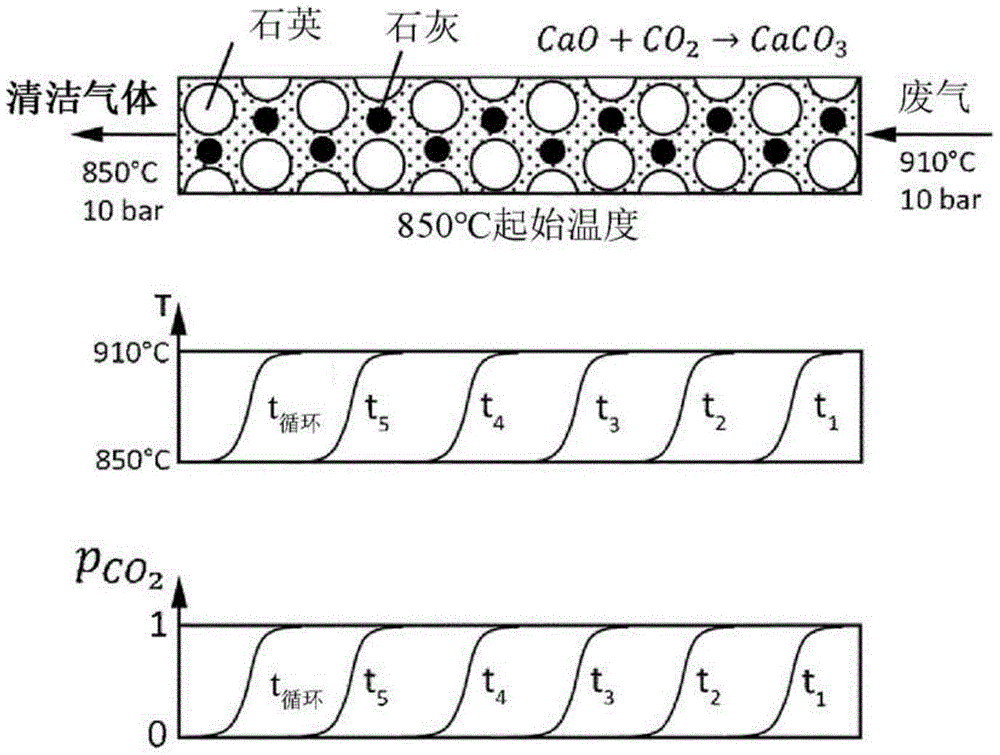
本发明涉及用于从废气分离二氧化碳并且在内部回收反应焓的一种固体反应器、一种系统和一种方法。
背景技术
为了防止气候变化,需要将因燃烧而产生的二氧化碳气体从燃烧产物分离出来或者重新利用。为此,在现有技术中描述过各种方法和装置。
在引导废气穿过石灰颗粒(CaO)的情况下,能够将二氧化碳从废气分离(钙循环)。在此情形下,二氧化碳根据CaO CO2->CaCO3反应形成石灰石(CaCO3)。需要根据CaCO3->CaO CO2将CO2从形成的石灰石重新排出。在迄今为止的方法中,通过以纯氧燃烧化石燃料来确保这一点。纯氧是必要的,否则CO2会再次被空气污染。以纯氧燃烧始终是高耗能的。此外会产生额外的二氧化碳。
举例而言,EP 2 644 256 A1描述过用于高效地将二氧化碳分离的一种方法和一种装置。其中,在不同的设备部分中实施煅烧和碳化,其中需要将相应的设备部分中所包含的固体交替地转移。此外,在WO 2005/046862 A1中描述过一种通过二氧化碳将由石灰石构成的吸收剂再活化的方法。此外,WO 2005/046863 A1描述过通过水化对由石灰石构成的吸收剂进行的预处理。现有技术中已知的方法非常耗能,故其具有显著的缺点。石灰石的再生循环的数目也相对较小。
技术实现要素:
有鉴于此,本发明的目的在于,提供一种固体反应器以及一种系统,所述系统克服现有技术的缺点并且实现二氧化碳从燃烧产物的高能效的分离。
本发明用以达成上述目的的解决方案为,提供一种根据本发明的主权利要求所述的固体反应器。本发明用以达成上述目的的另一解决方案为,提供一种系统,其包括至少一个本发明的根据主权利要求所述的固体反应器。本发明用以达成上述目的的另一解决方案为,提供一种根据并列主权利要求所述的方法。
本发明的主题是一种用于存储和释放二氧化碳的固体反应器,包括气密或流体密封的具有内腔的壳体,包括至少一个用于将流体、特别是含有二氧化碳的废气馈入的入口,并且包括至少一个用于将流体、特别是脱除了二氧化碳的气体排出的出口,其中所述壳体的内腔是被至少两个不同的固体填充,其中一个固体用于存储热能,且另一固体用于可逆地存储和释放二氧化碳。
根据本发明的固体反应器的一个优选方案,所述壳体还包括用于将所述固体送入或者移除的构件。
根据本发明的固体反应器的一个特别优选的方案,在气体或流体的入口区域内和出口区域内设有截止机构,其以一定方式构建,用以改变固体反应器的内腔中的压力,和/或用以将气体或流体导入固体反应器,和/或用以将从固体反应器流出的气体或流体导出。
根据本发明的固体反应器的一个特别优选的方案,所述用于存储和释放二氧化碳的固体是选自氧化钙和含有氧化钙的物质,选自石灰石和白云石或白云岩。根据本发明,视情况而定预先将待使用的固体燃烧,从而实现对二氧化碳的吸收。
根据固体反应器的一个特别优选的方案,所述用于存储热能的固体是选自惰性矿物材料,如石英、花岗石、二氧化硅、火成岩、碳化硅、氧化锆、金属相变材料、铸铁、灰铸铁,或者上述材料的混合物。
根据本发明的固体反应器的一个优选方案,所述至少两种不同的固体是以经包覆的固体的形式存在,由外壳与内芯构成,其中该内芯用于存储热能,并且该外壳用于可逆地存储和释放二氧化碳。
其中特别优选地,所述复盐是选自白云石、白云岩、白云质岩石、含有白云石或白云岩的岩石或者上述的混合物。
根据本发明的固体反应器的一个特别优选的方案,所述至少两个不同的固体是以复盐的形式存在,其中所述复盐的盐中的一种适于存储热能,并且复盐的另一种盐适于可逆地存储和释放二氧化碳。其中特别优选地,所述复盐是选自白云石、白云岩、白云质岩石、含有白云石或白云岩的岩石或者上述的混合物。
根据本发明的固体反应器的一个优选方案,所述至少两个不同的固体具有处于cm范围内的粒度。
根据固体反应器的另一优选方案,在所述固体反应器中送入的固体形成可通流的固定床。
本发明的另一主题是一种用于存储和释放二氧化碳的系统,包括至少一个固体反应器,包括至少一个用于将经所述固体反应器的入口送入的含有二氧化碳的流体或废气压缩的压缩器,其中所述压缩器是以一定方式构建,从而对借助固体反应器的出口从反应器送出的、脱除了二氧化碳的气体或流体进行绝热膨胀,并且包括至少一个逆流换热器,其适于实现经压缩的含有二氧化碳的流体或废气与脱除了二氧化碳的气体或流体的热交换。
根据本发明的系统的一个特别优选的方案,在所述入口的区域内设有至少一个针对经加热的流体的输入装置,用于在在逆流换热器中加热后以及在进入固体反应器的入口前,对含有二氧化碳的流体作进一步加热。
根据系统的另一优选方案,设有一或数个压缩器,其将空气和/或天然气和/或燃料油压缩和燃烧,并且通过输入装置将燃烧气体送入。
根据系统的另一优选方案,所述输入装置是可电加热,以及,输入的流体为氢气。
根据系统的一个特别优选的方案,还设有管道和截止机构,这些组件用于将固体反应器从系统断开,并且将固体反应器通过所述用于将气体或流体排出的出口与换热器流体连接。
根据系统的另一特别优选的方案,所述系统具有至少两个固体反应器,其中所述固体反应器是以一定方式与系统的构件气体连接或流体连接,使得各固体反应器适于相互独立地存储或者释放二氧化碳。
本发明的另一主题为存储和释放二氧化碳的方法,其中
a)提供至少一个用于存储和释放二氧化碳的固体反应器,
b)将含有二氧化碳的废气或流体送入所述固体反应器,其中以一定方式压缩废气或流体,使得二氧化碳的分压为1至2bar,
c)当固体反应器内部的温度为910至960℃时,终止该含有二氧化碳的废气或流体的送入,
d)在达到910℃至960℃的内部温度后,将固体反应器膨胀至0.1至0.5bar的压力,
e)持续地将因膨胀而再次释放的二氧化碳从固体反应器导出,直至固体反应器内部的温度为810至850℃,
f)将导出的二氧化碳压缩至常压并存储。
其中特别优选地,在步骤b)中,二氧化碳的分压高于1bar。
根据另一特别优选的方案,在步骤d)中,固体反应器内部的压力小于0.4bar,特别优选小于0.2bar。
根据另一特别优选的方案,在步骤c)中,固体反应器内部的温度高于910℃。
根据另一特别优选的方案,在步骤e)中,固体反应器内部的温度低于850℃。
根据方法的另一优选方案,在同一温度范围内并且在同一反应器中进行对二氧化碳的存储以及随后的释放。
根据方法的另一优选方案,在二氧化碳吸收过程中或在存储过程中释放的焓引起温升,并借此被存储在保持惰性的材料中。
根据方法的另一优选方案,在压力下降后,重新利用存储的热来释放二氧化碳。
附图说明
下面结合附图对本发明进行详细说明。其中:
图1为以环境压力下的反应范围进行的煅烧和碳化的平衡曲线peq;
图2为以在废气的过压并且二氧化碳气体的负压条件下的反应范围进行的煅烧和碳化的平衡曲线peq;
图3为在以基本温度曲线和分压曲线进行碳化的情况下,固体反应器的第一实施方式;
图4在煅烧的情况下,固体反应器的第一实施方式;
图5为在以基本温度曲线和分压曲线进行碳化的情况下,固体反应器的第二实施方式;
图6为在以基本温度曲线和分压曲线进行煅烧的情况下,固体反应器的第二实施方式;
图7为针对碳化和煅烧的设备示意图的第一实施方式;
图8为针对碳化和煅烧的设备示意图的第二实施方式;以及
图9为包含用于并行工作的固体反应器配置的设备示意图的局部视图。
具体实施方式
二氧化碳根据CaO CO2->CaCO3反应形成石灰石(CaCO3)。在图1中示出这个反应的平衡曲线。对于这个所谓的碳化反应而言,CO2的分压需要高于平衡压力。例如,如果废气中的分压为0.1bar,即为10vol%CO2,则石灰(CaO)的温度需要低于760℃。碳化反应是放热的。因此,释放的热仅可应用于其他在远低于760℃的温度下进行的过程。故热的使用是受限的。例如可以将热用于产生蒸汽,并且在此情形下借助涡轮机转化成电能。
需要根据CaCO3->CaO CO2将CO2从形成的石灰石重新排出。对于此所谓的煅烧而言,平衡压力需要高于分压。亦即,如果期望产生一个bar(环境压力)的纯净CO2,则颗粒的温度需要高于910℃,因为此温度为针对1bar的平衡压力的温度。煅烧是吸热的,即需要热,并且温度水平高于910℃。
借助本发明的方法和固体反应器,与目前现有的方法相比,能够以显著减小的能量将二氧化碳从燃烧气体分离。在全球范围内,在以化石燃料产生能量的过程中将二氧化碳从废气分离并且随后储存于地下或者应用于其他过程,被视作最大限度减缓全球变暖所不可或缺的手段。由于CO2分离的能量需求极低,反应器适于在全球范围内实施CO2封存。该反应器原则上可以建在所有发电站以及诸如水泥厂和石灰厂的工业厂房(占全世界CO2排放量的5%)后。
本发明的方法的目的在于,将在碳化过程中释放的反应焓直接重新应用在针对吸热煅烧的反应器中。因此,在反应器中设有对应的存储热的材料。放热反应焓与吸热反应焓的大小相同。这样一来,既无需针对碳化进行繁琐的废热利用,也无需针对煅烧进行高成本的能量生产。根据热力学第二定律,热仅能从较高的温度流动至较低的温度,亦即,仅需要在与吸热煅烧(CaCO3->CaO CO2)相比更高的温度水平上进行碳化(CaO CO2->CaCO3)即可。
本发明的主题具有下列特征和优点:
-无需对现有设备进行改造,例如就富氧燃烧而言。固体反应器包含白云石和/或石灰石或石灰颗粒,以及诸如砾石颗粒的能够存储热的惰性无机材料。已知类型的相变材料同样适用。白云石的优点在于,内部的菱镁矿组分便已可用作存储介质。
-为了根据CaO CO2->CaCO3(碳化)吸收二氧化碳,在过压下引导废气穿过固定床。借此提升这个碳化反应的温度水平。
-在负压下实施随后的煅烧(CaCO3->CaO CO2)。借此降低这个煅烧反应的温度水平。
-如图2所示,碳化过程中的废气的CO2分压必须高于煅烧过程中的CO2纯净气体的压力。
-借此在与吸热煅烧相比更高的温度水平下进行放热碳化。
-将在碳化过程中释放的热存储在惰性材料中,且随后可利用该热来进行煅烧。
在本发明的一个特别优选的实施方式中,在反应器中存在处于cm范围的块状石灰石或者白云质岩石。近表面区域吸收二氧化碳(在图5中作为以球形示出的岩石的深色环形区域标示出来)。将在吸收过程中释放的反应焓导入岩石内部,并借此使得岩石升温。这样便将反应焓作为潜焓存储。
以使得未反应的内芯的质量足以存储该反应焓的方式,选择岩石的尺寸。可以仅近表面区域具备吸收二氧化碳的能力,因为借此引起的体积增大使得由CaCO3构成的外壳变得致密,并且防止二氧化碳进一步扩散进入芯部。
优选将白云质岩石用作岩石。一方面,惰性MgO组分用作存储物质,另一方面,MgO组分防止CaO组分的烧结,使得能够实施许多循环,而不会发生所谓的石灰过烧。在预试验中实施了超过500个循环,未出现吸收能力减弱的情况。在迄今为止的采用处于μm范围的颗粒的方法中,在10个循环后,原始吸收能力便下降至约10%。
在针对煅烧而将压力降低后,通过存储的潜焓来覆盖吸热反应焓,并且岩石在此情形下重新冷却,如图6所示。
根据本发明的一个特别优选的方案,应用于反应器中的岩石具有处于cm范围的尺寸。借此确保,在为岩石装载二氧化碳并且从而使得岩石体积增大的过程中,气体或流体的通流不会受阻。岩石的这一尺寸也有助于增加循环数目,因为避免了烧结。岩石尺寸优选为0.5cm至10cm,特别优选为2cm至5cm。
下列实施例详细阐释本发明,而不对本发明的范围构成限制。
本发明的方法的基本理念在于,针对碳化将废气压缩,并且在负压下实施随后的煅烧。其中,在设置压力比时,需要使得碳化过程中的CO2分压高于煅烧过程中的CO2压力。结合图2阐释此原理。在本示例中,假定以使得CO2分压为1bar的方式来压缩废气。亦即,需要将包含10vol%CO2的废气压缩至10bar。在此,在0.2bar的绝对压力下实施煅烧。对应的平衡温度为910℃或810℃。于是可在810℃至910℃的温度范围内实施碳化,因为在此范围内,CO2分压总是大于平衡压力。在同一温度范围内同样可以也可以实施煅烧,因为满足为此所需的平衡压力大于CO2压力的条件(参阅图2)。
使用固体反应器来将热从碳化传递至煅烧。如图3所示,这个固体反应器由石灰颗粒和诸如石英颗粒的惰性固体颗粒构成。惰性颗粒用于存储在碳化过程中产生的热。视碳化与煅烧之间的温差而定,惰性颗粒与石灰颗粒的体积比为10至15。温差越小,需要的用于存储的惰性颗粒便越多。在如图3所示的示例中,假定固定床在煅烧后具有850℃的温度。如果具有例如1bar的CO2分压的、910℃的废气流入,则该气体冷却。在此情形下,分压高于平衡压力,故而可将CO2沉积在石灰颗粒上。基于反应热,固定床随时间的推移升温至910℃。在此示意性示出随时间推移而产生的分压及温度曲线。无法采用高于910℃的温度,因为在此情形下反应会停滞。可通过CO2分压调节反应器的最大温度。此分压越高,可能的最大温度便越高。
如果反应器经过装载并达到910℃,则将废气流导入另一经卸载的反应器(为此参阅图4)。在此情形下,将经装载的反应器中的压力降至0.4bar。平衡压力现高于分压,故发生反应性颗粒的煅烧。此操作类似于将水从潮湿的多孔体蒸发,此多孔体的温度高于周围水蒸气的饱和蒸汽温度。在蒸发期间,多孔体冷却,以应用蒸发焓。类似地,固定床冷却至850℃的平衡温度,以应用反应焓。产生的CO2流在惰性壳体与反应性颗粒之间传递热。如果CO2流不足以进行热传递,则可视情况而定使得CO2循环运动,用以增大反应器中的流量。在卸载后,重新对反应器进行装载。亦即,发生再生式焓交换。
在图5和图6中示出本发明的反应器的另一特别优选的实施方式。使用固体反应器来将热从碳化传递至煅烧。如图5所示,这个固体反应器由块状的石灰石和白云质岩石构成。惰性芯部用于存储在碳化过程中产生的热。视碳化与煅烧之间的温差而定,惰性芯部与反应性外壳的体积比为5至10。在如图5所示的示例中,假定固定床在煅烧后具有810℃的温度。如果具有例如1bar的CO2分压的、910℃的废气流入,则该气体冷却。在此情形下,分压高于平衡压力,故而可将CO2沉积。基于反应热,固定床随时间的推移升温至910℃。在此示意性示出随时间推移而产生的分压及温度曲线。无法采用高于910℃的温度,因为在此情形下反应会停滞。可通过CO2分压调节反应器的最大温度。此分压越高,可能的最大温度便越高。
如果反应器经过装载并达到910℃,则将废气流导入另一经卸载的反应器,如图6所示。在此情形下,将经装载的反应器中的压力降至例如0.2bar。平衡压力现高于分压,故发生反应性岩石的煅烧。此操作类似于将水从潮湿的多孔体蒸发,此多孔体的温度高于周围水蒸气的饱和蒸汽温度。在蒸发期间,多孔体冷却,以应用蒸发焓。类似地,固定床冷却至810℃的平衡温度,以应用反应焓。在卸载后,重新对反应器进行装载。亦即,发生再生式焓交换。
图7为整个过程的设备示意图100。为了更好地阐释过程,在本实施例中给出的温度基于以下示例:在1bar的CO2分压下实施碳化,并且在纯净CO2条件下在0.4bar下实施煅烧。所有温度均适用于绝热的、可逆的理想过程。废气13具有20℃的温度、1bar的环境压力和10%的CO2。为了进行碳化,需要10bar的压力和910℃。因此,首先将废气13压缩至10bar,其中温度提升至293℃。850℃的纯净气体从碳化器1流出。这个气体在逆流换热器6中将废气加热至约800℃。剩余的到910℃的加热需要天然气9。这个天然气流9为整个过程的主要能量需求。将在纯净气体的膨胀过程中释放的能量用于压缩。这样一来,在废气的压缩过程中仅需要相对较小的电能。850℃的二氧化碳流从煅烧过程流出。例如通过ORC 18利用这个热来发电。这个电流足以将二氧化碳流压缩至环境压力。
下面对在图7中示出的本发明的系统进行详细说明。将待脱除二氧化碳的流体、即废气通过废气入口13导入所述系统。借助压缩器7将废气压缩至CO2的对应分压,并且通过进入管线4导引废气穿过逆流换热器6。将借此被加热的废气通过入口3导入用于碳化的反应器1a。在反应器1a中将CO2作为碳酸钙加以结合,并且将CO2含量低的废气通过排出管线5重新导入逆流换热器6。借助膨胀装置8,将经净化的废气在常压下通过废气出口14放出。为了将含有二氧化碳的废气13加热至所需的910℃的反应温度,将诸如天然气的燃料通过入口9导入,在压缩器10中将燃料压缩至反应压力(在此为10bar),并且通过馈送管线12将燃料注入废气。燃料量是如此之小,以至于废气中的氧气便足以实现燃烧。通过燃烧,废气中的氧含量降低约1%至1.5%。为了实现稳定的燃烧,可借助压缩器10将空气11压缩,并且与天然气9一起燃烧。随后将燃烧气体通过气体输入管线12注入废气13。为了实现稳定的燃烧,可以替代性地将废气流的一部分改道。将天然气注入这个经改道的废气流。经改道的废气流的量是如此之大,使得温度上升至1200℃以上,在此温度下确保彻底燃烧。
如果固体反应器1处于CO2被卸载的状态1b下,则在固体反应器冷却期间,将结合在碳酸钙中的CO2通过出口2从固体反应器导出。在低压热交换器15中将CO2冷却,随后在压缩器16中调节至环境压力,并且在常压热交换器17中再次冷却。在ORC设备18(其也可以是汽轮机)中,将在热交换器15和17中导出的热转化成电能。将这个电流应用在针对压缩器的设备中。纯净的CO2在常温常压下通过出口19逸出。通过流体流的能量耦合实现高能效,使得仅需要将少量的能量从外部导入系统,便能实施碳化和煅烧的对应的反应过程。
图8示出本发明的系统的第二实施方式。图8为整个过程的设备示意图100。为了更好地阐释过程,在本实施例中给出的温度基于以下示例:在1bar的CO2分压下实施碳化,并且在纯净CO2条件下在0.2bar下实施煅烧。所有温度均适用于绝热的、可逆的理想过程。废气13具有20℃的温度、1bar的环境压力和10%的CO2。为了进行碳化,需要10bar的压力和910℃。因此,首先将废气13压缩至10bar,其中温度提升至293℃。810℃的纯净气体从碳化器1a流出。这个气体在逆流换热器6中将废气加热至约700℃。可通过加热元件将电能用于剩余的到910℃的加热,如果在废气中还含有氧气,可注入氢气并燃烧,或者可以注入燃烧气体。但后者会产生额外的二氧化碳。这个气流9为整个过程的主要能量需求。将在纯净气体的膨胀过程中释放的能量用于压缩。这样一来,在废气的压缩过程中仅需要相对较小的电流量。810℃的二氧化碳流从煅烧过程流出。可以利用这个热来发电,例如通过ORC 18来实现。
下面对在图8中示出的本发明的系统进行详细说明。将待脱除二氧化碳的流体、即废气通过废气入口13导入所述系统。借助压缩器7将废气压缩至CO2的对应分压,并且通过进入管线4导引废气穿过逆流换热器6。将借此被加热的废气通过入口3导入用于碳化的反应器1a。在反应器1a中将CO2作为碳酸钙加以结合,并且将CO2含量低的废气通过排出管线5重新导入逆流换热器6。借助膨胀装置8,将经净化的废气在常压下通过废气出口13放出。为了将含有二氧化碳的废气14加热至所需的910℃的反应温度,可以通过喷管21将氢气注入,可以使气体穿过电气加热盘管22流动,或者可以通过喷管12将热的燃烧气体注入。
如果固体反应器1处于CO2被卸载的状态1b下,则在固体反应器冷却期间,将结合在碳酸钙中的CO2通过出口2从固体反应器导出。在低压热交换器15中将CO2冷却,随后在压缩器16中调节至环境压力,并且在常压热交换器17中再次冷却。纯净的CO2在常温常压下通过出口19逸出。通过气流的能量耦合实现高能效,使得仅需要将少量的能量从外部导入系统,便能实施碳化和煅烧的对应的反应过程。
图9为本发明的系统的第一实施方式的局部视图。固体反应器1是相互平行布置,并且各自与入口3、排出管线5以及出口2流体连接,其中截止机构20是以一定方式布置,从而可以将这两个反应器中的每一个相互独立地针对碳化过程与管线3和5连接,或者针对煅烧过程与出口2连接。这样一来,可能处于不同工作状态下的各固体反应器1便能独立地工作。这表示,固体反应器中的一个处于装载CO2的状态1a下,而另一固体反应器则处于CO2被卸载的状态1b下。在本发明的其他实施方式中,可以设有更多的固体反应器1,其中,反应器中的每一个均可在状态1a或1b中的一个下工作(未示出)。根据本发明,也可以相应地布置更多的、数目依据本发明不受限制的固体反应器。
附图标记表
1 固体反应器
1a 处于装载CO2的状态下的固体反应器
1b 处于CO2被卸载的状态下的固体反应器
2 出口
3 入口
4 进入管线
5 排出管线
6 逆流换热器
7 针对废气的压缩器
8 针对纯净气体的膨胀装置
9 燃料气体输入装置
10 压缩器
11 空气输入装置
12 燃烧气体输入装置
13 废气入口或废气
14 废气出口(CO2含量低)
15 低压热交换器
16 针对CO2的压缩器
17 常压热交换器
18 用于发电的ORC设备
19 CO2出口
20 截止机构
21 氢气注入装置
22 电气加热装置
100 用于存储和释放二氧化碳的系统
本文用于企业家、创业者技术爱好者查询,结果仅供参考。