49.在导流网9上表面铺设上模板10,在其每个流道11的交叉处布设注胶口12,见图7所示。
50.在脱模布8、导流网9和上模板10的开口位置布设抽气口13。
51.用粘有密封胶条16的真空袋15在下模具2上将含凸台多面复杂复合材料壳体1预制件密封;开启抽气管,当真空度达到-0.095mpa后,通过真空注胶系统的注胶口12将不饱和聚酯树脂通过流道11注入含凸台多面复杂复合材料壳体1预制件中,在整个注胶过程中保证注胶管路中树脂不间断,真空系统见图7所示。灌注结束后,真空保持6h,待树脂固化后,关闭真空泵,完成含凸台多面复杂复合材料壳体1坯料制备。
52.8)脱模:在树脂固化后进行脱模工序,将含凸台多面复杂复合材料壳体1坯料从下模具上取下,完成含凸台多面复杂复合材料壳体1坯料的脱模工序。
53.9)后处理。按照产品要求,对外形进行加工修整,制得含凸台多面复杂复合材料壳体1。
54.本实施例制备的含凸台多面复杂复合材料壳体1坯料为一体成型,结构性能好,工艺成本低。
再多了解一些
本文用于企业家、创业者技术爱好者查询,结果仅供参考。