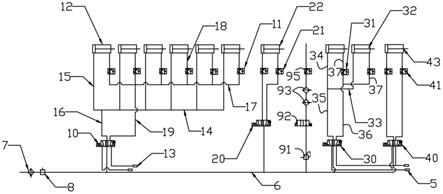
1.本实用新型涉及一种实验平台,具体涉及一种混合动力液压模块试验平台气动系统。
背景技术:
2.随着世界人口的迅速增长和各国经济的增长,人们对能源方面的需求日益增大,而石化能源的不可再生性导致全世界的石化能源不断减少,石化能源产生的能量已经不足够满足人们对能源方面的需求。以目前石化能源的消耗速度,根据国际的能源预测结果显示,地球上的石化能源(石油、煤、天然气)可供我们开采的年限分别只有40年、220年、60年。能源短缺和环境污染的问题促使各国研究和开发新能源和环保类产品。
3.交通工具的能源消耗占到世界能源消耗总量的40%,而汽车的能源消耗占到约1/4,随着高科技技术的发展,同时在节能和环保的压力下,各国纷纷开始研究和开发新能源汽车和节能环保型汽车。中国是世界汽车生产大国,根据发展研究中心产业部的预测,汽车的燃油消耗量将近达到全国石油总需求量的一半,且此能源消耗量将越来越大,导致我国新增的石油需求越来越依赖于进口,能源短缺问题越来越严重。
4.在面临能源短缺和环境污染的压力下,新能源的研究必须提上日程,混合动力作为领头羊在新能源方面起到了带头的作用,例如,将液压技术、电气技术进行结合并应用于汽车上,可制成混合动力汽车。混合动力汽车作为传统燃油汽车向纯电动汽车的过渡阶段,在我国汽车工业发展有着举足轻重的地位。由于混合动力汽车可采取不同的工作模式来适应实际行驶过程中多变的工况,以实现汽车动力性与燃油经济性的平衡,且能很大程度上减少污染气体的排放,其节能潜力和存续期不容小觑。混合动力汽车不同工作模式的切换是通过对离合器的控制来完成,且大多采用的是湿式离合器,而这个任务将由液压控制模块来承担,液压控制模块通过接受到的来自电控单元(tcu)的控制电信号,发送给电磁换向阀,以此来调节液压模块内的油液的压力和流量的大小及改变油液的流向,从而改变各元件所处状态,实现对离合器断开与接合的控制。
5.此外,追求自动化、省力化的今天,除了液压技术、电气技术等,气动技术也在快速发展,气动技术相比于液压与电气技术,具有结构简单、使用安全的优点,因此,气动技术在各行业已经被广泛地应用,在各行业有着举足轻重的作用。研究和发展气动技术是必要的,气动技术已经成为工业生产化的必不可少的使用技术,也是人类社会发展离不开的一门技术。因此,有必要提供一种气动系统,以利用气动系统对混合动力液压模块试验平台提供夹紧、翻转、定位、排残油的功能,进而方便对混合动力进行研究。
技术实现要素:
6.针对上述存在的问题,提供一种混合动力液压模块试验平台气动系统,以利用气动系统对混合动力液压模块试验平台提供夹紧、翻转、定位、排残油的功能,进而方便对混合动力进行研究。
7.为达到上述目的,本发明所采用的技术方案是:
8.一种混合动力液压模块试验平台气动系统,包括:
9.夹紧气动气路,包括第一电磁换向阀、第一调速阀及夹紧气缸,第一电磁换向阀的第一工作口连接夹紧气缸的第一气口,夹紧气缸的第二气口通过第一调速阀与第一电磁换向阀的第二工作口连接;
10.定位气动气路,包括第二电磁换向阀、第二调速阀及定位气缸,第二电磁换向阀的第一工作口通过一第二调速阀连接定位气缸的第一气口,定位气缸的第二气口通过另一第二调速阀与第二电磁换向阀的第二工作口连接;
11.翻转气动气路,包括第三电磁换向阀、第三调速阀及翻转气缸,第三电磁换向阀的第一工作口连接翻转气缸的第一气口,翻转气缸的第二气口通过第三调速阀与第三电磁换向阀的第二工作口连接;
12.排残油拨叉气动气路,包括第四电磁换向阀、第四调速阀及排残油拨叉气缸,第四电磁换向阀的第一工作口通过一第四调速阀连接排残油拨叉气缸的第一气口,排残油拨叉气缸的第二气口通过另一第四调速阀与第四电磁换向阀的第二工作口连接;
13.第一电磁换向阀的进气口、第二电磁换向阀的进气口、第三电磁换向阀的进气口及第四电磁换向阀的进气口均通过一主供气管路与气源连接;
14.外部供气气路,包括依次连接的减压阀、二通阀、精细过滤器及第五调速阀,减压阀的进气口与主供气管路连接。
15.进一步地,夹紧气缸的数量为多个,第一电磁换向阀的第一工作口通过第一气路与多个夹紧气缸的第一气口连接,第一气路包括第一主气管及与一端第一主气管连接的多个第一分支气管,第一主气管通过第一连接气管与第一电磁换向阀的第一工作口连接,多个第一分支气管的另一端分别与多个夹紧气缸的第一气口连接;第一电磁换向阀的第二工作口通过第二气路与多个夹紧气缸的第二气口连接,第二气路包括第二主气管及与一端第二主气管连接的多个第二分支气管,第二主气管通过第二连接气管与第一电磁换向阀的第二工作口连接,多个第二分支气管的另一端分别与多个夹紧气缸的第二气口连接;第一调速阀对应夹紧气缸设有多个,多个第一调速阀分别装设于对应的第二分支气管上。
16.进一步地,翻转气缸的数量为多个,第三电磁换向阀的第一工作口通过第三气路与多个翻转气缸的第一气口连接,第三气路包括第三主气管及与一端第三主气管连接的多个第三分支气管,第三主气管通过第三连接气管与第三电磁换向阀的第一工作口连接,多个第三分支气管的另一端分别与多个翻转气缸的第一气口连接;第三电磁换向阀的第二工作口通过第四气路与多个翻转气缸的第二气口连接,第四气路包括第四主气管及与一端第四主气管连接的多个第四分支气管,第四主气管的自由末端与第三电磁换向阀的第二工作口连接,多个第四分支气管的另一端分别与多个翻转气缸的第二气口连接;第四调速阀对应翻转气缸设有多个,多个第四调速阀分别装设于对应的第四分支气管上。
17.进一步地,第一电磁换向阀还与第一消声器连接。
18.进一步地,第三电磁换向阀及第四电磁换向阀还与第二消声器连接。
19.进一步地,第二消声器的数量为两个,第三电磁换向阀的第一排气口及第四电磁换向阀的第一排气口均与其中一第二消声器连接,第三电磁换向阀的第二排气口及第四电磁换向阀的第二排气口均与另一第二消声器连接。
20.进一步地,还包括均装设于主供气管路上的空气过滤器及控制阀,第一电磁换向阀的进气口依次通过控制阀及空气过滤器与气源连接,第二电磁换向阀的进气口依次通过控制阀及空气过滤器与气源连接,第三电磁换向阀的进气口依次通过控制阀及空气过滤器与气源连接,第四电磁换向阀的进气口依次通过控制阀及空气过滤器与气源连接。
21.进一步地,夹紧气缸选择型号为cdg1ua32-50-m9b的气缸,定位气缸选择型号为cdq2b16-20d-m9b的气缸,翻转气缸选择型号为cdg1ua32-100-m9b的气缸,排残油拨叉气缸选择型号为cdq2b32-20dz-m9b的气缸。
22.进一步地,第一调速阀及第三调速阀均采用型号为as2201f-01-06s的调速阀,第二调速阀采用型号为as1201f-m5-04的调速阀,第四调速阀采用型号为as2201f-01-08s的调速阀。
23.进一步地,第一电磁换向阀、第三电磁换向阀及第四电磁换向阀均采用型号为sy7140-5d-02的电磁换向阀,第二电磁换向阀采用型号为sy3120-5l-m5的电磁换向阀。
24.由于采用上述技术方案,本发明具有以下有益效果:
25.1、上述混合动力液压模块试验平台气动系统,包括夹紧气动气路、定位气动气路、翻转气动气路及排残油拨叉气动气路,使用时,以空气作为介质,以夹紧气缸、定位气缸、翻转气缸及排残油拨叉气缸作为执行元件,辅以调速阀、电磁换向阀等元件对系统气源进行控制分配,气源通过电磁换向阀阀控制对应气缸的工作状态,通过调速阀控制气缸的工作速率,从而使气缸动作,完成夹紧、定位、翻转和排残油的功能;此外,通过设有外部供气气路,外部供气气路包括依次连接的减压阀、二通阀、精细过滤器及第五调速阀,减压阀的进气口与主供气管路连接,通过减压阀控制供气气路的出口压力,通过二通阀控制供气气路传气的通断,经精细过滤器过滤出干净的空气,再经过第五调速阀调节气体流速后,以为混合动力液压模块试验平台的气仓等用气设备提供更清洁、安全的气源,进而方便对混合动力进行研究。
26.2、上述混合动力液压模块试验平台气动系统,其气动气路所采用的气动元件的结构简单、安装维护不需耗费大动作。对压力的要求不高,故使用安全可靠,气动元件的成本较低。
27.3、上述混合动力液压模块试验平台气动系统,通过设置第一消声器、第二消声器能够控制噪声,消除气动系统运作时产生的噪音对试验的干扰。将第二消声器同时连接第三电磁换向阀及第四电磁换向阀,能够降低消声器的使用数量,进一步降低成本,且降低消声器安装所需的空间要求。
28.4、上述混合动力液压模块试验平台气动系统,还包括空气过滤器及控制阀,接通气源后,空气通过空气过滤器去除空气中的油、水、灰尘等杂质微粒,通过控制阀能够控制气源的供给量,通过电磁换向阀能够改变和控制压缩空气的流动方向,进而实现对各气缸作业的控制,而调速阀能够调节对应气缸中气体流动速度,即控制气缸的运动速度,从而使其能够对气动技术进行较为全面的研究。
29.5、上述混合动力液压模块试验平台气动系统,通过第一气路及第二气路将多个夹紧气缸连接在一起,能够实现多个夹紧气缸的同时夹紧作业,满足混合动力液压模块的试验要求,且能够通过多个第一调速阀能够分别调节多个夹紧气缸的运作速度,试验更方便;同理,通过第三气路及第四气路将多个翻转气缸连接在一起,能够实现多个翻转气缸的同
时翻转作业,满足混合动力液压模块的试验要求,且能够通过多个第三调速阀能够分别调节多个翻转气缸的运作速度,试验更方便。
30.6、上述混合动力液压模块试验平台气动系统,其第一调速阀、第二调速阀、第三调速阀及第四调速阀的分布为根据夹紧、定位、翻转和排残油功能而进行针对性的设置,满足试验要求且能够最大化的降低成本。
附图说明
31.图1为本实用新型一较佳实施方式中混合动力液压模块试验平台气动系统的气路图。
32.主要元件符号说明
33.10、第一电磁换向阀;11、第一调速阀;12、夹紧气缸;13、第一消声器;14、第一主气管;15、第一分支气管;16、第一连接气管;17、第二主气管;18、第二分支气管;19、第二连接气管;20、第二电磁换向阀;21、第二调速阀;22、定位气缸;30、第三电磁换向阀;31、第三调速阀;32、翻转气缸;33、第三主气管;34、第三分支气管;35、第三连接气管;36、第四主气管;37、第四分支气管;40、第四电磁换向阀;41、第四调速阀;43、排残油拨叉气缸;5、第二消声器;6、主供气管路;7、空气过滤器;8、控制阀;91、减压阀;92、二通阀;93、精细过滤器;95、第五调速阀。
具体实施方式
34.下面将结合本实用新型实施例中的附图,对本实用新型实施例中的技术方案进行清楚、完整地描述,显然,所描述的实施例仅仅是本实用新型一部分实施例,而不是全部的实施例。基于本实用新型中的实施例,本领域普通技术人员在没有做出创造性劳动前提下所获得的所有其他实施例,都属于本实用新型保护的范围。
35.需要说明的是,当组件被称为“固定于”另一个组件,它可以直接在另一个组件上或者也可以存在居中的组件。当一个组件被认为是“连接”另一个组件,它可以是直接连接到另一个组件或者可能同时存在居中组件。当一个组件被认为是“设置于”另一个组件,它可以是直接设置在另一个组件上或者可能同时存在居中组件。本文所使用的术语“垂直的”、“水平的”、“左”、“右”以及类似的表述只是为了说明的目的。
36.除非另有定义,本文所使用的所有的技术和科学术语与属于本实用新型的技术领域的技术人员通常理解的含义相同。本文中在本实用新型的说明书中所使用的术语只是为了描述具体的实施例的目的,不是旨在于限制本实用新型。本文所使用的术语“及/或”包括一个或多个相关的所列项目的任意的和所有的组合。
37.请参见图1,本实用新型一较佳实施方式提供一种混合动力液压模块试验平台气动系统,包括夹紧气动气路、定位气动气路、翻转气动气路、排残油拨叉气动气路及外部供气气路。
38.夹紧气动气路包括第一电磁换向阀10、第一调速阀11及夹紧气缸12,第一电磁换向阀10的进气口用于与气源连接,第一电磁换向阀10的第一工作口连接夹紧气缸12的第一气口,夹紧气缸12的第二气口通过第一调速阀11后与第一电磁换向阀10的第二工作口连接。
39.在本实施方式中,第一电磁换向阀10为二位五通电磁换向阀,二位五通电磁换向阀为用来控制流体的自动化基本元件,在气动回路中,控制气流管路的通断或改变气体的流动方向。二位五通电磁换向阀的一侧设置有两个接口,即第一工作口及第二工作口,第一工作口及第二工作口用于与气缸连接,为换向工作口;二位五通电磁换向阀的另一侧设置有三个接口,分别为一进气口及两个排气口,其中,进气口用于与气源连接,在本实施方式中,第一电磁换向阀10的进气口通过一主供气管路6与气源连接。使用时,通过给二位五通电磁换向阀中的磁铁线圈通电,吸引二位五通电磁换向阀中阀体移动,通过调节阀体的移动来控制各接口的遮住或掀开,使压缩空气会进入气缸的缸体中,从而推动气缸的活塞来回运动。二位五通电磁换向阀的结构属于现有技术,为省略篇幅,这里不再赘述。在本实施方式中,第一电磁换向阀10还与第一消声器13连接,具体地,第一电磁换向阀10的两个排气口均与一第一消声器13连接。
40.在本实施方式中,夹紧气缸12的数量为多个,第一电磁换向阀10的第一工作口通过第一气路与多个夹紧气缸12的第一气口连接,具体为:第一气路包括第一主气管14及与一端第一主气管14连接的多个第一分支气管15,第一主气管14通过第一连接气管16与第一电磁换向阀10的第一工作口连接,多个第一分支气管15的另一端分别与多个夹紧气缸12的第一气口连接;第一电磁换向阀10的第二工作口通过第二气路与多个夹紧气缸12的第二气口连接,第二气路包括第二主气管17及与一端第二主气管17连接的多个第二分支气管18,第二主气管17通过第二连接气管19与第一电磁换向阀10的第二工作口连接,多个第二分支气管18的另一端分别与多个夹紧气缸12的第二气口连接。第一调速阀11对应夹紧气缸12设有多个,多个第一调速阀11分别装设于对应的第二分支气管18上。
41.夹紧气缸12的结构属于现有技术,为省略篇幅,这里不再赘述。当压缩气体从第一气口进入夹紧气缸12的缸体时,夹紧气缸12处于夹紧工件状态,当压缩气体从第二气口进入夹紧气缸12的缸体时,夹紧气缸12恢复原状,工件脱离夹紧状态。第一调速阀11,即速度控制阀,是由单向阀和节流阀并联组合成的流量控制阀,所以又称单向节流阀,第一调速阀11的结构属于现有技术,为省略篇幅,这里不再赘述。
42.定位气动气路包括第二电磁换向阀20、第二调速阀21及定位气缸22,第二电磁换向阀20的进气口用于与气源连接,第二电磁换向阀20的第一工作口通过一第二调速阀21连接定位气缸22的第一气口,定位气缸22的第二气口通过另一第二调速阀21后与第二电磁换向阀20的第二工作口连接。
43.在本实施方式中,第二电磁换向阀20为二位五通电磁换向阀,二位五通电磁换向阀的一侧设置有两个接口,即第一工作口及第二工作口,第一工作口及第二工作口用于与气缸连接,为换向工作口;二位五通电磁换向阀的另一侧设置有三个接口,分别为一进气口及两个排气口,其中,进气口用于与气源连接,在本实施方式中,第二电磁换向阀20的进气口通过主供气管路6与气源连接。二位五通电磁换向阀的结构属于现有技术,为省略篇幅,这里不再赘述。
44.在本实施方式中,定位气缸22的数量为一个,第二调速阀21的数量设为两个,第二电磁换向阀20的第一工作口通过一第二调速阀21与定位气缸22的第一气口连接,第一电磁换向阀10的第二工作口通过另一第二调速阀21与定位气缸22的第二气口连接。定位气缸22的结构属于现有技术,为省略篇幅,这里不再赘述。当压缩气体从定位气缸22的第一气口进
入定位气缸22的缸体时,定位气缸22处于定位状态,当压缩气体从定位气缸22的第二气口进入定位气缸22的缸体时,定位气缸22恢复原状,脱离定位状态。第二调速阀21,即速度控制阀,是由单向阀和节流阀并联组合成的流量控制阀,所以又称单向节流阀,第二调速阀21的结构属于现有技术,为省略篇幅,这里不再赘述。本实施例根据定位气缸22的实验需求,通过设置两个第二调速阀21,能够对定位气缸22的定位及复位过程的速度均进行控制,以进一步提高定位的精度。
45.翻转气动气路包括第三电磁换向阀30、第三调速阀31及翻转气缸32,第三电磁换向阀30的进气口用于与气源连接,第三电磁换向阀30的第一工作口连接翻转气缸32的第一气口,翻转气缸32的第二气口通过第三调速阀31后与第三电磁换向阀30的第二工作口连接。
46.在本实施方式中,第三电磁换向阀30为二位五通电磁换向阀,其一侧设置有两个接口,即第一工作口及第二工作口,第一工作口及第二工作口用于与气缸连接,为换向工作口;二位五通电磁换向阀的另一侧设置有三个接口,分别为一进气口及两个排气口,其中,进气口用于与气源连接,在本实施方式中,第三电磁换向阀30的进气口通过主供气管路6与气源连接。
47.在本实施方式中,翻转气缸32的数量为多个,第三电磁换向阀30的第一工作口通过第三气路与多个翻转气缸32的第一气口连接,具体为:第三气路包括第三主气管33及与一端第三主气管33连接的多个第三分支气管34,第三主气管33通过第三连接气管35与第三电磁换向阀30的第一工作口连接,多个第三分支气管34的另一端分别与多个翻转气缸32的第一气口连接;第三电磁换向阀30的第二工作口通过第四气路与多个翻转气缸32的第二气口连接,具体为:第四气路包括第四主气管36及与一端第四主气管36连接的多个第四分支气管37,第四主气管36远离第四分支气管37的自由末端与第三电磁换向阀30的第二工作口连接,多个第四分支气管37的另一端分别与多个翻转气缸32的第二气口连接。第四调速阀41对应翻转气缸32设有多个,多个第四调速阀41分别装设于对应的第四分支气管37上。第四调速阀41,即速度控制阀,是由单向阀和节流阀并联组合成的流量控制阀,所以又称单向节流阀,第四调速阀41的结构属于现有技术,为省略篇幅,这里不再赘述。
48.翻转气缸32的结构属于现有技术,为省略篇幅,这里不再赘述。当压缩气体从翻转气缸32的第一气口进入翻转气缸32的缸体时,翻转气缸32能够沿第一方向进行转动180
°
以实现对工件的翻转作业,当压缩气体从第二气口进入翻转气缸32的缸体时,翻转气缸32能够沿与第一方向相反的第二方向转动以恢复原状。
49.排残油拨叉气动气路包括第四电磁换向阀40、第四调速阀41及排残油拨叉气缸43,第四电磁换向阀40的进气口用于与气源连接,第四电磁换向阀40的第一工作口通过一第四调速阀41连接排残油拨叉气缸43的第一气口,排残油拨叉气缸43的第二气口通过另一第四调速阀41后与第四电磁换向阀40的第二工作口连接。
50.在本实施方式中,第四电磁换向阀40为二位五通电磁换向阀,其一侧设置有两个接口,即第一工作口及第二工作口,第一工作口及第二工作口用于与气缸连接,为换向工作口;二位五通电磁换向阀的另一侧设置有三个接口,分别为一进气口及两个排气口,其中,进气口用于与气源连接,在本实施方式中,第四电磁换向阀40的进气口通过主供气管路6与气源连接。第四调速阀41的数量为两个,第四电磁换向阀40的第一工作口通过一第四调速
阀41与排残油拨叉气缸43的第一气口连接,第四电磁换向阀40的第二工作口通过另一第四调速阀41与排残油拨叉气缸43的第二气口连接。在本实施方式中,通过设置两个第四调速阀41,能够对混合动力液压模块试验平台气动系统中用于排残油的阀门的开关速度分别进行控制,减小对排残油阀门的损伤。
51.排残油拨叉气缸43的结构属于现有技术,为省略篇幅,这里不再赘述。当压缩气体从第一气口进入排残油拨叉气缸43的缸体时,排残油拨叉气缸43处于排残油状态,当压缩气体从第二气口进入排残油拨叉气缸43的缸体时,排残油拨叉气缸43恢复原状,停止排残油。
52.在本实施方式中,第三电磁换向阀30及第四电磁换向阀40还与第二消声器5连接,具体为:在本实施方式中,第二消声器5的数量为两个,第三电磁换向阀30的第一排气口及第四电磁换向阀40的第一排气口均与其中一第二消声器5连接,第三电磁换向阀30的第二排气口及第四电磁换向阀40的第二排气口均与另一第二消声器5连接。
53.在本实施方式中,第一电磁换向阀10的进气口、第二电磁换向阀20的进气口、第三电磁换向阀30的进气口及第四电磁换向阀40的进气口均通过主供气管路6与气源连接。气动系统还包括均装设于主供气管路6上的空气过滤器7及控制阀8,第一电磁换向阀10的进气口依次通过控制阀8及空气过滤器7与气源连接,第二电磁换向阀20的进气口依次通过控制阀8及空气过滤器7与气源连接,第三电磁换向阀30的进气口依次通过控制阀8及空气过滤器7与气源连接,第四电磁换向阀40的进气口依次通过控制阀8及空气过滤器7与气源连接。控制阀8用于控制主供气管路6传气的通断及通气量的大小,其可采用现有技术中的气阀,为省略篇幅,这里不再赘述。
54.外部供气气路包括依次连接的减压阀91、二通阀92、精细过滤器93及第五调速阀95。减压阀91的进气口与主供气管路6连接,第五调速阀95的出气口用于与混合动力液压模块试验平台的气仓等其他用气设备连接。在本实施方式中,精细过滤器93的数量为两个,两个精细过滤器93串联于外部供气气路中。使用时,通过减压阀91控制供气气路的出口压力,通过二通阀92控制供气气路传气的通断,经两级精细过滤器93过滤出干净的空气,再经过第五调速阀95调节气体流速后,以为混合动力液压模块试验平台的气仓等用气设备提供更清洁、更安全的气源。本实施例的减压阀91、二通阀92、精细过滤器93及第五调速阀95的结构均属于现有技术,为省略篇幅,这里不再赘述。
55.本实施方式还提供一种混合动力液压模块试验平台气动系统的搭建方法,包括以下步骤:
56.s1,构造所述混合动力液压模块试验平台气动系统,其包括夹紧气动气路、定位气动气路、翻转气动气路、排残油拨叉气动气路及外部供气气路,夹紧气动气路、定位气动气路、翻转气动气路、排残油拨叉气动气路及外部供气气路的结构如前述所示,为省略篇幅,这里不再赘述。
57.s2,对构成夹紧气动气路、定位气动气路、翻转气动气路及排残油拨叉气动气路的元件进行型号选择。
58.在本实施方式中,夹紧气缸12、定位气缸22、翻转气缸32及排残油拨叉气缸43的选型方法包括以下步骤:
59.s21,根据气缸的预设工作状态,确定气缸的负载率;具体地,可根据表1确定各气
缸的负载率:
60.表1负载率选择表
[0061][0062]
在本实施例中,根据夹紧气缸12、定位气缸22、翻转气缸32及排残油拨叉气缸43预设的工作状态,取负载率η=0.7。
[0063]
s22,确定各气缸的工作压力及气缸输出力;具体地,需根据气缸预设的使用条件确定气缸的工作压力及气缸输出力,在本实施方式中,夹紧气缸12、定位气缸22、翻转气缸32及排残油拨叉气缸43预设的使用条件如表2所示,并预设夹紧气缸12、定位气缸22、翻转气缸32及排残油拨叉气缸43的工作压力均为p=0.5mpa。
[0064]
表2:气缸的使用条件
[0065]
名称夹紧气缸定位气缸翻转气缸排残油拨叉气缸输出力/n25060250250行程/mm502010020
[0066]
s23,根据气缸输出力、负载率及工作压力计算得到气缸内径,具体地,根据以下公式计算获得气缸内径d:
[0067]
式中:f-气缸输出力;p-工作压力;η-负载率。
[0068]
具体地,夹紧气缸12的气缸内径d计算如下:
[0069][0070]
故按照gb/t2348-1993标准,夹紧气缸12的气缸内径d选择32mm。
[0071]
定位气缸22的气缸内径d计算如下:
[0072][0073]
故按照gb/t2348-1993标准,定位气缸22的气缸内径d选择16mm。
[0074]
翻转气缸32的气缸内径d计算如下:
[0075][0076]
故按照gb/t2348-1993标准,翻转气缸32的气缸内径d选择32mm。
[0077]
排残油拨叉气缸43的气缸内径计算如下:
[0078]
[0079]
故按照gb/t2348-1993标准,排残油拨叉气缸43的气缸内径d选择32mm。
[0080]
s24,根据各气缸所需完成的任务要求,选择满足各气缸内径要求的对应型号的气缸。
[0081]
具体地,夹紧气缸12和翻转气缸32要求达到行程终端时无冲击和噪声,因此,本气动系统的夹紧气缸12和翻转气缸32均选择气缓冲式气缸,此外,由于夹紧气缸12、翻转气缸32的活塞杆除了作直线运动以外,还随缸体做摆动,因此,本气动系统的夹紧气缸12、翻转气缸32均选择安装方式为杆侧耳轴式的气缸。由于定位气缸22和排残油拨叉气缸43的行程短,安装空间窄,因此,本气动系统的定位气缸22和排残油拨叉气缸43均选择薄型cq式气缸。综合上述气缸所需完成的任务要求及气缸的内径要求,具体地,在本实施方式中,夹紧气缸12选择型号为cdg1ua32-50-m9b的夹紧气缸,定位气缸22选择型号为cdq2b16-20d-m9b的定位气缸,翻转气缸32选择型号为cdg1ua32-100-m9b的翻转气缸,排残油拨叉气缸43选择型号为cdq2b32-20dz-m9b的排残油拨叉气缸,其能够满足步骤s23中计算得到的各气缸的气缸内径要求,具体请参见表3。
[0082]
表3
[0083]
序号名称型号厂家1夹紧气缸cdg1ua32-50-m9bsmc2定位气缸cdq2b16-20d-m9bsmc3翻转气缸cdg1ua32-100-m9bsmc4排残油拨叉气缸cdq2b32-20dz-m9bsmc
[0084]
第一调速阀11、第二调速阀21、第三调速阀31及第四调速阀41分别用于调节对应气缸中气体流动的速度,即控制对应气缸的工作速度,在本实施方式中,第一调速阀11、第二调速阀21、第三调速阀31及第四调速阀41的选型方法包括以下步骤:
[0085]
s31,根据气缸的气缸内径、气缸最大运动速度、工作压力计算获得气缸的瞬时流量:在本实施方式中,根据以下公式计算获得气缸的瞬时流量q:
[0086]
其中,d-气缸内径,单位:mm;vmax-气缸最大运动速度,单位:mm/s,其可根据选择的气缸的参数获得;p—气缸的工作压力,单位:105pa。
[0087]
具体地,夹紧气缸12的瞬时流量q计算如下:
[0088][0089]
定位气缸22的瞬时流量q计算如下:
[0090][0091]
翻转气缸32的瞬时流量q计算如下:
[0092][0093]
排残油拨叉气缸43的瞬时流量q计算如下:
[0094][0095]
s32,根据气缸的瞬时流量确定对应调速阀的流量,并根据调速阀的流量选择对应调速阀的型号。在本实施方式中,所采用的调速阀的最大流量不能小于对应气缸的瞬时流量q,具体地,第一调速阀11及第三调速阀31均采用型号为as2201f-01-06s的调速阀,第二调速阀21采用型号为as1201f-m5-04的调速阀,第四调速阀41采用型号为as2201f-01-08s的调速阀,具体参数请见表4。
[0096]
表4
[0097][0098]
其所选用的调速阀均具有以下优点:
[0099]
(1)结构小、重量轻;
[0100]
(2)具有良好的流量特性,高度小、能紧凑设计、有效面积符合要求;
[0101]
(3)工作压力可高至1mpa;
[0102]
(4)适合管子材质:尼龙、软尼龙、聚氨酯;
[0103]
(5)低流量范围内,速度控制变得容易,可等速控制。
[0104]
二位五通电磁换向阀由电磁控制部分和换向阀组成。电磁铁是二位五通电磁换向阀的主要组成部件,它由线圈、静铁芯和动铁芯构成。按照电磁原理将电磁能转换成机械能,使铁芯推动阀芯运动,从而改变气体流动的方向。由于夹紧气缸12、定位气缸22、翻转气缸32、排残油拨叉气缸43都为双作用活塞气缸,而二位五通电磁换向阀可以控制双作用活塞气缸来回往复运动,且不能使气缸在行程范围内任意位置停止运动,因此我们选择二位五通电磁换向阀来控制气体流动的方向。
[0105]
在本实施方式中,第一电磁换向阀10、第二电磁换向阀20、第三电磁换向阀30及第四电磁换向阀40的选型方法包括以下步骤:
[0106]
s41,根据对应气缸的气缸内径、气缸最大运动速度、工作压力计算获得气缸的最大耗气量,并根据气缸的最大耗气量选择对应电磁换向阀的型号。具体地,在本实施方式中,根据以下公式计算获得气缸的最大耗气量g:
[0107]
g=0.046d
2vmax
(p 0.102),其中,d-气缸内径,单位:mm;vmax-气缸的最大运动速度,单位:mm/s;p—气缸的工作压力,单位:mpa。
[0108]
其中,夹紧气缸12的最大耗气量g计算如下:
[0109]
g=0.046d
2vmax
(p 0.102)=0.046
×
3.22×
700
×
0.602=198.50l/min
[0110]
定位气缸22的最大耗气量g计算如下:
[0111]
g=0.046d
2vmax
(p 0.102)=0.046
×
1.62×
700
×
0.602=49.63l/min
[0112]
翻转气缸31的最大耗气量g计算如下:
[0113]
g=0.046d
2vmax
(p 0.102)=0.046
×
3.22×
700
×
0.602=198.50l/min
[0114]
排残油拨叉气缸43的最大耗气量g计算如下:
[0115]
g=0.046d
2vmax
(p 0.102)=0.046
×
3.22×
700
×
0.602=198.50l/min
[0116]
根据上述求得的夹紧气缸12的最大耗气量g,选择第一电磁换向阀10的型号为sy7140-5d-02;根据上述求得的定位气缸22的最大耗气量g,选择第二电磁换向阀20的型号为sy3120-5l-m5;根据上述求得的翻转气缸32的最大耗气量g,选择第三电磁换向阀30的型号为sy7140-5d-02;根据上述求得的排残油拨叉气缸43的最大耗气量g,选择第四电磁换向阀40的型号为sy7140-5d-02,具体参数请见表5。
[0117]
表5
[0118]
用途型号额定压力有无托架第一、第三及第四电磁换向阀sy7140-5d-0224v无第二电磁换向阀sy3120-5l-m524v无
[0119]
在本实施方式中,空气过滤器7的结构属于现有技术。考虑到本实施方式中采用的夹紧气缸12、定位气缸22、翻转气缸32及排残油拔叉气缸43均为普通标准气缸,过滤精度要求一般,同时为了缩小外形尺寸,节省空间,便于集中管理与维修,为此选择型号为aw30-03be的smc的空气过滤器7,过滤精度在5um左右。
[0120]
当压缩空气进入气动系统后,到达电磁换向阀时,须经过多个管径不同的直管和弯头,导致管道内空气剧烈扰动而辐射出噪声。本实施方式采用消声器消除气动系统运作时产生的噪音对试验的干扰。在本实施方式中,消声器型号选择的基本要求为:
[0121]
①
能具有较好的消音性能,即要求具有较好的消音频率性能,噪声一般范围控制在74~80db之间;
[0122]
②
具有较好的空气动力性能,消声器应用时对气流的阻损要小;
[0123]
③
消声器结构应较简单,有利于便捷地加工,经济且耐用,无再生噪声产生。
[0124]
根据上述要求,选择型号为an200-02的smc金属主体型消声器,由于其通气阻力小、体形小、且安装简单,可以消除30db的噪声,故选择该型号。其结构尺寸如表6所示:
[0125]
表6消声器结构尺寸
[0126]
通口尺寸有效面积/mm2质量/g1/43517
[0127]
空气经过空气过滤器7得到清洁的压缩空气,分别经过控制夹紧气缸12的五通电磁换向阀、控制翻转气缸32的五通电磁换向阀、控制位移的五通电磁换向阀、控制排油拨叉的五通电磁换向阀来控制对应气缸的往复运动。具体地:
[0128]
夹紧气路作业时,接通气源后,空气通过空气过滤器7去除空气中的油、水、灰尘等杂质微粒,控制阀8控制气源供给量,后通过第一电磁换向阀10改变和控制压缩空气的流动方向,即控制夹紧气缸12中活塞的往复运动,在此过程中,通过第一调速阀11调节夹紧气缸12中气体流动的速度,即控制夹紧气缸12的运动速度,以推动夹紧气缸12中的活塞运作,从而使夹紧气缸12执行夹紧或释放的动作。
[0129]
定位气路作业时,接通气源后,空气通过空气过滤器7去除空气中的油、水、灰尘等
杂质微粒,控制阀8控制气源供给量,后经过第二电磁换向阀20改变和控制压缩空气的流动方向,即控制定位气缸22中活塞的往复运动,在此过程中,通过第二调速阀21调节定位气缸22中气体流动的速度,即控制定位气缸22的运动速度,以推动定位气缸22中的活塞运作,再配合定位气缸22本身自带的位移传感器达到定位的功能。
[0130]
翻转气路作业时,接通气源后,空气通过空气过滤器7去除空气中的油、水、灰尘等杂质微粒,控制阀8控制气源供给量,后通过第三电磁换向阀30改变和控制压缩空气的流动方向,即控制翻转气缸32中活塞的往复运动,在此过程中,通过第三调速阀31调节翻转气缸32中气体流动的速度,即控制翻转气缸32的运动速度,以推动翻转气缸32中的活塞运作,实现翻转的功能。
[0131]
排残油气路作业时,接通气源后,空气通过空气过滤器7去除空气中的油、水、灰尘等杂质微粒,控制阀8控制气源供给量,后通过第四电磁换向阀40改变和控制压缩空气的流动方向,即控制排残油拔叉气缸43的往复运动,进入拨叉部分,在此过程中,通过第四调速阀41调节排残油拔叉气缸43中气体流动的速度,即控制排残油拔叉气缸43的运动速度,完成排残油动作。
[0132]
上述混合动力液压模块试验平台气动系统,包括夹紧气动气路、定位气动气路、翻转气动气路及排残油拨叉气动气路,使用时,以空气作为介质,以气缸作为执行元件,辅以调速阀、电磁换向阀等元件对系统气源进行控制分配,气源通过电磁换向阀阀控制气缸的工作状态,通过调速阀控制气缸的工作速率,从而使气缸动作,完成夹紧、定位、翻转和排残油的功能;此外,通过设有外部供气气路,外部供气气路包括依次连接的减压阀91、二通阀92、精细过滤器93及第五调速阀95,减压阀91的进气口与主供气管路6连接,通过减压阀91控制供气气路的出口压力,通过二通阀92控制供气气路传气的通断,经精细过滤器93过滤出干净的空气,再经过第五调速阀95调节气体流速后,以为混合动力液压模块试验平台的气仓等用气设备提供更清洁、安全的气源,进而方便对混合动力进行研究。
[0133]
上述混合动力液压模块试验平台气动系统,通过设置第一消声器13、第二消声器5能够控制噪声,消除气动系统运作时、产生的噪音对试验的干扰,满足夹紧气缸12和翻转气缸32及排残油拔叉气缸43要求达到行程终端时无噪声的要求,而对于无噪声大小要求的定位气缸21,其未连接消声器,能够在满足试验的前提下进一步节约成本。本实施例还将第二消声器5同时连接第三电磁换向阀30及第四电磁换向阀40,能够降低消声器的使用数量,进一步降低成本,且能够降低消声器的占用空间,允许其在狭小空间内安装。
[0134]
上述混合动力液压模块试验平台气动系统,还包括空气过滤器7及控制阀8,接通气源后,空气通过空气过滤器7去除空气中的油、水、灰尘等杂质微粒,通过控制阀8能够控制气源的供给量,通过电磁换向阀能够改变和控制压缩空气的流动方向,进而实现对各气缸作业的控制,而调速阀能够调节对应气缸中气体流动速度,即控制气缸的运动速度,从而使其能够对气动技术进行较为全面的研究。
[0135]
上述混合动力液压模块试验平台气动系统,通过第一气路及第二气路将多个夹紧气缸12连接在一起,能够实现多个夹紧气缸12的同时夹紧作业,满足混合动力液压模块的试验要求,且能够通过多个第一调速阀18能够分别调节多个夹紧气缸12的运作速度,试验更方便;同理,通过第三气路及第四气路将多个翻转气缸32连接在一起,能够实现多个翻转气缸32的同时翻转作业,满足混合动力液压模块的试验要求,且能够通过多个第三调速阀
31能够分别调节多个翻转气缸32的运作速度,试验更方便。
[0136]
上述混合动力液压模块试验平台气动系统,以压缩空气为工作介质,空气来源广,用后排到大气中处理方便简单,清洁,对环境不构成威胁,由于空气流动的损失小,且空气具有可压缩性,对于集中供气提供了条件,便于远距离的输送;与液压传动等相比,起动时动作快速、反应灵敏、维修更是便捷,由于其工作介质是空气,因此管路不易堵塞,且不需要考虑介质变质、补充和更换的难题,对工作环境的要求不高,能够适应易燃、易爆等场所,且保证安全可靠。
[0137]
上述混合动力液压模块试验平台气动系统,其构造的气动气路所采用的气动元件的结构简单、安装维护不需耗费大动作。对压力的要求不高,故使用安全可靠,气动元件的成本较低。
[0138]
上述混合动力液压模块试验平台气动系统的搭建方法,其还提供了一种对构成夹紧气动气路、定位气动气路、翻转气动气路及排残油拨叉气动气路的元件型号进行选择的方法,通过该方法可根据气缸所需完成的任务要求来选择气缸、电磁换向阀、调速阀等元件,使其满足试验需求且具有安全性、适用性和经济性的优点。
[0139]
上述说明是针对本实用新型较佳可行实施例的详细说明,但实施例并非用以限定本实用新型的专利申请范围,凡本实用新型所提示的技术精神下所完成的同等变化或修饰变更,均应属于本实用新型所涵盖专利范围。
再多了解一些
本文用于企业家、创业者技术爱好者查询,结果仅供参考。