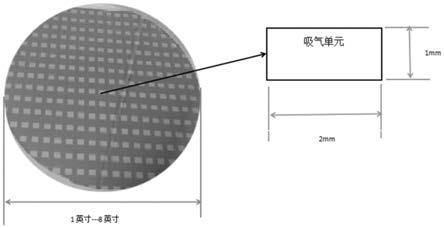
1.本发明涉及功能材料技术领域,特别涉及一种高性能薄膜吸气剂及其应用。
背景技术:
2.人们对于真空封装的研究较为久远,早期对于气体放电的研究就已经涉及到真空封装。20世纪初对于分子泵和扩散泵的发明,使得真空技术得到了突飞猛进的发展。随着真空电子管技术的发展,真空封装技术逐渐形成了玻璃—玻璃、玻璃—金属、金属—陶瓷等封装形式。
3.但对于新型发展的高灵敏智能传感器的真空封装,特别是mems(micro electromechanical system)真空封装技术,虽然很多电真空的封装技术可以借鉴,但是由于mems器件体积小、封装的工艺温度低于400℃的限制,很多电真空技术中行之有效的技术与方法,并不适用于mems真空封装,为此mems真空封装面临极大挑战。传统的技术方案是在mems的真空封装中,采用单质金属如钛和锆的薄膜吸气剂,放置于mems器件中,吸收器件中的残余气体,达到真空封装的目的。但单质金属钛和锆的薄膜吸气剂,在吸气过程的动力学不佳,进而影响相应mems器件的性能。因此,亟需发明一种新的薄膜吸气剂。
技术实现要素:
4.本发明的技术人员发现,在zr系合金和ti系合金中,y元素和sc元素单独添加或者复合添加,有利于提高主体元素ti或者zr吸气动力学,高效吸收吸mems芯片器件腔体的残余气体,维持器件处于高真空状态,提高mems器件使用寿命的目的。
5.本发明的目的在于发明一种新的薄膜吸气剂,该薄膜吸气剂具备高的吸气量,能够有效的维持mems芯片器件的高真空性能要求,达到信号的稳定性和高灵敏性。
6.具体的,本发明的技术方案如下:
7.本发明第一个方面公开了一种薄膜吸气剂,其特征在于,所述薄膜吸气剂包括主体元素,所述主体元素为ti、zr中的一种或两种;优选的,所述薄膜吸气剂还包括sc、y、v、hf和ta中的任意一种或者任何组合。
8.优选的,所述薄膜吸气剂的化学成分按照重量百分数计,包括以下组分:
[0009][0010]
其中,所述主体元素为ti、zr中的一种或两种。
[0011]
更优选的,所述主体元素的成分含量为32wt%
‑
80wt%,所述sc的成分含量为0.1wt%
‑
28wt%,y的成分含量为0.1wt%
‑
28wt%,所述v的成分含量为0.1wt%
‑
1.8wt%,所述hf的成分含量为0.1wt%
‑
1.8wt%,所述ta的成分含量为0
‑
1.8wt%。
[0012]
优选的,所述薄膜吸气剂为:
[0013]
(ti
x
zr
y
)
34
‑
90
(y1‑
a
sc
a
)0‑
30
(v1‑
b
‑
c
hf
b
ta
c
)0‑2(wt%);其中,0≤x≤1,0≤y≤1,x y=1;0≤a≤1,0≤b≤0.5,0≤c≤0.5;
[0014]
优选的,所述薄膜吸气剂为:(ti
x
zr
y
)
35
‑
80
(y1‑
a
sc
a
)1‑
28
(v1‑
b
‑
c
hf
b
ta
c
)(wt%);其中,0≤x≤1,0≤y≤1,x y=1;0≤a≤1,0≤b≤0.5,0≤c≤0.5。
[0015]
在本发明的一些具体实施例中,所述薄膜吸气剂选自:
[0016]
zr
72
sc
28
(wt%)、
[0017]
zr
72
y
28
(wt%)、
[0018]
zr
40
ti
33
y
27
(wt%)、
[0019]
zr
70
hf2y
28
(wt%)、
[0020]
ti
72
sc
28
(wt%)
[0021]
ti
72
y
28
(wt%)或
[0022]
zr
60
ti
10
ta1hf1v1y
24
sc3(wt%)。
[0023]
在其中一些实施例中,所述主体元素至少含有zr。在其中一些实施例中,所述主体元素为ti、zr和hf或者ta的组合。
[0024]
在一些实施实例中,所述吸气薄膜吸气剂中至少含有zr、sc或者zr和y。在一些实施实例中,所述吸气薄膜吸气剂中至少含有ti、sc或者ti和y。
[0025]
本发明第二个方面公开了一种薄膜吸气剂,所述薄膜吸气剂以与其化学成分相同的合金吸气靶材为原材料制备得到。
[0026]
优选的,所述薄膜吸气剂的制备方法包括:
[0027]
通过磁控溅射工艺将所述合金吸气靶材溅射于基体上,即制备得到薄膜吸气剂。
[0028]
更优选的,所述薄膜吸气剂的激活温度为250~710℃,激活时间15~40min,初始吸氢速率100~1200ml/s.cm2,薄膜吸气剂和所述基体的附着力为1~5n/cm;和/或薄膜吸气剂的厚度1
‑
12μm。
[0029]
更优选的,所述基体选自硅晶圆、锗硅晶圆、锗晶圆或氮化镓晶圆、sic晶圆中的至
少一种;或
[0030]
石英、蓝宝石、玻璃中的至少一种;或
[0031]
金属薄膜;
[0032]
所述金属薄膜选自不锈钢薄膜、ni
‑
cr电阻合金薄膜、不锈钢薄膜、可阀合金薄膜、陶瓷薄膜或无机金属薄膜中的至少一种。
[0033]
优选的,所述磁控溅射工艺中所述合金吸气靶材选自:直径为1~8英寸靶材;或者矩形靶,尺寸:长(0~990mm)
×
宽(0~230mm)
×
厚度(4~10mm)。
[0034]
在本发明的一些具体实施例中,磁控溅射工艺:功率50
‑
800w,压力0.01
‑
10pa。
[0035]
所述基体为各种mems器件晶圆(硅晶圆、锗硅晶圆、锗晶圆或氮化镓晶圆、sic晶圆等基体);玻璃(石英、蓝宝石等)绝缘性晶圆进行溅射;或者在金属薄膜基体样品上,如不锈钢基体及其薄膜、ni
‑
cr电阻合金薄膜基体、不锈钢薄膜、可阀合金薄膜等金属薄膜、陶瓷薄膜或无机金属薄膜。
[0036]
应当理解,本发明中的基体并不限于上述种类,本领域技术人员可以根据需要,选择任意合适的基体,且均在本发明的保护范围之内。
[0037]
本发明第三个方面公开了一种mems器件,其包括上述的薄膜吸气剂。
[0038]
在符合本领域常识的基础上,上述各优选条件,可任意组合,而不超出本发明的构思与保护范围。
[0039]
本发明相对于现有技术具有如下的显著优点及效果:
[0040]
本发明公开了一种新的薄膜吸气剂,该薄膜吸气剂以与薄膜吸气剂化学成分相同的合金吸气靶材为原材料,通过磁控溅射制备得到。该薄膜吸气剂具备高的吸气量,能够有效的维持mems芯片器件的高真空性能要求,达到信号的稳定性和高灵敏性。
附图说明
[0041]
图1为实施例1、实施例5和实施例6中具有圆形化的硅晶元基体上的薄膜吸气剂的示意图;
[0042]
图2为实施例2、实施例7中不锈钢基体的示意图;
[0043]
图3为实施例3中不锈钢基体的示意图;
[0044]
图4为实施例4中可阀合金基体的示意图。
具体实施方式
[0045]
下面结合附图和实施例对本发明的技术方案进行详细描述,但并不因此将本发明限制在所述的实施例范围之中。
[0046]
下列实施例中未注明具体条件的实验方法,按照常规方法和条件,或按照商品说明书选择。本发明所用试剂和原料均市售可得。
[0047]
实施例1
[0048]
用直径2英寸的靶材。在磁控溅射上机器上,在2英寸的基体硅晶元上溅射合金吸气靶材,得到薄膜吸气剂(见图1),磁控溅射工艺参数为:腔体溅射压力为0.01pa;基体衬底样品温度为25℃;溅射功率为45w;得到的薄膜吸气剂的厚度为1.8微米,薄膜吸气剂成分为zr
72
sc
28
(wt%),与硅晶元基体的结合强度1.8n/cm。对薄膜吸气剂进行吸气性能的测试,即
在真空度3
‑4×
10
‑4pa下,在320℃保温30分钟,薄膜吸气剂初始吸氢速率达到350ml/s.cm2。
[0049]
实施例2
[0050]
用直径4英寸的靶材。在磁控溅射上机器上,在4英寸的不锈钢基体(见图2)上溅射合金吸气靶材,得到薄膜吸气剂,磁控溅射工艺参数为:腔体溅射压力为0.1pa;基体衬底样品温度为30℃;溅射功率为60w;薄膜吸气剂的厚度为2.0微米,薄膜吸气剂成分为zr
72
y
28
(wt%),与不锈钢基体的结合强度1.8n/cm。对薄膜吸气剂进行吸气性能的测试,即在真空度3
‑4×
10
‑4pa下,在350℃保温15分钟,薄膜吸气剂初始吸氢速率达到385ml/s.cm2。
[0051]
实施例3
[0052]
用直径8英寸的靶材。在磁控溅射上机器上,在8英寸的不锈钢基体(见图3)上溅射合金吸气靶材,得到薄膜吸气剂,磁控溅射工艺参数为:腔体溅射压力为1.2pa;基体衬底样品温度为28℃;溅射功率为120w;薄膜吸气剂的厚度为2.1微米,薄膜吸气剂成分为zr
40
ti
33
y
27
(wt%),与不锈钢基体的结合强度2.5n/cm。对薄膜吸气剂进行吸气性能的测试,即在真空度3
‑4×
10
‑4pa下,在380℃保温15分钟,薄膜吸气剂初始吸氢速率达到428ml/s.cm2。
[0053]
实施例4
[0054]
用直径8英寸的靶材。在磁控溅射上机器上,在8英寸的可阀合金基体(见图4)上溅射合金吸气靶材,得到薄膜吸气剂,磁控溅射工艺参数为:腔体溅射压力为1.2pa;基体衬底样品温度为32℃;溅射功率为130w;薄膜吸气剂的厚度为2.15微米,薄膜吸气剂成分为zr
70
hf2y
28
(wt%),与可阀合金基体的结合强度3n/cm。对薄膜吸气剂进行吸气性能的测试,即在真空度3
‑4×
10
‑4pa下,在400℃保温15分钟,薄膜吸气剂初始吸氢速率达到402ml/s.cm2。
[0055]
实施例5
[0056]
用直径8英寸的靶材。在磁控溅射上机器上,在8英寸的硅晶元基体上溅射合金吸气靶材,得到薄膜吸气剂(见图1),磁控溅射工艺参数为:腔体溅射压力为1.2pa;基体衬底样品温度为32℃;溅射功率为130w;薄膜吸气剂的厚度为2.15微米,薄膜吸气剂成分为ti
72
sc
28
(wt%),与硅晶元基体的结合强度3.8n/cm。对薄膜吸气剂进行吸气性能的测试,即在真空度3
‑4×
10
‑4pa下,在410℃保温15分钟,薄膜吸气剂初始吸氢速率达到482ml/s.cm2。
[0057]
实施例6
[0058]
用直径4英寸的靶材。在磁控溅射上机器上,在4英寸的硅晶元基体上溅射合金吸气靶材,得到薄膜吸气剂(见图1),磁控溅射工艺参数为:腔体溅射压力为1.5pa;基体衬底样品温度为33℃;溅射功率为180w;薄膜吸气剂的厚度为2.05微米,薄膜吸气剂成分为ti
72
y
28
(wt%),与硅晶元基体的结合强度2.8n/cm。对薄膜吸气剂进行吸气性能的测试,即在真空度3
‑4×
10
‑4pa下,在450℃保温30分钟,薄膜吸气剂初始吸氢速率达到501ml/s.cm2。
[0059]
实施例7
[0060]
用直径4英寸的靶材。在磁控溅射上机器上,在4英寸的不锈钢基体(见图2)上溅射合金吸气靶材,得到薄膜吸气剂,磁控溅射工艺参数为:腔体溅射压力为1.5pa;基体衬底样品温度为29℃;溅射功率为230w;薄膜吸气剂的厚度为2.25微米,薄膜吸气剂成分为zr
60
ti
10
ta1hf1v1y
24
sc3(wt%),与硅晶元基体的结合强度18n/cm。对薄膜吸气剂进行吸气性能的测试,即在真空度3
‑4×
10
‑4pa下,在500℃保温30分钟,薄膜吸气剂初始吸氢速率达到
628ml/s.cm2。
[0061]
所述实施实例1
‑
7是各技术特征可以进行任意的组合,为了描述简洁,本技术未对上述实施例中的各个技术特征所有可能的组合都进行描述,然而,只要这些技术特征的组合不存在矛盾,应当认为是本说明书记载的范围。
[0062]
上述实施例为本发明较佳的实施方式,但本发明的实施方式并不受上述实施例的限制,其他的任何未背离本发明的精神实质与原理下所作的改变、修饰、替代、组合、简化,均应为等效的置换方式,都包含在本发明的保护范围之内。
再多了解一些
本文用于企业家、创业者技术爱好者查询,结果仅供参考。