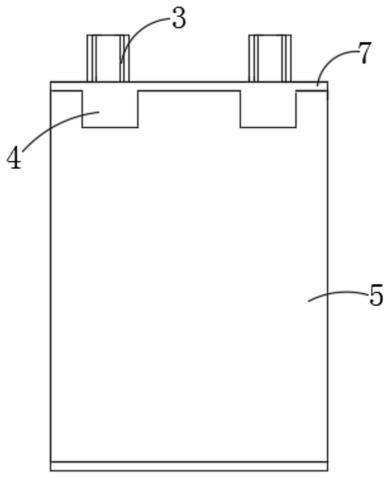
1.本发明属于锂电池技术领域,具体涉及一种多极耳电芯制作工艺和多极耳电芯。
背景技术:
2.目前,在锂电池行业内,多箔材极耳结构电芯的头部折箔材极耳结构常用二折方案,其折弯一致性较差,且折弯后结构较松散,易在顶封前张开,导致裸电芯入壳困难,对封装时的箔材极耳位置影响较大,封装优率较低,同时在电芯头部占用一定的长度空间,电芯内部空间利用率较低,导致电芯的能量密度存在一定损失。
技术实现要素:
3.本发明的目的之一在于:针对现有技术存在的不足,提供了一种多极耳电芯制作工艺,其能够提高箔材极耳群弯折一致性,保证弯折后的箔材极耳群结构紧凑,降低了裸电芯的封装难度,同时,能够提高裸电芯的能量密度。
4.为了实现上述目的,本发明采用以下技术方案:一种多极耳电芯制作工艺,包括s1、制备极片:经过搅拌、涂布、辊压和分切工艺,制备极片;s2、箔材极耳模切:在所述极片上裁切出箔材极耳和容置槽;s3、制备多极耳电芯:将所述极片和隔膜卷绕,制备得多极耳电芯;s4、第一次裁切:将所述箔材极耳模切成预设形状;s5、箔材极耳焊接:将多个所述箔材极耳压合后向上弯折,所述箔材极耳的一竖直面与金属带极耳固定连接;s6、第二次裁切:对所述箔材极耳进行裁切;s7、折箔材极耳:将所述箔材极耳向所述容置槽内弯折,使得所述箔材极耳和所述金属带极耳容置于所述容置槽内;s8、贴保护胶:将保护胶纸分别贴在所述箔材极耳和所述金属带极耳上。
5.进一步地,在s2步骤中,所述箔材极耳和所述容置槽同侧设置。
6.进一步地,在s2步骤中,所述箔材极耳的宽度小于或等于所述容置槽的宽度。
7.进一步地,在s4步骤中,所述箔材极耳呈凸台型或一字型。
8.进一步地,在s5步骤中,所述箔材极耳的弯折角度为90
°
。
9.进一步地,在s7步骤中,所述箔材极耳的弯折角度为90
°
。
10.进一步地,在s5步骤中,通过上压块和下压块对所述箔材极耳进行压合,压合温度为50~100℃,压合的压力值为0.8mpa~1.2mpa。
11.进一步地,在s4步骤中,采用激光对所述箔材极耳进行模切,在s6步骤中,采用刀模对所述箔材极耳进行裁切。
12.进一步地,在s5步骤中,通过超声波焊接工艺将所述金属带极耳固定焊接在所述箔材极耳的一侧。
13.本发明的目的之二在于:提供了一种多极耳电芯,由上述的多极耳电芯制作工艺制备,其能够降低箔材极耳弯折后的空间占用率,提高多极耳电芯的能量密度,保证箔材极耳群结构紧凑。
14.本发明的有益效果在于:
15.1、与常规多极耳电芯的头部折极耳结构相比,本发明提供的一种多极耳电芯制作工艺,其提高了箔材极耳群在弯折后的一致性,避免箔材极耳群出现松散的情况,提高裸电芯的封装优率;
16.2、与常规多极耳电芯的头部折极耳结构相比,本发明提供的一种多极耳电芯制作工艺,其能够降低箔材极耳弯折后的空间占用率,提高多极耳电芯的能量密度。
附图说明
17.图1为本发明实施例1中的阳极极片的结构示意图;
18.图2为本发明实施例1中的阴极极片的结构示意图;
19.图3为本发明实施例1中的多极耳电芯在第一次裁切箔材极耳前的示意图;
20.图4为本发明实施例1中的多极耳电芯在第一次裁切箔材极耳后的示意图;
21.图5为本发明实施例1中的箔材极耳在收拢前的示意图;
22.图6为本发明实施例1中的箔材极耳在收拢后的示意图;
23.图7为本发明实施例1中的箔材极耳在第二次裁切时的示意图;
24.图8为本发明实施例1中的箔材极耳和金属带极耳焊接后的示意图;
25.图9为本发明实施例1中的箔材极耳第二次弯折后的示意图;
26.图10为本发明实施例1中的多极耳电芯的结构示意图;
27.其中:1、阳极极片;2、阴极极片;3、箔材极耳;4、容置槽;5、多极耳电芯;6、金属带极耳;7、隔膜;8、上压块;9、下压块;10、左刀模;11、右刀模;12、保护胶。
具体实施方式
28.在申请的描述中,需要理解的是,术语“上”、“下”、“前”、“后”、“左”、“右”、水平”等指示的方位或位置关系为基于附图所示的方位或位置关系,仅是为了便于描述本发明和简化描述,而不是指示或暗示所指的装置或元件必须具有特定的方位、以特定的方位构造和操作,因此不能理解为对本发明的限制。
29.在本技术的描述中,除非另有明确的规定和限定,术语“第一”、“第二”、“第三”仅用于描述的目的,而不能理解为指示或暗示相对重要性;术语“多个”是指两个或两个以上;除非另有规定或说明,术语“连接”、“固定”等均应做广义理解,例如,“连接”可以是固定连接,也可以是可拆卸连接,或一体地连接,或电连接;“连接”可以是直接相连,也可以通过中间媒介间接相连。对于本领域的普通技术人员而言,可以根据具体情况理解上述术语在本技术中的具体含义。
30.在本发明的描述中,除非另有明确的规定和限定,术语“安装”、“相连”、“连接”、“固定”应做广义理解,例如,可以是固定连接,也可以是可拆卸连接,或成一体;可以是机械连接,也可以是电连接;可以是直接相连,也可以通过中间媒介间接相连,可以是两个元件内部的连通或两个元件的相互作用关系。对于本领域的普通技术人员而言,可以具体情况理解上述术语在本发明中的具体含义。
31.对于本领域技术人员而言,显然本发明不限于上述示范性实施例的细节,而且在不背离本发明的精神或基本特征的情况下,能够以其他的具体形式实现本发明。因此,无论从哪一点来看,均应将实施例看作是示范性的,而且是非限制性的,本发明的范围由所附权
利要求而不是上述说明限定,因此旨在将落在权利要求的等同要件的含义和范围内的所有变化囊括在本发明内。不应将权利要求中的任何附图标记视为限制所涉及的权利要求。
32.为使本发明的技术方案和优点更加清楚,下面将结合具体实施方式和说明书附图,对本发明及其有益效果作进一步详细的描述,但本发明的实施方式不限于此。
33.实施例1
34.如图1~10所示,本实施例1提供的一种多极耳电芯制作工艺,包括s1、制备极片:经过搅拌、涂布、辊压和分切工艺,制备极片;s2、箔材极耳3模切:在极片上裁切出多个箔材极耳3和多个容置槽4;s3、制备多极耳电芯5:将极片和隔膜7卷绕,制备得多极耳电芯5;s4、第一次裁切:将箔材极耳3模切成预设形状;s5、箔材极耳3焊接:将多个箔材极耳3压合后向上弯折,箔材极耳3的一竖直面与金属带极耳6固定连接;s6、第二次裁切:对箔材极耳3进行裁切;s7、折箔材极耳3:将箔材极耳3向容置槽4内弯折,使得箔材极耳3和金属带极耳6容置于容置槽4内;s8、贴保护胶12:将保护胶12纸分别贴在箔材极耳3和金属带极耳6上。
35.具体地,按照电芯型号设计要求依次经过搅拌、涂布、辊压、分切、极耳模切和容置槽4模切等工艺,制备得相互匹配的阴极极片2和阳极极片1,阴极极片2、阳极极片1和隔膜7卷绕成多极耳电芯5。
36.需要说明的是,本实施例1中,阴极极片2包括空白区、敷料区和安全区,安全区位于空白区和敷料区之间,安全区涂覆有安全涂层,其中,安全涂层和敷料区可邻接设置,安全涂层和敷料区可同时涂覆,从而能够节约涂覆时间,还能够在后续辊压时保证敷料区和安全区的应力和延展性相同,避免在辊压时出现波浪起皱的现象。在一些实施例中,安全涂层和敷料区部分重叠设置,安全涂层和敷料区间歇涂覆,如此设置,对涂布设备的涂布精密程度要求相对较低,降低生产成本。当激光模切时,其沿空白区表面的安全涂层模切,可避免极片产生毛刺,能够防止因模切产生的毛刺刺破隔膜7而导致电芯内部发生短路,提高了电芯的安全性能。
37.目前,在锂电池头部折极耳结构中,均是在裸电芯的一侧将箔材极耳3经过至少两次弯折后与外接的金属带极耳6焊接在一起,在弯折过程中,箔材极耳3弯折一致性差,结构松散,增加了金属带极耳6和箔材极耳3的焊接难度,而且,容易使得箔材极耳3在裸电芯头部占用较大空间,增加了电池的体积,增大了裸电芯的入壳难度,针对目前行业存在的不足,本实施例1提供的一种多极耳电芯制作工艺,其在s2步骤中,在极片的空白区剪切出极耳,同时,在敷料区裁切出容置槽4,容置槽4的裁切位置和极耳的裁切位置相互匹配,保证阴阳极片片和隔膜7卷绕成裸电芯后,容置槽4能够分别与正极箔材极耳和负极箔材极耳正对齐,便于将正极箔材极耳和负极箔材极耳弯折放置在容置槽4内,减少正极箔材极耳和负极箔材极耳在裸电芯头部的空间占用率。
38.为了提高电池的能量密度和裸电芯的封装优率,本实施例1提供的一种多极耳电芯制作工艺,其箔材极耳3从多极耳电芯5一侧水平引出后,沿多极耳电芯5的侧面向上弯折90
°
,然后将箔材极耳3的一竖直面与金属带极耳6贴合,并通过超声波焊接工艺使之固定连接在一起,再次将箔材极耳3向容置槽4弯折,其弯折角度为90
°
,使得箔材极耳3的一端容置在容置槽4内,一端和多极耳电芯5连接。其中,金属带极耳6始终呈一字型,从而保证金属带极耳6和箔材极耳3的连接牢固性。
39.在本实施例1中,隔膜7包括基材层和表面处理层。基材层为具有多孔结构的无纺
布、膜或复合膜,基材层的材料选自聚乙烯、聚丙烯、聚对苯二甲酸乙二醇酯和聚酰亚胺中的至少一种。具体的,可选用聚丙烯多孔膜、聚乙烯多孔膜、聚丙烯无纺布、聚乙烯无纺布或聚丙烯-聚乙烯-聚丙烯多孔复合膜。
40.具体地,基材层的至少一个表面上设置有表面处理层,表面处理层可以为聚合物层或无机物层,也可以为混合聚合物与无机物所形成的层。无机物层包括无机颗粒和粘结剂,无机颗粒选自氧化铝、氧化硅、氧化镁、氧化钛、二氧化铪、氧化锡、二氧化铈、氧化镍、氧化锌、氧化钙、氧化锆、氧化钇、碳化硅、勃姆石、氢氧化铝、氢氧化镁、氢氧化钙和硫酸钡中的一种或几种的组合。粘结剂选自聚偏氟乙烯、偏氟乙烯-六氟丙烯的共聚物、聚酰胺、聚丙烯腈、聚丙烯酸酯、聚丙烯酸、聚丙烯酸盐、聚乙烯呲咯烷酮、聚乙烯醚、聚甲基丙烯酸甲酯、聚四氟乙烯和聚六氟丙烯中的一种或几种的组合。聚合物层中包含聚合物,聚合物的材料选自聚酰胺、聚丙烯腈、丙烯酸酯聚合物、聚丙烯酸、聚丙烯酸盐、聚乙烯呲咯烷酮、聚乙烯醚、聚偏氟乙烯或聚(偏氟乙烯-六氟丙烯)中的至少一种。
41.为了提高隔膜7的耐热性能、抗氧化性能和电解质浸润性能,增强隔膜7与正负极片之间的粘接性。本实施例1提供的隔膜7,其表面设置有多孔层,多孔层设置在隔膜7的至少一个表面上,多孔层包括无机颗粒和粘结剂,无机颗粒选自氧化铝(al2o3)、氧化硅(sio2)、氧化镁(mgo)、氧化钛(tio2)、二氧化铪(hfo2)、氧化锡(sno2)、二氧化铈(ceo2)、氧化镍(nio)、氧化锌(zno)、氧化钙(cao)、氧化锆(zro2)、氧化钇(y2o3)、碳化硅(sic)、勃姆石、氢氧化铝、氢氧化镁、氢氧化钙或硫酸钡中的至少一种。粘结剂选自聚偏氟乙烯、偏氟乙烯-六氟丙烯的共聚物、聚酰胺、聚丙烯腈、聚丙烯酸酯、聚丙烯酸、聚丙烯酸盐、羧甲基纤维素纳、聚乙烯呲咯烷酮、聚乙烯醚、聚甲基丙烯酸甲酯、聚四氟乙烯或聚六氟丙烯中的至少一种。
42.优选地,在s2步骤中,箔材极耳3和容置槽4同侧设置。在剪切时,箔材极耳3的宽度小于或等于容置槽4的宽度,在本实施例1中,箔材极耳3的宽度比容置槽4的宽度小5~15mm,既能够保证箔材极耳3在弯折后能够容置在容置槽4内,同时,也能够保证裸电芯的能量密度符合生产要求。
43.优选地,在s4步骤中,箔材极耳3呈凸台型或一字型。在本实施例1中,箔材极耳3采用的是凸台型结构,这种结构设计,能够增强箔材极耳3和裸电芯的连接牢固性,同时,使得箔材极耳3易于弯折,本发明的箔材极耳3其外形结构不限于本实施例1所列举的类型,其还可为工字型、梯形等结构。
44.优选地,在s5步骤中,箔材极耳3的弯折角度为90
°
,在s7步骤中,箔材极耳3的弯折角度为90
°
。
45.优选地,在s5步骤中,通过上压块8和下压块9对箔材极耳3进行压合,压合温度为50~100℃,压合的压力值为0.8mpa~1.2mpa。在本实施例1中,压合温度优选为65℃,压合的压力值优选为1.2mpa,此处,仅作示例说明,可变换地,在其他可行的实施例中,压合温度还可为50℃、60℃、70℃、75℃、80℃、85℃、90℃、95℃或100℃,压合的压力值还可为0.8mpa、0.9mpa、1.0mpa或1.1mpa。在箔材极耳3弯折时,温度和压力值的配比,直接影响着极耳的弯折效果,温度过高或压力值过大,将会降低箔材极耳3的机械性能,甚至会导致箔材极耳3出现断裂,温度过低或压力值过小,将会导致箔材极耳3的弯折一致性差,降低了箔材极耳3和金属带极耳6的焊接牢固性。
46.优选地,在s4步骤中,采用激光对箔材极耳3进行模切,在s6步骤中,采用刀模对箔材极耳3进行裁切。在s4中采用激光模切出箔材极耳3,提高了箔材极耳3的裁切精度。此外,在s6步骤中,对于箔材极耳3的长度进行裁切时,刀模设置有两个,分别为左刀模10和右刀模11,箔材极耳3位于左刀模10和右刀模11之间,左刀模10和右刀模11同步进给,使得箔材极耳3在裁切时左右两侧受力均匀,有效避免了箔材极耳3弯曲变形的情况出现。
47.优选地,在s5步骤中,通过超声波焊接工艺将金属带极耳6固定焊接在箔材极耳3的一侧,采用超声波焊接避免了热熔融因温度过高或过低产生的一些负面影响,提高了金属带极耳6和箔材极耳3的连接牢固性。
48.需要说明的是,金属带极耳6和箔材极耳3之间的焊接方式还可以为激光焊接或其它的焊接方式。
49.实施例2
50.本实施例2提供的一种多极耳电芯,由实施例1的多极耳电芯制作工艺制备,其能够降低箔材极耳3弯折后的空间占用率,提高多极耳电芯5的能量密度,保证箔材极耳3结构紧凑。
51.此外,应当理解,虽然本说明书按照实施方式加以描述,但并非每个实施方式仅包含一个独立的技术方案,说明书的这种叙述方式仅仅是为清楚起见,本领域技术人员应当说明书作为一个整体,各实施例中的技术方案也可以经适当组合,形成本领域技术人员可以理解的其他实施方式。
52.根据上述说明书的揭示和教导,本发明所属领域的技术人员还能够对上述实施方式进行变更和修改。因此,本发明并不局限于上述的具体实施方式,凡是本领域技术人员在本发明的基础上所作出的任何显而易见的改进、替换或变型均属于本发明的保护范围。此外,尽管本说明书中使用了一些特定的术语,但这些术语只是为了方便说明,并不对本发明构成任何限制。
再多了解一些
本文用于企业家、创业者技术爱好者查询,结果仅供参考。