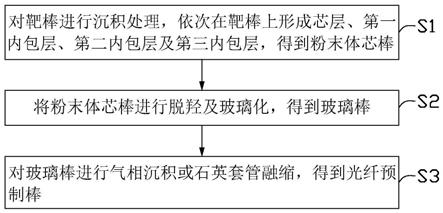
1.本发明涉及光纤制备的技术领域,尤其涉及一种光纤预制棒的制造方法、光纤预制棒及光纤。
背景技术:
2.随着宽带业务开始光纤到户,通信网络的建设重点由核心网向光纤接入网乃至于光纤到户发展。在光纤到户建设中,由于光缆被安放在拥挤的管道中或经过多次弯曲后被固定在接线盒和插座等狭小空间的线路接收端中,导致传统的g.652光纤已不能完全满足使用要求,因此光纤制造商纷纷开展抗弯曲单模光纤的研究。对于光纤制造商而言,在保证光纤光学参数(截止波长、模场直径、零色散波长)可控的范围内,需考虑如何降低弯曲损耗;在满足光纤弯曲损耗的同时,再考虑如何实现简单可控的制造工艺及低成本的光纤制造。众所周知,光纤的衰减、宏弯、光学参数性能取决于光纤预制棒的性能,因此,开发设计和制造一种抗弯曲光纤预制棒将成为光纤制造商的核心。
3.而提高光纤弯曲性能的途径主要有三种,分别为:减小光纤芯径使模场直径减小;提高光纤纤芯与包层折射率差;通过光子晶体光纤(pcf)、孔助光纤(haf)等特殊工艺改变现有g.652光纤阶跃型折射率分布剖面结构。然而,现有的弯曲损耗不敏感单模光纤,光纤剖面复杂,外包层掺杂锗或氯,增加生产工艺难度,加剧剖面不稳定性,不适合批量生产。
技术实现要素:
4.有鉴于此,有必要提供一种光纤预制棒的制造方法、光纤预制棒及光纤,生产难度低,适合大批量生产,且光纤预制棒及光纤具有良好的抗弯曲性能。
5.本发明一实施方式中提供一种光纤预制棒的制造方法,包括以下步骤:
6.对靶棒进行沉积处理,依次在靶棒上形成芯层、第一内包层、第二内包层及第三内包层,得到粉末体芯棒;
7.将粉末体芯棒进行脱羟及玻璃化烧结,得到玻璃棒;
8.对玻璃棒进行气相沉积或石英套管融缩,得到光纤预制棒。
9.在本发明的一些实施例中,沉积所述芯层的步骤包括使用一芯层喷灯,所述芯层喷灯与水平与水平方向的夹角30
°
~90
°
,通入sicl4、gecl4、h2、o2、ar,其中sicl4流量控制在2~5g/min,gecl4流量控制在50~300cc/min,火焰温度在850~950℃,形成芯层。
10.在本发明的一些实施例中,沉积所述第一内包层时,通入sicl4、碱金属掺杂剂、氟化物、h2、o2、ar,其中sicl4流量控制在5~50g/min,通入氟化物的流量控制在50~400cc/min,通入碱金属掺杂剂的流量控制在0~20cc/min,以在芯层表面形成所述第一内包层。
11.在本发明的一些实施例中,沉积所述第二内包层时,通入sicl4、h2、o2、ar,其中sicl4流量控制在5~20g/min,火焰温度在1250~1400℃,以在第一内包层表面形成所述第二内包层。
12.在本发明的一些实施例中,沉积所述第三内包层时,通入sicl4、氟化物、h2、o2、ar,
其中sicl4流量控制在10~50g/min,氟化物的流量控制在500~1000cc/min,火焰温度在1250~1400℃,以在所述第二内包层表面形成所述第三内包层。
13.在本发明的一些实施例中,通入sicl4、氟化物、h2、o2、ar,以增加和控制所述第三内包层的掺氟深度其中sicl4流量控制在0~5g/min,氟化物的流量控制在200~1000cc/min,火焰温度在1250~1400℃。
14.在本发明的一些实施例中,烧结反应时,脱羟温度控制在800~1000℃,并通入400~1000cc/min的cl2以及10~30l/min的he,同时通过压力控制器控制压力在5~20pa提高脱羟效果。
15.在本发明的一些实施例中,烧结反应时,脱羟结束后按照2~5℃/min的升温速率升至1300℃~1600℃,保持通入10~30l/min的he。
16.在本发明的一些实施例中,烧结反应时,在1100℃~1400℃之间恒温3~6h,同时保持通入10~30l/min的he,将疏松体烧结为玻璃棒。
17.本发明一实施方式中提供一种光纤预制棒,所述光纤预制棒由上述权光纤预制棒的制造方法制备而成。
18.本发明一实施方式中还提供一种光纤,由上述的光纤预制棒制备而成,所述光纤依次包括芯层、第一内包层、第二内包层、第三内包层及外包层,其中芯层的剖面中心凹陷折射率差值为0.00~0.03,相对折射率差值为0.340~0.400%,第一内包层相对折射率差值为-0.030~-0.060%,第三内包层相对折射率差值为-0.100~-0.200%。
19.上述光纤预制棒的制造方法、光纤预制棒及光纤,光纤预制棒制造时,一次完成光学芯层掺锗和包层掺氟结构的设计,降低生产难度,避免氟套管使用,减少生产成本,可批量生产,通过所述光纤预制棒制造方法制得的光纤预制棒以及通过光纤预制棒制得的光纤,弯曲性能优异且衰减低。
附图说明
20.图1为本发明一实施方式中的光纤预制棒的制造方法的流程示意图。
21.图2为本发明一实施方式中的沉积设备的结构示意图。
22.图3为本发明一实施方式中的烧结设备的结构示意图。
23.图4为本发明一实施方式中光纤的截面示意图。
24.图5为本发明一实施方式中光纤折射率剖面图。
25.主要元件符号说明
26.[0027][0028]
如下具体实施方式将结合上述附图进一步说明本发明。
具体实施方式
[0029]
下面将结合本发明实施例中的附图,对本发明实施例中的技术方案进行清楚、完整地描述,显然,所描述的实施例仅仅是本发明一部分实施例,而不是全部的实施例。
[0030]
需要说明的是,当组件被称为“装设于”另一个组件,它可以直接在另一个组件上或者也可以存在居中的组件。当一个组件被认为是“设置于”另一个组件,它可以是直接设置在另一个组件上或者可能同时存在居中组件。
[0031]
为了便于理解,定义如下术语:折射率剖面:光纤或光纤预制棒(包括芯棒)玻璃折
射率与其半径之间的关系;
[0032]
相对折射率差值:δni=(ni-n0)/n0,ni对应光纤各部分的折射率,n0为纯二氧化硅玻璃折射率。
[0033]
除非另有定义,本文所使用的所有的技术和科学术语与属于本发明的技术领域的技术人员通常理解的含义相同。本文中在本发明的说明书中所使用的术语只是为了描述具体的实施例的目的,不是旨在于限制本发明。本文所使用的术语“或/及”包括一个或多个相关的所列项目的任意的和所有的组合。
[0034]
本发明的实施例提供一种光纤预制棒的制造方法,包括以下步骤:
[0035]
在芯层的表面依次沉积形成第一内包层、第二内包层及第三内包层;
[0036]
将形成的包含第一内包层、第二内包层及第三内包层的芯层整体进行脱羟及玻璃化烧结,得到玻璃棒;
[0037]
在所述玻璃棒表面通过气相沉积法或石英套管融缩形成外包层,得到光纤预制棒。
[0038]
本技术一实施方式中提供一种光纤预制棒,所述光纤预制棒由上述权光纤预制棒的制造方法制备而成。
[0039]
本技术一实施方式中还提供一种光纤,由上述的光纤预制棒制备而成,所述光纤依次包括芯层、第一内包层、第二内包层、第三内包层及外包层,其中芯层的剖面中心凹陷折射率差值为0.00~0.03,相对折射率差值为0.340~0.400%,第一内包层相对折射率差值为-0.030~-0.060%,第三内包层相对折射率差值为-0.100~-0.200%。
[0040]
上述光纤预制棒的制造方法、光纤预制棒及光纤,光纤预制棒制造时,一次完成光学芯层掺锗和包层掺氟结构的设计,降低生产难度,避免氟套管使用,减少生产成本,可批量生产,通过所述光纤预制棒制造方法制得的光纤预制棒以及通过光纤预制棒制得的光纤,弯曲性能优异且衰减低。
[0041]
下面结合附图,对本发明的一些实施方式作详细说明。
[0042]
请一并参阅图2和图3,首先对本发明实施例的光纤预制棒的制造方法中使用的设备进行说明,所述设备包括沉积设备10和烧结设备20,用于光纤预制棒的制造,所述沉积设备10用于对靶棒200进行沉积以得到粉末体芯棒300,所述烧结设备20用于对粉末体芯棒300进行脱羟及玻璃化。
[0043]
所述沉积设备10包括沉积室11、提升组件12、吊杆13及喷灯组件15,所述沉积室11包括沉积腔体111,所述提升组件12安装于所述沉积腔体111一端,且所述提升组件12可绕自身轴线转动并沿所述沉积室11长度方向上下移动。所述吊杆13一端固定于所述提升组件12上,另一端用于悬挂所述靶棒200。在一实施方式中,所述吊杆13上设置有卡槽(图中为示出)以与所述靶棒200配合,所述靶棒200在所述吊杆13的带动下沿轴线方向上下移动。在一实施方式中,所述沉积室11大体为中空圆柱状。所述喷灯组件15安装于所述沉积室11一侧,并且所述喷灯组件15一端朝向所述靶棒200,以对所述靶棒200进行沉积。在一实施方式中,所述喷灯组件15包括芯层喷灯151、第一内包层喷灯152、第二内包层喷灯153、第三内包层喷灯154及第四内包层喷灯155,依次设置在所述沉积室11外部,用于对靶棒200进行沉积。所述沉积设备10还包括红外热成像仪16,所述红外热成像仪16连接于所述沉积室11,用于监控各层喷灯火焰温度以控制氢氧流量、设定粉末密度,达到掺氟效果。
[0044]
所述烧结设备20包括炉芯管21、围绕所述炉芯管21设置的加热体22、吊杆23、提升组件24、隔热板25及压力控制器26,所述提升组件24安装于所述炉芯管21一端,且所述提升组件24可绕自身轴线转动并沿所述炉芯管21长度方向上下移动。所述吊杆23一端固定于所述提升组件24上,另一端用于悬挂所述粉末体芯棒300。所述隔热板25设置在所述炉芯管21内,且套设于所述吊杆23上,以实现隔热保温的作用。所述压力控制器26连接于所述炉芯管21,以控制所述炉芯管21内的压力。所述炉芯管21远离所述提升组件24一端设置有进气孔211,所述进气孔211用于通气,以实现烧结。
[0045]
请参阅图1,本发明实施例提供的光纤预制棒的制造方法,包括以下步骤:
[0046]
s11:对靶棒进行沉积处理,依次在靶棒上形成芯层、第一内包层、第二内包层及第三内包层,得到粉末体芯棒;
[0047]
具体的,在一实施例中,所述靶棒200为石英玻璃种棒,先将靶棒200通过吊杆13悬挂在所述提升组件12上,沉积反应时,所述芯层喷灯151中通入sicl4、gecl4、h2、o2、ar,sicl4流量控制在2~5g/min,gecl4流量控制在50~300cc/min,通过高温水解反应生成芯层粉末sio2、geo2附着在所述靶棒200表面,并且随着所述靶棒200向上提升,芯层粉末体逐渐生长形成芯层101,同时在沉积过程中监控芯层喷灯151的火焰温度在850~950℃,以控制geo2最佳反应温度,从而降低gecl4用量同时在沉积芯层101时,通过设置所述芯层喷灯151与水平方向的夹角为30
°
~90
°
,形成具有凹陷结构的芯层101;
[0048]
一实施例中,沉积所述第一内包层102时,所述第一内包层喷灯152中通入sicl4、碱金属掺杂剂、氟化物、h2、o2、ar,以在所述芯层表面形成具有一定厚度的sio2层,即第一内包层102,其中通入sicl4流量控制在5~50g/min,氟化物的流量控制在50~400cc/min,碱金属掺杂剂的流量控制在0~20cc/min,粉末密度控制在0.3~0.7g/cm3,生成的第一内包层102粉末厚度是芯层棒径的1.0~2.0倍,其中碱金属掺杂剂可以是na、k、rb、cs、mg、ca任意一种的卤化物。碱金属掺杂剂起降低包层粘度、降低由结构不均匀性造成的瑞利散射损耗的作用。
[0049]
一实施例中,沉积所述第二内包层103时,所述第二内包层喷灯153中通入sicl4、h2、o2、ar,以在所述第一内包层表面形成具有一定厚度的sio2层,即第二内包层,其中sicl4流量控制在5~20g/min,粉末密度控制在0.7~1.0g/cm3,生成的第二内包层103粉末厚度是芯层棒径的0.5~1.0倍,且在沉积过程中,监控火焰温度在1250~1400℃,控制第二内包层103粉末密度,以降低沉积时氟过多的渗入芯层。
[0050]
一实施例中,沉积所述第三内包层104时,所述第三内包层喷灯154中通入sicl4、氟化物、h2、o2、ar,以在所述第二内包层103表面形成具有一定厚度的掺杂有氟的sio2层,即第三内包层104,其中,通入sicl4流量控制在10~50g/min,氟化物的流量控制在500~1000cc/min,粉末密度控制在0.2~0.6g/cm3,生成的第三内包层104粉末厚度是芯层棒径的1.5~2.5倍,且沉积过程中,监控火焰温度在1250~1400℃,以控制第三内包层粉末密度,通过氟化物掺杂达到预期掺氟深度,减少氟套管的使用,且沉积达到设定长度后,停止沉积。具体的,所述第三喷灯是掺氟喷灯,且其原料层端面与所述第六层相距100~140mm,其中原料层sicl4,第一层o2及氟化物,第二层ar,第三层h2,第四层ar,第五层o2,具体多少层此处不作详细描述。
[0051]
一实施例中,所述第四内包层喷灯155中通入sicl4、氟化物、h2、o2、ar,用于增加所
0.06%之间,第三内包层相对折射率差值δn3在-0.15~-0.20%之间,第三内包层采用ovd沉积工艺,将透明玻璃棒延伸到直径55mm长度1800mm,进行ovd沉积,沉积结束后进行通cl2脱羟烧结,最终形成弯曲损耗不敏感光纤预制棒,对光纤预制棒通过拉丝得到弯曲损耗不敏感光纤。
[0064]
实施例2
[0065]
1)芯层火焰的温度控制在850~950℃之间;
[0066]
2)芯层喷灯通入sicl4流量3g/min,gecl4流量240cc/min;芯层喷灯与水平的夹角38
°
;
[0067]
3)第一内包层喷灯通入sicl4流量20g/min,cf4的流量400cc/min,kcl的流量5cc/min;第二内包层喷灯通入sicl4流量5g/min;第三内包层喷灯通入sicl4流量25g/min,通入cf4的流量500cc/min;第四内包层喷灯通入sicl4流量1g/min,cf4的流量300cc/min,火焰的温度控制在1250~1400℃之间。
[0068]
4)第一阶段,脱羟温度设定1000℃,从中部炉芯管底部通入500cc/min的cl2,通入20l/minhe,压力控制在10pa;第二阶段,脱羟结束后按照3℃/min的升温速率升至1300℃,保持通入20l/min的he;第三阶段,在1300℃之间恒温3.5h,将疏松体烧结为透明玻璃棒,保持通入20l/min的he;
[0069]
根据以上的流量设定,形成芯层的剖面中心凹陷折射率差值在0~0.03之间,芯层相对折射率差值δn1在0.340~0.400%之间,第一内包层相对折射率差值δn2在-0.03~-0.06%之间,第三内包层相对折射率差值δn3在-0.15~-0.20%之间,
[0070]
第三内包层采用ovd沉积的工艺,将透明玻璃棒延伸到直径55mm长度1800mm,进行ovd沉积,沉积结束后进行通cl2脱羟烧结,最终形成弯曲损耗不敏感光纤预制棒,光纤预制棒通过拉丝得到弯曲损耗不敏感光纤。
[0071]
实施例3
[0072]
1)芯层火焰的温度控制在850~950℃之间;
[0073]
2)芯层喷灯通入sicl4流量3g/min,gecl4流量260cc/min;芯层喷灯与水平的夹角42
°
;
[0074]
3)第一内包层喷灯通入sicl4流量20g/min,cf4的流量150cc/min,kcl的流量5cc/min;第二内包层喷灯通入sicl4流量5g/min;第三内包层喷灯通入sicl4流量25g/min,通入cf4的流量700cc/min;第四内包层喷灯通入sicl4流量1g/min,cf4的流量300cc/min,火焰的温度控制在1250~1400℃之间。
[0075]
4)第一阶段,脱羟温度设定1000℃,从中部炉芯管底部通入500cc/min的cl2,通入20l/minhe,压力控制在10pa;第二阶段,脱羟结束后按照3℃/min的升温速率升至1300℃,保持通入20l/min的he;第三阶段,在1300℃之间恒温3.5h,将疏松体烧结为透明玻璃棒,保持通入20l/min的he;
[0076]
根据以上流量设定,形成芯层的剖面中心凹陷折射率差值在0~0.03之间,n1在0.340~0.400%之间,n2在-0.03~-0.06%之间,n3在-0.15~-0.20%之间,第三内包层采用ovd沉积工艺,将透明玻璃棒延伸到直径55mm长度1800mm,进行ovd沉积,沉积结束后进行通cl2脱羟烧结,最终形成弯曲损耗不敏感光纤预制棒,对光纤预制棒通过拉丝得到弯曲损耗不敏感光纤。
[0077]
通过以上三个实施例得到的光纤的相关参数如下:
[0078]
请参阅图3,光纤剖面参数:其中,h为剖面中心凹陷折射率差值,δn为相对折射率差值,r为光纤半径,δn1为芯层相对折射率差值,δn2为第一内包层相对折射率差值,δn3为第三内包层相对折射率差值,r1为芯层半径,r2为第一内包层半径,r3为第二内包层半径,r4为第三内包层半径,具体的,所述折射率剖面可以使用vad沉积工艺,也可以使用pcvd沉积工艺。
[0079]
参数单位数值实例1实例2实例3h\0.00~0.030.0150.0130.018δn1%0.340~0.4000.3580.3520.362δn2%-0.030~-0.060-0.030-0.040-0.035δn3%-0.100~-0.200-0.150-0.150-0.180r1mm3.5~5.04.03.94.2r2mm8~10999r3mm10~13111111r4mm18~20191919
[0080]
光纤测试性能参数:
[0081][0082][0083][0084]
上述光纤预制棒的制造方法、光纤预制棒及光纤,其中光纤预制棒的制备通过红外热像仪监控温度,优化各层氢氧气配比,控制粉末密度,为掺氟效果提供依据;同时在第一内包层中通入碱金属和氟化物,降低包层粘度,使得预制棒网络结构均匀,进一步降低由
结构不均匀性造成的瑞立散射损耗;同时通过控制各内包层粉末密度以及掺氟结构设计,保证了制得的光纤的弯曲性能,改善了衰减,适合批量化生产。
[0085]
本技术领域的普通技术人员应当认识到,以上的实施方式仅是用来说明本发明,而并非用作为对本发明的限定,只要在本发明的实质精神范围内,对以上实施方式所作的适当改变和变化都落在本发明要求公开的范围内。
再多了解一些
本文用于企业家、创业者技术爱好者查询,结果仅供参考。