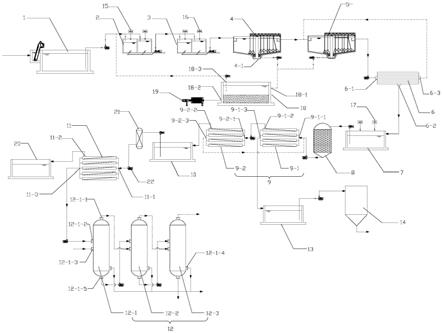
1.本发明涉及脱酸废水资源化利用技术领域,尤其是涉及一种高含盐脱酸废水资源化利用系统及方法。
背景技术:
2.焚烧技术是城市生活垃圾及危废的有效处理技术之一,随着烟气排放指标的日益严苛,湿法脱酸工艺是目前焚烧烟气达标排放的有效保障手段,但湿法工艺会产生组成复杂、含盐量高的酸性废水,脱酸废水的有效处置成为垃圾焚烧厂废水零排放的重点和难点之一。
3.目前,脱酸废水的处理方法主要是采用物化处理工艺对其中的杂质及盐进行去除,使处理后的出水满足排放标准。例如,一种在中国专利文献上公开的“湿法脱酸废水的处理方法及处理系统”,其公开号cn108439651a,处理方法包括:s1、将湿法脱酸废水进行预处理,氧化湿法脱酸废水中的还原性物质;s2、将预处理后的湿法脱酸废水进行一级絮凝沉淀处理,去除其中的钙、镁、硅酸盐;s3、将一级絮凝沉淀处理获得的上清液进行二级絮凝沉淀处理,去除其中的重金属离子;s4、将二级絮凝沉淀处理获得的上清液进行ph值调节;s5、将ph值调节过的上清液进行一级过滤,以进行截留分离;s6、将一级过滤后得到的滤液进行二级过滤。
4.但使用现有技术中的方法对脱酸废水进行处理后,从脱酸废水中回收的盐为各种组分的混合盐,无法进行资源化回用处理,只能作为固废外运处置,废盐的综合处置成本很高,不满足节能减排要求。
技术实现要素:
5.本发明是为了克服采用现有技术中的方法对脱酸废水进行处理后,从脱酸废水中回收的盐为各种组分的混合盐,无法进行资源化回用处理,只能作为固废外运处置,废盐的综合处置成本很高的问题,提供一种高含盐脱酸废水资源化利用系统及方法,通过药剂反应和各级精度不同的膜处理装置的配合,可以将脱酸废水中的so
42
‑
和cl
‑
进行有效分离,最终得到纯度较高、可以直接进行资源化利用的na2so4和nacl,从而可以实现脱酸废水中盐类的有效回收和资源化利用,减少了固废产生量,提高了节能减排程度。
6.为了实现上述目的,本发明采用以下技术方案:一种高含盐脱酸废水资源化利用系统,包括依次连接的均质池、第一反应池、第二反应池、沉淀池、浓缩池、超滤装置、超滤产水池、纳滤装置、纳滤产水池、反渗透装置、三效蒸发单元以及依次与纳滤装置连接的纳滤浓液池和冷冻结晶装置;所述第一反应池上方设有cacl2加药装置,第二反应池上方设有na2co3加药装置,超滤产水池上方设有盐酸加药装置。
7.本发明还提供了一种使用上述系统进行高含盐脱酸废水资源化利用的方法,包括如下步骤:
(1)脱酸废水经均质池均质后进入第一反应池,投加cacl2进行反应;(2)第一反应池的出水进入第二反应池,投加na2co3进行反应;(3)第二反应池的出水依次经过沉淀池和浓缩池进行沉淀后,上清液进入超滤系统进行超滤;(4)超滤后的透过液进入超滤产水池,投加盐酸进行反应;(5)超滤产水池的出水进入纳滤装置进行纳滤,纳滤后的浓缩液进入冷冻结晶装置中,冷冻结晶后回收得到na2so4;(6)纳滤后的透过液经纳滤产水池进入反渗透装置中进行反渗透;(7)反渗透后的浓缩液进入三效蒸发单元,蒸发后回收得到nacl。
8.垃圾焚烧所产生的脱酸废水中,主要成分以氯化钠为主,并混有氟离子、硫酸根、碳酸根、碳酸氢根等离子,本发明先通过均质池去除脱酸废水中的硫酸钙等悬浮物,避免悬浮物对后续装置产生不必要的影响;然后经过第一反应池,通过cacl2加药装置向废水中投加cacl2,使水中大部分f
‑
和co
32
‑
与ca
2
反应生成氟化钙和碳酸钙沉淀,达到去除f
‑
和co
32
‑
的目的;出水再进入第二反应池,通过na2co3加药装置向废水中投加na2co3,使废水中的大部分金属离子(如钙、镁、钡、锶、铁、锰等)和co
32
‑
反应生成碳酸盐沉淀,达到初步去除金属离子的目的;由于第一和第二反应池内形成了大量悬浮物,因此第二反应池的出水先进入沉淀池,通过重力沉淀方式对水中的大颗粒悬浮物进行去除,上清液再进入浓缩池,进一步对废水中的悬浮物进行去除;浓缩池的上清液进入超滤装置中,通过超滤膜对废水中无法沉淀的悬浮物进行最终去除;超滤后的透过液进入超滤产水池中,通过盐酸加药装置向超滤产水中投加盐酸,对废水的ph进行回调,并去除废水中的hco3‑
;ph回调后的废水进入纳滤装置中,在纳滤膜的作用下将so
42
‑
与cl
‑
分离,富含so
42
‑
的纳滤浓缩液进入纳滤浓液池中,然后经冷冻结晶装置冷冻结晶后可以回收得到na2so4;富含cl
‑
的纳滤透过液进入纳滤产水池,然后继续进入反渗透装置中进行反渗透处理,将nacl与水分离,分离后的出水可进行回用或直接外排,分离后得到的富含nacl的浓缩液进入三效蒸发单元,蒸发后可回收得到纯度较高的nacl。
9.因此,本发明通过药剂反应和各级精度不同的膜处理装置的配合,可以将脱酸废水中的so
42
‑
和cl
‑
进行有效分离,最终回收得到的nacl纯度可达96.9~98.2%,达到工业盐标准的理化指标要求,na2so4纯度可达92.8~94.6%,达到无水硫酸钠标准的理化指标要求;从而可以实现脱酸废水中盐类的有效回收和资源化利用,减少了固废产生量,提高了节能减排程度。
10.作为优选,超滤产水池和纳滤装置之间设有除氟反应器,所述除氟反应器内设有除氟树脂。在纳滤装置之前设置除氟反应器,可以通过除氟树脂对废水中的f
‑
进行进一步吸附去除,从而提高最终得到的na2so4和nacl的浓度。
11.作为优选,系统内还设有相连接的污泥池和压滤机;所述污泥池上设有污泥进口、污泥出口以及废水出口;所述沉淀池和浓缩池底部设有污泥斗;污泥池的污泥进口分别与沉淀池和浓缩池的污泥斗连接,污泥池的污泥出口与压滤机连接,污泥池废水出口与第一反应池的进水口连接。本发明在系统内设置污泥池和压滤机,可以对沉淀池和浓缩池中产生的污泥进行回收和脱水处理,便于污泥的后续运输和处置;污泥池的上清液可以回流至第一反应池进重新进行处理。
12.作为优选,所述超滤装置中设有管式超滤膜组件;超滤装置上设有超滤装置进水口、超滤装置透过液出口及超滤装置浓缩液出口,所述超滤装置进水口与浓缩池的出水口连接,超滤装置透过液出口与超滤产水池连接,超滤装置浓缩液出口与浓缩池的进水口连接。废水经超滤装置后的透过液进入后续处理装置进行后续处理,浓缩液则回流至浓缩池,重新进行沉淀处理。
13.作为优选,所述纳滤装置包括一级纳滤装置和二级纳滤装置,所述一级和二级纳滤装置内设有纳滤膜组件,一级和二级纳滤装置上分别设有进水口、透过液出口以及浓缩液出口;所述一级纳滤装置的进水口与除氟反应器连接,一级纳滤装置的透过液出口与二级纳滤装置的进水口连接,一级纳滤装置的浓缩液出口与纳滤浓液池连接;所述二级纳滤装置的透过液出口与纳滤产水池连接,二级纳滤装置的浓缩液出口与一级纳滤装置的进水口连接。本技术在系统中设置两级纳滤装置,充分保证so
42
‑
与cl
‑
的分离效果,从而提高了三效蒸发后得到的nacl结晶盐的纯度,便于nacl的后续回收利用。
14.作为优选,所述纳滤膜组件中使用的纳滤膜的制备方法为:a)将摩尔比为1:1~2的zrcl4和2
‑
氨基对苯二甲酸溶解在dmf中,加入盐酸,超声分散20~30min,然后加热至120~140℃水热反应24~36h,冷却至室温后将产物过滤、清洗、干燥得到金属有机框架材料;其中加入的盐酸的质量浓度为35~37%,加入的盐酸与dmf的体积比为1:50~60;先通过步骤a),以zrcl4为金属源,2
‑
氨基对苯二甲酸为有机配体,制得带有氨基的金属有机框架材料;b)将金属有机框架材料和n
‑
甲基咪唑加入乙醇中,氮气保护下搅拌12~18h;再加入3
‑
溴丙胺氢溴酸盐,氮气保护下回流反应24~36h;其中,金属有机框架材料、n
‑
甲基咪唑及3
‑
溴丙胺氢溴酸盐的质量比为2~2.5:1:2.9~2.95;将产物过滤后用乙醇洗涤、真空干燥后得到离子液体改性的金属有机框架材料;步骤b)中,先使n
‑
甲基咪唑吸附扩散至金属有机框架材料的框架结构内,然后再使3
‑
溴丙胺氢溴酸盐吸附扩散至框架结构内与n
‑
甲基咪唑反应,生成离子液体1
‑
(3
‑
胺丙基)
‑3‑
甲基咪唑溴,从而将离子液体负载在金属有机框架材料的框架结构内,得到离子液体改性的金属有机框架材料;c)将哌嗪溶于去离子水中,然后加入离子液体改性的金属有机框架材料,分散均匀后调节溶液ph值至5~7,得到水相溶液,水相溶液中哌嗪的质量浓度为0.2~0.4%,哌嗪与金属有机框架材料的质量比为2~4:1;d)将均苯三甲酰氯加入乙基环己烷中,搅拌溶解后得到均苯三甲酰氯的质量浓度为0.1~0.2%的油相溶液;e)将多孔聚砜基膜浸入水相溶液中浸润5~10min,取出后将基膜上多余的水相溶液吹扫干净,至基膜表面没有水珠;再将基膜浸入油相溶液中接触反应2~5min;取出后将基膜在50~70℃下预干燥1~2min,然后用70~90℃热水清洗4~6min,再在质量浓度为7~9%的甘油中浸泡1~3min,取出后50~70℃烘干得到所述纳滤膜。步骤d)~e)中,通过哌嗪和均苯三甲酰氯在多孔聚砜基膜表面发生界面聚合反应,生成聚哌嗪酰胺功能层,从而使纳滤膜具有良好的选择透过性,可以将二价和一价离子进行分离。界面聚合过程中,金属有机框架材料中的氨基也可以参与反应,从而使金属有机框架材料可以牢固负载在聚哌嗪酰胺功能层中,不易从纳滤膜表面脱落。
15.目前,商业化的纳滤膜以聚哌嗪酰胺复合纳滤膜为主,现有的纳滤膜普遍水通量
较低,随着使用时间的延长,水通量衰减严重,影响cl
‑
和so
42
‑
的分离效果。因此本发明在制备纳滤膜时,在聚哌嗪酰胺功能层中添加了金属有机框架材料,利用金属有机框架材料的中空多孔结构,可有效提升纳滤膜的水通量;但金属有机框架材料的加入也会导致界面聚合过程中生成的聚哌嗪酰胺功能层的致密度下降,从而影响纳滤膜对so
42
‑
的截留率,因此本发明又在金属有机框架材料的多孔结构内修饰了离子液体,通过离子液体对so
42
‑
的吸附作用,提高了纳滤膜对so
42
‑
的截留率,从而使制得的纳滤膜兼具高的so
42
‑
截留率和水通量,可有效对cl
‑
和so
42
‑
进行分离。
16.作为优选,所述反渗透装置内设有反渗透膜组件,反渗透装置上设有反渗透装置进水口、反渗透装置透过液出口及反渗透装置浓缩液出口;所述反渗透装置进水口与纳滤产水池连接,反渗透装置浓缩液出口与三效蒸发单元连接;系统内还设有与反渗透装置透过液出口连接的回用水池。
17.作为优选,所述三效蒸发单元包括依次连接的第一效蒸发器、第二效蒸发器及第三效蒸发器,所述第一、第二及第三效蒸发器的顶部分别设有蒸汽出口,中部分别设有进料口和蒸汽入口,底部分别设有冷凝水出口和出料口;所述第一效蒸发器的进料口与反渗透装置浓缩液出口连接,第一效蒸发器的出料口和蒸汽出口分别与第二效蒸发器的进料口和蒸汽入口连接;所述第二效蒸发器的出料口和蒸汽出口分别与第三效蒸发器的进料口和蒸汽入口连接。本发明通过三效蒸发单元对经反渗透处理后的富含nacl的浓缩液进行蒸发处理,得到nacl结晶盐以进行回收利用。在三效蒸发单元中,反渗透的浓缩液依次经过第一、第二及第三效蒸发器,通过蒸汽对浓缩液进行加热,浓缩液中的水分不断被蒸发,nacl不断析出,实现盐水分离;第一效蒸发器中的浓缩液蒸发后的蒸汽可以进入第二效蒸发器作为加热热源,第二效蒸发器中的二次蒸汽又可以作为第三效蒸发器的加热热源,具有良好的节能效果。
18.作为优选,所述纳滤产水池和反渗透装置之间设有保安滤器,所述保安滤器内设有过滤精度为4~6μm的折叠式滤芯。本发明在反渗透装置前设置保安滤器,使废水在进入反渗透装置前先经过保安滤器对颗粒物进行进一步去除,避免由于颗粒物浓度过高造成反渗透膜堵塞;也避免了颗粒物粒径过大击穿反渗透膜组件,造成漏盐等现象,影响nacl的回收效果。
19.作为优选,所述超滤装置、纳滤装置及反渗透装置前分别设有高压泵。通过高压泵对超滤装置、纳滤装置及反渗透装置的进水加压,为各膜处理装置提供足够的进水量和进水压力,从而使膜处理装置进水具有一定的推动力去克服渗透压等阻力,以保证达到设计的产水量,有效实现盐水分离。
20.作为优选,步骤(1)中第一反应池内的停留时间为20~40min,cacl2的投加量为8~20kg/m3脱酸废水。
21.作为优选,步骤(2)中,第二反应池内的停留时间为20~40min,投加质量分数为20~40%的na2co3溶液,na2co3溶液的投加量为5~15l/m3脱酸废水。
22.作为优选,步骤(3)中超滤装置的运行压力为2~3mpa。
23.作为优选,步骤(4)中投加的盐酸质量分数为10~30%,盐酸的投加量为5~15l/m3脱酸废水。
24.作为优选,步骤(5)中一级纳滤装置的运行压力为2.5~3.5mpa,二级纳滤装置的
运行压力为1.5~2.0mpa。
25.作为优选,步骤(6)中反渗透装置的运行压力为7.5~8mpa。
26.因此,本发明的有益效果为:通过药剂反应和各级精度不同的膜处理装置的配合,可以将脱酸废水中的so
42
‑
和cl
‑
进行有效分离,最终得到纯度较高、可以直接进行资源化利用的na2so4和nacl,从而可以实现脱酸废水中盐类的有效回收和资源化利用,减少了固废产生量,提高了节能减排程度。
附图说明
27.图1是本发明的一种连接结构示意图。
28.图中:1均质池、2第一反应池、3第二反应池、4沉淀池、4
‑
1污泥斗、5浓缩池、6超滤装置、6
‑
1超滤装置进水口、6
‑
2超滤装置透过液出口、6
‑
3超滤装置浓缩液出口、7超滤产水池、8除氟反应器、9纳滤装置、9
‑
1一级纳滤装置、9
‑1‑
1一级纳滤装置的进水口、9
‑1‑
2一级纳滤装置的透过液出口、9
‑1‑
3一级纳滤装置的浓缩液出口、9
‑
2二级纳滤装置、9
‑2‑
1二级纳滤装置的进水口、9
‑2‑
2二级纳滤装置的透过液出口、9
‑2‑
3二级纳滤装置的浓缩液出口、10纳滤产水池、11反渗透装置、11
‑
1反渗透装置进水口、11
‑
2反渗透装置透过液出口、11
‑
3反渗透装置浓缩液出口、12三效蒸发单元、12
‑
1第一效蒸发器、12
‑1‑
1蒸汽出口、12
‑1‑
2进料口、12
‑1‑
3蒸汽入口、12
‑1‑
4冷凝水出口、12
‑1‑
5出料口、12
‑
2第二效蒸发器、12
‑
3第三效蒸发器、13纳滤浓液池、14冷冻结晶装置、15cacl2加药装置、16na2co3加药装置、17盐酸加药装置、18污泥池、18
‑
1污泥进口、18
‑
2污泥出口、18
‑
3废水出口、19压滤机、20回用水池、21保安滤器、22高压泵。
具体实施方式
29.下面结合附图与具体实施方式对本发明做进一步的描述。
30.在本发明中,若非特指,所有设备和原料均可从市场购得或是本行业常用的,下述实施例中的方法,如无特别说明,均为本领域常规方法。
31.如图1所示,一种高含盐脱酸废水资源化利用系统,包括依次通过废水管路连接的均质池1、第一反应池2、第二反应池3、沉淀池4、浓缩池5、超滤装置6、超滤产水池7、除氟反应器8、纳滤装置9、纳滤产水池10、保安滤器21、反渗透装置11、三效蒸发单元12以及依次与纳滤装置连接的纳滤浓液池13和冷冻结晶装置14;第一反应池上方设有cacl2加药装置15,第二反应池上方设有na2co3加药装置16,超滤产水池上方设有盐酸加药装置17。
32.系统内还设有污泥池18和压滤机19;污泥池上设有污泥进口18
‑
1、污泥出口18
‑
2以及废水出口18
‑
3;沉淀池4和浓缩池5底部设有污泥斗4
‑
1;污泥池的污泥进口分别与沉淀池和浓缩池的污泥斗通过污泥管路连接,污泥池的污泥出口与压滤机通过污泥管路连接,污泥池废水出口与第一反应池的进水口通过回流管路连接。
33.超滤装置上设有超滤装置进水口6
‑
1、超滤装置透过液出口6
‑
2及超滤装置浓缩液出口6
‑
3;超滤装置进水口与浓缩池的出水口连接,超滤装置进水口处设有高压泵,超滤装置透过液出口与超滤产水池连接,超滤装置浓缩液出口与浓缩池的进水口连接。
34.纳滤装置包括一级纳滤装置9
‑
1和二级纳滤装置9
‑
2,一级和二级纳滤装置上分别设有进水口、透过液出口以及浓缩液出口;一级纳滤装置的进水口9
‑1‑
1与除氟反应器8通
过废水管路连接,一级纳滤装置的透过液出口9
‑1‑
2与二级纳滤装置的进水口9
‑2‑
1通过废水管路连接,一级纳滤装置的浓缩液出口9
‑1‑
3与纳滤浓液池13通过废水管路连接;二级纳滤装置的透过液出口9
‑2‑
2与纳滤产水池10通过废水管路连接,二级纳滤装置的浓缩液出口9
‑2‑
3与一级纳滤装置的进水口通过回流管路连接;一级及二级纳滤装置进水口处设有高压泵。
35.反渗透装置上设有反渗透装置进水口11
‑
1、反渗透装置透过液出口11
‑
2及反渗透装置浓缩液出口11
‑
3;反渗透装置进水口处设有高压泵22,反渗透装置进水口与纳滤产水池通过废水管路连接,反渗透装置浓缩液出口与三效蒸发单元通过废水管路连接;系统内还设有与反渗透装置透过液出口连接的回用水池20。
36.超滤装置中设有管式超滤膜组件,一级和二级纳滤装置内设有纳滤膜组件,反渗透装置内设有反渗透膜组件,除氟反应器内设有除氟树脂,保安滤器内设有过滤精度为5μm的折叠式滤芯。
37.三效蒸发单元包括依次连接的第一效蒸发器12
‑
1、第二效蒸发器12
‑
2及第三效蒸发器12
‑
3,第一、第二及第三效蒸发器的顶部分别设有蒸汽出口12
‑1‑
1,中部分别设有进料口12
‑1‑
2和蒸汽入口12
‑1‑
3,底部分别设有冷凝水出口12
‑1‑
4和出料口12
‑1‑
5;第一效蒸发器的进料口与反渗透装置浓缩液出口连接,第一效蒸发器的出料口和蒸汽出口分别与第二效蒸发器的进料口和蒸汽入口连接;所述第二效蒸发器的出料口和蒸汽出口分别与第三效蒸发器的进料口和蒸汽入口连接。
38.实施例1:一种使用上述的系统进行高含盐脱酸废水资源化利用的方法,包括如下步骤:(1)脱酸废水经均质池均质后进入第一反应池,投加cacl2进行反应,cacl2的投加量为14kg/m3脱酸废水,停留时间25min;(2)第一反应池的出水进入第二反应池,投加30wt%的na2co3溶液进行反应,na2co3溶液的投加量为7.6l/m3脱酸废水,停留时间25min;(3)第二反应池的出水依次经过沉淀池和浓缩池进行沉淀后,上清液进入超滤系统进行超滤,超滤装置运行压力为2.4mpa,进水流量30m3/h;(4)超滤后的透过液进入超滤产水池,投加30wt%盐酸进行反应,盐酸的投加量为11.2l/m3脱酸废水;超滤后的浓缩液回流至浓缩池;(5)超滤产水池的出水经除氟反应器去除f
‑
后依次进过一级纳滤装置和二级纳滤装置进行两级纳滤;一级纳滤装置的运行压力为3.0mpa,进水流量1.2m3/h,二级纳滤装置的运行压力为1.8mpa,进水流量1.2m3/h;两级纳滤后的浓缩液进入冷冻结晶装置中,冷冻结晶后回收得到na2so4;(6)两级纳滤后的透过液进入纳滤产水池,然后经保安滤器后再进入反渗透装置中进行反渗透,反渗透装置的运行压力为7.8mpa,进水流量0.15m3/h;(7)反渗透后的透过液进入回用水池,浓缩液进入三效蒸发单元,蒸发后回收得到nacl。
39.其中,超滤装置中的管式超滤膜采用perox处理量1m3/h、1寸10芯的管式超滤膜;一级和二级纳滤装置中的纳滤膜采用dow nf8040;反渗透装置中的反渗透膜采用dow sw30
‑
400;除氟反应器中的除氟树脂采用杜笙ch
‑
87。
40.实施例2:实施例2中一级和二级纳滤装置中的纳滤膜的制备方法为:a)将摩尔比为1:1.5的zrcl4和2
‑
氨基对苯二甲酸溶解在dmf中,zrcl4和dmf的质量体积比为1g:120ml;加入盐酸,超声分散25min,然后加热至130℃水热反应30h,冷却至室温后将产物过滤、清洗、干燥得到金属有机框架材料;其中加入的盐酸的质量浓度为36%,加入的盐酸与dmf的体积比为1:55;b)将金属有机框架材料和n
‑
甲基咪唑加入乙醇中,氮气保护下搅拌14h;再加入3
‑
溴丙胺氢溴酸盐,氮气保护下回流反应30h;其中,金属有机框架材料、n
‑
甲基咪唑及3
‑
溴丙胺氢溴酸盐的质量比为2.3:1:2.93;将产物过滤后用乙醇洗涤、80℃真空干燥后得到离子液体改性的金属有机框架材料;c)将哌嗪溶于去离子水中,然后加入离子液体改性的金属有机框架材料,分散均匀后调节溶液ph值至6,得到水相溶液,水相溶液中哌嗪的质量浓度为0.3%,哌嗪与金属有机框架材料的质量比为3:1;d)将均苯三甲酰氯加入乙基环己烷中,搅拌溶解后得到均苯三甲酰氯的质量浓度为0.15%的油相溶液;e)将多孔聚砜基膜浸入水相溶液中浸润7min,取出后将基膜上多余的水相溶液吹扫干净,至基膜表面没有水珠;再将基膜浸入油相溶液中接触反应3min;取出后将基膜在60℃下预干燥1.5min,然后用80℃热水清洗5min,再在质量浓度为8%的甘油中浸泡2min,取出后60℃烘干得到所述纳滤膜。
41.其余均与实施例1中相同。
42.实施例3:一种使用上述的系统进行高含盐脱酸废水资源化利用的方法,包括如下步骤:(1)脱酸废水经均质池均质后进入第一反应池,投加cacl2进行反应,cacl2的投加量为8kg/m3脱酸废水,停留时间20min;(2)第一反应池的出水进入第二反应池,投加40wt%的na2co3溶液进行反应,na2co3溶液的投加量为5l/m3脱酸废水,停留时间20min;(3)第二反应池的出水依次经过沉淀池和浓缩池进行沉淀后,上清液进入超滤系统进行超滤,超滤装置运行压力为2.0mpa,进水流量30m3/h;(4)超滤后的透过液进入超滤产水池,投加30wt%盐酸进行反应,盐酸的投加量为5l/m3脱酸废水;超滤后的浓缩液回流至浓缩池;(5)超滤产水池的出水经除氟反应器去除f
‑
后依次进过一级纳滤装置和二级纳滤装置进行两级纳滤;一级纳滤装置的运行压力为2.5mpa,进水流量1.2m3/h,二级纳滤装置的运行压力为1.5mpa,进水流量1.2m3/h;两级纳滤后的浓缩液进入冷冻结晶装置中,冷冻结晶后回收得到na2so4;(6)两级纳滤后的透过液进入纳滤产水池,然后经保安滤器后再进入反渗透装置中进行反渗透,反渗透装置的运行压力为7.5mpa,进水流量0.15m3/h;(7)反渗透后的透过液进入回用水池,浓缩液进入三效蒸发单元,蒸发后回收得到nacl。
43.其中,一级和二级纳滤装置中的纳滤膜的制备方法为:
a)将摩尔比为1:1的zrcl4和2
‑
氨基对苯二甲酸溶解在dmf中,zrcl4和dmf的质量体积比为1g:100ml;加入盐酸,超声分散20min,然后加热至120℃水热反应36h,冷却至室温后将产物过滤、清洗、干燥得到金属有机框架材料;其中加入的盐酸的质量浓度为35%,加入的盐酸与dmf的体积比为1:60;b)将金属有机框架材料和n
‑
甲基咪唑加入乙醇中,氮气保护下搅拌12h;再加入3
‑
溴丙胺氢溴酸盐,氮气保护下回流反应36h;其中,金属有机框架材料、n
‑
甲基咪唑及3
‑
溴丙胺氢溴酸盐的质量比为2:1:2.9;将产物过滤后用乙醇洗涤、80℃真空干燥后得到离子液体改性的金属有机框架材料;c)将哌嗪溶于去离子水中,然后加入离子液体改性的金属有机框架材料,分散均匀后调节溶液ph值至5,得到水相溶液,水相溶液中哌嗪的质量浓度为0.2%,哌嗪与金属有机框架材料的质量比为2:1;d)将均苯三甲酰氯加入乙基环己烷中,搅拌溶解后得到均苯三甲酰氯的质量浓度为0.1%的油相溶液;e)将多孔聚砜基膜浸入水相溶液中浸润5min,取出后将基膜上多余的水相溶液吹扫干净,至基膜表面没有水珠;再将基膜浸入油相溶液中接触反应2min;取出后将基膜在50℃下预干燥2min,然后用70℃热水清洗6min,再在质量浓度为7%的甘油中浸泡3min,取出后50℃烘干得到所述纳滤膜。
44.实施例4:一种使用上述的系统进行高含盐脱酸废水资源化利用的方法,包括如下步骤:(1)脱酸废水经均质池均质后进入第一反应池,投加cacl2进行反应,cacl2的投加量为20kg/m3脱酸废水,停留时间40min;(2)第一反应池的出水进入第二反应池,投加20wt%的na2co3溶液进行反应,na2co3溶液的投加量为15l/m3脱酸废水,停留时间40min;(3)第二反应池的出水依次经过沉淀池和浓缩池进行沉淀后,上清液进入超滤系统进行超滤,超滤装置运行压力为3.0mpa,进水流量30m3/h;(4)超滤后的透过液进入超滤产水池,投加10wt%盐酸进行反应,盐酸的投加量为15.0l/m3脱酸废水;超滤后的浓缩液回流至浓缩池;(5)超滤产水池的出水经除氟反应器去除f
‑
后依次进过一级纳滤装置和二级纳滤装置进行两级纳滤;一级纳滤装置的运行压力为3.5mpa,进水流量1.2m3/h,二级纳滤装置的运行压力为2.0mpa,进水流量1.2m3/h;两级纳滤后的浓缩液进入冷冻结晶装置中,冷冻结晶后回收得到na2so4;(6)两级纳滤后的透过液进入纳滤产水池,然后经保安滤器后再进入反渗透装置中进行反渗透,反渗透装置的运行压力为8.0mpa,进水流量0.15m3/h;(7)反渗透后的透过液进入回用水池,浓缩液进入三效蒸发单元,蒸发后回收得到nacl。
45.其中,一级和二级纳滤装置中的纳滤膜的制备方法为:a)将摩尔比为1:2的zrcl4和2
‑
氨基对苯二甲酸溶解在dmf中,zrcl4和dmf的质量体积比为1g:150ml;加入盐酸,超声分散30min,然后加热至140℃水热反应24h,冷却至室温后将产物过滤、清洗、干燥得到金属有机框架材料;其中加入的盐酸的质量浓度为37%,加入
的盐酸与dmf的体积比为1:50;b)将金属有机框架材料和n
‑
甲基咪唑加入乙醇中,氮气保护下搅拌18h;再加入3
‑
溴丙胺氢溴酸盐,氮气保护下回流反应24h;其中,金属有机框架材料、n
‑
甲基咪唑及3
‑
溴丙胺氢溴酸盐的质量比为2.5:1:2.95;将产物过滤后用乙醇洗涤、80℃真空干燥后得到离子液体改性的金属有机框架材料;c)将哌嗪溶于去离子水中,然后加入离子液体改性的金属有机框架材料,分散均匀后调节溶液ph值至7,得到水相溶液,水相溶液中哌嗪的质量浓度为0.4%,哌嗪与金属有机框架材料的质量比为4:1;d)将均苯三甲酰氯加入乙基环己烷中,搅拌溶解后得到均苯三甲酰氯的质量浓度为0.2%的油相溶液;e)将多孔聚砜基膜浸入水相溶液中浸润10min,取出后将基膜上多余的水相溶液吹扫干净,至基膜表面没有水珠;再将基膜浸入油相溶液中接触反应5min;取出后将基膜在70℃下预干燥1min,然后用90℃热水清洗4min,再在质量浓度为9%的甘油中浸泡1min,取出后70℃烘干得到所述纳滤膜。
46.对比例1(cacl2加药量过低):对比例1的步骤(1)中cacl2的投加量为7kg/m3脱酸废水,其余均与实施例1中相同。
47.对比例2(离子液体直接与金属有机框架共混):对比例2中一级和二级纳滤装置中的纳滤膜的制备方法为:a)将摩尔比为1:1.5的zrcl4和2
‑
氨基对苯二甲酸溶解在dmf中,zrcl4和dmf的质量体积比为1g:120ml;加入盐酸,超声分散25min,然后加热至130℃水热反应30h,冷却至室温后将产物过滤、清洗、干燥得到金属有机框架材料;其中加入的盐酸的质量浓度为36%,加入的盐酸与dmf的体积比为1:55;b)将哌嗪溶于去离子水中,然后加入金属有机框架材料和离子液体1
‑
(3
‑
胺丙基)
‑3‑
甲基咪唑溴,分散均匀后调节溶液ph值至6,得到水相溶液,水相溶液中哌嗪的质量浓度为0.3%,哌嗪、金属有机框架材料及1
‑
(3
‑
胺丙基)
‑3‑
甲基咪唑溴的质量比为3:1:1.7;c)将均苯三甲酰氯加入乙基环己烷中,搅拌溶解后得到均苯三甲酰氯的质量浓度为0.15%的油相溶液;d)将多孔聚砜基膜浸入水相溶液中浸润7min,取出后将基膜上多余的水相溶液吹扫干净,至基膜表面没有水珠;再将基膜浸入油相溶液中接触反应3min;取出后将基膜在60℃下预干燥1.5min,然后用80℃热水清洗5min,再在质量浓度为8%的甘油中浸泡2min,取出后60℃烘干得到所述纳滤膜。
48.其余均与实施例2中相同。
49.一、脱酸废水处理效果的测定:对实施例1和对比例1处理过程中的水质情况进行测试,结果如表1和表2中所示。
50.表1:实施例1各阶段水质情况测试结果。
51.表2:实施例1和对比例1第一反应池出水水质情况测试结果。
52.从表1和表2中可以看出,实施例1中采用本发明中的方法,可有效降低脱酸废水中f
‑
、co
32
‑
、hco3‑
含量,实现f
‑
、co
32
‑
、hco3‑
的去除;二级纳滤浓缩液中具有较高的so
42
‑
含量,可实现na2so4的回收;反渗透出水中tds浓度低,可直接回用;反渗透浓缩液中具有较高的cl
‑
浓度,可实现nacl的回收。
53.而对比例1中第一反应池内cacl2的加入量过少,f
‑
、co
32
‑
、hco3‑
及so
42
‑
的去除效果与实施例1中相比显著降低。
54.二、纳滤分盐效果的测定:在0.7mpa测试压力和25℃测试条件下,采用1000ppm硫酸镁和氯化钠的混合溶液对上述实施例和对比例中使用的纳滤膜进行错流过滤测试,测定其水通量及so
42
‑
与cl
‑
的截留率,结果如表3中所示。
55.表3:纳滤膜性能测试结果。测试项目实施例1实施例2实施例3实施例4对比例3水通量(l/m2h)62889182110so
42
‑
截留率(%)99.0299.3398.8999.6195.48cl
‑
截留率(%)4.26.85.97.44.7
56.从表1中可以看出,实施例2~4中采用本发明中的方法制得的纳滤膜与实施例1中
市售的纳滤膜相比,水通量得到明显提升,并且在可以使cl
‑
通过的同时对so
42
‑
具有高的截留率。而在对比例3中的纳滤膜制备过程中,直接将离子液体与金属有机框架共混添加在水相溶液中,而不将离子液体负载在金属有机框架材料内,制得的纳滤膜的水通量与实施例2中相比有显著提升,但对so
42
‑
的截留率下降,不利于对nacl的回收;可能是由于离子液体直接加入水相溶液后,在离子液体的位阻等作用影响下,会降低形成的聚哌嗪酰胺功能层的致密度,导致纳滤膜对so
42
‑
的截留率下降,而将离子液体负载在金属有机框架材料内部后,则可以降低其对聚哌嗪酰胺功能层致密度的影响。
57.对实施例和对比例中系统运行过程中纳滤装置的产水率(产水流量/进水流量
×
100%)和对so
42
‑
的截留率进行测试,结果如表4中所示。
58.表4:纳滤装置产水流量及so
42
‑
截留率测试结果。
59.从表4中可以看出,实施例2中采用本发明中制得的纳滤膜,与实施例1中采用市售的纳滤膜相比,纳滤装置的产水率和so
42
‑
截留率均有所提高;而对比例2中使用将离子液体直接与金属有机框架共混加入水相溶液中制得的纳滤膜,虽然产水率有所提升,但so
42
‑
截留率下降明显,不利于nacl和na2so4的回收。
60.三、回用水质及nacl和na2so4回收效果测试:对上述实施例和对比例中反渗透后得到的回用水水质及冷冻结晶得到的na2so4纯度、三效蒸发得到的nacl纯度进行测试,结果如表5中所示。
61.表5:回收效果测试结果。结果。
62.从表5中可以看出,使用本发明中的系统和方法得到的回用水中tds较低,可直接进行回用或排放;回收得到的nacl和na2so4纯度较高,可以达到工业盐和无水硫酸钠标准的理化指标要求,可进行资源化利用。
再多了解一些
本文用于企业家、创业者技术爱好者查询,结果仅供参考。