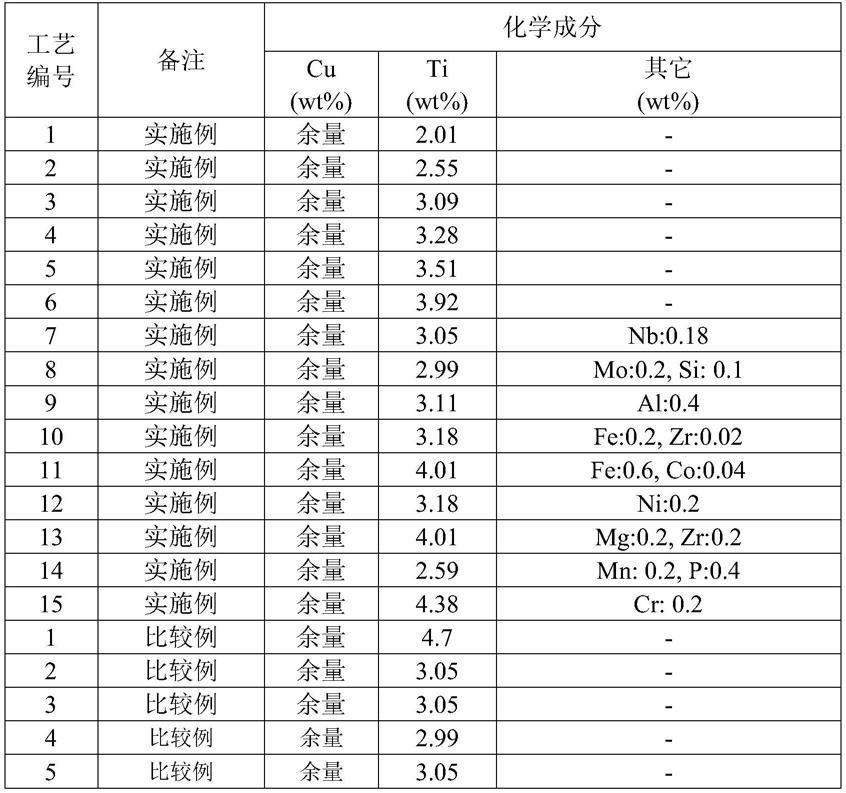
1.本发明属于铜合金技术领域,具体涉及一种钛青铜带材及其制备方法。
背景技术:
2.随着5g的快速发展,手机、电脑等产品也逐渐往小型化、轻薄化、多功能化方向发展。相对应的电子器件,包括连接器、高性能弹片等元件也需要小型化、轻薄化。设计者们倾向于选用性能高、各向异性小且弯曲加工性能优异的铜合金材料以满足现今零件高性能、加工复杂的需求。
3.一直以来,连接器及弹片领域对导电、机械性能及加工性的要求使得设计者选择材料时优先考虑铜合金,作为铜合金性能之王的铍铜更是最优选择,但铍铜合金的成本及加工过程中的剧毒让众多厂家望而却步。近些年高强、高弹、优异的加工性能的钛青铜以替代铍铜的角色进入了人们的视野,并广泛应用于接触件、弹性零件等领域。
4.钛青铜合金是调幅分解及时效强化型合金,通过调幅分解、时效强化和加工硬化,能够达到很高的强度。对于弹性接触件,高强度意味着更大的接触正向力,在同等情况下其接触电阻更小,产生的热量越小,散热需求也就越小。常规的钛青铜处理工艺在提高强度之后,弯曲加工性能下降,材料内部的各向异性增大,对应的各向延伸率差异较大,在进一步加工过程中非常容易出现开裂现象。
5.因此,为应对快速发展的消费电子、通讯基站等对铜合金的更高要求,现有的钛青铜合金仍需进一步改进。
技术实现要素:
6.本发明所要解决的第一个技术问题是提供一种强度高、各向异性小、弯曲加工性能等综合性能优异的钛青铜带材。
7.本发明解决第一个技术问题所采用的技术方案为:一种钛青铜带材,其特征在于,该钛青铜带材的质量百分比组成为ti:2.0~4.5wt%,余量为cu和不可避免的杂质;该钛青铜带材含有的高斯织构的体积分数为5%~20%,黄铜织构的体积分数为10%~25%,s织构的体积分数为5%~20%,铜型织构的体积分数为5%~15%,各织构取偏离标准角度15
°
以内的织构。
8.钛青铜中ti元素为主要强化元素,当ti含量低于2.0wt%时,调幅分解及时效强化的程度较低,虽然导电率较高,但得不到较高的强度,不能满足应用需求。当ti含量高于4.5wt%时,材料导电率低,严重增加零件电阻,导致接触部位发热明显;而且ti含量过高板料在热轧时容易开裂,增加轧制的难度,降低成品率。
9.铜合金中典型织构有高斯织构{011}<100>、黄铜织构{011}<211>、s织构{123}<634>和铜型织构{112}<111>。研究发现,上述织构的体积分数对钛青铜强度、各向延伸率、弯曲加工等性能的影响较为显著。现今制备技术中,通常对单一织构的体积分数进行控制,难以满足综合性能控制的需要。为获得强度高、各向延伸率优良、弯曲加工性能优异的钛青
铜带材,本发明把钛青铜的织构体积分数控制在以下范围内,高斯织构的体积分数为5%~20%,黄铜织构的体积分数为10%~25%,s织构的体积分数为5%~20%,铜型织构的体积分数为5%~15%,钛青铜带材的综合性能得到了明显的优化。
10.作为优选,该钛青铜带材的织构比例满足:0.5≤x1/x2≤1.5,其中x1为α取向线上高斯织构、黄铜织构的体积分数之和,x2为β取向线上黄铜织构、s织构和铜型织构的体积分数之和。
11.图1是利用ebsd进行测定且通过odf(取向分布函数)分析得到的铜合金板材代表性的结晶取向分布图,利用轧制面内的双轴正交方向即与轧制方向平行的方向rd和轧制垂直方向td、以及轧制面的法线方向nd这3个方向的欧拉角来表示,将rd轴的取向旋转表示为将nd轴的取向旋转表示为将td轴的取向旋转表示为其中α取向线上的典型织构有高斯织构和黄铜织构,β取向线上的典型织构有黄铜织构、s织构和铜型织构。伴随热处理及冷热加工工艺,材料内部的α取向线上的织构与β取向线上的织构会发生转变,本发明人研究发现控制上述α取向线和β取向线上典型织构的比例能够进一步地优化合金的综合性能。当x1/x2的比值为0.5~1.5时,钛青铜带材在兼顾强度的情况下能具有优异的弯曲加工性能及各向延伸率。若比值小于0.5,材料的强度更高,但是各向异性强,弯曲加工性能差,加工易开裂;当比值大于1.5时,板料的折弯性能好,但是屈服强度低。因此,为达到本发明的预期效果,实现钛青铜合金强度、各向延伸率及折弯性能的平衡,需对上述织构的比例进行控制。
12.作为优选,该钛青铜带材还含有总量为0.01~0.8wt%选自fe、co、nb、al、si、mo、zr、mg、cr、ni、mn、p中至少一种。添加这些微量元素能够提高ti在时效过程中的析出效果,提高强度及导电率。但如果微量元素添加过多将会导致析出相过多进而降低折弯性能。
13.作为优选,该钛青铜带材的平均晶粒尺寸为5~30μm。晶粒小,细晶强化效果高,延伸率与强度的匹配性更好;另外晶粒小其弯曲加工性能更好。
14.作为优选,该钛青铜带材各向延伸率差值δel为
‑
2.0%~2.0%,其中δel=(el0‑
2el
45
el
90
)/2,el0、el
45
、el
90
分别为偏离带材轧制方向0
°
、45
°
和90
°
的断裂延伸率。当δel的数值不满足
‑
2.0%~2.0%时,合金带材各向延伸率差值较大,对应的各向异性大,难以满足进一步加工需要。
15.作为优选,该钛青铜带材rd方向的屈服强度为850~1050mpa;rd方向的延伸率为5~15%;在150℃,暴露1000小时后的应力松弛率≤10%;td方向90
°
弯曲加工性能满足r/t≤0.5,r为弯曲半径,t为带材的厚度;其中,rd方向为平行于轧制方向,td方向为垂直于轧制方向。
16.本发明所要解决的第二个技术问题是提供一种钛青铜带材的制备方法。
17.本发明解决第二个技术问题所采用的技术方案为:一种钛青铜带材的制备方法,其特征在于,工艺流程包括:熔铸
→
均匀化退火
→
热轧
→
冷轧
→
预固溶处理
→
固溶处理
→
第一次时效处理
→
最终冷轧
→
第二次时效处理;所述均匀化退火温度为850~950℃,时间为1~16h,对均匀化退火后的铸锭热轧,热轧总变形量为85%~98%,其中750℃以下的变形量为15%~55%,并且保证热轧的终轧温度在650℃以上,终轧后以冷却速度≥100℃/s进行冷却。均匀化退火温度、热轧温度、热轧总变形量、750℃以下的变形量及终轧的温度直接影响到最终带材的织构比例。
18.作为优选,所述冷轧为单次或者多次,每次的总变形率为50%~80%,在两次冷轧之间可选择退火处理。
19.作为优选,所述预固溶处理的温度为350~500℃,时间1h~16h;所述固溶处理的温度为780℃~950℃,时间为2s~150s,固溶后冷却速度≥100℃/s。预固溶处理能降低材料内部的位错,让后续再结晶过程变慢,得到特定的织构组分及晶粒大小细小且均匀的晶粒。所以预固溶处理能保证固溶后的晶粒更小,有利于织构的控制,提高材料性能的可控性。固溶处理后晶粒尺寸控制在5~30μm,优选5~15μm。
20.作为优选,所述第一次时效处理在非活性气氛保护下350℃~500℃范围内保温1h~12h;所述第二次时效处理在非活性气氛保护下250℃~500℃温度范围内保温0.01h~10h。
21.作为优选,所述最终冷轧的总变形量为5%~20%,单道次轧制变形量为5%~10%。该加工率控制材料内部的α取向线、β取向线上的织构转变,最终提升材料的综合性能。
22.在本文中,所述“带材”是本领域中常见的材料形式,其厚度通常不大于1mm。
23.与现有技术相比,本发明的优点在于:
24.(1)本发明钛青铜带材通过成分及特定织构体积分数的控制,实现了合金在具有高强度的同时具有各向延伸率差异小、耐应力松弛和弯曲加工性能等综合性能的优异。
25.(2)本发明钛青铜带材各向延伸率差值δel为
‑
2.0%~2.0%,其中δel=(el0‑
2el
45
el
90
)/2,el0、el
45
、el
90
分别为偏离带材轧制方向0
°
、45
°
和90
°
的断裂延伸率。
26.(3)本发明钛青铜带材rd方向的屈服强度为850~1050mpa;rd方向的延伸率为5~15%;在150℃,暴露1000小时后的应力松弛率≤10%;td方向90
°
弯曲加工性能满足r/t≤0.5,r为弯曲半径,t为带材的厚度;其中,rd方向为平行于轧制方向,td方向为垂直于轧制方向。
附图说明
27.图1为铜合金板带代表性的结晶取向分布图。
28.图2为本发明实施例3的金相组织照片。
29.图3为本发明比较例2的金相组织照片。
具体实施方式
30.以下结合附图实施例对本发明作进一步详细描述。
31.设计了15个实施例和5个比较例合金,具体成分见表1。其中,实施例采用本发明制备方法进行制备,工艺流程包括:熔铸
→
均匀化退火
→
热轧
→
冷轧
→
预固溶处理
→
固溶处理
→
第一次时效处理
→
最终冷轧
→
第二次时效处理,关键控制参数见表2。为避免使得本技术的说明书过于冗长,以下记载实施例3的详细制备步骤和工艺参数作为示例。
32.实施例3的成品厚度规格为0.1mm,具体工艺如下:
33.设计具有钛含量3.09%的钛青铜合金,采用上述真空熔炼方法,在1300
±
50℃的熔炼温度下,铸造出7kg的方形铸锭。
34.铸锭完成后,对铸锭表面进行铣面,铣面深度为3~5mm之间。
35.将铣面后的铸锭在900℃温度下保温12h后进行热轧,总轧制变形量87%,在轧制过程中,750℃下变形量25%,且终轧温度为650℃以上,热轧完成后以100℃/s以上的冷却速度进行冷却。
36.热轧后依次进行冷轧、退火及冷轧,每次冷轧总加工率控制在50%~80%,最后一次冷轧控制板材厚度为0.11mm。
37.然后进行预固溶处理,预固溶处理的工艺为450℃保温6h。
38.预固溶处理后进行最终的固溶处理,固溶温度为800℃,时间为100s。
39.固溶后进行第一次时效处理,第一次时效工艺为420℃保温8h。
40.在第一次时效后进行合计18%变形量的最终冷轧,单道次轧制变形量为5%~10%。
41.冷轧后进行第二次时效处理,温度为270℃,时间为10h。
42.需要说明的是:上述所有的时效过程,其升温速度均为50~100℃/h范围内。
43.随后测量了合金中晶粒大小,并且测试所得的合金带材的织构体积分数、力学性能、折弯性能和热应力松弛性能。
44.测试标准:
45.室温拉伸试验按照《室温试验方法》在电子万能力学性能试验机上进行,试样采用比例系数为5.65的矩形横截面比例试样。下表1中给出的本发明实施例和对比例的带材屈服强度为平行轧制方向(rd方向)的屈服强度和延伸率。
46.延伸率各向异性系数δel的测试方法:分别沿偏离材料轧制方向(rd方向)0
°
、45
°
和90
°
方向上测定的断裂延伸率的值,通过以下公式计算δel值,其中δel=(el0‑
2el
45
el
90
)/2,el0、el
45
、el
90
分别为偏离带材轧制方向0
°
、45
°
和90
°
的断裂延伸率,δel表示合金的各向异性系数。
47.弯曲加工性能采用如下方法测定:将铜合金带材沿垂直于轧制方向(td方向)取长条样,试样宽度为10mm,随后采用90
°
、尖端具有不同半径的v形冲头对长条样进行折弯,然后采用体视显微镜观测折弯处外表面,以表面不产生裂纹的最小弯曲半径/板厚(r/t)来表示弯曲加工性能。当r/t值为0,表示最小弯曲半径r为0,弯曲加工性能最优异。
48.平均晶粒度按照《ys/t 347
‑
2004铜及铜合金平均晶粒度测定方法》的测试方法进行测定。
49.热应力松弛性能采用《astm e328
‑
2013 standard test methods for stress relaxationtests for materials and structures》进行测试,测试的条件为:暴露的温度为150℃,测试的时间为1000h。
50.采用ebsd分析实施例和对比例带材的织构类型及体积占比,各织构的体积分数取与标准角度偏离角度15
°
以内的织构。如图1所示,是利用ebsd进行测定且通过odf(取向分布函数)分析而得到的、铜合金板材的代表性的结晶取向分布图,利用轧制面内的双轴正交方向即与轧制方向平行的方向rd和轧制垂直方向td、以及轧制面的法线方向nd这3个方向的欧拉角来表示,即,将rd轴的取向旋转表示为将nd轴的取向旋转表示为将td轴的取向旋转表示为
51.参见表3,本发明实施例通过对各道工序的控制,织构的体积分数能控制到本发明要求范围:高斯织构的体积分数为5%~20%,黄铜织构的体积分数为10%~25%,s织构的
体积分数为5%~20%,铜型织构的体积分数为5%~15%,各织构取偏离标准角度15
°
以内的织构。0.5≤x1/x2≤1.5,其中x1为α取向线上高斯织构、黄铜织构的体积分数之和,x2为β取向线上黄铜织构、s织构和铜型织构的体积分数之和。参见表4,实施例具有优异的强度、弯曲加工性能、耐应力松弛性能及各向差异小的延伸率。
52.比较例1与实施例3的不同之处在于:钛含量为4.7wt%,检测结果显示平均晶粒大小为32μm,δel=3.21%,最终弯曲的最小弯曲半径r/t=2,与实施例3有所差距。
53.比较例2与本发明实施例的工艺不同之处在于:在750℃以下的热轧加工率为12%,没有预固溶处理工序。检测结果显示,其典型织构比例之比为0.44,屈服强度为891mpa,δel=2.53%,弯曲的最小弯曲半径r/t=1.5。
54.比较例3与本发明实施例的工艺不同之处在于:固溶温度较低,固溶温度为750℃s。结果显示,其晶粒大小为34μm,屈服强度为890mpa,δel=
‑
2.52%,弯曲加工性能r/t=0.5。
55.比较例4与本发明实施例的工艺不同之处在于:固溶处理与第一次时效处理之间设置冷变形30%,没有第二次时效处理。检测结果显示其应力松弛率为12%。
56.比较例5与本发明实施例的工艺不同之处在于:将最终冷变形量变化为40%。结果显示其弯曲加工性能恶化严重,为r/t=5。
57.表1本发明实施例和对比例的成分
58.59.表2本发明实施例和对比例关键工艺参数控制
[0060][0061]
表3本发明实施例和对比例的织构
[0062][0063]
表4本发明实施例和对比例的性能
[0064]
再多了解一些
本文用于企业家、创业者技术爱好者查询,结果仅供参考。