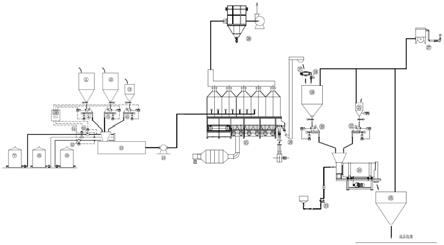
1.本发明涉及洗衣粉加工技术领域,尤其涉及一种连续混炼洗衣粉生产系统和生产工艺。
背景技术:
2.目前中国洗衣粉的生产都采用附图1所示高塔喷粉生产工艺:
3.工艺水、液碱、磺酸、泡花碱、纯碱与芒硝经过处理与称重后加入配料锅,经搅拌后的料浆浓度为65%左右,通过电动过滤筛与磁性过滤器后流入老化锅进行搅拌老化。
4.老化后的料浆经螺杆泵、均质泵、高压泵、平衡罐进入喷粉塔进行干燥;在喷粉前需开启尾气风机,通过一级旋风分离器组、二级湿法除尘器进行除尘,再开启热风炉、燃烧器、一次风机、二次风机,燃烧所用的热源为天然气或柴油;基粉从塔底出来时,表面温度为70~80℃,需采用空气冷却的方式进行冷却,冷却后的基粉才能进行包装,开启气提风机,塔底皮带、提升料斗、沉降分离器、气提布袋除尘器、振动筛送入基粉仓内。
5.基粉通过基粉失重称、总料皮带送入后配混合器内;粒子、酶分别从储存仓、粒子仓,通过失重称、粒子失重称称量后,经过总料皮带送入后配混合器内混合;香精泵将香精罐的香精抽出,在基粉与后配小料进入后配混合器的同时,通过香精计量泵将香精送入混合器内一起混合,后配混合器混合好的成品粉通过成品分配输送机输送到成品仓内,最后进行包装,在制作成品粉时,需通过除尘风机、后配抽风除尘袋式过滤器进行系统除尘。
6.目前这种洗衣粉生产工艺存在以下问题:
7.(1)、消耗大量的能源:
8.目前洗衣粉生产工艺需将固体原料和液体原料加入配料锅中,进行中和反应和均匀混合,为保证混合后料浆的流动性及后续造粒,料浆浓度必须在65%左右,而料浆干燥后的成品洗衣粉含水量在2%左右,每吨成品洗衣粉需要消耗约50kg柴油,相当于消耗100kg标准煤,按2020年中国全年生产320万吨洗衣粉计算,每年消耗约32万吨标准煤。
9.(2)、尾气排放:
10.料浆干燥是在喷雾干燥塔中完成的,塔顶排入大气中的尾气按每吨洗衣粉7000m3标方计,全年排出的尾气约224万方尾气,而尾气中含有大量的co2。
11.(3)、产生大量粉尘排放:
12.喷雾塔尾气需经二级除尘后达到国家规定排放标准100mg/m3。但按全年320万吨洗衣粉计,约有2240吨粉尘排入大气中。
13.(4)、消耗大量的电能:
14.目前洗衣粉生产工艺,由于生产设备众多,工艺复杂,装机容量大,按行业平均水平每吨洗衣粉耗电约65kw,全年耗电约2.08亿度电。
15.(5)、浪费大量的水资源:
16.目前洗衣粉生产工艺需将含水量35%的料浆平燥成含水2%的成品洗衣粉,有33%的水份被蒸发白白浪费掉,按全年320万吨洗衣粉计,有160万吨水被浪费掉。
17.(6)、投资大:
18.由于目前洗衣粉生产工艺,设备数量众多,工艺复杂,不仅设备投资过大,而且运输、安装至员工培训,至最后投产需要1年的时间,需要设置高度30米的干燥塔,相应的厂方投资过大,造成土地资源浪费。
技术实现要素:
19.鉴于背景技术存在的不足,本发明涉及一种连续混炼洗衣粉生产系统和生产工艺,采用混炼反应器中完成中和、混合、老化,料浆浓度可以达到90%,节约了大量水资源以及需要用于干燥的能源,且采用流化床去除8%的水分,减排的大量的粉尘与尾气,同时缩短了工艺流程,可以显著节约投入成本,系统中取消了干燥塔的设置,厂房建设从九层楼缩短至一层楼,显著节约了厂房建造成本。
20.本发明涉及一种连续混炼洗衣粉生产系统,包括原料部分、初加工部分、成品加工部分与环保部分:
21.所述原料部分包括固体原料仓、固体计量系统、液体原料罐、液体计量系统和plc控制系统,所述固体原料仓与固体计量系统连接,所述液体原料罐与液体计量系统连接,所述plc控制系统分别连接固体计量系统与液体计量系统;
22.所述初加工部分包括混炼反应器、料浆高压泵、流化床干燥系统、斗提机、振动筛与头子粉粉碎机,所述混炼反应器分别连接固体计量系统、液体计量系统与料浆高压泵,所述流化床干燥系统与料浆高压泵连接,所述斗提机设于流化床干燥系统与振动筛之间,所述振动筛设于头子粉粉碎机上部;
23.所述成品加工部分包括基粉仓、基粉计量系统、酶仓、酶计量系统、香精仓、香精计量系统、混合器、成品仓,所述基粉仓设于振动筛与头子粉粉碎机下部,所述基粉仓、酶仓与香精仓均通过管道连接至混合器,所述基粉计量系统、酶计量系统与香精计量系统分别设于各自与混合器连接的管道上,所述混合器与成品仓相连;
24.所述环保部分包括尾气处理系统与后配除尘系统,所述尾气处理系统与流化床干燥系统相连,所述后配除尘系统连接有基粉仓、酶仓与成品仓。
25.进一步的,所述固体原料仓包括芒硝仓、纯碱仓与小料仓,所述固体计量系统包括芒硝计量系统、纯碱计量系统与小料计量系统,所述液体原料罐包括液碱储罐、泡花碱储罐与磺酸储罐,所述液体计量系统包括液碱计量系统、泡花碱计量系统与磺酸计量系统,所述固体原料仓与固体计量系统、液体原料罐与液体计量系统一一对应连接。
26.进一步的,所述流化床干燥系统与料浆高压泵连接通过料浆管道连接,所述料浆管道设有料浆喷头,所述料浆喷头设有分叉。
27.进一步的,所述流化床干燥系统包括流化床与干燥器,所述干燥器设于流化床上部,所述流化床设有传送带,所述干燥器与尾气处理系统连接,所述料浆管道伸入流化床干燥系统。
28.进一步的,所述料浆管道延伸至传送带三分之二的位置。
29.本发明涉及一种连续混炼洗衣粉生产工艺,其操作步骤为:
30.s1、所述液体原料从液体原料罐通过对应的液体原料计量系统按plc控制系统控制的配方比例加入到混炼反应器,所述固体原料从固体原料仓通过固体计量系统按plc控
制系统控制的配方比例加入混炼反应器;
31.s2、s1步骤中加入的原料在混炼反应器中进行磺酸中和、物料混合、老化和料浆均质,获得洗衣粉料浆;
32.s3、所述洗衣粉料浆通过料浆高压泵打入流化床干燥系统中进行造粒干燥,所述料浆喷嘴喷出的雾化液滴和流化床内的热风进行沸腾交换,滴液干燥后掉落在流化床上生成基粉,干燥后的基粉在流化床内进一步冷却、老化,干燥器排出的少量尾气进行尾气处理系统后达到排放标准后排出;
33.s4、所述基粉通过斗提机送至振动筛,之后通过振动筛筛分后进入基粉仓,筛分产生的头子粉通过头子粉粉碎机后进入到基粉仓中之后通过振动筛筛分后进入基粉仓,筛分产生的头子粉通过头子粉粉碎机后进入到基粉仓中;
34.s5、所述基粉通过基粉计量系统计量后按配方比例加入到混合器中,同时酶和香精经过经过相应的计量系统计量后也按照比例加入到混合器中,经过充分,均匀混合后的成品进入到成品仓中等待包装,所述基粉仓、酶仓与成品仓中产生的粉尘经后配除尘系统处理达标后排出。
35.进一步的,s2步骤中生产的洗衣粉料浆浓度为90%。
36.本发明的有益效果在于:
37.(1)、用混炼反应器取代目前洗衣粉工艺中的配料、老化、干燥系统。使料浆浓度达到90%,按全年生产320万吨洗衣粉计,消耗约7.7万吨煤,与现有洗衣粉生产工艺相比,全年可节约24万吨煤。
38.(2)、本新技术不用喷粉干燥工艺,用流化床干燥,而干燥水份仅8%左右,只有少量尾气排放,因此全年可减排2000吨粉尘及220万方尾气。
39.(3)、本新技术的料浆浓度为90%,仅需去掉8%的水份,按全年320万吨洗衣粉计,耗水约29万吨,与现有洗衣粉生产工艺相比,可节约131万吨水。
40.(4)、本发明由于工艺流程短,生产设备少,因此可节约投资1/3,生产成本降低1/5。
41.(5)、由于没有尾气排放,可大大降低原材料的消耗,节约成本。
附图说明
42.图1是现有技术生产系统示意图;
43.图2是本发明实施例1的生产系统示意图。
44.附图标记:1、芒硝仓;2、纯碱仓;3、小料仓;4、芒硝计量系统;5、纯碱计量系统;6、小料计量系统;7、液碱储罐;8、泡花碱储罐;9、磺酸储罐;10、液碱计量系统;11、泡花碱计量系统;12、磺酸计量系统;13、混炼反应器;14、料浆高压泵;15、流化床干燥系统;16、斗提机;17、振动筛;18、头子粉粉碎机;19、基粉仓;20、基粉计量系统;21、酶仓;22、酶计量系统;23、香精计量系统;24、混合器;25、成品仓;26、尾气处理系统;27、后配除尘系统;28、plc控制系统。
具体实施方式
45.以下将结合本发明的附图,对本发明实施例中的技术方案进行清楚、完整的描述
和讨论,显然,这里所描述的仅仅是本发明的一部分实例,并不是全部的实例,基于本发明中的实施例,本领域普通技术人员在没有做出创造性劳动的前提下所获得的所有其他实施例,都属于本发明的保护范围。
46.为了便于对本发明实施例的理解,下面将结合附图以具体实施例为例作进一步的解释说明,且各个实施例不构成对本发明实施例的限定。
47.本发明的实施例1参照图2所示,涉及一种连续混炼洗衣粉生产系统和生产工艺,所述生产系统包括原料部分、初加工部分、成品加工部分与环保部分:所述原料部分包括固体原料仓、固体计量系统、液体原料罐、液体计量系统和plc控制系统28;所述初加工部分包括混炼反应器13、料浆高压泵14、流化床干燥系统15、斗提机16、振动筛17与头子粉粉碎机18;所述成品加工部分包括基粉仓19、基粉计量系统20、酶仓21、酶计量系统22、香精仓、香精计量系统23、混合器24、成品仓25;所述环保部分包括尾气处理系统26与后配除尘系统27。
48.所述固体原料仓与液体原料罐通过管道与混炼反应器13连接,所述固体计量系统设于固体原料仓与混炼反应器13的连接管道,所述液体计量系统设于液体原料罐与混炼反应器13的连接管道,所述料浆高压泵14一侧与混炼反应器13连接、另一侧与流化床干燥系统15连接,所述斗提机16设于流化床干燥系统15与振动筛17之间,所述振动筛17设于头子粉粉碎机18上部,所述基粉仓19设于振动筛17与头子粉粉碎机18下部,所述基粉仓19、酶仓21与香精罐均通过管道连接至混合器24,所述基粉计量系统20、酶计量系统22与香精计量系统23分别设于各自与混合器24连接的管道上,所述混合器24与成品仓25相连,所述尾气处理系统26与流化床干燥系统15相连,所述后配除尘系统27连接基粉仓19、酶仓21与成品仓25,所述基粉仓19、酶仓21与成品仓25产生的粉尘由后配除尘系统27进行处理。
49.所述固体原料仓包括芒硝仓1、纯碱仓2与小料仓3,所述固体计量系统包括芒硝计量系统4、纯碱计量系统5与小料计量系统6,所述液体原料罐包括液碱储罐7、泡花碱储罐8与磺酸储罐9,所述液体计量系统包括液碱计量系统10、泡花碱计量系统11与磺酸计量系统12,所述固体原料仓与固体计量系统、液体原料罐与液体计量系统一一对应连接。
50.所述流化床干燥系统15与料浆高压泵14连接通过料浆管道连接,所述料浆管道设有料浆喷头,所述料浆喷头设有分叉。
51.所述流化床干燥系统15包括流化床与干燥器,所述干燥器设于流化床上部,所述流化床设有传送带,所述干燥器与尾气处理系统26连接,所述料浆管道延伸至传送带三分之二的位置,所述传送带剩余的三分之一的位置,方便基粉进行进一步的冷却与老化。
52.一种连续混炼洗衣粉生产工艺:其操作步骤为:
53.s1、所述液体原料从液体原料罐通过对应的液体原料计量系统按plc控制系统28控制的配方比例加入到混炼反应器13,所述固体原料从固体原料仓通过固体计量系统按plc控制系统28控制的配方比例加入混炼反应器13;
54.s2、s1步骤中加入的原料在混炼反应器13中进行磺酸中和、物料混合、老化和料将均质,获得洗衣粉料浆;
55.s3、所述洗衣粉料浆通过料浆高压泵14打入流化床干燥系统15中进行造粒干燥,所述料浆喷嘴喷出的雾化液滴和流化床内的热风进行沸腾交换,滴液干燥后掉落在流化床上生成基粉,干燥后的基粉在流化床内进一步冷却、老化,干燥器排出的少量尾气进行尾气
处理系统26后达到排放标准后排出;
56.s4、所述基粉通过斗提机16送至振动筛17,之后通过振动筛17筛分后进入基粉仓19,筛分产生的头子粉通过头子粉粉碎机18后进入到基粉仓19中,之后通过振动筛17筛分后进入基粉仓19,筛分产生的头子粉通过头子粉粉碎机18后进入到基粉仓19中;
57.s5、所述基粉通过基粉计量系统20计量后按配方比例加入到混合器24中,同时酶和香精经过经过相应的计量系统计量后也按照比例加入到混合器24中,经过充分,均匀混合后的成品进入到成品仓25中等待包装,所述基粉仓19、酶仓21与成品仓25中产生的粉尘经后配除尘系统27处理达标后排出。
58.s1步骤中,所述固体计量系统通过失重秤对固体原料进行计量,所述液体计量系统通过输送泵与流量计进行对液体原料进行计量,所述plc控制系统28按照配方比例自动控制原料投入。
59.s2步骤中生产的洗衣粉料浆浓度为90%,固液物料在混炼反应器13中,完成剪切,混合,研磨,达到高效的分散和分布,从而使料浆更细腻,空气夹带更少,使成品洗衣粉的溶解度显著提高。
60.s4步骤中,所述基粉通过斗提机16提升到高处,提升过程中所述基粉通过进一步的冷却和老化。
61.本发明采用一台混炼反应器13取代目前洗衣粉生产工艺的中和配料、老化、过滤、料浆粉碎设备,显著简化了工艺流程,普通人更容易上手操作,显著节约了员工培训时间,本发明的生产系统在建设时,节约了运输成本、厂房建设时间、设备组装时间,从而减少投资及消耗。
62.在本发明的描述中,需要说明的是,术语“上部”、“下部”仅用于描述目的,而不能理解为指示或暗示相对重要性。
63.最后应说明的是:以上所述实施例,仅为本发明的具体实施方式,用以说明本发明技术方案,而非对其限制,本发明的保护范围并不局限于此,尽管参照前述实施例对本发明进行了详细的说明,本领域的普通技术人员应当理解:任何熟悉本技术领域的技术人员在本发明揭露的技术范围内,其依然可以对前述实施例所记载的技术方案进行修改或可轻易想到变化,或者对其中部分技术特征进行等同替换;而这些修改、变化或者替换,并不使相应技术方案的本质脱离本发明实施例技术方案的精神和范围,都应涵盖在本发明的保护范围之内。因此,本发明的保护范围应所述以权利要求的保护范围为准。
再多了解一些
本文用于企业家、创业者技术爱好者查询,结果仅供参考。