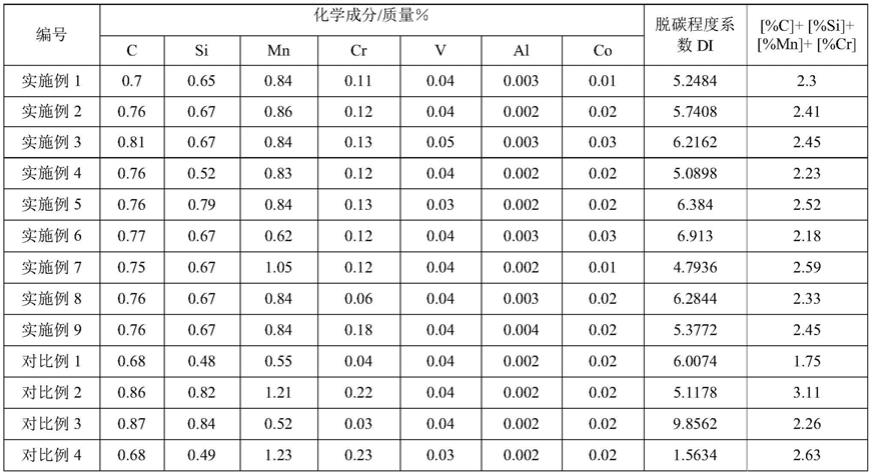
1.本发明涉及钢轨轧制技术领域,具体涉及一种降低高速铁路钢轨脱碳层厚度的方法。
背景技术:
2.钢轨作为铁路的走行部件,其质量的优劣、性能的高低严重制约着运输效率和行车安全,铁路运输速度的提升,对钢轨生产和品质提出了更高的要求。钢轨在制造过程中产生的脱碳现象不可避免,但钢轨表面产生脱碳层厚度直接影响着高速铁路轮轨关系匹配,导致接触应力变化,制约着行车安全,同时脱碳层厚度对钢轨的机械性能、表面硬度、耐磨性能等钢轨典型性能指标均产生影响。因此,降低高速铁路钢轨脱碳层厚度一直是各生产厂家和专家学者的研究热点之一。
3.钢轨脱碳是指钢轨铸坯在高温条件下,表层的碳原子由于热扩散的原理,从内部移至表面与加热炉内的氧化性气体发生作用,而导致钢表层一定范围内碳原子丢失的现象。钢轨脱碳从本质上说是加热过程钢中的碳元素与炉气中的氧、氧化物及水发生的化学反应,影响钢坯脱碳的因素很多,如氧化速度、钢坯的原始脱碳程度、钢种特性、加热温度、加热时间、加热炉内气氛、轧制速度及冷却工艺制度等,但在实际生产中,最主要的影响因素是钢轨钢种特性、加热炉温度、加热炉时间和加热炉内气氛。
4.目前,现有技术中为降低高速铁路钢轨脱碳层厚度,主要通过控制步进式加热炉内气氛、加热温度、加热时间以及化学成分配比,来控制钢坯表面的脱碳程度,从而达到降低钢轨脱碳层的控制目的。
5.从化学成分配比角度来讲,就脱碳层突出问题,现有技术还没有通过成分优化配比,以及控制各化学成分波动及其匹配关系的针对性实施方案。cn109023044b、发明名称为《控制重轨钢脱碳层深度的方法》的专利申请公开了在重轨钢成分中加入0.015wt%~0.025wt%的钛元素,并匹配合适的连铸控制工艺和加热工艺,从而达到降低钢轨脱碳层厚度的目的,但该专利申请仅通过添加适量的ti元素,未涉及c、si、mn、cr等主要化学元素及其含量。
6.从改善钢坯加热参数角度来讲,鲜有通过分段式精准控制时间和温度来降低钢轨脱碳层的研究报道。cn109266830a、发明名称为《一种控制高碳钢轨脱碳层深度的加热生产方法》的专利申请中公开了钢轨铸坯采用冷装工艺,加热过程包含预热段、加热段和均热段,预热段温度不高于900℃,加热段温度介于1050℃
‑
1180℃之间,均热段温度介于1130℃
‑
1180℃,实现碳含量在0.74%
‑
0.79wt%的高碳钢轨踏面脱碳层深度小于0.5mm。该专利申请仅涉及c含量范围、加热炉各段温度控制范围,尚未提及各加热段精准控制时间。
7.cn104878177a、发明名称为《一种能降低钢轨脱碳层深度的轧制工艺》的专利申请中公开了连铸坯加热采用步进式加热炉,其中预热段温度﹤900℃,加热段温度为1160℃~1260℃,均热段温度为1220℃~1250℃,热炉两侧热电偶温差≤30℃,加热时间为3.5~4.0h,将钢轨表面脱碳层深度控制在0.18~0.41mm之间。该专利仅涉及各加热段温度控制
区间及总时间,并未涉及成分匹配与加热温度、时间的协同控制脱碳方法。
8.cn102399959a、发明名称为《一种减小钢轨脱碳层厚度的方法》的专利申请中公开了依次对钢坯进行加热、开坯轧制和万能轧制的步骤,加热步骤将钢坯的温度加热至1220℃~1250℃的范围内,加热时间不大于7小时,并且在加热步骤中,在钢坯温度不大于800℃时,将空气过剩系数控制为1.10~1.15,在钢坯温度为800℃~1200℃时,将空气过剩系数控制为0.95~1.00,在钢坯温度不小于1200℃时,将空气过剩系数控制为0.90~0.95,将所述万能轧制步骤的压缩比控制为2.70~2.75,达到将钢轨的脱碳层厚度减小至0.50mm以下的目的。该专利申请仅涉及各加热段的控制温度和空气过剩系数,并未提到成分配比和各加热段的精准控制时间。
9.因此,现有技术中针对降低高速铁路钢轨脱碳层的方法主要集中在钢坯加热炉温度控制,并未涉及系统综合考虑对脱碳利害的主要化学成分、各加热段精准时间、温度控制以及各加热段空气过剩系数对高速铁路钢轨脱碳层的影响及控制技术。
技术实现要素:
10.针对现有技术的不足,本发明的目的在于提供一种降低钢轨脱碳层厚度的方法。
11.为了实现上述目的,本发明采用以下技术方案:
12.本发明提供了一种降低钢轨脱碳层厚度的方法,按照以下公式确定钢轨脱碳程度系数di:
13.di=(4.61[%c] 2.62[%si]
‑
2.25[%mn]
‑
3.78[%cr])/0.5
[0014]
式中:
[0015]
[%c]为钢轨中c元素的质量含量;
[0016]
[%si]为钢轨中si元素的质量含量;
[0017]
[%mn]为钢轨中mn元素的质量含量;
[0018]
[%cr]为钢轨中cr元素的质量含量;
[0019]
其中,脱碳程度系数di与[%c] [%si] [%mn] [%cr]的值之间满足预定的匹配关系。
[0020]
进一步地,所述预定的匹配关系为:脱碳程度系数di为4.5
‑
7.0,并且[%c] [%si] [%mn] [%cr]的值为1.85
‑
3.02质量%。
[0021]
进一步地,所述钢轨的化学成分为:
[0022]
c:0.70
‑
0.82质量%、si:0.50
‑
0.80质量%、mn:0.60
‑
1.20质量%、cr:0.05
‑
0.20质量%,以及,
[0023]
还包括v、al和co中的一种或几种,其中,v:0.01
‑
0.05质量%、al:0.003质量%以下、co:0.03质量%以下。
[0024]
进一步地,经连铸后对钢坯进行加热,依次经过预热段、加热段和均热段,其中,
[0025]
预热段时间为30
‑
80min,预热段温度为540
‑
800℃;加热段时间为120
‑
180min,加热段温度为990
‑
1200℃;均热段时间为10
‑
30min,均热段温度为1150
‑
1250℃。
[0026]
进一步地,在步进式加热炉中对钢坯进行加热。
[0027]
进一步地,预热段空气过剩系数为1.05
‑
1.20,加热段空气过剩系数为0.90
‑
1.05,均热段空气过剩系数为0.85
‑
1.00。
[0028]
进一步地,还包括将钢坯在线轧制成60
‑
75kg/m的钢轨。
[0029]
进一步地,还包括对钢轨进行在线热处理,在线热处理工序包括:
[0030]
将终轧后的有余热的钢轨空冷至820
‑
890℃,然后对钢轨轨头实施压缩气剂混合气冷却,当将钢轨轨头冷却至400
‑
560℃时,将钢轨空冷至室温。
[0031]
进一步地,钢轨轨头的冷却速率为1.0
‑
5.2℃/s。
[0032]
进一步地,在线热处理工序之后还包括后处理工序,所述后处理工序包括对钢轨依次进行矫直、探伤和加工。
[0033]
与现有技术相比,本发明的有益技术效果为:本发明通过对影响脱碳的c、si、mn、cr等主要化学元素的添加量进行优化,并且将[%c] [%si] [%mn] [%cr]的值与脱碳程度系数di进行匹配,建立各加热段精准化的温度时间控制,从而使钢轨脱碳层厚度显著降低,同时强韧性匹配和耐磨损性能得到提高,采用本发明生产的产品获得更加优异线路服役性能,更适用于高速铁路。
具体实施方式
[0034]
为使本发明的目的、技术方案和优点更加清楚明白,对本发明实施例进一步详细说明。
[0035]
本发明提供了一种降低钢轨脱碳层厚度的方法,按照以下公式确定钢轨脱碳程度系数di:
[0036]
di=(4.61[%c] 2.62[%si]
‑
2.25[%mn]
‑
3.78[%cr])/0.5
[0037]
式中:
[0038]
[%c]为钢轨中c元素的质量含量;
[0039]
[%si]为钢轨中si元素的质量含量;
[0040]
[%mn]为钢轨中mn元素的质量含量;
[0041]
[%cr]为钢轨中cr元素的质量含量;
[0042]
其中,脱碳程度系数di与[%c] [%si] [%mn] [%cr]的值之间满足预定的匹配关系。具体来讲,预定的匹配关系为:脱碳程度系数di为4.5
‑
7.0,并且[%c] [%si] [%mn] [%cr]的值为1.85
‑
3.02质量%。
[0043]
钢轨的化学成分对碳原子的扩散程度产生影响,从而钢的成分是影响其脱碳问题的决定性因素。脱碳由于钢坯表面碳原子与内部的碳原子形成浓度梯度,使碳原子不断地从钢坯内部向表面扩散,碳原子扩散速度取决于浓度梯度的大小和碳原子化学能大小。钢轨成分中的c元素对钢轨脱碳影响效果最为显著,一般c元素高时脱碳严重。si元素虽然不形成碳化物,但是它们能够提高了碳原子的活度,增大扩散系数d,同时,可使碳游离或石墨化的倾向,所以对脱碳起到了促进作用。mn和cr容易降低碳原子的活度,从而降低扩散系数,对脱碳起到抑制作用。所以上述元素对脱碳均存在影响,且存在影响效果不同的交互作用。
[0044]
di值表示钢轨脱碳严重程度,并可作为判断钢轨脱碳层厚度值高低的指标来应用,本发明中用于评价影响钢轨脱碳的化学元素良好匹配达到综合降低钢轨脱碳层厚度的指标来使用,优选维持在合适范围内。在本发明中,若脱碳程度系数di值大于7.0,则表示影响钢轨脱碳的主要元素未实现良好匹配,或者其中某一种或多种元素控制不佳,导致钢轨
脱碳严重,从而影响到钢轨的力学性能。若要使脱碳程度系数di值小于4.5,现有技术中的炼钢技术无法实现该成分的如此精准严格控制,难以应用于生产实践。因此,di为4.5
‑
7.0。
[0045]
在一优选实施例中,本发明的钢轨的化学成分为:c:0.70
‑
0.82质量%、si:0.50
‑
0.80质量%、mn:0.60
‑
1.20质量%、cr:0.05
‑
0.20质量%,以及,还包括v、al和co中的一种或几种,其中,v:0.01
‑
0.05质量%、al:0.003质量%以下、co:0.03质量%以下。其中,[%c] [%si] [%mn] [%cr]的值为1.85
‑
3.02质量%。
[0046]
当[%c] [%si] [%mn] [%cr]的值小于1.85质量%时,虽然可实现降低钢轨脱碳层厚度的目的,但钢轨力学性能降低,无法满足标准要求。当[%c] [%si] [%mn] [%cr]的值大于3.02质量%时,虽然钢轨力学性能得以保证,但未达到降低钢轨脱碳层厚度的目的。因此,优选[%c] [%si] [%mn] [%cr]的值为1.85
‑
3.02质量%。
[0047]
c是珠光体钢轨提高强硬度与耐磨损性能,促进珠光体转变最重要、最廉价的元素,对于应用于客货混运铁路或重载铁路的钢轨来说,在本发明条件下,当c含量<0.70质量%时,钢轨经热处理后强硬度较低,难以满足钢轨的磨耗需求;当c含量>0.82质量%时,经热处理后钢轨的强硬度过高;同时,还将析出晶界先共析渗碳体,恶化钢轨的韧塑性。因此,c含量限定为0.70
‑
0.82质量%。
[0048]
si作为钢中的固溶强化元素存在于铁素体和奥氏体中用以提高组织的强度。同时,可抑制先共析渗碳体析出,从而提高钢轨的韧塑性。在本发明条件下,当si含量<0.50质量%时,固溶量偏低导致强化效果不明显;当si含量>0.80质量%时,将损失钢轨的韧塑性特别是抵抗裂纹扩展性能。因此,si含量限定为0.50
‑
0.80质量%。
[0049]
mn可以和fe形成固溶体,提高铁素体和奥氏体的强度。同时,mn又是碳化物形成元素,进入渗碳体后可部分替代fe原子,增加碳化物的硬度,最终增加钢的硬度。在本发明条件下,当mn含量<0.60质量%时,强化效果甚微;当mn含量>1.20质量%时,钢中碳化物硬度过高,韧塑性明显降低;同时高mn易产生系列偏析问题,显著影响钢轨性能。因此,mn含量限定为0.60
‑
1.20质量%。
[0050]
cr能均匀钢中碳化物分布,减小碳化物尺寸,改善钢轨的耐磨损性能,cr含量限定为0.05
‑
0.20质量%。
[0051]
v在钢中能够形成细小、均匀、高度弥散的碳化物和氮化物颗粒,使钢轨耐磨性能提高,能够补偿因钢轨脱碳造成的磨损性能降低,同时晶粒细化能够抑制脱碳现象产生。若v元素含量小于0.01质量%,钢轨材料晶粒细化程度不高,对脱碳抑制低;若v元素含量大于0.05质量%,钢轨次表面硬度值不够。因此,v含量限定为0.01
‑
0.05质量%。
[0052]
al元素能够使钢轨脱碳倾向增大,同时易生成硬质夹杂,使钢轨力学性能降低。因此优选al含量为0.003质量%以下。
[0053]
co元素对钢轨脱碳的作用效果类似于al元素的作用效果,能够使钢轨脱碳倾向增大。因此优选co含量为0.03质量%以下。
[0054]
满足上述成分要求的铸坯经连铸后在步进式加热炉对钢坯进行加热,依次经过预热段、加热段和均热段。在一优选实施例中,预热段时间为30
‑
80min,预热段温度为540
‑
800℃;加热段时间为120
‑
180min,加热段温度为990
‑
1200℃;均热段时间为10
‑
30min,均热段温度为1150
‑
1250℃。
[0055]
在预热阶段,若预热段时间小于30min或预热段温度大于800℃时,则导致预热段
加热速率太大,钢坯心部热应力变大,将导致钢坯心部残余应力增大,甚至导致钢坯内裂;若预热段时间大于80min或预热段温度小于540℃时,将导致钢坯在预热段停留时间过长,延缓轧制速度,工业成本加大。因此,优选预热段时间为30
‑
80min、预热段温度为540
‑
800℃。
[0056]
在加热阶段,若加热段时间小于120min或加热段温度大于1200℃时,易导致钢坯表面和心部温差增大,热应力增大,存在烧裂风险;若加热段时间大于180min或加热段温度小于990℃时,则导致钢坯加热阶段停留时间过长,从而加大了加热阶段脱碳和钢坯表面过烧风险。因此,优选加热段时间为120
‑
180min、加热段温度为990
‑
1200℃。
[0057]
在均热阶段,若均热段时间小于10min或均热段温度大于1250℃时,易导致钢坯表面和心部组织不均匀,伴随出现钢坯表层晶粒粗大,心部未能完全奥氏体均匀化,降低了钢轨机械性能,同时在高温下增加了钢轨脱碳概率;若均热段时间大于30min或均热段温度小于1150℃时,既增加了钢轨脱碳概率,又容易引起高温力学性能降低,增加轧机负荷。因此,优选均热段时间为10
‑
30min、均热段温度为1150
‑
1250℃。
[0058]
在一优选实施例中,预热段空气过剩系数为1.05
‑
1.20,加热段空气过剩系数为0.90
‑
1.05,均热段空气过剩系数为0.85
‑
1.00。
[0059]
在满足上述加热工艺的同时,当预热段空气过剩系数小于1.05时,加热炉气体燃烧不充分,热效率降低,当预热段空气过剩系数大于1.20时,易加剧钢坯的氧化和脱碳,因此优选将预热段的空气过剩系数控制为1.05~1.20。
[0060]
在满足上述加热工艺,同时满足预热段空气过剩系数时,当加热段空气过剩系数小于0.90时,加热炉气体燃烧不充分,热效率降低,当加热段空气过剩系数大于1.05时,易加剧钢坯的氧化和脱碳,因此优选将加热段空气过剩系数控制为0.90~1.05。
[0061]
在满足上述加热工艺,同时满足预热段、加热段空气过剩系数时,当均热段空气过剩系数小于0.85时,加热炉气体燃烧不充分,热效率降低,当均热段空气过剩系数大于1.00时,易加剧钢坯的氧化和脱碳,因此优选将均热段空气过剩系数控制为0.85~1.00。
[0062]
钢坯在加热炉内加热完毕后,将钢坯在线轧制成60
‑
75kg/m钢轨。将满足上述要求的热轧钢轨进行在线热处理。在线热处理工序包括将终轧后的有余热的钢轨空冷至820
‑
890℃,然后对钢轨轨头实施压缩气剂混合气冷却,当将钢轨轨头加速冷却至400
‑
560℃后,钢轨轨头相变已完成,继续将钢轨空冷至室温,并经后续冷床、矫直、探伤、加工等后处理工序获得成品钢轨。本领域技术人员应当了解的是,后处理工序为本领域的常规操作。
[0063]
在本发明中,将钢轨轨头的冷却速率控制在1.0
‑
5.2℃/s,当冷却速度小于1.0℃/s时,钢轨踏面及以下部位(轮轨接触区域)难以形成细化的珠光体组织,在该过冷度下次表面温度难以传递出来,易产生片层较大的珠光体组织,当冷却速度大于5.2℃/s时,虽然能使钢轨次表面热量得以充分释放,组织得到显着细化,但在该过冷度范围内,在上述区域内极易产生马氏体或者贝氏体相变,造成组织异常风险。因此,钢轨轨头压缩气剂混合气冷速控制在1.0
‑
5.2℃/s之间。
[0064]
在下文中,将结合实施例来具体描述本发明的降低钢轨脱碳层厚度的方法。表1示出了本发明的实施例1
‑
9和相应的对比例1
‑
4的化学成分、脱碳程度系数di以及[%c] [%si] [%mn] [%cr]的值之间的匹配关系,其中,将钢轨成分组成的c的质量含量记为[%c],si的质量含量记为[%si],mn的质量含量记为[%mn],cr的质量含量记为[%cr],[%c]
[%si] [%mn] [%cr]表示c、si、mn和cr的质量含量之和。其中,实施例1
‑
9和相应的对比例1
‑
4选用表2中示出的加热工艺参数。
[0065]
表1实施例1
‑
9和对比例1
‑
4的化学成分、脱碳程度系数di以及[%c] [%si] [%mn] [%cr]的值之间的匹配关系
[0066][0067]
表2实施例1
‑
9和对比例1
‑
4采用的加热工艺参数
[0068][0069]
将实施例和对比例中得到的钢轨空冷至室温,在tb/t2344
‑
2012标准位置取轨头脱碳层试样,在标准位置取d0=10mm、l0=5d0圆形双肩拉伸试样,根据gb/t 228.1分别检测抗拉强度、屈服强度;并且对待测位置进行磨损试验取样。磨损试验要求:接触应力600mpa(赫兹应力),滑差10%,无润滑(干磨)环境下进行。本领域技术人员应当了解的是,上述测试过程为本领域的常规操作。实施例1
‑
9与对比例1
‑
4采用相同的测试部位与测试方法,结果详见表3。
[0070]
表3实施例1
‑
9和对比例1
‑
4的钢轨的性能参数
[0071][0072]
本发明选取了9种不同成分的试验钢种作为实施例,以及选取了4种不同成分的试验钢种作为对比例(表1所示)。其中实施例1
‑
9所采用的钢轨的化学成分、加热工艺参数均在本发明的钢轨的化学成分和加热工艺参数的范围之内,实施例1
‑
9的di值与[%c] [%si] [%mn] [%cr]的值满足预定的匹配关系,即脱碳程度系数di为4.5
‑
7.0,并且[%c] [%si] [%mn] [%cr]的值为1.85
‑
3.02质量%。对比例1
‑
4所采用的钢轨的化学成分在本发明的钢轨的化学成分的范围之外,对比例1
‑
4所采用的加热工艺参数在本发明的加热工艺参数的范围之内。数据对比结果表明,优化成分配比、di值与[%c] [%si] [%mn] [%cr]的值的匹配关系,加之适当的加热工艺参数对钢轨产品的轨头脱碳层厚度以及产品强韧化性能产生明显影响。
[0073]
如表1和表3的实施例1
‑
9所示,只有当di值与[%c] [%si] [%mn] [%cr]的值之间满足预定的匹配关系时,制得的钢轨轨头标准位置脱碳层厚度才会明显降低,并且远低于对比例;同等抗拉强度范围内,钢轨标准位置的屈服强度及综合强韧性更优;同等条件下具有更高的耐磨性能。
[0074]
当限定di值与[%c] [%si] [%mn] [%cr]的值满足预定的匹配关系时,即可确定c、si、mn、cr的质量含量的取值范围。由表1可知,对比例1
‑
4采用的c、si、mn、cr的质量含量在本发明的钢轨的化学成分的范围之外,即使对比例1
‑
2的di值满足预定范围(di在4.5
‑
7.0之间),但是,[%c] [%si] [%mn] [%cr]的值未满足预定范围(即,未在1.85
‑
3.02质量%之间);即使对比例3
‑
4的[%c] [%si] [%mn] [%cr]的值满足预定范围(即,在1.85
‑
3.02质量%之间),但是,其di值未满足预定范围(即,未在4.5
‑
7.0之间)。换句话说,对比例1
‑
4的脱碳程度系数di与[%c] [%si] [%mn] [%cr]的值之间未满足预定的匹配关系,因此,所制得的钢轨的脱碳层厚度较高、钢轨产品强韧性较差。
[0075]
结合表1和表3的数据,并且例如将实施例3与对比例3进行对比进行以下说明,虽然实施例3的钢轨的抗拉强度(1321mpa)与对比例3的钢轨的抗拉强度(1310mpa)差别不大,但是,实施例3的钢轨的屈服强度(912mpa)明显大于对比例3的钢轨的屈服强度(854mpa),即,实施例3的钢轨的强韧性整体优于对比例3的钢轨的强韧性。又例如将实施例1和对比例1进行比较,虽然实施例1的钢轨的脱碳层厚度(0.21mm)与对比例1的钢轨的脱碳层厚度
(0.24mm)差异不大,但对比例1的抗拉强度(1056mpa)和屈服强度(756)显著低于实施例1的抗拉强度(1256mpa)和屈服强度(901mpa)。基于上述分析,采用本发明的方法生产的钢轨轨头标准位置脱碳层厚度明显降低,远低于对比例;即使在具有类似的脱碳层厚度的情况下,本发明的钢轨相比于对比例的钢轨具有较好的抗拉强度和屈服强度。而且同等抗拉强度范围内,屈服强度更高,强韧性匹配更优;同等条件下具有更高的耐磨性能。
[0076]
本发明提供了一种降低高速铁路钢轨脱碳层厚度的方法,为了降低高速铁路钢轨脱碳层厚度,通过对影响脱碳的c、si、mn、cr等主要化学元素的添加量进行优化,并且将[%c] [%si] [%mn] [%cr]的值与脱碳程度系数di进行匹配,建立各加热段精准化的加热温度、加热时间、加热炉内空气过剩系数,从而使钢轨脱碳层厚度显著降低,同时强韧性匹配和耐磨损性能得到提高,采用本发明生产的产品获得更加优异线路服役性能,更适用于高速铁路。
[0077]
尽管已经详实介绍了本发明的降低高速铁路钢轨脱碳层厚度的方法的实施例,本发明上述实施例公开的顺序仅仅为了描述,不代表实施例的优劣。但是应当注意,以上任何实施例的讨论仅为示例性的,并非旨在暗示本发明实施例公开的范围(包括权利要求)被限于这些例子,在不背离权利要求限定的范围的前提下,可以进行多种改变和修改。根据这里描述的公开实施例的方法权利要求的功能、步骤和/或动作不需以任何特定顺序执行。此外,尽管本发明实施例公开的元素可以以个体形式描述或要求,但除非明确限制为单数,也可以理解为多个。
[0078]
所属领域的普通技术人员应当理解:以上任何实施例的讨论仅为示例性的,并非旨在暗示本发明实施例公开的范围(包括权利要求)被限于这些例子;在本发明实施例的思路下,以上实施例或者不同实施例中的技术特征之间也可以进行组合,并存在如上所述的本发明实施例的不同方面的许多其它变化,为了简明它们没有在细节中提供。因此,凡在本发明实施例的精神和原则之内,所做的任何省略、修改、等同替换、改进等,均应包括在本发明实施例的保护范围之内。
再多了解一些
本文用于企业家、创业者技术爱好者查询,结果仅供参考。