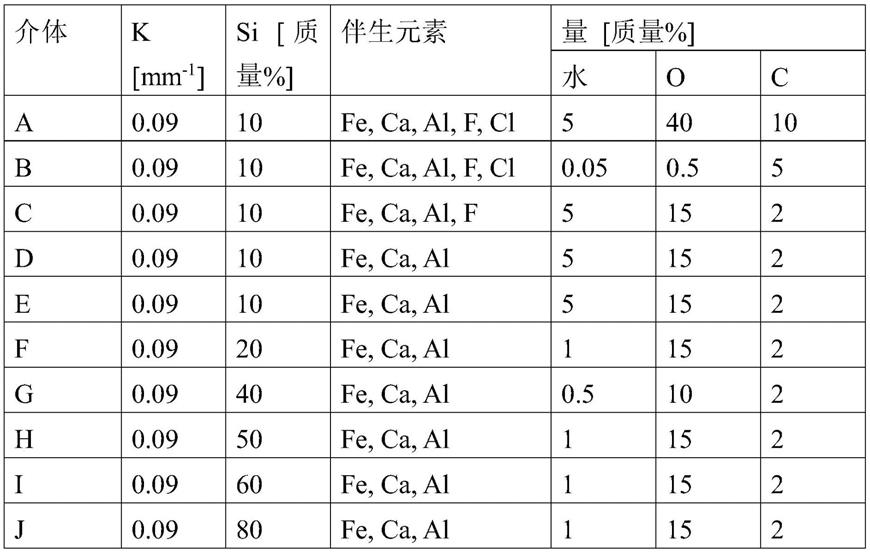
使用颗粒介体精炼粗硅熔体的方法
1.本发明涉及一种在工业硅的生产中氧化精炼粗熔融硅的方法,其中所述粗熔融硅与包含金属硅的颗粒介体(particulate mediator)混合。
2.目前工业级硅(工业硅)的主要应用是用于硅热操作中,金属提取中,以及作为炼钢中的脱氧剂,其中硅用作铝、铜、钛和铁的铸造合金的合金成分,也用作化学化合物的原材料。
3.工业级硅在工业上是通过石英(sio2;任选地进一步添加,例如含铁废料[硅铁]或碳化钙[硅钙])在电炉(电弧还原炉)中在高温(约2000℃)和大气压力下根据净反应方程式(1)进行碳热还原而生产的。该工艺全面描述在标准作业“高硅合金的生产”(a.schei,j.k.tuset,h.tveit,production of high silicon alloys,1998,tapir forlag,trondheim)中。
[0004]
sio2 2c
→
si(l) 2co(g)
ꢀꢀꢀꢀ
(1)
[0005]
在操作期间,反应物、中间体和产物以各种物质状态存在:固态(c,sic,sio2,si),液态(si,sio2)和气态(主要为co,sio)。所使用的碳源通常是由焦炭、石油焦炭、烟煤、木炭和木材颗粒组成的还原混合物。在炉子中占主导的气氛是强还原气氛,尤其是由sio和co组成的。在操作过程中,sio2和c向下移动,而sio和co向上流动。根据以下方程式(2)
‑
(7)形成中间物质:
[0006]
sio2 c
→
sio co
ꢀꢀꢀꢀꢀꢀꢀꢀꢀꢀ
(2)
[0007]
sio 2c
→
sic co
ꢀꢀꢀꢀꢀꢀꢀꢀꢀꢀ
(3)
[0008]
sio2 2sic
→
3si 2co
ꢀꢀꢀꢀꢀꢀ
(4)
[0009]
2sio2 sic
→
3sio co
ꢀꢀꢀꢀꢀꢀ
(5)
[0010]
sio2 co
→
sio co2ꢀꢀꢀꢀꢀꢀꢀꢀ
(6)
[0011]
2co2 sic
→
sio 3co
ꢀꢀꢀꢀꢀꢀ
(7)
[0012]
硅主要通过反应(8)中所示的反应形成。
[0013]
sio sic
→
2si co
ꢀꢀꢀ
(8)
[0014]
这种高温操作需要极其连续的状态。原材料和液态粗硅也分别间歇地投入和排出。排出通常通过将炉子排出并随后将液态粗硅(在约1600至1900℃的温度下)转移到处理容器中来完成。
[0015]
关键因素是所生产的产品的质量,以及工业操作的经济方面(例如生产率和生产成本)。当冶金硅用于生产化学化合物例如氯硅烷时,经过多个操作步骤,硅中所含的杂质(例如以挥发性氯化物形式存在的硼)部分地——尽管经过了中间纯化阶段——被带入到各自的最终产品中(例如,多晶硅、硅酮)。然而,根据应用的领域,这些最终产品必须满足非常严格的质量要求(半导体/制药/食品/化妆品行业)。因此,对于以工业规模生产这些产品,高质量的原材料——冶金硅——是很重要的。
[0016]
通常用于sio2的碳热还原的原材料和电极含有各种杂质。液态粗硅通常在上述处理容器中进行氧化精炼,因为此时粗产物中仍存在高达5质量%的杂质。在该领域,通常通过用反应性气体混合物(例如cl2、o2、sicl4、湿h2和co2或它们的组合,通常用惰性气体稀释)
处理并添加成渣添加剂(例如,硅砂、石灰石、生石灰、白云石、萤石等)来精炼粗硅,对于次量元素在硅相和渣相之间建立分配平衡。在精炼过程中,精炼混合物的温度从约1900℃下降到约1500℃。为了防止混合物凝固,如上所述,向其供应在操作条件下呈气态的试剂。例如,加入氧气导致硅氧化成二氧化硅,释放的能量使处理容器内的混合物保持液态。术语“氧化精炼”包括加入含氧的气体混合物和添加一种或多种造渣剂的组合。
[0017]
当氧化精炼结束时,通常仍为液态混合物的硅相和渣相被分离。
[0018]
传统氧化精炼方法的主要缺点是硅通过炉渣以二氧化硅或金属硅的形式存在于炉渣中而损失掉,并且还不能有效去除不需要的次量元素。这降低了硅生产的经济可行性和相应产品的质量。
[0019]
本发明的目的是提高工业硅生产的经济可行性,以及去除不需要的次量元素的效率,从而提高产品的质量。
[0020]
本发明提供一种在工业硅的生产中氧化精炼粗熔融硅的方法,其中粗熔融硅在精炼过程中与颗粒介体混合,所述颗粒介体包含最小量为8质量%的金属硅以及包含元素h、c、o、f、cl、ca、fe和al中的至少一种或多种,所述介体由特征数k描述,该特征数k的值为0.03至6mm
‑1,并且通过下式计算:
[0021][0022]
其中
[0023]
d
50,m
是介体级配曲线的筛下质量的50%处的粒径(直径)d
50,med
[mm],以及
[0024]
ε
m,m
是颗粒介体的平均有效孔隙率。
[0025]
出人意料地发现,在粗熔融硅精炼过程中添加特征数k为0.03至6mm
‑1的颗粒介体能够提高工业硅生产的生产率以及工业硅的质量。其原因首先是通过硅和炉渣之间更有效的相分离来减少硅损失,其次是更有效地去除不需要的伴生元素。前者因此导致工业硅的更高产率并且因此导致用于生产工业硅的更低的比能耗。本发明的方法的另一个优点在于在循环经济的背景下利用和/或回收副产物和废料的可能性。
[0026]
优选通过在电炉中用煤对石英进行碳热还原来生产粗熔融硅。
[0027]
粗熔融硅的氧化精炼优选通过用反应性气体混合物处理来完成,所述反应性气体混合物优选包含选自cl2、o2、sicl4、湿h2和co2及其组合的化合物。反应性气体混合物优选用选自氮气和氩气及其组合的惰性气体稀释。
[0028]
基于工业硅的总重量,工业硅具有<99.9质量%的si含量。伴生元素通常选自fe、ca、al、ti、cu、mn、cr、v、ni、mg、co、w、mo、as、sb、bi、s、se、te、zr、ge、sn、pb、zn、cd、sr、ba、y、b、c、p和o。
[0029]
si含量如下确定:100质量%减去伴生元素的重量分数。
[0030]
在该方法中精炼的工业硅的重要品种是具有55
‑
65质量%的si和35
‑
45质量%的ca的硅钙(二硅化钙,casi2)、具有45
‑
90质量%的si和10
‑
55质量%的fe的硅铁和具有98
‑
99.5质量%的si的冶金硅。
[0031]
所生产的工业硅优选具有至少90质量%,更优选至少95质量%,更特别是至少97质量%的si含量。
[0032]
在粗熔融硅的氧化精炼中,将介体添加到粗熔融硅中以补充或代替常规的成渣添
加剂。成渣添加剂优选选自硅砂、石灰石、生石灰、白云石和萤石。
[0033]
在一个优选的实施方案中,介体中活性碳的重量分数,基于介体的总质量为至多0.1,优选至多0.08,更优选至多0.06,更特别是至多0.04。在本发明中,“活性碳”旨在指介体中的与o2反应至高达1100℃的温度并发生热氧化降解的碳部分。活性碳通常包括有机化合物(例如油、脂肪、聚合物)中的碳以及无机化合物(例如碳酸盐、碳化物)中的碳和同素异形体的元素碳。
[0034]
根据一个优选实施方案,介体的水含量不超过5质量%,优选不超过3质量%,更优选不超过1质量%,更特别是不超过1000ppmw。根据一个优选实施方案,介体的氧重量分数不超过0.4,优选不超过0.3,更优选不超过0.2,更特别不超过0.15,但至少为0.01。
[0035]
介体中金属硅的最小量优选为10质量%,更优选至少20质量%,非常优选至少30质量%,更特别地至少40质量%。
[0036]
介体优选包含硅残留物,所述硅残留物优选选自来自硅生产或硅加工工业的副产物或废料,实例为:
[0037]
‑
在硅,例如多晶硅、多晶体硅或单晶硅的生产或机械加工中产生的硅残留物,尤其是与破碎、研磨和/或锯切相关的机械加工;
[0038]
‑
在生产颗粒状金属硅时产生的硅残留物,例如在流化床、离心、气体雾化和水粒化过程中;
[0039]
‑
通过碳热还原sio2生产工业级硅中产生的硅残留物;
[0040]
‑
在机械加工和任选的一种或多种工业硅分级过程中产生的硅残留物。机械加工可以更具体地涉及粉碎和/或研磨。典型的分级过程的实例是筛分和/或筛选;
[0041]
‑
硅烷生产中产生的硅残留物。这些可以是例如在回收cu之前和/或之后来自氯硅烷反应器的中和催化剂材料;更具体地说,来自m
ü
ller
‑
rochow直接合成操作、氢氯化或硅烷的低温转化。
[0042]
在这些硅残留物用于根据本发明的介体中之前,它们的纯化通常不是必需的。
[0043]
介体优选包含至少10质量%的硅残留物,更优选至少20质量%,非常优选至少30质量%,更特别是至少50质量%的硅残留物。
[0044]
介体优选经受粉碎(例如研磨、压碎)、分级(例如筛分、筛选)和/或附聚(例如造粒、压块、烧结)的过程以获得特征数k的期望值。
[0045]
为了确定特征数k的具体限定值,优选将介体附聚(例如通过造粒、压块和/或烧结)并干燥。
[0046]
与金属硅一起存在于介体中的元素可以采用这些元素的化合物或合金的形式。
[0047]
除了已经描述的元素之外,颗粒介体还可以包括以下伴生元素:si、li、na、k、mg、ca、ba、ti、zr、v、cr、mo、w、mn、fe、co、ni、cu、zn、b、sn、pb、n、p、as、sb、bi、s。
[0048]
添加介体时,质量(介体)与质量(粗熔融硅)的质量比优选为0.01至0.5,更优选为0.02至0.25,非常优选为0.03至0.15,更特别为0.04至0.1。
[0049]
d
50,m
优选为1至100mm,更优选为10至75mm,非常优选为15至50mm,更特别为20至30mm。
[0050]
颗粒介体优选具有0至0.6的平均有效孔隙率,更优选0.05至0.4,非常优选0.1至0.35,更特别是0.15至0.3的平均有效孔隙率。
[0051]
当氧化精炼结束时,通常仍为液态混合物的工业硅和矿渣相被分离,并且液态工业硅在冷却的表面或在冷却的介质中凝固。这可以通过例如倾析混合物、将漂浮的工业硅相倒入槽中并凝固所述槽中的工业硅来实现。
[0052]
液态工业硅可以进一步优选地特别用元素掺杂或合金化。例如,如果要生产的工业硅旨在用于合成氯硅烷,这可能是合适的。这涉及来自包含al、cu、sn、zn、o和p的组中的一种或多种元素,或这些元素的化合物或两种或更多种化合物,或这些元素和化合物的混合物。
[0053]
介体的硅含量例如可以通过x射线荧光分析(xfa)、基于icp的分析方法(icp
‑
ms、icp
‑
oes)或原子吸收光谱(aas)来确定。
[0054]
对于粒径主要>0.1mm的颗粒物质的混合物,通常进行筛分分析以表征颗粒混合物。根据din 66165,通过筛分分析确定粒径分布。可以根据din iso 9276
‑
2从粒径分布计算平均粒径/直径。
[0055]
物质的总孔隙率由相互连通以及与周围环境连通的空隙(开孔孔隙率;在本发明中:有效空隙率)和相互不连通的空隙(闭孔空隙率)的总和组成。依据阿基米德原理,根据astm c373
‑
88进行孔隙率测量。材料的孔隙率也可以通过绝对密度和表观密度的计算来完成。可以通过使用气体比重瓶,通过重量测量和体积测量来确定绝对密度和表观密度。din 66137
‑
2:2019
‑
03中描述了固体密度的测定。
[0056]
优选使用多相分析仪,例如leco rc
‑
612(也参见din 19539)来确定介体中的“活性碳”的量和水含量。
实施例
[0057]
下面描述的实验是在环境空气和室温(20℃)下进行的。
[0058]
来自冶金硅的连续生产过程的液态粗硅被收集在处理容器中,然后在100分钟的时间内,在加入不同的介体下进行氧化精炼(精炼气体:氧气/空气混合物[基于气体混合物的总体积,氧气含量为30体积%];混合物的体积流速:每吨液态粗硅16nm3/h),将硅相倒入到槽中并最终凝固。在冷却至室温并从槽中机械移除硅后,确定每吨硅产品的比能耗和硅产品的纯度。实验对比传统工艺进行了分析:每吨硅产品的比能耗通常为13.0mwh/t,硅产品的纯度约为98.5%。表1和表3提供了所用介体的概况——实验结果总结在表2和表4中。
[0059]
表1
[0060][0061]
表2
[0062][0063]
表3
[0064][0065]
表4
[0066][0067]
实施例表明,在本发明中在冶金硅的生产中使用介体在经济上是有利的。
再多了解一些
本文用于企业家、创业者技术爱好者查询,结果仅供参考。