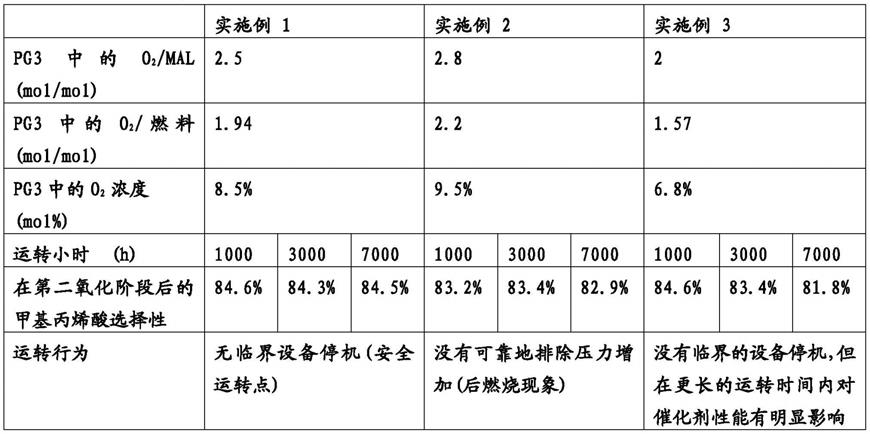
采用甲基丙烯醛返回和再循环制备mma的c-4-基方法
技术领域
1.本发明描述了基于c-4原料制备甲基丙烯酸酯,尤其是制备甲基丙烯酸和甲基丙烯酸甲酯(mma)的改进方法。在这种情况下c4原料尤其是异丁烯或叔丁醇。另外,还提供了用于有效制备这些产物的范围广泛的实施方案。
2.本发明尤其涉及通过气相氧化异丁烯制备甲基丙烯酸和甲基丙烯酸甲酯的方法。在第二气相氧化步骤中,将甲基丙烯醛转化成甲基丙烯酸并从甲基丙烯酸中除去未转化的甲基丙烯醛。在蒸发设备中在各种气体和蒸汽存在下使这种甲基丙烯醛蒸发并以气态形式与其中制备了甲基丙烯醛的第一氧化阶段的工艺气体混合在一起。这样,可以将再循环的甲基丙烯醛再供给到方法和催化部分氧化。
背景技术:
3.甲基丙烯酸甲酯(mma)大量用于制备聚合物,并与其它可共聚化合物一起用于共聚物。此外,甲基丙烯酸甲酯是多种基于甲基丙烯酸(maa) 的特种酯的重要合成单元,这些酯是通过与合适的醇进行酯交换制备的。
4.因此,以非常简单、经济且环境友好的方法制备这种重要的化学产品存在重大利益。
5.mma的制备基于三种可能的原材料组。其中一种是c3单元,另一种是c4单元和c2单元。
6.c3单元是第一具有商业意义的组。在这里,mma主要是从氰化氢和丙酮出发经由作为中心中间体形成的丙酮氰醇(ach)制备的。所述方法的缺点是获得非常大量的硫酸铵,其后处理与非常高的成本相关联。使用除ach之外的原材料基础的其它方法在相关专利文献中进行了描述并同时已在生产规模上实现。
7.如今,使用异丁烯或叔丁醇作为c-4-基原料作为制备甲基丙烯酸酯的反应物越来越重要。这些经过多个工艺阶段转化为所需的甲基丙烯酸衍生物。作为第三备选方案,也可以使用甲基叔丁基醚(mtbe),它通过消除甲醇转化为异丁烯。
8.在这种c4-基方法中,异丁烯或叔丁醇通常在第一阶段中被氧化成甲基丙烯醛,然后使这种甲基丙烯醛与氧气反应以生成甲基丙烯酸。然后用甲醇将所获得的甲基丙烯酸转化成mma。关于这种方法的更多细节尤其在以下文献中给出:ullmann's encyclopedia of industrialchemistry 2012,wiley-vch verlag gmbh&co. kgaa,weinheim,methacrylic acid and derivatives,doi: 10.1002/14356007.a16_441.pub2和trends and future ofmonomer-mma technologies,sumitomo kagaku 2004-ii。关于一般性 mma和甲基丙烯酸制备方法,特别是关于从c4单元开始的多阶段气相方法的更多细节描述在krill和r
ü
hling等的"many paths lead tomethacrylic acid methyl ester",wiley-vch verlag gmbh&co. kgaa,weinheim,doi.org/10.1002/ciuz.201900869中。
9.一般而言,c4路线从蒸汽裂化产物iben或者还有tba开始,其在第一步中通过气相氧化被氧化为mal。在另外的第二气相氧化阶段中,将作为中间体获得的甲基丙烯醛(mal)
氧化成maa。将气态反应产物在下游骤冷步骤中冷却并在很大程度上冷凝。所述方法的特点是,第二反应阶段不涉及mal的完全转化并且未转化的mal在吸收和解吸收单元 (再循环mal)中回收,以便随后将其送回作为第二反应阶段的进料。
10.异丁烯或叔丁醇可以在非均相催化剂上与气相中的大气氧反应以生成甲基丙烯醛(mal),然后使用甲醇利用mal的氧化酯化反应转化为 mma。这种方法尤其描述在us 5,969,178和us 7,012,039中。这种方法也在sumitomo的文章中进行了描述(参见上文),其中明确提到了这种方法的缺点,特别是尤其由非加压操作模式引起的高能量需求。在这种方法中,由于所述方法发生在液相中,因此避免了mal蒸发的问题,因此mal不需要转变成气态,从而避免了与临界含氧气体混合的问题。不能由此推导出用maa作为中间阶段优化两阶段异丁烯气相方法的解决方案。
11.相对不令人满意的产率(尤其是由氧化步骤中的高损失以及因此伴随的co2形成引起)也是所有这些方法中的问题。必须另外指出副产物的形成,所述副产物进一步伴随于此,并且需要用于离析产物的复杂方法步骤。例如,从异丁烯或等效的c-4-基原料例如tba或mtbe开始的所有方法在非均相催化剂体系上在气相氧化中针对每个工艺阶段达到 80%-90%的选择性。因此,达到至多65%-70%的总产率。自然地,气相方法在1-2巴绝对压力的中等压力下进行,并产生其中产物组分仅以大约4体积%-6体积%存在的工艺气体。从惰性气体镇流器(ballast)中离析有价值的产物相应地是能源密集型的,并且在多阶段蒸馏后处理步骤中消耗大量的冷却能量和蒸汽。
12.因此,总的来说,以下三种c4-基mma制备路线是众所周知的:
13.方法a,“串联c4直接氧化法”,没有甲基丙烯醛中间离析:此处,在第一步骤中,甲基丙烯醛由异丁烯制备并在方法步骤2中氧化成甲基丙烯酸,然后在方法步骤3中,通过用甲醇酯化甲基丙烯酸获得mma。这种方法在文献中也称为“串联方法”,因为来自第一阶段的工艺气体被直接氧化为甲基丙烯酸,而无需离析甲基丙烯醛中间体。
14.方法b,“单独的c4直接氧化”:此处,与方法a类似,在第一个方法步骤中由异丁烯制备甲基丙烯醛,并在单独的方法步骤中以液体形式离析和纯化,然后在方法步骤3中蒸发并氧化成甲基丙烯酸,最后通过在方法步骤4中酯化转化成mma。
15.方法c,“直接甲基法”,或直接氧化酯化方法:此处,在第一方法步骤中,在催化剂i上在气相中由异丁烯制备甲基丙烯醛,并同样首先在方法步骤2中分离和中间提纯,和然后在方法步骤3中直接氧化酯化成mma。方法步骤3在悬浮催化剂ii上在液相中进行。因此,气相步骤和液相中的方法步骤的组合是这种方法与方法a和b相比的本质区别,其中两个部分氧化都在不同的催化剂上进行,每种催化剂均在气相中。
16.根据现有技术的所有描述的方法都有很好的文献记录,例如记录在 (i)ihs chemical process economics program,review 2015-05,r.j. chang,syed naqvi或(ii)vapor phase catalytic oxidation ofisobutene to methacrylic acid,stud.sci.catal.1981,7,755-767 中。
17.方法a和b的共同点是甲基丙烯酸是主要产物,其可以非必要地在与甲醇的酯化反应中转化成甲基丙烯酸甲酯。一般而言,活性布朗斯台德酸性催化剂用于这种最后的酯化步骤。在均相变型中可以使用溶解的强酸。优选的酸是硫酸、甲烷磺酸或具有类似pka的酸。在另一个变型中,可以使用具有固定的酸官能团的离子交换剂。
18.方法c,即“直接甲基方法”,按照与方法b类似的方式,如前两个步骤中已经描述的那样用液体甲基丙烯醛的中间离析进行。在这种情况下,在液相氧化中直接从甲基丙烯醛获得mma,并且不需要甲基丙烯酸生产的中间步骤。
19.因此,方法a和b的特征在于,当经过第二氧化阶段时,气体混合物中所含的mal仅发生部分转化。除了一氧化碳和二氧化碳之外,还会形成很多其它反应产物,即尤其是甲醛、乙酸、丙酮、乙醛和丙烯醛。在随后的加工步骤中,必须将未转化的mal从所需的甲基丙烯酸产物中离析出来。通常,这种分离任务通过至少一个蒸馏或萃取步骤进行。 mal本身从工艺气体中吸收并进一步加工、提纯到一定程度,并通过解吸过程和非必要地,至少一个蒸馏操作进行离析。吸收和解吸之后非必要地进行进一步蒸馏。由于除丙烯醛之外还存在挥发性但可冷凝的组分,所以根据分离的复杂性,获得具有一些有机副产物成分的粗甲基丙烯醛,通常是mal浓度》70重量%的mal混合物。这意味着通过去除甲基丙烯酸得到的呈液体形式的粗甲基丙烯醛混合物不仅可以含有一些痕量组分例如甲基丙烯酸、乙酸、对苯二甲酸和稳定剂,而且还含有一定量的与mal相比具有相似或更低沸点的组分。存在多种将液态再循环的甲基丙烯醛重新引入主气体系统(尤其是在第二反应阶段的上游)的方法。粗甲基丙烯醛的蒸发和与其它气体和蒸汽混合的步骤,尤其是添加含氧气体,特别是混合和再循环到所述方法中,是一个复杂且关键的操作,其在现有技术中不能令人满意地实现。这些次要组分中的一些具有临界闪点并影响所得具有含氧气体的混合物的爆炸特性。将再循环的甲基丙烯醛重新引入主工艺的方法,例如在第二反应阶段的上游重新引入,是整个工艺中尤其安全-关键的步骤。在现有技术中已经提出了许多建议以通过各种方法解决这个问题,以便将未完全转化的甲基丙烯醛返回到所述方法中。然而,所述现有技术并不令人满意,特别是在以下安全相关的方面:第二氧化阶段之后经移除、未转化的甲基丙烯醛的再循环、其调节和蒸发以及与惰性气体和含氧气体混合以及另外的用蒸汽必要的调节以便为第二部分气相氧化步骤创造最佳条件。
20.在所有这些工艺中,存在以下涉及安全相关方面的困难,尤其是在粗甲基丙烯醛级分的移除和离析以及其蒸发和用气体调节期间,必须对这些方面进行优化:
21.1)甲基丙烯醛通常在除去甲基丙烯酸后以液体形式离析。然后必须通过蒸发使其变成气体形式并引入到气体反应系统中。液体再循环甲基丙烯醛在存在的温度下敏感地反应,其中在特定温度以上和特定停留时间内可能发生聚合、二聚及其它伴随的不希望的作用。因此,有必要找到一种路线,在所述路线中,对于蒸发所需的给定能量输入,将液体再循环甲基丙烯醛保持在这样的浓度下,即在所述浓度下停留时间可以保持得如此短,以致可以使聚合最小化或完全停止。
22.2)再循环的甲基丙烯醛可能不仅含有一些痕量成分例如甲基丙烯酸、乙酸、对苯二甲酸和稳定剂,而且含有一定量的沸点相近或更低的组分。此外,对苯二甲酸和常用的稳定剂是第二阶段催化剂的催化剂毒物,因为它们会导致催化剂在长期运转中的结焦和覆盖增加。这反过来又会对催化剂的性能和使用寿命产生负面影响。因此,在将反应上游的再循环甲基丙烯醛重新引入到第二阶段的气体反应系统中之前,有必要尽可能除去对苯二甲酸和稳定剂,例如氢醌(hq)。由于沸点高于甲基丙烯醛的组分而产生的进一步重大问题是在蒸发和返回区域,特别是在长期操作中使用的许多设备部件和管道上可观察到的沉积和覆盖。由此产生的问题会导致操作中断以及用于除去这些残留物的昂贵且不方便的停机时
间。在此,对改进的相当大的需求也是本发明的一个目的。
23.3)根据催化剂状态,两个温控反应区具有不同的温度水平。离开第一反应区的气体料流在进入第二反应区之前必须冷却。之所以如此是因为,在根据现有技术的常规方法中,第一阶段的盐浴温度(其可被视为反应温度的直接指标)比相应的第二阶段的盐浴温度高30℃至100℃。一般而言,第一阶段的更热的工艺气体通过与含再循环甲基丙烯醛的更冷含氧气体料流混合来冷却。这种程序能够增加第二阶段的进料气的氧气含量,同时能够将再循环的甲基丙烯醛送回到工艺中。在安全操作方面,这种方法对所有物理参数和化学计量以及停留时间和混合物的质量都非常敏感地反应。否则,较高的氧气浓度和在较高温度的区域内的一定停留时间会增加“后燃烧效应”的风险。后燃烧是对一些对温度敏感性物质如呈气体混合物形式的甲基丙烯醛已知的现象。相应的物质有分解成更小碎片的趋势。这些反过来又会导致自发的压力和/或温度升高,这在安全方面是成问题的。
24.4)最后但并非最不重要的是,甲基丙烯醛不能在第二反应区中完全转化。在70%-85%的转化率下,可以达到合理且良好的选择性。然而,在更高的转化率下,选择性开始显著下降。为了达到甲基丙烯酸的高收率,必须将甲基丙烯醛再循环。再循环构成自(i)在恒温控制的冷凝工艺液体中冷却和骤冷工艺气体和(ii)在下游设备单元中吸收、解吸和非必要地蒸馏甲基丙烯醛。下面的甲基丙烯醛再引入涉及一定质量的再循环甲基丙烯醛的蒸发,并需要将蒸发的粗甲基丙烯醛与含氧气体如再循环气体、空气和非必要的蒸汽混合。在某些情况下,由于局部区域具有高温或高于爆炸下限的过高燃料浓度,在这种再循环步骤期间可能会形成爆炸性气体混合物。特别是在长期、连续操作的情况下,其中一些设备部件和管道显示副产物和聚合物材料的沉淀、污染和沉积,可以观察到不恰当的分布,这与过高的氧气浓度结合导致临界安全条件。最后,这也会导致经由安全孔释放超压,或者在最坏的情况下甚至导致局部爆炸,或者取决于破坏的严重程度,导致爆燃。
25.因此,一种在工业规模上提高工艺安全性同时优化产率的新方法必须考虑到这四个所讨论的方面中的每一个。
26.因此,例如,在usa7,799,946和gb 2 004 886中,首先使再循环的甲基丙烯醛经过骤冷塔(用工艺介质骤冷),其中包括甲基丙烯酸的重质成分被冷凝。含甲基丙烯醛的气体在随后的塔中被吸收,最后从吸收的液体中解吸和汽提,以获得可被引入第二反应器的含甲基丙烯醛的气体混合物。在此,这种气体混合物是具有足够低氧浓度的非爆炸性气体。然而,即使采用这种方法,氧气也不足以充分和最佳地供应第二阶段的反应。在此,必须在第二阶段中的反应之前再次供应额外的含氧气体。
27.ep 3 007 69描述了在含甲基丙烯醛的再循环气体料流的引入点处的特殊分布器构造以及这种气体料流与第一阶段的反应气体的混合。这样做是为了防止导致甲基丙烯醛分解的上述后燃烧效应。ep 3 007 69 进一步描述了将第一阶段的较热的工艺气体与较冷的含甲基丙烯醛的再循环气体料流混合的方法。这经由分布器或喷嘴的特别布局通过气体料流的喷雾注射进行,所述气体料流非必要地与空气、惰性气体和再循环的甲基丙烯醛混合。作为这种注射的结果,将较热气体(其例如具有 350℃-400℃的温度)冷却到200℃-240℃的所得温度。在这种方法中,含甲基丙烯醛的气体混合物将在较高甲基丙烯醛浓度下含有高达13 mol%的富氧浓度。因此形成爆炸性气体。即使通过喷雾注射将气体混合物充分冷却到低于着火温度,也不能排除温度高于着火点的局部热点。由于焦油状沉积物和成问
题的聚合残留物,在分布器中形成并观察到热点。这种残留物局部沉积的关键区域会导致管道的某些部分和分布器区域的污染和堵塞。虽然就设备而言,这种构思的所述执行方式在原理上是合适的,但它容易弄脏,特别是在连续永久操作中,这使得需要定期停机以除去这些污染物,这些污染物有时是焦油状的,有时是粉状的。污染物可以通过燃烧以热解方式、手动移除或用合适的介质冲洗来除去。通常只有在拆卸分布器机构后才能实现设备的完全清洁,这需要设备停工多天。管道中的污染,特别是在分布器区域上游和内部的出口喷嘴处的污染导致含有甲基丙烯醛的出口气体的不恰当分布并产生可燃的局部气体混合物;在这方面,操作不能被认为是安全的,尤其是在操作两周或更多周之后。
28.在us 3,876,693和us 3,147,084中,在每种情况下,第一反应气体由配备有附加热交换器的反应器冷却。这样做是为了进一步降低第一反应器的反应气体的温度。不涉及将再循环的甲基丙烯醛和氧气安全重新引入的主题。然而,在这里,副产物,尤其是tpa,可能会在换热器管道中凝华并至少在一定程度上阻塞这些管道。热交换效率和反应运行时间因此减少。此外,反应器体系结构将非常复杂,并且这种基于设备的解决方案的生产和维护成本相应很高。
29.在另一提案ep 2 158 954中,描述了将未转化的甲基丙烯醛再循环的具体方法。描述了使甲基丙烯醛蒸发的具体设备,其中将含液态甲基丙烯醛的料流输送到填充塔,并将所得的含mal气体料流直接供给氧化反应器。更高沸点组分在底部排出,从而基本上避免这种设备中的污染物。气体共混(以便调节第二部分氧化反应器上游的氧气含量),特别是与含氧气体共混的问题,特别是返回到反应器的较高压力区域的问题,没有得到令人满意地解决。设备的底部温度会在连续操作中导致进一步的问题,因为对苯二甲酸和聚合物沉积物会在介质中形成。由于底料的循环模式,将相当一部分重沸点组分送回到后处理工艺,这与更高的能量消耗相联系。所得含mal气体料流的组成基本上由装置和设备的压力和底部温度决定。
30.总之,可以说,从安全有效的工艺状况的观点来看,这些现有技术方法构成了相当大的技术挑战。当使所谓的再循环甲基丙烯醛,即在第二氧化阶段中未转化的甲基丙烯醛蒸发,并将其注入在这两个氧化反应器之间时,所述方法在所谓的“贫含”范围内运转。这种贫含范围非常接近于混合物的爆炸极限。混合物的所述贫范围由气体混合物(其尤其还包括甲基丙烯醛)中较低浓度的挥发性化合物限定。原则上,对于本发明的物质组合物,基于有机化合物的总和,在低于2.5体积%,优选低于2.2体积%的情况下进行工作。原则上,气体混合物变得不那么重要,有机成分的比例越低,气体中的氧气含量越低并且气体混合物的停留时间和热负荷越低。此处不那么重要是指可以避免在后燃烧的情况下所描述的分解问题的程序。
31.如果将这种临界混合物与工艺气体一起供给第一反应器阶段,例如在通常高于300℃的温度下,则在第二氧化反应器上游的进料气体中经常会出现焦油状沉积物和有问题的成分。这个问题在很多现有技术文件中都有描述,并带有相应的建议解决方案。然而,所有这些解决方案都有一个共同特征,即它们只能经由复杂且昂贵的措施来实施。此外,许多问题不能得到充分补偿,尤其是在连续操作中。
32.因此,在这一点上可以说,迄今为止,还没有描述过基于c4原料的以下方法:其中去除和转化工艺气体中未转化的甲基丙烯醛的关键步骤已被描述为对于长期操作足够安
全。因此,这里非常需要改进。
技术实现要素:
33.目的
34.本发明的一个目的是优化用于制备甲基丙烯酸或mma的c4-基方法,尤其是那些使用甲基丙烯酸作为中间体或最终产物的方法。意图是从所述方法获得高产率,同时达到所用催化剂的长使用寿命,特别是在第二氧化阶段中。此外,应该可以在氧气和挥发物的非临界浓度下和/或在非临界温度下进行所优化的方法。
35.另一个目的是优化方法,使其可以在单独改装或清洁停机时间之间以更长的加工时间运转。这尤其涉及在两个氧化阶段之间的所谓分布器部分中的装置部件的更换。这涉及设备的以下区域:其中含有各种副产物和残留反应物以及氧气、蒸汽和氮气的mal以气体形式提供用于第二氧化阶段的反应。
36.总之,因此本发明的一个目的尤其是提供制备甲基丙烯酸作为最终产物或中间体的改进的c4-基方法,所述方法可以在更少的与维护相关的操作中断,以及总体更高的生产率和效率,以及整体改进的操作安全的情况下进行操作。这种方法应该特别有效地避免在再循环mal的蒸发区域以及下游分布器部分的污物沉积。
37.这些目的特别涉及包括异丁烯的两阶段催化气相氧化的方法。为此,应以尽可能简单的方式在所有方法步骤中避免在临界反应条件下形成临界气体混合物。这尤其还涉及避免在分布器部分中形成聚合物和高沸点组分。否则,此类沉积物会导致操作风险增加和/或与维护和清洁相关的操作中断增加。
38.未明确提及的其它目的可以从描述或实施例以及从申请的整体上下文中变得明显,尤其是相对于现有技术。
39.解决方案
40.已经通过提供制备甲基丙烯酸和/或甲基丙烯酸类酯的新方法实现了所述目的。这种新方法包括以下方法步骤:
41.(a)在第一催化气相氧化步骤中将异丁烯、叔丁醇或含异丁烯和/ 或叔丁醇的混合物转化以获得主要含甲基丙烯醛的反应产物,
42.(b)在第二催化气相氧化步骤中将方法步骤(a)的主要含甲基丙烯醛的反应产物转化以获得主要由甲基丙烯酸和未转化的甲基丙烯醛组成的气态反应产物,
43.(c)将方法步骤(b)中的气态反应产物中积累的未转化的甲基丙烯醛的一部分移除、初步提纯和冷凝,以形成液态再循环甲基丙烯醛级分,
44.(d)将所述再循环甲基丙烯醛级分转移到气态料流中,和
45.(e)在催化氧化步骤中将这种气态再循环甲基丙烯醛料流转化。
46.根据本发明的方法的特征特别在于方法步骤(d)包括以下方法方面:
47.i)将步骤c)中获得的液态再循环甲基丙烯醛级分呈液滴形式均匀分布在填料(a packing)表面上以获得液膜,
48.ii)使步骤(i)中获得的液膜与含3体积%-21体积%氧气并具有比所述液态甲基丙烯醛的温度高10-150℃的温度的气体料流接触,以获得含再循环甲基丙烯醛的气体混合物,
49.iii)非必要地将根据(ii)获得的气体料流与额外的蒸汽混合,和
50.iv)将含甲基丙烯醛、氧气、蒸汽、氮气及其它含1-6个碳原子的有机化合物的所得气体料流与第一氧化阶段(a)的反应产物混合。
51.步骤(a)和(b)中描述的氧化步骤优选包括在含氧气体混合物和蒸汽存在下进行的催化气相氧化。这特别优选在管式反应器中在非均相催化剂上进行。
52.对于步骤(c),特别优选从未转化的甲基丙烯醛中除去至少80%的所形成的甲基丙烯酸。特别优选地,根据步骤(c)的移除和初步提纯通过以下方面(i)至(iii)实施:
53.(i)将所述反应混合物骤冷以获得工艺气体和工艺液体,
54.(ii)通过结晶从所述工艺液体除去副产物的至少一部分,和
55.(iii)依次进行吸收和解吸步骤,以获得液态再循环甲基丙烯醛级分和含氮气、氧气和蒸汽的再循环气相。
56.在这种情况下,根据本发明,虽然不太优选,但可以不实施或仅实施这些方面中的单个方面。
57.步骤(c)中获得的液态再循环甲基丙烯醛级分最佳地含有65重量%-99重量%的甲基丙烯醛,0重量%-5重量%的甲基丙烯酸,0重量%-5 重量%的水,至多5000ppm的稳定剂、对苯二甲酸、非挥发性化合物, 0.5重量%-10重量%的丙酮和总共0重量%-5重量%的乙酸、乙醛和丙烯醛。在一个优选的实施方案中,这种液态级分(主要含有甲基丙烯醛,特别是重质挥发性级分,例如乙酸和甲基丙烯酸)还含有痕量的稳定剂,例如氢醌或其衍生物,或n氧化物,例如tempol或其它在现有技术中描述的抑制剂以及这些的混合物。因此,蒸发段可以提供有抑制剂以防止沉积物。然而,另一方面,在蒸发区域和通向分布器的管道中,优选安装合适的排放点,以便以预定间隔连续或不连续地清洁设备并去除液体或固体残留物或以悬浮形式存在的残留物。因此,设备在运转过程中可以保持无残留物,并且可以在很大程度上避免沉积物。
58.对于方法步骤(d),当在一个或多个具有不同氧气含量的气体料流存在下利用一个或多个喷嘴将再循环甲基丙烯醛级分喷雾和分布时,则又是优选的。这特别优选形成具有100-1000μm的平均直径的液滴。此外,优选供应具有小于9体积%的氧气含量的第一气体料流并且非必要供应具有大于9体积%的氧气含量的第二气体料流。在一个优选的实施方案中,可以将氧气含量不同并导致氮气含量不同的两个气体料流单独供应给蒸发设备或预先混合和结合以形成均匀的气体混合物。在最简单的情况下,氧气含量大于9体积%的气体料流是压缩空气。具有小于9 体积%的氧气含量的非必要气体料流源自后处理段(workup section)并且含有再循环气体,所述再循环气体在吸收中已经完全基本上不含挥发性有机成分,尤其是甲基丙烯醛。当然,这种再循环气体料流仍含有一氧化碳和二氧化碳组分。
59.此时设备在大气压或高达2巴的低正压下运转。此处应选择温度和压力,以免低于所得气体混合物中的甲基丙烯醛和水的露点。因此,只有少量更易挥发的成分与一定量的水和乙酸冷凝,然后可以经由如上所述的排放点将其除去。
60.步骤(e)也有各种优选的实施方案。例如,在步骤(e)(i)中,具有小于500μm的液滴尺寸的再循环甲基丙烯醛液滴的至少50%可以优选地分布在填料上。
61.在步骤(e)中,通过又将步骤(a)和/或步骤(b)中获得的返回工艺气体和额外的空气混合优选获得含3体积%-21体积%氧气的气体料流。这种返回的含氧气体在吸收步骤中
已不含挥发性有机成分,并非必要地已在催化后燃烧中进行了处理,以便也去除痕量的有机成分,或将它们转化为惰性氧化产物,例如一氧化碳和二氧化碳。在一个优选的实施方案中,此种的再循环气体应具有小于9体积%的氧气含量并且在返回到甲基丙烯醛蒸发器之前应被压缩。根据本发明,这种气体料流在蒸发器中作为惰性气体的返回和使用在步骤e(i)和e(ii)中进行。
62.在蒸发和混合设备中进行粗甲基丙烯醛、新鲜空气和再循环气体的混合以及蒸汽的添加,使得所得气体料流pg8包含浓度小于或等于2体积%的c1-c6组分。这些组分以一定比例存在于粗甲基丙烯醛中,例如痕量的且在某些情况下,显著量的丙酮、乙醛、丙烯醛和类似组分。对于这种设备部分的安全运转至关重要的是将产生的所得气体混合物调整到贫含区域,并且有机组分的总量不超过2体积%。燃料与总气体的比例以及同样重要的氧气与燃料的比例由此定义。否则,存在较高浓度的这些挥发性成分会导致形成可燃混合物,或者会导致其中个体组分的闪点被认为是关键的混合物。
63.所得的气体料流pg8典型地具有》9体积%的氧气浓度。这种所得气体混合物在蒸发和混合区域内被设置在远低于200
°
(℃),优选低于100
°ꢀ
(℃)的温度。直到分布器段的区域才通过第一氧化阶段的工艺气体将这种再循环的甲基丙烯醛-氧气进一步加热,然后它离开所述分布器尖端。通过使pg8与pg2接触所形成的所得气体料流pg3具有小于9体积%的氧气含量。pg3必须满足基本条件以便用作第二部分氧化的进料气。
64.通过使pg8与pg2接触而形成的所得气体料流pg3具有6.5体积%-8.7体积%的氧气含量,同时氧气与c-1至c-6组分的总量的摩尔化学计量为1.4-3.0。2.0-2.9的范围已证明是所述组分的化学计量的尤其优选且安全的范围。对于安全操作同样重要的是气体料流pg3中甲基丙烯醛的浓度。典型地,在进入到催化剂床之前气体料流pg3中甲基丙烯醛的浓度为2.5体积%-5体积%,尤其优选3.0体积%-4.6体积%。
65.令申请人惊讶的是,已经发现,pg3中的氧气与燃料之比和甲基丙烯醛浓度与第二部分氧化的选择性和转化率具有相当大的相关性,并且还对所使用的经改性杂多酸(heteropolyacid)催化剂的使用寿命具有显著影响。
66.特别是在3.0体积%-4.6体积%的优选浓度范围内,并且氧气与 c1-c6组分的摩尔比为2.0-2.9时,达到最佳选择性。如果设置更高的氧气比例,则甲基丙烯醛转化为甲基丙烯酸的选择性降低,对催化剂使用寿命几乎没有影响。如果反过来设置过低的氧气过量,则会损害催化剂的使用寿命。催化剂的使用寿命可以根据第二阶段的盐浴温度必须提高多少才能在第二阶段反应中实现近似相等的转化率来评估。典型地,将第二反应阶段中的转化率设定为65%-85%,优选70%-80%的甲基丙烯醛转化率(对于单程通过催化剂床)。以气时空速(ghsv)表示的气体速度也会影响系统的整体目标性能。通常使用500-1500(1/秒)的ghsv值,优选700-1300的ghsv。
67.对于步骤(e)(iv),已证明有利且因此优选的是,将在所述步骤中获得的气体混合物利用气体分布器以如下方式引入到步骤(a)中所得的气体混合物中:气体分布器的出口点处的温度低于250℃。以技术上有利的方式设计分布器,使得用含氧气体和蒸汽调节的气体混合物在导管和进料内具有温度梯度。原则上,在甲基丙烯醛蒸发区域中设置较低的蒸发温度。然而,它们应该足够高以确保mal完全蒸发并避免低于露点。然而,另一方面,它们应该足够低以致不会形成聚合物沉积物。取决于所选择的压力,这在50℃-150℃的温度下
是可能的,优选低于100℃的温度。分布器可以经设计使得将所得的具有含氧气体和惰性气体的 mal混合物引导进入具有一个或多个中心管线的反应器区域,然后,向多个管道供应该气体混合物。在工业反应器中,当多个喷嘴和出口管与分布器主管连接时是优选的实施方案。在一个优选的实施方案中,这些出口管或喷嘴以等距间隔沿分布器布置,但自由管直径或长度不同,以确保尽可能均匀的气体分布。原则上,当离主管路最远的出口的自由管直径大于主管路附近的出口的所述管直径时,这是非常优选的。图4中示意性地示出了这样的实施方案。
68.用于分布再循环mal气体的设备的基本特征是从分布器排出的气体的不同温度,特别是在它与第一反应器阶段的工艺气体混合的位置处。在此,原理适用于远离主管的出口处的气体温度例如高于更靠近主管的出口处的气体温度。原则上,分布器和出口的构造应经设计以致在最外出口点处的气体温度不超过260℃的温度。所述设计优选使得最外出口点处的最高温度小于或等于240℃。自然地,考虑到痕量的高沸点组分的存在,在要观察的温度方面也存在下限,特别是考虑到由对苯二甲酸 (“tpa”)引起的问题。tpa在180℃和220℃之间的温度下升华/凝华,这意味着当设计分布器时必须考虑到这一点。如果这些温度低于所述温度,则会产生沉积物和导致操作中断。
69.如本领域技术人员已知的那样,混合可以按逆流或并流进行,原则上可以想到这两种变型。一个优选的实施方案是以逆流方式混合各种气体料流。
70.从步骤(d)和(e)中获得的工艺液体中除去存在的高沸点污染物并将其排出是进一步有利和优选的。
71.此外,有利的是使步骤(b)和/或步骤(e)中获得的甲基丙烯酸经历纯化步骤。这尤其优选经进行以使得获得具有大于99重量%的纯度的纯甲基丙烯酸。
72.甲基丙烯酸可以另外——与其纯度无关——被纯化并随后经历酯化步骤,例如用甲醇酯化得到mma。
73.与现有技术已知的方法相比,根据本发明的方法特别具有以下优点:
74.1)所述方法惊人地节能,特别是因为不必为再循环的mal的蒸发提供额外的能量。
75.2)可以令人惊讶地有效地防止聚合,特别是mal的聚合。特别是因为在临界点液体只能非常短暂地形成,如果有的话,例如呈液滴或液膜形式形成而实现这一点。
76.3)令人惊讶地,由于反应系统在较低压力下运转,所以不需要用于引入气态或液态料流的特殊设备。
77.4)在生产设备中几乎没有发生潜在临界混合过程的临界点。作为以下事实的结果这是可能的,首先将再循环的mal与氧气混合,然后直接导入分布器。
78.5)根据本发明的方法在中间冷却方面也特别有效,因为特别是第一阶段的反应气体在具有较大量较冷气体的分布器中以有效且期望的方式冷却。
79.6)根据本发明的方法在原料效率和选择性以及所达到的总产率方面具有优于现有技术的重大优点。特别地,精确监测和调节氧气与甲基丙烯醛之比(摩尔)在2.0-2.6的范围内和总气体中的氧气含量小于9 体积%且大于7体积%使得在第二催化剂阶段中使用的催化剂的高选择性和长使用寿命之间达到最佳折中。总体而言,达到c4原料如异丁烯或mtbe的较低特定成本并且也增加特定催化剂利用率,后者可以表示为甲基丙烯酸的量/吨催化剂。本发明方法明显减少了处理成本昂贵的副产物如丙烯醛、乙酸和一氧化碳的量。
80.除了根据本发明所述的方法外,本发明还提供相应的制备甲基丙烯酸和/或甲基丙烯酸类酯的生产设备。这种生产设备至少包括以下设备:
81.(a)至少一种c4化合物的至少一个供应设备,
82.(b)第一反应器,含第一氧化催化剂,
83.(c)第二反应器,含第二氧化催化剂,
84.(d)至少一个分离设备,和
85.(e)至少一个蒸发设备。
86.所述生产设备还具有以下方面的特征:
87.(1)蒸发设备(e)装备有填料和非必要地装备有至少一个在所述填料下方用于除去液体的排放阀。
88.(2)蒸发设备(e)经由至少一个分布设备与至少一个液态甲基丙烯醛供应设备连接。
89.(3)蒸发设备(e)经由入口与至少一个空气供应设备和至少一个贫氧气体混合物供应设备连接。
90.(4)所述蒸发设备经由气体导管与第二反应器(c)连接。
91.(5)气体导管经由包括气体分布器的入口通入第二反应器(c)。
92.(6)非必要地,气体导管还与至少一个蒸汽供应设备连接。
93.为此,生产设备的以下设计是优选的:其中分离设备(d)包括至少一个骤冷步骤、至少一个结晶步骤和至少一个吸收/解吸步骤。
94.与此无关,方面(2)的分布设备优选包括多个喷嘴。
95.在蒸发设备内部,用于空气和用于贫氧气体的入口布置在分布设备上方,并且填料布置在分布设备下方的其它实施方案已经证明是特别有利的。
96.最后,本发明还提供根据以上描述的生产设备用于制备甲基丙烯酸和/或甲基丙烯酸类酯,优选mma的用途。
附图说明
97.图1描绘了示意性工艺流程图。尽管所述描绘是根据本发明并且用于举例说明本发明,但所述描绘并不适合以任何方式限制本发明。
98.f1:空气
99.f2:再循环气体
100.f3:异丁烯和/或叔丁醇气体料流
101.f4:蒸汽
102.f5:甲醇
103.r1:第一阶段的反应器
104.r2:第二阶段的反应器
105.r3:酯化反应器
106.g1:气体分布器
107.g2:mal蒸发器
108.su1:骤冷
109.su2:结晶
110.su3:吸收
111.su4:解吸
112.su5:萃取
113.su6:甲基丙烯酸提纯
114.su7:mma提纯
115.ou:废气单元
116.ws:固体废物
117.wg:废气料流
118.dp1:排放1
119.dp2:排放2
120.pg:工艺气体
121.ps:工艺料流
122.图2举例说明了本发明的一个具体实施方案:
123.(1)第一阶段的反应器
124.(2)第二阶段的反应器
125.(3)气体分布器
126.(4)骤冷/骤冷塔
127.(5)结晶
128.(6)吸收塔
129.(7)解吸塔
130.(8)冷凝器
131.(9)甲基丙烯醛蒸发器
132.图3举例说明了mal蒸发器的一个具体实施方案:
133.(102)具有喷嘴的区域
134.(103)填料和喷嘴之间的自由空间
135.(104)主填料
136.(105)下部填料
137.图4举例说明了气体分布器的一个具体实施方案:
138.(108)分布器:主管路入口
139.(109)分布器:中间段
140.(110)分布器:尾段
141.(111)分布器:出口管
142.工艺料流ps1-ps10和工艺气体pg1-pg7的确认将根据图1-4的上下文和下文实施例的描述变得明显。
具体实施方式
143.实施例1
144.在对应于图1的设置中,将工艺气体进料(pg1)通入反应器(r1),所述进料含有异
丁烯(f3)作为起始材料、空气(f1)、含有氧气和惰性气体的循环气体料流(f2)和蒸汽(f4)。所述料流具有1:2:1.5的异丁烯与氧气与水的总体摩尔比。反应器中的温度保持在350℃并将反应器入口的压力保持在1.2巴正压力。这导致1.000h-1
的气时空速(ghsv)。使用根据us 2007/0010394制备的基于氧化钼的催化剂在管束反应器(atube bundle reactor)中进行反应。获得具有343℃的温度的所得工艺气体(pg2)。这种工艺气体具有以下组成:4.8体积%的甲基丙烯醛、0.74 mol%的co、0.21mol%的甲基丙烯酸、0.21mol%的乙酸、0.12mol%的丙酮、0.21mol%的乙醛、0.04mol%的丙烯醛、0.03mol%的甲醛、0.03 mol%的丙烯酸、250ppm的异丁烯和3.5体积%的氧气。异丁烯转化率是 99.6%,并且甲基丙烯醛的产率是79.6%。
145.在下一步骤中,使工艺气体(pg2)与附加工艺气体(pg6)以1比0.8 的(pg6)与(pg2)体积流量比接触并混合。通过气体分布器(g1)进行混合。额外的工艺气体(pg6)是部分再循环的甲基丙烯醛,其在mal蒸发器 (g2)中蒸发并与进一步循环的再循环气体(未命名)、空气(f1)和蒸汽 (f4)混合后,具有80℃的温度。工艺气体(pg6)具有以下组成:1.41mol%的有机成分,其含1.2mol%的甲基丙烯醛、0.03mol%的甲基丙烯酸、 0.09mol%的丙酮、0.05mol%的乙醛、0.04mol%的丙烯醛,和17mol%的氧气和13mol%的水。在这种混合和与反应器气体(pg2)接触期间产生的工艺气体(pg3)具有245℃的温度和1比2.5比4.1的甲基丙烯醛与氧气与水的摩尔比。工艺气体(pg3)总共包含4.38mol%的有机成分,所述有机成分主要由以下成分组成:3.44mol%的甲基丙烯醛、0.31mol%的co、0.12mol%的甲基丙烯酸、0.12mol%的乙酸、0.15mol%的丙酮、 0.15mol%的乙醛、0.06mol%的丙烯醛、0.02mol%的甲醛和0.01mol%的丙烯酸。然后将这种工艺气体(pg3)引导通过第二反应器(r2)。反应器(r2)部分填充有催化剂,所述催化剂是含有磷钼酸盐 (phosphomolybdate)的混合物。催化剂根据us 2007/0010394制备,并且反应最初在292℃(盐温)下并以1.000h-1
(ghsv)的通流速率(athroughflow rate)进行。反应器r2中甲基丙烯醛的转化率大约为78%,操作期间甲基丙烯酸的选择性平均为85%(各种操作测量和气体分析的波动范围 /-1%)。
146.为了在数千小时的整个操作时间内持续转化,定期略微升高反应器的盐浴温度。为保持转化率恒定,每月升温1℃左右,达到7000运转小时后的最终温度为302℃。存在于反应器r2下游的反应气体(pg4)具有以下组成:0.7体积%的甲基丙烯醛、1mol%的co、2.28mol%的甲基丙烯酸、0.31mol%的乙酸、0.12mol%的丙酮、0.21mol%的乙醛、0.04mol%的丙烯醛、0.03mol%的甲醛、0.03mol%的丙烯酸和6.5体积%的氧气。含甲基丙烯酸和mal的工艺气体(pg4)的气体温度约为306℃,并利用气体冷却器降低至230℃,然后在骤冷塔(su1)中将工艺气体冷却至 80℃。在骤冷塔底部,主要是甲基丙烯酸、乙酸、tpa和丙烯酸及其它沸点高于甲基丙烯醛的组分与部分工艺水一起被吸收或冷凝。
147.在骤冷塔(su1)内将含甲基丙烯醛的反应气体冷却到低于30℃的温度。在骤冷塔(su1)中,气体混合物(pg5)由此形成并用多个外部冷却器进一步冷却至13℃。大部分甲基丙烯酸和大部分水在骤冷塔中冷凝。在所述过程中形成的骤冷液体(ps1)在塔底收集并含有35重量%的甲基丙烯酸、0.2%的甲基丙烯醛、1000ppm的tpa(对苯二甲酸)和水。液体在通入tpa结晶(su2)之前被冷却至13℃。在这种结晶(su2)中,过饱和的tpa结晶出来并且让液体滤过tpa过滤单元。tpa然后作为废固体 (ws)收回。又将滤出液通向甲基丙烯醛回收塔
(su4),现在基本上不含 tpa。
148.然后将来自骤冷塔(su1)的气体混合物(pg5)通入甲基丙烯醛吸收塔(su3)的底部。在这个吸收塔(su3)中,一部分工艺料流(ps3)用作甲基丙烯醛的吸收剂介质。工艺料流(ps3)源自下游解吸(su4)并在被引入甲基丙烯醛吸收塔的塔顶之前冷却至17℃。气体混合物(pg5)中的大部分甲基丙烯醛被以逆流模式操作的工艺料流(ps3)吸收,以形成液体工艺料流ps2。经由吸收塔su3的顶部离开的气体混合物(其包含mal吸收塔的大部分未吸收或冷凝的气相)经过洗涤,然后在多个除雾器中加热,并经由来自燃烧系统的热量加热到300℃以形成工艺气体(pg7)。最后,将工艺气体pg7通入配备标准pt-pd燃烧催化剂的燃烧系统 (ou,废气单元),并在那里使所有有机成分燃烧。燃烧系统以再生方式运转,也就是说,来自反应的废热用于预加热入口气体。将从燃烧系统排出的一部分废气在废气压缩机中压缩并再循环到氧化反应系统中。这种气相在下文称为再循环气体(f2)。其余部分作为废气(wg)排放到大气中。
149.将来自甲基丙烯醛吸收塔(su3)底部的工艺料流(ps2)和来自tpa 过滤的液相各自通入mal回收塔(su4)以便在那里回收未转化的甲基丙烯醛。这种塔在350毫巴(绝对压力)减压下运转。底部中的液体温度为大约80℃,塔顶气相温度为大约40℃;这对应于冷凝器上游的蒸气温度。如上所述,来自底部(ps3)的一部分液体被重新用作吸收剂介质。将底料(ps3)的包含33重量%的甲基丙烯酸、80ppm的甲基丙烯醛和 250ppm的tpa的其余部分输送到甲基丙烯酸后处理系统中。使气相中的大部分甲基丙烯醛经由塔顶蒸馏出,冷却至30℃,并获得为含甲基丙烯醛的液体。将一部分来自冷凝器的液体作为回流导回塔中。将液相 (ps4)的其它部分作为再循环料流通入甲基丙烯醛蒸发器(g2)。
150.甲基丙烯醛再循环料流(ps4)含有85重量%的甲基丙烯醛、5重量%的丙酮、3重量%的丙烯醛和0.5重量%的甲基丙烯酸,以及抑制剂。在将其通入甲基丙烯醛蒸发器(g2)之前,将再循环料流冷却至3℃以便进行中间存储。然后将甲基丙烯醛再循环料流(ps4)泵入装备有雾化器系统的液体分布器中。在此产生喷雾到甲基丙烯醛蒸发器(g2)中的填料上的液滴。这会产生均相、均匀的表面分布,以便实现快速、完全蒸发。将供应的空气(f1)和再循环气体(f2)在压缩后冷却至90℃。在将f2和 f1混合后所得的气相组成随后含有15体积%的氧气。然后将压缩气体混合物通入甲基丙烯醛蒸发器(g2)的顶部。在1.2巴正压的压力下进行蒸发,并获得温度为80℃的含氧气体,所述温度高于mal在所选压力下的露点。在蒸发过程中重要的是在接近或高于有机混合物的露点进行蒸发。这确保有机成分尽可能多地实现所需完全蒸发。在蒸发操作过程中,一部分沸点高于甲基丙烯醛的有机成分(例如抑制剂、甲基丙烯酸或对苯二甲酸)可能不完全地或仅以痕量进入气相。因此,定期用水清洗甲基丙烯醛蒸发器,并从甲基丙烯醛蒸发器(g2)底部的排放点(dp1)和稍后的第二个排放点(dp2)排出。将如此清洁的甲基丙烯醛相(pg6)最后通入气体分布设备,即分布器(g1)。使甲基丙烯醛、丙烯醛、丙酮及其它低沸点组分蒸发并作为气相以高速通入分布器(g1),非必要地与额外的蒸汽(f4)一起通入。分布器在第一反应器(r1)的出口区正下方引导和分布气体混合物。在气体分布设备和与其连接的管道装置与第一反应区的热反应气体(pg2)直接接触期间,将气态再循环甲基丙烯醛料流(pg6)与反应气体(pg2)结合以形成具有238℃的温度的所得气体料流(pg3)。这种温度测量与靠近分布器段的外出口管的混合温度有关。
151.连续评估和检查操作和生产操作的结果以评价转化率和选择性,特别是第二反应
阶段的选择性。
152.在7000小时的运转后结束对生产率和选择性的连续评价;结果提供在表1中。在整个时间段内,可以实现大约84%-85%的恒定高选择性;可以利用盐浴温度升高来评价催化剂活性的降低是中度到低度。所述催化剂在运转7000小时后仍保持完全活性,可达78%的转化率,并有足够的继续运转储备。不需要因临界设备条件引起的停机,并且未观察到可能导致安全设备(例如爆破片)拉削(broaching)的临界设备部件中的后燃烧现象或自发压力增加。
153.实施例2
154.异丁烯氧化以类似于实施例1的方式进行,但具有修改的含再循环甲基丙烯醛的气体混合物(pg6)的组成。料流f1、f2、f4和ps4经调整,使得工艺气体(pg6)具有以下组成:1.40mol%的甲基丙烯醛、0.03 mol%的甲基丙烯酸、0.09mol%的丙酮、0.05mol%的乙醛、0.04mol%的丙烯醛、17.1mol%的氧气和13.5mol%的水。如实施例1中那样,将温度为80℃的工艺气体pg6通入分布器(g1)并与工艺气体(pg2)混合以形成温度为240℃的工艺气体(pg3),然而,所述工艺气体(pg3)具有比例为1/2.8/4.1的甲基丙烯醛、氧气和水之比,并含有总共4.44mol%的有机成分。所述有机成分为如下构成:3.31mol%的甲基丙烯醛、0.30 mol%的co、0.12mol%的甲基丙烯酸、0.12mol%的乙酸、0.15mol%的丙酮、0.15mol%的乙醛、0.06mol%的丙烯醛、0.02mol%的甲醛和0.01 mol%的丙烯酸。
155.在7000小时的运转后同样结束对生产率和选择性的连续评价;结果同样提供在表1中。在这里,在整个时间段内,也可以实现大约83%的恒定高选择性,这些比实施例1中的略低。可以利用盐浴温度的升高评价的催化剂活性的降低再次是中度到低度。所述催化剂在运转7000 小时后仍保持完全活性,可达77%-80%的转化率,并有足够的继续运转储备。与实施例1不同,通过较高的氧气浓度不能可靠地排除压力增加事件。这些表明存在可能导致安全设备(例如爆破片)拉削的后燃烧现象。因此,不能排除使用所描述的操作模式会耗尽催化剂的整个使用寿命。
156.实施例3
157.异丁烯氧化以类似于实施例1的方式进行,但具有修改的含再循环甲基丙烯醛的气体混合物(pg6)的组成。料流f1、f2、f4和ps4经调整,使得工艺气体(pg6)具有以下组成:1.40mol%的甲基丙烯醛、0.03mol%的甲基丙烯酸、0.09mol%的丙酮、0.05mol%的乙醛、0.04mol%的丙烯醛、10mol%的氧气和13.5mol%的水。如实施例1中那样,将温度为 80℃的工艺气体pg6通入分布器(g1)并与工艺气体(pg2)混合以形成温度为240℃的工艺气体(pg3),然而,所述工艺气体(pg3)具有比例为 1/2/4.1的甲基丙烯醛、氧气和水之比,并含有总共4.44mol%的有机成分。所述有机成分为如下构成:3.31mol%的甲基丙烯醛和0.30mol%的co、0.12mol%的甲基丙烯酸、0.12mol%的乙酸、0.15mol%的丙酮、 0.15mol%的乙醛、0.06mol%的丙烯醛、0.02mol%的甲醛和0.01mol%的丙烯酸。
158.在7000小时的运转后同样结束对生产率和选择性的连续评价;结果同样提供在表1中。在整个时间段内,第二氧化阶段后的甲基丙烯酸选择性从84.6%(在1000小时的运转后)显著下降至81.8%(在7000小时的运转后)。与实施例2不同,通过低的氧气浓度可始终保证安全操作;可以可靠地排除压力增加事件。然而,总体而言,低的氧气浓度导致根据本发明的实施例1中表现的催化剂使用寿命在这一实施例中也不会耗尽。
159.表1:结果
[0160][0161]
实施例4
[0162]
工艺气体pg3的组成与安全的相关性可以使用爆炸性试验来证明。为此,就它们的可燃性而言研究了表1中列出的气体混合物pg3(对应于实施例1-3)。试验在体积为10l的电加热爆炸球中在240℃的温度和 2.18bara的压力下进行;根据标准din en 1839“气体和蒸气爆炸极限的测定(determination of the explosion limits of gases andvapours)”按照其中规定的“炸弹法(bomb method)”进行测量。对于所有计量组分,气体计量的最大偏差保持在0.1体积%(绝对)的值。试验结果提供在表2中。
[0163]
如点火后最初60秒内可达到的压力的比较显示的那样,在9.5 mol%的氧气浓度下(根据实施例2,对比实施例),可以达到正好低于6 巴的压力,这表明存在爆燃反应。当使用8.5mol%(类似于实施例1,根据本发明的实施例)和6.8mol%(类似于实施例3,对比实施例)的较低氧气浓度时,相对于启动压力在最初60秒内压力几乎保持不变,这表明这些运转参数确保安全的设备运转。
[0164]
表2:爆炸性试验的结果(试验条件:温度=240℃,压力=2.18bara)
[0165]
再多了解一些
本文用于企业家、创业者技术爱好者查询,结果仅供参考。