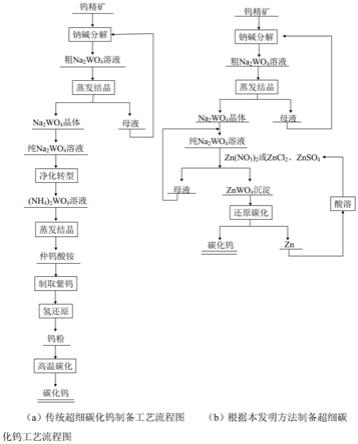
1.本发明属于钨冶炼技术领域,具体涉及钨浸出液的提取转型及碳化钨的制备。
背景技术:
2.钨是一种重要的战略性稀有金属,广泛应用于硬质合金、武器装备、机械加工、电子器件等诸多领域,被多个国家列为战略储备资源。我国是钨资源产出和消耗大国,随着科技的不断发展,国家对钨相关产业的要求也提升到一个新的战略高度。
3.钨冶炼的传统工艺是naoh压煮工艺(国内)和苏打压煮工艺(国外),某些工厂亦采用naoh—na3po4分解工艺。最近几年,新发明的硫酸混酸协同浸出工艺的成功产业化应用,实现钨矿的常压高效连续生产,实现了分解渣的资源化利用和废水的近零排放,具有广阔的应用前景。上述的钨冶炼应用技术均遵循了从钨精矿的湿法分解,到含钨浸出液(钨酸钠或磷钨酸)经离子交换或溶剂萃取转型为钨酸铵溶液,再蒸发结晶制备仲钨酸铵(apt)产品这一流程。apt经密闭煅烧或控制气氛煅烧(氢气轻度还原法),高温煅烧过程中随着分解产出的h2o、n2和h2(nh3分解)的排出,最终剩得了不同的氧化钨产品(黄钨、蓝钨或紫钨)。这说明了apt是从钨矿到制备钨氧化物原料过程中最重要的中间产品,也就是含钨浸出液提取转型成钨酸铵溶液到蒸发结晶制备仲钨酸铵成为了近百年来钨冶炼中必经的环节。随着氨(铵盐)的引入,蒸发结晶过程中氨的回收和母液氨氮废水的治理、提取转型过程产生的氨氮废水的治理则无法回避。例如,传统的强碱性阴离子交换技术(在我国的技术应用一度达到90%以上)生产每吨apt排除的废水量约为湿法炼锌的60倍。
4.为了解决上述难题,需要研发一种新工艺来取代钨酸钠转型为钨酸铵的过程。根据相关报道,正钨酸盐中除碱金属钨酸盐外均难溶于水,因此可将钨酸钠转变为某些难溶钨酸盐,然后再将其用于后续的钨产品如碳化钨制备。更关键的一点是,得到的难溶性钨酸盐能够在高温还原气氛下分解、且被还原逸出,从而实现与钨或碳化钨的分离。考虑到钨酸铅、钨酸锌均难溶于水;而且铅锌具有熔点低、蒸气压高的性质,在高温下可与碳反应时能够生成碳化钨,铅或锌则被还原成金属挥发出来。
5.碳化钨(wc)作为钨冶炼企业生产的重要产品,具有高熔点、高硬度、高导热性和导电性等优点,是一种性能优异的硬质合金原材料,被广泛应用于航空航天、军事、采矿、金属切削等行业,目前世界上绝大部分钨都是以wc形式用于硬质合金领域。目前国内外制备超细碳化钨的方法主要有氧化钨直接碳化法、气相碳化法、高能球磨法、等离子体法等。现阶段批量生产超细碳化钨的工艺仍然以氢还原—碳化法为主,具体来说就是以仲钨酸铵作为原料,对仲钨酸铵煅烧得到氧化钨,氧化钨氢还原得到钨粉,钨粉配碳后于1400℃左右通氢碳化,碳化完成后用球磨机或者气流粉碎技术对碳化钨进行破碎,最后制得wc粉末。陈丽杰等采用上述方法制备的粒度为0.2~0.3微米的超细钨粉为原料,在碳化温度为1350℃,碳化时间为10min/舟的条件下,成功制备出粒度为0.4~0.5微米的超细碳化钨粉(陈丽杰,谢中华,王瑞祥,田磊,聂华平,氧化钨粉还原碳化机理分析及超细碳化钨粉的制备,稀有金属与硬质合金,2018,46(02):11-15 20)。
6.有研究表明,硬质合金的机械性能与碳化钨的晶粒尺寸紧密相关,当碳化钨的晶粒尺寸减小到微米甚至纳米级别时,碳化钨基硬质合金的硬度、强度、韧性、耐磨性等性能显著提升。然而现有通用的氧化钨氢还原过程制备方法制得的碳化钨的粒径较大,且颗粒容易出现团聚,此外,需要专用设备,制备成本较高。
技术实现要素:
7.针对现有碳化钨制备过程存在的问题,本发明第一目的在于,提供一种mwo4制备碳化钨的方法,旨在制备高质量的碳化钨材料。
8.一种mwo4制备碳化钨的方法,将碳还原剂、mwo4在1100℃~1600℃的温度下反应,制得碳化钨,并回收m蒸气;
9.所述的m为zn和/或pb;
10.碳还原剂、mwo4的摩尔比为5~10:1。
11.本发明首次利用mwo4和碳还原剂固-固反应机制制备碳化钨,并进一步通过所述的物料成分比例以及反应温度参数的联合控制,能够有效解决所述全新反应机制所面临的积碳、m金属回收以及颗粒团聚的问题。研究发现,通过所述的反应机制以及比例和反应温度的联合控制,可以获得超细且分布均匀的碳化钨,不仅如此,还能够有效避免颗粒团聚,改善m金属的回收率,并有效降低产物中的积碳;可以获得高质量的碳化钨产品。
12.本发明中,所述的碳还原剂可以是行业内公知的含有碳单质的材料;例如可以是炭黑。
13.优选地,所述的碳还原剂的d50小于或等于45um。
14.本发明中,所述的mwo4的纳米材料,优选的d50小于或等于500nm,例如,可以是100~500nm。
15.本发明中,所述的mwo4可以是商用产品,也可以自制。例如:mwo4由包含所述的水溶性钨酸盐、m源的溶液经水热反应制备;
16.优选地,所述的水溶性钨酸盐为钨酸钠;
17.制备过程中,将水溶性钨酸盐溶液和m源及其溶液混合,随后进行水热反应。
18.所述钨酸钠的溶液为naoh分解钨矿工艺的钨酸钠浸出液,或na2co3分解钨矿工艺得到的钨酸钠浸出液经镁盐法净化后的钨酸钠溶液;
19.优选地,m源为m金属的水溶性盐;优选为硝酸铅、醋酸铅、硝酸锌、氯化锌、硫酸锌、草酸锌中的任意一种。
20.作为优选:水溶性钨酸盐中的w和m源中的m摩尔比为1:1~1:2;
21.优选地,水热反应的起始溶液的ph为5.0~8.0;水热反应的温度优选为110℃~180℃;反应时间优选为2h~24h。
22.本发明中,mwo4和碳还原剂固-固反应机制以及比例和温度的联合控制是协同改善产物粒径、团聚、积碳以及m回收率的关键。研究还发现,进一步控制反应阶段的机制以及参数反应,有助于进一步碳化钨团聚、积碳等问题。
23.本发明可以通过一段反应方式(也称为一步反应)或者两段反应方式(也称为二步反应)进行所述的反应。
24.当所述的反应为一段反应方式时,所述的碳还原剂、mwo4的摩尔比优选为5~6:1。
一段反应的时间可以为1~4h;一段反应结束以及冷却后,可向反应体系中通入空气。通入空气的时间例如为0.5~3h。
25.当所述的反应为两段反应时,其中,第一段反应阶段的碳还原剂为mwo4摩尔量的4~4.5倍;第二段反应阶段添加的碳还原剂为mwo4摩尔量的1~1.2倍。基于本发明所述的两段反应的控制,可无需对反应后的体系通空气。
26.作为优选:第一段反应的温度为1100~1300℃;第一段反应的时间为1h~4h;
27.第二段反应的温度为1400℃~1600℃,第二段反应的时间为1h~4h。
28.本发明中,所述的反应可以在耐压反应设备中反应。
29.本发明中,可基于现有手段,对m蒸气进行冷凝,回收得到m金属;
30.优选地,冷凝得到的金属zn采用硝酸、盐酸或硫酸溶解;得到的铅采用硝酸或醋酸溶解。回收得到的金属循环利用。
31.本发明优选的制备方法,将钨酸钠溶液与沉淀剂混合均匀后,调节ph,然后将其转移至高压釜内,控制反应温度与时间,反应结束后过滤、洗涤、干燥后得到钨酸盐沉淀。然后钨酸盐粉末与炭黑按比例混合,在高温下进行还原、碳化反应,得到超细碳化钨粉末。在还原、碳化过程中,金属蒸汽通过冷凝装置回收,金属经酸溶后得到的含沉淀剂的溶液用于制备纳米钨酸盐。反应结束后向设备内吹入压缩空气,经空气分选来分离完全渗碳的wc和游离碳。
32.所用钨酸钠溶液为naoh分解钨矿工艺得到的钨酸钠晶体溶解后的溶液,钨酸钠溶液浓度为50-200g/l,或苏打分解钨矿工艺得到的钨酸钠浸出液经镁盐法净化后的溶液,钨酸钠溶液浓度为50-200g/l。加入的沉淀剂溶液为硝酸铅、醋酸铅、硝酸锌、氯化锌、硫酸锌中的任意一种,含铅/锌溶液浓度为50-200g/l;钨酸钠溶液和含铅/锌溶液混合过程两者的摩尔比为1:1~1:2,混合液ph控制为5.0~8.0。将混合溶液加入高压釜中,反应温度控制在110℃~180℃,反应时间为2h~24h。
33.采用一步还原碳化制备碳化钨的操作为钨酸盐粉末与炭黑的摩尔比控制为1:5~1:10,还原碳化温度为1100℃~1600℃,保温时间为1h~4h;反应后随炉冷却,随后向反应体系中通入空气0.5~3h。
34.采用钨酸盐为原料进行碳还原制备钨粉、钨粉碳化制备碳化钨的分步操作。第一步的温度为1100℃~1300℃,钨酸盐粉末与炭黑的摩尔比控制为1:4~1:4.5,保温时间为1h~4h。随后再对第一段反应的产物中加入炭黑,进行第二段反应,制得所述的碳化钨;第二段加入的炭黑相比于mwo4摩尔量的1~1.2倍。第二段反应的温度为1400℃~1600℃,保温时间为1h~4h。
35.得到的锌采用盐酸、硫酸或硝酸溶解;得到的铅采用硝酸或醋酸溶解。
36.本发明具有的优点是:
37.1、采用mwo4和碳还原剂固-固反应机制,进一步配合所述的比例以及温度的联合控制,能够获得超细碳化钨,还能够有效降低颗粒团聚,此外,还有助于控制积碳,降低m金属残留,改善m的回收率。
38.2、紧密衔接钨冶炼工艺,可从本质上解决传统钨冶炼工艺中氨氮废水排放大、治理成本高的难题。
39.3、整个工艺过程流程较短,工艺简单,成本较低。
附图说明
40.图1是根据本发明方法以及传统方法制备超细碳化钨粉的工艺流程图(以钨酸锌为例);
41.图2是根据实施例1制备的纳米级钨酸锌x射线衍射图谱;
42.图3是根据实施例1制备的纳米级钨酸锌的扫描电镜照片,放大倍率4万倍;
43.图4是根据实施例1制备的超细碳化钨x射线衍射图谱;
44.图5是根据实施例1制备的超细碳化钨的扫描电镜照片,放大倍率4万倍。
45.图6是根据实施例2制备的纳米级钨酸铅x射线衍射图谱;
46.图7是根据实施例2制备的纳米级钨酸铅的扫描电镜照片,放大倍率4万倍;
47.图8是根据实施例2制备的超细碳化钨x射线衍射图谱;
48.图9是根据实施例2制备的超细碳化钨的扫描电镜照片,放大倍率4万倍。
具体实施方式
49.下面结合实施例作进一步说明,以下实施例旨在说明本发明而不是对本发明的进一步限定。
50.实施例1
51.钨酸钠溶液浓度为100g/l,硝酸锌溶液浓度为100g/l,将钨酸钠溶液和硝酸锌溶液混合均匀,混合过程中二者的摩尔比为1:1,控制混合液ph为7.0。然后将混合液转移至高压釜内,反应温度控制为180℃,反应时间为6h。反应结束后将钨酸锌沉淀过滤、洗涤、干燥,钨酸锌产率为96.4%,平均粒径小于0.05um。采用一步还原碳化制备碳化钨,将钨酸锌粉末与炭黑按摩尔比为1:8混合均匀,控制还原碳化温度为1300℃,保温时间为2h。反应结束后,样品随炉冷却至室温,通入空气1h,得到平均粒径小于0.05um的超细碳化钨粉末。通过冷凝装置回收的锌采用1mol/l的硝酸溶液溶解,锌的回收率为99.5%。
52.实施例2
53.钨酸钠溶液浓度为50g/l,硝酸铅溶液浓度为200g/l,将钨酸钠溶液和硝酸铅溶液混合均匀,混合过程中二者的摩尔比为1:1.5,控制混合液ph为5.0。然后将混合液转移至高压釜内,反应温度控制为160℃,反应时间为8h。反应结束后将钨酸铅沉淀过滤、洗涤、干燥,钨酸铅产率为80.0%。采用一步还原碳化制备碳化钨,将钨酸铅粉末与炭黑按摩尔比为1:10混合均匀,控制还原碳化温度为1100℃,保温时间为4h。反应结束后,样品随炉冷却至室温,之后向设备内吹入压缩空气2h,得到平均粒径小于0.05um超细碳化钨粉末。通过冷凝装置回收的铅采用1mol/l的硝酸溶液溶解,铅的回收率为99.1%。
54.实施例3
55.钨酸钠溶液浓度为200g/l,硝酸锌溶液浓度为50g/l,将钨酸钠溶液和硝酸锌溶液混合均匀,混合过程中二者的摩尔比为1:2,控制混合液ph为8.0。然后将混合液转移至高压釜内,反应温度控制为110℃,反应时间为24h。反应结束后将钨酸锌沉淀过滤、洗涤、干燥,钨酸锌产率为86.0%。采用一步还原碳化制备碳化钨,将钨酸锌粉末与炭黑按摩尔比为1:5混合均匀,控制还原碳化温度为1400℃,保温时间为1h。反应结束后,样品随炉冷却至室温,之后向设备内吹入压缩空气2h,得到平均粒径小于0.05um超细碳化钨粉末。采用1mol/l的硝酸溶液溶解通过冷凝装置回收的锌,锌的回收率为99.2%。
56.实施例4
57.钨酸钠溶液浓度为100g/l,硝酸铅溶液浓度为100g/l,将钨酸钠溶液和硝酸铅溶液混合均匀,混合过程中二者的摩尔比为1:1,控制混合液ph为7.0。然后将混合液转移至高压釜内,反应温度控制为180℃,反应时间为6h。反应结束后将钨酸铅沉淀过滤、洗涤、干燥,钨酸铅产率为96.0%。采用钨酸铅为原料进行碳还原制备钨粉、钨粉碳化制备碳化钨的分步操作,首先将钨酸铅粉末与炭黑按摩尔比为1:4混合均匀,控制还原温度为1100℃,保温时间为2h,得到还原产物钨粉。接着将钨粉与炭黑按摩尔比为1:1.2混合均匀,控制碳化温度为1600℃,保温时间为1h。反应结束后,样品随炉冷却至室温,无需通入空气,得到平均粒径小于0.05um超细碳化钨粉末。采用1mol/l的硝酸溶液溶解通过冷凝装置回收的铅,铅的回收率为99.0%。
58.实施例5
59.钨酸钠溶液浓度为100g/l,氯化锌溶液浓度为100g/l,将钨酸钠溶液和硝酸锌溶液混合均匀,混合过程中二者的摩尔比为1:1,控制混合液ph为7.0。然后将混合液转移至高压釜内,反应温度控制为180℃,反应时间为6h。反应结束后将钨酸锌沉淀过滤、洗涤、干燥,钨酸锌产率为92.7%。采用钨酸锌为原料进行碳还原制备钨粉、钨粉碳化制备碳化钨的分步操作,首先将钨酸锌粉末与炭黑按摩尔比为1:4.2混合均匀,控制还原温度为1200℃,保温时间为2h,得到还原产物钨粉。接着将钨粉与炭黑按质量比为1:1.1混合均匀,控制碳化温度为1500℃,保温时间为2h。反应结束后,样品随炉冷却至室温,无需通入空气,得到平均粒径小于0.05um超细碳化钨粉末。采用1mol/l的稀盐酸溶液溶解通过冷凝装置回收的锌,锌的回收率为99.1%。
60.实施例6
61.钨酸钠溶液浓度为100g/l,硫酸锌溶液浓度为100g/l,将钨酸钠溶液和硝酸锌溶液混合均匀,混合过程中二者的摩尔比为1:1,控制混合液ph为7。然后将混合液转移至高压釜内,反应温度控制为180℃,反应时间为12h。反应结束后将钨酸锌沉淀过滤、洗涤、干燥,钨酸锌产率为93.0%。采用钨酸锌为原料进行碳还原制备钨粉、钨粉碳化制备碳化钨的分步操作,首先将钨酸锌粉末与炭黑按摩尔比为1:4.5混合均匀,控制还原温度为1100℃,保温时间为4h,得到还原产物钨粉。接着将钨粉与炭黑按摩尔比为1:1混合均匀,控制碳化温度为1400℃,保温时间为4h。反应结束后,样品随炉冷却至室温,无需通入空气,得到平均粒径小于0.05um超细碳化钨粉末。采用1mol/l的稀硫酸溶液溶解通过冷凝装置回收的锌,锌的回收率为99.3%。
再多了解一些
本文用于企业家、创业者技术爱好者查询,结果仅供参考。