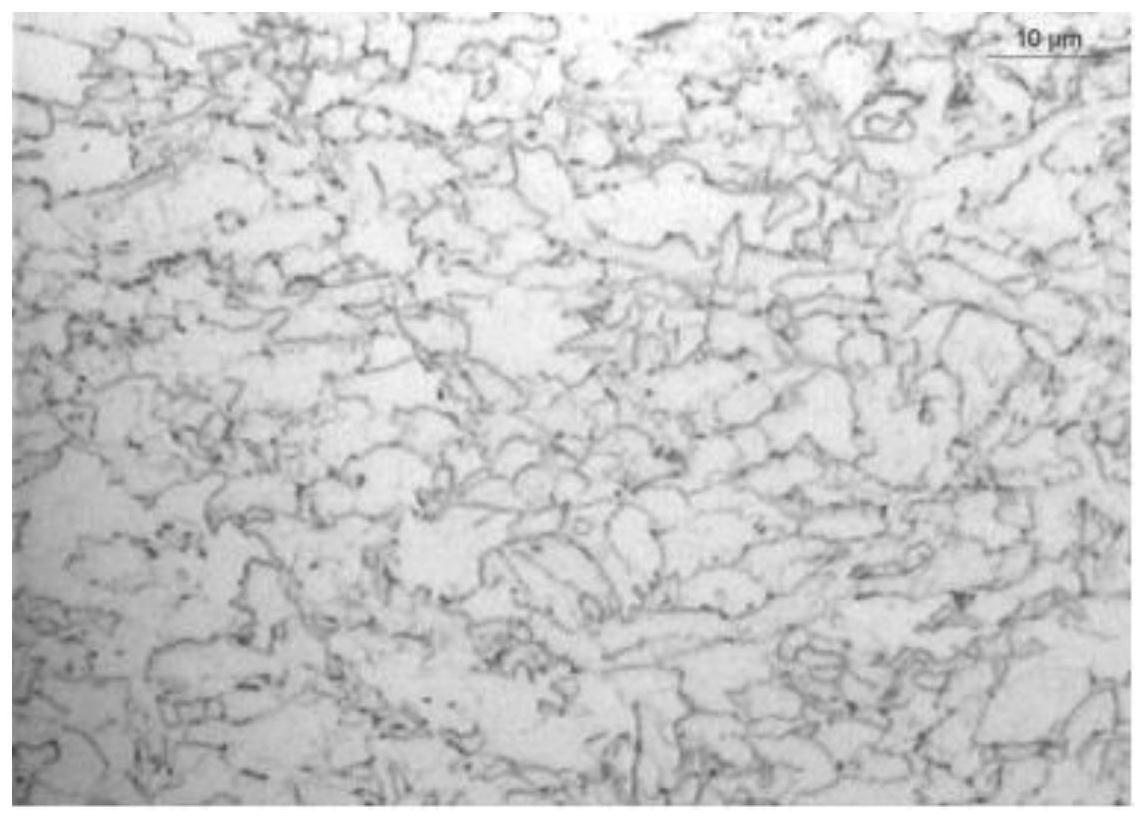
1.本发明属于冶金轧制技术领域,特别是涉及一种一钢多级多规格大梁钢及其生产方法。
背景技术:
2.钢铁企业在传统大梁钢制造过程中,生产量是按照炉次重量的整数倍进行生产,因此经常会出现坯料剩余,库存压力增大。订货厂家对不同级别、不同规格的合金钢需求较多,但对相同级别的大梁钢订货量较少,每次订货量一般在120吨以内,而目前的钢铁企业1炉大梁钢一般在200吨以上。传统大梁钢在实际生产中受订单量小、连铸连浇能力增加的影响,对于不同牌号的大梁钢单独组织生产时经济和时间损耗过大,已不能满足高效智能化生产的需求。
3.为此,钢铁企业采取的措施普遍为不同钢种之间进行连续浇铸,基本能够解决单浇次内不同钢种连续浇铸,但是存在混交坯改判的问题。轧制后需要单独做性能检验,检验结果有时不符合连续浇铸的任何一个钢种的强度要求,产生库存、计划合同交货少量亏吨等问题。并且类似于510l、550l和700l等强度梯度差别较大的牌号之间混交坯改判量较大,改判铸坯头尾成分波动大,轧制成卷后,钢卷前1/2符合一个牌号的性能,钢卷后1/2符合另一个牌号的性能,在改判方面都带来了较大难度。
4.总体情况是钢厂目前能够解决不同钢种之间连续生产,但解决的不充分,只能达到相邻牌号之间的连续,并且存在改判等一系列麻烦。而生产是灵活的,有时需要多个牌号、多个规格连续生产,有时需要跨强度等级之间连续生产,才能保证单个浇次耐材和设备的合理利用。
5.专利申请号:201910956748.1一种一钢多级用高强钢坯料生产方法,通过合金元素调整,减少钢种数量,大大提高了钢种的替代使用率,能够生产出满足不同级别、不同厚度性能要求的高强钢产品,提高钢厂的生产作业率,但其在工艺设计时增加rh工序,成分设计时添加贵重金属v,并且其坯料生产对应的成分设计未能与轧制工序的工艺优化相结合,单纯依靠合金的改变来改变强度,造成一定的资源浪费和成本损失。
6.专利申请号:201310621228.8一种一钢多级的热轧钢板及其制造方法,在成分设计时无贵重合金元素添加,降低经济成本,但其单纯通过轧制工序的控制轧制和控制冷却来控制强度,产生马氏体、贝氏体等硬相组织。而大梁钢受使用条件的苛刻要求,对成品的延伸率、冲击功等要求比较严格,硬相组织不能满足这些严格要求,具有软硬相匹配优异的铁素体 珠光体组织能够较好的适应车辆运行中的动态冲击力。
7.因此钢铁企业针对单个级别订单量少的生产组织特点,应当通过合理的成分设计和工艺参数优化,实现一种成分体系生产不同级别大梁钢的生产工艺,不仅满足单个用户对产品多性能、多规格的要求,同时也降低和钢铁企业的制造成本。
技术实现要素:
8.本发明所要解决的技术问题是公开一种一钢多级多规格大梁钢及其生产方法,该方法通过合理的成分设计和工艺参数优化,实现一种成分体系生产不同级别大梁钢的生产工艺,满足了单个用户对产品多性能、多规格的要求,同时降低钢铁企业的制造成本。
9.为解决上述技术问题,本发明采用的技术方案如下:一种一钢多级多规格大梁钢,所述大梁钢化学成分组成及质量百分含量为:c:0.06-0.08%,si:0.10-0.15%,mn:1.30-1.50%,p≤0.018%,s≤0.003%,als:0.015-0.045%,nb:0.020-0.040%,ti:0.075-0.095%,n≤0.0050%,余量为fe和不可避免的杂质。
10.进一步的,所述大梁钢厚度规格为3-15mm;显微组织为铁素体 珠光体,晶粒度等级11级以上,冷弯性能合格;所述大梁钢包括:510l牌号产品,横向性能指标如下:屈服强度410-447mpa,抗拉强度533-568mpa,延伸率a:24-26%,-20℃冲击功≥140j;550l牌号产品,横向性能指标如下:屈服强度425-471mpa,抗拉强度566-589mpa,延伸率a:22-24%,-20℃冲击功≥128j;610l牌号产品,横向性能指标如下:屈服强度510-537mpa,抗拉强度615-640mpa,延伸率a:20-22%,-20℃冲击功≥115j;650l牌号产品,横向性能指标如下:屈服强度562-598mpa,抗拉强度668-693mpa,延伸率a:18-20%,-20℃冲击功≥93j;700l牌号产品,横向性能指标如下:产品屈服强度640-671mpa,抗拉强度711-738mpa,延伸率a:16-18%,-20℃冲击功≥76j。
11.本发明还提供一种一钢多级多规格大梁钢的生产方法,包括铁水预处理、转炉冶炼、lf精炼、连铸、轧制工序;所述轧制工序,加热温度1140-1240℃、加热时间140-240min、终轧温度820-920℃、卷取温度460-620℃。
12.进一步的,所述轧制工序,炼钢连铸产出的铸坯,经热轧工序进行轧制,当加热温度1140-1160℃、加热时间140-160min、终轧温度820-840℃、前段1/2冷却模式、卷取温度460-490℃时,产出的是510l牌号产品。
13.进一步的,所述轧制工序,炼钢连铸产出的铸坯,经热轧工序进行轧制,当加热温度1161-1180℃、加热时间161-180min、终轧温度841-860℃、前段1/2冷却模式、卷取温度491-520℃时,产出的是550l牌号产品。
14.进一步的,所述轧制工序,炼钢连铸产出的铸坯,经热轧工序进行轧制,当加热温度1181-1200℃、加热时间181-200min、终轧温度861-880℃、前段3/4冷却模式、卷取温度521-550℃时,产出的是610l牌号产品。
15.进一步的,所述轧制工序,炼钢连铸产出的铸坯,经热轧工序进行轧制,当加热温度1201-1220℃、加热时间201-220min、终轧温度881-900℃、前段3/4冷却模式、卷取温度551-580℃时,产出的是650l牌号产品。
16.进一步的,所述轧制工序,炼钢连铸产出的铸坯,经热轧工序进行轧制,当加热温度1221-1240℃、加热时间221-240min、终轧温度901-920℃、前段集中冷却模式、卷取温度581-620℃时,产出的是700l牌号产品。
17.进一步的,所述铁水预处理工序,进行铁水预脱硫,脱硫后铁水硫质量百分比控制在≤0.0020%;
18.所述转炉冶炼工序,终点氧控制在0.040-0.060%,控制终点温度1610-1630℃,终点c≤0.035%,p≤0.015%,出钢后进行脱氧合金化,控制als:0.030-0.050%,转炉出站s
控制在≤0.008%;
19.所述lf精炼工序,送电升温,根据温度测定值,按照1610℃进行设定升温时间,送电升温同时加入石灰,石灰加入量按照5-5.5kg/吨钢加入,升温后进行脱硫和取样,合金调整,同时加入ti铁,喂入纯钙线,调整净吹气量,并保持净吹时间6-12min。
20.所述连铸工序,根据液相线计算公式得出钢水的液相线温度为1520℃,连铸浇铸时保证中包温度在1530-1545℃,确保连铸过热度在10-25℃,拉速控制在1.1-1.3m/min。
21.进一步的,所述一钢多级多规格大梁钢厚度区间为3-15mm;所述连铸工序,连铸坯化学成分组成及质量百分含量为:c:0.06-0.08%,si:0.10-0.15%,mn:1.30-1.50%,p≤0.018%,s≤0.003%,als:0.015-0.045%,nb:0.020-0.040%,ti:0.075-0.095%,n≤0.0050%,余量为fe和不可避免的杂质。
22.本发明成分工艺设计理论依据:
23.510l、550l、610l、650l、700l在以往常规成分设计时,往往根据性能等级情况,控制不同的c、mn、nb、ti元素的含量来控制各强度级别大梁钢的强度,系统维护和生产组织较为复杂,尤其在零散合同不断增多的情况下。
24.本发明针对大梁钢全牌号随机组合式连浇连轧,通过对钢的强化机理进行研究,针对510l、550l、610l、650l、700l在成分设计上主要采用c、mn固溶强化、nb细晶强化、ti析出强化,成分设计使c、mn、nb的固溶强化和细晶强化等强化方式强度贡献约500mpa,与510l强度级别附近,通过轧制工艺的改变,使ti的析出强化强度贡献区间控制在50-250mpa,强度的叠加组合,能够对应不同级别牌号对强度的需求。即采用一个成分体系设计,通过轧制工艺的调整控制ti的析出量,使不同的轧制工艺生产出来的强度可以根据合同需求任意对应不同级别牌号的大梁钢产品。并且ti是廉价金属,低牌号大梁钢在ti的固溶富余等成本上可以忽略,相比以上常规连浇改判带来的各种损失,本发明节约了时间和经济成本,生产变得高效简单,创造性的从根本上解决了传统问题。
25.本发明成分设计原理:
26.通常大梁钢的强化机理,采用固溶强化和低成本的ti的析出强化,本发明也是在本机理的基础之上,通过仅仅的一个成分,合理搭配热轧工艺参数,达到产出不同强度等级的大梁钢牌号。
27.c:碳是廉价而有效间隙固溶强化元素,在普通钢中,为了保证钢板高的强度、硬度和淬透性需要相当的碳含量做保证。但在大梁钢中,过高的c对冲击韧性影响较大,不利于大梁钢成品的质量稳定。因此,成分设计要求c:0.06-0.08%。
28.si:在钢中si同样可以起到固溶强化贡献强度的作用,同时在精炼过程中,钢中含有0.1%的si能够促进钢渣中脱氧进程,减少精炼造渣时间,节省钢水工序处理时间,增加钢水纯净度,但过高的si含量,容易引起钢卷的表面红秀效应,导致后续材料加工过程中氧化铁皮脱落,加工零件表面压坑现象。因此,成分设计时要求si:0.10-0.15%。
29.mn:锰是固溶强化元素,同时其与s相结合形成mns,固硫效果好,高于1.5%时,容易产生铸坯偏析,增加轧制成品的分层和冲击功不合的概率。因此在成分设计时,考虑在保证铸坯的良好质量前提下,充分发挥mn的固溶强化效应,将mn的含量控制在1.30-1.50%。
30.s:钢中的s容易引起热脆效应,因此在大多数钢中s被视作有害元素而尽量的控制在较低水平。同样在大梁钢中作为有害元素来控制,在考虑了精炼渣料脱硫率和s含量对大
梁钢的影响作用的情况下,本发明控制s含量要求为s≤0.003%。
31.al:在钢成品中含有0.01%以上的al可以保证钢中氧含量在0.0015%以下,同时过高的al对连铸浇铸不利,容易堵塞水口,对钢成品的焊接不利,并且增加合金成本损耗。因此,本发明中al含量控制在0.015-0.045%。
32.nb:nb元素可以起到较好的细晶强化作用,在成分设计时,要充分考虑510l、550l等牌号大梁钢的强度级别,不能添加较多的nb导致强度偏高引起强度富余量过大造成的原料浪费,其余强度不足的牌号通过合理发挥ti的析出强化作用来满足更高牌号的强度需求。因此,本发明nb的含量设计为nb:0.020-0.040%。
33.ti:在汽车大梁钢中,采用ti的析出强化是一种经济型的成分设计,为了保证炼钢只用一种成分,将ti控制在最高强度控制水平能够达到700l的范围,保证一种成分能够满足最高设计强度的需要。因此,结合实际700l的ti含量设定为ti:0.075-0.095%。
34.n:在大梁钢中,过高的n会与ti、nb等形成块状物析出,当析出尺寸较大时,增加钢的脆性和性能的不稳定性,需尽可能的控制n元素在较低水平。因此,本发明中n含量控制在≤0.0050%。
35.采用上述技术方案所产生的有益效果在于:1、本发明通过对控制轧制和控制冷却工艺参数进行精确调整,1个成分体系可以生产出满足不同性能要求的大梁钢产品。2、不浪费成本的情况下实现大梁钢一个成分对应多个牌号多种规格,使生产组织更加灵活方便,提高生产效率、节约时间、降低成本。
附图说明
36.图1为实施例1中510l金相组织图(1000
×
);
37.图2为实施例2中550l金相组织图(1000
×
);
38.图3为实施例3中610l金相组织图(1000
×
);
39.图4为实施例4中510l金相组织图(1000
×
);
40.图5为实施例5中550l金相组织图(1000
×
);
41.图6为实施例6中610l金相组织图(1000
×
);
42.图7为实施例7中650l金相组织图(1000
×
);
43.图8为实施例8中650l金相组织图(1000
×
);
44.图9为实施例9中700l金相组织图(1000
×
)。
具体实施方式
45.下面结合具体实施例1-9及附图对本发明做进一步详细的说明。
46.一种一钢多级多规格大梁钢的生产方法,包括铁水预处理、转炉冶炼、lf精炼、连铸、轧制工序,以260吨转炉为例,关键过程按照本发明参数生产,未提及参数按照常规参数进行生产。
47.本发明工艺路线制定:
48.1、铁水预处理工序:铁水预脱硫,减少铁水中的s含量,减轻lf对s的控制压力,脱硫按照3-3.3kg脱硫剂/吨钢,脱硫剂的成分为mg粉 白灰,配比为mg粉/白灰=1:3,脱硫后进行扒渣,为充分保证扒渣效果,扒渣铁损控制在0.15-0.20%,使脱硫后铁水硫质量百分
比控制在≤0.0020%。
49.2、转炉冶炼工序:转炉采用高碱度、高氧化性炉渣,实现低碳低磷冶炼,转炉吹氧量控制在48-50nm3/吨钢,吹氧流量设定800-850nm3/min,终点氧控制在0.040-0.060%,吹炼过程石灰加入量46-48kg/吨钢,控制终点温度1610-1630℃,终点c≤0.035%,p≤0.015%,出钢后进行脱氧合金化,控制als:0.030-0.050%,转炉出站s控制在≤0.008%。
50.3、lf精炼工序:精炼lf工序钢水进站后进行温度测定,送电升温,根据温度测定值,按照1610℃进行设定升温时间,送电升温同时加入石灰,石灰加入量按照5-5.5kg/吨钢加入,停电后进行脱硫和取样,合金调整,同时加入ti铁,喂入纯钙线,调整净吹气量,并保持净吹时间6-12min。
51.4、连铸工序:根据液相线计算公式得出钢水的液相线温度为1520,为确保连铸过热度在10-25℃;连铸浇铸时保证中包温度在1530-1545℃,拉速控制在1.1-1.3m/min,提高钢液在中间包内的停留时间,促进非金属夹杂物上浮去除,采用超低碳专用保护渣保护浇铸,防止钢液吸气及二次氧化,同时连铸过程中采用电磁搅拌、轻压下等技术防止液相穴内富集溶质母液的流动,降低合金元素偏析,以保证良好的铸坯质量,铸坯采用指直接热装,避免温度过低时,细小硫化物夹杂的析出,并降低燃料消耗。
52.5、轧制工序:
53.1)加热工艺。
54.510l牌号加热温度1140-1160℃、加热时间140-160min;
55.550l牌号加热温度1161-1180℃、加热时间161-180min;
56.610l牌号加热温度1181-1200℃、加热时间181-200min;
57.650l牌号加热温度1201-1220℃、加热时间201-220min;
58.700l牌号加热温度1221-1240℃、加热时间221-240min。
59.2)控制轧制、冷却工艺。目的为保证各级别牌号大梁钢强韧性匹配良好。
60.510l牌号产品终轧温度820-840℃、前段1/2冷却、卷取温度460-490℃;
61.550l牌号产品终轧温度841-860℃、前段1/2冷却、卷取温度491-520℃;
62.610l牌号产品终轧温度861-880℃、前段3/4冷却、卷取温度521-550℃;
63.650l牌号产品终轧温度881-900℃、前段3/4冷却、卷取温度551-580℃;
64.700l牌号产品终轧温度901-920℃、前段集中冷却、卷取温度581-620℃。
65.实施例1
66.一种一钢多级多规格大梁钢的生产方法,包括铁水预处理、转炉冶炼、lf精炼、连铸、轧制工序;具体工艺如下:
67.1)铁水预处理工序:根据设计的成分进行冶炼,铁水预脱硫,铁水预脱硫工序采用脱硫剂(mg粉/白灰=1:3)进行喷吹脱硫,脱硫剂喷吹量为3kg/吨钢,脱硫后铁水硫质量百分比0.0020%;
68.2)转炉冶炼工序:转炉采用高碱度、高氧化性炉渣,实现低碳低磷冶炼,转炉吹氧量控制在48nm3/吨钢,吹氧流量设定800nm3/min,终点氧控制在0.040%,控制终点温度1610℃,终点c:0.035%,p:0.015%,出钢后进行脱氧合金化,控制als:0.030%,转炉出站s:0.008%;
69.3)lf精炼工序:精炼lf工序钢水进站后进行温度测定,送电升温,根据温度测定
值,按照1610℃进行设定升温时间,送电升温同时加入石灰,石灰加入量按照5kg/吨钢加入,停电后进行脱硫和取样,合金调整,同时加入ti铁,喂入纯钙线,调整净吹气量,并保持净吹时间6min;
70.4)连铸工序:根据液相线计算公式得出钢水的液相线温度为1520℃,为确保连铸过热度在10-25℃;连铸浇铸时保证中包温度在1530-1545℃,拉速控制在1.1m/min;
71.5)轧制工序:
72.(1)当加热温度1140℃、加热时间140min、终轧温度820℃、前段1/2冷却、卷取温度460℃得到的是510l产品;
73.(2)当加热温度1161℃、加热时间161min、终轧温度841℃、前段1/2冷却、卷取温度491℃得到的是550l产品;
74.(3)当加热温度1181℃、加热时间181min、终轧温度861℃、前段3/4冷却、卷取温度521℃得到的是610l产品;
75.(4)当加热温度1201℃、加热时间201min、终轧温度881℃、前段3/4冷却、卷取温度551℃得到的是650l产品;
76.(5)当加热温度1221℃、加热时间221min、终轧温度901℃、前段集中冷却、卷取温度581℃得到的是700l产品。
77.实施例1获得3mm厚度大梁钢成分控制及性能情况如表1。
78.表1实施例1成分控制及性能情况
[0079][0080]
对3mm厚度的510l、550l、610l、650l、700l大梁钢按照发明设计的成分、工艺进行生产,总体控制满足设计预期,同一成分不同轧制工艺的各牌号均能满足标准要求,图1显示为本实施例1的510l微观组织为铁素体 珠光体,厚度方向不同位置组织均匀,晶粒度等级11级。
[0081]
实施例2
[0082]
一种一钢多级多规格大梁钢的生产方法,包括铁水预处理、转炉冶炼、lf精炼、连铸、轧制工序;具体工艺如下:
[0083]
1)铁水预处理工序:根据设计的成分进行冶炼,铁水预脱硫,铁水预脱硫工序采用脱硫剂(mg粉/白灰=1:3)进行喷吹脱硫,脱硫剂喷吹量为3.3kg/吨钢,脱硫后铁水硫质量百分比0.0018%;
[0084]
2)转炉冶炼工序:转炉采用高碱度、高氧化性炉渣,实现低碳低磷冶炼,转炉吹氧
量控制在50nm3/吨钢,吹氧流量设定850nm3/min,终点氧控制在0.06%,控制终点温度1630℃,终点c:0.030%,p:0.014%,出钢后进行脱氧合金化,控制als:0.050%,转炉出站s:0.007%;
[0085]
3)lf精炼工序:精炼lf工序钢水进站后进行温度测定,送电升温,根据温度测定值,按照1610℃进行设定升温时间,送电升温同时加入石灰,石灰加入量按照5.5kg/吨钢加入,停电后进行脱硫和取样,合金调整,同时加入ti铁,喂入纯钙线,调整净吹气量,并保持净吹时间12min;
[0086]
4)连铸工序:根据液相线计算公式得出钢水的液相线温度为1520℃,为确保连铸过热度在10-25℃;连铸浇铸时保证中包温度在1530-1545℃,拉速控制在1.3m/min;
[0087]
5)轧制工序:
[0088]
(1)当加热温度1160℃、加热时间160min、终轧温度840℃、前段1/2冷却、卷取温度490℃得到的是510l产品;
[0089]
(2)当加热温度1180℃、加热时间180min、终轧温度860℃、前段1/2冷却、卷取温度520℃得到的是550l产品;
[0090]
(3)当加热温度1200℃、加热时间200min、终轧温度880℃、前段3/4冷却、卷取温度550℃得到的是610l产品;
[0091]
(4)当加热温度1220℃、加热时间220min、终轧温度900℃、前段3/4冷却、卷取温度580℃得到的是650l产品;
[0092]
(5)当加热温度1240℃、加热时间240min、终轧温度920℃、前段集中冷却、卷取温度620℃得到的是700l产品。
[0093]
实施例2获得3mm厚度大梁钢成分控制及性能情况如表2。
[0094]
表2实施例2成分控制及性能情况
[0095][0096]
对3mm厚度的510l、550l、610l、650l、700l大梁钢按照发明设计的成分、工艺进行生产,总体控制满足设计预期,同一成分不同轧制工艺的各牌号均能满足标准要求,图2显示为本实施例2的550l微观组织为铁素体 珠光体,厚度方向不同位置组织均匀,晶粒度等级11级。
[0097]
实施例3
[0098]
一种一钢多级多规格大梁钢的生产方法,包括铁水预处理、转炉冶炼、lf精炼、连铸、轧制工序;具体工艺如下:
[0099]
1)铁水预处理工序:根据设计的成分进行冶炼,铁水预脱硫,铁水预脱硫工序采用脱硫剂(mg粉/白灰=1:3)进行喷吹脱硫,脱硫剂喷吹量为3.1kg/吨钢,脱硫后铁水硫质量百分比0.0017%;
[0100]
2)转炉冶炼工序:转炉采用高碱度、高氧化性炉渣,实现低碳低磷冶炼,转炉吹氧量控制在49nm3/吨钢,吹氧流量设定830nm3/min,终点氧控制在0.05%,控制终点温度1620℃,终点c:0.033%,p:0.013%,出钢后进行脱氧合金化,控制als:0.040%,转炉出站s:0.006%;
[0101]
3)lf精炼工序:精炼lf工序钢水进站后进行温度测定,送电升温,根据温度测定值,按照1610℃进行设定升温时间,送电升温同时加入石灰,石灰加入量按照5.2kg/吨钢加入,停电后进行脱硫和取样,合金调整,同时加入ti铁,喂入纯钙线,调整净吹气量,并保持净吹时间10min;
[0102]
4)连铸工序:根据液相线计算公式得出钢水的液相线温度为1520℃,为确保连铸过热度在10-25℃;连铸浇铸时保证中包温度在1530-1545℃,拉速控制在1.2m/min;
[0103]
5)轧制工序:
[0104]
(1)当加热温度1150℃、加热时间151min、终轧温度833℃、前段1/2冷却、卷取温度480℃得到的是510l产品;
[0105]
(2)当加热温度1170℃、加热时间170min、终轧温度850℃、前段1/2冷却、卷取温度510℃得到的是550l产品;
[0106]
(3)当加热温度1190℃、加热时间190min、终轧温度871℃、前段3/4冷却、卷取温度540℃得到的是610l产品;
[0107]
(4)当加热温度1211℃、加热时间210min、终轧温度891℃、前段3/4冷却、卷取温度570℃得到的是650l产品;
[0108]
(5)当加热温度1230℃、加热时间230min、终轧温度905℃、前段集中冷却、卷取温度600℃得到的是700l产品。
[0109]
实施例3获得3mm厚度大梁钢成分控制及性能情况如表3。
[0110]
表3实施例3成分控制及性能情况
[0111][0112][0113]
对3mm厚度的510l、550l、610l、650l、700l大梁钢按照发明设计的成分、工艺进行生产,总体控制满足设计预期,同一成分不同轧制工艺的各牌号均能满足标准要求,图3显
示为本实施例3的610l微观组织为铁素体 珠光体,厚度方向不同位置组织均匀,晶粒度等级12级。
[0114]
实施例4
[0115]
一种一钢多级多规格大梁钢的生产方法,包括铁水预处理、转炉冶炼、lf精炼、连铸、轧制工序;具体工艺如下:
[0116]
1)铁水预处理工序:根据设计的成分进行冶炼,铁水预脱硫,铁水预脱硫工序采用脱硫剂(mg粉/白灰=1:3)进行喷吹脱硫,脱硫剂喷吹量为3kg/吨钢,脱硫后铁水硫质量百分比0.0020%;
[0117]
2)转炉冶炼工序:转炉采用高碱度、高氧化性炉渣,实现低碳低磷冶炼,转炉吹氧量控制在48nm3/吨钢,吹氧流量设定800nm3/min,终点氧控制在0.04%,控制终点温度1610℃,终点c:0.035%,p:0.012%,出钢后进行脱氧合金化,控制als:0.030%,转炉出站s:0.008%;
[0118]
3)lf精炼工序:精炼lf工序钢水进站后进行温度测定,送电升温,根据温度测定值,按照1610℃进行设定升温时间,送电升温同时加入石灰,石灰加入量按照5kg/吨钢加入,停电后进行脱硫和取样,合金调整,同时加入ti铁,喂入纯钙线,调整净吹气量,并保持净吹时间6min;
[0119]
4)连铸工序:根据液相线计算公式得出钢水的液相线温度为1520℃,为确保连铸过热度在10-25℃;连铸浇铸时保证中包温度在1530-1545℃,拉速控制在1.1m/min;
[0120]
5)轧制工序:
[0121]
(1)当加热温度1140℃、加热时间140min、终轧温度820℃、前段1/2冷却、卷取温度460℃得到的是510l产品;
[0122]
(2)当加热温度1161℃、加热时间161min、终轧温度841℃、前段1/2冷却、卷取温度491℃得到的是550l产品;
[0123]
(3)当加热温度1181℃、加热时间181min、终轧温度861℃、前段3/4冷却、卷取温度521℃得到的是610l产品;
[0124]
(4)当加热温度1201℃、加热时间201min、终轧温度881℃、前段3/4冷却、卷取温度551℃得到的是650l产品;
[0125]
(5)当加热温度1221℃、加热时间221min、终轧温度901℃、前段集中冷却、卷取温度581℃得到的是700l产品。
[0126]
实施例4获得8mm厚度大梁钢成分控制及性能情况如表4。
[0127]
表4实施例4成分控制及性能情况
[0128][0129]
对8mm厚度的510l、550l、610l、650l、700l大梁钢按照发明设计的成分、工艺进行生产,总体控制满足设计预期,同一成分不同轧制工艺的各牌号均能满足标准要求,图4显示为本实施例4的510l微观组织为铁素体 珠光体,厚度方向不同位置组织均匀,晶粒度等级11级。
[0130]
实施例5
[0131]
一种一钢多级多规格大梁钢的生产方法,包括铁水预处理、转炉冶炼、lf精炼、连铸、轧制工序;具体工艺如下:
[0132]
1)铁水预处理工序:根据设计的成分进行冶炼,铁水预脱硫,铁水预脱硫工序采用脱硫剂(mg粉/白灰=1:3)进行喷吹脱硫,脱硫剂喷吹量为3.3kg/吨钢,脱硫后铁水硫质量百分比0.0015%;
[0133]
2)转炉冶炼工序:转炉采用高碱度、高氧化性炉渣,实现低碳低磷冶炼,转炉吹氧量控制在50nm3/吨钢,吹氧流量设定830nm3/min,终点氧控制在0.06%,控制终点温度1620℃,终点c:0.030%,p:0.012%,出钢后进行脱氧合金化,控制als:0.040%,转炉出站s:0.005%;
[0134]
3)lf精炼工序:精炼lf工序钢水进站后进行温度测定,送电升温,根据温度测定值,按照1610℃进行设定升温时间,送电升温同时加入石灰,石灰加入量按照5.5kg/吨钢加入,停电后进行脱硫和取样,合金调整,同时加入ti铁,喂入纯钙线,调整净吹气量,并保持净吹时间8min;
[0135]
4)连铸工序:根据液相线计算公式得出钢水的液相线温度为1520℃,为确保连铸过热度在10-25℃;连铸浇铸时保证中包温度在1530-1545℃,拉速控制在1.3m/min;
[0136]
5)轧制工序:
[0137]
(1)当加热温度1160℃、加热时间160min、终轧温度840℃、前段1/2冷却、卷取温度490℃得到的是510l产品;
[0138]
(2)当加热温度1180℃、加热时间180min、终轧温度860℃、前段1/2冷却、卷取温度520℃得到的是550l产品;
[0139]
(3)当加热温度1200℃、加热时间200min、终轧温度880℃、前段3/4冷却、卷取温度550℃得到的是610l产品;
[0140]
(4)当加热温度1220℃、加热时间220min、终轧温度900℃、前段3/4冷却、卷取温度580℃得到的是650l产品;
[0141]
(5)当加热温度1240℃、加热时间240min、终轧温度920℃、前段集中冷却、卷取温度620℃得到的是700l产品。
[0142]
实施例5获得8mm厚度大梁钢成分控制及性能情况如表5。
[0143]
表5实施例5成分控制及性能情况
[0144][0145]
对8mm厚度的510l、550l、610l、650l、700l大梁钢按照发明设计的成分、工艺进行生产,总体控制满足设计预期,同一成分不同轧制工艺的各牌号均能满足标准要求,图5显示为本实施例5的550l微观组织为铁素体 珠光体,厚度方向不同位置组织均匀,晶粒度等级11级。
[0146]
实施例6
[0147]
一种一钢多级多规格大梁钢的生产方法,包括铁水预处理、转炉冶炼、lf精炼、连铸、轧制工序;具体工艺如下:
[0148]
1)铁水预处理工序:根据设计的成分进行冶炼,铁水预脱硫,铁水预脱硫工序采用脱硫剂(mg粉/白灰=1:3)进行喷吹脱硫,脱硫剂喷吹量为3.2kg/吨钢,脱硫后铁水硫质量百分比0.0016%;
[0149]
2)转炉冶炼工序:转炉采用高碱度、高氧化性炉渣,实现低碳低磷冶炼,转炉吹氧量控制在49nm3/吨钢,吹氧流量设定850nm3/min,终点氧控制在0.052%,控制终点温度1630℃,终点c:0.033%,p:0.011%,出钢后进行脱氧合金化,控制als:0.050%,转炉出站s:0.005%;
[0150]
3)lf精炼工序:精炼lf工序钢水进站后进行温度测定,送电升温,根据温度测定值,按照1610℃进行设定升温时间,送电升温同时加入石灰,石灰加入量按照5.3kg/吨钢加入,停电后进行脱硫和取样,合金调整,同时加入ti铁,喂入纯钙线,调整净吹气量,并保持净吹时间12min;
[0151]
4)连铸工序:根据液相线计算公式得出钢水的液相线温度为1520℃,为确保连铸过热度在10-25℃;连铸浇铸时保证中包温度在1530-1545℃,拉速控制在1.15m/min;
[0152]
5)轧制工序:
[0153]
(1)当加热温度1150℃、加热时间153min、终轧温度835℃、前段1/2冷却、卷取温度485℃得到的是510l产品;
[0154]
(2)当加热温度1171℃、加热时间172min、终轧温度855℃、前段1/2冷却、卷取温度513℃得到的是550l产品;
[0155]
(3)当加热温度1192℃、加热时间190min、终轧温度873℃、前段3/4冷却、卷取温度539℃得到的是610l产品;
[0156]
(4)当加热温度1215℃、加热时间215min、终轧温度895℃、前段3/4冷却、卷取温度568℃得到的是650l产品;
[0157]
(5)当加热温度1235℃、加热时间235min、终轧温度908℃、前段集中冷却、卷取温度606℃得到的是700l产品。
[0158]
实施例6获得8mm厚度大梁钢成分控制及性能情况如表6。
[0159]
表6实施例6成分控制及性能情况
[0160][0161]
对8mm厚度的510l、550l、610l、650l、700l大梁钢按照发明设计的成分、工艺进行生产,总体控制满足设计预期,同一成分不同轧制工艺的各牌号均能满足标准要求,图6显示为本实施例6的610l微观组织为铁素体 珠光体,厚度方向不同位置组织均匀,晶粒度等级12级。
[0162]
实施例7
[0163]
一种一钢多级多规格大梁钢的生产方法,包括铁水预处理、转炉冶炼、lf精炼、连铸、轧制工序;具体工艺如下:
[0164]
1)铁水预处理工序:根据设计的成分进行冶炼,铁水预脱硫,铁水预脱硫工序采用脱硫剂(mg粉/白灰=1:3)进行喷吹脱硫,脱硫剂喷吹量为3kg/吨钢,脱硫后铁水硫质量百分比0.0015%;
[0165]
2)转炉冶炼工序:转炉采用高碱度、高氧化性炉渣,实现低碳低磷冶炼,转炉吹氧量控制在48nm3/吨钢,吹氧流量设定800nm3/min,终点氧控制在0.04%,控制终点温度1630℃,终点c:0.030%,p:0.012%,出钢后进行脱氧合金化,控制als:0.050%,转炉出站s:0.006%;
[0166]
3)lf精炼工序:精炼lf工序钢水进站后进行温度测定,送电升温,根据温度测定值,按照1610℃进行设定升温时间,送电升温同时加入石灰,石灰加入量按照5kg/吨钢加入,停电后进行脱硫和取样,合金调整,同时加入ti铁,喂入纯钙线,调整净吹气量,并保持净吹时间12min;
[0167]
4)连铸工序:根据液相线计算公式得出钢水的液相线温度为1520℃,为确保连铸过热度在10-25℃;连铸浇铸时保证中包温度在1530-1545℃,拉速控制在1.1m/min;
[0168]
5)轧制工序:
[0169]
(1)当加热温度1160℃、加热时间160min、终轧温度840℃、前段1/2冷却、卷取温度490℃得到的是510l产品;
[0170]
(2)当加热温度1180℃、加热时间180min、终轧温度860℃、前段1/2冷却、卷取温度520℃得到的是550l产品;
[0171]
(3)当加热温度1200℃、加热时间200min、终轧温度880℃、前段3/4冷却、卷取温度550℃得到的是610l产品;
[0172]
(4)当加热温度1220℃、加热时间220min、终轧温度900℃、前段3/4冷却、卷取温度580℃得到的是650l产品;
[0173]
(5)当加热温度1240℃、加热时间240min、终轧温度920℃、前段集中冷却、卷取温度620℃得到的是700l产品。
[0174]
实施例7 15mm厚度大梁钢成分控制及性能情况如表7。
[0175]
表7实施例7成分控制及性能情况
[0176][0177]
对15mm厚度的510l、550l、610l、650l、700l大梁钢按照发明设计的成分、工艺进行生产,总体控制满足设计预期,同一成分不同轧制工艺的各牌号均能满足标准要求,图7显示为本实施例7的650l微观组织为铁素体 珠光体,可见弥散析出的含ti化合物,厚度方向不同位置组织均匀,晶粒度等级12级。
[0178]
实施例8
[0179]
一种一钢多级多规格大梁钢的生产方法,包括铁水预处理、转炉冶炼、lf精炼、连铸、轧制工序;具体工艺如下:
[0180]
1)铁水预处理工序:根据设计的成分进行冶炼,铁水预脱硫,铁水预脱硫工序采用脱硫剂(mg粉/白灰=1:3)进行喷吹脱硫,脱硫剂喷吹量为3.3kg/吨钢,脱硫后铁水硫质量百分比0.0017%;
[0181]
2)转炉冶炼工序:转炉采用高碱度、高氧化性炉渣,实现低碳低磷冶炼,转炉吹氧量控制在50nm3/吨钢,吹氧流量设定810nm3/min,终点氧控制在0.06%,控制终点温度1625℃,终点c:0.035%,p:0.013%,出钢后进行脱氧合金化,控制als:0.045%,转炉出站s:0.007%;
[0182]
3)lf精炼工序:精炼lf工序钢水进站后进行温度测定,送电升温,根据温度测定值,按照1610℃进行设定升温时间,送电升温同时加入石灰,石灰加入量按照5.5kg/吨钢加入,停电后进行脱硫和取样,合金调整,同时加入ti铁,喂入纯钙线,调整净吹气量,并保持
净吹时间9min;
[0183]
4)连铸工序:根据液相线计算公式得出钢水的液相线温度为1520℃,为确保连铸过热度在10-25℃;连铸浇铸时保证中包温度在1530-1545℃,拉速控制在1.3m/min;
[0184]
5)轧制工序:
[0185]
(1)当加热温度1160℃、加热时间160min、终轧温度840℃、前段1/2冷却、卷取温度490℃得到的是510l产品;
[0186]
(2)当加热温度1180℃、加热时间180min、终轧温度860℃、前段1/2冷却、卷取温度520℃得到的是550l产品;
[0187]
(3)当加热温度1200℃、加热时间200min、终轧温度880℃、前段3/4冷却、卷取温度550℃得到的是610l产品;
[0188]
(4)当加热温度1220℃、加热时间220min、终轧温度900℃、前段3/4冷却、卷取温度580℃得到的是650l产品;
[0189]
(5)当加热温度1240℃、加热时间240min、终轧温度920℃、前段集中冷却、卷取温度620℃得到的是700l产品。
[0190]
实施例8获得15mm厚度大梁钢成分控制及性能情况如表8。
[0191]
表8实施例8成分控制及性能情况
[0192][0193][0194]
对15mm厚度的510l、550l、610l、650l、700l大梁钢按照发明设计的成分、工艺进行生产,总体控制满足设计预期,同一成分不同轧制工艺的各牌号均能满足标准要求,图8显示为本实施例8的650l微观组织为铁素体 珠光体,可见弥散析出的含ti化合物,厚度方向不同位置组织均匀,晶粒度等级12级。
[0195]
实施例9
[0196]
一种一钢多级多规格大梁钢的生产方法,包括铁水预处理、转炉冶炼、lf精炼、连铸、轧制工序;具体工艺如下:
[0197]
1)铁水预处理工序:根据设计的成分进行冶炼,铁水预脱硫,铁水预脱硫工序采用脱硫剂(mg粉/白灰=1:3)进行喷吹脱硫,脱硫剂喷吹量为3.1kg/吨钢,脱硫后铁水硫质量百分比0.0020%;
[0198]
2)转炉冶炼工序:转炉采用高碱度、高氧化性炉渣,实现低碳低磷冶炼,转炉吹氧量控制在49nm3/吨钢,吹氧流量设定850nm3/min,终点氧控制在0.05%,控制终点温度1610
℃,终点c:0.035%,p:0.015%,出钢后进行脱氧合金化,控制als:0.030%,转炉出站s:0.008%;
[0199]
3)lf精炼工序:精炼lf工序钢水进站后进行温度测定,送电升温,根据温度测定值,按照1610℃进行设定升温时间,送电升温同时加入石灰,石灰加入量按照5.2kg/吨钢加入,停电后进行脱硫和取样,合金调整,同时加入ti铁,喂入纯钙线,调整净吹气量,并保持净吹时间6min;
[0200]
4)连铸工序:根据液相线计算公式得出钢水的液相线温度为1520℃,为确保连铸过热度在10-25℃;连铸浇铸时保证中包温度在1530-1545℃,拉速控制在1.2m/min;
[0201]
5)轧制工序:
[0202]
(1)当加热温度1155℃、加热时间154min、终轧温度831℃、前段1/2冷却、卷取温度486℃得到的是510l产品;
[0203]
(2)当加热温度1173℃、加热时间168min、终轧温度853℃、前段1/2冷却、卷取温度511℃得到的是550l产品;
[0204]
(3)当加热温度1191℃、加热时间194min、终轧温度875℃、前段3/4冷却、卷取温度541℃得到的是610l产品;
[0205]
(4)当加热温度1208℃、加热时间212min、终轧温度898℃、前段3/4冷却、卷取温度569℃得到的是650l产品;
[0206]
(5)当加热温度1233℃、加热时间228min、终轧温度907℃、前段集中冷却、卷取温度616℃得到的是700l产品。
[0207]
实施例9获得15mm厚度大梁钢成分控制及性能情况如表9。
[0208]
表9实施例9成分控制及性能情况
[0209][0210]
对15mm厚度的510l、550l、610l、650l、700l大梁钢按照发明设计的成分、工艺进行生产,总体控制满足设计预期,同一成分不同轧制工艺的各牌号均能满足标准要求,图9显示为本实施例9的700l微观组织为铁素体 珠光体,可见弥散析出的含ti化合物,厚度方向不同位置组织均匀,晶粒度等级12级。
[0211]
通过上述实施例1-9可以得知,本发明一种一钢多级大梁钢及其生产方法,通过对大梁钢基础固溶强化元素含量进行确定,添加廉价的金属ti,对热轧工序加热制度、轧制制度、冷却制度、卷取制度进行针对性调整和优化,生产出能够满足大梁钢系列牌号对应性能要求的大梁钢产品,不浪费成本、一个成分对应多个牌号,生产组织更灵活方便,提高生产
效率,增加合同的承接率和交付率,对企业高效、智能制造发展具有重要意义。
[0212]
以上实施例仅用以说明而非限制本发明的技术方案,尽管参照上述实施例对本发明进行了详细说明,本领域的普通技术人员应当理解:依然可以对本发明进行修改或者等同替换,而不脱离本发明的精神和范围的任何修改或局部替换,其均应涵盖在本发明的权利要求范围当中。
再多了解一些
本文用于企业家、创业者技术爱好者查询,结果仅供参考。