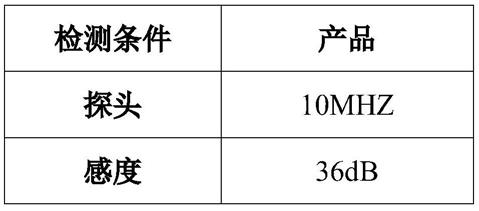
1.本发明属于半导体制造领域,涉及一种合金背板,尤其涉及一种无氧铜背板及其制备方法。
背景技术:
2.磁控溅射是物理气相沉积的一种,以溅射温度低、沉积速率高等特点而被广泛应用于半导体领域。溅射靶材主要由靶坯、背板等组成。其中,靶坯是高速离子束轰击的目标材料,属于溅射靶材的核心部分。在溅射镀膜过程中,靶坯被离子击中后,靶坯表面的原子被溅射并沉积在基板上,形成电子薄膜。由于金属溅射靶坯往往是高纯的铝、铜、钛、镍、钽及贵金属等比较贵重的材料,在磁控溅射镀膜过程中,靶坯同时承受背面的冷却水压力和正面的真空负压,所以在其制造时常常使用比较普通的材料作为背板。
3.靶材背板的选择尤其重要,通常选择铝和铜合金材料作为目标背板,主要是因为铝和铜合金材料具有较高的强度和良好的电导率、延展性、导热性。但是关于无氧铜背板的制备方法却鲜有报道。
4.cn102127721a公开了一种铝合金材料及铝合金背板的制备方法,所述铝合金材料按重量比组成为0.1%
‑
1%石墨烯,1%
‑
5%碳纳米管,其余为al;所述制备方法将铝合金原料放入加热炉中进行加热熔化,熔化后的铝合金材料进行压铸成型,形成铝合金背板。该制备方法能够提高原料的利用率,降低背板的制备成本,但其制备出的铝合金背板内部晶粒不够细化、均匀,使得制造出的背板材料不能满足半导体芯片的要求。
5.cn109804096a公开了一种高强度铝合金背板及制备方法,所述背板的溅射组件包括由铝材料形成的金属基体,分布在整个金属基体中的含钪的弥散体制备的铝合金,及分散在整个铝合金中的第二弥散体,所述第二弥散体由所述铝材料与氧化物、碳化物、富勒烯或纳米管中的任意一种组合形成。该方法制备出的背板在高温下稳定性高和屈服强度高,但其原料价格较高,对生产设备的要求很高。
6.综上所述,亟需开发一种无氧铜背板的制备方法,减少无氧铜背板内部缺陷,提升晶粒细化程度,进而可以制备得到内部结构均匀的无氧铜背板,且具有工艺简单、成本较低等优点,符合半导体、传感器等行业的质量要求。
技术实现要素:
7.为解决上述技术问题,本发明提供一种无氧铜背板及其制备方法,所述制备方法减少了无氧铜背板内部缺陷,提高了晶粒细化程度,保证了溅射过程稳定,溅射膜厚度分布均匀。
8.为达到上述技术效果,本发明采用以下技术方案:
9.本发明目的之一在于提供一种无氧铜背板的制备方法,所述制备方法包括:将坯料依次进行第一锻伸、第一热处理、压制、第二热处理和退火。
10.所述第一锻伸的预热温度为490
‑
510℃,例如可以是490℃、492℃、494℃、496℃、
498℃、500℃、502℃、504℃、506℃、508℃或510℃,但不仅限于所列举的数值,数值范围内其他未列举的数值同样适用。
11.本发明通过一次锻伸、两次热处理、压制与退火等一系列工序将坯料加工成高质量的无氧铜背板。本发明的锻伸处理使得原本粗大的晶粒破碎成细小晶粒,将无氧铜背板内部的疏松、气孔和夹渣等被压实和焊合,从而使得组织结构更为紧密,提高了内部晶粒细化程度,制备得到的无氧铜背板平面度达到0.2mm以下,无内部缺陷,其硬度和电导率达到应用要求。
12.作为本发明优选的技术方案,所述第一锻伸包括依次进行的预热、拔长和墩粗,其中拔长和墩粗交替重复进行至少2次,例如可以是2次、3次、4次或5次,但不仅限于所列举的数值,数值范围内其他未列举的数值同样适用。
13.优选地,所述拔长至坯料原长度的195
‑
205%,例如可以是195%、197%、199%、201%、203%或205%,但不仅限于所列举的数值,数值范围内其他未列举的数值同样适用。
14.优选地,所述墩粗至坯料原长度的45
‑
55%,例如可以是45%、47%、49%、51%、53%或55%,但不仅限于所列举的数值,数值范围内其他未列举的数值同样适用。
15.本发明中,所述第一锻伸以水冷的方式进行冷却。
16.作为本发明优选的技术方案,所述第一热处理的温度为345
‑
355℃,例如可以是345℃、347℃、349℃、351℃、353℃或355℃,但不仅限于所列举的数值,数值范围内其他未列举的数值同样适用。
17.优选地,所述第一热处理的时间为115
‑
125min,例如可以是115min、117min、119min、121min、123min或125min,但不仅限于所列举的数值,数值范围内其他未列举的数值同样适用。
18.本发明中,所述第一热处理以水冷的方式进行冷却。
19.作为本发明优选的技术方案,所述压制至第一锻伸后坯料长度的195
‑
205%,例如可以是195%、197%、199%、201%、203%或205%,但不仅限于所列举的数值,数值范围内其他未列举的数值同样适用。
20.作为本发明优选的技术方案,所述第二热处理的温度为445
‑
455℃,例如可以是445℃、447℃、449℃、451℃、453℃或455℃,但不仅限于所列举的数值,数值范围内其他未列举的数值同样适用。
21.优选地,所述第二热处理的时间为25
‑
35min,例如可以是25mm、27mm、29mm、31mm、33mm或35mm,但不仅限于所列举的数值,数值范围内其他未列举的数值同样适用。
22.本发明中,所述第二热处理以水冷的方式进行冷却。
23.作为本发明优选的技术方案,所述第二热处理与退火之间还包括依次进行的校平和粗加工。
24.优选地,所述校平后坯料的平面度≤0.5mm,例如可以是0.1mm、0.2mm、0.3mm、0.4mm或0.5mm,但不仅限于所列举的数值,数值范围内其他未列举的数值同样适用。
25.优选地,所述粗加工包括:将坯料全周进行车削至余量为0.5
‑
1mm,例如可以是0.5mm、0.6mm、0.7mm、0.8mm、0.9mm或1mm,但不仅限于所列举的数值,数值范围内其他未列举的数值同样适用。
26.本发明中,所述校平与粗加工之间还包括进行切除。
27.本发明中,所述切除包括:切除坯料四周开裂或有裂纹的边料。
28.本发明中,所述切除的边料长度为10
‑
15mm,例如可以是10mm、11mm、12mm、13mm或15mm,但不仅限于所列举的数值,数值范围内其他未列举的数值同样适用。
29.作为本发明优选的技术方案,所述退火的温度为445
‑
455℃,例如可以是445℃、447℃、449℃、451℃、453℃或455℃,但不仅限于所列举的数值,数值范围内其他未列举的数值同样适用。
30.优选地,所述退火的时间为295
‑
305min,例如可以是295mm、297mm、299mm、301mm、303mm或305mm,但不仅限于所列举的数值,数值范围内其他未列举的数值同样适用。
31.本发明中,所述退火以空冷的方式进行冷却。
32.作为本发明优选的技术方案,所述退火后还包括依次进行的整形和抛光。
33.优选地,所述整形后坯料的平面度≤0.2mm,例如可以是0.01mm、0.04mm、0.08mm、0.12mm、0.16mm或0.2mm,但不仅限于所列举的数值,数值范围内其他未列举的数值同样适用。
34.优选地,所述抛光后坯料的粗糙度为0.8
‑
1.6μm,例如可以是0.8μm、0.9μm、1μm、1.1μm、1.2μm、1.3μm、1.4μm、1.5μm或1.6μm,但不仅限于所列举的数值,数值范围内其他未列举的数值同样适用。
35.作为本发明优选的技术方案,所述制备方法包括以下步骤:
36.(1)第一锻伸:在490
‑
510℃下预热,拔长至坯料原长度的195
‑
205%,墩粗至坯料原长度的45
‑
55%,其中拔长和墩粗交替重复进行至少2次;
37.(2)第一热处理:在345
‑
355℃下热处理115
‑
125min;
38.(3)压制:压制至第一锻伸后坯料长度的195
‑
205%;
39.(4)第二热处理:在445
‑
455℃下热处理25
‑
35min;
40.(5)校平:将坯料校平至平面度≤0.5mm;
41.(6)粗加工:将坯料全周进行车削至余量为0.5
‑
1mm;
42.(7)退火:在445
‑
455℃下保温295
‑
305min;
43.(8)后处理:将坯料整形至平面度≤2mm,再抛光至粗糙度为0.8
‑
1.6μm。
44.本发明目的之二在于提供一种无氧铜背板,所述无氧铜背板采用如第一方面所述的制备方法制备得到。
45.与现有技术相比,本发明具有以下有益效果:
46.(1)本发明提供的制备方法通过一次锻伸、两次热处理、压制与退火等一系列工序将坯料加工成高质量的无氧铜背板。本发明的锻伸处理使得原本粗大的晶粒破碎成细小晶粒,将无氧铜背板内部的疏松、气孔和夹渣等被压实和焊合,从而使得内部组织结构更为紧密,提高了内部晶粒细化程度。
47.(2)本发明提供的制备方法得到无氧铜背板的平面度达到0.2mm以下,无内部缺陷,其硬度和电导率达到应用要求,制备方法操作简便,成本较低,适用性广。
具体实施方式
48.为便于理解本发明,本发明列举实施例如下。本领域技术人员应该明了,所述实施例仅仅是帮助理解本发明,不应视为对本发明的具体限制。
49.实施例1
50.本实施例提供一种无氧铜背板的制备方法,所述制备方法包括以下步骤:
51.(1)第一锻伸:在500℃下预热,拔长至坯料原长度的200%,墩粗至坯料原长度的50%,其中拔长和墩粗交替重复进行至少2次,之后进行水冷;
52.(2)第一热处理:在350℃下热处理120min,之后进行水冷;
53.(3)压制:压制至第一锻伸后坯料长度的200%;
54.(4)第二热处理:在450℃下热处理30min,之后进行水冷;
55.(5)校平:将坯料校平至平面度为0.3mm;
56.(6)粗加工:将坯料全周进行车削至余量为0.75mm;
57.(7)退火:在450℃下保温300min,之后进行空冷;
58.(8)后处理:将坯料整形至平面度为1mm,再抛光为1.2mm。
59.实施例2
60.本实施例提供一种无氧铜背板的制备方法,所述制备方法包括以下步骤:
61.(1)第一锻伸:在490℃下预热,拔长至坯料原长度的195%,墩粗至坯料厚度的45%,其中拔长和墩粗交替重复进行至少2次,之后进行水冷;
62.(2)第一热处理:在345℃下热处理125min,之后进行水冷;
63.(3)压制:压制至第一锻伸后坯料长度的195%;
64.(4)第二热处理:在445℃下热处理35min,之后进行水冷;
65.(5)校平:将坯料校平至平面度为0.1mm;
66.(6)粗加工:将坯料全周进行车削至余量为0.5mm;
67.(7)退火:在445℃下保温305min,之后进行空冷;
68.(8)后处理:将坯料整形至平面度为1mm,再抛光为0.8mm。
69.实施例3
70.本实施例提供一种无氧铜背板的制备方法,所述制备方法包括以下步骤:
71.(1)第一锻伸:在510℃下预热,拔长至坯料原长度的205%,墩粗至坯料原长度的55%,其中拔长和墩粗交替重复进行至少2次,之后进行水冷;
72.(2)第一热处理:在355℃下热处理115min,之后进行水冷;
73.(3)压制:压制至第一锻伸后坯料长度的205%;
74.(4)第二热处理:在455℃下热处理25min,之后进行水冷;
75.(5)校平:将坯料校平至平面度为0.5mm;
76.(6)粗加工:将坯料全周进行车削至余量为1mm;
77.(7)退火:在455℃下保温295min,之后进行空冷;
78.(8)后处理:将坯料整形至平面度为2mm,再抛光为1.6mm。
79.实施例4
80.本实施例提供一种无氧铜背板的制备方法,所述制备方法中除了将第一热处理与第二热处理的时间分别改为105min和20min,其余条件均与实施例1相同。
81.实施例5
82.本实施例提供一种无氧铜背板的制备方法,所述制备方法中除了将第一热处理与第二热处理的时间分别改为135min和40min,其余条件均与实施例1相同。
83.实施例6
84.本实施例提供一种无氧铜背板的制备方法,所述制备方法中除了将第一热处理的温度降为335℃,其余条件均与实施例1相同。
85.实施例7
86.本实施例提供一种无氧铜背板的制备方法,所述制备方法中除了将第二热处理的温度降为435℃,其余条件均与实施例1相同。
87.实施例8
88.本实施例提供一种无氧铜背板的制备方法,所述制备方法中除了将第一热处理的温度升为365℃,其余条件均与实施例1相同。
89.实施例9
90.本实施例提供一种无氧铜背板的制备方法,所述制备方法中除了将第二热处理的温度升为465℃,其余条件均与实施例1相同。
91.对比例1
92.本对比例提供一种无氧铜背板的制备方法,所述制备方法中除了将第一锻伸的温度降为480℃,其余条件均与实施例1相同。
93.对比例2
94.本对比例提供一种无氧铜背板的制备方法,所述制备方法中除了将第一锻伸的温度升为520℃,其余条件均与实施例1相同。
95.对比例3
96.本对比例提供一种无氧铜背板的制备方法,所述制备方法中除了不进行压制处理,其余条件均与实施例1相同。
97.对比例4
98.本对比例提供一种无氧铜背板的制备方法,所述制备方法中除了不进行退火处理,其余条件均与实施例1相同。
99.以上实施例和对比例的测试方法和结果如下:
100.晶粒尺寸:按照国标gb/t 6394
‑
2017《金属平均晶粒度测定方法》中公开的截面法进行测定。
101.实施例1
‑
9以及对比例1
‑
4使用的铝坯料的纯度为99.999%。钎焊方法为铟焊,具体为:铝靶与无氧铜背板实装良好,加热平台温度降低到200℃,设置炉子温度210℃,焊料槽铟焊焊料填充blank与bp表面浸润,焊料开始熔化温度:铟150℃~160℃。
102.靶材浸润:使用硅胶刮除表面焊料,焊接面已被银白色焊料均匀附着即可;背板浸润:超声波头划过的区域表面无气泡,且成银白色,焊料的流动性好。焊接后随炉冷却。焊接后确保焊接位置无焊料溢出即可。
103.采用c
‑
scan检测验证实施例1
‑
9以及对比例1
‑
4提供的无氧铜背板与铝靶的焊接效果,其检测条件如表1所示,结果如表2所示。
104.表1
[0105][0106][0107]
表2
[0108][0109][0110]
由表2可以得出以下几点:
[0111]
(1)本发明提供的制备方法,可以有效地控制无氧铜背板的晶粒尺寸,无氧铜背板的晶粒尺寸≤22μm,满足集成电路工艺对于晶粒尺寸的要求,保证了溅射过程稳定,溅射膜厚度分布均匀。
[0112]
(2)将实施例1和实施例6
‑
9进行对比,由于实施例6
‑
9的热处理温度范围选择不合理,导致所得无氧铜背板的晶粒尺寸变大,整体结合率较差,出现内部缺陷。
[0113]
(3)将实施例1和对比例1、2进行对比,由于对比例1、2的锻伸处理温度范围选择不合理,导致所得无氧铜背板的晶粒尺寸≥24μm,整体结合率差,甚至出现内部缺陷。
[0114]
(4)将实施例1和对比例3、4进行对比,由于对比例3没有进行压制处理和对比例4没有进行退火处理,导致所得无氧铜背板的晶粒尺寸过大,整体结合率差,甚至出现内部缺陷。
[0115]
申请人声明,以上所述仅为本发明的具体实施方式,但本发明的保护范围并不局限于此,所属技术领域的技术人员应该明了,任何属于本技术领域的技术人员在本发明揭露的技术范围内,可轻易想到的变化或替换,均落在本发明的保护范围和公开范围之内。
再多了解一些
本文用于企业家、创业者技术爱好者查询,结果仅供参考。