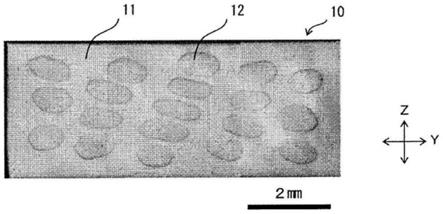
1.本发明涉及一种散热板材及散热板材的制造方法,例如,涉及一种在安装电力用功率半导体元件、高频设备、中央处理器(central processing unit,cpu)等半导体元件等时所使用的散热板材及散热板材的制造方法。
背景技术:
2.以前,电力用功率半导体元件、高频设备及cpu等半导体元件(以下,称为“半导体元件”)包括包含si(硅)、sic(碳化硅)、gan(氮化镓)、gaas(砷化镓)等的陶瓷系材料。由于此种半导体元件在工作中发热,因此配置有用于使热从发热的半导体元件释放的散热板。散热板例如通过焊料而与半导体元件接合。作为散热板材的一例,已知有cu合金板材,所述cu合金板材包含热传导率充分大的cu(铜)、与线膨胀率比较小的w(钨)、mo(钼)或cr(铬)的合金(cu
‑
w、cu
‑
mo或cu
‑
cr)。另外,作为散热板材的另一例,已知有:如日本专利特开2012
‑
243925号公报、日本专利特开2019
‑
79978号公报所公开的那样的、所述cu合金板材的任一者与cu(纯铜)的复合板材;或如日本专利特开2011
‑
3800号公报所公开的那样的、将热传导率充分大的cu(纯铜)或al(纯铝)设为表层、将线膨胀率充分小的fe
‑
36质量%ni(合金(alloy)36)设为中间层的三层结构的包层压延板材。
3.现有技术文献
4.专利文献
5.专利文献1:日本专利特开2012
‑
243925号公报
6.专利文献2:日本专利特开2019
‑
79978号公报
7.专利文献3:日本专利特开2011
‑
3800号公报
技术实现要素:
8.发明所要解决的问题
9.用于构成与半导体元件接合的散热板的散热板材例如优选为满足以下的要求事项。
10.(1)具有用于从半导体元件效率良好地散热的高热传导特性(大的热传导率)
11.(2)具有用于不会对半导体元件赋予过剩的热应力畸变的低热膨胀特性(与半导体材料接近的线膨胀率)
12.(3)与焊料的相容性(尤其是润湿性)良好
13.然而,在包含所述cu
‑
w、cu
‑
mo或cu
‑
cr等cu合金板材的散热板材中,例如有以下那样的不满。
14.(1)由于焊料的润湿性差,因此需要例如镀ni被覆处理等表面处理
15.(2)由于缺乏延伸性,因此压延及压制加工等变成高成本(尤其是cu
‑
w、cu
‑
mo)
16.(3)由于使用昂贵的原料,因此变成高成本(尤其是cu
‑
w、cu
‑
mo)
17.所述cu合金板材的任一者与cu的复合板材由于cu合金板材的表面包含cu,因此与
焊料的润湿性得到改善,但并未解决高成本的问题。相对于此,所述cu或al与合金36的三层结构的包层压延板材(以下,称为“cic包层材”)由于压延及压制加工中的加工性良好,且具有与构成半导体元件的半导体材料(例如,si)接近的线膨胀率,因此是可解决所述针对cu合金板材的问题的散热板材。cic包层材在平面方向(压延方向、压延宽度方向)上不易在高热传导特性或低热膨胀特性中产生各向异性。然而,认为,cic包层材由于构成中间层的合金36的热传导率相当小(以cu对比计为约1/13),因此厚度方向(层叠方向)上的热传导率变得相当小。具体而言,根据日本专利特开2011
‑
3800号公报的揭示,在高热传导材(cu)的体积比为50体积%的cic包层材的情况下,厚度方向上的热传导率为21w/(m
·
k),平面方向上的线膨胀率为8.4
×
10
‑6(1/k)。在所述cic包层材的情况下,由于认为平面方向上的热传导率与cu的热传导率(约400w/(m
·
k))为相同程度,因此平面方向与厚度方向的高热传导特性产生大的各向异性。另外,所述cic包层材的厚度方向上的线膨胀率并不明了,但由于cu的线膨胀率充分大于合金36,因此平面方向与厚度方向的低热膨胀特性有可能产生大的各向异性。
18.另外,认为,日本专利特开2011
‑
3800号公报所公开的、在包含合金36的中间层均等地分散配置有多个狭缝孔(开口部)的包层压延板材(cic包层材的变形例)在平面方向(压延方向、压延宽度方向)上不易在高热传导特性或低热膨胀特性中产生各向异性,且可在厚度方向上根据中间层的开口面积来调整高热传导特性。具体而言,根据日本专利特开2011
‑
3800号公报的公开,在高热传导材的体积比为50体积%的变形例的情况下,厚度方向上的热传导率为163w/(m
·
k),具有cic包层材的约8倍的热传导特性,平面方向上的线膨胀率为8.9
×
10
‑6(1/k)。另外,在增加了高热传导材的体积比的68体积%的变形例的情况下,厚度方向上的热传导率为221w/(m
·
k),具有cic包层材的约10倍的热传导特性,平面方向上的线膨胀率为11.9
×
10
‑6(1/k)。在任一变形例的情况下,由于认为均与cic包层材的情况相同,平面方向上的热传导率与cu为相同程度,因此平面方向与厚度方向的高热传导特性产生各向异性。另外,任一变形例的厚度方向上的线膨胀率均不明了,但由于cu的线膨胀率充分大于合金36,因此平面方向与厚度方向的低热膨胀特性有可能产生大的各向异性。
19.本发明的目的之一在于提供一种能够缓和散热板材的高热传导特性或低热膨胀特性的各向异性的散热板材及散热板材的制造方法。
20.解决问题的技术手段
21.本发明的散热板材包括包含高热传导材的高热传导部、以及包含低热膨胀材的多个低热膨胀部,所述多个低热膨胀部分别在所述高热传导部的长边方向上呈直线状连续地配置,并且在所述高热传导材部的长边方向、宽度方向及厚度方向上彼此不接触地配置。
22.在本发明的散热板材中,所述高热传导部优选为包含cu或cu合金。另外,所述多个低热膨胀部优选为包含fe
‑
ni系合金。另外,在将所述高热传导部的体积设为v1、将所述多个低热膨胀部的体积设为v2时,优选为满足v1/(v1 v2)为35体积%以上且80体积%以下。
23.本发明的散热板材可利用以下的制造方法而获得。
24.即,本发明的第一方面的散热板材的制造方法包括:准备工序,准备包含高热传导材且在长边方向上具有多个孔的线材、以及包含低热膨胀材的多个芯材;复合化工序,将所述多个芯材以填埋所述线材的所述多个孔各孔的方式插入,由此将所述多个芯材在所述线材的长边方向上呈直线状连续地配置、并且以在所述线材的长边方向、宽度方向及厚度方
向上彼此不接触的方式配置,由此制作复合原线材,通过对所述复合原线材进行伸展加工而获得复合线材;以及压延工序,对所述复合线材进行压延而成形为板状。
25.另外,本发明的第二方面的散热板材的制造方法包括:准备工序,准备包含高热传导材的管、以及在包含高热传导材的多个中空线材的各中空部插入包含低热膨胀材的多个芯材而成的多个复合芯材;复合化工序,将所述多个复合芯材以填埋所述管的中空部的方式插入,由此将所述多个芯材在所述管的长边方向上呈直线状连续地配置、并且以在所述管的长边方向、宽度方向及厚度方向上彼此不接触的方式配置,由此制作复合原线材,通过对所述复合原线材进行伸展加工而获得复合线材;以及压延工序,对所述复合线材进行压延而成形为板状。
26.再者,所述“横剖面”是指位于与物体的长度方向垂直的平面上的所述物体的剖面。另外,所述“伸展加工”是用于形成板、条、管、棒、线等各种制品的塑性加工,是指压延、挤压、拉拔、锻造等热加工或冷加工。
27.发明的效果
28.根据本发明,可提供一种能够缓和散热板材的高热传导特性或低热膨胀特性的各向异性的散热板材及散热板材的制造方法。具体而言,可提供一种例如对于安装电力用功率半导体元件、高频设备、cpu等半导体元件等时所使用的散热板而言适宜的散热板材、以及所述散热板材的制造方法。
附图说明
29.图1是表示作为本发明的散热板材的一实施方式的散热板材的横剖面的一例的图(光学显微镜照片)。
30.图2是表示作为本发明的散热板材的一实施方式的散热板材的横剖面的一例的图(光学显微镜照片)。
31.图3是用于说明构成作为本发明的散热板材的一实施方式的散热板材的芯材(低热膨胀材)的配置结构的图(照片)。
32.图4是用于说明本发明的第一方面的散热板材的制造方法的图。
33.图5是用于说明本发明的第二方面的散热板材的制造方法的图。
34.图6是表示用于构成本发明的散热板材的复合线材的横剖面的一例的图(光学显微镜照片)。
35.图7是表示作为本发明的散热板材的一实施方式的散热板材的横剖面的一例的图(光学显微镜照片)。
36.图8是表示作为本发明的散热板材的一实施方式的散热板材的横剖面的一例的图(光学显微镜照片)。
37.图9是表示使用从本发明的散热板材切出的样品进行的热膨胀测定的结果的图(图表)。
具体实施方式
38.以下,适宜参照附图对本发明的散热板材的实施方式进行说明。
39.本发明的散热板材包括包含高热传导材的高热传导部、以及包含低热膨胀材的多
个低热膨胀部,多个低热膨胀部分别在高热传导部的长边方向上呈直线状连续地配置,并且在高热传导部的长边方向、宽度方向及厚度方向上彼此不接触地配置。通过所述结构而成为如下散热板材,所述散热板材中,通过包含低热膨胀材的多个低热膨胀部而具有相应的低热膨胀特性,同时通过包含低热膨胀材的多个低热膨胀部在长边方向及宽度方向上彼此不接触地配置,而缓和了平面方向(长度方向、宽度方向)与厚度方向的高热传导特性的各向异性。再者,本发明的散热板材并不限定于后述的图1至图3所示的散热板材。另外,以下,将长边方向称为x方向,将宽度方向称为y方向,将厚度方向称为z方向。
40.本发明的散热板材可利用后述的散热板材的制造方法来制作。所述情况下,由于构成散热板材的高热传导部及多个低热膨胀部的配置结构在x方向上大致均等,因此成为具有在x方向上的任一位置横剖面均大致同等的形态的散热板材。关于所述结构,将所述散热板材在x方向上的规定位置切断而获得的规定长度的散热板也相同。
41.在本发明的散热板材中,低热膨胀部的根数并无特别限制。低热膨胀部的根数例如可考虑高热传导部的体积并且考虑作为散热对象的半导体元件的尺寸来适宜选择,以便调整为与半导体元件的线膨胀率近似的线膨胀率。另外,本发明的散热板材的大小并无特别限制,使用所述散热板材获得的散热板的大小也没有特别限制。散热板材例如可为厚度为0.3mm以上且4.0mm以下、宽度为5mm以上且40mm以下的规定长度的带状散热板材。另外,由散热板材获得的散热板可将厚度设为例如0.3mm以上且4.0mm以下,将宽度设为例如5mm以上且40mm以下,且可根据作为散热对象的半导体元件的尺寸来适宜选择。
42.此处,将作为本发明的散热板材的一实施方式的、散热板材的横剖面的光学显微镜照片的一例示于图1及图2中。另外,将表示作为本发明的散热板材的一实施方式的散热板材的芯材(低热膨胀材)的配置结构的照片的一例示于图3中。图1及图2所示的散热板材10中,作为低热膨胀部的芯材12为19根,y方向上的长度为8mm,z方向上的长度为3mm。图2所示的散热板材20中,作为低热膨胀部的芯材22为19根,y方向上的长度为8mm,z方向上的长度为3mm。图3所示的散热板材30中,作为低热膨胀部的芯材32为7根。再者,图3所示的散热板材30是通过蚀刻来去除作为高热传导部的线材31的一部分并使配置于线材31的内部的作为低热膨胀部的芯材32部分露出而成。
43.图1所示的散热板材10包括包含高热膨胀材的线材11(高热传导部)、以及包含低热膨胀材的多个芯材12(低热膨胀部)。散热板材10是将19根芯材12配置于线材11的内部而成的19芯结构的散热板材。构成散热板材10的多个芯材12分别在线材11的x方向上呈直线状连续地配置,并且在线材11的x方向、y方向及z方向上彼此不接触地配置。再者,散热板材10的x方向对应于压延方向,y方向对应于与压延方向垂直的宽度方向。
44.图2所示的散热板材20包括包含高热膨胀材的线材21(高热传导部)、以及包含低热膨胀材的多个芯材22(低热膨胀部)。散热板材20是将19根芯材22配置于线材21的内部而成的19芯结构的散热板材。构成散热板材20的多个芯材22分别在线材21的x方向上呈直线状连续地配置,并且在线材21的x方向、y方向及z方向上彼此不接触地配置。再者,散热板材20的x方向对应于压延方向,y方向对应于与压延方向垂直的宽度方向。
45.图3所示的散热板材30包括包含高热膨胀材的线材31(高热传导部)、以及包含低热膨胀材的多个芯材32(低热膨胀部)。散热板材30是7根芯材32配置于线材31的内部而成的7芯结构的散热板材。构成散热板材30的多个芯材32分别在线材31的x方向上呈直线状连
续地配置,并且在线材31的x方向、y方向及z方向上彼此不接触地配置。再者,散热板材30的x方向对应于压延方向,y方向对应于与压延方向垂直的宽度方向。
46.构成所述散热板材10、散热板材20及散热板材30的作为高热传导部的线材11、线材21及线材31均包含高热传导材,作为高热传导材,例如可使用cu(纯铜)、cu合金、al(纯铝)或al合金等。另外,也可使用相对于cu或al而例如包含0.01质量%以上且3.0质量%以下的ag(银)、或者包含0.01质量%以上且0.50质量%以下的zr(锆)的cu合金或al合金等。关于表示高热传导特性的热传导率,例如cu为约400w/(m
·
k),al为约240w/(m
·
k)。仅作参考,不锈钢的热传导率为约85w/(m
·
k)至约90w/(m
·
k)。因此,构成散热板材10、散热板材20及散热板材30的作为高热传导部的线材11、线材21及线材31优选为包含cu或cu合金,可获得效率良好地进行来自半导体元件的散热的具有优异的高热传导特性、即大的热传导率的散热板。另外,包含cu或cu合金的线材11、线材21及线材31与焊料的润湿性良好,因此优选。
47.构成散热板材10、散热板材20及散热板材30的作为低热膨胀部的多个芯材12、芯材22及芯材32包含低热膨胀材。作为低热膨胀材,例如可使用以质量%计的fe
‑
36%ni(合金36)、fe
‑
42%ni(合金42)或fe
‑
29%ni
‑
17%co等低热膨胀材。关于表示低热膨胀特性的线膨胀率,构成半导体元件的所述半导体材料(si、sic、gan、gaas等)为2
×
10
‑6(1/k)至6
×
10
‑6(1/k),相对于此,例如,fe
‑
36%ni为2
×
10
‑6(1/k)以下,fe
‑
42%ni为约6
×
10
‑6(1/k),fe
‑
29%ni
‑
17%co为约5
×
10
‑6(1/k)。仅作参考,cu的线膨胀率为约17
×
10
‑6(1/k)。因此,构成散热板材10的作为低热膨胀部的多个芯材12优选为包含fe
‑
ni系合金,可获得难以对半导体元件赋予过剩的热应力畸变的具有优异的低热膨胀特性、即与半导体材料更接近的线膨胀率的散热板。再者,就更接近构成半导体元件的半导体材料的线膨胀率的观点而言,也可将线膨胀率为7
×
10
‑6(1/k)以下的包含cr、mo、w等的单一金属材用作多个芯材12、芯材22及芯材32,也可将所述fe
‑
ni系合金与单一金属适宜组合来用作多个芯材12、芯材22及芯材32。
48.在所述散热板中,为了具有相应的低热膨胀特性、同时缓和平面方向(x方向和/或y方向)与厚度方向(z方向)的高热传导特性的各向异性,优选为使用包含高热传导材的高热传导部(例如,图1所示的线材2)、与包含低热膨胀材的多个低热膨胀部(例如,图1所示的多个芯材3)的配置结构经适当地设定的散热板材。就所述观点而言,规定长度的散热板材及使用其的散热板优选为在将构成所述散热板材的高热传导部的体积设为v1、将多个低热膨胀部的体积设为v2时,满足v1/(v1 v2)为25体积%以上且80体积%以下。关于所述方面,图1所示的散热板材10的v1/(v1 v2)为约67体积%,图2所示的散热板材20的v1/(v1 v2)为约51体积%,因此,均具有相应的低热膨胀特性,同时可缓和平面方向(x方向和/或y方向)与厚度方向(z方向)的高热传导特性的各向异性。
49.在散热板材及使用其的散热板中,通常,适于构成高热传导部的高热传导材虽然热传导率大,但线膨胀率大,另外,适于构成多个低热膨胀部的低热膨胀材虽然线膨胀率小,但热传导率小。因此,若包含高热传导材的高热传导部的体积比过小,则散热板的热传导特性降低,从半导体元件释放热的散热功能变得不充分的可能性提高,因此优选为v1/(v1 v2)为35体积%以上。再者,若散热板的v1/(v1 v2)超过80体积%,则包含低热膨胀材的多个低热膨胀部的体积比过度变小,散热板的热膨胀特性降低,因此,半导体元件与散热
板的例如包含焊料的接合部损坏的可能性提高。另外,就使散热板的线膨胀率更接近构成半导体元件的半导体材料的线膨胀率的观点而言,优选为v1/(v1 v2)为80体积%以下。根据此种理由,优选为散热板材及使用其的散热板的v1/(v1 v2)为35体积%以上且80体积%以下。
50.如上所述,关于散热板材,在作为高热传导部的线材的内部,作为低热膨胀部的多个芯材在x方向上呈直线状连续地配置,并且在x方向、y方向及z方向上彼此不接触地配置。由此,散热板材在x方向上的全长中成为多个芯材(低热膨胀部)在x方向上呈直线状连续的结构,并且成为多个芯材(低热膨胀部)在y方向及z方向上不连续的结构。具有所述结构的散热板材通过包含高热传导材的线材(高热传导部)而可在x方向上确保充分的高热传导特性,且可在y方向及z方向上确保相应的高热传导特性。同时,具有所述结构的散热板材通过包含低热膨胀材的多个芯材(低热膨胀部)而可在x方向上确保充分的低热膨胀特性,且可在y方向及z方向上确保相应的低热膨胀特性。通过使用此种散热板材,此外,通过v1/(v1 v2)为35体积%以上且80体积%以下,能够充分缓和所述散热板的z方向上的高热传导特性的各向异性。因此,散热板材及使用其的散热板例如可用于安装电力用功率半导体元件、高频设备、cpu等半导体元件等,且对于其他的要求高热传导特性及低热膨胀特性的用途而言也有用。
51.接着,适宜参照附图对本发明的散热板材的制造方法进行说明。再者,本发明的散热板材并不限定于应用以下叙述的散热板材的制造方法的散热板材。
52.首先,对本发明的第一方面的散热板材的制造方法进行说明。
53.本发明的第一方面的散热板材的制造方法包括:
54.(1)准备工序,准备包含高热传导材且在长边方向上具有多个孔的线材、以及包含低热膨胀材的多个芯材;
55.(2)复合化工序,将多个芯材以填埋线材的多个孔各孔的方式插入,由此将多个芯材在线材的长边方向上呈直线状连续地配置、并且以在线材的长边方向、宽度方向及厚度方向上彼此不接触的方式配置,由此制作复合原线材,通过对复合原线材进行伸展加工而获得复合线材;以及
56.(3)压延工序,对复合线材进行压延而成形为板状。
57.在本发明的第一方面的散热板材的制造方法中,进行所述(1)的工序、即准备工序,准备包含高热传导材且在长边方向上具有多个孔的线材、以及包含低热膨胀材的多个芯材。再者,线材及多个芯材也可进行软化退火等热处理。包含高热传导材的线材是构成散热板材的高热传导部的主材,可具有圆形形状、椭圆形形状或多边形形状的横剖面。例如,图4所示的线材2具有圆形形状的横剖面。包含低热膨胀材的多个芯材是构成散热板材的低热膨胀部的主材,可具有圆形形状、椭圆形形状或多边形形状的横剖面。例如,图4所示的多个芯材3具有圆形形状的横剖面。再者,位于线材2的中心部分的芯材3a的有无并无特别限制。在所述工序中所准备的线材2,设置有用于插入多个芯材3的多个孔2a。多个孔2a的配置结构是在线材2的x方向上呈直线状连续,并且在线材2的x方向、y方向及z方向上彼此不接触。另外,孔2a的横剖面的形状只要分别是可插入芯材3的形状即可,为了更顺畅地进行芯材3的插入而优选为与芯材3的横剖面的形状对应。
58.接着,进行所述(2)的工序、即复合化工序,将多个芯材以填埋线材的多个孔各孔
的方式插入,由此将多个芯材在线材的长边方向上呈直线状连续地配置、并且以在线材的长边方向、宽度方向及厚度方向上彼此不接触的方式配置,由此制作复合原线材,通过对复合原线材进行伸展加工而获得复合线材。具体而言,例如,将图4所示的多个芯材3以填埋图4所示的线材2的多个孔2a各孔的方式插入至多个孔2a。此时,根据多个孔2a的所述配置结构,多个芯材3在线材2的x方向上呈直线状连续地配置,且以在线材2的x方向、y方向及z方向上彼此不接触的方式配置。由此,获得如图4所示的那样的复合原线材5。进而,通过对所述复合原线材5进行伸展加工,而制作成形为例如图3所示的散热板材30之前的规定尺寸的复合线材。
59.在所述(2)的工序中,为了通过对复合原线材5进行伸展加工而获得复合线材,例如,能够应用冷挤压加工、热静水压挤压加工、冷拉拔加工及热拉拔加工等伸展加工。另外,也能够在所述伸展加工后,进一步进行相同种类或不同种类的伸展加工,由此获得更小径化的复合线材。另外,在伸展加工的期间内,也可适宜地追加软化退火等热处理工序。再者,图3所示的散热板材30为具有7根芯材32的7芯结构,但构成本发明的散热板材的芯材的根数并无特别限制。芯材的根数可出于如下目的来适宜选择:与作为散热对象的半导体元件的尺寸相符;调整为与半导体元件的线膨胀率近似的线膨胀率。
60.接着,进行所述(3)的工序、即压延工序,对复合线材进行压延而成形为板状。具体而言,对在所述(2)的工序中所制作的规定尺寸的复合线材进行压延而成形为板状,由此,最终制作规定尺寸的散热板材。例如,制作图3所示的散热板材30等。在所述工序中,关于针对复合线材的压延,只要在最终所制作的散热板材的横剖面中,多个芯材(芯材3)分别在线材(线材2)的x方向上呈直线状连续地配置、并且以在线材(线材2)的x方向、y方向及z方向上彼此不接触的方式配置,则并无特别限制。针对复合线材的压延例如可根据复合线材的调质状态来调整压延条件(温压延、冷压延、压下率、压延速度、压延负荷、道次数等),也可分为多次反复进行,也可适时进行软化退火等热处理。
61.接着,对本发明的第二方面的散热板材的制造方法进行说明。
62.本发明的第二方面的散热板材的制造方法包括:
63.(1a)准备工序,准备包含高热传导材的管、以及在包含高热传导材的多个中空线材的各中空部插入包含低热膨胀材的多个芯材而成的多个复合芯材;
64.(2a)复合化工序,将多个复合芯材以填埋管的中空部的方式插入,由此将多个芯材在管的长边方向上呈直线状连续地配置、并且以在管的长边方向、宽度方向及厚度方向上彼此不接触的方式配置,由此制作复合原线材,通过对复合原线材进行伸展加工而获得复合线材;以及
65.(3a)压延工序,对复合线材进行压延而成形为板状。
66.在本发明的第二方面的散热板材的制造方法中,进行所述(1a)的工序、即准备工序,准备包含高热传导材的管、以及在包含高热传导材的多个中空线材的各中空部插入包含低热膨胀材的多个芯材而成的多个复合芯材。再者,管、中空线材及多个芯材也可进行软化退火等热处理。此处,包含高热传导材的管是构成散热板材的高热传导部的主材,可具有圆形形状、椭圆形形状或多边形形状的横剖面。例如,图5所示的管2p为具有圆形形状的横剖面的圆形管。包含高热传导材的多个中空线材是与管一起构成散热板材的高热传导部的主材,可具有圆形形状、椭圆形形状或多边形形状的横剖面。例如,图5所示的多个中空线材
2s是具有环状六边形形状的横剖面的六边形管。包含低热膨胀材的多个芯材是构成散热板材的低热膨胀部的主材,可具有圆形形状、椭圆形形状或多边形形状的横剖面。例如,图5所示的多个芯材3s具有与中空线材2s的中空部的横剖面的形状对应的六边形形状的横剖面(参照横剖面的放大图)。再者,图5所示的管2p的横剖面的形状为圆筒形状,多个中空线材2s及多个芯材3s的横剖面的形状为六边形形状,但在构成本发明的散热板材时,并无特别限制。
67.另外,在所述(1a)的工序中,如图5所示,准备在包含高热传导材的中空线材2s的中空部插入包含低热膨胀材的芯材3s而成的复合芯材4s(参照横剖面的放大图)。具体而言,例如,通过伸展加工,使在1根中空线材的中空部插入1根芯材而成者长地延展,之后,切断为规定长度,由此,制成如图5所示的那样的在多个中空线材2s的中空部插入芯材3s而成的多个复合芯材4s。
68.接着,进行所述(2a)的工序、即复合化工序,将多个复合芯材以填埋管的中空部的方式插入,由此将多个芯材在管的长边方向上呈直线状连续地配置、并且以在管的x方向、y方向及z方向上彼此不接触的方式配置,由此制作复合原线材,通过对复合原线材进行伸展加工而获得复合线材。具体而言,例如,如图5所示,制成将多个复合芯材4s加以组合而插入至管2p的中空部,并由多个复合芯材4s填埋管2p的中空部的那样的配置结构。此时,若复合芯材4s的横剖面的形状为多边形形状(图5的情况下为六边形形状),则可使多个复合芯材4s彼此无间隙地邻接,因此优选。再者,为了进一步减小将多个复合芯材4s加以组合时的外围形状与管2p的内周形状之间的间隙,也可插入与管2p为相同材质的虚设材或与中空线材2s为相同材质的虚设材,也可将管2p的内周形状设为与将多个复合芯材4s加以组合时的外围形状对应的形状。
69.根据多个复合芯材4s的所述配置结构,多个复合芯材4s在管2p的x方向上呈直线状连续地配置,且构成多个复合芯材4s的多个中空线材2s及多个芯材3s也在管2p的x方向上呈直线状连续地配置。由此,多个芯材3s在管2p的x方向上呈直线状连续地配置,且以在管2p的x方向、y方向及z方向上彼此不接触的方式配置。由此,可获得如图5所示的那样的复合原线材5s。进而,通过对所述复合原线材5s进行伸展加工,例如,可制作成形为图1及图2所示的散热板材10及散热板材20之前的规定尺寸的复合线材。
70.在所述(2a)的工序中,为了通过对复合原线材5s进行伸展加工而获得复合线材,例如,能够应用冷挤压加工、热静水压挤压加工、冷拉拔加工及热拉拔加工等伸展加工。另外,也能够在所述伸展加工后,进一步进行相同种类或不同种类的伸展加工,由此获得更小径化的复合线材。另外,在伸展加工的期间内,也可适宜地追加软化退火等热处理工序。再者,图1及图2所示的散热板材10及散热板材20为具有19根芯材12及芯材22的19芯结构,但构成本发明的散热板材的芯材的根数并无特别限制。芯材的根数可出于如下目的来适宜选择:与作为散热对象的半导体元件的尺寸相符;调整为与半导体元件的线膨胀率近似的线膨胀率。
71.接着,进行所述(3a)的工序、即压延工序,对复合线材进行压延而成形为板状。具体而言,对在所述(2a)的工序中所制作的规定尺寸的复合线材进行压延而成形为板状,由此,最终制作规定尺寸的散热板材。例如,制作图1及图2所示的散热板材10及散热板材20等。在所述工序中,关于针对复合线材的压延,只要在最终所制作的散热板材的横剖面中,
多个芯材(芯材3s)分别在管(管2p)的x方向上呈直线状连续地配置、并且以在管(管2p)的x方向、y方向及z方向上彼此不接触的方式配置,则并无特别限制。针对复合线材的压延例如可根据复合线材的调质状态来调整压延条件(温压延、冷压延、压下率、压延速度、压延负荷、道次数等),也可分为多次反复进行,也可适时进行软化退火等热处理。
72.图6中表示通过所述(2a)的工序获得的复合线材的横剖面的一例。图6所示的复合线材6s是成形为图1所示的散热板材10之前的规定尺寸的19芯结构的复合线材。所述复合线材6s的横剖面是将复合线材6s在x方向上的任意位置切断而成。所述复合线材6s的高热传导部2c是由管2p及多个中空线材2s构成,高热传导部2c的v1/(v1 v2)为67体积%。所述复合线材6s被配置为:由多个芯材3s构成的低热膨胀部3c在横剖面(y方向及z方向)中彼此不接触,并且低热膨胀部3c在x方向上呈直线状连续。再者,v1/(v1 v2)在经过所述(3a)的工序后也没有发生变化。因此,通过所述(3a)的工序对v1/(v1 v2)为67体积%的复合线材6s进行压延而获得的、规定尺寸的散热板材的v1/(v1 v2)也为67体积%。
73.以下,适宜参照附图对实施例(本发明例)进行说明。具体而言,利用本发明的第二方面的所述散热板材的制造方法制作图1及图2所示的散热板材10及散热板材20。然后,使用从散热板材10及散热板材20切出的单片(散热板),求出线膨胀率及热传导率。
74.首先,制作散热板材10。具体而言,准备如图5所示的那样的、无氧铜制的管2p(外径28mm、内径25mm、长度180mm)、与无氧铜制的中空线材2s(外径14mm、内径10.3mm、长度500mm)、以及合金36制的芯材3s(外径10mm、长度500mm)。然后,在中空线材2s的中空部插入芯材3s,通过伸展加工,于在x方向上延展的同时小经化,进而,使用对边距离为4.75mm的六边模具形成为六边形形状的横剖面,制作长条的复合芯材4s。继而,将长条的复合芯材4s在x方向上切分,准备19根复合芯材4s(长度150mm)。
75.接着,将19根复合芯材4s捆扎后插入至管2p。在管2p的内周面与19根复合芯材4s的间隙中,以填埋所述间隙的方式,插入与中空线材2s为相同材质的线材(虚设材)。由此,填埋管2p的内部间隙,将填充率设为90%以上。继而,在管2p的x方向上的一端嵌入铜插塞并加以铆接,在另一端嵌入铁插塞并加以铆接,由此,在管2p内部密封19根复合芯材4s,制成伸展加工用坯料(billet)。由此,所述坯料变成如下坯料:在其内部,多个芯材3s在管的x方向上呈直线状连续地配置,且以在管2p的x方向、y方向及z方向上彼此不接触的方式配置。
76.接着,一边将所述坯料加热至400℃,一边通过伸展加工使其在x方向上延展并小径化(直径12mm),制作复合原线材5s。对所述复合原线材5s进一步进行伸展加工,使其小径化(直径6mm),制作复合线材6s。接着,对直径6mm的复合线材6s进行在600℃下保持1小时的热处理使其软化,之后进行压延而成形为板状。由此,获得厚度为约3mm、宽度为约8mm的图1所示的散热板材10。再者,所述散热板材10的v1/(v1 v2)为67体积%。以下,将从散热板材10切出的单片(试验体:厚度3mm、宽度8mm、长度8mm)称为样品a。
77.同样地,制作厚度为约3mm、宽度为约8mm的图2所示的散热板材20。所述散热板材20的v1/(v1 v2)为51体积%。再者,关于散热板材20的制造方法,除了在准备如图5所示的那样的无氧铜制的中空线材2s时将其外径变更为12mm以外,经过与所述散热构件10的制造方法相同的工序,因此参照所述散热板材10的制造方法,省略此处的说明。以下,将从散热板材20切出的单片(试验体:厚度3mm、宽度8mm、长度8mm)称为样品b。
78.同样地,制作厚度为约1.5mm、宽度为约10mm的图7所示的散热板材40c(线材41、芯材42)。关于散热板材40c,除了将构成如图5所示的那样的复合原线材5s的复合芯材4s设为31根、以散热板材的v1/(v1 v2)成为约65体积%的方式调整各构件的尺寸、以成为直径6mm的复合线材6s的方式进行伸展加工以外,经过与所述散热构件10的制造方法相同的工序,因此参照所述散热板材10的制造方法,省略此处的说明。以下,将从散热板材40c切出的单片(试验体:厚度1.5mm、宽度10mm、长度10mm)称为样品c。
79.同样地,将复合芯材4s设为31根,以散热板材的v1/(v1 v2)成为约65体积%的方式调整各构件的尺寸,并以成为直径5mm的复合线材6s的方式进行伸展加工,制作厚度为约1.3mm、宽度为约9mm的散热板材40d。以下,将从散热板材40d切出的单片(试验体:厚度1.3mm、宽度9mm、长度9mm)称为样品d。
80.同样地,将复合芯材4s设为31根,以散热板材的v1/(v1 v2)成为约65体积%的方式调整各构件的尺寸,并以成为直径4mm的复合线材6s的方式进行伸展加工,制作厚度为约1.1mm、宽度为约8mm的散热板材40e。以下,将从散热板材40e切出的单片(试验体:厚度1.1mm、宽度8mm、长度8mm)称为样品e。
81.同样地,制作厚度为约1.5mm、宽度为约10mm的图8所示的散热板材50f(线材51、芯材52)。关于散热板材50f,除了将构成如图5所示的那样的复合原线材5s的复合芯材4s设为55根、以散热板材的v1/(v1 v2)成为约60体积%的方式调整各构件的尺寸、以成为直径6mm的复合线材6s的方式进行伸展加工以外,经过与所述散热构件10的制造方法相同的工序,因此参照所述散热板材10的制造方法,省略此处的说明。以下,将从散热板材50f切出的单片(试验体:厚度1.5mm、宽度10mm、长度10mm)称为样品f。
82.同样地,将复合芯材4s设为55根,以散热板材的v1/(v1 v2)成为约60体积%的方式调整各构件的尺寸,并以成为直径5mm的复合线材6s的方式进行伸展加工,制作厚度为约1.3mm、宽度为约9mm的散热板材50g。以下,将从散热板材50g切出的单片(试验体:厚度1.3mm、宽度9mm、长度9mm)称为样品g。
83.同样地,将复合芯材4s设为55根,以散热板材的v1/(v1 v2)成为约60体积%的方式调整各构件的尺寸,并以成为直径4mm的复合线材6s的方式进行伸展加工,制作厚度为约1.1mm、宽度为约8mm的散热板材50h。以下,将从散热板材50h切出的单片(试验体:厚度1.1mm、宽度8mm、长度8mm)称为样品h。
84.接着,求出利用所述制造方法制作的散热板材10及散热板材20的线膨胀率。具体而言,使用热膨胀测定装置(理学(rigaku)制造,型号tg8120),使用从散热板材10及散热板材20切出的试验体(样品a、样品b),分别求出从25℃到250℃的温度范围内的x方向及y方向上的线膨胀率。在试验体的x方向上的线膨胀测定中,从试验体的x方向以100n的力按压位移测定用元件(石英棒),在此状态下,从25℃升温到250℃,测定试验体的x方向上的位移量(热膨胀量)。在试验体的y方向上的线膨胀测定中,从试验体的y方向以100n的力按压位移测定用元件(石英棒),在此状态下,从25℃升温到250℃,测定试验体的y方向上的位移量(热膨胀量)。然后,用试验体相对于温度变化的位移量(热膨胀量)除以试验体的长度,进而除以温度变化量,求出线膨胀率。另外,同样地,根据从散热板材40c、散热板材40d、散热板材40e、散热板材50f、散热板材50g及散热板材50h切出的试验体(样品c、样品d、样品e、样品f、样品g及样品h)的相对于从28℃至200℃的温度变化的位移量(热膨胀量),求出各自的线
膨胀率。将其结果示于表1及图9中。
85.[表1]
[0086][0087]
如表1所示,样品a的线膨胀率在x方向上为约6.3
×
10
‑6(1/k),在y方向上为约11.4
×
10
‑6(1/k)。另外,样品b的线膨胀率在x方向上为约5.4
×
10
‑6(1/k),在y方向上为约9.1
×
10
‑6(1/k)。另外,样品c的线膨胀率在x方向上为约10.2
×
10
‑6(1/k),在y方向上为约12.3
×
10
‑6(1/k)。另外,样品d的线膨胀率在x方向上为约9.7
×
10
‑6(1/k),在y方向上为约11.5
×
10
‑6(1/k)。另外,样品e的线膨胀率在x方向上为约9.5
×
10
‑6(1/k),在y方向上为约11.1
×
10
‑6(1/k)。另外,样品f的线膨胀率在x方向上为约7.5
×
10
‑6(1/k),在y方向上为约11.6
×
10
‑6(1/k)。另外,样品g的线膨胀率在x方向上为约7.8
×
10
‑6(1/k),在y方向上为约11.5
×
10
‑6(1/k)。另外,样品h的线膨胀率在x方向上为约7.1
×
10
‑6(1/k),在y方向上为约11.2
×
10
‑6(1/k)。
[0088]
另外,图9是一并记载并表示样品a的x方向及y方向上的热膨胀测定结果、与样品b的x方向及y方向上的热膨胀测定结果的图表。通过所述图表中所示的x方向与y方向的比较,得知x方向上的热膨胀量(位移量)小于y方向上的热膨胀量(位移量)。所谓x方向,即是指作为低热膨胀部的合金36制的芯材3s呈直线状连续地配置的方向,所谓y方向,即是指作为低热膨胀部的合金36制的芯材3s彼此不接触地配置的方向。因此,确认到:通过样品a及样品b均是作为低热膨胀部的包含合金36的多个芯材3s呈直线状连续地配置的结构,而x方向上的热膨胀量变小。
[0089]
关于热膨胀量,通过所述图表中所示的样品a与样品b的比较,得知样品b比样品a小。如表1所示,样品b的表示高热传导部的体积比的v1/(v1 v2)为51体积%,比67体积%的样品a小。换句话说,样品b的低热膨胀部的体积比大于样品a。由此,确认到:通过适当地设定构成散热板材的高热传导部与低热膨胀部的体积比,而通过低热膨胀部所发挥的低热膨胀特性缓和高热传导部所发挥的高热膨胀特性。
[0090]
在本发明中,作为表示散热板材的平面方向(x方向、y方向)上的热膨胀特性的各向异性的指标,导入用x方向上的线膨胀率除以y方向上的线膨胀率而得的值(以下,将所述值称为“ais”)。ais越接近1,是指线膨胀率的平面方向(x方向、y方向)上的各向异性越小。如表1所示,例如,样品a的ais为约0.55,样品b的ais为约0.59。根据所述结果,得知,样品a与样品b的线膨胀率的平面方向(x方向、y方向)上的各向异性大致同等。同样地,求出样品c、样品d、样品e、样品f、样品g及样品h的ais,结果,如表1所示,样品c~样品e的ais为0.83~0.86,样品f~样品g的ais为0.63~0.68。根据所述结果,得知,样品c与样品d及样品e的线膨胀率的平面方向(x方向、y方向)上的各向异性大致同等,样品f与样品g及样品h的线膨胀率的平面方向(x方向、y方向)上的各向异性大致同等。另外,得知,芯材为31根的样品c~
样品e与芯材为10根的样品a、样品b及芯材为55根的样品f~样品h相比,ais接近1。如此,通过导入ais,能够评价散热板材的各向异性。
[0091]
根据所述内容,确认到:散热板材的热膨胀特性的各向异性(ais)可通过调整构成低热膨胀部的芯材的根数、内包芯材的复合线材的直径、由v1/(v1 v2)求出的高热膨胀部的体积比例来缓和。而且,判明:优选为尤其是在散热板材的制造阶段,对将构成散热板材的低热膨胀部的芯材内包的复合线材的直径适当地进行调整。
[0092]
接着,求出利用所述制造方法制作的散热板材10及散热板材20的热传导率。为了求出热传导率,首先,使用从散热板材10及散热板材20切出的、厚度3mm、宽度8mm、长度8mm的试验体(样品a、样品b),分别测定电阻。在样品a的情况下,电阻的测定是构成以样品a为中心层的7层结构的被测定部来进行。具体而言,在样品a的z方向上的两面接触配置电压端子用的铜箔(厚度0.02mm),在各铜箔的与样品a为相反侧的表面接触配置接触电阻减低用的锡箔(厚度0.1mm),进而,在各锡箔的与样品a为相反侧的表面接触配置电流端子用的铜板(厚度0.2mm)。然后,从层叠方向适当地对所述被测定部进行加压,制成样品a、铜箔、锡箔及铜板相互充分密接的状态。在所述状态下,对被测定部的铜板之间施加5a的电流,测定25℃下的铜箔之间的电压。再者,样品b的情况也同样如此。结果,电阻r在样品a的z方向上为约1.16
×
10
‑6ω,在样品b的z方向上为约1.56
×
10
‑6ω。
[0093]
继而,通过r=ρ
·
l/s求出电阻率ρ(ω
·
m)。再者,r为电阻(ω),l为样品厚度(3mm),s为样品面积(8mm
×
8mm)。然后,根据魏德曼
‑
弗朗茨(wiedemann
‑
frantz)法则(ρk=lt)求出样品a及样品b的x方向上的热传导率k(w/(m
·
k))。再者,ρ为电阻率(ω
·
m),l为玻尔兹曼常数(boltzmann constant),t为绝对温度(k)。结果,关于样品a,在z方向上,25℃下的电阻率ρ为约2.47
×
10
‑8ω
·
m,由此,热传导率k为约270w/(m
·
k)。另外,关于样品b,在z方向上,25℃下的电阻率ρ为约3.33
×
10
‑8ω
·
m,由此,热传导率k为约200w/(m
·
k)。
[0094]
在所述样品a及样品b中,z方向上的热传导率为约200w/(m
·
k)至约270w/(m
·
k)。相对于此,在现有的散热板材(将高热膨胀材的体积比设为68体积%的cic包层材的变形例)中,如上所述,z方向上的热传导率为221w/(m
·
k)。因此,确认到:样品a及样品b的z方向上的高热传导特性与现有的散热板材同等或在其以上。另外,在所述样品a及样品b中,x方向上的线膨胀率为约5.4
×
10
‑6(1/k)至约6.3
×
10
‑6(1/k),y方向上的线膨胀率为约9.1
×
10
‑6(1/k)至约11.4
×
10
‑6(1/k)。相对于此,在现有的散热板材(将高热膨胀材的体积比设为68体积%的cic包层材的变形例)中,如上所述,平面方向(x方向和/或y方向)上的线膨胀率为11.9
×
10
‑6(1/k)。因此,确认到:样品a及样品b的x方向上的低热膨胀特性提高到现有的散热板材的约1.9倍至约2.2倍,y方向上的低热膨胀特性提高到现有的散热板材的约1.0(大致同等)至约1.3倍。因此,判明,本发明的散热板材具有相应的低热膨胀特性、同时缓和平面方向(x方向、y方向)与厚度方向(z方向)的高热传导特性的各向异性。
[0095]
再者,所述样品a及样品b由于x方向与y方向的线膨胀率有差异,因此平面方向上的低热膨胀特性产生各向异性(以ais计为约0.55至0.59)。关于此方面,极其有意义是所述样品a及样品b在与以前的散热板材的对比中x方向上的低热膨胀特性充分提高的方面。就所述观点而言,即便平面方向上的低热膨胀特性具有所述各向异性,由于具有相应的低热膨胀特性、同时缓和了平面方向(x方向、y方向)与厚度方向(z方向)的高热传导特性的各向异性,因此,在实用上,也为能够作为所述半导体元件的散热板来充分应用的水准。
[0096]
符号的说明
[0097]
<图1~图3>
[0098]
10.散热构件、11.线材、12.芯材
[0099]
20.散热板材、21.线材、22.芯材
[0100]
30.散热板材、31.线材、32.芯材
[0101]
<图4>
[0102]
2.线材、2a.孔、3.芯材、3a.芯材、5.复合原线材
[0103]
<图5>
[0104]
2p.管、2s.中空线材、3s.芯材、4s.复合芯材、5s.复合原线材
[0105]
<图6>
[0106]
2c.高热传导材部、3c.低热膨胀材部、6s.复合芯材
[0107]
<图7、图8>
[0108]
40c.散热板材、41.线材、42.芯材
[0109]
50f.散热板材、51.线材、52.芯材
再多了解一些
本文用于企业家、创业者技术爱好者查询,结果仅供参考。