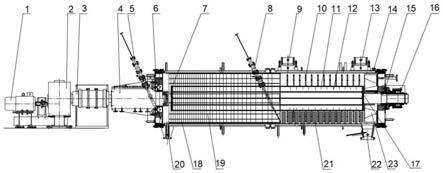
1.本发明涉及一种反应器及生产聚酯的方法,尤其涉及一种终缩聚反应器及生产聚酯的方法。
背景技术:
2.目前,pet熔融聚合反应器一般采用两种搅拌形式。
3.其一,80年代由德国吉玛公司改进而来的五釜流程技术,该技术终缩聚反应器采用实心轴圆盘搅拌,主要用于纤维级pet生产,特性粘度一般控制在0.690dl/g。此后该技术改进后,反应器最大产能已经能够做到30万吨/年。这种反应器的工作原理是将经过预缩聚处理的物料借助于设在反应器内部圆盘的旋转,使pet熔体粘附在圆盘表面,并在重力、设在筒体内壁刮板的作用下形成一定厚度的下垂膜,随着液膜不断下滑,反应器圆盘上内部不断产生新的界面,形成界面更新现象,使pet中脱出的乙二醇分子得以在界面、下垂膜处脱逸,使得分子链逐步增长,在圆盘转动和液面更替的作用下使缩聚反应不断地进行下去,获得聚对苯二甲酸乙二醇酯。但是由于常规终缩聚反应器所形成的液膜均垂直于圆盘的驱动轴,即仅在圆盘的平面内形成液膜,使得用于pet中乙二醇蒸发的熔体表面积小,而为了增加蒸发面积和气相流通面积,普遍采用的方法是增加筒体的体积,并在筒体内部增设多组圆环,但采用这种方法的终缩聚反应器存在有不能充分利用反应器内部空间、反应器体积过大,占用空间过大及成本过高等问题,无法满足特性粘度大于0.750dl/g的聚酯生产。
4.其二,90年代由美国杜邦公司改进而来的三釜流程技术,该技术终缩聚反应器采用空心轴笼框搅拌(鼠笼搅拌)。由于鼠笼式熔融缩聚反应器体积小、能耗低、效率高,在用于生产0.60dl/g的瓶级切片时优势较圆盘反应器明显,目前已在瓶片行业大规模应用。与圆盘反应器相比,鼠笼搅拌利用笼框之间的间隙形成液膜,成膜密度、效率远高于圆盘反应器,因此反应器的体积、重量可大幅减少。但与圆盘相比,在低粘段鼠笼成膜效率较差,预缩聚进入终缩聚反应器的熔体粘度一般在0.25-0.30dl/g之间,动力粘度较低,鼠笼无法有效成膜,一般设备厂商采用前密后疏的方式解决低粘段成膜效率低的问题,但鼠笼一般为空心轴设计,用于制备高粘聚酯0.75dl/g高粘熔体时,前后熔体动力粘度相差100倍以上,搅拌前后的桡度较大,极易将搅拌器损坏,类似拧麻花状破坏。目前现有的鼠笼/笼框搅拌器可生产的pet特性粘度最高为0.74dl/g,但此时反应器内部已有异响,无法长期稳定生产。
技术实现要素:
5.发明目的:本发明的第一个目的是提供一种脱挥效率高、避免熔体粘轴的生产高粘pet聚酯的终缩聚反应器;
6.本发明的第二个目的是提供一种生产聚酯的方法。
7.技术方案:本发明的终缩聚反应器,包括筒体、设置于筒体内的笼框搅拌器和圆盘搅拌器,其特征在于,所述笼框搅拌器包括第一花盘和笼框,所述圆盘搅拌器包括第二花盘和多组圆环,所述第一花盘和第二花盘在筒体内相对设置,所述第一花盘和第二花盘之间
连接有刚性支撑件,所述笼框和多组圆环分别固定于所述刚性支撑件上随刚性支撑件旋转,所述第一花盘和/或第二花盘连接有用于带动花盘旋转的驱动装置。
8.刚性支撑件一方面可以代替传统的旋转主轴来支撑笼框搅拌器和圆盘搅拌器旋转,提高笼框和圆盘搅拌器搅拌强度,减轻桡度;另一方面,刚性支撑件在旋转过程中会形成横向膜,能够强化反应器内熔体混合效果,有助于低粘段的脱挥、增粘。为了进一步增强搅拌和拉膜效果,刚性支撑件可以设置多个,多个所述刚性支撑件平行于筒体轴向设置,刚性支撑件的两端可以间隔分布于第一花盘和第二花盘上。所述刚性支撑件的横截面形状没有限制,可以为多边形或圆形。多边形刚性支撑件能够更容易将挂在反应器内壁的熔体刮下,防止长时间高温碳化。为了使支撑和拉膜均达到较优的效果,所述刚性支撑件的直径占筒体直径的0.25~0.5。
9.进入笼框搅拌器的聚酯熔体粘度较低,成膜效果偏弱,为了促进成膜效率,所述笼框的外缘设有用于刮取并倒出熔体的凹形槽,可使笼框在旋转过程中,一方面提升笼框搅拌器的强度,另一方面可将低粘熔体部分提升至搅拌轴旋转的最高点,并从最高点向下流淌,提高低粘熔体成膜效率。优选地,所述凹型槽在笼框的外缘上沿筒体轴向设置,凹型槽可间隔设置多个;优选地,所述凹形槽的深度为2-10cm,宽度1-8cm。
10.为了减小花盘的重量,从而减轻整个装置的重量,所述第一花盘设置于笼框内部。
11.所述圆盘搅拌器包括固定于所述刚性支撑件上的多组圆环,高粘度物料从圆环的大圆和小圆之间通过时,由于物料粘度大,物料在外圆环上会有较慢的流动速度,加上刮刀的作用,使物料在圆环上及圆环之间都能形成有效膜,并且成膜面积大,时间长,这样就有效提高了脱挥面积,达到了增粘效果。为了一方面对搅拌器起到增强支撑作用,另一方面对高粘聚酯熔体进行盘面成膜,提高粘度,所述刚性支撑件上位于圆环内侧固定有带孔圆盘,更进一步的,所述圆盘为多孔圆盘。
12.为了提高成膜效果,所述圆环的外圆直径占筒体直径的0.05~0.5,所述带孔圆盘的面积占筒体截面面积的0.05~0.25;所述带孔圆盘与圆环的数量比为1:1~10。
13.除了圆环、圆盘对聚酯熔体进行平行成膜外,刚性支撑件随着花盘转动会对高粘聚酯熔体开展横向成膜,一方面扰动高粘聚酯熔体使之混合均匀,另一方面横向拉膜协助高粘聚酯熔体脱挥。为了方便将高粘熔体从筒体壁上刮下往出料口输送,所述刚性支撑件上位于所述圆盘搅拌器后端固定有随刚性支撑件旋转的刮板;其中,刮板固定于刚性支撑件两侧,刮板可以为通过两根斜杆支撑的矩形框架。
14.为了避免熔体在筒体内壁挂壁,长时间加热会产生结焦,所述笼框搅拌器及圆盘搅拌器顶部分别与筒体内壁之间的间隙为5~20mm、2~10mm。
15.为了平衡笼框搅拌器和圆盘搅拌器之间增黏的效果,所述笼框和多组圆环在刚性支撑件上所占的长度比为1:0.2~5。
16.本发明还公开了利用上述终缩聚反应器生产聚酯的方法,包括以下步骤:将聚酯熔体送入所述终缩聚反应器反应,制备得到特性粘度为0.7~0.95dl/g的聚酯熔体。
17.目前含有鼠笼和圆盘搅拌器的终缩聚反应器均采用双轴双驱动,主要是因为搅拌器过长,单驱动时搅拌器前后端桡度过大,高粘制备时容易发生损坏。而由于本发明的笼框搅拌器和圆盘搅拌器共同固定于刚性支撑件上,且仅使用两个花盘连接,减少了花盘数量,由于花盘为实心,尤其是20万吨的大容量终缩聚反应器,花盘重量极高,因此花盘数量减少
可减少成本及装置重量。同时刚性支撑件、凹型槽、圆环和带孔圆盘组合有效提高了成膜脱挥效率,使得本发明所需的搅拌器长度也大幅减小,因此,本发明既可实现双轴驱动也可实现单轴驱动,即,可以仅在筒体一侧的花盘上连接有驱动装置而带动两个搅拌器同时旋转,也可以在两端的花盘上分别连接驱动装置来带动旋转。在单轴驱动的情况下,可以极大的降低成本,同时也能使整个装置持续稳定地运行。
18.有益效果:本发明与现有技术相比,能够取得下列有益效果:1、通过两花盘及刚性支撑件带动笼框和圆盘搅拌器旋转并进行横向拉膜,使得成膜脱挥效率高,且由于代替了传统的旋转主轴避免了熔体的粘轴;2、既能实现双轴驱动也能实现单轴驱动;3、凹型槽可使笼框在旋转过程中,一方面提升笼框搅拌器的强度,另一方面由于凹型槽具有一定的持液量,可将持有的低粘熔体提升至搅拌旋转的最高点,并从最高点向下流淌,提高低粘熔体成膜效率;4、带孔圆盘一方面对搅拌器起到增强支撑作用,另一方面对高粘聚酯熔体进行盘面成膜,提高粘度;5、所需搅拌器的长度大幅减小,有效避免了因搅拌器过长引起前后端桡度大而损坏搅拌器的问题;6、可以仅使用两个花盘,有效减轻了整个装置的重量,降低了成本。
附图说明
19.图1为本发明的结构示意图;
20.图2为本发明的花盘与刚性支撑件的截面示意图;
21.图3为本发明的笼框搅拌器截面示意图;
22.图4为本发明的圆环及带孔圆盘结构示意图;
23.图5为本发明的刮板结构示意图。
具体实施方式
24.下面结合说明书附图对本发明作进一步详细描述。
25.实施例1
26.如图1~2所示,本发明的终缩聚反应器,包括筒体,本实施例为密封的卧式筒体,筒体的一端设有物料进口20,另一端设有物料出口22;进料端为前端,出料端为后端。筒体为单轴驱动,也可以为双轴驱动。在筒体前端设置驱动装置,驱动装置可以为常规设计,具体包括搅拌电机1,与搅拌电机1依次连接的传动箱2、差速器3、传动轴4。筒体的前后端分别设有前端盖6、后端盖15,后端设有右轴封16。筒体内前端设有笼框搅拌器,后端设有圆盘搅拌器。笼框搅拌器的前端设有第一花盘7,圆盘搅拌器的后端设有第二花盘17,两个花盘相对平行设置,两花盘之间连接有刚性支撑件11,刚性支撑件11上位于筒体的前部分固定有笼框18,后部分固定有多组圆环10。笼框18和多组圆环10可以通过焊接的方式固定于刚性支撑件11上,也可以通过其他方式固定。第一花盘7设置于笼框18内部,能够大幅减小花盘的直径,从而减小花盘的重量,整个装置的重量随之减小。第一花盘7与转动轴4连接,刚性支撑件11随第一花盘7在驱动装置的驱动下带动笼框搅拌器和圆盘搅拌器旋转并进行拉膜。
27.筒体内在两花盘之间固定有多组平行于筒体轴向的刚性支撑件11,刚性支撑件11为具有一定强度的能够支撑两搅拌器旋转的加强件;刚性支撑件11的形状没有限制,截面
形状可以为圆形、多边形或其它形状,多边形刚性支撑件11能够更容易将挂在反应器内壁的熔体刮下,防止长时间高温碳化。为了使支撑和拉膜均达到较优的效果,刚性支撑件11的直径占筒体直径的0.25~0.5。
28.如图3所示,笼框18的外缘设有用于刮取并倒出熔体的凹形槽,可使笼框18在旋转过程中,一方面提升笼框搅拌器的强度,另一方面可将低粘熔体部分提升至搅拌轴旋转的最高点,并从最高点向下流淌,提高低粘熔体成膜效率。凹型槽19在笼框18的外缘上沿筒体轴向设置,凹型槽19可间隔设置多个,凹形槽的深度可以为2-10cm,宽度可以为1-8cm。
29.如图4所示,刚性支撑件11上位于圆环10内侧固定有带孔圆盘12,孔设置有多个,形成多孔圆盘;带孔圆盘12一方面对搅拌器起到了增强支撑作用,另一方面对高粘聚酯熔体进行盘面成膜,提高粘度,且带孔圆盘12能够确保高粘熔体顺利流下,提高脱挥效果。圆环10的外圆直径占筒体直径的0.05~0.5,带孔圆盘12的面积占筒体截面面积的0.05~0.25;带孔圆盘12与圆环10的数量比为1:1~10。圆环10和带孔圆盘12、刚性支撑件11的组合形式可实现设备制造的简易化:先制备好带孔圆盘12,在带孔圆盘12的外侧焊接刚性支撑件11,再在刚性支撑件11上焊接圆环10。由内向外制造,既提高了搅拌器的强度,也减缓了搅拌器在高粘熔体制备过程中脱焊、挂壁等问题。
30.如图5所示,刚性支撑件11上位于圆盘搅拌器后端固定有随刚性支撑件11旋转的刮板23,确保高粘熔体能够顺利进入出料口,减少高粘熔体在出料端的筒体内壁粘附。其中,刮板23固定于刚性支撑件11两侧,刮板23可以为通过两根斜杆支撑的矩形框架。多组圆环10之间增加带倾斜角的定刮刀21,提高成膜效果,倾斜角可以为15~75
°
。
31.笼框18及圆环10顶部分别与筒体内壁之间的间隙为5~20mm、2~10mm,能够有效避免熔体在筒体内壁挂壁,长时间加热会产生结焦。笼框18和多组圆环10在刚性支撑件11上所占的长度比为1:0.2~5,能够更好的平衡笼框搅拌器和圆盘搅拌器之间增黏的效果。
32.筒体前段、中间段分别采用前端鼓泡液位计5、中段鼓泡液位计8检测液位,后段高粘出料口处采用放射源液位计14检测液位。筒体中段、后段分别设有中段真空抽气口9、后段真空抽气口13。
33.利用终缩聚反应器进行高粘聚酯生产的方法:将特性粘度为0.15dl/g~0.40dl/g的聚酯熔体物料连续送入上述聚合反应釜,在温度265℃~290℃,绝对压力0pa~2000pa的条件下反应50min~150min,制备得到特性粘度为0.60dl/g~1.0dl/g、动力粘度为600~1200pa.s的聚酯熔体,聚酯熔体端羧基为5~40mol/t。
34.实施例2
35.利用上述终缩聚反应器生产聚酯的方法,包括以下步骤:
36.pet瓶级聚酯由对苯二甲酸、间苯二甲酸、乙二醇、磷酸为原料制得,其中间苯二甲酸占合成聚酯总重量的1.8%,对苯二甲酸占合成聚酯总重量的69.2%,乙二醇占合成聚酯总重量的29%,磷酸占聚酯总重量的10-50ppm。对苯二甲酸、间苯二甲酸、乙二醇、磷酸在经历打浆、酯化、预缩聚后,预缩聚熔体的特性粘度控制在0.15dl/g,动力粘度为0.45pa.s。
37.预缩聚熔体进入本发明反应器内,在反应温度265℃,绝对压力10pa的条件下反应100min。反应器笼框段与圆盘段的长度比例为1:0.2,低粘预缩聚熔体首先在笼框的作用下高效成膜,此时熔体内的乙二醇及缩聚产生的乙二醇含量均较高,在真空作用下熔体粘度快速升高。同时聚酯熔体粘度较低,成膜效果偏弱,笼框顶部与反应器壁最小间隙控制在
5mm,有助于搅拌器在旋转过程中将附着在反应器壁的熔体刮下,笼框段刚性支撑件直径占反应器直径的0.25。
38.聚酯熔体经过笼框段的高效成膜脱挥后,特性粘度增加到0.6dl/g附近,随着熔体动力粘度增加,熔体在笼框段的尾部成膜效果减弱,液膜厚度增加,缩聚生成的乙二醇等小分子不能有效挥发,缩聚反应推动力下降,聚酯熔体粘度增幅减慢。此时聚酯熔体开始进入圆盘段进行圆环、圆盘成膜脱挥。圆盘段采用多组空心圆环,圆环与反应器壁最小间隙控制在2mm,圆盘段刚性支撑件直径占反应器直径的0.25,内部设有多孔圆盘,多孔圆盘与空心圆环的数量比为1:1,多孔圆盘面积占反应器截面面积的0.05,空心圆环直径占反应器直径的0.05,由于圆盘段熔体粘度较高,转速过高会导致液膜来不成型,不利于小分子脱除,此外高转速对圆环的桡度及形状产生不利影响,尤其在与反应器壁精密配合的基础上易刮擦,整台反应器的搅拌转速一般设置在3rpm。
39.利用该终缩聚反应器及反应工艺,将低粘聚酯熔体液相增粘至0.7dl/g,动力粘度为600pa.s。
40.实施例3
41.与实施例2相比,预缩聚熔体的特性粘度控制在0.20dl/g,动力粘度0.85dl/g。预缩聚熔体进入反应器内,反应温度275℃,绝对压力100pa的条件下反应120min。反应器内部结构设计:笼框段与圆盘段的长度比例为1:0.5,笼框段凹型槽有8组,顶部与反应器壁最小间隙控制在10mm,笼框段刚性支撑件直径占反应器直径的0.3。圆盘段采用多组空心圆环与反应器壁最小间隙控制在5mm,圆盘段刚性支撑件直径占反应器直径的0.3,内部设有多孔圆盘,多孔圆盘与空心圆环的数量比为1:3,多孔圆盘面积占反应器截面面积的0.1,空心圆环直径占反应器直径的0.1。
42.利用该终缩聚反应器及反应工艺,将低粘聚酯熔体液相增粘至0.78dl/g,动力粘度为850pa.s。
43.实施例4
44.与实施例2相比,预缩聚熔体的特性粘度控制在0.30dl/g,动力粘度为7.55pa.s。预缩聚熔体进入反应器内,反应温度280℃,绝对压力250pa的条件下反应150min。反应器内部结构设计:搅拌笼框段与圆盘段的长度比例为1:2.5,笼框段凹型槽有10组,笼框段顶部与反应器壁最小间隙控制在15mm,笼框段刚性支撑件直径占反应器直径的0.4。圆盘段采用多组空心圆环与反应器壁最小间隙控制在8mm,圆盘段刚性支撑件直径占反应器直径的0.4,内部设有多孔圆盘,多孔圆盘与空心圆环的数量比为1:5,多孔圆盘面积占反应器截面面积的0.2,空心圆环直径占反应器直径的0.25。
45.利用该终缩聚反应器及反应工艺,将低粘聚酯熔体液相增粘至0.82dl/g,动力粘度为1350pa.s。
46.实施例5
47.与实施例2相比,预缩聚熔体的特性粘度控制在0.35dl/g,动力粘度为20.12pa.s。预缩聚熔体进入反应器内,反应温度285℃,绝对压力500pa的条件下反应150min。反应器内部结构设计:搅拌笼框段与圆盘段的长度比例为1:4,笼框段凹型槽有10组,笼框段顶部与反应器壁最小间隙控制在18mm,笼框段刚性支撑件直径占反应器直径的0.45。圆盘段采用多组空心圆环与反应器壁最小间隙控制在9mm,圆盘段刚性支撑件直径占反应器直径的
0.45,内部设有多孔圆盘,多孔圆盘与空心圆环的数量比为1:8,多孔圆盘面积占反应器截面面积的0.25,空心圆环直径占反应器直径的0.4。
48.利用该终缩聚反应器及反应工艺,将低粘瓶用聚酯熔体液相增粘至0.85dl/g,动力粘度为1545pa.s。
49.实施例6
50.与实施例2相比,预缩聚熔体的特性粘度控制在0.40dl/g,动力粘度为35.47pa.s。预缩聚熔体进入专利设计的聚合反应器内,反应温度290℃,绝对压力2000pa的条件下反应150min。反应器内部结构设计:搅拌笼框段与圆盘段的长度比例为1:5,笼框段凹型槽有12组,笼框段顶部与反应器壁最小间隙控制在20mm,笼框段刚性支撑件直径占反应器直径的0.5。圆盘段采用多组空心圆环与反应器壁最小间隙控制在10mm,圆盘段刚性支撑件直径占反应器直径的0.5,内部设有多孔圆盘,多孔圆盘与空心圆环的数量比为1:10,多孔圆盘面积占反应器截面面积的0.25,空心圆环直径占反应器直径的0.5。
51.利用该终缩聚反应器及反应工艺,将低粘瓶用聚酯熔体液相增粘至0.95dl/g,动力粘度为3500pa.s。
52.对比例1
53.pet瓶级聚酯由对苯二甲酸、间苯二甲酸、乙二醇、磷酸为原料制得,其中间苯二甲酸占合成聚酯总重量的1.8%,对苯二甲酸占合成聚酯总重量的69.2%,乙二醇占合成聚酯总重量的29%,磷酸占聚酯总重量的10-50ppm。对苯二甲酸、间苯二甲酸、乙二醇、磷酸在经历打浆、酯化、预缩聚后,预缩聚熔体的特性粘度控制在0.25dl/g,动力粘度为3.25pa.s。
54.预缩聚熔体进入常规笼框和圆盘反应器,反应温度285℃,绝对压力100pa的条件下反应100min。得到聚酯熔体粘度为0.65dl/g,动力粘度为385pa.s。
55.表1反应器结构参数对聚酯性能的影响
56.
再多了解一些
本文用于企业家、创业者技术爱好者查询,结果仅供参考。