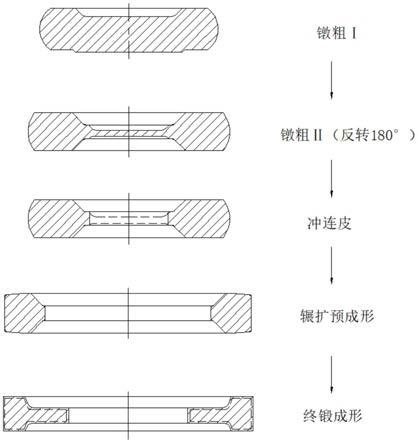
1.本发明涉及锻造技术领域,具体涉及一种主减齿毛坯的辗扩制坯终锻成型工艺。
背景技术:
2.所有燃油汽车的前驱车型和新能源汽车的驱动电机输出端都带有一套圆柱齿轮的主减速器,其目的是降低转速、增大扭矩,而主减速齿轮(简称“主减齿”)是一个带有较宽轮辐的圆柱斜齿轮。图1所示主减齿的锻造毛坯,主减齿采用锻件毛坯制作,由于主减齿总体厚度较薄,轮辐厚度通常为8mm
‑
13mm,而且直径也较大,最大外径在250mm左右。常规的锻造工艺如下:锯切下料
→
加热
→
镦粗
→
终锻成形
→
冲连皮。在采用常规锻造工艺进行模锻时,必须采用较大锻造力的设备,终锻成形工序中往往采用双击方式,而且由于打击力大,对设备的伤害较为严重。
3.由于受设备打击力的限制,毛坯的棱角处会出现充不满及连皮太薄打不动的情况,为保证机加工后的车坯质量及车削表面不留黑皮,必须适当增加加工余量及连皮的厚度。在1600t电动螺旋压力机进行终锻时,其连皮厚度需要达到11mm才能基本保证一次打击成形。传统工艺毛坯的重量为6.37kg,连皮重量为0.79kg,下料重量为7.31kg。
4.如果要减轻毛坯重量,增强市场竞争力,采用传统工艺就只能增大设备吨位,而提高一级设备的吨位,也就是采购2500t的电动螺旋压力机,其价格大约是1600t电动螺旋压力机的2.5倍,约为450万。
技术实现要素:
5.为降低主减齿毛坯成形所需的打击力、减轻毛坯重量、提高毛坯质量,需要另辟蹊径进行工艺革新,增加最小的设备投入,达到同样的锻造效果。
6.为此,本发明所采用的技术方案为:一种薄壁宽轮幅主减齿毛坯辗扩制坯终锻成型工艺,包括:步骤a、下料;步骤b、加热到1150℃以上的锻造温度;步骤c、镦粗及冲连皮;步骤d、辗扩预成型;步骤e、终锻成型;
7.所述步骤c中使用400t闭式单点压力机的三工位快换制坯模,所述三工位快换制坯模包括下模板、上模板,以及在下模板与上模板之间依次间隔设置的第一镦粗模、第二镦粗模和第三冲连皮模;所述第一镦粗模包括一工位下模座、一工位下模、一工位上模座、一工位上模、下模压紧圈、上模压紧圈,第二镦粗模包括二工位下模座、二工位下模、二工位上模座、二工位上模、下模压紧圈、上模压紧圈,第三冲连皮模包括三工位下模座、三工位冲连皮下模、三工位上模座、三工位冲连皮冲头、下模压紧圈、上模压紧圈;
8.所述一工位下模座、二工位下模座、三工位下模座的外壁均带有锥度,分别通过各自的下模压紧圈结合螺栓固定安装在下模板上方,一工位下模位于一工位下模座上方,并通过底部的圆柱凸起螺接在一工位下模座的中间孔内,二工位下模位于二工位下模座的上方,并通过底部的圆柱凸起螺接在二工位下模座的中间孔内,三工位冲连皮下模通过螺栓固定安装在三工位下模座上方;
9.所述一工位上模座、二工位上模座、三工位上模座的外壁带有锥度,分别通过各自的上模压紧圈结合螺栓固定安装在上模板下方,一工位上模位于一工位上模座的下方,并通过顶部的圆柱凸起螺接在一工位上模座的中间孔内,二工位上模位于二工位上模座的下方,并通过顶部的圆柱凸起螺接在二工位上模座的中间孔内,三工位冲连皮冲头的顶部通过中心螺栓固定安装在三工位上模座的下方;
10.所述一工位下模的顶部居中设置有比步骤a中使用的料棒直径大2%的圆形定位坑,且圆形定位坑根部角为钝角以防止镦粗时形成折叠或夹层;所述一工位上模的底部、二工位上模的底部、二工位下模的顶部分别设置有冲压凸台;所述三工位下模座顶部居中开有连皮接料仓,连皮接料仓底部开有斜向下接料滑道,连皮接料仓的一侧水平开有防堵清理孔,三工位冲连皮下模上开有上下贯通的中间孔,三工位冲连皮下模的顶部设置有定位凸台,当第三冲连皮模合模时,三工位冲连皮冲头落入三工位冲连皮下模的中间孔内;
11.在步骤c中,将加热后出炉后的棒料放置在400t闭式单点压力机的三工位快换制坯模的第一镦粗模上,棒料在圆锥形定位坑中定位,启动压力机,滑块下行至设定位置进行镦粗后,滑块返程至初始位置,停止,夹持坯件,将坯件取出;
12.夹持坯件,将坯件上下翻转180
°
,放入400t闭式单点压力机三工位快换制坯模的第二镦粗模上,启动压力机,滑块下行至设定位置进行镦粗后,滑块返程至初始位置,停止,夹持工件,将坯件取出;
13.夹持工件,将坯件放入400t闭式单点压力机的三工位快换制坯模的第三冲连皮模上,启动压力机,滑块下行至设定位置进行冲连皮,冲掉坯件中间连皮后,滑块返程至初始位置,停止,夹持工件,将坯件取出;
14.所述步骤e中使用1600t电动螺旋压力机的终锻成型模,所述终锻成型模包括终锻下模座、三叉形顶块、顶料杆、终锻下模定位座、终锻下成型模、终锻下凸模芯、终锻下模套、终锻下模压紧圈、终锻上模座、终锻上成型模、终锻上模变径圈和终锻上模压紧圈;所述三叉形顶块置于终锻下模座的沉台内,终锻下模定位座、终锻下成型模由下到上依次安装,三叉形顶块的每个叉脚配备有一根所述顶料杆,顶料杆穿过终锻下模定位座抵在终锻下成型模的底部,所述终锻下成型模套在终锻下凸模芯外,终锻下凸模芯通过螺栓固定在终锻下模定位座上,所述终锻下模套套在终锻下成型模外,终锻下模套的底部压在终锻下模定位座的台阶面上,终锻下模套的外壁带有锥度,并通过终锻下模压紧圈结合螺栓固定安装在终锻下模座上;所述终锻上模变径圈通过台阶面套在终锻上成型模外,终锻上模压紧圈通过台阶面套在终锻上模变径圈外,并通过螺栓固定安装在终锻上模座上;当终锻成型模合模时,终锻上成型模伸入终锻下模套内,终锻下凸模芯伸入终锻上成型模内;
15.在步骤e中,将辗扩预成型后的坯件放入1600t电动螺旋压力机终锻成形模中,启动电动螺旋压力机,滑块下行至设定位置打击坯件,使坯件终锻成形后,滑动返程至初始位置,停止,三叉形顶块带动顶料杆向上顶出工件,夹持工件,取出。
16.作为上述方案的优选,所述下模板用于安装一工位下模座、二工位下模座、三工位下模座的沉台内分别设置有下垫板,上模板用于安装一工位上模座、二工位上模座、三工位上模座的沉台内分别设置有上垫板,第三冲连皮模的下垫板与下模板、三工位下模座之间分别设置有不同的定位键。
17.进一步优选为,所述圆形定位坑的高度为2mm,根部角为135
°
。
18.进一步优选为,所述下模板、上模板之间设置有四根呈矩形布置的导向柱。
19.进一步优选为,所述终锻下模座内安装有下垫块,终锻上模座内安装有上垫块,终锻下模定位座抵在下垫块上方,三叉形顶块置于下垫块内,终锻上成型模抵在上垫块下方。
20.本发明的有益效果:(1)采用专用的两次镦粗工艺,并在首次镦粗时采用根部角为钝角的圆形定位坑,既能很好的定位,又能有效避免后续预锻及终锻过程中产生折叠或夹层,提高锻件的质量;(2)三工位快换制坯模能完成两次镦粗和一次冲连皮,只需要更换模具中关键的上模、下模、冲头、冲孔下模,就能满足不同规格尺寸的同类毛坯加工,并且需要更换的零部件采用螺纹或螺钉安装,能实现快速,进一步方便更换;(3)终锻成型模采用上模变径圈及下模压紧圈快速安装更换的结构,方便不同规格尺寸毛坯使用;采用三叉形顶块结合均布的顶料杆,能实现顶料过程中的均匀受力,进一步提高毛坯质量;(4)两次镦粗及一次冲连皮后,再进行辗扩预成型,在终端成型前,内孔已经做出,其锻件的投影面积大幅减小,同时中间薄的连皮部分也不复存在,坯件所需的成形力显著降低,尖角处的充满能力提高,毛坯可以适当减小一定的加工余量,既能达到节约材料的目的,又能避免使用大吨位压力机而增加高昂的设备成本。
附图说明
21.图1为主减齿毛坯的结构示意图。
22.图2为本发明的工艺流程图。
23.图3为三工位快换制坯模的主视图。
24.图4为三工位快换制坯模的俯视图。
25.图5为三工位下模座的剖视图。
26.图6为终锻成型模的主视图。
27.图7为辗扩预成型模的结构示意图。
具体实施方式
28.下面通过实施例并结合附图,对本发明作进一步说明:
29.如图2所示,一种薄壁宽轮幅主减齿毛坯辗扩制坯终锻成型工艺,包括:
30.步骤a、下料;采用棒料进行锯切下料。
31.步骤b、加热到1150℃以上的锻造温度;以不超过1200℃为宜。
32.步骤c、镦粗及冲连皮。
33.步骤d、辗扩预成型;
34.步骤e、终锻成型。
35.其中,其中步骤c分为两次镦粗和一次冲连皮,步骤c中使用400t闭式单点压力机的三工位快换制坯模。
36.结合图3—图5所示,三工位快换制坯模主要由下模板1、上模板2,以及在下模板1与上模板2之间依次间隔设置的第一镦粗模、第二镦粗模和第三冲连皮模组成。
37.第一镦粗模主要由一工位下模座3、一工位下模4、一工位上模座5、一工位上模6、下模压紧圈7、上模压紧圈8组成。
38.第二镦粗模主要由二工位下模座9、二工位下模10、二工位上模座11、二工位上模
12、下模压紧圈7、上模压紧圈8组成。
39.第三冲连皮模主要由三工位下模座13、三工位冲连皮下模14、三工位上模座15、三工位冲连皮冲头16、下模压紧圈7、上模压紧圈8组成。
40.一工位下模座3、二工位下模座9、三工位下模座13的外壁均带有锥度,分别通过各自的下模压紧圈7结合螺栓固定安装在下模板1上方。三个下模压紧圈7能互换,通用性好特别是第一、第二工位的下模圆柱螺纹与下模座内螺纹进行螺纹连接的结构方式,安装更加方便快捷。
41.一工位下模4位于一工位下模座3上方,并通过底部的圆柱凸起螺接在一工位下模座3的中间孔内;二工位下模10位于二工位下模座9的上方,并通过底部的圆柱凸起螺接在二工位下模座9的中间孔内;三工位冲连皮下模14通过螺栓固定安装在三工位下模座13上方。通过螺纹或螺栓连接,能实现快速换装,更换成不同规格毛坯件的制坯模,通用性好,特别是圆柱凸起插入进行螺纹的方式,省去了螺栓,且安装更加方便快捷。
42.一工位上模座5、二工位上模座11、三工位上模座15的外壁均带有锥度,分别通过各自的上模压紧圈8结合螺栓固定安装在上模板2下方。三个上模压紧圈8也能互换,通用性好。
43.一工位上模6位于一工位上模座5的下方,并通过顶部的圆柱凸起螺接在一工位上模座5的中间孔内;二工位上模12位于二工位上模座11的下方,并通过顶部的圆柱凸起螺接在二工位上模座11的中间孔内;三工位冲连皮冲头16的顶部通过中心螺栓固定安装在三工位上模座15的下方。同样采用螺纹或螺栓连接,能实现快速换装,且通用性好。
44.一工位下模4的顶部居中设置有比步骤a中使用的料棒直径大2%的圆形定位坑4a,鉴于工件在加热后有1.5%的热胀冷缩量,同时考虑预留一定余量便于放入工件,圆形定位坑4a比料棒直径大2%。圆形定位坑4a的作用是棒料在模具上的定位,以保证棒料处于模具的中心位置。
45.且圆形定位坑4a根部角为钝角以防止镦粗时形成折叠或夹层,如果采用根部直角,在后续的工艺中容易形成折叠或夹层,影响坯件局部位置处的强度。圆形定位坑4a的高度最好为2mm,根部角最好为135
°
。
46.一工位上模6的底部、二工位上模12的底部、二工位下模10的顶部分别设置有冲压凸台。三工位下模座13顶部居中开有连皮接料仓13a,冲掉的连皮则落入连皮接料仓13a中。连皮接料仓13a底部开有斜向下接料滑道13b,使连皮接料仓13a的连皮能在重力作用下自动向下滑落出来。连皮接料仓13a的一侧水平开有防堵清理孔13c,一旦发生堵塞时,借用棍棒插入防堵清理孔13c内,能清理堵塞物。
47.三工位冲连皮下模14上开有上下贯通的中间孔,三工位冲连皮下模14的顶部设置有定位凸台14a,当第三冲连皮模合模时,三工位冲连皮冲头16落入三工位冲连皮下模14的中间孔内,三工位冲连皮冲头16向下运动,冲下连皮,连皮落入连皮接料仓13a并顺底部接料滑道13b滑出模具。
48.下模板1用于安装一工位下模座3、二工位下模座9、三工位下模座13的沉台内分别设置有下垫板17。上模板2用于安装一工位上模座5、二工位上模座11、三工位上模座15的沉台内分别设置有上垫板18。第三冲连皮模的下垫板17与下模板1、三工位下模座13之间分别设置有不同的定位键19用于定位三工位下模座13的接料滑道13b的出口方向向后,避开操
作者所站的前方位置。下模板1、上模板2之间设置有四根呈矩形布置的导向柱20。
49.步骤c的具体工艺步骤为:将加热后出炉后的棒料放置在400t闭式单点压力机的三工位快换制坯模的第一镦粗模上,棒料在圆锥形定位坑4a中定位,启动压力机,滑块下行至设定位置进行镦粗后,滑块返程至初始位置,停止,夹持坯件,将坯件取出。
50.夹持坯件,将坯件上下翻转180
°
,放入400t闭式单点压力机三工位快换制坯模的第二镦粗模上,使用在第一镦粗模中形成的坯件圆锥沉孔定位,启动压力机,滑块下行至设定位置进行镦粗后,滑块返程至初始位置,停止,夹持工件,将坯件取出。
51.夹持工件,将坯件放入400t闭式单点压力机的三工位快换制坯模的第三冲连皮模上,使用在第二镦粗模中形成的坯件下部圆锥沉孔定位,启动压力机,滑块下行至设定位置进行冲连皮,冲掉坯件中间连皮后,滑块返程至初始位置,停止,夹持工件,将坯件取出。
52.步骤d中使用的辗扩预成型模如图7所示,该模具安装于d51k
‑
350b数控立式辗环机上;由芯辊35和辗压轮36组成。辗压轮上开有两个相同的型腔ⅰ及ⅱ,当型腔ⅰ磨损失效后,将辗扩模翻面180
°
安装,继续使用型腔ⅱ,从而将使用寿命增加一倍。
53.如图6所示,步骤e中使用1600t电动螺旋压力机的终锻成型模。终锻成型模主要由终锻下模座21、三叉形顶块22、顶料杆23、终锻下模定位座24、终锻下成型模25、终锻下凸模芯26、终锻下模套27、终锻下模压紧圈28、终锻上模座29、终锻上成型模30、终锻上模变径圈31和终锻上模压紧圈32组成。
54.三叉形顶块22置于终锻下模座21的沉台内。终锻下模定位座24、终锻下成型模25由下到上依次安装。
55.三叉形顶块22的每个叉脚配备有一根顶料杆23,共三个叉脚,相应的,顶料杆23呈圆周均布,共三根。顶料杆23穿过终锻下模定位座24抵在终锻下成型模25的底部,用于推动终锻下成型模25向上运动实现工件脱模。
56.终锻下成型模25套在终锻下凸模芯26外,终锻下凸模芯26通过螺栓固定在终锻下模定位座24上。设置终锻下凸模芯26,是为了确保工件中心孔在终锻成型中的形状尺寸。
57.终锻下模套27套在终锻下成型模25外,终锻下模套27的底部压在终锻下模定位座24的台阶面上,使得终锻下成型模25能相对终锻下模套27上下移动,而终锻下模定位座24不能移动。
58.终锻下模套27的外壁带有锥度,并通过终锻下模压紧圈28结合螺栓固定安装在终锻下模座21上,终锻上模变径圈31通过台阶面套在终锻上成型模30外,终锻上模压紧圈32通过台阶面套在终锻上模变径圈31外,并通过螺栓固定安装在终锻上模座29上。实现快速换装,以满足不同尺寸规格的工件终锻成型。
59.当终锻成型模合模时,终锻上成型模30伸入终锻下模套27内,终锻下凸模芯26伸入终锻上成型模30内。
60.最好是,终锻下模座21内安装有下垫块33,终锻上模座29内安装有上垫块34,终锻下模定位座24抵在下垫块33上方,三叉形顶块22置于下垫块33内,终锻上成型模30抵在上垫块34下方。
61.在步骤e中,将辗扩预成型后的坯件放入1600t电动螺旋压力机终锻成形模中,启动电动螺旋压力机,滑块下行至设定位置打击坯件,使坯件终锻成形后,滑动返程至初始位置,停止,三叉形顶块带动顶料杆向上顶出工件,夹持工件,取出。
62.镦粗、冲连皮、辗环制坯后再终锻,辗环时内孔已经做出,其锻件的投影面积大幅减小,中间薄的连皮部分也不复存在,坯件所需的成形力显著降低,尖角处的充满能力提高,毛坯可以适当减小一定的加工余量,达到节约材料的目的。终锻成型后毛坯重量为6.05kg,连皮重量为0.22kg,下料重量为6.66kg。相比传统工艺,单件下料重量相差:7.31
‑
6.66=0.65kg,大大降低了成本,具有显著的市场优势。
再多了解一些
本文用于企业家、创业者技术爱好者查询,结果仅供参考。