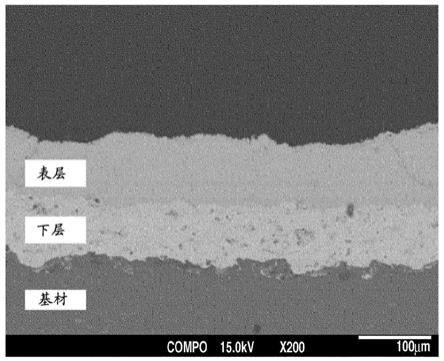
喷涂涂层、制造喷涂涂层的方法、喷涂的部件及喷涂材料
1.本技术是申请日为2019年8月14日,题为“喷涂涂层、制造喷涂涂层的方法、喷涂的部件及喷涂材料”的中国专利申请201910748398.x的分案申请。
2.相关申请的交叉引用
3.本非临时申请根据35u.s.c.
§
119(a)要求2018年8月15日在日本提交的专利申请no.2018
‑
152883的优先权,其全部内容以引用方式并入本文中。
技术领域
4.本发明涉及适用于诸如在半导体制造工艺的静电吸盘或等离子蚀刻装置中的零件或部件上形成的耐腐蚀性涂层的喷涂涂层。本发明还涉及制造该喷涂涂层的方法、形成有该喷涂涂层的喷涂的部件以及适于形成该喷涂涂层的喷涂材料。
背景技术:
5.根据材料之间的不同,用于半导体制造装置中的下部电极的静电吸盘一般分为库仑力型(coulomb force type)静电吸盘和约翰逊
‑
拉贝克力型(johnson
‑
rahbek force type)静电吸盘两种。对于库仑力型静电吸盘,通常使用诸如具有高纯度的氧化铝和氮化铝的烧结陶瓷,使得介电层部分的体积电阻率超过1
×
10
15
ω
·
cm。因此,这种类型存在生产成本高的问题。进一步,库仑力型静电吸盘必须施加约2000v至3000v的高压,以确保足够的吸附功率,因为在库仑力型静电吸盘中很少发生电荷转移。
6.对于约翰逊
‑
拉贝克力型静电吸盘,通常使用诸如氧化铝和氮化铝(其中使用掺杂金属氧化物等添加剂)的烧结陶瓷,使得介电层部分的体积电阻率为约1
×
109ω
·
cm至1
×
10
12
ω
·
cm。这种类型也存在生产成本高的问题。进一步,在约翰逊
‑
拉贝克力型静电吸盘中,由于吸附性能取决于体积电阻率,因此要求材料具有低的温度依赖性。
7.另外,在等离子刻蚀装置中,在高腐蚀性卤素系气体气氛下对处理对象(半导体)进行处理。采用氟系气体和氯系气体作为处理气体。氟系气体的实例包括sf6、cf4、chf3、clf3、hf及nf3,氯系气体的实例包括cl2、bcl3、hcl、ccl4及sicl4。
8.在组成等离子蚀刻装置的零件或部件的表面上,通常通过大气等离子喷涂(aps)形成耐腐蚀性涂层,该喷涂以粒料形式提供稀土化合物作为原料。进一步,在通过清洗溶液去除由于卤素系气体等离子而沉积或附着在部件表面上的反应产物的情况下,专利文件1建议通过具有多层结构的涂层抑制由于产生自反应产物与清洗溶液的反应的酸的渗透而导致的基材溶解量。作为另一个问题,喷涂颗粒的平均颗粒尺寸优选为10μm以上,以便以粒料的形式喷涂。如果尺寸小于该范围,颗粒的流动性可能变低,导致供应管被喷涂材料堵塞,或火焰中引入的颗粒可能蒸发,导致工艺收率下降(专利文件2)。因此,通过利用具有大平均颗粒尺寸的颗粒的热喷涂获得的喷涂涂层,由于颗粒的激冷薄片直径(splat diameter)大,因此会导致许多裂纹和大孔隙。因此,不能获得致密的涂层,在蚀刻过程中从涂层中不利地产生颗粒。例如,当通过aps形成对卤素系气体等离子具有良好耐腐蚀性的氟化钇系喷涂涂层时,与通过aps形成的氧化钇喷涂涂层相比,初始颗粒的产生受到抑制。然
而,氟化钇系喷涂涂层的维氏硬度为350至470,孔隙率为约2%(专利文件3中),这并不一定意味着足够的性能。
9.特别是,最近,半导体的集成正在进行中,预计将达到10nm以下的布线宽度。在通过蚀刻对集成的半导体器件加工时,上述的钇系涂层容易从零件的钇系涂层表面掉落钇系颗粒,释放的颗粒容易掉到晶片上,阻碍了蚀刻处理。在半导体器件的制造中,这些颗粒可能引起工艺收率的恶化。因此,要求在构成暴露于等离子的腔室的部件上形成的耐腐蚀性涂层具有更高的耐腐蚀性。
10.最近,为解决上述问题,研究了悬浮等离子喷涂(sps)。在sps中,喷涂颗粒不是以粒料形式喷涂,而是以浆料形式喷涂,其中喷涂颗粒分散在分散介质中。当以浆料形式进行热喷涂时,难以应用于利用粒料形式的热喷涂的颗粒尺寸10μm以下的细颗粒可被引入热喷涂的火焰中。因此,获得的喷涂层非常致密,因为喷涂涂层的激冷薄片直径变得非常小。
11.例如,使用其中氧化钇颗粒分散在介质中的浆料的热喷涂方法称为以浆料形式喷射颗粒的方法。该方法可制备维氏硬度为500以上且孔隙率为1%以下的致密的喷涂涂层(专利文件4)。然而,即使喷涂涂层是致密的,氧化钇也有问题,使得氧化钇喷涂涂层可由于氧化钇与卤系气体等离子的化学反应而在其表面逐渐被卤化,许多钇系颗粒作为不利的颗粒源而产生。
12.为解决这一问题,提出了由浆料获得的喷涂涂层,在该浆料中将氟化钇或氟氧化钇喷涂颗粒分散在介质中,然而,在该方法中尚未形成可满足当前需要的致密的喷涂涂层(专利文件5和6)。
13.引文列表
14.专利文件1:jp
‑
b 4985928
15.专利文件2:jp
‑
a 2017
‑
186678
16.专利文件3:jp
‑
a 2017
‑
190475
17.专利文件4:jp
‑
b 5987097
18.专利文件5:jp
‑
a 2017
‑
61734
19.专利文件6:jp
‑
a 2017
‑
78205
技术实现要素:
20.本发明的目的是提供可制备适合于等离子蚀刻装置中的静电吸盘的致密的喷涂涂层的方法,以及适合于在等离子蚀刻装置中的零件或部件上形成的耐腐蚀性涂层的喷涂涂层,其难以由于卤素系气体等离子而产生颗粒,并且具有体积电阻率的低的温度依赖性。进一步,本发明的另一个目的是提供制造该喷涂涂层的方法、形成有该喷涂涂层的喷涂的部件以及适用于形成该喷涂涂层的喷涂材料。
21.发明人已经发现,通过调节每层的厚度、孔隙率、硬度和/或表面粗糙度,具有包含由含有稀土氧化物的喷涂涂层制成的下层,以及形成在下层上的由含有稀土氟化物和/或稀土氟氧化物的另外喷涂涂层制成的表层的多层结构的喷涂涂层具有体积电阻率的低的温度依赖性和优异的电特性,特别是在23℃下具有良好的体积电阻率,即1
×
109ω
·
cm至1
×
10
12
ω
·
cm,并且由200℃下的体积电阻率与23℃下的体积电阻率之比限定的体积电阻率的温度指数为0.1至10。进一步,反复研究了表面和下层的厚度、涂层的硬度、涂层的孔隙率
和涂层的表面粗糙度,从而完成了本发明。
22.在一个方面,本发明提供一种具有多层结构的喷涂涂层,其包含由含有稀土氧化物的喷涂涂层制成的下层和由含有稀土氟化物和/或稀土氟氧化物的另外喷涂涂层制成的表层,其中
23.具有多层结构的喷涂涂层具有23℃下的体积电阻率和200℃下的体积电阻率,23℃下的体积电阻率为1
×
109ω
·
cm至1
×
10
12
ω
·
cm,由200℃下的体积电阻率与23℃下的体积电阻率之比限定的体积电阻率的温度指数为0.1至10。
24.优选地,表层含有rf3,或rf3和选自r5o4f7、r7o6f9和rof中的至少一种,其中r是选自包括y和sc的稀土元素中的至少一种,并且每个r可以相同或不同。
25.优选地,下层含有r2o3,或r2o3和选自rf3、r5o4f7、r7o6f9及rof中的至少一种,其中r是选自包括y和sc的稀土元素中的至少一种,并且每个r可以相同或不同。
26.优选地,下层具有由喷涂涂层的至少两个子层构成的多层结构,并且子层中的至少一个由含有稀土氧化物的喷涂涂层构成。
27.优选地,下层的厚度为50μm至300μm,并且表层的厚度为10μm至200μm。
28.优选地,表层的维氏硬度为500以上,孔隙率为1%以下,和/或中心线平均粗糙度ra为0.1μm至6μm。
29.在另一方面,本发明提供一种喷涂的部件,其包含金属基材、陶瓷基材或碳基材,以及在其上形成的喷涂涂层。
30.优选地,金属基材由铝合金、阳极化铝合金或不锈钢组成,陶瓷基材由氧化铝、氧化锆、石英玻璃、碳化硅或氮化硅组成。
31.在另一方面,本发明提供一种制造喷涂涂层的方法,其包括以下步骤:
32.通过大气等离子喷涂在基材上热喷涂稀土氧化物粉末以形成下层,以及
33.通过悬浮等离子喷涂在下层上热喷涂包含有机溶剂和分散在其中的稀土氟化物粉末的浆料以形成表层。
34.优选地,所述浆料进一步包含稀土氧化物粉末,并且氟化物粉末/氧化物粉末的重量比为99/1到90/10。
35.在另一方面,本发明提供一种制造喷涂涂层的方法,其包括以下步骤:
36.通过大气等离子喷涂在基材上热喷涂稀土氧化物粉末以形成下层,以及
37.通过大气等离子喷涂向下层热喷涂含有稀土氟化物和稀土氧化物的粉末以形成表层。
38.在另一方面,本发明提供一种浆料形式的喷涂材料,其包含有机溶剂和分散在其中的稀土化合物粉末,所述稀土化合物粉末包含rf3粉末,并且r是选自包括y和sc的稀土元素中的至少一种。
39.优选地,rf3粉末的bet比表面积为2m2/g以下,且体积基准平均颗粒尺寸d
50
为2μm至6μm。
40.优选地,rf3粉末的圆度平均值为0.9以上,圆度由以下表达式(1)定义:
41.(圆度)=(在平面视图中具有与被观察颗粒的面积相等的面积的假设圆的周边长度)/(平面视图中被观察颗粒的周边长度)
ꢀꢀꢀ
(1)
42.优选地,通过纳米压痕法测定的rf3粉末的颗粒硬度为7gpa至12gpa。
43.优选地,rf3粉末具有通过压汞法测定的直径为10μm以下的孔隙的总体积为0.5cm3/g以下。
44.优选地,喷涂材料进一步包含r2o3粉末,r是选自包括y和sc的稀土元素中的至少一种,并且rf3粉末/r2o3粉末的重量比为99/1到90/10。
45.发明的有利效果
46.根据本发明的具有多层结构的喷涂涂层包含含有稀土氧化物的下层和含有稀土氟化物和/或稀土氟氧化物的表层,该喷涂涂层具有变化小的从室温至200℃的体积电阻率、良好的电特性(具有低的温度依赖性),在卤素系气体气氛或卤素系气体等离子气氛下的处理中发挥出优异的耐腐蚀性。进一步,该喷涂涂层能够尽可能地减少从反应产物或涂层上掉落的颗粒的产生。而且,通过本发明的方法和喷涂材料可容易地获得该喷涂涂层。
附图说明
47.图1是用于分析实施例3中制造的喷涂涂层中的横截面表面的照片图像,该实施例中在添加少量氧化钇细颗粒的情况下形成表层。
48.图2是用于分析在不添加氧化钇细颗粒的情况下,通过与实施例3相同的方法制造的喷涂涂层中的横截面表面的照片图像。
具体实施方式
49.本发明的喷涂涂层具有多层结构,包含由含有稀土氧化物的喷涂涂层制成的下层,以及由含有稀土氟化物和/或稀土氟氧化物的另外喷涂涂层(稀土氟化物系涂层)制成的表层。在本发明中,稀土元素包括sc、y和镧系元素(原子序数57的la至原子序数71的lu)。稀土元素单独使用或由两种以上的元素组合使用。
50.用于形成表层的含有稀土氟化物和/或稀土氟氧化物的喷涂涂层可以是含有rf3的喷涂涂层,或含有rf3和选自r5o4f7、r7o6f9和rof中的至少一种的喷涂涂层,其中,r独立地是选自包括y和sc的稀土元素中的至少一种元素,并且r可以相同或不同。在这种情况下,鉴于对卤素系气体气氛或卤素系气体等离子气氛的耐腐蚀性,稀土氟化物和/或稀土氟氧化物优选具有包括rf3和选自r5o4f7、r7o6f9和rof中的至少一种的晶体结构。然而不限于此。
51.特别是,作为稀土元素,可例示sc、y、la、ce、pr、nd、pm、sm、eu、gd、tb、dy、ho、er、tm、yb和lu。其中,优选y、gd、tb、dy、ho、er、tm、yb和lu,然而不限于此。
52.表层优选的厚度为10μm至200μm,更优选50μm至150μm,甚至更优选80μm至120μm,然而不限于此。如果表层的厚度小于10μm,则表层可能对卤素系气体等离子发挥不出足够的耐腐蚀性。另一方面,如果厚度大于200μm,则表层可能不利地从下层剥离。
53.表层的优选的维氏硬度为500以上,更优选500到700。如果维氏硬度小于500,在某些情况下,喷涂涂层可能容易由于卤素系气体等离子而从其表面产生颗粒。另一方面,如果维氏硬度大于700,则表层的涂层可能不利地从下层的涂层剥离。
54.为了控制由于卤素系气体等离子而产生颗粒并改善耐腐蚀性,形成表层的喷涂涂层优选为致密的涂层,其具有优选1%以下,更优选0.5%以下的孔隙率,然而不限于此。例如,如实施例和比较例中所述,测定孔隙率的方法包括通过电子显微镜拍摄横截面照片图像,对多个视场(实施例和比较例中的10个视场)中图像总面积的孔隙率进行量化,确定多
个视场的孔隙率的平均值,用百分比表示为孔隙率。
55.如以上所述,当喷涂涂层用于卤素系气体气氛或卤素系气体等离子气氛中时,由维氏硬度为500以上,更优选500至700且孔隙率小于1%的坚硬且致密的喷涂涂层形成的表层可有效地控制颗粒的产生和卤素系腐蚀性气体的混入。
56.形成表层的涂层的优选的中心线平均粗糙度ra(jis b 0601中所定义的)为0.1μm至6μm,更优选0.1μm至5.5μm,甚至更优选0.1μm至5μm,然而不限于此。如果中心线平均粗糙度ra大于6μm,则由于卤素系气体等离子导致的颗粒的产生不利地被加速。另一方面,如果中心线平均粗糙度ra小于0.1μm,则由于为调整厚度而进行的过度加工可能不利地损坏喷涂涂层,或者颗粒从涂层上不适当地掉落。
57.含有稀土氟化物的喷涂涂层的表层形成在下面描述的下层上。作为形成表层的方法,例如,采用使用包含稀土氟化物粉末的浆料的悬浮等离子喷涂(sps)方法,或使用稀土氟化物粉末的大气等离子喷涂(aps)方法,作为形成表层的方法。特别地,优选采用sps方法来形成表层,因为该方法可容易地形成具有在上述优选范围内的维氏硬度和孔隙率的致密的喷涂涂层。
58.作为用于形成表层的悬浮等离子喷涂(sps)方法中的浆料,优选使用包含有机溶剂作为分散介质和分散在其中的包含稀土氟化物粉末(rf3粉末,其中r是选自包括y和sc的稀土元素中的至少一种元素)的稀土化合物粉末的浆料。在这种情况下,有机溶剂包括例如醇、醚、酯和酮,然而不限于此。其中更优选使用乙醇、甲醇、1
‑
丙醇、2
‑
丙醇、乙基溶纤剂、二甲基二甘醇、乙二醇醚、乙基溶纤剂乙酸酯、丁基溶纤剂乙酸乙二醇酯、异佛尔酮或丙酮。浆料中的rf3粉末的含量优选为10wt%至45wt%,更优选20wt%至35wt%,然而不限于此。进一步,组成浆料的分散介质除有机溶剂外可以含有少量的水(例如,对于有机溶剂的量为10wt%以下,优选5wt%以下)。更优选地,组成浆料的分散介质基本上仅由有机溶剂构成,然而,其中可以以相关的量含有杂质。
59.分散在浆料中的rf3粉末优选的bet比表面积为2m2/g以下,更优选1.5m2/g以下,甚至更优选1m2/g以下、最优选0.8m2/g以下,且优选0.1m2/g以上。分散在浆料中的rf3粉末优选的体积基准平均颗粒尺寸d
50
为2μm至6μm,更优选2.5μm至5μm。通过纳米压痕法测定的分散在浆料中的rf3粉末优选的颗粒硬度为7gpa至12gpa,更优选7.5gpa至11.5gpa。通过压汞法测定的分散在浆料中的rf3粉末优选的直径为10μm以下的孔隙的总体积为0.5cm3/g以下,更优选0.4cm3/g以下。分散在浆料中的rf3粉末优选的圆度平均值(平均圆度)为0.9以上,由以下表达式(1)定义:
60.(圆度)=(在平面视图中具有与被观察颗粒的面积相等的面积的假设圆的周边长度)/(平面视图中被观察颗粒的周边长度)
ꢀꢀꢀ
(1)
61.值得注意的是,例如,当喷涂颗粒在平面视图中具有完美的圆形时,平均圆度为1(一),而当喷涂颗粒在平面视图中具有方形时,平均圆度为0.886。因此,平均圆度随着喷涂颗粒在平面视图中的形状接近完美圆形而增大,平均圆度随着喷涂颗粒在平面视图中的形状变得更加复杂而减小。然而,rf3粉末并不限于上述特征。
62.通过制备具有满足bet比表面积、平均颗粒尺寸d
50
、平均圆度、颗粒硬度和/或孔隙体积的rf3粉末的浆料,并且通过悬浮等离子喷涂(sps)法形成表层,可形成维氏硬度为500以上,尤其是500至700且孔隙率为1%以下的致密的表层。
63.该浆料可以以10wt%以下的范围包含由选自无机化合物、聚合物、非金属、准金属和有色金属中的一种或多种材料组成的细颗粒作为添加剂。喷涂涂层(表层)的热特性、电特性和机械特性可通过添加极少量的细颗粒来控制。
64.作为无机化合物,可例示包含选自稀土元素、硼、铝、镓、铟、铍、镁、钙、锶、钡、钛、锆、铪、硅、锗、锡、铅、磷或硫的氧化物、氮化物、碳化物、卤化物、氢氧化物、碳酸盐、铵盐、草酸盐、硝酸盐、硫酸盐和盐酸盐中的一种或多种的化合物,然而不限于此。
65.作为聚合物,可例示聚硅烷、聚碳硅烷、聚硅氧烷、聚硼硅氧烷、聚硅氮烷、聚有机硼硅氮烷、聚碳硅氮烷、聚碳酸酯等,然而不限于此。
66.作为非金属和准金属,可例示碳、硼、硅、锗、磷、硫等,然而不限于此。
67.作为有色金属,可例示稀土元素、铝、镓、铟、铍、镁、钙、锶、钡、钛、锆、铪、锡、铅等,然而不限于此。有色金属可以是金属的合金。
68.该浆料可以添加有少量的稀土元素的氧化物粉末(r2o3粉末,其中r是选自包括y和sc的稀土元素中的至少一种元素),其范围为99/1至90/10(重量比),其定义为rf3粉末与r2o3粉末的比,然而不限于此。在这种情况下,r2o3粉末的稀土元素优选与rf3粉末的稀土元素相同。所添加的r2o3粉末优选的bet比表面积为30m2/g至80m2/g,更优选40m2/g至60m2/g,且优选的体积基准平均颗粒尺寸d
50
为10μm至500μm,更优选50μm至300μm,然而不限于此,并且该细颗粒适于作为r2o3粉末。如下述的实施例3中所示,通过向浆料中添加少量这样的r2o3细颗粒粉末,可有效地控制表层中横向裂纹的产生。
69.另外,该浆料适合用作形成本发明的多层喷涂涂层的表层的喷涂材料,然而,该浆料并不限于该应用。该浆料可以用作形成单层的喷涂涂层或组成本发明以外的多层涂层的喷涂涂层的浆料。
70.如上所述,可以通过利用稀土氟化物粉末的大气等离子喷涂来形成组成本发明的喷涂涂层的表层。在这种情况下,通过例如将预定量的稀土氟化物粉末(rf3粉末)与预定量的稀土氧化物粉末(r2o3粉末)混合,以及任选地将混合物造粒,可将含有稀土元素的氟化物和氧化物的粉末提供给大气等离子喷涂。然而,该粉末并不限于此。通过该方法可获得含有rf3和选自r5o4f7、r7o6f9和rof中的至少一种的喷涂涂层,其中r是选自包括y和sc的稀土元素中的至少一种,并且每个r可以相同或不同。在这种情况下,添加的稀土氧化物的含量可以优选为喷涂粉末总量的1wt%至50wt%,更优选5wt%至30wt%。含有稀土元素的氟化物和氧化物的粉末优选的体积基准平均颗粒尺寸d
50
为15μm至45μm,更优选20μm至40μm。
71.在悬浮等离子喷涂和大气等离子喷涂的任一情况下,诸如等离子气体、喷枪输出功率、喷涂距离等的喷涂条件可以根据基材的材料和/或尺寸(喷涂面积)和/或喷涂涂层的类型和/或厚度来设定。
72.本发明的喷涂涂层具有多层结构,其中在由含有稀土氧化物的喷涂涂层组成的下层上形成表层。
73.含有组成下层的稀土氧化物的喷涂涂层可以是含有r2o3的喷涂涂层,或者是含有r2o3和选自rf3、r5o4f7、r7o6f9和rof中的至少一种的喷涂涂层,其中r是选自包括y和sc的稀土元素中的至少一种,并且每个r可以相同或不同。
74.在这种情况下,作为稀土元素r,可例示sc、y、la、ce、pr、nd、pm、sm、eu、gd、tb、dy、ho、er、tm、yb和lu,然而不限于此。其中,与表层相同,优选y、gd、tb、dy、ho、er、tm、yb和lu。
75.下层的优选厚度为50μm至300μm,更优选70μm至200μm,甚至更优选80μm至150μm,然而不限于此。如果下层的厚度小于50μm,则由酸引起的基材溶出量可能增加。另一方面,如果厚度大于200μm,则下层可能不利地从基材剥离。
76.由于形成下层的喷涂涂层的表面粗糙度对表层的表面粗糙度施加有影响,因此对于下层来说小的表面粗糙度是有利的。形成下层的涂层优选的中心线平均粗糙度ra(jis b 0601中定义的)为0.1μm至10μm,更优选0.1至6μm,然而不限于此。通过大气等离子喷涂形成下层的喷涂涂层后,可通过例如进行任选的机械抛光(表面研磨、内筒精加工、镜面精加工等)、使用微珠的喷砂处理,或者使用金刚石垫的手工抛光将表面粗糙度调节至上述范围。
77.进一步,由于与表层的相同原因,形成下层的涂层优选的孔隙率为5%以下,更优选3%以下,然而不限于此。可通过以下方法获得孔隙率,然而不限于此。
78.例如,孔隙率为5%以下的、由稀土氧化物组成的致密的喷涂涂层制成的下层可利用体积基础平均颗粒尺寸d
50
为0.5μm至50μm,更优选1μm至30μm的单一颗粒粉末或造粒的喷涂粉末作为稀土氧化物的原料,使颗粒充分熔化,通过大气等离子喷涂、爆炸喷涂等方式来形成。由于与一般的造粒的喷涂粉末相比,用于喷涂材料的单一颗粒的粉末是具有较小颗粒尺寸且由填充有内容物的颗粒构成的细颗粒,因此该方法可形成包含小直径的激冷薄片且控制裂纹产生的下层。根据该效果,可获得孔隙率为5%以下且中心线平均粗糙度ra小的喷涂涂层。本文中的单一颗粒粉末是指具有球形的粉末、具有角形的粉末、粉碎的粉末等,并且该颗粒牢固地填充了内容物。
79.下层可以具有多层结构,其中层叠至少两个喷涂涂层。在这种情况下,构成多层结构的至少一个子层是上述用于下层的含有稀土氧化物的喷涂涂层。进一步,在这种情况下,将含有稀土氟化物的喷涂涂层例示为与含有稀土氧化物的喷涂涂层层叠的其他层,然而不限于此。特别地,如下面实施例6中所述,通过在基材表面上通过大气等离子喷涂氧化钇粉末形成稀土氧化物的喷涂涂层,通过在其上大气等离子喷涂氟化钇粉末形成稀土氟化物的喷涂涂层,可以获得包含y2o3喷涂涂层和层叠在其上的yf3喷涂涂层的双层结构。
80.作为形成下层的方法,如下面实施例中所述,优选采用大气等离子喷涂,然而不限于此。
81.本发明的喷涂涂层是具有多层结构的涂层,该多层结构包含形成于基材表面上的下层,以及层叠于下层上的表层。通过多层结构,喷涂涂层发挥了优异的电性能。特别地,喷涂层在23℃下的体积电阻率为1
×
109ω
·
cm至1
×
10
12
ω
·
cm,这是良好的电阻能力,喷涂层在23℃至200℃温度范围内的体积电阻率变化非常小。特别地,可提供由200℃下的体积电阻率与23℃下的体积电阻率之比限定的体积电阻率的温度指数为0.1至10的喷涂涂层,并且喷涂涂层在电特性方面极为稳定。
82.在本发明中,由于喷涂涂层具有包含下层和表层的多层结构,因此体积电阻率的温度指数可利用下层和/或表层厚度的变化或表层的稀土氟化物系涂层的氧含量的变化来任意控制。例如,对于等离子蚀刻装置中使用的静电吸盘,要求在室温与200℃高温之间的体积电阻率变化小的材料。本发明可提供满足该要求的材料。
83.进一步,如下面实施例中所述,本发明的喷涂涂层具有足够稳定的表面电阻率和足够高的介电击穿强度,因此,通过该喷涂涂层,获得了适用于静电吸盘的材料的良好的介电击穿电压值。
84.本发明的喷涂涂层适合于用于半导体制造工艺的等离子蚀刻装置中的静电吸盘或零件或部件上形成的耐腐蚀性涂层,然而不限于此。该喷涂涂层适用于具有例如平板形状或筒形,并且由耐热材料,例如金属如铝合金、耐酸铝化处理的铝合金和不锈钢,陶瓷如氧化铝、氧化锆、石英玻璃、碳化硅、氮化硅、碳等的组成的基材。
85.实施例
86.以下通过例示而非限制的方式给出本发明的实施例。
87.实施例1
88.用丙酮在表面对表面尺寸为100mm见方和5mm厚的a5052铝合金基材进行脱脂,并用研磨刚玉对基材的一个表面进行粗糙化处理。通过使用大气等离子喷涂装置和平均颗粒尺寸(d
50
)为20μm的氧化钇粉末(造粒的颗粒)在基材上形成100μm厚的氧化钇喷涂涂层作为下层。作为喷涂条件,使用氩气和氢气作为等离子气体,采用30kw的输出功率和120mm的喷涂距离。通过如下说明的图像分析法确定下层的孔隙率,其为2.0%。
89.进一步,制备浆料,使得30wt%的bet比表面积为0.7m2/g且平均颗粒尺寸(d
50
)为3.3μm的氟化钇颗粒分散于乙醇中。通过使用悬浮等离子喷涂装置和浆料,将150μm厚的氟化钇系喷涂涂层作为表层形成在设置于基材上的下层上。通过研磨对表层的最外表面部分进行机加工以从表面除去50μm厚,并将表面抛光为表面粗糙度ra为0.1μm的镜面表面。然后,制备了具有双层结构和总厚度为200μm的耐腐蚀性涂层的试样件。通过如下说明的图像分析法确定表层的孔隙率,其为0.4%。
90.[孔隙测定]
[0091]
将试样件嵌入树脂中,将横截面表面抛光为镜面(表面粗糙度ra:0.1μm)。然后,拍摄横截面表面的电子显微照片(以200倍的放大率)。在横截面表面的10个视场(拍摄面积:0.017mm2/视场)拍摄照片图像。通过利用图像处理软件“photoshop”(由adobe systems co.,ltd.制作)对图像进行处理后,通过利用图像分析软件“section image”(由scion corporation制作)对孔隙进行定量,将孔隙率作为孔隙部分的总面积与观察区域的总面积的比来计算。以十个视场的平均值来评价孔隙率。
[0092]
实施例2
[0093]
用丙酮在表面对表面尺寸为100mm见方和5mm厚的a5052铝合金基材进行脱脂,并用研磨刚玉对基材的一个表面进行粗糙化处理。通过使用大气等离子喷涂装置和平均颗粒尺寸(d
50
)为20μm的氧化铒粉末(造粒的颗粒)在基材上形成100μm厚的氧化铒喷涂涂层作为下层。作为喷涂条件,使用氩气和氢气作为等离子气体,采用30kw的输出功率功率和120mm的喷涂距离。通过与实施例1中相同的图像分析法确定下层的孔隙率,其为3.2%。
[0094]
进一步,制备浆料,使得30wt%的bet比表面积为1.5m2/g且平均颗粒尺寸(d
50
)为2.3μm的氟化铒颗粒分散于乙醇中。通过使用悬浮等离子喷涂装置和浆料,将100μm厚的氟化铒系喷涂涂层作为表层形成在设置于基材上的由氧化铒喷涂涂层组成的下层上。作为喷涂条件,使用氩气、氮气和氢气作为等离子气体,采用100kw的输出功率和75mm的喷涂距离。然后,制备具有双层结构且总厚度为200μm的耐腐蚀性涂层的试样件。通过与实施例1中相同的图像分析法确定表层的孔隙率,其为0.8%。
[0095]
实施例3
[0096]
用丙酮在表面对表面尺寸为100mm见方和5mm厚的a5052铝合金基材进行脱脂,并
用研磨刚玉对基材的一个表面进行粗糙化处理。通过使用大气等离子喷涂装置和平均颗粒尺寸(d
50
)为20μm的氧化钇粉末(造粒的颗粒)在基材上形成100μm厚的氧化钇喷涂涂层作为下层。作为喷涂条件,使用氩气和氢气作为等离子气体,采用30kw的输出功率和120mm的喷涂距离。通过与实施例1中相同的图像分析法确定下层的孔隙率,其为2.9%。
[0097]
进一步,制备浆料,使得30wt%的bet比表面积为1.0m2/g且平均颗粒尺寸(d
50
)为3.7μm的氟化钇颗粒与bet比表面积为48.3m2/g且平均颗粒尺寸(d
50
)为200nm的氧化钇细颗粒的混合物分散在乙醇中,该混合物以氟化钇/氧化钇的重量比=99/1含有它们。在这种情况下,浆料中氧化钇细颗粒的含量为0.3wt%。通过使用悬浮等离子喷涂装置和浆料,将100μm厚的氟化钇系喷涂涂层作为表层形成在设置于基材上的由氧化钇喷涂涂层组成的下层上。作为喷涂条件,使用氩气、氮气和氢气作为离子气体,采用100kw的输出功率和75mm的喷涂距离。然后,制备具有双层结构且总厚度为200μm的耐腐蚀性涂层的试样件。通过与实施例1中相同的图像分析法确定表层的孔隙率,其为0.2%。
[0098]
实施例4
[0099]
用丙酮在表面对表面尺寸为100mm见方和5mm厚的a5052铝合金基材进行脱脂,并用研磨刚玉对基材的一个表面进行粗糙化处理。通过使用大气等离子喷涂装置和平均颗粒尺寸(d
50
)为30μm的氧化钇粉末(造粒的颗粒)在基材上形成180μm厚的氧化钇喷涂涂层作为下层。作为喷涂条件,使用氩气和氢气作为等离子气体,采用30kw的输出功率和120mm的喷涂距离。通过与实施例1中相同的图像分析法确定下层的孔隙率,其为3.5%。所获得的涂层的表面粗糙度ra为5.6μm。接下来,通过使用表面研磨机对氧化钇喷涂涂层的最外表面部分进行机加工,并且将研磨后的表面抛光为表面粗糙度ra为0.1μm的镜面表面。将涂层的厚度调节为100μm。
[0100]
进一步,制备浆料,使得30wt%的bet比表面积为0.6m2/g且平均颗粒尺寸(d
50
)为4.6μm的氟化钇颗粒分散于乙醇中。通过使用悬浮等离子喷涂装置和浆料,将100μm厚的氟化钇系喷涂涂层作为表层形成在设置于基材上的由氧化钇喷涂涂层组成的下层上。作为喷涂条件,使用氩气、氮气和氢气作为等离子气体,采用100kw的输出功率和75mm的喷涂距离。然后,制备具有双层结构且总厚度为200μm的耐腐蚀性涂层的试样件。通过与实施例1中相同的图像分析法确定表层的孔隙率,其为0.9%。
[0101]
实施例5
[0102]
用丙酮在表面对表面尺寸为100mm见方和5mm厚的a5052铝合金基材进行脱脂,并用研磨刚玉对基材的一个表面进行粗糙化处理。通过使用大气等离子喷涂装置和平均颗粒尺寸(d
50
)为18μm的氧化钇粉末(造粒的颗粒)在基材上形成100μm厚的氧化钇喷涂涂层作为下层。作为喷涂条件,使用氩气和氢气作为等离子气体,采用30kw的输出功率和120mm的喷涂距离。通过与实施例1中相同的图像分析法确定下层的孔隙率,其为2.9%。
[0103]
进一步,通过使用大气等离子喷涂装置和含有90wt%氟化钇和10wt%氧化钇,且平均颗粒尺寸(d
50
)为30μm的造粒颗粒,将100μm厚的氟化钇系喷涂涂层作为表层形成在设置于基材上的下层上。作为喷涂条件,使用氩气和氢气作为等离子气体,采用35kw的输出功率和120mm的喷涂距离。然后,制备具有双层结构且总厚度为200μm的耐腐蚀性涂层的试样件。通过与实施例1中相同的图像分析法确定表层的孔隙率,其为2.3%。
[0104]
实施例6
[0105]
用丙酮在表面对表面尺寸为100mm见方和5mm厚的a5052铝合金基材进行脱脂,并用研磨刚玉对基材的一个表面进行粗糙化处理。通过使用大气等离子喷涂装置和平均颗粒尺寸(d
50
)为20μm的氧化钇粉末(造粒的颗粒)在基材上形成50μm厚的氧化钇喷涂涂层作为第一层。作为喷涂条件,使用氩气和氢气作为等离子气体,采用30kw的输出功率和120mm的喷涂距离。接下来,通过使用大气等离子喷涂装置和含有90wt%氟化钇和10wt%氧化钇且平均颗粒尺寸(d
50
)为30μm的造粒颗粒在第一层上形成50μm厚的氟化钇系喷涂涂层作为第二层。作为喷涂条件,使用氩气和氢气作为等离子气体,采用35kw的输出功率和120mm的喷涂距离。在此,形成了具有由第一层和第二层构成的多层结构的组合涂层作为下层。通过与实施例1中相同的图像分析法确定下层的孔隙率,其为2.9%。
[0106]
进一步,制备浆料,使得30wt%的bet比表面积为0.5m2/g且平均颗粒尺寸(d
50
)为5.7μm的氟化钇颗粒与平均颗粒尺寸(d
50
)为2μm的碳化硅细颗粒的混合物分散在乙醇中,该混合物以氟化钇/碳化硅的重量比=95:5含有它们。在这种情况下,浆料中碳化硅细颗粒的含量为1.5wt%。通过使用悬浮等离子喷涂装置和浆料,将150μm厚的氟化钇系喷涂涂层作为表层形成在具有多层结构的涂层的下层上。作为喷涂条件,使用氩气、氮气和氢气作为离子气体,采用100kw的输出功率和75mm的喷涂距离。然后,制备具有三层结构且总厚度为250μm的耐腐蚀性涂层的试样件。通过与实施例1中相同的图像分析法确定表层的孔隙率,其为0.3%。
[0107]
实施例7
[0108]
用丙酮在表面对表面尺寸为100mm见方和5mm厚的a5052铝合金基材进行脱脂,并用研磨刚玉对基材的一个表面进行粗糙化处理。通过使用大气等离子喷涂装置和平均颗粒尺寸(d
50
)为15μm的氧化钆粉末(造粒的颗粒)在基材上形成300μm厚的氧化钆喷涂涂层作为下层。作为喷涂条件,使用氩气和氢气作为等离子气体,采用30kw的输出功率和120mm的喷涂距离。通过与实施例1中相同的图像分析法确定下层的孔隙率,其为2.2%。
[0109]
进一步,制备浆料,使得30wt%的bet比表面积为0.3m2/g且平均颗粒尺寸(d
50
)为5.9μm的氟化钆颗粒与平均颗粒尺寸(d
50
)为2μm的碳化硅细颗粒的混合物分散在乙醇中,该混合物以氟化钆/碳化硅的重量比=90:10含有它们。在这种情况下,浆料中碳化硅细颗粒的含量为3wt%。通过使用悬浮等离子喷涂装置和浆料,将50μm厚的氟化钆系喷涂涂层形成为表层。作为喷涂条件,使用氩气、氮气和氢气作为等离子气体,采用100kw的输出功率和75mm的喷涂距离。然后,制备具有双层结构且总厚度为350μm的耐腐蚀性涂层的试样件。通过与实施例1中相同的图像分析法确定表层的孔隙率,其为0.1%。
[0110]
比较例1
[0111]
用丙酮在表面对表面尺寸为100mm见方和5mm厚的a5052铝合金基材进行脱脂,并用研磨刚玉对基材的一个表面进行粗糙化处理。通过使用大气等离子喷涂装置和平均颗粒尺寸(d
50
)为18μm的氧化铝粉末(sumicorundum aa
‑
18)在基材上形成200μm厚的氧化铝喷涂涂层。作为喷涂条件,使用氩气和氢气作为等离子气体,采用30kw的输出功率和120mm的喷涂距离。然后,制备了由氧化铝喷涂涂层组成的耐腐蚀性涂层的试样件。通过与实施例1中相同的图像分析法确定氧化铝喷涂涂层的孔隙率,其为3.5%。
[0112]
比较例2
[0113]
用丙酮在表面对表面尺寸为100mm见方和5mm厚的a5052铝合金基材进行脱脂,并
用研磨刚玉对基材的一个表面进行粗糙化处理。使用大气等离子喷涂装置和平均颗粒尺寸(d
50
)为30μm的氧化钇粉末(造粒颗粒)在基材上形成200μm厚的氧化钇喷涂涂层。作为喷涂条件,使用氩气和氢气作为等离子气体,采用30kw的输出功率和120mm的喷涂距离。然后,制备了由氧化钇喷涂涂层组成的耐腐蚀性涂层的试样件。通过与实施例1中相同的图像分析法确定氧化铝喷涂涂层的孔隙率,其为1.8%。
[0114]
比较例3
[0115]
用丙酮在表面对表面尺寸为100mm见方和5mm厚的a5052铝合金基材进行脱脂,并用研磨刚玉对基材的一个表面进行粗糙化处理。制备浆料,使得30wt%的bet比表面积为2.8m2/g且平均颗粒尺寸(d
50
)为1.6μm的氟化钇颗粒分散在含有10wt%乙醇的纯水中。通过使用悬浮等离子喷涂装置和浆料形成100μm厚的氟化钇系喷涂涂层。作为喷涂条件,使用氩气、氮气和氢气作为等离子气体,采用100kw的输出功率和75mm的喷涂距离。然后,制备了由单层构成的耐腐蚀性涂层的试样件。通过与实施例1中相同的图像分析法确定氟化钇喷涂涂层的气孔率,其为3.5%。
[0116]
关于实施例1至7和比较例1至3的试样件的耐腐蚀性涂层,通过以下各方法对各喷涂涂层测定了晶相、维氏硬度、产生的颗粒量、对等离子的耐腐蚀性、厚度、中心线平均粗糙度(表面粗糙度)ra和稀土元素(r)、氧(o)和氮(n)的浓度。结果示于表1中。
[0117]
[晶相的测定]
[0118]
通过由malvern panalytical ltd.制造的x射线衍射仪“x'pert pro/mpd”对所获得的试样件的耐腐蚀性涂层中含有的晶相进行了鉴定。
[0119]
[厚度的测定]
[0120]
通过由kett电气实验室制造的涡流涂层厚度仪lh
‑
300j对所获得的试样件的厚度进行了测定。
[0121]
[维氏硬度的测定]
[0122]
将涂层表面抛光为镜面表面(表面粗糙度ra=0.1μm),并通过由mitutoyo corporation制造的显微维氏硬度计avk
‑
c1(载荷:300gf(2.94n),载荷时间:10分钟)在涂层表面测定了所获得的试样件的维氏硬度。以5点的平均值来评价维氏硬度。
[0123]
[颗粒产生评价试验]
[0124]
通过超声波清洗对所获得的试样件进行清洗(功率:200w,清洗时间:30分钟),然后干燥,将试样件浸入20cc的纯水中,通过超声波清洗进行进一步清洗。清洗后,将试样件从处理的水中取出,向处理的水中加入2cc的5.3n硝酸水溶液,以溶解包含在处理的水中的r2o3细颗粒,然后通过电感耦合等离子发射光谱法对r2o3进行定量。
[0125]
[耐腐蚀性评价试验]
[0126]
将所获得的试样件的表面抛光为表面粗糙度ra为0.1μm的镜面表面,并用遮蔽胶带覆盖表面的一部分以形成用遮蔽胶带覆盖的部分和用于暴露的部分。将试样件置于反应性等离子蚀刻装置中,然后,在440w的等离子输出功率、cf3和o2(20vol%)的气体物类、20sccm的流量、5pa的气体压力和8小时的试验时间的条件下进行耐等离子腐蚀试验。通过表面轮廓测定系统“dektak3030”测定由于腐蚀而造成的覆盖部分与暴露部分之间形成的台阶高度。以四个测定点的平均值评价结果。
[0127]
[中心线平均粗糙度(表面粗糙度)ra的测定]
[0128]
通过由tokyo seimitsu co.,ltd.制造的表面纹理测定仪handysurf e
‑
35a,对所获得的喷涂涂层的粗糙度ra进行了测定。
[0129]
[组分元素的测定]
[0130]
将所获得的喷涂涂层从其上设置有该喷涂涂层的基材上剥离,并将涂层的表层提供给组分元素的测定。通过edta滴定法测定r浓度,通过惰性气体熔融红外吸收分光光度法测定o浓度,通过naoh熔融ic法测定f浓度。
[0131]
表1
[0132][0133]
进一步,通过以下方法研究了实施例1至7和比较例1至3的每个耐腐蚀性涂层的电性能。制备三个试样件(n=3)用于电性能测试,分别研究了室温(23℃)和200℃下的体积电阻率、表面电阻率和介电击穿电压。结果示于表2至4中。
[0134]
[测定体积电阻率的方法]
[0135]
根据标准试验方法(astm d257:2007),通过超高电阻/最小电流数字表“8340a型”(由adc corporation制造)测定室温(23℃)和200℃下的体积电阻,并基于厚度计算体积电阻率。以三个试样件(n=3)的平均值来评价结果。表2中的“温度指数”是指通过表达式:(200℃下的体积电阻率)/(23℃下的体积电阻率)计算的值。当温度指数接近1(一)时,无论温度变化如何,耐腐蚀性涂层的体积电阻率都得以保持,这种温度指数意味着耐腐蚀性具有耐温度变化的能力。
[0136]
[测定表面比电阻的方法]
[0137]
根据标准试验方法(astm d257:2007),通过超高电阻/最小电流数字表“8340a型”(由adc corporation制造)测定室温(23℃)和200℃下的表面电阻,并计算表面电阻率。以三个试样件(n=3)的平均值来评价结果。
[0138]
[测定介电击穿电压的方法]
[0139]
根据标准试验方法(astm d149:2009),通过介电击穿测试仪“hat
‑
300
‑
100rho”型(由yamasaki sangyo kabushiki kaisha制造)测定室温(23℃)和200℃下的介电击穿电压,并基于厚度计算介电击穿强度。以三个试样件(n=3)的平均值来评价结果。
[0140]
表2
[0141]
[体积电阻率]
[0142][0143][0144]
表3
[0145]
[表面比电阻]
[0146][0147]
表4
[0148]
[介电击穿电压]
[0149][0150][0151]
如表1和表2中所示,具有由稀土氧化物涂层和在其上形成的稀土氟化物系涂层构成的多层结构的本发明的耐腐蚀性涂层的温度指数为0.1至10。确认了在23℃至200℃的温度范围内,体积电阻率的变化基本保持不变。也就是说,在本发明的耐腐蚀性涂层中,在23℃与200℃之间体积电阻率的变化非常小,因此本发明可提供电性能方面稳定的耐腐蚀性涂层。可通过下层和表层的厚度的变化和/或表层的稀土氟化物系涂层的氧含量的变化来
任意控制体积电阻率的温度指数。例如,对于等离子蚀刻装置中使用的静电吸盘,需要在室温与200℃的高温之间体积电阻率的变化小的材料。从这些结果确认本发明是满足要求的材料。如表3中所示,本发明的耐腐蚀性涂层具有对于温度变化稳定且足够的表面电阻率。进一步,如表4中所示,本发明的实施例1至7中的耐腐蚀性涂层具有足够高的介电击穿强度。确认该耐腐蚀性涂层具有适用于静电吸盘材料的介电击穿电压。
[0152]
如表1中所示,通过悬浮等离子浆料(sps)方法和仅包含有机溶剂(乙醇)作为分散介质的浆料获得了构成实施例1
‑
4、6和7中每一个的喷涂涂层的表层,所述表层包含由稀土氟化物和稀土氟氧化物构成的晶相。与其中大部分分散介质是水的比较例3相比,它们具有更高的维氏硬度,并且是具有低孔隙率的致密的涂层。确认在本发明中减少了颗粒的产生,并且喷涂涂层具有优异的耐腐蚀性。
[0153]
接下来,在实施例3中,通过悬浮浆料喷涂和包含其中添加了氧化钇细颗粒(d
50
:50nm)的氟化钇颗粒的浆料来形成喷涂涂层的表层。通过电子显微镜观察并比较了实施例3的喷涂涂层中的表层的横截面表面与除了排除添加氧化钇细颗粒以外相同的方法形成的喷涂涂层的横截面表面,确认了添加氧化钇细颗粒的效果。结果示于图1和2中。如图1和2中所示,确认了与利用不添加氧化钇细颗粒的浆料所获得的涂层相比,利用添加少量的氧化钇细颗粒的浆料所获得的表层涂层中,喷涂涂层的表层的横截面表面中横向裂纹的产生得到有效抑制。
[0154]
[实施例1
‑
4、6和7中用于形成表层的稀土氟化物颗粒的制备]
[0155]
通过以下方法制备用于形成实施例1
‑
4、6和7中的表层的稀土氟化物颗粒。首先,将包含稀土硝酸盐的溶液加热到50℃,将氟化铵溶液加入包含稀土硝酸盐的溶液中,然后在50℃下利用搅拌对该溶液进行30分钟混合。结果,白色沉淀结晶。之后,过滤沉淀物,用水清洗,然后干燥。通过x射线衍射分析,所获得的沉淀被鉴定为r3(nh4)f
10
形式的氟化铵复盐,其中r是稀土元素(即,实施例1、3、4和6中的y,实施例2中的er或实施例7中的gd)。进一步,在氮气气氛下在实施例6和7中于900℃下、在实施例4中于875℃下、在实施例1和3中于850℃下或在实施例2中于825℃下对复盐进行烧制。通过气流粉碎机对烧制的产物进行粉碎,然后获得了稀土氟化物颗粒。
[0156]
[比较例3中用于形成表层的氟化钇颗粒的制备]
[0157]
通过以下方法制备用于形成比较例3中的表层的氟化钇颗粒。首先,将氧化钇粉末与氟化氢铵粉末混合。将混合物在氮气气氛下于650℃烧制2小时,然后获得氟化钇。通过气流粉碎机将所获得的氟化钇粉碎,通过空气分级筛选,然后获得稀土氟化物颗粒。
[0158]
关于通过上述方法制备的、用于制备实施例1至4、6和7以及比较例3每一个中的用于热喷涂的浆料(喷涂材料)的稀土化合物粉末(氟化钇颗粒、氟化铒颗粒或氟化钆颗粒),通过以下各方法测定了bet比表面积、平均颗粒尺寸d
50
、平均圆度、颗粒硬度和孔隙体积。结果示于表5中。
[0159]
[bet比表面积的测定]
[0160]
通过由mountech co.,ltd制造的全自动bet比表面积分析仪macsorb hm型号1208测定了所获得的稀土化合物粉末的bet比表面积。
[0161]
[平均颗粒尺寸d
50
的测定]
[0162]
通过激光衍射法测定了稀土化合物粉末的颗粒尺寸分布,并以体积基准对平均颗
粒尺寸d
50
进行了评价。为了测量,使用由microtracbel corp制造的激光衍射/散射型颗粒尺寸分布测量装置"microtrac mt3300ex ii"。将所获得的浆料(在实施例1
‑
4、6或7或比较例3中)添加到30ml纯水中,用超声照射(40w,1分钟),然后进行提供以作为试样评价。将所获得的粉末(在实施例5或比较例1或2中)添加到30ml纯水中,然后直接进行提供以作为试样评价。将试样滴入测量装置的循环系统中,以便调节到用于测量装置规范的0.01
‑
0.09的浓度指数dv(衍射体积),并进行测量。
[0163]
[平均圆度的测定]
[0164]
平均圆度是由以下表达式定义的喷涂颗粒圆形度的评价值:
[0165]
(圆度)=(在平面视图中具有与被观察颗粒的面积相等的面积的假设圆的周边长度)/(在平面视图中被观察颗粒的周边长度)。
[0166]
通过由sysmex corporation制造的“fpia
‑
3000s”测定了所获得的稀土化合物粉末的平均圆度。特别地,通过鞘流(sheath flow)形成浆料试样的扁平试样流,并使用流动式颗粒图像分析仪“fpia
‑
3000s”,通过扁平鞘流法(flat sheath flow method),在频闪照明下拍摄颗粒的静止图像。通过图像分析技术对每个取样的颗粒进行分析,测定平均圆度。特别地,将20mg的试样粉末添加到烧杯中,将作为分散剂的水溶液的颗粒鞘(由sysmex corporation制造)添加到烧杯中以将混合物的体积固定为20ml,然后,通过超声波(100w)将浆料分散2分钟。使用所获得的用于测定的浆料进行测定。
[0167]
[颗粒硬度的测定]
[0168]
通过纳米压痕法测定了所获得的稀土化合物粉末的颗粒硬度。利用由elionix inc.制造的ent
‑
2100”作为分析装置。
[0169]
纳米压痕法是在纳米尺度上测定诸如材料硬度、弹性模量(表明塑性变形难度的物理性能值)和屈服应力(物质开始塑性变形的应力)的力学性能的技术。将金刚石压头压入放置在台架上的试样粉末中,测定载荷(压入强度)和变形(压入深度),由获得的载荷
‑
变形曲线计算力学性能。测定装置包括金刚石压头、用于检测金刚石压头的控制和测定值的传感器和控制器,以及用于操作的计算机。
[0170]
[孔隙体积的测定]
[0171]
利用由micromeritics instrument corporation制造的压汞仪autopore iii,通过压汞法测定稀土化合物粉末的孔隙体积,并由获得的相对于孔径的累积孔隙体积分布,计算直径为10μm以下的孔隙的总体积。
[0172]
表5
[0173][0174]
如表5中所示,在通过sps法形成表层的情况下,确认通过sps法和包含分散在有机溶剂中的稀土化合物粉末的浆料,获得了如表1中所示的具有非常高的硬度且耐腐蚀性方面优异的致密的喷涂涂层。在这种情况下,更优选使用bet表面积为2m2/g以下,平均颗粒尺寸d
50
为2μm至6μm,且进一步平均圆度为0.9以上,颗粒硬度为7gpa至12gpa,直径为10μm以下的孔隙的总体积为0.5cm3/g以下的稀土氟化物粉末作为稀土化合物粉末来形成有利的喷涂涂层。另一方面,在通过aps法形成的表层的情况下,确认获得了具有非常小的体积电阻率变化、稳定的电特性和足够高的介电击穿电压的喷涂涂层。
再多了解一些
本文用于企业家、创业者技术爱好者查询,结果仅供参考。